The presented 3 phase VFD circuit (designed by me) can be used for controlling the speed of any three phase brushed AC motor or even a brushless AC motor. The idea was requested by Mr. Tom
Using the VFD
The proposed 3-phase VFD circuit can be universally applied for most 3-phase AC motors where the regulation efficiency is not too critical.
It can be specifically used for controlling squirrel cage induction motor speed with an open loop mode, and possibly also in the closed loop mode which will be discussed in the later part of the article.
Modules Required for 3 Phase Inverter
For designing the proposed 3 phase VFD or variable frequency drive circuit the following fundamental circuit stages are essentially required:
- PWM voltage controller circuit
- 3 phase high side/low side H-bridge driver circuit
- 3 Phase generator circuit
- Voltage to frequency converter circuit for generating V/Hz parameter.
I have explained the functioning details of the above stages with the help of the following explanation:
A simple PWM voltage controller circuit can be witnessed in the diagram given below:

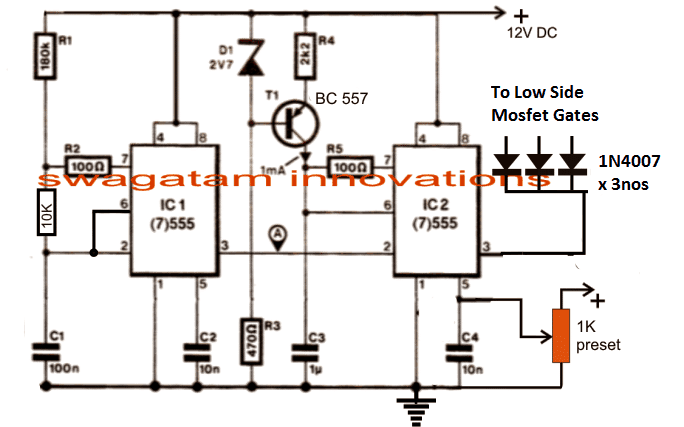
The PWM Controller
I have already incorporated and explained the functioning of the above PWM generator stage which is basically designed for generating a varying PWM output across pin3 of IC2 in response to the potential applied at pin5 of the same IC.
The 1K preset shown in the diagram is the RMS control knob, which may be appropriately adjusted for acquiring the desired proportionate amount of output voltage in the form of PWMs at pin3 of IC2 for further processing. This is set to produce a corresponding output that may be equivalent to the mains 220V or 120V AC RMS.
The H-Bridge Driver Circuit
The next diagram below shows a single chip H-bridge 3 phase driver circuit using the IC IRS2330.
The design looks straightforward as most of the complexities are handled by the chips in-built sophisticated circuitry.
A well calculated 3 phase signal is applied across the HIN1/2/3 and LIN1/2/3 inputs of the IC through a 3 phase signal generator stage.
The outputs of the IC IRS2330 can be seen integrated with 6 mosfets or IGBTs bridge network, whose drains are appropriately configured with the motor which needs to be controlled.
The low side mosfet/IGBT gates are integrated with the IC2 pin#3 of the above discussed PWM generator circuit stage for initiating the PWM injection into the bridge mosfet stage. This regulation ultimately helps the motor to gain the desired speed as per the settings (via the 1 k preset in the first diagram).
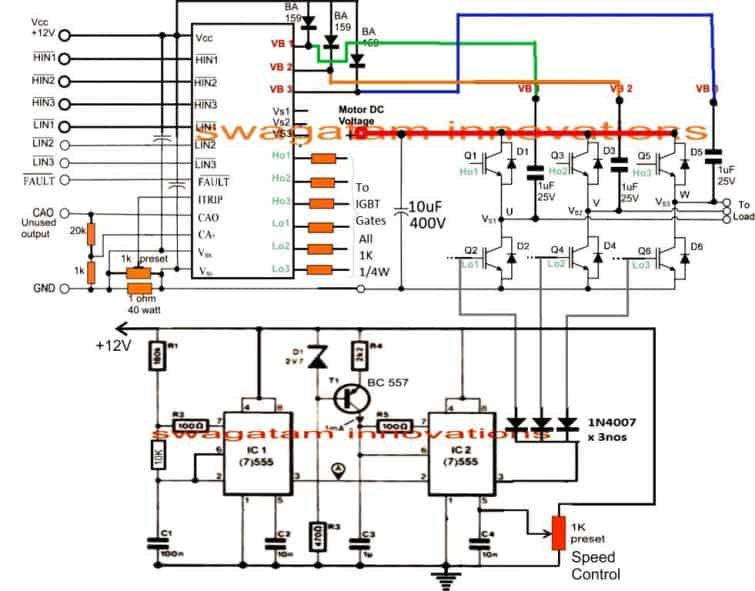
In the following diagram we visualize the required 3 phase signal generator circuit.
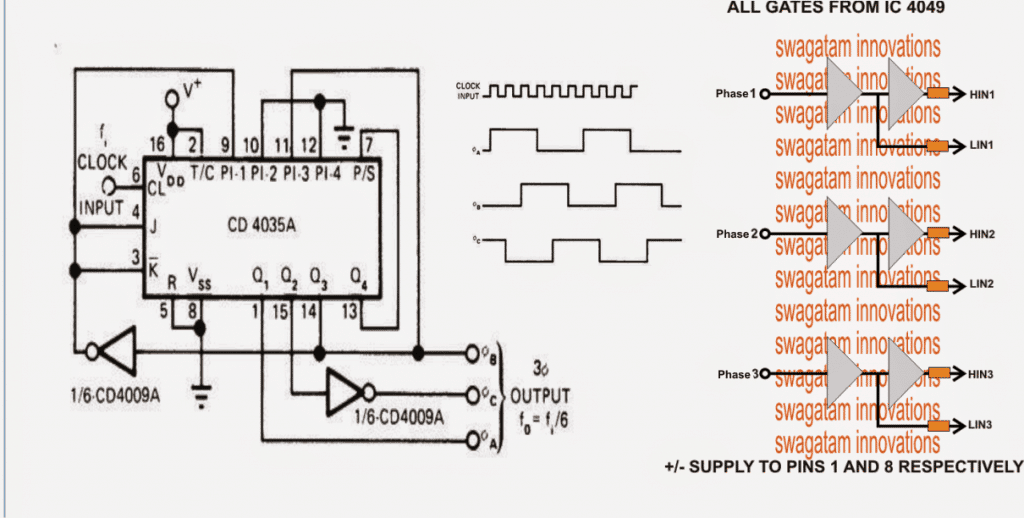
Configuring the 3-Phase Generator Circuit
The 3 phase generator is constructed around a couple of CMOS chips CD4035 and CD4009 which generates accurately dimensioned 3 phase signals across the shown pinouts.
The frequency of the 3 phase signals depends on the fed input clocks which should be 6 times the intended 3 phase signal. Meaning, if the required 3 phase frequency is 50 Hz, the input clock should be 50 x 6 = 300 Hz.
It also implies that the above clocks could be varied in order to vary the effective frequency of the driver IC which in turn would be responsible of varying the motor operational frequency.
However since the above frequency alteration needs to be automatic in response to the varying voltage, a voltage to frequency converter becomes essential. The next stage discusses a simple accurate voltage to frequency converter circuit for the required implementation.
How to Create a Constant V/F Ratio
Typically in induction motors, in order to maintain an optimal efficiency of the motor speed and toque, the slip speed or the rotor speed needs to be controlled which in turn becomes possible by maintaining a constant V/Hz ratio. Since the stator magnetic flux is always constant regardless of the input supply frequency, the rotor speed becomes easily controllable by maintaining the V/Hz ratio constant.
In an open loop mode, this can be done roughly by maintaining predetermined V/Hz ratios, and implementing it manually. For example in the first diagram this may be done by suitably adjusting the R1 and the 1K preset. R1 determines the frequency and the 1K adjusts the RMS of the output, therefore by suitably adjusting the two parameters we can enforce the required amount V/Hz manually.
However to get a relatively accurate control of an induction motor torque and speed, we have to implement a closed loop strategy, wherein the slip speed data needs to be fed to the processing circuit for an automatic adjustment of the V/Hz ratio so that this value always remains near about constant.
Implementing the Closed Loop Feedback
The first diagram on this page can be suitably modified for designing the closed loop automatic V/Hz regulation as shown below:
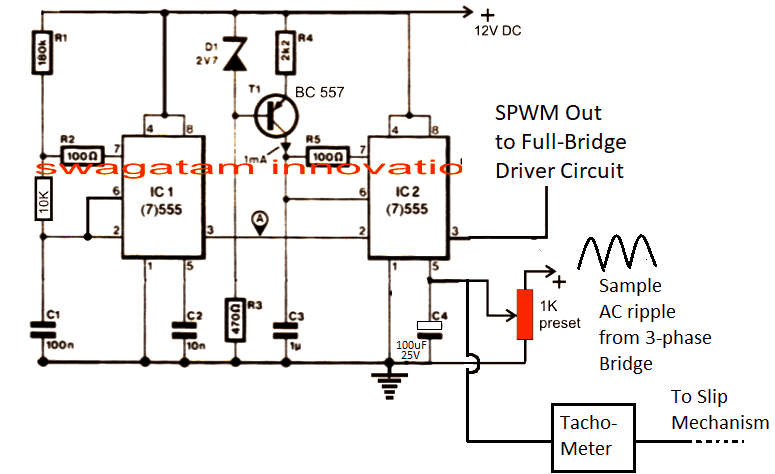
In the above figure, the potential at pin#5 of IC2 determines the width of the SPWM which is generated at pin#3 of the same IC. The SPWM are generated by comparing the mains 12V ripple sample at pin#5 with triangle wave at pin#7 of IC2, and this is fed to the low side mosfets for the motor control.
Initially this SPWM is set at some adjusted level (using 1K perset) which triggers the low side IGBT gates of the 3-phase bridge for initiating the rotor movement at the specified nominal speed level.
As soon the rotor rotor begins rotating, the attached tachometer with the rotor mechanism causes an proportional additional amount of voltage to develop at pin#5 of IC2, this proportionately causes the SPWMs to get wider causing more voltage to the stator coils of the motor. This causes further increase in the rotor speed causing more voltage at pin#5 of IC2, and this goes on until the SPWM equivalent voltage is no longer able to increase and the stator rotor synchronization attains a steady-state.
The above procedure goes on self adjusting throughout the operational periods of the motor.
How to Make and Integrate the Tachometer
A simple tachometer design can be seen in the following diagram, this could be integrated with the rotor mechanism such the rotational frequency is able to feed the base of the BC547.
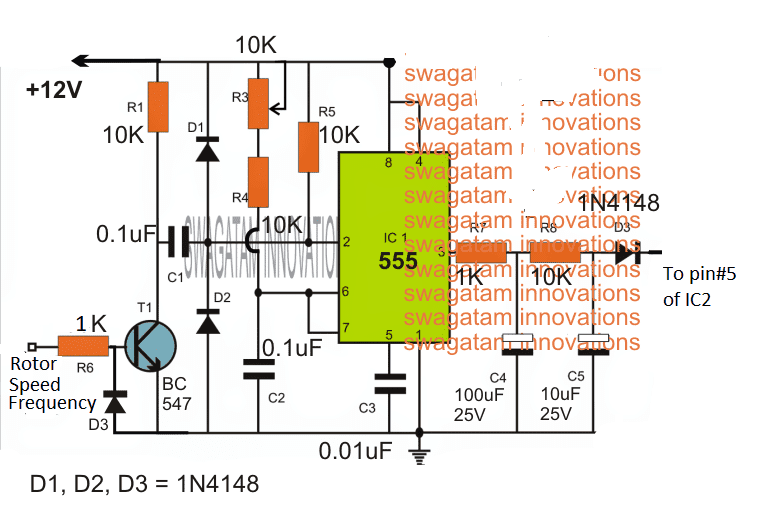
Here the rotor speed data is collected from a hall effect sensor or a IR LED/Sensor network and is fed to the base of T1.
T1 oscillates at this frequency and activates the tachometer circuit made by appropriately configuring an IC 555 monostable circuit.
The output from the above tachometer varies proportionately in response to the input frequency at the base of T1.
As the frequency rises the voltage at the extreme right side D3 output also rises and vice versa, and helps to keep the V/Hz ratio to a relatively constant level.
How to Control Speed
The speed of motor using constant V/F can be achieved by altering the frequency input at the clock input of IC 4035. This can be achieved by feeding a variable frequency from a IC 555 astable circuit or any standard astable circuit to the clock input of IC 4035.
Changing the frequency effectively changes the operating frequency of the motor which correspondingly lowers the slip speed.
This is detected by the tachometer, and the tachometer proportionately reduces the potential at pin#5 of the IC2 which in turn proportionately reduces the SPWM content on the motor, and consequently the voltage for the motor is reduced, ensuring motor speed variation with the correct required V/F ratio.
A Homemade V to F Converter
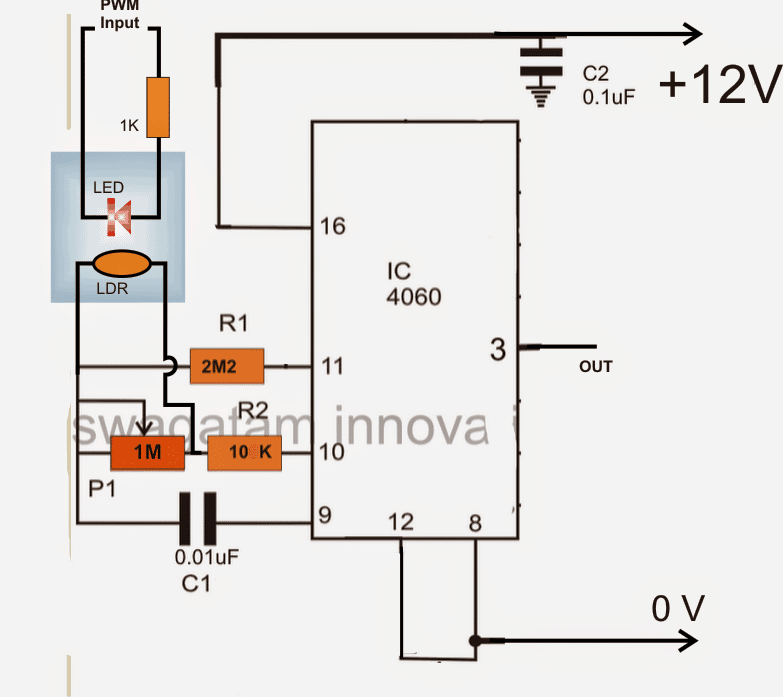
In the above voltage to frequency converter circuit a IC 4060 is used and its frequency dependent resistance is influenced through a LED/LDR assembly for the intended conversions.
The LED/LDR assembly is sealed inside a light proof box, and the LDR is positioned across a 1M frequency dependent resistor of the IC.
Since the LDR/LDR response is fairly linear, the varying illumination of the LED on the LDR generates a proportionately varying (increasing or decreasing) frequency across pin3 of the IC.
The FSD or the V/Hz range of the stage could be set by appropriately setting up the 1M resistor or even the C1 value.
The LED is voltage is derived and illuminated through the PWMs from the first PWM circuit stage. It implies that as the PWMs vary, the LED illumination will also vary which in turn would give rise to a proportionately increasing or decreasing frequency at pin3 of the IC 4060 in the above diagram.
Integrating the Converter with VFD
This varying frequency from the IC 4060 now simply needs to be integrated with the 3 phase generator IC CD4035 clock input.
The above stages form the main ingredients for making a 3 phase VFD circuit.
Now, it would be important to discuss regarding the DC BUS required for supplying the IGBT motor controllers and the setting up procedures for the entire design.
The DC BUS applied across the IGBT H-bridge rails may be obtained by rectifying the available 3 phase mains input using the following circuit configuration. The IGBT DC BUS rails are connected across the points indicated as "load"
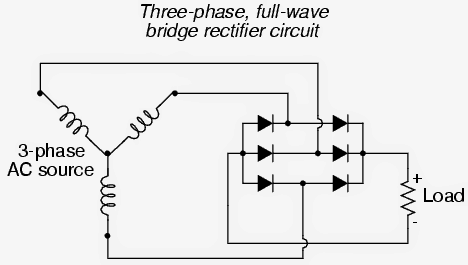
For a single phase source the rectification may be implemented using standard 4 diode bridge network configuration.
How to Set Up the proposed 3 phase VFD circuit
It may be done as per the following instructions:
After applying the DC bus voltage across the IGBTs (without the motor connected) adjust the PWM 1k preset until the voltage across the rails become equal to the intended motor voltage specs.
Next adjust the IC 4060 1M preset in order to adjust any of IC IRS2330 inputs to the required correct frequency level as per the given motor specifications.
After the above procedures are completed, the specified motor may be connected and supplied with different voltage levels, V/Hz parameter and confirmed for an automatic V/Hz operations over the connected motor.
Dynamic Braking Resistor (DBR) or Dynamic Braking Unit (DBU) is an essential electrical component used in various industrial applications to safely dissipate extra energy produced when an electric motor or other devices are braking. When a motor slows down or stops, it behaves like a generator, creating a reverse electrical current called back electromotive force (EMF). If this energy isn’t managed properly, it could cause damage to both the motor and the connected drive system.
To handle this excess energy, dynamic braking is used in systems like elevators, cranes, electric trains, and vehicles—basically any equipment that requires frequent, controlled slowing down or stopping. In most setups, the DBR works alongside a Variable Frequency Drive (VFD), which is a motor-controlling system that helps regulate this braking process. In this guide, we’ll walk through how to connect a Dynamic Braking Resistor to a VFD.
Step-by-Step Connection Guide
Identify the DBR Terminals in the VFD:
Most VFDs come with specific terminals dedicated to connecting a DBR. Typically, there are two terminals, one for the positive connection and another for the negative. These terminals are usually labeled “+” and “-” or more commonly as “DC+” and “DC-”. In the wiring diagram provided, you’ll see that the VFD has clearly marked “DC+” and “DC-” terminals.
Connect the Input of the DBR to the VFD:
You’ll then connect one terminal of the DBR to the “DC+” terminal on the VFD and the other DBR terminal to the “DC-” on the VFD. This setup allows the DBR to absorb the extra energy generated by the motor while braking.
Consider a Resistor Contactor or Brake Chopper:
In some VFD setups, you might need an additional component like a resistor contactor or brake chopper to control how the DBR is connected to the VFD. A brake chopper is a solid-state device that regulates the flow of energy between the VFD and the DBR. If your system includes one, make sure to follow the manufacturer’s directions for proper installation.
Configure the VFD’s Parameters:
To enable the DBR to function properly, you’ll need to adjust some settings on the VFD. This might include turning on dynamic braking mode, entering the correct resistance value of the braking resistor, and configuring torque or current limits. These settings vary depending on the model of your VFD and the specific needs of your application.
Always follow the manufacturer’s instructions for both the VFD and DBR when making connections and adjusting parameters. Incorrect setup or misconfigured parameters can result in system errors or even damage the equipment. Consulting the user manuals is highly recommended.
How Dynamic Braking Works
When the motor is slowing down or stopping, the VFD senses this and switches to dynamic braking mode. Instead of just cutting power to the motor (as in normal stopping), the VFD directs the surplus energy generated during braking to the DBR.
In this system, the DBR is connected in parallel with the VFD’s DC bus and acts as a load that absorbs this excess energy. The DBR has a high-power rating and specific resistance designed to convert the energy into heat safely.
Because dissipating energy in the form of heat can cause the DBR to overheat, they are usually equipped with cooling systems like heatsinks or fans to keep the temperature down.
Once the braking process is complete, the VFD switches back to its normal mode, resuming its role of supplying the right amount of voltage and frequency to the motor for smooth operation.
In summary, a DBR ensures that the energy generated when slowing down a motor is safely and efficiently managed, preventing damage to the motor and other electrical components.
Thank you Jitu,
you can try the following circuit:
" rel="ugc">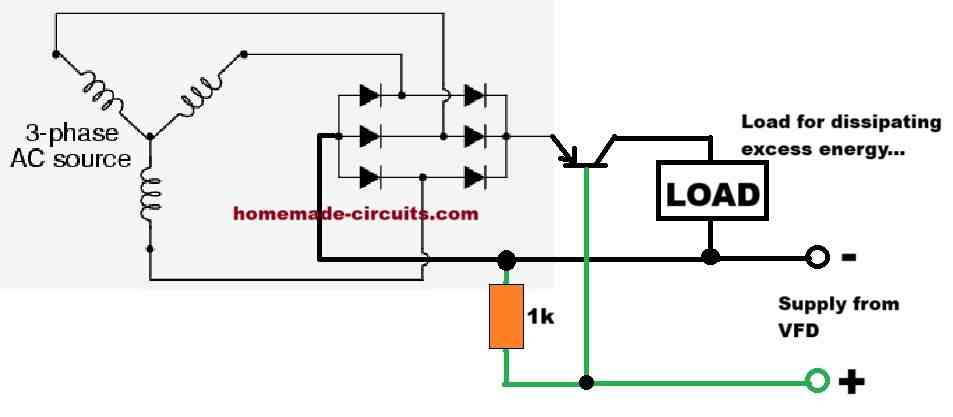
Sir, Namaskar.
I am technician
I won’t full circuit diagram of DBU
(DYNAMIC BRAKING UNIT ) & DBR for three phase motor.
My email : jvpateljv@gmail.com
Thank you.
Hi Jitu,
Can you please provide more details on how dynamic braking is supposed to work, about its working concept?
I will try to figure it out…
Dear Sir
IC IRS2330 is not available in Sri Lanka. Is it available in India. Otherwise manufacturers sells it in large quantities only.
Grateful for your help and guidance.
Regards
Pradeep
Thank you Pradeep,
The IC is available in India, or you can also try getting it from popular online stores like amazon or Ebay.
Dear Sir, what is the recommended IGBT for 110VX3 phase motor? Can we use IXSK 80N60B for this? Grateful for your advice.
Hello Pradeep, can you please provide the power rating (wattage) of the motor, I will try to figure it out…
Could you provide me a complete (composite) and clear diagram for the circuit.
The full diagram can be too large to fit on the screen, therefore I have shown the stages separately.
Do you have the circuit board & components for this as DIY project?
Sorry, PCB is not available for this project.
Hi Sir,
My circuit is almost completed earlier but due to my father’s cervical spine surgery I unable to take field trial bcz without his help and guidance it is risky (it is High voltage and high current power supply).
Now he is comfortable to do this.We will be planned it in this week.
after taking the same testing I will be shared all details to you.
I have required a information before it about heat sink. If I connected 5HP 3 phase submersible motor to the circuit load which heat sink I should be required?
Thank you Sanika, for updating the information!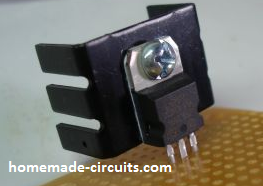
Glad to know your father has recovered from the illness and is doing good.
Regarding the heatsink, it can be difficult to assume how large the heatsink should be. It can be verified only though some practical testing. Initially you can use a medium sized finned type heatsink and check whether it gets too hot or not. If it gets too hot you may have to increase the size and so on.
" rel="ugc">
Hi sir,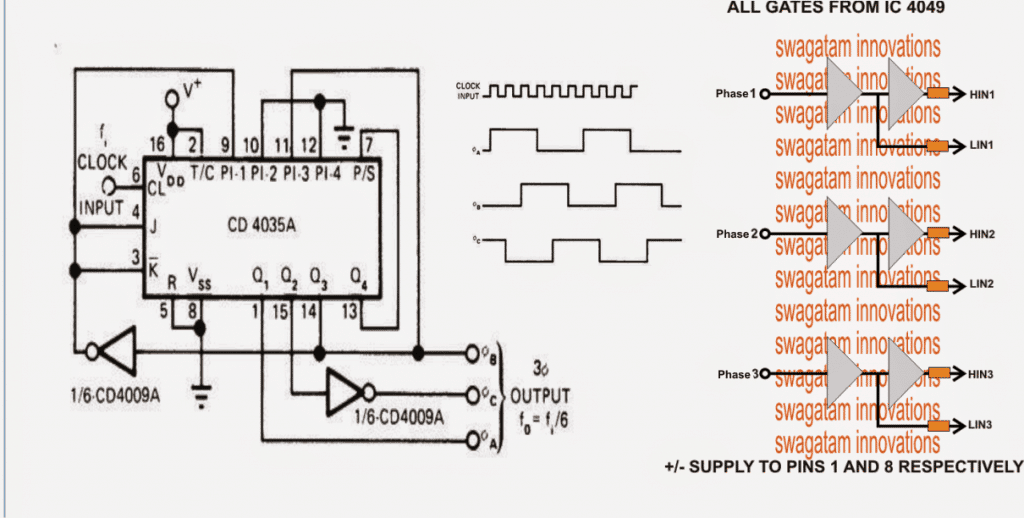
Getting the oscilloscope will take some time (2-3 days) so I decided to work on the above project . I have first built CD4035, CD4009 and CD4049 circuit so can you guide me in detail how should I check it?
" rel="ugc">
Without clock input (Pin 6) is it possible to check it?
CD4009 IC Pin1 VCC, Pin16 VDD, both have to be connect +12vdc And if only Pin16 have to required +12v then what is about Pin1?
Pin8 connected to GND (-) and Pin 7,9,11&14 also connected to GND. Pin 6,10,12&15 kept free.
Pin3 used for input from CD4035 pin14.
Pin2 used for output and connected to to CD4035 Pin 3
Pin 5 used input from CD4035 pin 15
Pin4 used for out put to the input of CD4049 pin 7
CD4035 Pin 1 connected to Input of CD4049 pin3
CD4035 Pin14 and CD4009 pin2 connected to CD4049 input Pin 5.
Sorry to bother you.
Thanking you
Hi Sanika,
For this project also you will need an oscilloscope.
The IC 4009 VDD and VCC is a bit confusing. According to the datasheet, it says “CONNECT VCC TO DTL OR TTL SUPPLY, CONNECT VDD TO COS/MOS SUPPLY”
I think 4009 can be also replaced with a 4049 IC which also has NOT gates. So you can use two 4049 ICs. Use 6 gates from one 4049 IC to connect with the HIN and LIN inputs of the 3 phase inverter IC, and use only two gates from the other 4049 IC to connect with the 4035 IC.
You can use any two gates from the 4049 IC to work with the 4035 IC. For the remaining 4 gates make sure to connect their inputs with the ground line, outputs can be kept open or unconnected.
Hi Sir, Good morning.
I made a oscilloscope with Raspberry Pi Pico (Scoppy Android App) it’s work good. plz check wave image of CD4035 and CD4049 output. I used CD4049 instead of CD4009 means 02 nos CD4049 as per your suggestion.
I check each output signal wave
https://drive.google.com/file/d/1DGsYktKpBYdQn1zGGlL9u3ZurAnJWk1e/view?usp=drivesdk
Plz check and suggest what can i do next?
Can i built inverting circuit with IR2130 IC which is similar to IRS2330?
Thanking you
Good Morning Sanika,
That looks good and a correct waveform from the respective ICs. However it is also important to check the 120 degree shifts from the 3 phase outputs of the CD4035 IC. How will you check and confirm that?
Yes IR2130 IC will also work fine.
Hi Sir,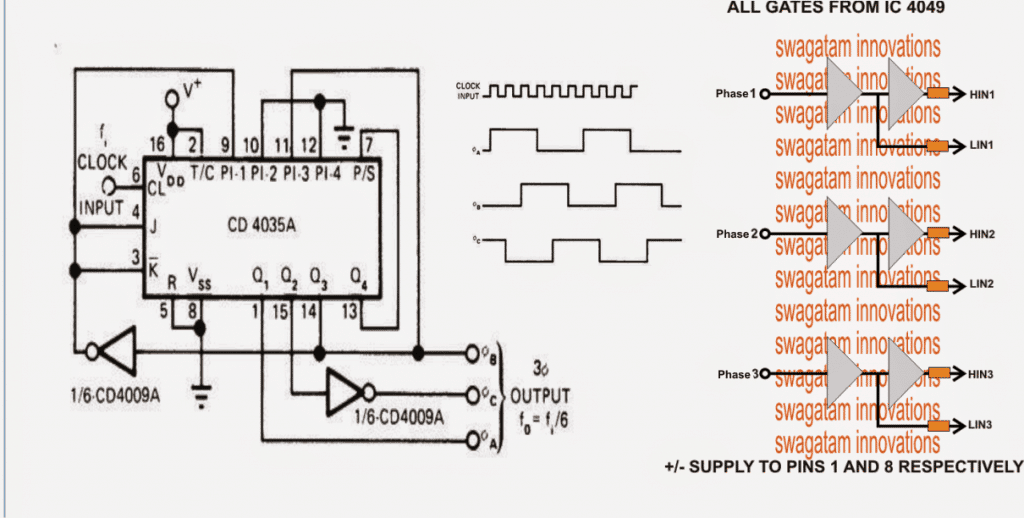
Plz advice about resistors at output HIN 123 and LIN 123 after CD4049.
I used 1k 1/4 watt.
" rel="ugc">
Thanking you
Hi Sanika,
Actually resistors are not required at HIN, LIN inputs since they are all high impedance inputs, but if you have used 1K resistors there’s no problem, it’s fine.
Hi Sir,
Sorry since there was a wedding ceremony at home so I could not do any work for so long. Now I have started working again. I have built and tested this circuit but all the igbt base is getting supply just not HO2. Frequency is available in all bases except HO2 pin 24. Also in IR2130 this HO2 Pin 24 is not getting frequency and Igbt is getting hot. Please advise on this.
Hi Sanika,
Did you supply the 3 phase signal to HIN and the LIN pins correctly? You must check the 3 phase signals with an oscilloscope and they must be 120 degrees phase apart. Also the Vcc pin of the IC must get 12V, I hoe you have connected that.
Hi Sir
It’s my mistake.
I checked all circuit thoroughly and I found Pin No.23 solder issue.i was corrected it and above mentioned problem was solved.
I got below frequency wave form them plz check.
From HO1
https://drive.google.com/file/d/11NLExlFRmGWJcND1rM3wQiTeku1aOhYr/view?usp=drivesdk
From Ho2
https://drive.google.com/file/d/11Ue3_WCV4NWN8Zm1y_XbPbEam19mL2Sf/view?usp=drivesdk
From Ho3
https://drive.google.com/file/d/11Pgn3f4OSt_w6thLiFPfLOlEh2CBnm-n/view?usp=drivesdk
IGBT not getting hot
Sorry.
Hi Sanika, But are these waveform 120 degrees apart, that’s the thing we want to check….all the 3 phase signal must be shown together on the oscilloscope.
Please see how the waveform is shown in the following article:
https://www.homemade-circuits.com/3-phase-signal-generator-using/
Sir
If it is ok plz suggest which is next stage?
Sanika, The 3 phase inverter needs a 3 phase signal, did you check the 3 phase 120 degree phase shift for the 3 phase generator output?
Hi Sir,
Yesterday it was checked at our technical institute with the oscilloscope. It is generated 3 Phase signal 0,120 and 240 degree but I couldn’t able to click pic.
I checked HIN ,and LIN output of CD4049.
Hi Sanika,
If you are able to get the 3 phase square wave waveform across the outputs of the 4049 NOT gates then the basic IRS2330 inverter circuit should work, because the IRS2330 circuit was referred from the datasheet of the IC.
Alternatively you can also try the following concept if possible, it looks much easier:
" rel="ugc">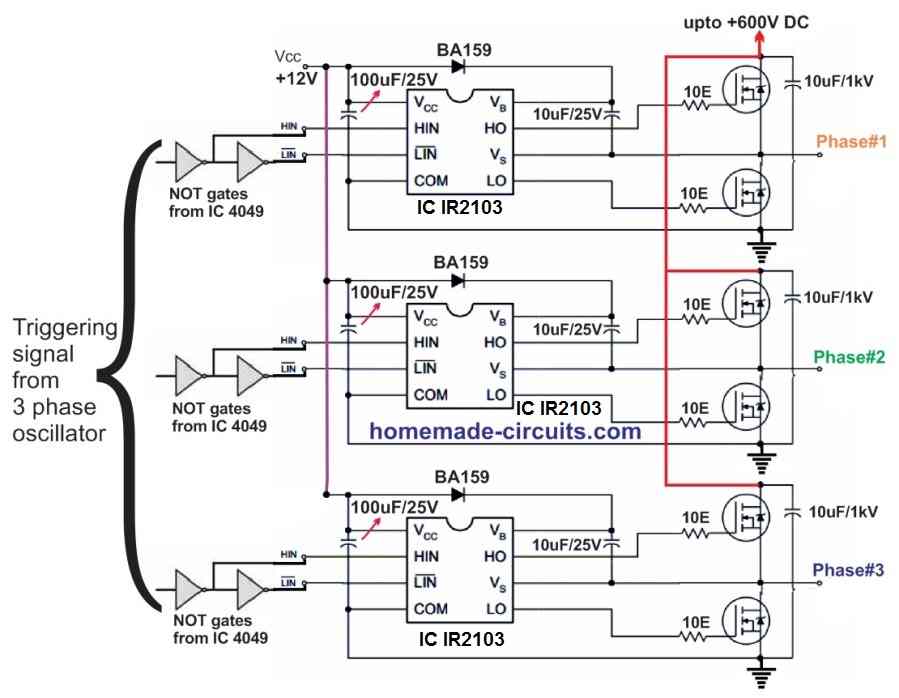
Sir
I am using IR2130 and 25N120 IGBT .it’s all ckt done and tested all IGBT output same (Input 12vdc and output 12 vac)
For clock input used frequency generator which earlier I made for test the my old oscilloscope.
I tested it upto 48vdc and output also get same.
Plz suggest what will be next stage?
Thanks
Sanika,
Is your 3 phase inverter circuit working OK? Are you getting 48V 3 phase output? Please confirm this first.
Hi Sir,
Yes my 3 Phase inverter ckt working.
When I input 24vdc to IGBT I got 24 vac at all 3 output
Then I input 48vdc that time I got 48vac at all 3 output.
Sanika, That is very good, however you must confirm the 3 phase output with a load. After that we can proceed to the IC 555 speed control stage.
Hi Sir,
That means I have to connect it with 3 Phase motor and input dc voltage.
How much dc voltage I should be input? Which filter capacitor (e.g. 150uf/450v , 330uf/450v or 220uf/450v) I have to connect in dc bus to filter?
I will be generate dc voltage from single phase 220v with KBPC3510 Bridge rectifier.
Is it possible? Plz advice about it.
Hi Sanika,
First test with 3nos 24V or 12V bulbs using the same DC input as the bulb rating.
If it works then only you can try 310 V DC from 220 V AC as the bus voltage and a 3 phase motor, for the actual testing.
For the filter capacitor I think 220uF/450V or 330uF/450V will be quite enough.
Good morning Sir,
I currently use the following ckt to test the circuit. Because I was not satisfied with the IC555 circuit I made earlier, its square wave was not satisfactory and after setting the CLOCK input of CD4035 to 220-230 Hz frequency, it was getting 50Hz after CD4049, like Fluctuations were happening, so I prepared it with the reference of your second article and the result was very good
" rel="ugc">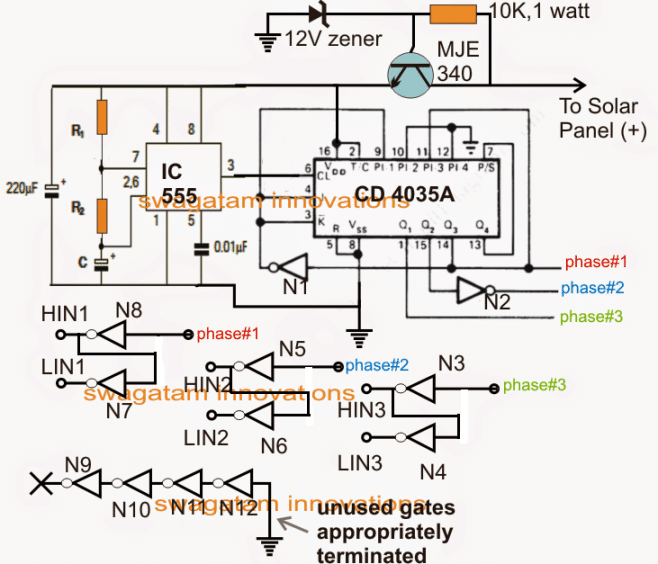
Now there is no fluctuation and the waveform is also very smooth.
After setting 300Hz frequency, finally exactly 50Hz, 50% duty cycle and 20ms time period are obtained.
I used C- 0.1uf
R1- 10k potentiometer
R2- 100k potentiometer so it was easy for me to set.
Thank you very much indeed. I am continuously learning a lot from you and thank you again for explaining in difficult times.
Good Morning Sanika,
I am always glad to help, and I am also glad your 3 phase signal generator is working perfectly for you.
All the best to you.
Feel free to ask if you have any further questions.
Hi Sir,
Tested 12vdc with 3 lamp on each phase. Plz check the attached pic.
https://drive.google.com/file/d/12iCguc41pjvaPigaI585zBuYmjquIO63/view?usp=drivesdk
Voltage is dropping around 1v to 1.5 volt in each phase ( input 12vdc output in each phase around 11.5,11 or 10.5)
Thanks Sanika,
that looks great, But still we are not sure how the inverter will respond to 300V or 400V DC with a 3 phase motor. Only time will tell. 1V voltage drop is OK since the bulbs are high amp bulbs.
If you want, we can proceed to the 555 speed controller stage next..
Hi sir
It’s all lights are 2 watts .
Another thing first we will check it on 300vdc if it’s run its ok if not then we will try for next step …
It is not compulsory to run it on decided voltage , it’s our project for us
OK great, no problem, let’s see how it goes.
Yes sir we will get accepted results when will try for it positively
You are right Sanika, all the best to you!
Sir
That’s why I regularly posted comments and results with photos for reference of other like me .
Failure is the first step of success this is my concept. If we fail that means we can’t do it?
Forget it Sir
Can I start to built IC555 ckt?
You are very much right Sanika, I appreciate your understanding.
Yes you can surely start building the 555 circuit exactly as shown. If the 1K pot does not give proper results we can use a 4.7K pot or a 10K pot for the output PWM adjustment at pin#3 of IC2
Hi sir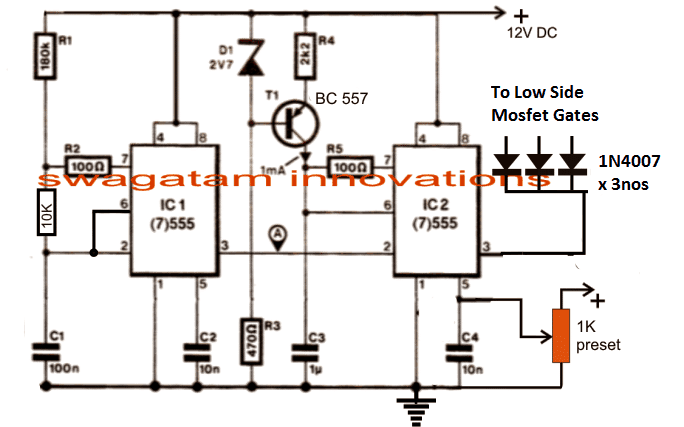
Is it possible to use 3v3 ZD bcz 2v7 is not available at my end.
" rel="ugc">
Sanika,
Yes 3.3V zener will also work, no issues.
Hi Sir,
I built the IC 555 ckt with 1k pot and tested separately so plz check attached video ( increasing and decreasing pot)
https://drive.google.com/file/d/13ELmUbayV5csKZQfpsHfXDq79oyCCoM5/view?usp=drivesdk
Please let me suggest Is it ok or any changes will be required?
Hi Sanika,
That looks perfect to me. So your 555 PWM controller is also working perfectly. Now you can integrate this PWM with the gates of the low side IGBTs.
When you alter the 555 PWM, the output voltage from the IGBTs must also change proportionately from minimum to maximum.
Hi Sir
Good morning
I built V to F convertor and tachometer circuit also.
I want to make confirm about integration of those ckt.
1.pwm input of LED/LDR from PWM IC 555 no.2 pin no.3 to LED positive and GND to negetive.
2.plz let me guide about Rotor Speed Frequency connection of Tachometer at base T1.
Good Morning, Sanika,
Actually I am not sure about the V to F converter and the tachometer circuits, I am not sure whether they will give proper results or not. I am only sure about the first three circuits.
So it can be difficult for me to suggest about the V to F converter and the tachometer concepts.
I won’t recommend you to build the V to F and the tachometer circuits.
These are complex concepts, difficult to implement and have greater chance of a failure.
Ok sir,
I will integrate IC 555 with LOW side IGBT.
1. Is it required frequency generator which is I attached before CD4035 for clock input (300Hz)
2.which Diode should be used at (D1…D6 ) H-Bridge Driver Circuit across the IGBT.
3.For DC bus filter which capacitor and discharge resistor I have use bcz I want to test the circuit with 3HP 3 phase induction motor 415v.
After confirmation of above points I will be planned for final testing.
No problem Sanika,
1) The 555 frequency generator which you have connected to feed the clock pulses to the IC 4035 pin#6 is required, otherwise the 3 phase inverter cannot be supplied with the 3 phase signals. So it is required.
2) You can use 1N5408 for the D1—D6 diodes.
3) Any capacitor with a value higher than 220uF/400V can be used as the filter capacitor across the BUS line.
Ok Sir ,Thanks
Now I don’t have 1N5408 Diode available. Can I use 1N4007 Diode in parallel 3 together until it is available?
Sanika, I don’t think parallel 1N4007 diodes will work, but for the time being you can try it. Most probably single 1N4007 diodes can be also tried for the time being if the load is a low current type load. For heavier 3 phase loads 1N5408 diode or 6A4 diodes will be required.
Hi Sir,
For time being I tried 1N4007 diode, after getting above mentioned diode I should replaced it.
Today I completed my ckt building with IC 555 PWM integration and conducted a trial with 24-25 VDC.
I noted below results
1). Output voltage at each load end 26.9 AC constant voltage no any fluctuations found.
2). AT the gate of HO 1/2/3 getting 17VDC and the gate of LO 1/2/3 getting upto 6.0 VDC.
3). I tested with oscilloscope LO 1/2/3, HO 1/2/3 and LOAD 1/2/3 output as well as Frequency Generator to the CD4035 clock input.
Plz check attached video and advice any changes will be required.
https://drive.google.com/file/d/13X5jvZj6vHsYNkxgedFWDBZXixZSkyOk/view?usp=drivesdk
Hi Sanika,
When you decrease the 555 PWM duty cycle to minimum then the output voltage should also decrease proportionally. At minimum PWM, the low side IGBTs would be also conducting with minimal switching which should cause the output voltage to minimize. Conversely when you increase the PWM duty cycle the output voltage from the IGBTs must increase proportionately, because at higher PWM duty cycle the low side IGBT would conduct more and more causing an increase in the output voltage.
From where have you taken the waveform image, is it from the IGBT output across the load?
Yes Sir
PWM duty cycle increasing and decreasing but for setting it have very little margin can I replace with 10k preset.
Now voltage is equal to input DC voltage i.e. 24 VDC input and output 24 VAC ( adjustment done by 1k preset at IC555 PWM)
And plz find attached waveform video of IGBT output across the load.
https://drive.google.com/file/d/141j5nBKiR9McabH_zU_gumgOhvwhpnyK/view?usp=drivesdk
Sanika, that is strange, if the low side IGBT gate switching is altered with a PWM then the output voltage should also vary accordingly. Try with a 10K pot, then fix the pot at the narrowest (minimum) PWM on the low side IGBT gate and then check the output voltage and also check the response on the bulb illumination.
Hi Sir
I made the change as told. Also, when checked, the no-load voltage can be increased and there is no increase or decrease when the load is given. E.g. Given a voltage of 12DC it goes to 17-18 AC without the bulb but at the same time if the bulb is added to the load the same voltage comes to 11-12 AC.
During attached load no any increasing and decreasing happened while rotating 10k preset.
Hi Sanika,
It is difficult to understand why the low side IGBT PWM control is not regulating the speed, that should not happen. Try to set the narrowest possible PWM at pin#3 of IC2 555 and check the PWM across gate/ground of each LOW-SIDE IGBTS. If the low side IGBT switches as per the narrowest PWM then its average conduction should decrease causing the output voltage also to decrease proportionately.
If somehow this does not work out then we will have to try the PWM from the IC 555 circuit which is connected with the IC 4035: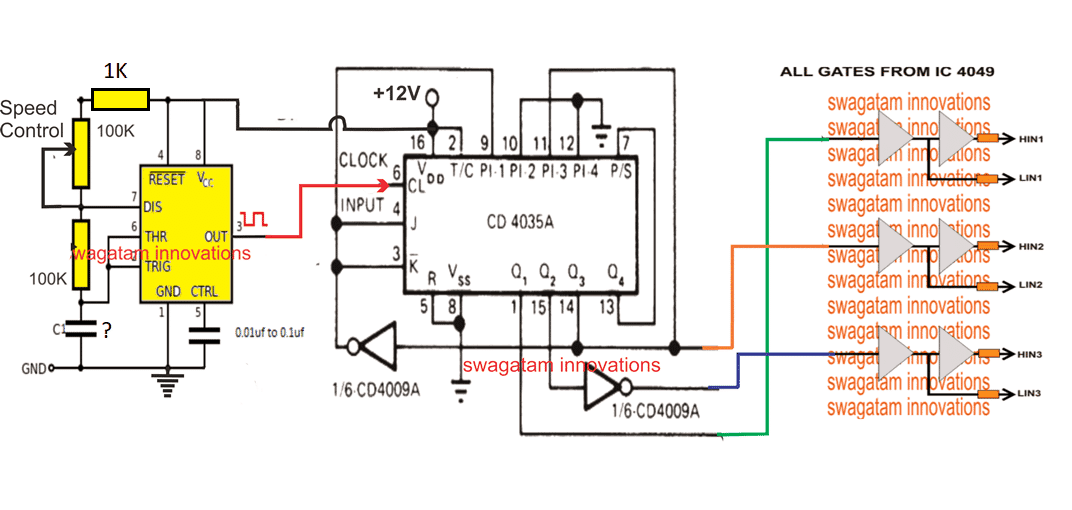
" rel="ugc">
Hi Sir
I checked both the ICs in the PWM circuit and found one of them faulty. So we were not getting the desired result. I don’t have it available now, I will get it tomorrow after further inspection and will be forward all the results.
Until then I am making a circuit for my house water tank and borewell motor to automatically turn on and off and show the water level.
" rel="ugc">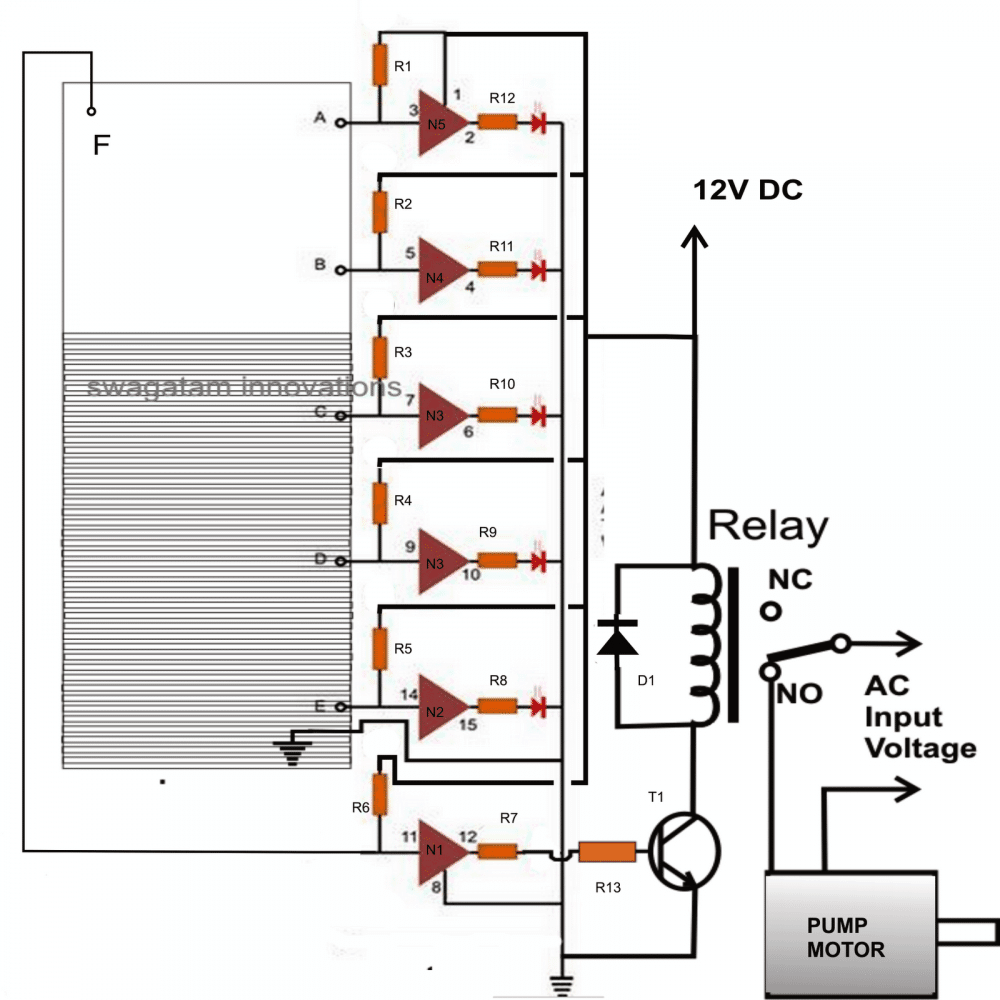
Hi Sanika,
But, the varying waveform that you showed for the 555 PWM circuit looked good to me.
Anyway if yo think there’s some issue with this circuit you can rectify it.
You can use the water level controller circuit.
In the water level controller the relay will OFF the motor as soon the water touches the point “F” and the relay will switch ON the motor back as soon as the water level drops below the point “F”.
Hi Sir
Sorry for delayed response.
Pappa was checked it and he told me about IC555 after that I also did it once again and I found it faulty.
https://drive.google.com/file/d/15zu8pEYrD64JA-aZCNAlov4lWdTwlIed/view?usp=drivesdk
No problem Sanika,
Thanks for sharing the video. It is very nice. You guys are real engineers.
Please let me know if you have any further questions, I will try to help.
Hi Sir
Plz check attached video for wave form of IC555(2) output pin 3.
Voltage is increasing and decreasing while rotating the 10k variable resistor.
https://drive.google.com/file/d/160JtM7Xa7u7SuO5kA1WyyRWYZwrlfOje/view?usp=drivesdk
Now plz suggest for next stage.
Hi Sanika,
Now you will have integrate the PWM output with the low side gates of the IGBTs, just as you did before. As you can see the 555 PWM can be varied from low to high and high to low, this means when the PWM duty cycle is low the IGBT will conduct less and produce proportionately lower output voltage, an when the PWM is higher the IGBT will conduct more causing the output voltage to increase proportionately. In this way the VFD voltage can be varied by adjusting the PWM.
Hi Sir
I don it, just as earlier.
I have a confusion about 1k pot connection which is connected to +12VDC at below diagram
" rel="ugc">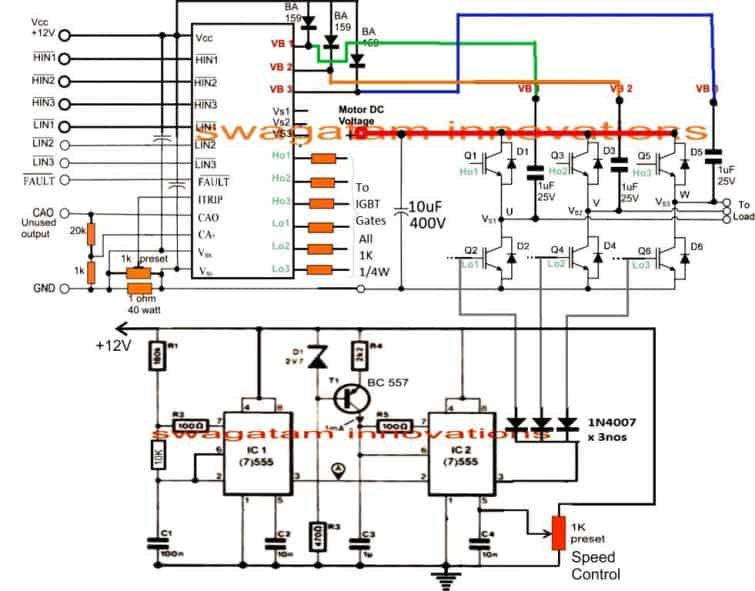
And another circuit diagram showing it will be connected with AC ripple from 3 phase bridge
" rel="ugc">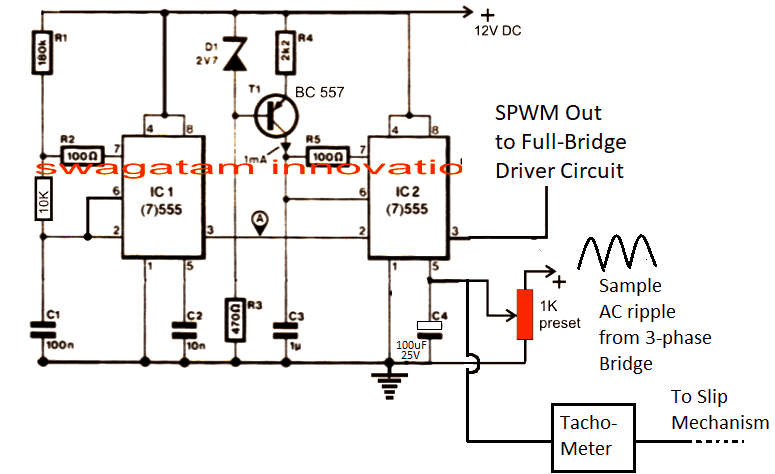
Now I connected it with +12VDC
And plz check attached screenshot for DC Bus which I will be going to use my this project.plz suggest if any changes should be required.
https://drive.google.com/file/d/16I3bciz3KxAXmlGqV0qHBC4C1CBZyI3s/view?usp=drivesdk
Hi Sanika,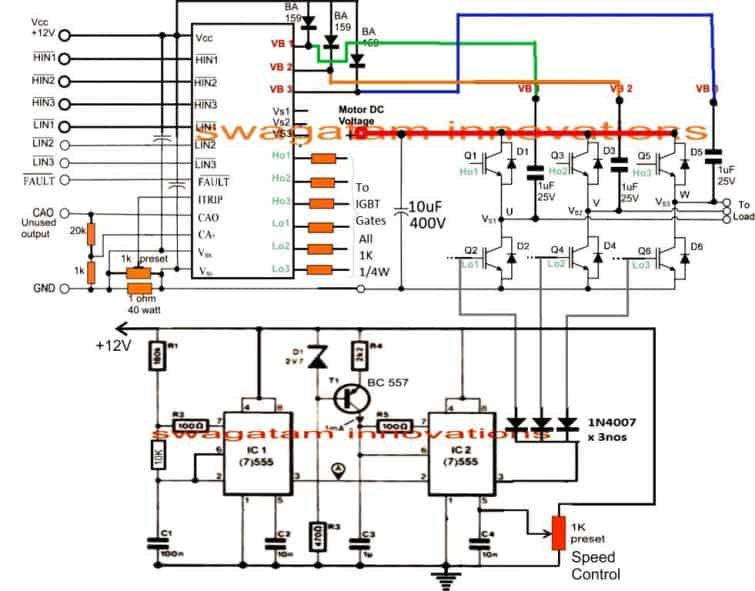
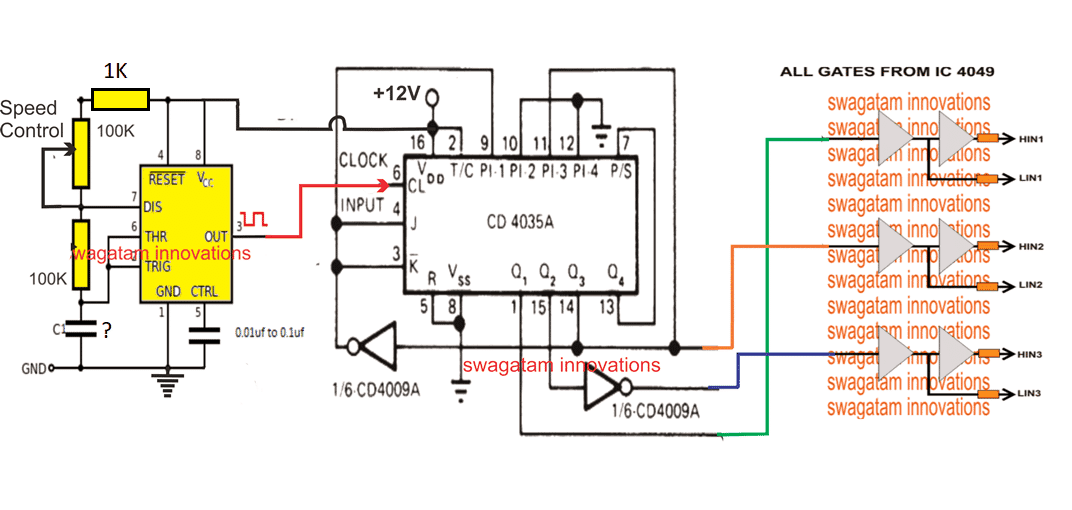
You will have to do according to the following circuit, please ignore the ripple circuit:
" rel="ugc">
There’s another interesting way to vary the output of the IGBT.
You can do it by varying the PWM on pin6 of IC4035, meaning by varying the PWM output of the 555 IC in the following circuit:
" rel="ugc">
Your DC bus circuit is OK, but please add a 100 watt in series initially so that if anything is wrong then the IGBTs will not burn. If the IGBTs are working fine then the 100 watt bulb must remain switch OFF, if it’s glowing brightly that means something’s wrong.
Hi sir,
I am working on this kind of project with the reference of your valuable articles, and I got a lot of information from it.
I want to assemble the above project and hope you will be support for it.
1. I have a DC power supply of 550 to 600vdc 50amp (Sorry this is very dangerous but I am taking care and will continue to take care of it.)but I can’t understand how to attach filter means which capacitor and inductor attached with the same power supply for 25 amp .plz suggest
2. Can I use IRS2110 (03 nos) instead of IRS2330 ( it is not available)
3. Can I use IGBT FGA25N120 = 12 pc (2 parallel at Hi side and 2 parallel at low side) in with IRS2110 Driver IC? If yes then which resistor should be used with IGBT gate?
4. Diode BA159 also not available so can I use FR607 (FAST RECOVERY DIODE) instead of BA159?
First I will make PWM VOLTAGE CONTROLLER and should be check it’s output after that I will move on next stage (i.e.03 Phase Signal Generator, then driver circuit)
Before that I want to clear all daubt which is faced during understanding the whole circuit project.
Sir please I am waiting for your suggestions and guidance.
Thanking you
Regards
Avdhoot
Hi Avdhoot,
I appreciate your interest in this project, and I wish you are able to complete it.
However, please note that the above circuit was designed by me with my own understanding about the concept, I have not yet tested the circuit practically.
So the problem is, if you happen to get stuck somewhere while building the project then I will not be able to solve it for you because that would need a practical checking of your circuit.
For the questions you have asked, here are the answers:
1) I would strictly recommened not to use a high current power supply initially, instead use a 310V DC created by attaching two transformers back to back and then rectifying/filtering the AC. Only a 100uF/500V capacitor would be enough for the filtration.
2) Yes, 3 nos of IRS2110 will also work.
3) You can use FGA25N120, but not 12 pcs, rather only 6 pcs, use single devices only, not in parallel. If your circuit works perfectly then you can go for parallel connections, but for the initial basic setup use only single IGBTs.
4) FR107 should also work according to me.
Yes, you must go step wise. Build the 3 phase generator first.
Then make the 555 PWM generator and finally build the 3 phase inverter circuit.
Test and confirm them separately, if all work perfectly, then go for the integration.
Thank you sir for your quick response.
Ok sir I can do as per your instructions.
1.This means I only need to use a 310vdc power supply.
2.How many ohm and watts resistor (1ohm,10ohm,100ohm) should be connected to IGBT gate.
Thanking you.
Regards
Avdhoot
Sure, no problem!
Yes, test the circuit with 310V DC acquired from two small back to back connected transformers:
You can add 100 ohm resistors to the IGBT gates.
" rel="ugc">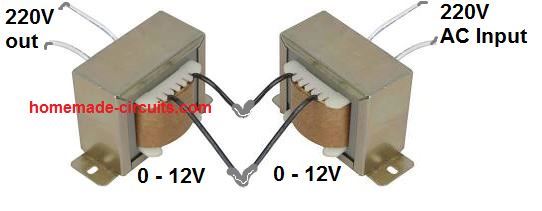
Sir can it possible to use 3.3v zener 1/2 watt or 1 watt instead of 2v7 zener diode.
Hi Avdhoot, yes 3.3V zener will also work instead of 2.7 V zener
Hi sir
I I have received CD4033 instead of CD4035 from online shop. I ordered CD4035 but dispatched CD4033 I Contacted but the same is not available.
Other all components received to me so plz advice me what can I do for the same? It is possible to use it instead of CD4035?
Thanking you
Hi Avdhoot, IC 4035 and IC 4033 are two completely different ICs with different pinouts and functions, so they cannot be interchanged with each other.
Hi Sir,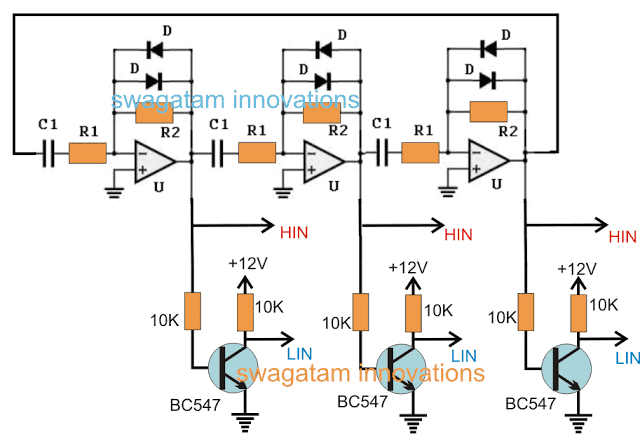
Can I use this circuit design instead of CD4035 circuit
" rel="ugc">
Plz suggest
It is already I made earlier and tested seperately.
Thanks and regards
Avdhoot
Hi Avdhoot, that circuit is good but I haven’t tested it using an oscilloscope. If you have confirmed its 3 phase signal output using an oscilloscope, then definitely you can use it instead of the 4035 circuit.
Dear Sir,
Good Morning
I got CD4035 and i started to built ckt. Almost CD4035, CD4009 and CD4049 section is competed. Plz let me guide about CD4009 VDD pin connection. Is it connect to GND? And what is about remained pin of the same? Is it kept free or connected to GND also?
How to check 3 phase generator ckt?
Regards
Avdhoot
Good Morning Avdhoot,
according to the datasheet, the pin16 of 4009 is VDD (+) and pin8 is VSS (-). The inputs of the unused gates are connected to ground, and the outputs are kept open.
Good morning Sir,
Just I gave 12VDC supply to ckt and checked output of HIN and LIN at CD4049 section. It is as mention below.
HIN 1# 12V
LIN 1# 0 V
HIN 2# 12V
LIN 2# 0V
HIN 3# 0V
LIN 3# 12V
Hi Avdhoot,
Before connecting you must check the 3 phase waveform from the 4035 IC using an oscilloscope. If you are getting 120 degrees apart 3 phase signal waves only then you can proceed to connect it with the 3 phase inverter IC.
Hello Sir,
Please guide me for below points
1) A homemade V to F converter LED Anode (1k Resistor) and Cathode point where to connect ?
" rel="ugc">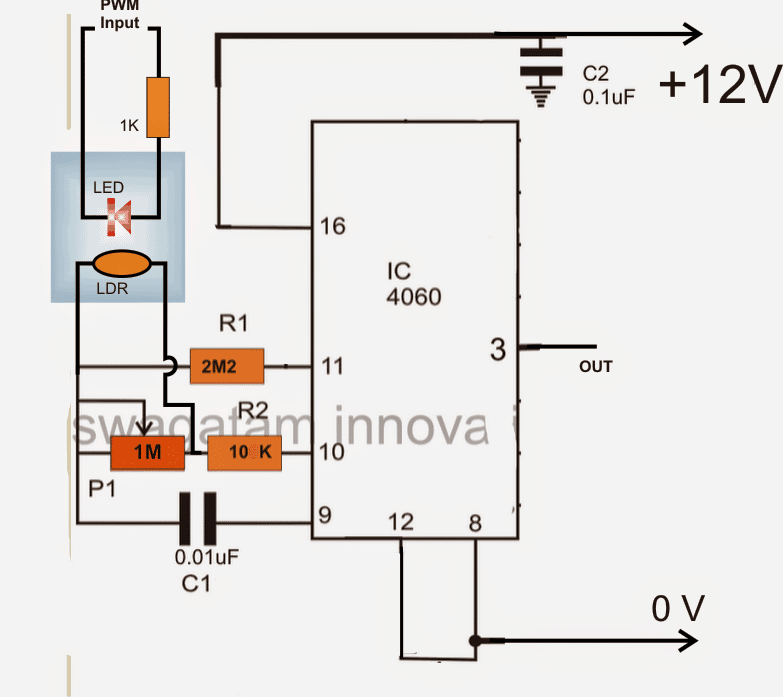
2) What is about Rotor Speed Frequency (Base point of T1 BC547) which point required to be connect?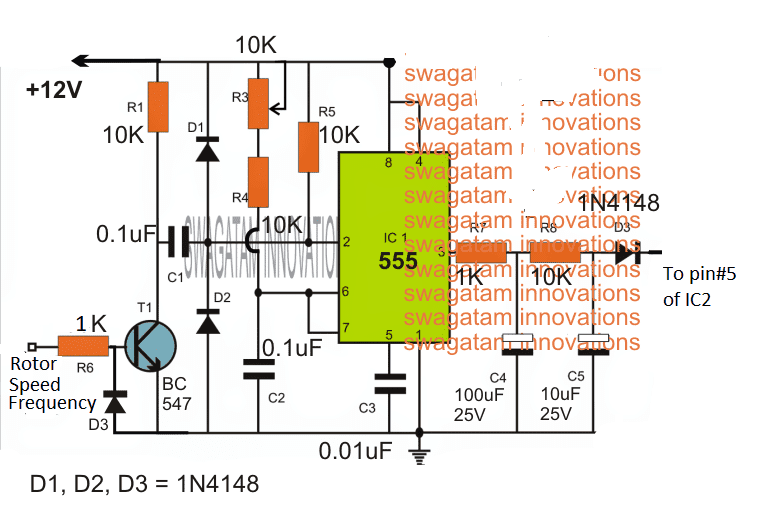
" rel="ugc">
I am little bit confused so…
Regards
Avdhoot
Hello Avdhoot,
Did you try the first two schematics? I can only recommend the first concepts as I have more confidence on them. The remaining concepts are based on my assumptions only, so I cannot recommend them.
Hi, advhoot
I also using ir2110, i use 10ohm series with the igbt gate. Add around 1k between gate to drain to save u some $$ from burned igbt.
Thanks
I have a IR2130 for the same use. What is about 1 ohm 40 watt resistor? It is not available at my location.
Ir2130 is quite similar to 3x ir2110 i use, it has 3ch independent half bride. Except it has dead time adjustment, overvoltage protection and work with 2.5v logic. I just build fan78932, which is similar to ir2136 as it only take single pwm input and output 3 pwm shifted at 120° each. It has overcurrent protection too. You could parallel/series 5watt resistor which i think you could find. 10x 0.1r in series or 10x 10ohm parallel 5 watt resistor equal to 1ohm 50watt. Download any electronic calc app, you ll find it handy. Btw, if you didn’t know how to parallel/series resistor i think you should stay away from main voltage, or try your circuit with step down transformer first. I, just like many electronics hobbyist, start from class ab amplifier to learn the basic. Be careful with what you are doing.
Oh, if you do experiment with lower voltage like from 24-32v transformer, you could scale down your parts. Like using fan motor(connect one to any phase mosfet output and your psu ground), 50v capacitor, 5 watt resistor onstead of 40watt, and cheaper mosfet. Resistor did not to be at exact value, just get as close you could find. For mosfet you could use irf540, xxnyy series(xx is ampere, yy is voltage/10; 30n60 is 30amp/600v max) in to-220 pack which is around 20% the price of an igbt. You only need min of 10amp and 200v max rating. A set of 30n60 mosfet do not even need heatsink for just 1-3min testing.
first of all i have to say something that i am new to this project but i have to make it because it is important to me, i am still stuck on the IGBTs family number that what type of number have to select i requested to all who are on this project. if anyone interested join me on WhatsApp 00923052300002
Hello sir can I use drv8305 ic from Texas instruments as the gate driver
Vinmu, DRV8305 is a full fledged 3 phase motor driver IC….and it can used to drive 3 phase motors.
You can refer to the datasheet of the IC for all the details:
https://www.ti.com/lit/ds/symlink/drv8305.pdf?ts=1680508971625&ref_url=https%253A%252F%252Fwww.ti.com%252Fproduct%252FDRV8305
Hello,
apparently you used all N-type power transistors for the high and the low side of the bridge. What I learned was to use preferably P-type on the high side?
Hi, preferably it should be always N-type mosfets for all the transistors in an H Bridge circuit sine N channel mosfets have minimum resistance and highest efficiency. However, configuring an H-bridge using N channel mosfets cn be complex, compared to using P channel on the high side….but using P channel on the high side can be inefficient due to its relatively higher resistance spec.
Hi I have understand the way of conversion and the inversion of the VFD, But the logic used to switch the IGBT can you explain in detail for a clear understanding.
The gates of the IGBTs are switched by the HO1,2,3 and LO1,2,3 outputs of the IRS2330 IC. The IC uses bootstrapping technology to switch the high side IGBTs using the BA159 diodes and the 1uF capacitors. Let me know if you have any further questions.
Hello and thank you for this nice tutorial ! I am glad I found it. I still have some questions though. Is this type of circuit good to use in a cnc spindle type bldc motor where I want to mill materials or do I need another type of circuit ? I have seen there are so many control algorythems for VFD motor drives. Your tachometer is just for speed control or will it also limit the current(torque) If I load the motor via milling ? It´s a sensorless type bldc motor by the way rated for 1,5Kw/325V/400Hz = 24000RPM you may know them. The last thing I wish is tripping the overcurrent protection everytime I try to mill something.
Thank you for your answer
Thank you for your question and feedback. Actually this circuit was designed by me and I assume that if all the mentioned aspects are correctly built and optimized then it would give the intended results. The tachometer will adjust the speed depending on the load current according to my understanding.
Yes an over current trip is already provided. You can see it in the first diagram, configured with the top IC, across its ITRIP pin.
Actually I have given only a general description, I am not very sure how this would suit a specific application.
Thanks for your fast answer. Yes I can see it and according to my calculation based on 0,5V reference voltage inside the IC I have choosen a 0,1ohm resistor because motor will pull 1500W/230V=6,5A and ITRIP= 0,5V/6,5A = 0,08Ohm next value is 0,1Ohm so it should not burn at least. My IC is labeled IR2136 but it looks very similar to yours in the datasheet so it should work fine.
Yes, your calculations seem to be perfect, and the configuration should work with your IR2136 also!
Hi, I’m finishing the project but I have two questions. First using the Closed Loop Feedback, pin#3 of IC2 (555) must be connected to Low Side Mosfets and also to the Led used with the LDR in the IC4060 or Low Side Mosfets is not necessary?
The other thing is how to generate the 12V ripple to feed 1K preset. I had thought to use a transformer between one of the phases and neutral but the ripple would be single-phase and not three-phase (three times less), could this work? Thanks
Hi, you must build the project stage-wise and confirm the results stage wise. If you try to build the whole project at once it is never going to work.
First build the 4035 circuit and check whether it is producing the 3 phase signals or not, then build the 3 phase mosfet inverter and integrate with the 4035 circuit and check whether the inverter is generating the required 3 phase AC.
Once the above are confirmed then you must build the 555 pwm generator and proceed with its testing and integration with the inverter.
Once all the above are confirmed then you can think about the feedback connections.
Sir
Can you provide me 10kw single phase to 3 phase inverter full circuit diagram with components discription.
I have to use it for my farm 5hp 3phase submersible pump.
Plz
BR
Vijay
Pune
Hello Vijay,
You can try the second concept from the following article:
https://www.homemade-circuits.com/three-phase-inverter-circuit/
You can increase the MOSFET specifications to satisfy the 10kW need.
Thanks Sir,
it is very very helpful to me and you described very nicely. Let me ask 3 things :-
1.) Can I use LF411 ic shown in PWM (which is simple and easy )for suggested concept by you?
2.)Can i use IR2104 Driver IC instead of IRS2608D?
Once again very very thanks.
BR
Vijay
Hi Vijay,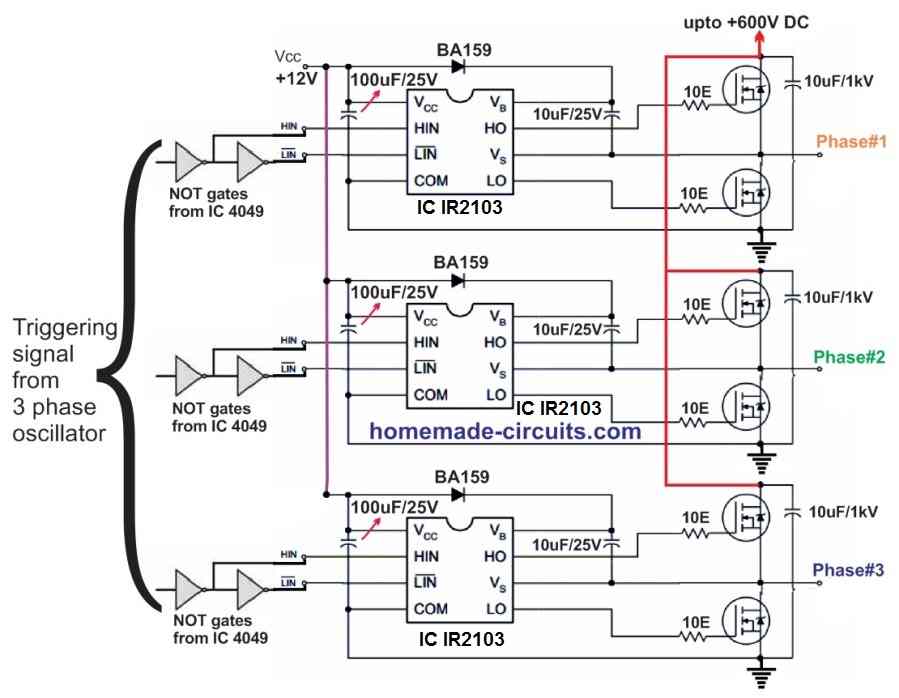
Yes you can use LF411 IC as the oscillator.
You can IR2104 IC in the following diagram:
" rel="ugc">
Good morning sir,
Thanks for very quickly response.
In Above circuit
Can I use 220 VAC input convert into 230VDC 10kW to run a 5 hp motor?
Thanks
Vijay
Good morning Vijay,
Do you mean, convert 220V DC to 220V AC? yes you can do that.
But I guess you would need a 440V Dc to get 220V AC.
Sir, I tell you my problem for which I am making this plan.
We have only eight hours of three phase power supply for agriculture daily and it is constantly interrupted and its supply schedule changes weekly (day and night). The remaining 16 hours are single phase (220V) supply. This makes it very difficult to irrigate the farm. So I wanted to make a device to drive a single phase to three phase motor to irrigate agriculture.I always visit your websites and I have learned a lot from it. After seeing your inverter project, I decided that by doing this project, we can solve our problem and avoid the loss of agriculture.
Thank you Vijay, Glad this website helped you to learn.
However i don’t think 220V AC or 310V DC can be used to generate 3 phase AC output, you might need 440V Dc instead.
Thanks Sir,
Sorry for distrub you again.
In this case which is the best way to achieved 440V Dc without transformer?
Plz suggest i read few articles in this website but I am little bit confusing.
Thanks
Regards
Vijay
Hi Vijay,
It can be done with a 220V to 440V transformer, but i am not sure whether that will work correctly or not.
When I checked online regarding “220V AC to 3 phase converter”, I got many results….that means it is possible to generate 3 phase from 220 V, but I am still not sure whether a 310V from 220V can work or do we need 440V
I think it is better to buy a ready made unit from the market instead of building one.
R/Sir,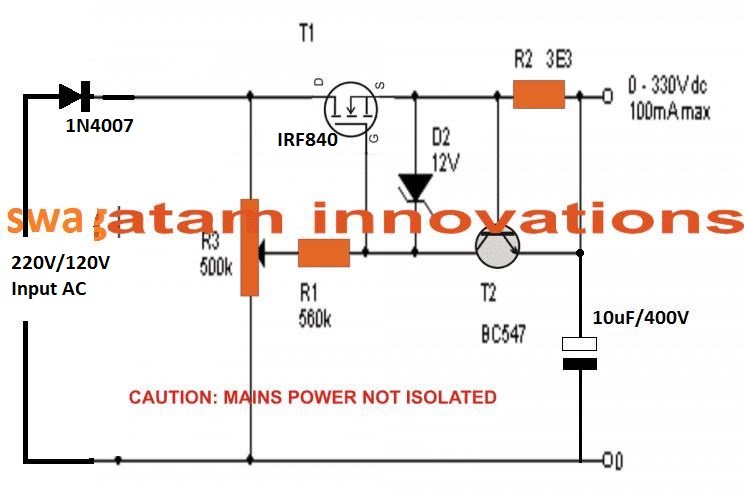
can it possible for 300-330vdc 50amp with suitable change.
" rel="ugc">
Vijay,
It may be possible, but you may have to put at least 10 MOSFETs in parallel.
Sir thanks for quick reply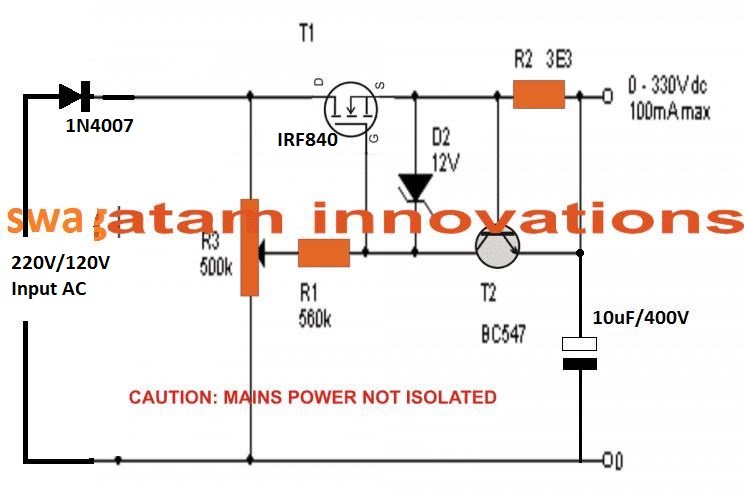
Sir as you suggested first i will make it first and check it after that I will plan for remaining project. can I keep BC547 as it is as mentioned in diagram?" rel="ugc">
No problem Vijay. All the best to you!
You can keep the BC547 section as it is which will help to provide a current controlled output.
R/sir,
good morning
I can get +400vdc (I attended few practicle projects for that) so please suggest me a circuit for 3 phase 5hp sumbercible motor inverter. Phase to phase voltage 315/380v.
Thanks again for this invaluable support .
Best Regards
Hi Vijay,
you can try the circuit from the following article, the one which is given below the heading USING IC IR2130
https://www.homemade-circuits.com/three-phase-inverter-circuit/
But before building the main circuit please confirm whether the following 3 phase generator is working correctly or not?
" rel="ugc">
I don’t want to question too much, but has this been tested and can it be used for any 3-Phase motor that’s within the power range that can be provided? This interests me because I’m an engineering student coming up with a senior project. I want to use a bike to generate power by spinning the rotor of an alternator and use that generated power to power a 3-Phase VFD to drive the motor.
The circuit modules have been tested separately for their individual functions, but the combined VFD circuit is not yet tested.
Is it possible to use the AUIRS2336s? because 2330 is not in my country. Also, is it better to use this circuit or this https://www.homemade-circuits.com/3-phase-induction-motor-speed/ for a squirrel cage motor as I asked earlier. Thank you and sorry for so many questions.
You can use any H-bridge, as long as the power devices are appropriately rated to handle the the load. Induction motors are also squirrel cage motors according to me, so you can use it…
Hello, is it possible to use this VFD to control a squirrel cage motor?. Thank you.
Yes it may be possible according to me…
I just found this website, and of course it has a tremendous amount of info. I am trying to build a engine cranking circuit using igbts, that will “motor” a 220 vac phase to phase, three phase, 100 kva, 120 hz at 900 rpm alternator. The diesel engine the alt is attached to will need a min cranking speed of 100 rpm, but i want to design for a max speed of 200 rpm which corresponds to approx 27 hz output, and approx 49 vac, based onvolts/hz ratio.
Hi, thanks, I will to figure it out if it is possible for me, and let you know soon!
Controlling V/Hz is important. I don’t see any type of motor current limit or setting the current to the motor. Have I overlooked something?
Current limit is provided in the second driver schematic at the bottom left, using 1k preset
I saw that current limit. It is on the DC side of the equation basically monitoring the KW of the motor and adjusting the trip point when the motor KW gets to high. What I am worried about is that a three phase induction motor needs not just KW but KVAR to get the motor running. This KVAR is usually supplied by the Large Capacitance in the DC link. There is really no horsepower generated at low speeds but to get the motor started, torque will have to be generated which is the KVAR. It is possible to overcurrent the motor without pulling excess current through the DC side current limit measuring resistor shown the diagram. It that type of motor current limit included in the design or am I still missing something?
The current sensor is on the negative line which is common to both the high voltage DC BUS and the 12V DC, so the filter capacitor across the H bridge would be getting the current through this limiting resistor which will ensure that they are never allowed to charge above the max current limit of the motor.
The negative of the H bridge DC BUS and the 12V Dc both should be connected to the point indicated as GND
Not necessarily. The reactive current is exchange between the motor and the DC link Capacitance. Where the current sensor is located is solely in the DC side of the power bridge outside of the capacitor motor interaction. If the motor was starting with high torque, before the motor starts to turn, the current of the motor, which is mostly KVAR, is exchanged between the motor and the DC Capacitance through the transistors and diodes in the H bridge and does not pass through the 1 ohm resistor current sensor. The current sensor is only sensing the losses of the H bridge and the motor, which would be very low. The diagram shows a constant voltage inverter, not a constant current inverter, so the Vdc stays relatively constant coupled with the low power losses of the system and the fact that the motor is not turning yet developing horsepower, the Idc that is being monitored is very low. Motor torque is developed with the reactive current which is high because the real power current is very low since the motor is starting with high torque. The vector sum of the two can create a KVA current that can exceed the rating of the motor.
This is what prompted the question.
I couldn’t figure out how the above inverter is a constant voltage inverter, according to me it is a constant current inverter, since it prevents the current from exceeding a specified limit. The limiting resistor must be calculated such that the torque current is also restricted, but this will also mean the motor cannot start. In that case we can use a method in which a relay mechanism would initially bypass the limiting resistor and then as soon as the motor has gained speed, the relay will release enabling the current limit to be active.
I have been studying many KVAR related articles but I could not understand how the interaction between the motor inductance and the capacitor reactance can be detrimental to the motor, except the self-excitation phenomenon
It would be nice to have an off line conversation. It is just too difficult to discuss in this way for me. Anyways, do you have a synchronizing circuit to sync the output of the drive to the input AC and once in/held in sync provide an output that could be used to close a bypass contactor?
Regarding the synchronization if I can get proper working explanations and specifications then perhaps I may be able to imagine an appropriate design for it….
Hello, Sr. first of all, thanks for that formidable explanation.
I followed each detail of your explanation and found it very clear.
In a previous message, you recommended some IGBT based on the current, also you said using more voltage, current decrease and IGBT could be smaller.
At this point, I want to ask how to determine the voltage that could be used to power the motor based on the power of it. Example, 5hp 3 phase motor.
Thanks in advance.
Hi julian, 1 hp = 746 watts, so 5 hp = 3730 watts or 4000 watts
diving this with the IGBT voltage will give the current requirement of the device and vice versa
hi dear,
pls find this link. here it has been shown SPWM with micro-controller. But it can not control PWM frequency. for this reason i could not make that. i hope you will find any technique to control this circuit. please try to do that.
thanks.
Hello, the code is incomplete in the link you provided, and presently I do not know how to upgrade it.
Hi Gaurav,
Please explain the problem here, I’ll try to help!
hlw sir, i want to use ir2110 driver ic .that means i will create 3 phase bridge with 3nos ir2110 ic. because our local market didn’t sell that ic (irs2330). please tell me if i use that driver ic what will happen? can i use it prperly.
thanks
Hi milon, that’s possible, the description can be found here:
https://www.homemade-circuits.com/three-phase-inverter-circuit/
Hello sir,
This is very good idea. can u please tell me about PWM and SPWM and Which is the better between PWM and SPWM.
Thanks.
Thanks Milon, SPWM is better as it facilitates a pure sinewave equivalent.
Thanks sir, is this possible to making SPWM signal without micro-controller ? Please tell me, can i control the motor from 1hz to 50hz using your VFD circuit.
Hi Milon, SPWM is not related to frequency control, it is for creating a sinewave output. You can control frequency by adjusting R1 in the IC 555 circuit
yes it an be created without microcontroller, as explained here:
https://www.homemade-circuits.com/how-to-generate-sinewave-pwm/
thanks sir, actually i want to make your VFD circuit. My induction motor capacity is 0.5hp 3-phase. actually you are the professional at this sector.please suggest me, what i should? just i want to control frequency of this motor also RPM without any problem. frequency control means rpm automatic controlled. that means i want to control 1hz to 50hz only.for testing purpose i will use digital frq meter….please tell me is it possible..
Hi Milon, it is possible to control the motor using the above idea, however the concept may not be easy for a newcomer, or a less experienced person.
There’s perhaps an easier method using a bidirectional switch concept. I will try try to update it soon, which you can try.
Hola señor. Un verdadero placer encontrar tanta información, desde ya muchas gracias por su atención.
Hace tiempo estoy intentando realizar mi motocicleta eléctrica y debido a políticas de importación, me es muy difícil adquirir motor y demás.
Logre convertir un alternador en motor con 3 fases y alimentación de escobillas con poca tensión. Mi pregunta es, este circuito me sirve para eso?. Creo que los componentes electrónicos puedo conseguirlos.
Una vez más GRACIAS. atte Raúl.
Gracias Raul, es un placer para mí también! Sí, puedes usar el segundo circuito para controlar la velocidad a través del potenciómetro 1K. Dado que un alternador no es un motor de inducción, el control de V / Hz puede no ser esencial, y puede implementar el control de velocidad utilizando el método PWM.
good day sir, i know the reason why the gate driver ic produce heat, when i tested it, at first the gate driver ic have a normal temperature but when i start to vary the pwm voltage controller to its minimun value, the driver ic start to produce heat, my guess is that the excess voltage that have been reduce by pwm voltage controller return to gate driver ic as a result the ic produce excessive heat. from your point of view sir swagatam is my theory is right? thanks for responding in advanced.
yes that may be possible, that’s why it is important to include the BJT buffer stage so that a high value resistor can be used at the base, which can stop the reverse entry of the PWMs
Thanks sir, where can i get the the circuit of bjt buffer stage?
please refer to the following article, see how the mosfets are connected to BJT stage instead of the IC directly
Hello sir ,how you?
I have work out your inverter circuit sir . It’s awesome.
some time the IGBT gets short circuited. I have used the IGBT FGA25N120ANT and the load is about 7.5 hp415v .
In inverters ,is the pwm used for regulating the output rms voltage ? If that so why do we regulate that in the input DC bus.
Reply me sir ,pwm is must or not ?why it is used in inverters?
Thank you Sageyu, yes that’s quite right PWM determines the RMS of the output and also the waveform of the output AC. Regulating it at the DC side becomes more convenient than on the AC side, which would otherwise require special devices and configurations.
can we replace the 40 watt 1 ohm resistor by 5watt 1ohm is because it is only available on our place?
I am not sure at what voltage the ITRIP is designed to trip…you can refer to the datasheet of the IC and find this value.
Once you find it, you can multiply this value with the maximum safe current limit of the load…this will give you the wattage rating of the resistance…subsequently you can also calculate the resistance value applying this ITRIP voltage with Ohm’s law
good day sir,does the gate driver ic irs2330 suppose to produce heat?
absolutely not, it should remain dead cold…..
we used 5 watts 1ohm on the gate driver ic circuit in replace of 40 watts 1ohm, is it alright?
sir swagatam, the igbt is shorted, we will change it to mosfet is it alright?
dave, if your IGBTs burnt, your mosfet would also probably burn…you must first a build small model of it using BJTs such MJE13005 and check whether your basic circuit is working correctly or not, if it does only then you must go ahead with higher alternative devices.
good day again sir swagatam, we follow all the process, when we test it, we supply 3phase, and after we supply the positive dc rail and negative dc rail become shorted, then the gate driver ic become hot and it do not produce the right output, from your point of view what happen?)
please confirm the 3 phase signal with a scope, if possible please show me the image of the waveform to understand the situation….if applying Vcc supply to the full bridge iC is causing a short circuit that means your IC is faulty.
Good Day Sir, how will the pwm voltage controller vary the output voltage of the inverter circuit? can you explain it to me because i am so confused on how the circuit works. thank for responding to dumb question
Dave, the PWM will chop the low side mosfet conduction and force the load to conduct as per the average conduction rate of the applied PWM and in this way control the power of the load and its operational rate
Good day sir, where will i connect the ground of the gate driver ic? Is it in the same source of other circuit like 3phase gen and etc. And for confirmation is the negative dc bus is connected to the ground of gate driver ic?
Hi Dave, all the ground connections should be joined in common, meaning all the negatives, from DC BUS and the circuit DC should be joined together as common.
Hai sir, I have almost done with first three circuit of 3 phase VFD , but i have small problem that IRS2330 IC or IRS2332 IC that is in last circuit before igbt bridge is not available here in our location so plz instead of that IC which can use for this circuit
Hi Shivaji,
The full bridge IC is the heart of the circuit.
you should have started only after procuring all the parts, if you don’t get the full bridge IC now, your 3 circuits will be wasted.
You can inquire with your local part dealer regarding any other full-bridge driver IC, or H-bridge driver IC option?
But before buying the full bridge IC it would be better if you first confirm the 3 circuits that you have built and make sure you succeed with it first.
hai sir, plz can i know what output pins of PWM voltage controller circuit should connect the voltage to frequency converter circuit ( pwm inputs)
shivaji, the LED should be integrated with pin#3 and ground(negative supply) of the IC2 of the first circuit
Good day sir,Thank you for your support ..
you are welcome!
HAI SIR, i got output from first pwm ckt from 50hz to 160hz frequency by varying 1k preset is it correct output sir. and i connected it to ic4060 ckt then i got clock pulse with time period 4.7sec and 209mhz freq.
Hi Shivaji, yes 50Hz-160Hz looks OK, but 209 MHz is not OK.
first confirm the 4060 output frequency without the PWM integration….and also check the LED/LDR assembly separately before connecting it with the 4060 IC, check whether the LDR resistance is changing proportionately with the PWM or not.
sir, i cross checked the terminal outputs of 4060ic wtout pwm input and i got same 114v mean value to 70v mean without any frequency value .
With pwm input i got output as 203Mhz with square pulse.
Shivaji, 4060 works on DC and its output will be in DC not in AC and not in such high level.
This circuit is suitable only for the advanced and expert electronic hobbyists and engineers, please attempt this only if you are completely aware of what you are doing…
Good day sir, LDR is also woking (cross checked it )
Good day sir ,i apologize for such mistakes . i doing my master degree in power electronics and i am trying to publish it as my project if i done with this . so plz help me sir . plz give your mail id and i will send all my ckt connection diagram.
Hi Shivaji, since you are doing your maters degree you will know for example, that a CMOS IC cannot generate 170V at its output, right? so these are small things you must be well versed with. It will be difficult for me to explain all the small basic things regarding of the above circuit operation.
If you have any specific questions regarding a particular component or stage then I can help, but not regarding every small things, you will have to first learn how a 4060 IC operates… how the other mentioned ICs in the circuit operate, only then you will be able to grasp the working of the above concept…
Good day sir, can i put 1k resistor value to the 6 resistor that is connected to the output pins of the ic4049 at the 3 phase generator circuit?
Another question sir, if I use polarized capacitor to replaced the 1uF 25V capacitor at the output pin of the igbt , where will I connect the positive pin of capacitor, is it at the output or at the VB pin of the Gate driver IC
Good day Dave, it does not matter whether you connect a resistor or not because the HIN, LIN inputs are CMOS based and have infinite input impedance so the presence or absence of resistors do not matter.
I would not recommend polarized capacitor because I am not sure how they work with the IC pinouts, so better to use a non-polar type.
The VB1/2/3 all will go the respective IC pinouts marked VB1/2/3… which are also connected with the cathodes of BA159 diodes.
good day sir, what is the value of the 6 resistor at the output ic4049 in the 3 phase generator?
Hi Mark, those are actually not required…you can replace them with direct links…
Hi Sir, I would like to know why does the potentiometer (1M) cannot vary the output frequency of the 3 phase generator circuit?
Hi Reyn, in the 4060 circuit the 1M will definitely vary the frequency across all the output pins….you can confirm this without the LED assembly connected to it.
Okay Thank you Mr. Swagatam.
Do I need to supply with 12v on the Vdd(pin16) of the CD4009? Thank you for your response
obviously yes, otherwise the IC will not work.
Good day sir, may I ask what would be the expected output in pin 3 of CD4060?
It will show a varying frequency depending on the LED brightness and the initial setting of the adjoining preset.
good day sir, is the IC 4060 is suppose to create heat?
No, it should be at normal temperature, unless you do something wrong with its specifications.
Good Day Sir Swagatam, thank for the responds for all of my question,
Sir can you explain the voltage to frequency converter circuit, is it suppose to construct the circuit as the diagram indicated, can i leave the other pin of ic 4060 hanging?
Hi Christian, yes you can construct it as shown in the diagram and adjust the response appropriately.
for getting more accurate results you can try the following V to F converter circuits, if the parts are available in your area.
https://www.homemade-circuits.com/?s=voltage+to+frequency
good day sir, is the source and ground of all the ic used are connected at one source and ground, thank you sir
Christian, yes, all the +12V and the ground symbols should be supplied from a common supply source.
Sir, what is the specification of the LED(intensity) and LDR(resistance) that can be use for the optoisolator?
Mark, it is not critical, you can use any standard LED, the 1M preset can be used for customizing the outcome.
Good day sir, can I raise the value of the resistor of gate of the igbt?
Hi Christian, It is not necessary and not advisable too.
good day sir swagatam is it possible to change the value of the capacitor 40uF 400V to higher a value of capacitance of the capacitor?
Hi Dave, are you referring to the 10uF/400V capacitor? yes you can increase its value
good day sir swagatam what is the maximum current and voltage rating of that 3phase vfd?
thanks for response sir
It will depend on the selected IGBT specs which can be verified through their respective datasheets
thank you sir swagatam, i have another question sir, what is the value of the two capacitor across the vcc pin and vss pin of the irs 2330?
thank you again sir
Hi Dave, you can use 10uF/25V for those, the value sis not so crucial, it’s only for providing extra filtration for the IC pinouts
Good Day Sir Swagatam Can I replace the PWM voltage controller circuit with Arduino?
thanks for response.
Good day Kim, if you know exactly how to replace the existing PWM connections with your Arduino then yes you can do it….
Hi Sir,
Whats the difference between PWM voltage controller circuit mentioned in this circuit and the one described in the following link
https://www.homemade-circuits.com/2012/12/how-to-use-ic-555-for-generating-pwm.html
Thanks
Uday
Hi Uday, both have used the same principle of driving a 555 IC in the PWM mode by applying a square wave at its pin#2 and a modulating wave at its pin#5
Sir, In my application I am restricted to use 48V DC battery for the DC bus.
Now, I need to run an induction motor at speeds ranging from 400RPM to 800RPM.
So can I get 120V AC (or even higher than that) across the inverter with 48V DC as input?
Thanks
Uday
Uday, you can use a 3 phase transformer across the 6 mosfets (IGBTS), and convert the 48V into the required 120V AC through it…
Hi Swagatham,
I connected 3 phase generator circuit as per your diagram and fed the gating signals to the driver. Initially the motor ran with very low speed, if I try to increase the frequency of the clock, then the motor stalls(making some noise when frequency is increased). Can you help me in debugging the circuit? What modification do I need to do to make the motor run for higher speeds? I know its tough to tell like this, but any guess is appreciated.
Thanks
Uday
Hi Uday,
if you increase or decrease the frequency, it could damage the motor, the frequency should be exactly as per the motor's recommended specifications, and make sure the input 3 phase signal is 120 degrees apart, please confirm these parameters first before applying it to the main driver IC.
you must verify the 3 phase generator output first….
if you have difficulty with the 3 phase generator explained in the above circuit, you can use the one which is explained in the following article
https://www.homemade-circuits.com/2016/12/3-phase-solar-submersible-pump-inverter.html
Yes Sir, I have checked the output of the 3 phase generator. It is doing its job as it is supposed to be. And the motor is rated to operate at 400Hz, but it is unable to run for some reason.
Thanks for your response
Uday
Uday, please check the peak voltage and RMS voltage across the output terminals without connecting the motor and after connecting the motor.
Hi Sir, I am grateful for your contribution. The motor is now running. However I am confused about PWM Voltage Controller circuit.
Questions:
1. When you say "set PWM voltage controller circuit to produce a corresponding output that may be equivalent to the mains 220V or 120V AC RMS", How come a 12VDC input circuit produces that much AC voltage? (Apologies if the question is too dumb).
2. Can we integrate the DC bus voltage with the frequency converter circuit, so that if we vary DC bus voltage linearly, it increases the frequency maintaining constant V/Hz ratio.
Thanks in advance
Uday
One more sir,
What happens if we vary the duty cycle of the clock?
Thanks
Uday
You are welcome Uday!
The PWMs are at 12V level, but it's controlling the gate of the mosfets, which in turn is causing the mains DC BUS voltage at their drains to get chopped in the same ratio, resulting in a proportionately reduced 220V AC, this value can be increased or decreased by varying the PWM duty cycle proportionately…I hope you know how PWM duty cycles work, right?
your second question will need to be investigated before answering…
Great Sir, I think I got what you are saying!
I don't know in candid about the PWM duty cycle concept. But I will look into it for deeper understanding. Appreciate if you provide any link to understand that!
And Sir, what happens if we vary the duty cycle of the clock by some means?
As always thanks for your time Sir!
-Uday
if you vary the duty cycle of the clock that will also result in a proportionately reduced AC mains at the mosfet drains
No… sorry it won't have any effect, because the clocks are being converted to triangle waves which is compared with the pin#5 potential…but since the clock frequency has no relevance to the triangle wave height, it won't affect the PWM waveform in any manner
One more Sir,
The outputs from IC 4049 should be inverted?
Since the driver pins has bar over (-ve logic) for HIN and LIN
Thanks
Uday
the outputs of the IC 4049 are inverted as per the the HIN/LIN compatibility.
Got that!
Thanks
Where does the Fault(-ve Logic) and CAO pin go?
They cant be left unconnected right?
Thanks
Uday
it can be left unused and configured as indicated in the diagram, these are actually the pinouts of an extra internal opamp which could be used for switching an external parameter if required, otherwise it could be simply left unused
So all unused pins are grounded or they just left unconnected?
Thanks
Uday
Hi Swagatham,
Fabulous idea of integrating the V/Hz parameters.
However I have one question, the PWM voltage signals are only connected to low side MOSFET gates, why they are not required for High side gates, Can you throw some light on this please?
Thanks
Uday
Thanks Uday,
the low side mosfet PWM chopping is sufficient for achieving the required RMS control and sine wave equivalent waveform at the output, because the current from the high side mosfet cannot reach the load unless it passes through the low side mosfet, and during this process the current has to go through the injected low side PWM chopping at any cost, before it can reach the load, therefore only a low side switching is good enough and does the job…
Thanks for sharing your knowledge, I am learning step by step.
Have you implemented this circuit in reality?
I am connecting it as per your circuit diagram.
Question: What will be the outputs across the HO1, HO2, HO3 and LO1, LO2, LO3 pins of the driver without connecting the MOSFETS? Since I want to confirm the proper outputs of the driver before I feed them to the MOSFETS.
Thanks
Uday
I have designed the circuit after doing an intense research of all the details of the IC pinouts, as mentioned in the datasheet of the IC.
Outputs of any logic IC can remain open if required, it will never affect the IC in any manner.
by the way here for HO1—-HO3 and LO1—-Lo3 all are supposed to be connected with the gates of the respective power devices through low value resistors as indicated in the diagram
Hello sir as you discussed about 3 Phase Variable Frequency Drive Circuit
In IRS2330 instead of it Can I use IR2110 – 3 ICs to drive 6 Mosfet 2N60. Individually 2 MOSFETs by one IC IR2110.
Hello Parth, yes that's possible, you can go ahead with it.
Hi. This is the answer that I want. I am in the project to control the pumps in the plastic industry. Is it applicable for the pump that has ac power above 3 KW? Thank you.
yes it is applicable for all AC motors
Hi,
Nice job!, keep it going!
I wanted to ask something, not that off-topic after all.
I've been reading for a time already about squirrel-cage and blcd's, and I'm just a bit puzzled about power ratings (consumed vs. delivered).
I've read blcd's offer a higher size/power ratio than asynchronous ac induction motors, overall outrunners, so my question is:
Does this mean that, say, a small hobbyking's donkey brushless outrunner (14.8V – 680W) can develop more or less the same (or even more) torque than a bulky 3/4 hp (750W) 3-phase squirrel-cage motor?
I'd really appreciate if somebody could clear this one up for me.
Thanks so much,
Eduardo.
Hi thanks for your interesting question, however I have not yet investigated motors deeply so I am presently quite clueless…possibly Ill do some research, and hopefully update the answer here…
Hello Sir, I have a few questions regarding the circuits above;
1. Can you suggest the suitable IGBT that should be used for a 1HP 3Phase motor?
2. Is it possible for me to use ARDUINO as the PWM controller?
I'm currently on a project that needs to create a system that may control and monitor the type of motor I've stated above,by using ARDUINO. Please advise, Sir.
Thank You.
Hello Zuleikha,
1) You can try STGW10M65DF2 or similar
2) If you have a 3 phase signal generator using Arduino, then definitely you can use it with the full bridge driver IC LIN, HIN pinouts
you can link the SD pinout of the driver IC with your Arduino feedback control and achieve the desired control on the motor
thank you sir for your feedback, can I use the mentioned IGBT for a 1hp single phase motor as well?
according to me the mentioned will work, but it would be better if you confirm it yourself through the datasheet of the device.
Thank you sir for the quick response. Am grateful. Please sir sorry to bother you again. I would have actually mentioned this from the onset but I forgot. The alternator is a 3 phase alternator with star winding on the stator. So do you insist I make use of the pwm based motor circuit as you advised, considering the fact that it has 3 phase winding or is there a way I can work through this either with a different circuit or better still the pwm based motor circuit. Thanks.
You are welcome Andrew,
for a 3 phase winding you will require a 3 phase driver as described in the above article therefore you can use the concept which is explained in the above article.
if the 4035 stage looks difficult you can alternatively try the following idea
https://www.homemade-circuits.com/2016/12/3-phase-solar-submersible-pump-inverter.html
Goodday sir, I really want to commend your efforts. More grease to your elbows sir. I have looked at the circuits above and I really appreciate you for them. I am currently working on a project where I will have to convert a car alternator to a brushless DC motor with speed control. I have not been able to get an ESC because I live in a very remote area in Nigeria, so I really think your circuit would be of great help to me. But I actually have a little problem with understanding the various connections and how or where to connect them. First is the pwm voltage controller circuit, where do I connect the other pin from the 1k preset variable resistor I.e the pin with a plus (+) sign. Secondly, are the pins labelled fault and cao from the irs2330 to be left just like that without connecting anything to it? Thirdly, in the 3 phase signal generator circuit you made use of ic4009 and you also made mention of ic4049, but sir when I checked the pinout for these ICS online, I noticed that they had 16 pins each. Pls sir how do I go about this? I couldn't really figure out how to connect them as shown in your circuit. Lastly sir, on the frequency converter circuit where do i connect the pwm input and 0v. I initially thought that the 0v was the ground but I later saw the ground at the top, just after the capacitor. Sir pls I would be most grateful to have all these explanations I really need it for the sake of this project and any suggestions you may have is highly welcomed. Thanks a million.
Thanks Andrew,
VFDs are actually used for controlling AC motors which operate on mains voltages, for DC motor application the above complicated theory may not be required.
You can simple use the first circuit from above and use it with your alternator. You will need to connect a mosfet at pin#3 of IC2, and connect the motor across its drain and the positive supply…after this, varying the 1K pot will enable you to achieve the required speed control of the motor.
alternatively you can also try the following concept for the same:
https://www.homemade-circuits.com/2012/05/make-this-pwm-based-dc-motor-speed.html
Hi
i am omkar pawaskar from Goa
i want to make Variable frequency drive to control 3 phase Induction motor on batteries
Thank you I make this I have any problem you help me.. thank you
This circuit I can use for the electrical car (I make 555ic with variable resistor ) ?
yes you can
Where to connect Vb1, Vb2, Vb3
to the identically marked IC pins, which are also connected to the BA159 diodes
and also igbt burnt
hi sir, i have complete my cct but when i connect the single phase to measure the o/p , the 555 timer ic 1 and 2 got burned plz tell me what i should i do
Hi Muhammad, you must complete each stage separately, test them separately, confirm them separately and then gradually integrate them for the final results….if you make the whole thing at once it won't work or might cause unexpected results
hi dear swagatam i want to build 3 phase inverter with 220 volt singlr phase(actually 1 phase to 3 phase inverter) i have some question to you, first of all thank you for your sharing your knowledge,first question that is , can we use sg 3525a ic for input clock of cd4035a insted of 4060 ic? and why we use 2 555 ic for low mosfet's or igbt's whereas the IR 2330 have 6 output and 3 of this output for low igbt's, i mean are we must conect the output of ic2 555 pin 3 to IR 2330 low igbt's signals?what is that mean? and the other is how can we generate 6 pulse from cd 4049 ic?i mean can you show the connection the 3 output of cd 4035a to 4049?and can we use cd 4009 instead of cd4049?
Thanks Ghaghabay, yes SG3525 can be used for clocking the 4035 IC.
the output from the IC555 is supposed to chopp the gate trigger into smller section so that output waveform also comes out in choppped form and not in the full square wave form
you can refer to the following article for more info:
https://www.homemade-circuits.com/2013/04/how-to-modify-square-wave-inverter-into.html
the HIN and LIN work in tandem using complementary Hi/Lo from the 3 phase input…and the 4049 only helps to produce the high and low logics acceding to the input 3 phase signal and convert it into 6 outputs
correction…the word "acceding" was incorrectly typed for "according"
Good day sir 🙂 as I connected the pwm generator to voltage/frequency converter the LED tends to not vary its illumination. it has a constant illumination and the 1K potentiometer seems to be its switch to turn onandoff the LED, may I ask sir to what IC ouput should specifically be inputted to the pwm inputs of the LED?
And also sir, should the frequency on the IC4060 should be square wave?
Goodday Johnny, that means your PWM circuit is not working correctly.
first check frequency at pin#3 of IC1, make sure it's generating square waves at a frequency rate depending on R1 value, may be around 100 Hz or 150Hz, then you can confirm further the pin#3 response, check voltage here by varying the 1K pot….the voltage should also vary from 0 to 8V, for a supply voltage of 12V.
yes 4060 frequency will be square wave….
hy sir
please tell me the values of capacitors which are connected to the igbt and also tell the value of the capacitors which are connected to irs2330
Hi Muhammad, IGBT caps are all 1uF/25v, and the IC caps can be 10uF/25V
Hy sir,
so sir my IC1 and IC2 circuit functional and i have seen the waveform on the CRO.Nw i connect the Cd4035 clock on pin number 6 so tell me which circuit give me clock pulse for CD4035 and also tell me that if i connect Low side of mosfet to IC2 pin number 3 then i will be not needed to connect IRS2330 LO1.Lo2.Lo3 output to low side of MOSFET.
Thanks
Hi Muhammed, connect the frequency pin of 4035 with pin#3 of IC1, and make sure the IC1 is adjusted to generate frequency at the rate of 300Hz.
the low side mosfets should be connected with pin#3 of IC2 via isolating diodes as indicated,
No, the "LIN" inputs of the driver IC does not need to be connected with pin#3 of IC2
hy,
there is any resistor connection between IC2 o/p to CD4035 and Cd4035 o/p to CD4009 and CD4009 o/p to CD4049 and CD 4049 o/p to IR2130 for dropping the voltage level from one IC to the Other IC.
Thanks
And I use IR2130 instead to IRS2330. Is this right Choice in this circuit ???
And also Tell me that optoisolator LED/LDR is not available in the market Am is use another optoisolator like as PC817??
Thanks
Hi, IC2 is not connected with 4035, IC2 is connected with the low side mosfet gates without any resistors.
CMOS inputs don't require resistors as they have high input impedance so resistors are not involved with the shown 40XX ICs and their i/p, o/p terminals.
please don't make the opto coupler based circuit as yet, first confirm the first two circuit operations if you succeed then later you can think about building the 4060 stage.
Hy
i make this circuit bt ckt have some problem ,
Firstly o/p of 555 ic2 is squire wave form on the CRO bt when i check the o/p of CD4035 then there is no o/p on pin1,15,14.CRO show only single line and there is no wave form bt when i disconnect the gound pin 8 of cd4035 the CRO o/p show like as input.
Please tell me that what is the problem in my circuit that no show o/p on CRO.
Thanks
Hi, the 4035 circuit is a single phase frequency to 3 phase frequency converter circuit which I got from internet after some searching, I am not sure regarding its working principle, you may have to consult its datasheet for the details, or try some other design which can replicate its function for this project.
Hy Sir,
How can i control the speed by using the variable resistance in this circuit?
Thanks
Hi Ali, you can control it by replacing the 1K preset in the first circuit with a 1K pot…
Ajay, you can try 15 amp, 700V IGBT
Thanks alot sir.Pls tell me 1)why 3 diodes connected between op of PWM generatorpin (3) and lower MOSFETS gates ? 2) Actually lower MOSFETS gates are driven by IRS2330,is it rite?
Hi Sir,Can you pls suggest me IGBT suitable for your circuit to Drive 10HP ,3 phase Induction motor.
Hi Swagatam, It seem any image won't be able embed in this reply box. Is there alternative way to do so? I did captured 2 wave form images for you views and make some input.
Regards,
Cong
Hi Cong, you can send it here
/forums/forum/electronic-circuit-discussions
By the way if you are getting a square waveform then your 555 IC is working correctly….anyhow you should first confirm what exactly your control board requires for the processing of the motor control….until you know the exact specifications I don't think the experiment would make any sense
Hi Swagatam,
I have attached 2 images with the square wave form captured, one set at 7Hz and 34Hz the other. I don't know what i'd missed
at the first shot; the motor did not run at all. The controlled board was in good shape before the washer dismantled. I'll double check the control board as needs.
The Fq. generator build from timer 555. I'll do a new circuit with IC either 4047 or 4060 per your suggestion.
Thank you in advance.
Cong
7Hz_25%dutycycle.JPG
34Hz_25%dutycycle.JPG
I not sure how to attache the image. c&p function the 2 above lines.
Hi Swagatam, Additional question; Is that true if the variable frequency signal output from IC 4060 or 4070 prototype be able to substitute the software signal as seen in that video clip? I'd heard someone had said NO! What your though? Thank you in advance.
Cong
Cong, if the waveform is an ordinary square wave then definitely any variable square wave frequency will work as good as the arduino source…if you can show me the waveform of the input then I can confirm my suggestion
Hi Swagatam, Thank you so much for your prompted respond my question. When i came across on the net and had seen a short video clip from " https://www.youtube.com/watch?v=Npxd_H7FeSQ " run the same washer motor and the controlled board as mine with his laptop; I then think about a timer 555 circuit [can generate from 1 to 60 Hz], with a 5Vcc to pin 1, an output of the timer to IO pin 2, and GND to pin 3 of the controlled board as seen as those 3 blue wires in the video clip. One thing i am missing is an amplitude of the signal. And of course, i haven't get any luck at all. Please help if you would
Thanks Cong, I can't say much about IC 555 in the mode which you have suggested, but if you are looking for a good variable 1 to 60Hz frequency with a fixed duty cycle then IC 4060 should be the best choice according to me.
Can a dual 555 timer circuit on the top page be able to feeds to the 3 pin [ GND, I/O, and VCC pins] input connector of the controlled board will run a good salvage washer 3 inductor motor VFD from 120VAC?
the first circuit is a PWM generator, I am not sure whether it will be suitable for your control boar or not.
yes they are the recommended ones.
Good day sir. May I ask, am I going to connect the pwm generator directly to the pwm input of the clock generator? or is it directly connected to the driver ic? or is it that the IC4049 is the one connected to the driver IC? and also what is the ouput frequency of the PWM generator, Clock generator and Signal generator. I am currently studying this circuit for a proposal device
The first design is the PWM generator circuit, whose output needs to be fed to the gates of the low side mosfet.
the second circuit is the mosfet full bridge driver circuit which receives its 3 phase signal from IC 4049 buffer stage.
THe 4049 buffer stages receive the relevant inputs from the 3-phase generator IC 4035.
IC 4035 receives the clocks from either IC1 (555) from the first design or it could be integrated with the output of 4060 IC as shown in the last design for an automatic regulation
OK as you wish, but two 555 ICs makes more sense, as indicated in the first diagram.
okay sir thank you 🙂 and sir am i going to connect the 555 timer directly to the clock generator,ic 4060?
the frequency can be adjusted by varing R1, it should be around 200Hz.
how would you get 3 HIN, and 3 LIN for the IC IRS2330 with a IC 555 at 120 phase shift?? not possible
Thanks for your reply. I want to control the speed of three phase motor with controller and from a single phase (240 volts)(actually convert single phase to 3 phase). i need your guidance to complete this project. i make simple pwm with variable frequency from pic controller like 50Hz -100Hz. Then i apply this pwm to 4035 circuit so that i got 3 pwms with 120 deg difference from 4009 i got 6 pwms according to your circuit. Now i am going to attached IR2110 3 phase mosfet drive circuit with 6 pwms according to your circuit.
Now my question is that is these pwm's is good for IR2110 to drive IRF840 the positive DC volts of IRF840 is 240 volts single phase.
Thanks
The 3 phase driver IC is IRS2330, not IR2110…you may have to use 3nos of IR2110 circuits if you are this IC…. the IRS2330 has been configured exactly as per its datasheet instructions, and it is designed to accept the 120 phase shift square wave from a given source….so everything's fine in the diagram…but you will need to confirm all the stages separately and by using a low voltage at the mosfet side initially
yes IRF840 can be driven with the above discussed ICs
HELLO,
I am not getting this IC IRS 2330 in market.What alternative IC can be used for this?
you can use 3nos of single phase full bridge driver ICs and configure them to achieve 3 phase driver function as given here
https://www.homemade-circuits.com/2015/04/solar-3-phase-inverter-circuit.html
Can we use IR 2130 in place of it..in same configuration.
yes you can use it, or also any other similar….
1.Are the capacitors 1uF 25V are polar capacitors or non polar capacitor(H bridge driver circuit)?
2. Diode values or number that are connected across the IGBT s ?
3. Can we use a Axial fuse in place of that 1ohm 40 watt resistance
1) 1uF can be polar or non-polar does not make any difference.
2) diodes are internally present in the IGBTs, no need to connect from outside
3) 1ohm is the current sensing resistor it cannot be replaced by a fuse.
can you please send me a detailed paragraph on working of the IC s.
you can get all the details in the datasheet of the IC
Swagatam whats is the explanation that there will be no single phasing in the Induction motor.As i dont find any relation or synchronization between the signal generator and PWM regulator circuit.
I dont understand that.
Sorry, I could not understand your question properly. this is an artificially created 3 phase driver circuit which will never cause single phasing as long as the devices are working correctly.
the PWM is specifically for adjusting the RMS voltage while the signal generator is for generating the required 3 phase 120 degree shift signals for the 3 phase driver…
Please elaborate what kind of synchronization are you referring to?
how will the IRS 2330 IC will know the phases that are going to be delieverd by the PWM Controller circuit if they both deliver the same phase on the IGBT s then their might be single phasing right? Synchoronization between the signals that will trigger the IGBT s
the IC IRS 2330 is a specialized 3 phase driver device which will feed the phases exactly in the same sequence as supplied to its HIN, LIN pins, so there cannot be anything wrong in this regard.
however the 3 phase generator must be accurate and must supply the 3 phase sequence with the correct required 120 degree phase shifts, that's the only critical thing that will need to be verified.
i done this circuit by interfacing pic16f877a as pwm and frequency genrator with cd4035 circuit. But i am confused regarding to cd3045 circuit that the output frequency is just simple pwm base with shift of 120 degree but its not spwm. and when i interface your circuit with ir2110 base fet driver circuit it shows nothing in output.
the above circuit will produce a square wave 3 phase control, not an SPWM.
for SPWM you may have to inject the PWM at the bases of the lower IGBTs
Dear sir can we change direction of motor in this circuit.
Dear Anjula, it can be probably done by changing the polarity of the input clock frequency of the IC 4035
Dear brother LEDs are blinking in 3 phase sequence if i give 1Hz at 4049, then what will be problem in driver ic 2113? Can i get ouput at no load condition?
Dear brother, it could mean that your full bridge driver IC is not responding.
It will be difficult for me to troubleshoot without practically seeing it.
pleas refer to the datasheet of the driver IC and see if you have done everything correctly as per the given specifications.
…if you connect your voltmeter across the "load" points you should be able to see the required AC without any load connected
Brother i'm getting 6.76v from ic 4049 in every high and low logigate and i'm using ic 2113 for half bridge driver ic 3 sets in that i'm getting 80mv in ho and 25mv in lo, i didn't pass any dc at the drain side of the mosfet, if i passed 310v dc there will be no output in every phase, what will be the problem in that ? Pls help me out
measuring voltage is not the right method….you should measure frequency at the outputs of the 4049….
you can make the frequency rate very low at the rate of 1 Hz and then check by connecting LEDs across the respective outputs of the 4049…if these LEDs blink in a 3 phase like sequence then you can be sure of the working….and then increase the frequency to 50Hz…
after this you can feed the signal to the half bridge drivers for the final results….initially do not connect 310V….instead connect 12V and check the response using a lamp
Hello Sir,
I am a littlebit confused about connecting the 4049 in the 3phase generator. Vcc (+) goes to 1, -/GND to 8, but I don't understand the connection between 4035 Q1/2/3, 4049 & HIN/LIN 1/2/3 of the driver. Could you pls elaborate on it a little? Thx
Hello Julio,
Q1,Q2, Q3 are associated with two more NOT gates from the IC CD4009. The 3 phase outputs from the 4035 circuit connects with the inputs of the 4049 circuit marked phase1, phase2, phase3…the outputs from the 4049 gate then integrates with the relevant pins HIN, LIN of the main driver IC.
furthermore 4035 IC will need a 555 atable multivbrator circuit for acquiring clock signals at its pin#6
Yepp, I intend to make a multiplicator using a CD4046 PLL + SN74LS92 counter. It will make a reliable and fast 6x multiplication of the modulation frequency coming from IC1 555.
Regarding the 4049, so let's say I connect 4035 Q1 to 4049 A (pin3) and LIN1 of the driver, and get HIN1 from 4049 G (pin2)? And similarly for the pins 5/4 and 6/7 for phase 2/3?
OK, that's great!
and yes your mentioned procedure is correct!
Hello Swagatam, ltns 🙂
I was just wondering the other day – why do we need a multiplicator at all? Why dont we use IC1 & IC2 to generate 6x the desired frequency from the beginning? I mean if we need 50Hz x 3phase signal, lets generate 300Hz on IC1 and call it a day. Eventually in case of PWM frequency of 10kHz let's make it 60kHz on IC2. Let's say we don't want to go under 20Hz base modulation frequency, so we use the appropriate resistor in parallel to the control pot. Also for a standard 3ph motor we don't need more than let's say 100Hz, let's limit the pot size. So all in all, the applied modulation frequency would be between 120-600Hz with PWM of 60kHz (or even 120), directly on input of the 3 phase signal generator w/o the need of 6x multiplication. What am I overlooking? Some 555 limit?
Hello Julio, sorry I could not interpret your suggestion.
where do you think the PWM could be applied directly?
By multiplicator I believe you are referring to the mosfet driver IC stage, right? Please elaborate more on this.
OK, seems like I messed up a little. Let me explain.
1. In your diagrams you use a pair of 555s as a PWM voltage controller to generate the PWM signal at the required modulation frequency (let's say modulation frequency fm = 50Hz with the pulse frequency fp = 10kHz).
2. That PWM signal goes then to the frequency converter. You used a CD4060 with a coupled LED/LDR, I decided to use a CD4046 PLL + SN74LS92 counter (doesn’t matter, does the same). On the output you get your PWM signal with 6x fm (and also 6x fp for that matter).
3. That multiplied PWM signal at 6fm and 6fp serves as a clock for the CD4035 Shift Register (3 phase signal generator stage), which divides the clock signal to 3 LIN/HIN pairs using CD4049.
Now my question/idea is the following – how about to omit the frequency converter (point 2) altogether, generate the PWM (point 1) already at 6fm and 6fp to feed it to the shift register (point 3)?
I am still confused! you mean to say you want to eliminate the IC 555 stage?
then how would you generate the PWMs corresponding to the varying 220V AC? These PWMs ultimate determine the RMS of the output voltage to the motor equivalent to the input mains AC
Nonono, I mean to eliminate the frequency converter stage. And generate the PWMs at 6x frequency from the beginning. As I said, you need a 3 phase 50Hz PWM signal on output. So you generate 6x50Hz = 300Hz from the 555s with the corresponding pulse frequency of 6x10kHz = 60kHz, and you have the same result as your original design after the frequency converter stage. Do I understand that correctly? Maybe I can't explain myself, or am I missing something?
please ignore the previous comment, may be I got it now.
you want to eliminate the frequency converter stage which uses the 4060 IC or the one that you have referred to using 4046/74LS92, right?
well this stage is employed to make the system automatic, so that the VFD becomes independent of manual adjustments, and is able to read the mains fluctuations and auto-adjust the V/F ratio for the motor.
Hmmm, now I'm confused. What mains fluctuations are you referring to? The input 1phase or 3 phase AC mains is rectified to DC both for the high voltage power stage and for low voltage 5 & 20V logic stage. The pulse frequency is constant and the pulse width only depends on the modulation frequency wave amplitude (at least after your soft start circuit saturates, thx for that one, too), which frequency depends on the settings of R1 (replaced with a pot) and C1.
I feel like we are talking about the same think but somehow struggle to understand each other. Also it seems to me I am missing something terribly. Maybe I won't find out till I build the circuit finally at least on a breadboard. I wish I could skype you.
sorry…. actually it's not about the mains fluctuation issue, the frequency converter stage is for making the unit automatically compatible with all the the viable voltage input ranges, such as 440V, 120V, 220V, etc so that it becomes universally acceptable for all, and no manual settings are required by the user who buys the unit.
sorry I do not have a skype account, but now it seems we have almost sorted it out finally
….the frequency may be constant from IC1 of the first circuit, but the PWM from IC2 is dependent on the 12V supply, which is in turn proportionately dependent on the mains input voltage level….so this PWM needs to be converted into a proportionately adjusting frequency for the driver stage and eventually for the motor….otherwise if the frequency is not changed, then the V/F ratio would become incorrect for the particular motor and the whole purpose of the circuit would become zero.
Good day Sir,
Can you please post another circuit for a single phase brushed/brushless A/C motor. Thanks in advance.
please refer to the following post:
https://www.homemade-circuits.com/2013/09/single-phase-variable-frequency-drive.html
please explain how the voltage is changing in this ckts. and explain that with low frequency low voltage and high frequency high voltage is provide the ckt m i right?
Sir, if this circuit is used for a submersible motor of 10 HP, 415V with long cable of 1000 feet , it need any choke in its output?
then , what will be the swg and turns of the choke.
Hi SS, presently I do not have its calculation details, I'll try to investigate and possibly update it for you in the above post.
Hi sir,I have refer other vfd circuits also. they said,"if the frequency of the pwm is b/w 3.5khz to15khz only, the motor will be run with less hormonics. Otherwise it will damage the bearings".
In your circuit, what will be the frequency of the pwm from 555 IC?
Hi Sageyu, here it's only 80Hz, but you may increase it to 8kHz by reducing C1 to 1nF
Hello sir, can i use it for 5hp 3phase 415volts ac motor? is there any modification need to be run?
Hello Sivaraj, you can use any wattage motor as per your specifications just by upgrading the IGBTs appropriately
Hello sir,
Generally, In other VDF circuits comparator is used to generate the pwm which is corresponds to given signal i.e, sine wave or square wave.In your circuit ,How did you give a separate pwm signal that is not corresponds to the input. If this pwm is not given to it what happens
Hello S.Sageyu, a synchronized PWM is good but it's not absolutely necessary, in the above circuit the PWMs are adjusted so that the output's RMS matches with the AC mains voltage RMS. This reduces harmonics and creates safe voltage parameters for the motor. if the PWM is not introduced then the output will be a square wave with a lot of harmonics and generate noise while the motor is running.
Sir, I have decided to use FGA25N120D IGBT.Is this IGBT can be used for up to what hp motor?can i use the IR 2130 instead for IRS 2330 in your circuit.
this IGBT may be capable of handling upto 50Hp motors if the voltage is 1kv, otherwise upto 10hp at 220V
yes the two ICs can be replaced with each other
Hello sir fine?i have almost finish the above circuit using the igbt Fga 25n120d.i have littlebit confused that if the additional soft recovery diode is need for this IGBT or not in case of inductive load
It is recommended to ensure 100% safety for the devices, so you should include it.
Sir,can I use the fast rectifier diode instead for soft recovery diode since it is not available in the shop.
In case it is not possible tell me the alternate solution
yes you can