The lead acid battery charger circuits I have explained in this article can be used for charging all types of lead acid batteries at a specified rate.
This article explains a few lead acid battery charger circuits with automatic over charge, and low discharge cut off. All these designs are thoroughly tested and can be used to charge all automotive and SMF batteries up to 100 Ah, and even 500 Ah.
Introduction
Lead acid batteries are normally used for heavy duty operations involving many 100s of amps. To charge these batteries we specifically need chargers rated to handle high ampere charging levels for long periods of time.
Lead acid battery charger are specifically designed for charging heavy duty batteries through specialized control circuits.
The 5 useful and high power lead acid battery charger circuits presented below can be used for charging large high current lead acid batteries in the order of 100 to 500 Ah, the design is perfectly automatic and switches of the power to the battery and also itself, once the battery gets fully charged.
UPDATE: You may also want to build these simple Charger circuits for 12 V 7 Ah Batteries, check them out.
What does Ah Signify
The unit Ah or Ampere-hour in any battery signifies the ideal rate at which the battery would be fully discharged, or fully charged within a span of 1 hour.
For example, if a 100 Ah battery was charged at 100 ampere rate, it would take 1 hour for the battery to get fully charged. Likewise, if the battery was discharged at 100 ampere rate, the backup time would last not more an hour.
But wait, never try this, as charging/discharging at the full Ah rate can be disastrous for your lead acid battery.
The unit Ah is there only to provide us with a benchmark value which can be used for knowing the approximate charge/discharge time of the battery at a stipulated current rate.
For example when the above discussed battery is charged at 10 ampere rate, using the Ah value we can find the full charge time through the following formula:
Since charging rate is inversely proportional to the time, we have:
Time = Ah Value / Charging Rate
T = 100 / 10
where 100 is the Ah level of the battery, 10 is the charging current, T is the time at the 10 amp rate
T = 10 Hours.
The formula suggests it would ideally require around 10 hours for the battery to get optimally charged at 10 amp rate, but for a real battery this may be around 14 hours for the charging, and 7 hours for the discharging.
Because in real world even a new battery won't work with ideal conditions, and as it ages the situation may get even worse.
Important Parameters to be Considered
Lead acid batteries are expensive, and you will want to ensure that it lasts as long as possible. So please do not use cheap and untested charger concepts, which may look easy but may harm your battery slowly.
The big question is, is ideal method of charging a battery essential? The simple answer is NO. Because when we apply ideal charging method as discussed in "Wikipedia" or "Battery University" websites, we try to charge the battery at its maximum possible capacity.
For example, at the ideal 14.4 V level your battery may be fully charged, but it can be risky to do this using ordinary methods.
To achieve this without risks you may have to employ an advanced charger step charger circuit, which can be difficult to build, and might require too many calculations.
If you want to avoid this, you can still charge your battery optimally (@ around 65%) by ensuring that the battery is cut-off at a little lower level.
This will allow the battery to be always under less stressful condition. The same goes for the discharge level and rate.
Basically it must have the following parameters for a safe charging which does not require special step chargers:
- Fixed Current or Constant Current (1/10th of Battery Ah Rating)
- Fixed Voltage or Constant Voltage (17% higher than Battery Printed Voltage)
- Over Charge Protection (Cut-OFF when Battery gets charged to the above level)
- Float Charge (Optional, not compulsory at all)
If you do not have these minimum parameters in your system, then it may slowly degrade the performance and damage your battery, reducing its back up time drastically.
- For example, if your battery is rated at 12 V, 100 Ah, then the fixed input voltage should be 17% higher than the printed value, that's equal to around 14.1 V ( not 14.40 V, unless you are using a step charger).
- Current (ampere) ideally should be 1/10th of the Ah level printed on the battery, so in our case this can be 10 amperes. A slightly higher Amp input can be fine since our full charge level is already lower.
- Charging auto cut off is recommended at the above mentioned 14.1 V, but it's not compulsory since we already have the full charge level slightly lower.
- Float Charge is a process of reducing the current to negligible limits after the battery has reached full charge. This prevents the battery from self discharging and holds it at the full level continuously until it's removed by the user for usage. It is completely optional. It may be necessary only if you are not using your battery for long periods of time. In such cases too it's better to remove the battery from the charger and top it up occasionally once every 7 days.
The easiest way to get fixed voltage and current is by using voltage regulator ICs, as I have explained below.
Another easy way is to use a ready made 12 V SMPS 10 Amp unit as the input source, with an adjustable preset. The SMPS will have a small preset at the corner which can be tweaked to 14.0 V.
Remember you will have to keep the battery connected for at least 10 to 14 hours, or until your battery terminal voltage reaches 14.2 V.
Although this level may look slightly undercharged than the standard 14.4 V full level, this ensures your battery can never get over charged and guarantees a long life for the battery.
All the details are presented in this infographic below:

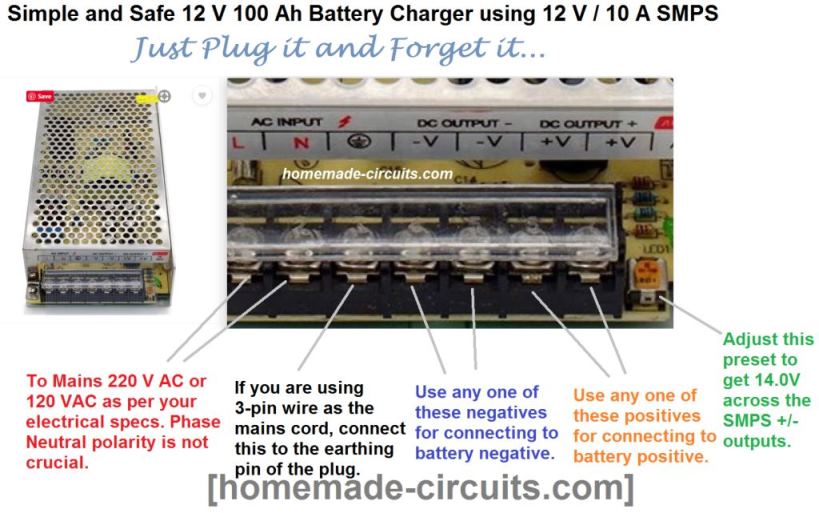
However, if you are an electronic hobbyist and interested to build a full fledged circuit with all the ideal options, in that case you can go for the following comprehensive circuit designs.
[New Update] Current Dependent Battery Auto Cut OFF
Normally, a voltage detected or voltage dependent automatic cut off is used in all conventional battery charger circuits.
However, a current detection feature can be also employed for initiating an auto cut off when the battery reaches its most optimal full charge level. The complete circuit diagram for the current detected auto cut off is shown below:
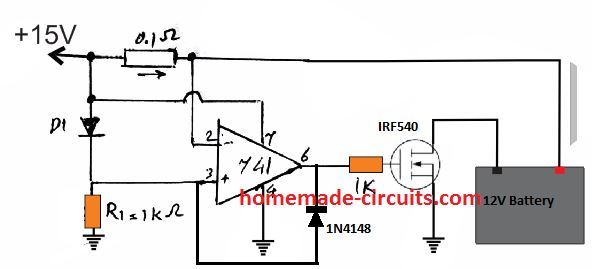
How it Works
The 0.1 Ohm resistor acts like a current sensor by developing an equivalent potential difference across itself .
The value of the resistor must be such that the minimum potential deference across it is at least 0.3V higher than the diode drop at pin 3 of the IC, until the battery has reached the desired full charge level.
When the full charge is reached this potential should come down below the diode drop level.
Initially , while the battery is charging, the current draw develops a negative potential difference of say -1V across the input pins of the IC.
Which means that the pin 2 voltage now becomes lower than the pin3 voltage by at least 0.3V. Due to this pin 6 of the IC goes high allowing the MOSFET to conduct and connect the battery with the supply source.
As the battery charges to its optimal level, the voltage across the current sensing resistor drops to a sufficiently lower level causing the potential difference across the resistor to become almost zero.
When this happens, pin 2 potential rises higher than pin3 potential, causing pin 6 of the IC to go low, and switching OFF the MOSFET.
The battery thus gets disconnected from the supply disabling the charging process. The diode connected across pin 3 and pin 6 locks or latches the circuit in this position until power is switched OFF and ON again for a fresh cycle.
The above current dependent charging circuit can be also expressed as given below:
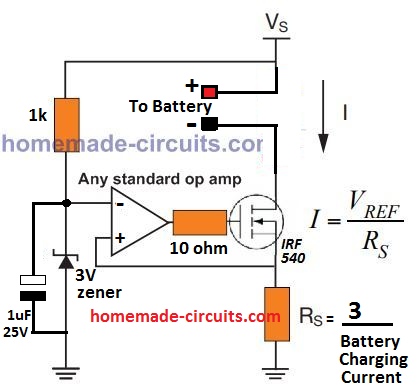
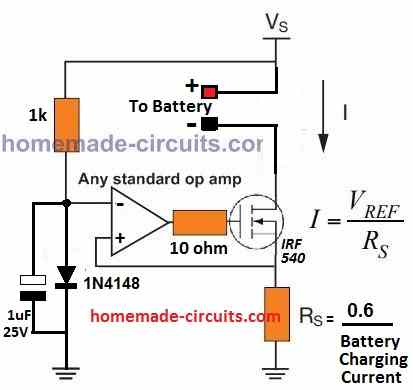
When power is switched ON, the 1 uF capacitor grounds the inverting pin of the op amp causing a momentary high at the op amp output, which switches ON the MOSFET. This initial action connects the battery with the supply via the MOSFET and the sense resistor RS.
The current drawn by the battery causes an appropriate potential to develop across RS which raises the non-invering input of the op amp above the reference inverting input (3V).
The op amp output now latches ON and charges the battery, until the battery is almost fully charged. This situation reduces the current through RS such that the potential across it drops below 3 V reference and the op amp output turns low, switching OFF the MOSFET and the charging process for the battery.
The above current dependent battery charging system design can be understood more elaborately in the below comprehensively drawn diagram, which can be used for charging very high capacity batteries in the order of 200 Ah to 500 Ah very safely:
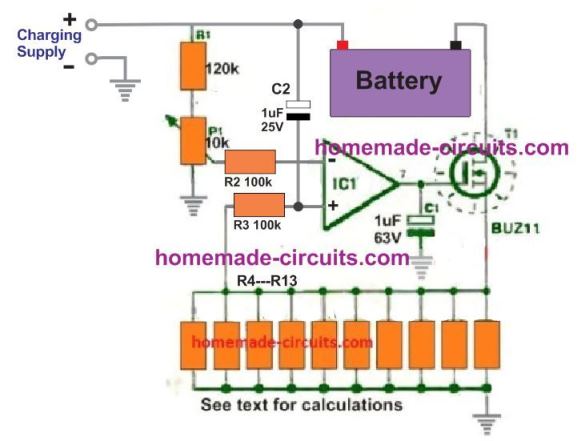
Adjust the 10 k preset so that just around 0.3 V or 0.4 V is available at the (-) input of the op amp, and set the R4---R13 resistor bank such that their net resistance is:
R = 1 / Max charging current.
Suppose the battery is 100 Ah, then the max charging current will be 10 amps, therefore,
R = 1 / 10 = 0.1 Ohms
Calculating the Parameters Accurately to Improve the above Design
The gate resistor affects the charging and discharging of the MOSFETs gate capacitance, which determines the switching speed. The formulas and explanation for improving the circuit are given as shown below:
Sense Resistor (Rs): We can calculate the charging current through the sense resistor:
I = Vref / Rs
Where:
I is the battery charging current.
Vref is the reference voltage applied to the op-amp's non-inverting input.
Rs is the sense resistor value.
To calculate Rs we can use the following formula:
Rs = Vref / I
For example if Vref = 0.6 V and the target charging current is 1 A:
Rs = 0.6 / 1 = 0.6 ohms
The power dissipation across Rs is given by: PRs = I2 * Rs
For a 1 A charging current:
PRs = 12 * 0.6 = 0.6 W
Please Choose a resistor with a power rating of at least 1 W for safety margin.
Reference Voltage (Vref): You must adjust the Vref to be stable and can be generated using a precision voltage reference IC or a resistor-divider network with a Zener diode. If you want the charging current needs to be adjustable then a potentiometer can be used to vary Vref.
Capacitor (1 µF): This capacitor stabilizes the op-amp input. It s value can be estimated using the time constant:
Tau = R * C, Where the Tau is the time constant, the R is the equivalent resistance seen by the capacitor and C is the capacitance value.
Make sure to Use a low ESR ceramic capacitor to ensure proper filtering.
MOSFET (IRF540): The IRF540 has a threshold voltage (Vgs(th)) of ~4 V. You must ensure that the op-amp can supply sufficient gate voltage for full enhancement. If the op-amp supply voltage is low (e.g., 5 V) then you must replace the IRF540 with a logic-level MOSFET like IRLZ44N.
Diode (1N4148): This diode ensures the proper operations but for better efficiency it can be replaced with a Schottky diode which has a lower forward voltage drop.
Op-Amp Selection: You must choose an op-amp with rail-to-rail output if the gate drive voltage of the MOSFET is close to the supply voltage. The Examples include LM358 (basic design) or TLV2372 (for better performance).
Example Calculation:
Let us Assume that a 12 V battery with a desired charging current of 1 A:
Vref = 0.6 V Rs = 0.6 / 1 = 0.6 ohms (use a 1 W resistor or higher)
Power dissipated in Rs:
PRs = 12 * 0.6 = 0.6 W
Then you must Choose the IRLZ44N as the MOSFET (logic level). Use a 1 µF ceramic capacitor for stabilization.
1) Using a Single Op amp
Looking at the first high current circuit for charging large batteries, we can understand the circuit idea through the following simple points:
There are basically three stages in the shown configuration viz: the power supply stage consisting of a transformer and a bridge rectifier network.
A filter capacitor after the bridge network has been ignored for the sake of simplicity, however for better DC output to the battery one can add a 1000uF/25V capacitor across the bridge positive and negative.
The output from the power supply is directly applied to the battery which requires to be charged.
The next stage consists of an opamp 741 IC voltage comparator, which is configured to sense the battery voltage while it is being charged and switch its output at pin #6 with the relevant response.
Pin #3 of the IC is rigged with the battery or the supply positive of the circuit via a 10K preset.
The preset is adjusted such that the IC reverts its output at pin #6 when the battery becomes fully charged and reaches about 14 volts which happens to be the transformer voltage at normal conditions.
Pin #2 of the IC is clamped with a fixed reference via a voltage divider network consisting of a 10K resistor and a 6 volt zener diode.
The output from the IC is fed to a relay driver stage where the transistor BC557 forms the main controlling component.
Initially, power to the circuit is initiated by pressing the "start" switch. On doing this, the switch bypasses the contacts of the relay and powers the circuit momentarily.
The IC senses the battery voltage and since it will be low during that stage, the output of the IC responds with a logic low output.
This switches ON the transistor and the relay, the relay instantly latches the power via its relevant contacts such that now even if the "start" switch is released, the circuit remains switched ON and begins charging the connected battery.
Now as the battery charge reaches about 14 volts, the IC senses this and instantly reverts its output to a high logic level.
The transistor BC557 responds to this high pulse and switches OFF the relay which in turn switches of the power to the circuit, breaking the latch.
The circuit gets completely switched OFF until the start button is pressed once again and the connected battery has a charge that's under the set 14 volt mark.
How to set up.
It's very easy.
Do not connect any battery to the circuit.
Switch ON power by pressing the start button and keep it depressed manually, simultaneously adjust the preset such that the relay just trips or switches OFF at the given rated transformer voltage which should be around 14 volts.
The setting is complete, now connect a semi discharged battery to the shown points in the circuit and press the "start" switch.
Due to the discharged battery, now the voltage to the circuit will drop under 14 volts and the circuit will instantly latch, initiating the procedure as explained in the above section.
Circuit Diagram for the proposed battery charger with high ampere capacity is shown below
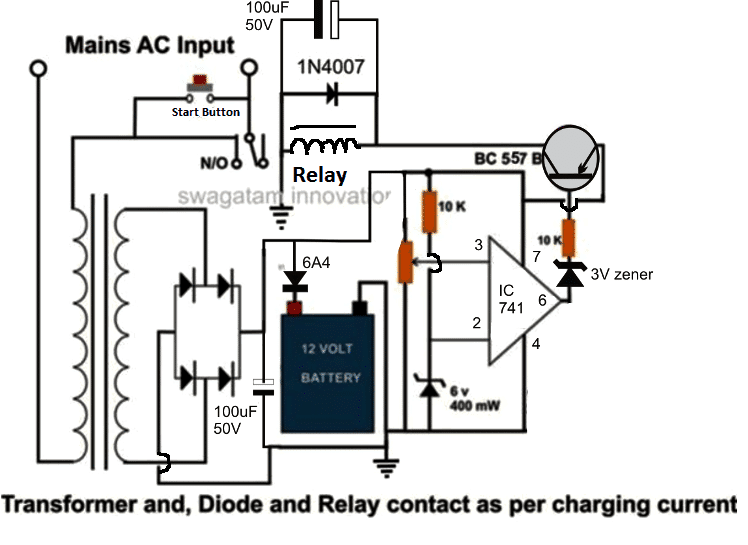
2) 12V, 24V / 20 amp Charger Using two opamps:
The second alternative way of achieving battery charging for a lead acid battery with high amperage can be observed in the following diagram, using a couple of op amps:
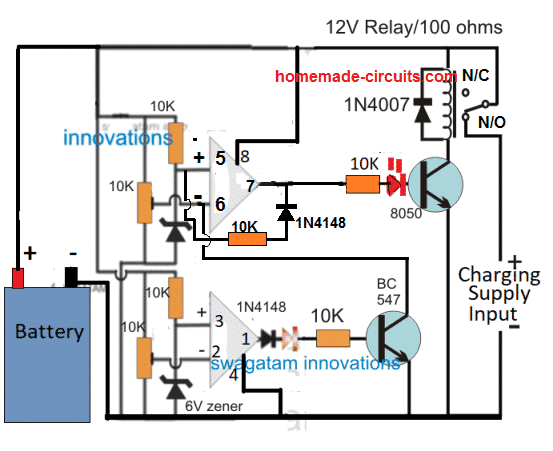
The working of the circuit can be understood through the following points:
When the circuit is powered without a battery connected, the circuit does not respond to the situation since the initial N/C position of the relay keeps the circuit disconnected from the charging supply.
Now suppose a discharged battery is connected across the battery points. Let's assume the battery voltage to be at some intermediate level, which may be between the full charge level and the low charge level.
The circuit gets powered through this intermediate battery voltage. As per the setting of the pin 6 preset, this pin detects a low potential than the pin 5 reference level. which prompts its output pin 7 to go high.
This in turn causes the relay to activate and connect the charging supply to the circuit and the battery via the N/O contacts.
As soon as this happens, the charging level also drops to the battery level and the two voltages merge at the battery voltage level. The battery now begins charging, and its terminal voltage begins increasing slowly.
When the battery reaches it full charge level, the pin 6 of the upper opamp becomes high than its pin 5 causing its output pin 7 to go low, and this switches off the relay, and the charging is cut off.
At this point another thing happens. The pin 5 is connected to the negative potential at pin 7 via the 10k/1N4148 diode, which further lowers the pin 5 potential compared to pin 6.
This is called hysteresis, which ensure that even if the battery now drops to some lower level that won't trigger the op amp back to charging mode, instead the battery level now has to drop significantly down until the lower op amp is activated.
Now, suppose the battery level keeps dropping due to some connected load, and its potential level reaches the lowest discharge level.
This is detected by pin 2 of the lower op amp whose potential now goes below its pin 3, which prompts its output pin 1 to become high and activate the BC547 transistor.
The BC547 grounds the pin 6 of the upper op amp competely. This causes the hysteresis latch to break due to pin 6 potential dropping below pin 5.
This instantly causes the output pin 7 to go high and activate the relay, which yet again initializes the charging of the battery, and the cycle repeats the procedure as long as the battery remains connected with the charger.
LM358 Pinout
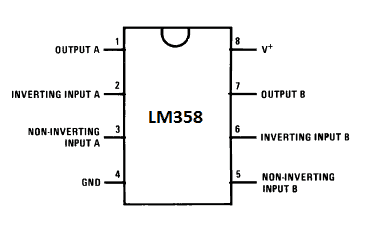
For more auto cut-off charger ideas, you can read this article regarding opamp automatic battery charger circuits.
Video Clip:
The set up of the above circuit can be visualized in the following video which shows the cut off responses of the circuit to the upper and the lower voltage thresholds, as fixed by the relevant presets of the opamps
3) Using IC 7815
The third circuit explanation below details how a battery may be charged effectively without using any IC or relay, rather simply by using BJTs, I have explained the procedures:
The idea was suggested by Mr. Raja Gilse.
Charging a Battery with a Voltage Regulator IC
I have a 2N6292 . My friend suggest me to make the simple fixed voltage high current DC power supply to charge an SMF battery.
He had given the attached rough diagram. I don't know anything about the above transistor. Is it so ?
My input is 18 volt 5 Amp transformer. He told me to add 2200 uF 50 Volt capacitor after rectification. Is it works ?
If so , is there any heat sink necessary for transistor or/and IC 7815 ? Is it stops automatically after battery reaches 14.5 volt ?
Or any other alteration needed ? Please guide me sir
Charging with an Emitter Follower Configuration
Yes it will work and will stop charging the battery when around 14 V is reached across the battery terminals.
However I am not sure about the 1 ohm base resistor value...it needs to be calculated correctly.
The transistor and the IC both may be mounted on a common heatsink using mica separator kit.
This will exploit the thermal protection feature of the IC and will help safeguard both the devices from overheating.
Circuit Diagram
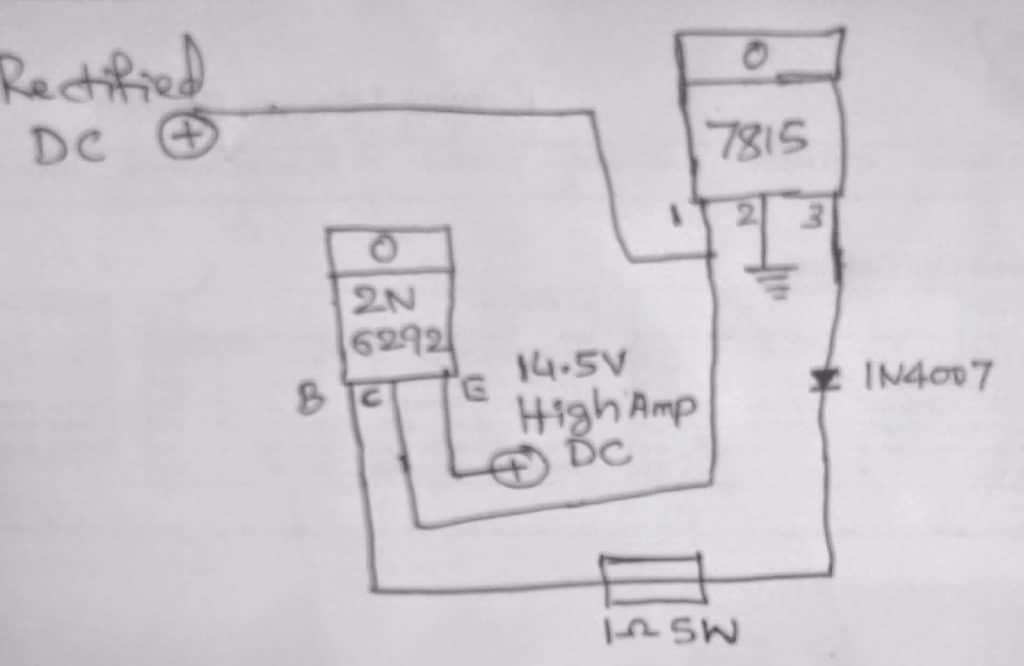
Circuit description
The shown high current battery charger circuit is a smart way of charging a battery and also achieving an auto shut off when the battery attains a full charge level.
The circuit is actually a simple common collector transistor stage using the shown 2N6292 power device.
The configuration is also referred as an emitter follower and as the name suggests the emitter follows the base voltage and allows the transistor to conduct only as long as the emitter potential is 0.7V lower that the applied base potential.
In the shown high current battery charger circuit using a voltage regulator, the base of the transistor is fed with a regulated 15 V from the IC 7815, which ensures a potential difference of about 15 - 0.7 = 14.3 V across the emitter/ground of the transistor.
The diode is not required and must be removed from the base of the transistor in order to prevent an unnecessary drop of an extra 0.7 V.
The above voltage also becomes the charging voltage for the connected battery across these terminals.
While the battery charges and its terminal voltage continues to be below the 14.3 V mark, the transistor base voltage keeps conducting and supplying the required charging voltage to the battery.
However as soon as the battery begins attaining the full and above 14.3 V charge, the base is inhibited from a 0.7 V drop across its emitter which forces the transistor to stop conducting and the charging voltage is cut off to the battery for the time being. As soon as the battery level begins going below the 14.3 V mark, the transistor is switched ON again...the cycle keeps repeating ensuring a safe charging fr the connected battery.
Base resistor = Hfe x battery internal resistance
Here's a more appropriate design which will help to achieve optimal charging using IC 7815 IC
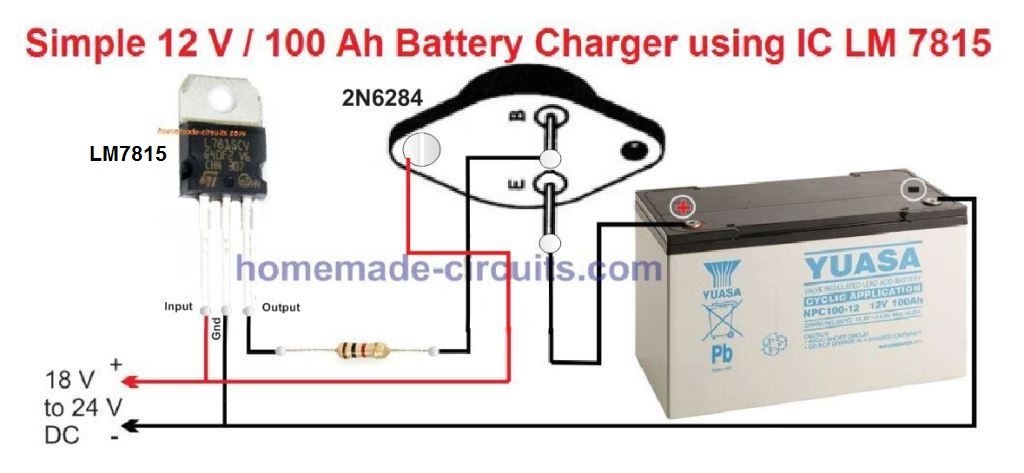
As you can see, a 2N6284 is used here in the emitter follower mode. This is because 2N6284 is a Darlington transistor with high gain, and will enable optimal charging of the battery at the intended 10 amp rate.
This can be further simplified by using a single 2N6284, and a potentiometer as shown below:
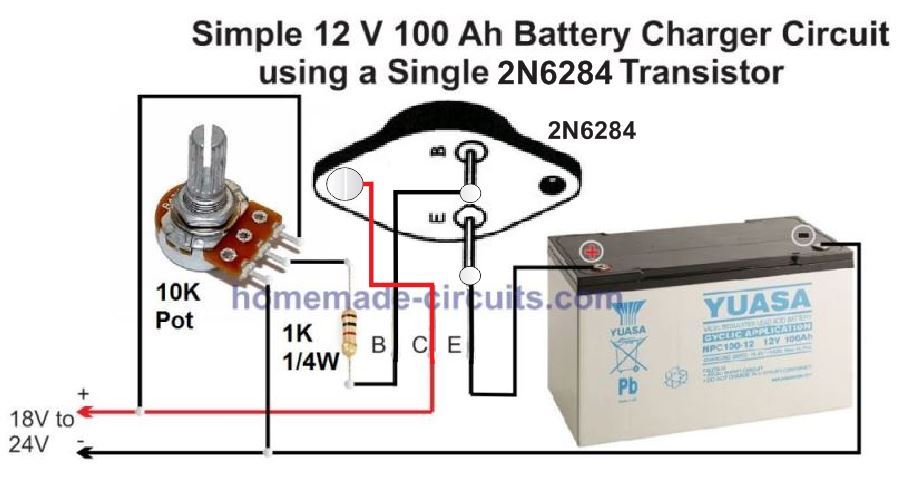
Make sure that you adjust the pot to get a precise 14.2 V at the emitter of the battery.
All the devices must be mounted on large heatsinks.
4) 12V 100 Ah Lead Acid Battery Charger Circuit
The proposed 12V 100 ah battery charger circuit was designed by one of the dedicated members of this blog Mr. Ranjan, I have explained more regarding the circuit functioning of the charger and how it could be used as a trickle charger circuit also.
The Circuit Idea
My self Ranjan from Jamshedpur, Jharkhand. Recently while googling I came to know about your blog, and become a regular reader of your blog. I learned a lot of things from your blog. For my personal use I would like to make a battery charger.
I have a 80 AH tubular batery and a 10 Amps 9-0-9 volts transformer. So I can get 10 amps 18-0 volts if I use the two 9volts leads of transformer.(Transfomer is actually obtained from an old 800VA UPS).
I have constructed a circuit diagram based on your blog. Please have a look on it and suggest me. Please note that,.
1) I am belonging to very rural area hence there is a huge power fluctuation it varies from 50V ~ 250V. Also note that I will draw very less amount of current from the battery( Generally using LED lights during power cuts) approx 15 - 20 Watt.
2) 10amps transformer i think safely charges 80AH Tubular Battery
3) All diodes used for the circuit are 6A4 dides.
4) Two 78h12a used as parallel to get 5+5 = 10 amps output. Although I think Battery must not draw full 10 amps. as it will be in charged condition in day to day use so internal resistance of battery will be high and will draw lesser current.
5) A switch S1 is used thinking that for normal charge it will be kept in off state. and after fully charging the battery it switched to on state to maintain a trickle charge with lower voltage. NOW question is that is this safe for the battery to kept in charge unattended for long time.
Please reply me with your valuable suggestions.
100 Ah battery charger circuit diagram designed by Mr. Ranjan
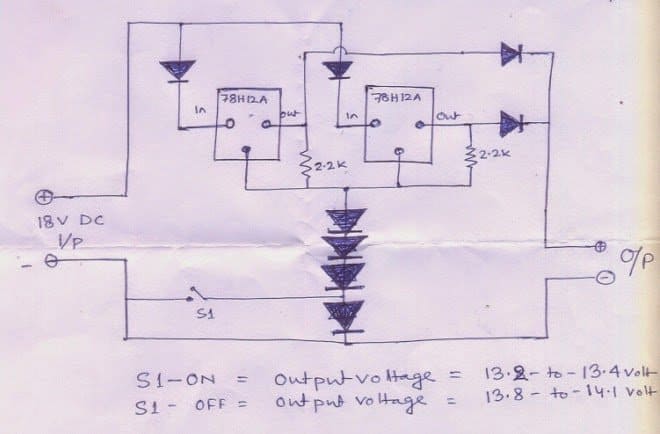
Solving the Circuit Request
Dear Ranjan,
To me your high current VRLA battery charger circuit using IC 78H12A looks perfect and should work as expected. Still for guaranteed confirmation it would be advisable to check the voltage and current practically before connecting it with the battery.
Yes, the shown switch can be used in the trickle charge mode and in this mode the battery can be kept permanently connected without attending, however this should be done only after the battery has been fully charged upto around 14.3V.
Please note that the four series diodes attached with the GND terminals of the ICs could be 1N4007 diodes, while the remaining diodes should be rated well over 10amps, this could be implemented by connecting two 6A4 diodes in parallel at each of the shown positions.
Also, it is strongly recommended to put both the ICs over a single large common heatsink for better and uniform thermal sharing and dissipation.
Caution: The shown circuit does not include a full charge cut-off circuit, therefore the maximum charging voltage should be preferably restricted between 13.8 to 14V. This will ensure that the battery is never able to reach the extreme full charge threshold, and thus remain safe from over charge conditions.
However this would also mean that the lead acid battery would be able to attain only around 75% charge level, nevertheless keeping the battery undercharged will ensure longer life for the battery and allow more charge/discharge cycles.
Using 2N3055 to Charge a 100 Ah Battery
The following circuit presents a simple and safe alternative way of charging a 100 Ah battery using 2N3055 transistor. It also has a constant current arrangement so the battrey can e charged with the correct amount of current.
Being an emitter follower, at the full charge level the 2N3055 will be almost OFF, ensuring the battery is never over charged.
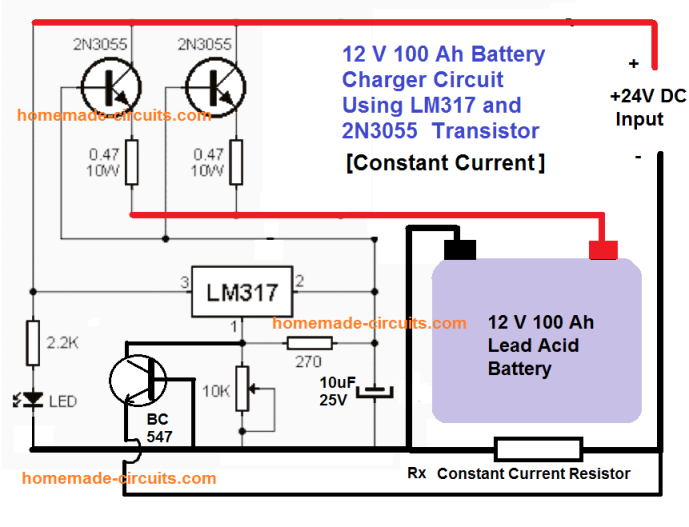
The current limit can be calculated using the following formula:
R(x) = 0.7 / 10 = 0.07 Ohms
Wattage will be = 10 watts
How to Simply Add a Float Charge
Remember other sites may present unnecessarily complex explanation regarding float charge making it complex for you to understand the concept.
Float charge it simply a small adjusted current level which prevents self discharge of the battery.
Now you may ask what's self discharge of the battery.
It's the declining level of charge in battery as soon as the charging current is removed. You can prevent this by adding a high value resistor such as a 1 K 1 watt across the input 15 V SOURCE and the battery positive.
This will not allow the battery to self discharge and will hold the 14 V level as long as the battery is attached to the supply source.
5) IC 555 Lead Acid Battery Charger Circuit
The fifth concept below explains a simple, versatile automatic battery charger circuit. The circuit will allow you to charge all types of lead acid battery right from a 1 Ah to a 1000 Ah battery.
Using IC 555 as the Controller IC
The IC 555 is so versatile, it can be considered the single chip solution for all circuit application needs. No doubt it's been utilized here too for yet another useful application.
A single IC 555, a handful of passive component is all that's needed for making this outstanding, fully automatic battery charger circuit.
The proposed design will automatically sense and keep the attached battery up to date.
The battery which is required to be charged may be kept connected to the circuit permanently, the circuit will continuously monitor the charge level.
If the charge level exceeds the upper threshold, the circuit will cut off the charging voltage to it, and in case the charge falls below the lower set threshold, the circuit will connect, and initiate the charging process.
How it Works
The circuit may be understood with the following points:
Here the IC 555 is configured as a comparator for comparing the battery low and high voltage conditions at pin#2 and pin#6 respectively.
As per the internal circuit arrangement, a 555 IC will make its output pin#3 high when the potential at pin#2 goes below 1/3 of supply voltage.
The above position sustains even if the voltage at pin#2 tends to drift a little higher. This happens due to the internal set hysteresis level of the IC.
However if the voltage continues to drift higher, pin#6 gets hold of the situation and the moment it senses a potential difference higher than 2/3rd of supply voltage, it instantly reverts the output from high to low at pin#3.
In the proposed circuit design, it simply means that, the presets R2 and R5 should be set such that the relay just deactivates when the battery voltage goes 20% lower than printed value and activates when the battery voltage reaches 20% above printed value.
Nothing can be as simple as this.
The power supply section is an ordinary bridge/capacitor network.
The diode rating will depend on the charging current rate of the battery. As a rule of thumb the diode current rating should be twice that of the battery charging rate, while the battery charging rate should be 1/10th of the battery Ah rating.
It implies that TR1 should be around 1/10th of the connected battery Ah rating.
The relay contact rating should be also selected as per the ampere rating of TR1.
How to set the battery cut off threshold
Initially keep the power to the circuit switched OFF.
Connect a variable power supply source across the battery points of the circuit.
Apply a voltage that may be exactly equal to the desired low voltage threshold level of the battery, then adjust R2, such that the relay just deactivates.
Next, slowly increase the voltage up to the desired higher voltage threshold of the battery, adjust R5 such that the relay just activates back.
The setting up of the circuit is now done.
Remove the external variable source, replace it with any battery which needs to be charged, connect the input of TR1 to mains, and switch ON.
Rest will be automatically taken care of, that is now the battery will start charging and will cut off when its fully charged, and also will get connected to power automatically in case its voltage falls below the set lower voltage threshold.
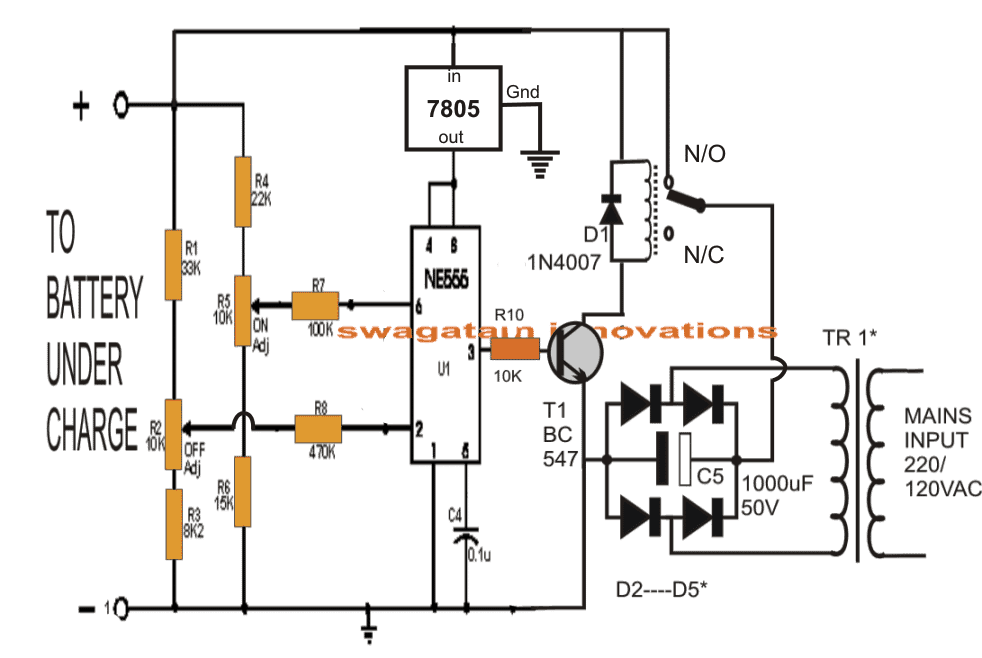
IC 555 Pinouts
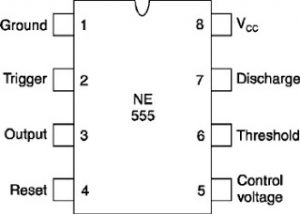
IC 7805 Pinout
How to Set Up the Circuit.
The setting up of the voltage thresholds for the above circuit may be done as I have explained below:
Initially keep the transformer power supply section at the right hand side of the circuit completely disconnected from the circuit.
Connect an external variable voltage source at the (+)/(-) battery points.
Adjust the voltage to 11.4V, and adjust the preset at pin#2 such that the relay just activates.
The above procedure sets the lower threshold operation of the battery. Seal the preset with some glue.
Now increase the voltage to about 14.4V and adjust the preset at pin#6 to just deactivate the relay from its previous state.
This will set up the higher cut off threshold of the circuit.
The charger is now all set.
You may now remove the adjustable power supply from the battery points and use the charger as explained in the above article.
Do the above procedures with lot of patience and thinking
Feedback from one of the dedicated readers of this blog:
Hi, you have made a mistake on preset R2 and R5, they should not be 10k but 100k, I just made one and it was a success, thank you.
As per the above suggestion, the previous diagram may be modified as shown below:
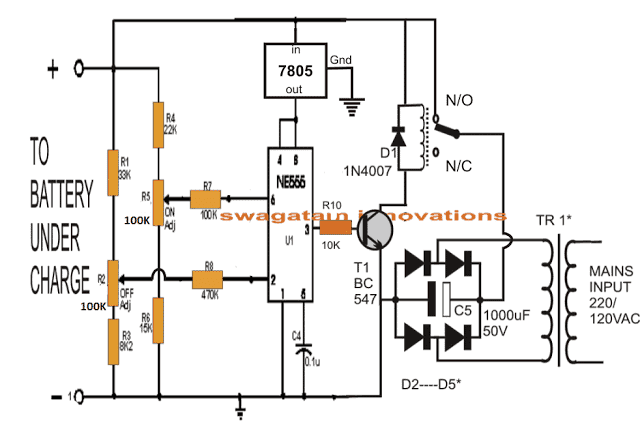
Design Steps for Automatic Lead-Acid Battery Charger using IC 555
Specifications:
- Upper cutoff voltage (V_cutoff): 14.4V (fully charged battery).
- Lower restart voltage (V_restart): 11.8V (recharge threshold).
- IC 555 supply voltage (V_CC): 12V.
Step 1: Voltage Divider for Battery Voltage
The battery voltage must be scaled to match the internal reference levels of IC 555:
- Lower reference: V_CC/3.
- Upper reference: 2 × V_CC/3.
The voltage divider is designed using resistors R1 and R2. The scaled voltage V555V_555V555 is calculated as:
V_555 = V_battery × (R2 / (R1 + R2))
For proper operation:
- At V_cutoff (14.4V), V_555 = 2 × V_CC / 3.
- At V_restart (11.8V), V_555 = V_CC / 3.
Use these conditions to calculate R1 and R2
Step 2: Calculations for R1 and R2
For Upper Cutoff (14.4V):
At V_battery = 14.4V, the scaled voltage is:
V_555 = 2 × V_CC / 3
V_555 = 2 × 12 / 3 = 8V
Using the voltage divider formula:
8 = 14.4 × (R2 / (R1 + R2))
R2 / (R1 + R2) = 8 / 14.4 = 0.555
Choose R1 + R2 = 100kΩ (standard value for simplicity):
R2 = 100kΩ × 0.555 = 55.5kΩ
R1 = 100kΩ - 55.5kΩ = 44.5kΩ
For Lower Restart (11.8V):
At V_battery = 11.8V, the scaled voltage is:
V_555 = V_CC / 3
V_555 = 12 / 3 = 4V
Using the voltage divider formula:
4 = 11.8 × (R2 / (R1 + R2))
R2 / (R1 + R2) = 4 / 11.8 = 0.338
Choose R1 + R2 = 100kΩ:
R2 = 100kΩ × 0.338 = 33.8kΩ
R1 = 100kΩ - 33.8kΩ = 66.2kΩ
Step 3: IC 555 Connections
- Pin 2 (Trigger): Connected to the voltage divider to monitor the lower threshold.
- Pin 6 (Threshold): Connected to the voltage divider to monitor the upper threshold.
- Pin 4 (Reset): Tied to V_CC (12V) to avoid accidental resets.
- Pin 3 (Output): Drives a relay or NPN transistor to control charging.
Step 4: Output Control
- Use the output of Pin 3 to drive a relay or an NPN transistor (e.g., BD139).
- Add a flyback diode (e.g., 1N4007) across the relay coil to protect against voltage spikes.
Final Component Values
Voltage Divider Resistors:
- R1 = 44.5kΩ (for cutoff), 66.2kΩ (for restart).
- R2 = 55.5kΩ (for cutoff), 33.8kΩ (for restart).
Relay: Rated for the charging current (e.g., 5A for a 12V 7Ah battery).
Flyback Diode: 1N4007.
Power Supply: Stable 12V for IC 555 (use a voltage regulator if needed)
IC 555 Current Dependent Battery Charging
The IC 555 lead acid battery charger circuit could be also built using a current sensor at its pin#2.
The complete circuit diagram is shown below:
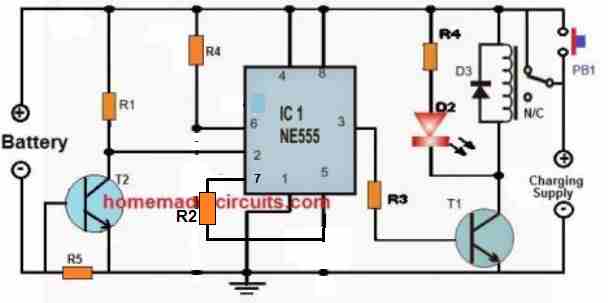
- R1, R3 = 10k
- R2 = 100k
- LED resistor can be 1k
- Pin#6 resistor R4 can be shorted with jumper link
- R5 = 1 / max charging current
- Relay = 12V relay for 12V battery.
- Relay diode = 1N4007
- T1, T2 = BC547
How it Works
The circuit is actually configured as a set/reset latch circuit.
The R4 can be replaced with a wire short.
At the start when power is applied, the relay contact being at the N/C, the circuit does not respond.
Pressing the PB1 push button, initializes the circuit by momentarily supplying the current throgh the PB1 to the battery.
The battery acts as the load, and creates a voltage drop across R5, which triggers ON the T2.
With T2 conducting pin#2 of the IC is held low, which prompts the output pin#3 to become high, and switch ON the relay.
The relay contacts now changes to N/O point and the circuit gets latched. The PB1 pressing is thus only required momentarily, and then it can be released.
As the battery gets charged, the voltage across R5 keeps getting lower, until the point when the battery is almost fully charged, when the R5 voltage drop is unable to hold the T2 ON any longer.
T2 switches OFF, causing pin#2 to go high again, and this in turn causes the pin#3 to go low, and turn OFF the relay and turn OFF the charging supply to the circuit and the battery.
Wrapping it up
In the above article I have explained 5 great techniques which could be applied for making lead acid battery chargers, right from 7 Ah to 100 Ah, or even 200 Ah to 500 Ah, simply by upgrading the relevant devices or the relays.
If you have specific questions regarding this concepts, please feel free to ask them through the comment box below.
Sir, I have a few questions on IC 555 example 1, voltage regulated.
Do I have to limit charging current somehow for smaller capacity units or does setting a diode rating only limits a maximum unit capacity that can be charged? For example I have 50Ah battery unit but I would like to use it for 100Ah in the future.
What voltage needs to be supplied for a 12V battery unit? I have access to 24V supply and a regulated step-down voltage converter.
Should I consider anything specific other than current rating when selecting a relay, for example coil resistance?
Thank you and good day, Sir.
Hi Radoslaw,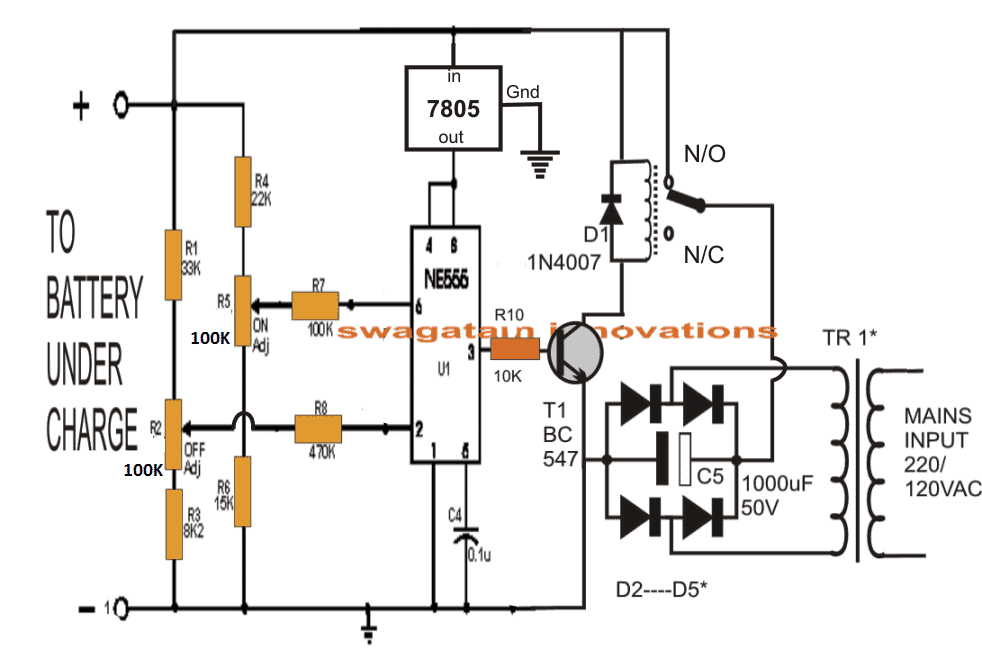
With reference to the following circuit that you are referring to:
" rel="ugc">
Yes, your transformer must be rated with a current which must be 1/10th of the battery Ah rating, considering it is a lead acid battery.
For example, for a 100 Ah battery, the transformer must be rated at 10 amp or a maximum of 15 amps.
For a 12 V battery the maximum full-charge cut-off limit can be set at 14.3 V.
The relay coil resistance mostly depends on its contact current rating, for high current contacts, the relay coil resistance will be lower and vice versa. You only have to consider the relay coil voltage which must be 12V for a 12V battery and the contact current rating must twice that of the charging current value, so for a 100 Ah battery, 10 amp charging current, the relay contacts must be rated at 20 amps or higher.
Thank you, however let me ask one of questions in another way:
What operating voltage needs to be supplied to the circuit from bridge/capacitor network for charging a 12V battery unit? Can I use a SMPS instead? If yes what voltage it should provide? I have access to 24V supply and I would need a 15-20A buck converter circuit if it needs to be lowered.
Thank you, Sir.
Radoslaw, For a 12V battery the SMPS should be rated at around 15V, and must have a current rating that is 1/10th of the battery Ah.
Yes, if you use a 24V SMPS then you must use a buck converter that can convert it into a 15V DC output with a current as mentioned above.
Sir, I followed your setup procedure however I cannot get the relay working properly.
I have successfully set R2 to activate relay at 11.5V on battery pins however as I try to tune R5 at 14.4V the relay never deactivates – I went through entire range on R5.
Any suggestions what am I possibly doing wrong here?
Hi Radoslaw,
When you adjust R2 preset at 11.5V, the relay will activate only when the pin#2 of the IC has reached below 1/3rd of Vcc 5V.
When you adjust R5 preset at 14.4V, the relay will deactivate only when the pin#6 of the IC has reached above 2/3rd of the Vcc 5V.
2/3rd of 5V is around 3.33V, so please check whether the pin#6 goes over 3.33V or not while adjusting the R5 preset.
If not, then try reducing the R4 value to 10k and check again….
Thank you Sir, for making it clear. I did manage to set the circuit by measuring voltage on pin #2 and #6.
I confirm this works as expected with R4@100k.
That’s great Radoslaw, thanks so much for updating the information….
Hi stumbled upon your site after looking into building a charger for a camper van. I had already bought a 12v 50A switching PSU, that i was going to modify for about 14.2v and just leave it connected all the time, but after reading this I realise that this would not be a good idea. So using your information on the simple safe 12v 100 amp charger, i had an idea that, what if the Voltage was set to 14.4v to fast charge, then when the battery becomes fully charged, drop the voltage to 14 volts to maintain, this could be done by altering the feedback voltage (resistance of the V adj pot).
I have in the past converted these SMPS to give different voltages, by altering the resistor divider network associated with the feedback pot (within reason to avoid letting all the smoke out!) Something as simple as a transistor or relay that just switches in a little more resistance.
Any thoughts ???
You are right, if you charge a 12V lead acid battery upto 14.3V, then you must cut off the supply immediately once reaches the 14.3V level.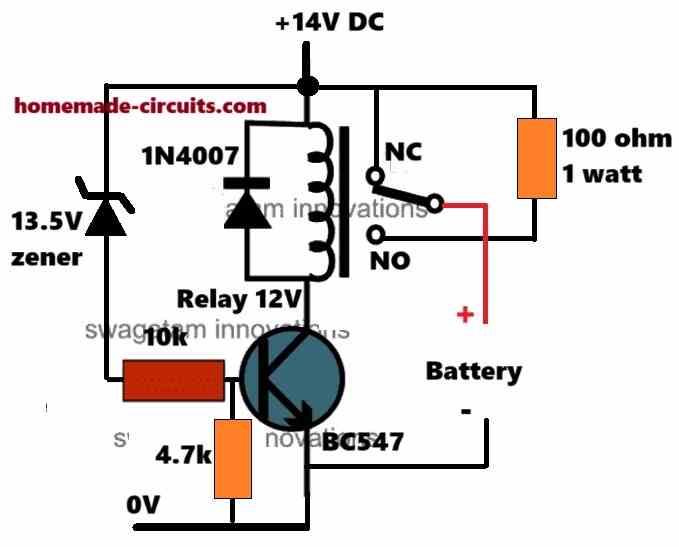
I would rather recommend not to reach the 14.3V mark at all, instead keep the input fixed at 14V, or maybe at 13.9V, to enhance the battery life further.
If you want to fast charge the battery, you can keep the initial charging current at maybe 30% to 40% of the battery value, and then reduce the current to 10% of the battery Ah once the battery voltage has reached at around 13.5V.
Here’s a simple circuit which can be used to toggle the supply current from high current to low current for implementing the fast charging safely:
" rel="ugc">
Hi,
Your circuit diagrams and explanations are excellent and I really appreciate you putting up this page.
My question is how do I modify the “Using IC 555 as the Controller IC” charging circuit to provide 30 amps of charging current to the battery?
You said to upgrade the relay and the components but I’m not sure exactly what I would need to do.
I thank you very much in advance for any guidance you can give me.
Ted
Hi, Thanks very much, and glad you found the post useful!
The relay contacts are responsible for handling the battery current so the relay must be upgraded to have a contact rating of at least 35 amps to handle 30 amp current. So for 30 amp current you would a relay whose contacts are rated at 35 amps, 40 amps or maybe 50 amps.
However, there are much easier ways to charge a battery using transistors and ICs only, without involving relays. I would recommend these instead.
Let me know if you need any further assistance.
Good day sir. For the 555 timer based 12v charger, can I replace the resistors at pin#6 and pin#2 with a series 1k resistor 5.1v zener and 4.7 v zener respectively? Will it work and is there any disadvantage?
Hello Emmanuel,
I am not sure about it, you will have to test it through a practical experimentation.
Ok sir
Thanks for your reply sir. But my second doubt still not cleared by you sir. I wanted to know whether this 555 circuit i refered to can be used for cutting of the charging process alone without making it to auto charge the battery? I want it for an emergency lamp circuit without automatic charging, but only employing auto cutoff only..and what changes need to be done for that.. pls help me sir
Binoj, If you do not want an automatic low battery detection and charging, then you can remove the pin#2 preset entirely and instead connect a push button across pin#2 and ground. Make sure to have a 10K resistor connected between pin#2 and the positive line.
But please note that I have not tested the 555 circuit yet. If you want a tested alternative you can try an op amp version which will only do automatic cut off but no automatic recharging.
Simple 3.7 V Li-Ion Battery Charger Circuit
Hlo sr, regarding the ic 555 battery charger circuit, i cant figure out how the voltage regulator actually gets the power if the output from bridge is fed through the NO contact of relay. Or is there any mistake in the diagram? Can u pls clarify the relay contacts connection. And another thing is that shall this circuit be used only for auto cutoff function and not for auto charging. If so what changes are to be made??
Hello Binoj. there’s no mistake in the diagram, it is correct.
When the battery is low. pin#2 is below 1/3rd Vcc which causes pin#3 to go high and it switches ON the relay. The relay contacts shift to N/O and start supplying power to the regulator and the battery.
Initially, at the start, when the relay contacts are at N/C, the regulator and the IC get the power from the battery.
The circuit can be used for auto cut off and also for auto charging.
Hello Sir, I have a DC supply which is 26v,52amps but I just need 24v, 17 amps to charge my 24v ,170AH battery . Can you please help me with a charger I can regulate the current and voltage?
Hello Chris, for charging a 24V lead acid battery fully you will require a minimum of 28 V. So even 26V is insufficient.
Hello sir thanks for your assistance and correction but I also have a Delta rectifier module which is 100-240v input and 54vdc-53.7A Output. Can you please assist with a charger circuit I can use with this to charge my 24v battery?
Hi Chris,
First you will need a buck converter to drop the 54V to 28V Dc, only after this you will be able to charge your battery. I don’t have this circuit with me at this moment.
Thanks for your support
hi swagatam can I implement the current sensor from the second IC555 to the first IC555 circuit?
Hi Sam, both current and voltage cut off is not recommended, you can use either of them for the cut off. Using both will not make sense!
Hello Swagatam I was talking about the first circuit in this article. Can it be ok for the 200ah 12v battery and can I use 6.2v zenar instead of 6v zena? Secondly, I was asking to know if high current Mosfet’s of about 150amp are better and makes the inverter more efficient than low current Mosfet’s?
Hello Morris, I guess you are referring to the following circuit: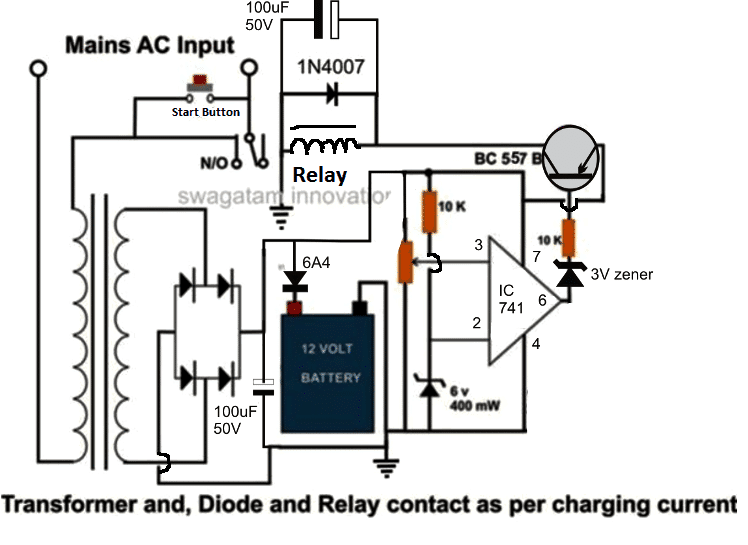
" rel="ugc">
Yes 6.2V zener will also work instead of 6V zener.
Yes, higher the current the better will be the performance of the mosfet
Ok sir. But does MOSFETs with high current consume more power from the battery faster? Secondly in an inverter circuit is it the oscillator stage design that makes inverter consume voltage Faster or the MOSFETs used in the amp stage. Thanks in advance my teacher.
The current rating of the mosfet suggests its maximum capacity to handle the current, its breakdown limit. The consumption of the mosfet depends on the wattage of the load connected across its drain, which is a transformer for an inverter. Yes the oscillator duty cycle determine how much average current the mosfet will consume.
Ok sir thanks for the response. Do u hv inverter charger circuit design that uses is mosfet as diode to charge battery whn battery gets low without bridge diode. I tried a separate transformer with bridge diodes to charge the 200ah battery but the four metal bridge diodes gets too hot???? pliz guide me
Hi Morris, yes I have one related post on how to use mosfet body diode for charging battery, you can read it here:
https://www.homemade-circuits.com/using-mosfet-body-diodes-to-charge-battery-in-inverters/
Hae Swagatam I built the first circuit and charged the battery. I used also an digital battery indicator to show me if around 14.4v it will trip the relay. The two voltages merged and started indicating 11.7 upto 14.6v without tripping the relay. Whn I disconnected the battery now reads 13.3v. Does it reads upto around 15v up for the real voltage itself to reach 14.4 to trip? Advise
Hi Morris,
14.6V is too high, you must not use more than 14.3V. Actually 14.1 V is the recommended level. If you adjust the preset correctly to trip at 14.3V or 14.1 V then the circuit surely trip at that point. Remember at the full charge level, the pin#3 voltage of the IC should become slightly higher than pin#2, this is when the op amp output will become high and the BC557 will shut off, switching OFF the relay. You can replace the 3V zener with an LED for the indication. Cathode will go to pin#6 of the IC and anode towards the resistor.
When you remove the battery after the full charge, the battery voltage will slowly drop to 12.8V and this is perfectly normal, do not expect it to stay at 14V permanently, because in the idle state the a fully charged 12V battery will show a voltage level of around 12.8v.
And what will happen if I remove also the diode to the battery terminal (6A4)? I used the circuit without it coz the 6a4 I had exploded????????.
6A4 can handle only upto 5 amps so it won’t work. You can remove it. But after full charge remove the battery from the charger otherwise it might self discharge through the op amp 10K resistor
Hello Swagatam,pliz check the first circuit in this article if it is really that way. Thi is how i set it: I first tweaked my supply to around 14.0v. Then loaded it to the circuit before connecting a battery…..tweaked again the 10k preset until the relay comes to N/O because whn it comes to N/C u will find that u just continue holding the start button for it to come on. So whn it’s tweaked to activate u just find is coming on whn u press the button once but u will wait for the relay to cut off until u see he’ll my friend???????? pliz try circuit the way it is and see then tell me. I just unplug it and find the battery is full but not cutting off
Hello Morris,
I will explain you the right process for adjusting the preset.
1) Replace the 3V zener with an LED. Cathode will go to pin#6
2) Keep the 10k preset slider to ground level.
3) Keep the push button shorted.
4) Supply around 14.1V DC across the positive and the negative lines of the 741 circuit.
5) You will find the LED switching ON, and the relay clicking to the N/O side contacts.
6) Now, slowly adjust the 10K preset until the LED just shuts off and the relay switches off to N/C contacts.
Your circuit is all set now. You can now remove the push button shorting and test the set up with an actual battery.
Hello sir can u get me the procedure of setting the second circuit in this article to function as expected.
Hello Swagatam, I have original 24v automatic charger which has two led indicators ie one for float charge and the other for quick charge. Now I bought two 100ah battery which I connected in series. Whn I connected them to that charger the red led for quick charge indicates then upon full charge or whn nearing full charge it shifts to float charge indicator. My question is that is that how the charger should be working? Can that cause any harm to the batteries? Thanks!
Hi Morris, from your description it looks like your charger controller is working correctly.
So I should not worry any harm to the bad? Now whn it shifts to float charge what happens at that time to the battery and should I just leave it to stay unplugged? Thanks sir.
Float charge is like trickle charging, using very low current, just to ensure that the battery does not self discharge. It is perfectly safe, you can keep it plugged.
Dear Swagatam
I am very thankful to you for the reply, and I suggest removing the old circuit and build a simple one without attaching the other accessories only working on AC &DC is it possible to get such a circuit .
I would like to thank u for the second part also.
You are welcome Nabeel, it is not possible to know or judge what circuit was used in your fan, because different fans have different circuits, there’s no standard circuit available in the market
Dear Sir,
I am from Iraq, I need your help with many things in the electronic field first is a circuit for the fan that can work on mains (ac) and a battery, that means when the AC is available it works normally but when AC goes off it will switch to the battery, in fact, the fan has a circuit and due to fluctuation of
electricity the Ic in charge burnt up In the power section and I don’t know the number or any think on it so I had to go for changing the circuit I could replace the bridge
and the Optocoupler but I can not read any number on it
second – I would like to learn how to design a PCB with easy aid
Hello Nabeel, If the fan has a circuit then it can be difficult to troubleshoot the issue without checking it practically.
To learn how to design PCB you can refer to the following article:
How to Make PCB at Home
Thanks for the detail and various different designs. I am trying to mimic what we commonly get off the shelf these days (smart charging, float, trickle, reverse connection protection, etc.) with the exception that i need it to have a continuous running capacity of 70A or more at 14.2 (up to 14.4V) . Is it possible to mod one of these? I am a electronics enthusiast with no formal training and have completed several small projects following plans. Thanks for your help.
Hi, the only advantage of a smart charger is that it allows a fast charging of the battery compared to the ordinary chargers. However, if the charging at normal speed is acceptable then smart charger is absolutely not required, moreover charging any battery at a standard slow rate is the most recommended since it promises longer life to the battery.
A Smart charger basically comprises of fast charging through 3 step charging, float charging or trickle charging, and temperature compensation.
In contrast, a normal good charger will have a constant current constant voltage charging, with float charging and trickle charging, which is extremely easy to implement yet is very safe.
If possible I will design a smart charger circuit soon and post in my blog, with all the above mentioned features.
I will make the IC 555 Current Dependent Battery Charging. Please i will like you to guide me. Thanks
No problem, you can ask your questions, I will try to answer them.
Hi.
Could you please share an example formula for calculating the 7.pin output for circuit 2?
I do not know how to calculate because hysteresis is made in the circuit
Hi, For hysteresis formula you can read the following article:
Opamp Hysteresis – Calculations and Design Considerations
Hai sir,
I have a few doubts regarding this circuit (5 IC 555 Lead Acid Battery Charger Circuit)
I need to design a charger for 4v 1.5AH lead-acid battery
1.Instead of using Relay we can use Transistor BD139 or BD140.
2.Preset R2,R5 value 100k for 12v battery . We can use the same value for 4v battery or need to change.
3.In this circuit the 555IC power supply is taken from Battery. Instead of taking the power supply from the battery, we can use the transformer output power supply. If we take transformer output power supply When power failure appears the IC will remain in the same state or reset.
pls guide me sir
Hi Kesavaraj,
You can replace the relay with transistors as given in the following diagram:
The IC 555 has to be connected on the battery side so that it is able to detect the battery voltage and implement the required switching of the charging input….if it is connected at the charging supply then the output will be immediately switched OFF on power switch ON
Sorry, actually the IC 555 Vcc supply can be easily shifted on the input supply side, by simply connecting the IC 7805 input to the emitter of the TIP127
Ok sir
Thank you sir
Offer of cooperation on the production of Ultra fast chargers.
I have achieved a new method by which I can charge lipoly and other types of high C batteries in up to 5 minutes without heating the battery to destruction in the battery.
Please send all the data, I’ll pot it with your credentials
hello sir I’m sorry I asked outside the contents, but this question is important for me what diode (UB02 diode.) What kind of diode is it, sir?
I am talking about circuit No:2 (12V, 24V / 20 amp Charger Using two opamps:)
And also asking the use of veriable resistor connected to pin 2 of the IC
Upper preset is for adjusting the full charge threshold, lower preset for setting the lower discharge restoration.
I mean the 10k veriable resistors
In the 3rd circuit? 3rd circuit with the relay does not have a low detection, it is only for over-charge cut off protection
For the circuit number 2 please which preset is for the set of low charge it is the preset connect to the pin 6 if yes. What is the use of the preset connected to the pin 2??? Please explain to me
I cannot see any preset? Do you want to connect a preset?
Dear Swagatam,
What is the best charger for 12 V 30 Ah Tubular Lead Acid Solar Battery with over charge protection and charging current should be within 10Amp so that the battery always will be in a good condition.
Hi Sayem,
the following circuit is perhaps the most recommended design for any lead acid battery:
https://www.homemade-circuits.com/regulated-car-battery-charger-circuit-for-garage-mechanics/
Good day Sir,
On my observation of the above; two-Opamps-in-one battery charger circuit.I think the normally open [NO] should initiate charging while[ Nc] disengages it based on the diagram.The two charge -status LEDs are not labeled ie charging and fully charged.Are they the ones close to the 10kohm at the base of the transistor?.Can the circuit be used for 8-10amp current requirement?.
Pls make a video or article on dead battery revival as i would like to learn more on epson salt.
Thank You.
Hi Patrick, you are right, the explanation needs a correction, I’ll do it soon. Yes the charger can be used for charging any battery, by suitably upgrading the relay specs.I already have an article regarding treating sulfated batteries, however I do not have the necessary calculations for getting guaranteed results, it might require some experimentation.
2 Simple Battery Desulfator Circuits Explored
Hi sir, between 15.5v and 14.4v charging voltage with auto cut off , which one do you recommend.
Hi Sheun, If you are referring to the input supply, then both will work since the auto cut-off is in operation, however for better safety 14.4V is preferable.
My dearest engineer Sir
I really appreciate your assistance regarding the battery charger.it was a success.tnk u
I have a issue at work .the 3phase 110vdc battery charger we are using got burnt and av been tasked with you must do it.am thinking of designing a controller circle for controlling the charging of the charger.the voltage I have a battery 92cells series together at low voltage it gives 110vdc and at full voltage it gives 120vdc approximately.each cell at low voltage is 1.19vdc and at full is 1.30.the transformer is 7.5kva.pls I need a controller circuit diagram for it having short circuit protection polarity protection and overcharging protection.making it full automatic.pls help me out.i want to incorporate display with it.if possible can I have ur direct mail?
Thanks Oladimeji, you can try implementing the following concept by suitably adjusting the input parameters.
https://www.homemade-circuits.com/high-voltage-360v-battery-charger/
The input supply must have a constant voltage and constant current features in-built.
Dear Sir,
Pls assist me I need an automatic battery charger circuit for 24v charger with with overcharging ,polarity protection and Auto cut off with relay, it’s o be use to charge 100 amps to 500amps pls help me out.from oladimeji
Oladimeji, you can use any one of the designs mentioned in the following article;
Op amp Battery Charger Circuit with Auto Cut Off
Replace the relay with a 24 V 50 amp relay, and transistor with a 2N2222
Hello sir tanx for your reply,if I may ask how do I set the low battery cut off and full battery cut of.also how do i determine the R6 for the automatic 24v battery charger as advertised
Tnx
Oladimeji, I have updated the setting up procedure in the op amp battery charger article, you can check it out
– What is the purpose of the 3v zener diode at the ouput of the IC741 ( Using a Single Op amp project)?
– I have replaced it with a led and it works BUT it doesn’t work if i replace it with a diode (1n4148 for instance). Have you an explanation? Thanks.
It is two block the offset leakage voltage from the op amp output, 1N4148 will work if two are used in series, cathode should be towards the op amp output pin6
Hello sir swagatam, have you ever thought how internal mosfet diodes can be used as bridge rectifiers? If so then try to figure out how this auto cut with Lm358 can be connected to a mosfet system to control charging process of a ups charging 2nos 200Ah batteries. Assume a mosfet system using 4nos mosfets say irfp3006 and design a full circuit and help me design one with an aid of a circuit diagram.
Hello Evans, I remember talking about this concept with another follower of this blog, but I can’t recall under which article the whole discussion is posted?
However, there is a similar concept is published in the following article, which probably you can modify for fulfilling your application needs
https://www.homemade-circuits.com/solid-state-relay-ssr-circuit-using-mosfets/
It has been a little while since this covid-19 lockdown and I want to say, ‘Hi’ to you. I hope you are fine.
Please continue to keep safe.
Thank you I am fine! You too keep safe.
Thanks but which configuration gives the highest current output?
Thanks.
It is common emitter which gives maximum current but needs to be cut off with an op amp at full charge
First I commend your fast responsiveness making your blog highly active. Secondly, I have been carrying out some researches on battery charging system for some days now because the life of an inverter depends to a large extent on the battery and I find your blog has the best in the world. Congratulations!
I again I want you to please explain why the emitter pin of 2N6292 and 2N6284 goes to the anode of the battery under charge in the lm7815 but it is grounded in some other configuration i.e. common emitter. Which mode, emitter follower or common emitter is the best for current amplification in charging system with 2Nxxxx family?
When the load is connected on the transistor emitter, it is called emitter follower or common collector circuit, when the load is connected on the transistor collector, it is called common emitter circuit. The advantage of emitter follower is that it allows the emitter voltage to be controlled by adjusting the base voltage, whereas in common emitter this advantage is not there. Even a 0.7V at the base will cause the whole supply to reach the load when connected at the collector side. But on the emitter side, the emitter voltage to the load will follow the base voltage and will be always 0.7 V lower than the base.
Considering the third battery charger design above using IC7815 and 2N6284, how can a BJT whether Darlignton transistor or not deliver 10amp without faulting the law of conservation of energy since the person who made the circuit-request said, ‘My input is 18 volt 5 Amp transformer.’
Input is 18Vx5A=90W
Output is 14.3Vx10A=134W.
Pls., how can this be possible? I think this transformer should be changed. I’m trying to go through again before I recommend this site to more people because it is educating.
It is basic knowledge that the output from any system will be lower than the input, so just upgrade the input according to the load requirement. It is the working concept that is important, upgrading as per personal specifications is just a matter of minutes. By the way I cannot see where I have mentioned that a 5 amp input can be used to get 10 amp output
Hello Swagatam, I have been following u since last year and I must say, ‘I like u for ur work,’
God bless u.
Don’t u think an extra diode at the anode end will help to prevent battery self-discharge? Although, I think it may prevent the system from reactivating the relay since it won’t prevent current from flowing back into the system.
Thanks.
Emmanuel.
Thanks Olamide, are you referring to the op amp transformer based design? It is supposed to be a one shot off design, so detecting the low battery is not included in the design
No, that one already has a diode at the anode. I’m referring to the fifth one having IC555. I have tested almost all the designs and I think that fifth one is most suitable for Nigerian Grid system or any other situations with unstable voltage but I suspect a slow current discharge which is taken care of by a diode but won’t allow the operating amp to detect low voltage which does still allows it to detect the 14.4v and deactivates the relay.
Thanks.
The resistor values are very high so the discharge will be extremely slow and negligible…
You are correct sir I was just thinking about complete elimination of the discharge.
Lastly I think it should work normally with regulated solar panel of correct voltage like the special one you designed with 48v. If a regulated voltage between 14-15v is fed into this fifth design in question I THINK IT SHOULD WORK to power a 12Vx10A=120w battery from a 150w panel (Energy losses considered with 5-6hrs insolation).
Have a nice Sunday.
Sir,in this high capacity charger,if one don’t want to use Relay but transistor in place of the relay what can you recommend? Thanks
Andy, you can try the following concept
Good day Swag, last year I was involved in the repair of the charging system of an imported inverter of a friend by just replacing the fuse. It also happened to the charging system of the inverter I personally built, by replacing the fuse within 2 weeks.
Please what could be responsible, sir.
Adeyemi, a fuse will blow when there’s an overload or a short circuit, you can put a current limiter in series with the supply line to make sure the fuse never blows.
Please sir, how can I get a current limiter circuit for it
You can try any of the MOSFET based designs explained in the following article:
https://www.homemade-circuits.com/universal-high-watt-led-current-limiter/
Good day sir, I bought used battery, charged it to full, but blew the inverter 2-3 times maybe due to battery short circuit. But thereafter, it worked well with the inverter. Please explain to me the principle.
Hi Adeyemi, if the battery voltage is as per the inverter specs then the inverter can never blow. Either your inverter is faulty, or the battery voltage is much higher than the inverter voltage.
Please post inverter related comments under inverter only.
Please sir, can high value capacitor used to filter the output cause overload or short circuit.Thanks Swag
No, it is fine to use a capacitor at the battery terminal.
Thanks for being always there, please what is advice on either getting a Grade A battery of 65ah and grade B of 100ah 12v battery which are same price for powering a load of 140watts.
Thanks Ademyei, I won’t be able to suggest much on this since I am not a battery expert, perhaps the manufacturer will be able to explain better.
Thanks for your reply, please to 200w freezer which set up is better in terms of efficiency, durability for 400ah battery, 200ah/24v or 100ah/48v using appropriate inverters
100Ah/48V option will be the most efficient.
Hi.
How can I use inverted power regulator for charging 100Ah battery?
i have 24V from solar panel and i need to have to charge 2 x 12V battery which is in series.
i guess the best method is using 7915 and 2N6287 a PNP version for 2N6284, but how to connect PNP darlington, with C to output and E from IC output, or viceversa?
thank you
Hi, for 24V solar panel, you don’t need any regulator, simply connect the two batts in series. Connecting them in parallel will reduce the efficiency drastically. Make sure the panel current is 5 times less than the Batt Ah value.
i connect 2 batt’s in series, but on one batt i get 14.8V (sometimes worst about 15V) and to the second 14V (or 13.8V). That’s i need to charge individualy. i didnt put batt’s in parallel, is in series, but from your excelent article, i intend to make schematic with 7815 and NPN Darlington, but i need schematic for the negative batt charger with PNP Darlington and 7912.
Thank you, also for great article!
Thanks Criss, you can try the following option, If possible I’ll update using 7912 also soon
" rel="ugc">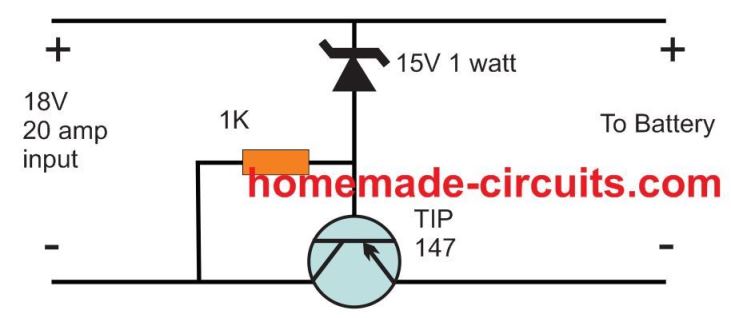
Thank you Swagatam.
Your link is what i wanted.
I found many interested article on your web site, inverters, tutorials…
You are great, thank you for your work!
Thank you Criss, Glad you liked my posts, wish you the best!
Hi sir,
I have some sort of questions regarding the auto cut off battery charger. is there any of your ideas on how to auto turn off back the relay from N-Open to N-Close position to auto recharge again the battery during low voltage at about 10 vdc? In this case I don’t have to worry about the full or the discharge of the battery and can continuously supply to my dc to ac inverter?.
I’m hoping you could share some of your good ideas regarding this matter.
Jing G. Amora from Philippines!
Thank you very much Sir!
Hi Jing,
the 3rd design from top is designed for both high and low cut offs.
You can also try the concepts presented in the following article:
https://www.homemade-circuits.com/opamp-low-high-battery-charger/
hello sir,
yes I’ve missed to read the third part of the article just before sending my text message, and
the circuit for me was so easy to understand. I’ve tried it on actual with my own pcb layout and it’s working so far right now only there are few that I have to modify about the circuit, two of the 6 volts zener diode was replaced to a bit higher 6.8 volts and all of the resistors, I replaced it to 8.2K but the 2 trimmers were as is 10K. my cut off voltage charging settings is set to 12.9 volts the relay goes to (N/C) and when the battery voltage drops to 11 volts the relay goes back to (N/O). one more idea had come to my mind is that I’ve replaced the relay to DPDT one pole is for the charging and one pole is for the ac line, so during the relay charging goes off the ac line also goes to off position.
Thank you very much Sir, you have broaden my mind and I will keep on following your good circuit designs. More Power!
Thanks Jing for your interesting feedback, I am glad the two opamp version is working for you.
However modifying the relay contact wiring may cause rapid ON/OFF vibration if the circuit is powered without a battery connected.
Anyway appreciate your involvement very much…keep up the good work!
Hi Swagatam. Thanks a lot for sharing your knowledge.
In this page there are several designs and circuits labelled as follows :
1) Using a Single Op amp
2) 12V, 24V / 20 amp Charger Using two opamps
3) Using IC 7815
4) 12V 100 Ah Lead Acid Battery Charger Circuit
5) IC 555 Lead Acid Battery Charger Circuit
My question is simple : I am planning to construct a charger for my batteries car witch are 12v – 60AH to 80AH capacity (several batteries). What are the suitable circuits i have to use witch are fully working and already tested by yourself.
Thanks.
Thanks Hedi, It will depend on a few things regarding the selection of the designs presented in the above article.
Whether you are interested to have a quicker charging, optimal charging, higher back up time and lower life, and/or the level of experience and knowledge you have in the field of practical electronics.
I would recommend the SMPS option given at the beginning of the article, since it will do the job without any fuss.
Just plug it and forget it, as it says. However all easy things come with a slight disadvantage, in this case the charging will be slightly lower than the full charge level and therefore a lower backup time. But the good thing is that it will ensure a longer life and an increased number of charge discharge cycles for your battery, provided the discharging conditions also complement the charging procedure.
So finally, just buy one 12 V 10 amp SMPS, adjust the preset to 14.1V, connect it to the battery and that’s it. Keep checking from time to time, once it reaches the set 14.1V , you can remove it and use it for the required purpose.
Thanks a lot for the quick reply . I have enough knowledge in the field of practical electronics and what i am looking for is an optimal charging design with automatic cut off circuit for 12v batteries with a capacity around 60 AH to 80 AH (this is the important criteria).
Actually as a hobbyist i don’t like to buy ready “plug and forget it” devices. As i said i have enough knowledge in electronics and a great part of the components needed for the designs listed in this page are already available in my “electronic component box”. Have as well several home made arduino uno if required. Thanks again .
OK, then you can try the first circuit using a single op amp. replace the 3V zener with a red LED, for getting the cut off indication. Cathode will go to pin#6. Make sure the transformer current is not more than the 12 amps, and the voltage can be 0-12V. Adjust the preset to get a cut off at 15V, which will produce a cut off at 14.4V for the battery due to the series diode..
By using this design, is it safe to apply directly 16.8 v at 12amps to the battery? You have mentioned in your tutorials that it is important to respect the charging voltage of a battery as well as the charging current?
Honestly i feel more confident when using voltage regulators and apply the exact charging voltage to the battery witch have also the advantage of having a larger choice of transformer voltage . Don’t you?
It is absolutely safe because the current is limited to 10 amps which is quite low for a 100 Ah battery, and moreover the cut off is set at 14.4.
If you still want to include a voltage regulator, you can use a LM396 IC after the bridge.
Another aspect is the 100uF filter which is very low and will cause the average voltage to drop even lower than 14V. If required you can eliminate the 100uF cap.
The peak voltage may become crucial when the there’s no cut off.
Absolutely clear. Thanks a lot for the explanation. I’ll give it a try and let you know how it goes.
Thanks again.
No problem, wish you all the best!
Actually i discover that it is very hard to find this kind of transformers here. My question is : can i use a 12v/10A smps power supply tweaked to 14v in replacement of the transformer and its rectifier diodes?
Yes an SMPS will also work as described in the first diagram. Adjust to 14.4V if you are use the op amp cut off
I have made the first project (auto cut off) and done the preset voltage procedure without problem (cut off at 13,8v) by using a variable voltage supply for this purpose . Till here all is ok. BUT as soon as i connect the powered circuit using a main power supply (15v at 10A) to the actual car battery (12v / 80AH) the relay enter in a big vibration mode (switching between N/O and N/C at high frequency) same thing for the leds. What may be the issue?
PS : As main power supply i am using an ATX pc power supply modified to get the 15v/10A as output.
Do you see this happening even if the push button is held depressed continuously? Also, please check whether the voltage is dropping to the battery discharge level or not. Because the if voltage is dropping then the opamp output will produce a zero voltage at its output enabling the PNP to conduct and latch the relay ON. Alternatively, you can try connecting a 1000uF capacitor right across the relay coil and check whether this solves the issue.
Also please replace the 3V zener at the op amp output with an LED for getting a direct indication of the situation, Cathode will go to the op amp pin6
No if the push button is held depressed continuously this is no more happening. I have also made the second project (automatic charger with double op amp) and successfully achieved the preset task (11,9v / 13,6v) but the issue is the same. Have replaced the relay with another brand without success. Have also put a 1500uf capacitor across the relay coil and then the switching ON/OFF frequency have decreased (the relay switch itself between ON and OFF every one second now).
ps : Have from the beginning replaced the 3v zener diode with an led.
That looks strange, I’ll check it tomorrow myself and let you know!
After several tests here are my conclusion : The vibration issue have been solved after installing the 6A4 diode at the Battery + connector (haven’t installed it initially to avoid the voltage drop across it) but now and after connecting my car battery and switching ON the power supply, the relay is never triggered when pressing the push button . In fact the system works very well when using laboratory psu without connecting a battery BUT in real life as soon as a battery AND a power supply are connected you have either a relay vibration issue if the 6A4 diode is not installed or Nothing if it’s installed.
Your conclusion is not correct. Electronics is about understanding and solving, it’s as simple as that. Some concepts are too simple and does not require testing, but they might sometimes have some minor hidden issue..and that’s why I am here… to diagnose and solve it for the needy hobbyists.
I checked the circuit and yes it was oscillating, due to the one simple issue.
As soon as the relay switches OFF at the full charge threshold, the input supply is cut off. Now the filter capacitor across the bridge begins discharging and as soon as it drops below the cut off threshold, the relay energizes again, and this continues.
The remedy is to remove the filter capacitor from the power supply, and keep a 1000uF capacitor connected across the relay coil.
If filter capacitor cannot be removed, then simply place a 1000uF capacitor across pin#3 and ground. Or add an additional 10K resistor in series with the existing base 10 K of the transistor and connect a 100uF across the junction of these 10K and ground line.
Remember, since the capacitor will initially charge, it will keep the relay ON even after the push button is released, but once the capacitor charges, the relay will switch OFF…and this result will be when battery is not connected….with battery connected everything will run normally
Swagatam have you tested one of these projects in REAL LIFE ?
Thanks a lot for the explanation witch is clear and logic. I’ll do the modification and let you know how it goes.
Meanwhile i have a question : in what cases the circuit voltage does not drop to the battery discharge level but remain at the power supply level and what is the reason of this?
Again thanks a lot for helping.
You are welcome! The voltage will not drop under two conditions, if the battery is dead, and not accepting the charge, or the battery is already fully charged. Under all circumstances the input current must be substantially low compared to the battery Ah value.
If a high current is used for a good battery, the voltage will drop initially but will rise quickly, as the battery fluid boils and the battery gets slowly destroyed and dead.
Why not use a low current threshold (battery full charged) for the cut off instead of voltage threshold?
Current based is also possible, but voltage control is the conventional and the easier option. If possible I’ll update the current based design also soon…
Thanks a lot.
I’m asking for a current based cut off circuit because i’m actually using a constant voltage battery charger (an ATX power supply modified to get 14.5 v as output connected to a current limiting resistor ) . It is working very well. But i’m obliged to verify continuously the charging current and to manually power off the psu when the charging current decreases to let’s say 100mA to avoid unnecessary loss of energy especially if I am absent. Is there a solution for this. Thanks again.
OK, You can try the following circuit for deactivating the battery charging when current reaches almost 0V:
" rel="ugc">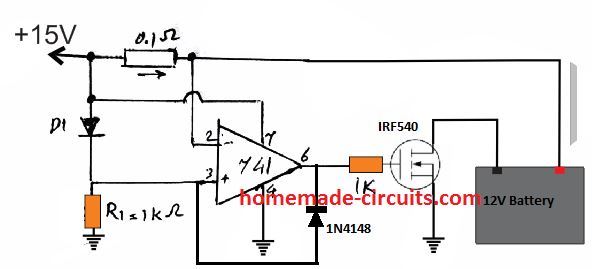
Thanks a lot Swagatam. That’s exactly what i’m looking for. You are the best.
My pleasure Hedi, I have also updated the circuit description in the article.
Thank You Very Much
TIP 147 is PNP darlington transistor.On emiter will be plus 16-24 V in and on colector is plus out.In picture is wrong.
Thank you for pointing it out, I have replaced the image with the proper one.
Good evening, is it possible to charge three 12v lead acid batteries connected in series using number 5 battery charger, if not how can I improve it to be able to charge 36v batteries.
Hello,
sorry I could not understand what you meant by “number 5 battery charger”
I mean the lead acid battery charger with 555 timer
I would recommend the second circuit, not IC 555, because I have not yet tested the IC 555 design
You are welcome!
No it is not safe to charge a 12V 5 Ah battery with 22V, 5 amp supply.
You can use an LM317 IC regulator circuit for controlling the 22V, 5 amp to 14V 500 mA, as explained in the following artcile:
12V Battery Charger Circuits [using LM317, LM338, L200, Transistors]
Thanks for taking your time sir.
I have a 1500w rated sine wave UPS I want to convert. It is designed to use 2x12v 9Ah SLA batteries (24v circuit). I want to know how possible it is to adapt it for 24v 200Ah SLA batteries, and then increase the load capacity to 5000w. I know I can increase the mosfets and change to a bigger transformer for the load (hope it’s safe), but I’d also want to upgrade the charging circuit to 20A. Please what do you recommend sir?
Hi Foxy, assuming it is a 12V UPS, you can upgrade it to 24V by replacing the transformer and the MOSFETs accordingly with matching specs, and make sure the circuit gets a regulated and stable 12V. It is perfectly safe to do this. But 24V 200 Ah will not give you 5 kva, the battery will get damaged very quickly. You may require 24V, 500 Ah for this. The charger will be 25 Ah in that case.
Good day sir! I have question about IC 555 Lead Acid Battery Charger Circuit number 5 in this article. I want to add a 5mm LEDs. 1 red led for charging and 1 green led when its done and what are the resistors in each led. Is it possible sir?
Good Day Michael, Add one LED in series with T1 base, add another LED across pin#4/8 and pin#3 through a 1K resistor
Olá amigo.
Estou tentando fazer um carregador ajustável para baterias de litio, com corte automatico de carga de 1,4V até 4,2V com um relé de 5V, um trimpot 1K e um 2n2222a. É possivel? Você tem um diagrama?
obrigado
Oi amigo, você pode fazer isso usando dois transistores como mostrado abaixo:
https://www.homemade-circuits.com/battery-full-charge-indicator-circuit/
Você pode usar 2N2907 para o transistor de LED e substituir o resistor de LED por uma bobina de relé. Certifique-se de adicionar diodos em paralelo com a bobina do relé
Sir in the 2nd circuit can i use 555 timer instead of lm358? it is not available here in our place..
Paul, sorry that is not possible because the the two ICs have different pinout arrangement.
You can try two separate IC741, or use 2 opamps from the IC LM324
sir which rating transformer is used in this circuit.
in using two opamp ckt what is charging supply input (from transformer?).
and in two opamp ckt what u use before 8050 thansistor which u show a diode sign with different colour and before bc547
Imran, the red color thing is a RED LED.
The transformer rating should match the battery voltage rating and current should be preferably 10 times less than the Ah rating of the battery if it is a Lead acid battery, or 50% less if it’s a li-ion battery
I thing there is a small mistake on this circuit.
PIN number 2 is mention next to PIN number 8. I think it should be pin 7.
thank you paaker for pointing out the mistake, I have corrected it now, please check it
Both circuits work perfect,
I hav assemble and using it.
Thanks Swag.
Thanks Paaker, I am glad it’s working!
again sir.
I am needing this automatic charge cutoff for my solar installations, if it can work well for both solar and windmill it would be great!
yes it will work for kinds of sources between 3V and 30V, for higher voltages just make sure that the IC supply is restricted below 30V (for the last circuit)
Thanks for directing me here sir… now i have some questions, can i replace IC LM358 with TL072? can i replace transistor 8050 With any darlington pair or any high voltage transistor such as tip transistor? please i will take your advice from here if i have anymore questions.
thanks for the help sir.
Youre amazing teacher for real
Thanks Nkwenti, yes you can replace LM358 with TL072, just make sure the pinouts are correctly exchanged.
The relay driver transistor can be replaced with other types but preferably it should be selected as per the rating of the relay, having said this any transistor such as a TIP122 will also work
hi sir, can this circuit be used to charge a 12v 60AH battery. thanks
Hi Joseph, yes it can used!
dear sir,
on the second circuit in the link you provided,i am asking if LM338 input is connected to battery input?
and what formular should i use when calculating resistor in parallel with the LEDS?
Regards
Jude,
yes the input is connected to the supply source (+), the output is connected to the LED (+), the negative goes directly to the LEDs. The formula is
R1 = 1.25 / LED safe current (max current)
Dear Sir,
is it proper to just connect all my bulbs(dc bulbs) directly to the positive and negative terminal of the battery without any damage to the bulbs? using the bottom charging circuit diagram.
or advise on how best i can handle this.
Thanks
It will need to be calculated with formulas, give me the V and I specs of the LED and the supply input, I’ll show you how to do it.
Dear Sir,
i have five(5) 12V , 4watts bulbs already, and i have 12V, 200AH battery for this purpose,
Thank you so much while i await your response
Jude, the total wattage of your becomes 4 x 5 = 20 watts,
You may have to include a current limiter circuit in between the supply and the LED assembly.
You can opt for the following current limiter design and use it for the purpose
https://www.homemade-circuits.com/universal-high-watt-led-current-limiter/
This will allow the supply current to pass through the above circuit and limit current before entering your LEDs
Dear Sir,
i appreciate so much for the kind responses.
i will be building the charger circuit at the bottom article this weekend.
i need a simple dc emergency light circuit diagram where i have to go straight and connect my load(i.e DC bulbs) through the charging circuit..
i just need to power five DC bulbs of 5Watts each.
Humble regards
You are welcome Jude!
I wish you all the best!
Dear Sir,
i want to build this circuit,but i want to use it to charge 12V, 200AH battery.
My questions are:
1-what are needed to be modified in the circuit to be able to charge this battery comfortably?
2-will the battery discharge after power outage when the battery is not in use,if yes,how do i prevent this?
3-how can i set up this circuit to power dc bulbs without having to build extra circuit for it.
4-i want it in such a way where i have to switch to DC for lighting in my home when there is power outage from the utility,how do i achieve this?
5-how do i wire it so that when the utility restores the light and i switches to utility,my battery starts charging automactically.
Best regards
Hi Jude,
If you want to have an automatic load switch ON, then you can try the following concept
https://www.homemade-circuits.com/make-this-automatic-10-watt-to-1000/
Only the relay will be required to be changed with a 30 amp relay.
Dear Sir,
thanks for your quick response.
i have checked the link and this questions to ask;
i am a newbie and i don`t want to make a lot of mistakes while building this circuit…does the circuit in the link has charging capacity?,
i want to build a kind of DC project where i have to power ten dc bulbs like 4watts each,through my 12V, 200AH battery.
i need a clearer explanation on how i can achieve this project in such a way that the battery will keep charging automatically when there is AC and won`t give out power except the AC is OFF.
Please note i don`t want the battery to discharge when it is not in use.
i appreciate your assistance.
regards
Jude, if you are a newbie then I am afraid this circuit may not be suitable for you, it will require a good knowledge of electronics to finish it successfully. If possible I’ll try to find an alternative design which may be easier than this one, and let you know
Dear Sir,
Newbie here does not mean i can`t finish it successfully,what i needed know is if the combination of the charger and the emergency light circuits can achieve the design i want and how to prevent discharging of the battery when not in use.
The emergency light circuit in the link does not have a charging unit and wanted to be clarified and how best i can integrate the charging circuit with the emergency light circuit to achieve my aim.
thank you again for the kind responses
Jude, yes it will accomplish the required objectives. To stop the battery from self discharging when no load is connected you could add a small value resistor from the charging supply + directly with the battery +, this will enable a permanent trickle charging for the battery and never allow it to self-discharge. The resistor value could around 1K 5 watt
Is the 741 used just as a comparator? Can it be replaced with any other regular comparator like lm393 which has two comparators as opposed to 741 which has just 1?
LM393 is a comparator and the output might need a pull up resistor, but can be applied in the above concept, other opamps like LM321 LM358 etc can also be used
I have found one problem in this circuit Sirji.
Whenever circuit is in high cut mode, I discharged the battery at 11v. But the charging doesn’t start automatically. Then I set preset for low cut so led will not off of low cut led even at 14v. So set high preset so low cut problem starts. I used 42ah battery. So what can I do?
Please guide me sir.. ..
Prashant, which circuit are you referring to?
the second circuit is tested, you can see it in the video how it correctly responds to the high and low voltage thresholds..
Prashant, do one thing, just swap the input supply with battery and battery with input supply….meaning apply supply input from the relay side on the right…and connect the battery at the left side….
I’ll update this in the second diagram soon….
Dear swag sir,
I am requesting to you that l want to make 15-20 A charging current circuit. So please give me the components list for that including transformers and bridge circuit data.
Dear Prashant, you just have to buy a 20 amp transformer, connect a 30 amp bridge rectifier with the output and a 10,000uF / 50V filter capacitor to get the required output, if you want to have any special design, please specify the details….
I have 1.5kva inverter with 24v dc and 5a charging Current circuit but I want to make 15 to 20a charging Current circuit and add it in that inverter and synchronized with it.
Can you give me details of transformer winding like primary and secondary winding gauge and no. of turns of charging transformer. Dear sir,
I want a Transformer data for 12v and 24v DC Battery charging with 15 to 20a charging current.
Hi Prashant, I am sorry, I do not have the data for the specified transformer winding, you will have to consult a professional trafo designer for this…
OK no problem sirji
Hello, its not that simple as i thought. I just purchased all the items, 10k preset, 10k resistors, LM358, BC 547, 8050, 12v Relay, 1N4007 diode,1N4148 diodes, 6V Zener, leds. But after 2 days of completely attaching the components together I am not able to use it. “””” I want a Wiring Diagram of the Second Diagram””‘ so that i can remake it again. What happen to that i build? When i attached the input voltage of above 12v relay turns on and no output on the other side and even no led lights glow. On other side I have a 12v battery connected to the circuit, when i removes the input voltage the battery itself powers relay and makes zzzzzzzz noise.
Please provide me a Wiring diagram in which all the components are connected in simple manner and with pics…. Or u can also provide me a sketch of this too… Its my first time so please help !
It is an extremely simple circuit idea but only if you do it with proper understanding, how did you set up the presets? did you use a variable power supply for this?
Give me two days I’ll make a working video of it and upload it.
I will be waiting for that video…. Please make that video as soon as possible… “” Talking about presets I didn’t setup them just soldered them into the board and thought I will rotate the screw at the top of them to set when I need it to turn ON and OFF but …… Problem persists…
yes you have set it up after soldering only, so how did you do it….I’ll try to upload the video but can’t guarantee you whether it will be quickly or not because I have other work also, but I will do it for sure, it will be not just for you for but all other readers…
In the meantime you should try fixing your circuit by correctly setting up the presets
Okay at least for now You can Provide a drawing of Second Diagram/Schematic. Just show components instead of their symbols. It will make me clear about the connections. “””” Actually I am not sure about my connections and It is difficult for me to read schematic where LM358 is connected and where Relay is connected. I hope you will provide me a Wiring diagram of mentioned schematic.
My breadboard set up is ready and the presets are responding perfectly, now only the actual battery charging procedure is pending which I’ll try to finish by tomorrow…I’ll update the diagram by inserting the pin numbers to the IC soon…
Im waiting for drawing or video. Please make me feel better as i haven’t slept from 2 days… Red eyes…. Figuring out solutions… Resolving schematic
I have updated the circuit diagram with the IC pinouts, and also I have shifted the upper LED towards the base of the transistor since this showed a better response while testing my prototype
What is this 1234 5628 written on the above diagram. Is it the lm358 pin out numbers… Thanks for Replying fast
those are IC pin numbers.
What should be the values of preset 1 & 2 ?
10K, it’s mentioned in the diagram…
Yes, but how can set up this variable value?
suppose, I want to set high cut at 14v DC. So what should be the value between 2 and 3 lead of preset of both preset.
you will have to set it up by piratical procedures, first keep the slider of upper presets to ground level, adn the slider of the lower preset to the POSITIVE level.
then feed the over charge voltage from the left side, say at 14.3V, now adjust the upper preset until the relay just clicks ON and the upper LED is ON. At this point the upper opamp will be latched.
Now reduce the input voltage slowly up to the lower discharge value, say at 11V, now adjust the lower preset until the lower LED is ON and the upper LED is OFF and the relay is also OFF.
That’s all your circuit is setnow…you can stick or glue the presets in that position.
Thanks for cooperation.
Now the circuit works.
How can increase or decrease charging ampere?
I am glad the circuit is working for you…current will need to be adjusted from the input power supply side, the above designs are only for controlling the charging levels of the battery…
I am referring second circuit.
1. How many lm358 ICs are Used in that circuit ?
2. How many Supply voltage is providing to lm358?
3. Can I providing the capacitor in parallel with relay diode? What value?
yes BC547 can be used if the relay coil resistance is not less than 200 ohms.
only one LM358 is used
LM358 can operate with max 32V supply
you an put a capacitor in parallel with relay coil, it can be a 100uF/25V
Can I use bc547 instead of 8050 transistor?
Sir, Im am a newbee… I wanted the simplified/wiring diagram of the Second Schematic diagram. Please provide me that, as i am unable to figure it out how to connect the components.
Hi Aayan, If you are confused about the opamp then you can refer to the following diagram of the IC’s internal layout IC, you just have to match and assemble it as per the given pinout specifications, if you have any other doubts please let me know…
" rel="nofollow ugc">
Hi Swag,
Hope you’re doing well.
I have three questions.
1. Can this circuit be used to charge different amperage batteries? I mean if I want to charge 45 AH, 70 AH and 200 AH?
2. What is the best way to calculate input amp/transformer power rating for a battery, assume 100 AH?
3. Do you have any transformerless power supply circuit that can provide that kind of high amperage?
Hi Saqib,
1) the circuit can be used for charging any preferred battery, by upgrading the transformer, diodes, and the relay accordingly.
2) for lead acid batteries the ideal rate of charging is always 1/10th of its AH rating, the trafo can be selected based on this rule.
3) sorry I do not have any high current transformeless SMPS circuit at this moment.
OK thanks.
To avoid having multiple chargers for different amperage batteries, can we modify this circuit to automatically detect battery capacity and give out as required like Samsung adaptive charging technology which gives 5v 2amp output when required by cellphone otherwise gives some milliamps for normal cellphones.
It may be possible, it will require some thinking, and the design can be little complex.
If possible, whenever you get some extra time from your busy schedules please try to build this circuit.
Thanks for your quick help.
sure, I’ll try to do it in my free time…
Hello Sir,
I am a fan of your work. I am having a little problem. I need a circuit that will automatically cutoff supply from a charger to 3pieces of 200ah battery charging in parallel. I was thinking of using a comparator but I have not found anything useful. The maximum charge voltage for the batteries must not be above 14volts and I definitely would love one that works with MOSFETs or any other transistor you may prescribe. Thanks a lot sir
Thanks Kelly, appreciate your feelings!
A conparator circuit is the most useful and the ultimate thing that should be used for any voltage cut off related circuit…so you must employ only an opamp based circuit for your application too!
you can try try the first circuit from the following article:
https://www.homemade-circuits.com/2014/04/48v-solar-battery-charger-circuit-with.html
if your battery is 12V you can remove the 22K resistors and the the pin#7 components, pin#7 can be directly connected with the positive line.
I am sorry I have provided the wrong link, the correct one can be seen here
https://www.homemade-circuits.com/2012/08/make-this-48v-automatic-battery-charger.html
please sir i have great challenge i need design a battery in the the battery capacity is 3.7V and overall battery capacity is 20A and a need a rechargeble circuit for that
That’s not difficult,
you can use the second design from this article:
https://www.homemade-circuits.com/2013/12/usb-automatic-li-ion-battery-charger.html
replace the 2N2907 with an IRF9540, and calculate the 3 ohm accordingly for limiting at around 15 amp.
my battery capacity is 20 amps if i connect to
that battery section that op-amp may damage i need a circuit with an IC specifically used for charging
IC will not get damaged due to current, it will get damaged if the voltage is increased above 18V.
no special IC is required, it just needs to have a CC, CV and auto cut off.
But sorry a mosfet cannot be used here because the voltage is too low to trigger a mosfet, you can use an IGBT or use a 2N2907/TIP36 in Darlington mode.
Hai swagatami want to make automatic battery charger (without switch) with cut off. I have battery 24v with 200AH. Would u like to show me how the circuit diagram? And the components? Thanks
Regards
Septian
Sir please I'm having serious challenge after making those changes and connect my power supply at the point were we have the battery connected still the led did not come up when varying, and when i measure, the voltage is not in line with the zener diode at pin#3 i have 13.16v, pin#7 i have 16.2v while pin#2 is 12.6v but when i apply the voltage sample in the opposite side i have at pin#3 4.7v, pin#7 15.18v then when i vary the 10k preset at pin#2 such that i have a voltage higher than that at pin#3 there will be no output at pin#6 but when i vary it such that voltage at pin#3 is greater there will be output at pin#6 which i have to 13.2v
But in all these varying i noticed that the led is on irrespective of fact that the voltage at pin#2 is changing its remain on
Then when i measure the voltage at the point were the battery will be it's 19.23v
Please sir what could possibly be the error and the voltage at the point were the battery will be connected i thought it should be my supply voltage and not less
If this is going to give me little problem please can you recommend another working 24v automatic battery charger please ur advice is seriously needed
Thanks and best regards
Faith, in the previous link of 48V charger which you are trying, you must feed the voltage from the points where it is mentioned "48V"….you cannot apply from the other side for this design because the mosfet would be blocking the voltage….right??
therefore if you are applying the voltage from the left hand side then it is correct and your adjustment results also look perfectly correct.
when pin#2 voltage goes above pin#3 voltage then pin#6 must become zero (cut-off)…that's correct.
Now as for the LED being illuminated all the time, this could be due to the leakage offset voltage from pin#6 of the IC741. Did you connect the shown zener diode at pin#6 of the IC?? make sure you connect that to solve the LED switching problem.
And what did you use for the power transistor, is it a mosfet or a BJT, remember if it is a BJT then you will require a resistor at its base, and the LED shifted towards the zener side, and not at the base of the BJT.
this circuit is the easiest one, and you are almost near….if you are having difficulty with such an easy circuit then just imagine what you might have to face with the other relatively complex ones…actually all opamp designs are extremely straightforward it's just about understanding them patiently.
Please sir the first circuit in this article can i use it for 24v charger?
https://www.homemade-circuits.com/2012/08/make-this-48v-automatic-battery-charger.html
yes you can use the same circuit for 24V also
I really appreciate your help and fast response please i build and tested the first circuit thishttps://www.homemade-circuits.com/2012/08/make-this-48v-automatic-battery-charger.html during setting when vary the preset the led never turn up, could it the 22k or any component i will remove from the circuit to make it work properly
the pin#2 resistor must vary and become higher or lower than pin#3 reference voltage in order to change the output state, while adjusting the preset.
yes, you can try replacing the 22K with 1K, and remove the 4k7 attached with the pin#2/ground since your supply is not 48V rather 24V only
And what could be current rating of the relay that i Wil use at that transformer current rating
I won't recommend the above circuit for a 68amp charging because the relay will need to be rated at 100A…which may be difficult to procure.
better to use the first circuit from the following article….but make sure to remove all the 22K resistors, and zener diode from pin#7 of the IC because we are using a 14V supply for your case
https://www.homemade-circuits.com/2012/08/make-this-48v-automatic-battery-charger.html
Wen i put my digital meter across the transformer and at the same time clap it with my clap meter and power it burn of my digital meter but the clap meter read 68A. My question is can this transformer be use to charge a three 12v @200A connected in parallel?
68A is too high for any standard digital meter but will be OK for a 600AH battery (200AH x 3nos)
Sir please sorry to disturb please can 650va center tap transformer charge a 12v 200A battery?
what is the current rating of the trafo…if it's 10 times less than the AH value of the batt, then it would be fine….
Please sir how do test the current of my power supply because when i use a clap meter to test the current at the positive line its reading 8. 5A could that be the current of my power supply
Faith, you can connect you DMM prods directly with the trafo wires for a few seconds and check the reading which will inform you regarding the current rating of the trafo.
make sure the DMM is set at AC 10 amp or 20 amp range.
Please sir how do test the current of my power supply because when i use a clap meter to test the current at the positive line its reading 8. 5A could that be the current of my power supply
Again i noticed that if connect it to battery for charging the battery voltage rises to the transformer voltage as if its fully charged so please i want to ask it the charging voltage or the its fully charged once connected
your power supply current(amp) rating must be 10 times lower than the battery AH rating….did you follow this rule?…if not then please make sure you do it.
Hi
i have built this circuit but when i try to set it the relay dose not flikers and it only works if the switch is connected pls what could be problem
I have explained the setting up procedure using a few simple steps, just follow those and it will be fixed.
Hi dear Swagatam thanks a lot with this good battery charger circuit. This circuit is for 10 to 20 ok. There five diodes 4 diodes are rectifier and 5 diode is used between bridge positive and battery positive and all diodes have the same value. Now if I charge a 50 ah or 70 ah batteries. should I change all diodes amp or only the bridge rectifier. Thank you very much with best regards. Rohullah.
Dear Nazari, you will have to change all the diodes except the relay diode.
please how can i determine the amp of a transformer?
connect AC ammeter directly across the secondary wires and measure
Dear sir, again my transformer with three terminal produce 14V between the last 2terminal and 7V between any of the last terminal and the center terminal. Is this the type of transformers you recommend?
yes it will do, you can use the 14V for your 12V battery, and make sure the current of the transformer is 8 to 10 times less than the AH value of the battery
Dear sir,
Thanks for this circuit. I couldn't get 6V zener but 6.8V and 3V zener but 2.8V. will still give me a good result. my hope is the 10K pot. please put me through
Dear Elvis, yes those zeners will also do, and 10k preset will also work….do not use pot.
hello swagatam,
Is this a 3-state battery charger? if no, do you have any circuit that is 3-state and charges 300AH battery. Tnx
Hi Jade,
No, the above is a single step charger, for a 3 step charger you can refer to the following article;:
https://www.homemade-circuits.com/2012/10/make-this-3-step-automatic-battery.html
King, you can try the first circuit from this article:
https://www.homemade-circuits.com/2012/08/make-this-48v-automatic-battery-charger.html
Pls sir, can u guide me to upgrade this battery charger to be able to charge my 96vols/400amps car battery, tnx!
Hi…I am confused that how are u producing dc output just after the bridge because u said in a comment that u can remove 100u capacitor.although if we continue with this capacitor I think it will discharge very quickly and produce huge ripples at output
Hi, 100% pure DC is not essential for charging a battery, however in the other comment my recommendation about removing the filter capacitor in order to eliminate the relay chattering might not be correct.
the correct remedy to prevent relay chattering at the cut-off threshold is to add 100K hysteresis resistor across pin#6 and pin#3. This will latch the opamp at the cut off levels and enable a quick and complete switch OFF of the relay and the entire system.
Filter capacitor need not be removed.
hello jade, only the transformer, the relay and the diode rating will need to be upgraded as per the battery charging current and voltage specs.
the charging current rate of a 300AH batt can be around 30 to 40 amps
hello sir.. still, the relay did not tripped after the battery is fully charged.. i also put and LED in series with the transistor base. there is no changes in the led too after the battery is fully charged. thank you for your response sir…
Erwin, please tell me how did you set the pin3 preset?
did you do it exactly as explained at the end of the article?
when you connect the discharged battery pin3 voltage is supposed to be lower than the pin2 voltage and when battery is fully charged pin3 should become higher than pin2….please confirm whether this is happening or not
sir.. is there any other way to test the circuit (if it is working) without using a battery?
erwin, you can use a 5amp 12V power supply for testing it
sir after i finished making the circuit on the breadboard and tested it… the output voltage of my charger becomes 16~17 vdc even though my battery was discharged…when i pressed the pushbutton, the relay latched but when the battery is fully charged it did not tripped or turn off the charger… i followed your circuit in every detail…by the way sir thank you for your reply on my first question..
erwin, connect an LED in series with the base of the transistor…anode to base and cathode 10K…this will give the exact idea how the opamp is behaving.
I am assuming you have done preset adjustment correctly as per the given instructions
sir…will the circuit still function even if my charger's output voltage is 16~17 volts dc? thank you for your quick reply sir..
It will work, but the current should be significantly less than the battery AH, preferably 1/10th of it.
thank you sir…
Pls sir, I need an auto-cut off 96volts/600amps car battery charger circuit diagram, tnx alot
you can try this
https://www.homemade-circuits.com/2016/01/high-voltage-360v-battery-charger.html
Can I connect a fixed resistor without using variable resistor
yes you can, after correctly calculating it..
Pls reply
What if I have to charge 7.5 v battery from wall?
use a 10V DC input
Hi Swagatam,
I need to change 50-64 amp car battery. Can I use this circuit? How much amp transformer I would be required. And also is there any other changes with capacitors and diode are need to be done here?
Hi Nabeel, yes definitely you can use this circuit for charging a 50AH 0r 60AH battery, the transformer current rating should not be more than 8 amps.
the bridge rectifier diodes must be rated at 10amps each…or a single 10amp bridge module will also work at the indicated position
Sir, can I use this circuit for charging lead acid battery 24v?
yes you can do it….
Oke. Thankyou sir, by the way I need to change that ic or not? Example that relay, comparator, or something else?
yes, just forgot to tell you, you can use a LM321 IC as it's rated to work with upto 32V…the IC 741 IC will burn at over 22V so won't work with 28V inputs
oke, thankyou so much sir..
Plz swagatam videos URL send me
sorry sharanab, there's no video for this circuit.
Hi, this system would serve me to charge a solar battery and 300Ah 24v?
thank you very much
you are welcome popipo
Plz swagatam 100 AH 12 V battery charg. And inverter system circuit send me
My mail : sharanbs.basava39@gmail.com
you can use the above circuit for the charging the battery or the second circuit from the following link:
https://www.homemade-circuits.com/2011/12/how-to-make-simple-low-battery-voltage.html
for the inverter I'll need more info regarding its specs
I have a modified pc smps that gives 14v and 20A
so I want a circuit that charges a 12v 100ah battery automatically ie it should turn off the smps when battery is full and turn on the smps when the battery is low
you can try the second circuit from the following article:
https://www.homemade-circuits.com/2011/12/how-to-make-simple-low-battery-voltage.html
if i just avoid the rectifier portion and use a varying dc source, will the circuit work .please let me know
i did not understad what you are trying to implement…pls make it clearer
thank you for the replayed sir,no i did not make any modifications but one thing is that i use 1n5399 for the 4 diode showing there and also i used In540(16A4) the one that connect to the battery positive is it 6A or 6.4A? sir i build one of your circuit How to Make a Simplest 200 VA Uninterrupted Power Supply UPS Circuit i build only the charger it work very well but i don't think it can charge 24vDC battery two 12v battery? if it can chard what can i do sir help me with the circuit thank you jah guide you and hop to hear from you soon..
Daniel, Referring to the charger circuit shown in this article:
https://www.homemade-circuits.com/2012/02/how-to-make-simplest-200-va.html
You can use it for charging 24V batt also…you just have to upgrade the circuit with a 0-24V transformer and 24V relays. R1 should be replaced with 10k resistor.
Remember the transformer current should 1/10th of battery AH.
Hi Swagatam,
Thanks for your prompt and positive response.
I just read, – Hire me for Designing Circuits – Circuit Ideas, Inventions for Sale – in your blog.
I have a special requirement for my set up, the details I will send to your email ids you have mentioned, would you be kind enough to reply whether there is any scope for making them and your charges as well?
Regards
NG
Thanks Naga, I have replied to your email, please check it.
Hi Swagatam,
I wish I had seen your blog earlier. In my set up, I need my charger, connected to the 220 Volts AC mains to start automatically to charge the battery when the voltage drops to 11 and stop the charger when the battery is charged to 14 volts.
Your advise and guidance would be of immense value.
Regards
NG
Thanks NG,
you can try the last circuit from the following link:
https://www.homemade-circuits.com/2011/12/how-to-make-simple-low-battery-voltage.html
You will see two relays in the diagram, the lower relay is not required so you can just eliminate it from the design.
…during normal charging operation switch ON the circuit only after connecting the battery to the shown points.
Thanks very much, you can do the following things:
Connect an LED in series with the transistor base 10k (anode to base, cathode to 10k) for indication.
Keep the transformer disconnected, and apply an external power supply of 14.4v across IC supply pins.
Now flick the preset to and fro until you find a point where the LED toggles ON/OFF, adjust this point to just switch ON the LED.
Your circuit is all set now.
Now carry on with its normal operations through the trafo.
While adjusting the preset do not connect the battery.
remove push-button connections, connect the trafo directly to mains, and connect the battery positive to bridge positive via relay N/O and pole contacts.
Hi Daz, please check it out here:
https://www.homemade-circuits.com/2013/08/automatic-dual-battery-charger-with.html
thanks my friend.. looking forward in your design.
Thank you Daz,
It might take some days to complete it, I'll inform you as soon as it's done.
thank you so much my friend… youre so very kind and very quick when it comes in response.. once youre circuit done and it worked for me, i will then donate something to you. i am very interested with this design to build. thank you so much and more power swagatam! please keep update me soonest possible. thanks again.
Hi Daz,
Thanks!
I have noted it, will try to update the article soon.
it would be possible to you design that circuit? thank you so much swagatam
yes you're right sir! thanks for the response! can you design that for me sir? thank you so much and more power!
Sir,
Thank you very much for your quick reply. 10 amps would be enough for me , would you be able guide us for using ICs like 338, 196 etc on this circuit ? it would be very useful for you.
Thank you once again sir
With best regards
Maung Pru
Hi Maung,
You can try the last circuit given in this article:
https://www.homemade-circuits.com/2012/07/making-simple-smart-automatic-battery.html
Replace the IC LM338 with LM196 for 10 amp specs.
Hi Maung,
can you specify your current requirement, if it's upto 10 amps then it can be simply done using ICs like 338, 196 etc, otherwise it would become sightly complicated.
Sir,
Thank you once again.
would it be possible to add a charging current controller?
would you please kindly explain us what type of component need to be use ?
Thank you and with best regards
Maung Pru
…the 100uF is not required, because its inclusion actually makes no difference, so it can be removed
Thanks, I appreciate your attempt, here are more precise answers:
AH signifies the charge or the discharge rate of the battery. ideally it indicates the full charge or full discharge rate of the battery in an hours period.
Opamps are excellent comparators and they work very well in battery charge cut off applications.
hysteresis is surely needed so that the relay doesn't keep switching ON/OFF at the thresholds due to the extreme accuracy and sensitivity of the opamp.
Hysteresis delays the relay actions and makes the response slower so that it doesn't chatter…… without hysteresis the relay would snap rapidly producing rapid switching at the thresholds.
A hysteresis can be added in the above diagram to avoid the same.
In the above diagram the position of the relay switches OFF power completely, right from the transformer, so it becomes much safer and reiable.