I have designed and published a variety of battery charger circuits in this website, however the readers often get confused while selecting the right battery charger circuit for their individual applications.
And I have to explicitly explain each of the readers regarding how to customize the given battery charger circuit for their specific needs.
This becomes quite time consuming, since it's the same thing that I have to explain to each of the readers from time to time.
This compelled me to publish this post where I have tried to explain a standard battery charger design and how to customize it in several ways to suit individual preferences in terms of voltage, current, auto-cut-off or semi-automatic operations.
Charging Battery Correctly is Crucial
The three fundamental parameters that all batteries require in order to get charged optimally and safely are:
- Constant Voltage.
- Constant Current.
- Auto-cutoff .
So basically, these are the three fundamental things one needs to apply to successfully charge a battery and also make sure that the life of the battery is not affected in the process.
A few enhanced and optional conditions are:
Thermal management.
and Step charging.
The above two criteria are especially recommended for Li-ion batteries, while these may not be so crucial for lead acid batteries (although there's' no harm in implementing it for the same)
Let's figure out the above conditions step wise and see how one may be able to customize the requirements as per the following instructions:
Importance of Constant Voltage:
All batteries are recommended to be charged at a voltage that may be approximately 17 to 18% higher than the printed battery voltage, and this level must not be increased or fluctuated by much.
Therefore for a 12V battery, the value comes to around 14.2V which should not be increased by much.
This requirement is referred to as the constant voltage requirement.
With the availability of a number voltage regulator ICs today, making a constant voltage charger is a matter of minutes.
The most popular among these ICs are the LM317 (1.5 amps), LM338 (5amps), LM396 (10 amps). All these are variable voltage regulator ICs, and allow the user to set any desired constant voltage anywhere from 1.25 to 32V (not for LM396).
You can use the IC LM338 which is suitable for most of the batteries for achieving a constant voltage.
Here's an example circuit which can be used for charging any battery between 1.25 and 32V with a constant voltage.
Constant Voltage Battery Charger Schematic
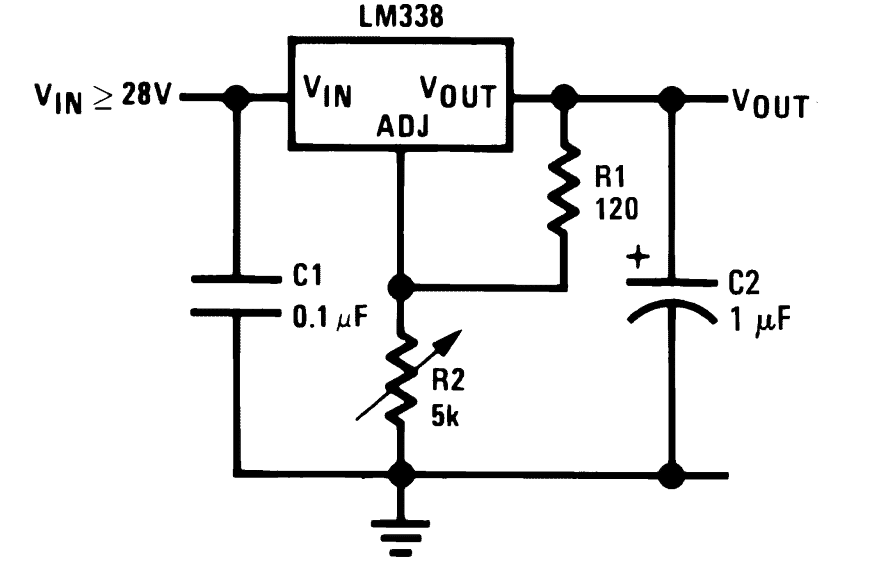
Varying the 5k pot enables setting of any desired constant voltage across the C2 capacitor (Vout) which can be used for charging a connected battery across these points.
For fixed voltage you could replace R2 with a fixed resistor, using this formula:
VO = VREF (1 + R2 / R1) + (IADJ × R2)
Where VREF is = 1.25
Since IADJ is too small it can be ignored
Although a constant voltage may be necessary, in places where the voltage from an input AC mains does not vary too much (a 5% up/down is quite acceptable) one may entirely eliminate the above circuit and forget about the constant voltage factor.
This implies that we can simply use a correctly rated transformer for charging a battery without considering a constant voltage condition, provided the mains input is fairly dependable in terms of its fluctuations.
Today with the advent of SMPS devices, the above issue completely becomes immaterial since SMPS are all constant voltage power supplies and are highly reliable with their specs, so if an SMPS is available, the above LM338 circuit can be definitely eliminated.
But commonly an SMPS comes with a fixed voltage, so in that case customizing it for a particular battery might become an issue and you may have to opt for the versatile LM338 circuit as explained above.... or if you still want to avoid this, you may simply modify the SMPS circuit itself for acquiring the desired charging voltage.
The following section have explained the designing of a customized current control circuit for a specific, selected battery charger unit.
Adding a Constant Current
Just like the "constant voltage" parameter, the recommended charging current for a particular battery should not be increased or fluctuated by much.
For lead acid batteries, the charging rate should be approximately 1/10th or 2/10th of the printed Ah (Ampere Hour) value of the battery. meaning if the battery is rated at say 100Ah, then its charging current (amp) rate is recommended to be at 100/10 = 10 Ampere minimum or (100 x 2)/10 = 200/10 = 20 amp maximum, this figure should not be increased preferably to maintain healthy conditions for the battery.
However for Li-ion or Lipo batteries the criterion is entirely different, for these batteries the charging rate could be as high as their Ah rate, meaning if the AH spec of a Li-ion battery is 2.2 Ah then it's possible to charge it at the same level that is at 2.2 ampere rate Here you don't have to divide anything or indulge in any kind of calculations.
For implementing a constant current feature, again a LM338 becomes useful and can be configured for achieving the parameter with a high degree of accuracy.
The below given circuits show how the IC may be configured for implementing a current controlled battery charger.
Make sure to check out this article which provides an excellent, and highly customizable battery charger circuit.
Schematic for CC and CV Controlled Battery Charger
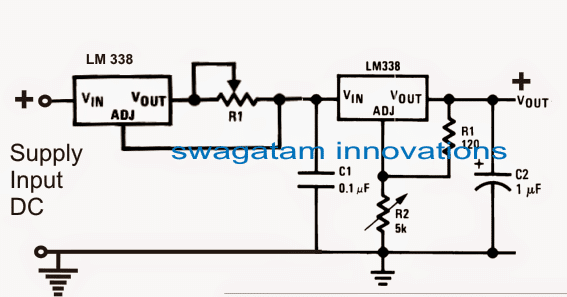
As discussed in the previous section, in case your input mains is fairly constant, then you can ignore the right hand side LM338 section, and simply use the left side current limiter circuit with either a transformer or an SMPS, as shown below:
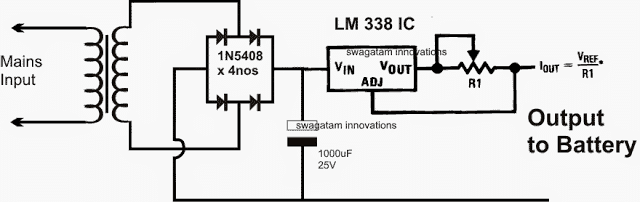
In the above design, the transformer voltage may be rated at the battery voltage level, but after rectification it might yield a little above the specified battery charging voltage.
This issue can be neglected because the attached current control feature will force the voltage to automatically sink the excess voltage to the safe battery charging voltage level.
R1 can be customized as per the needs, by following the instructions furnished HERE
The diodes must be appropriately rated depending on the charging current, and preferably should be much higher than the specified charging current level.
Customizing current for charging a battery
In the above circuits the referred IC LM338 is rated to handle at the most 5 amps, which makes it suitable only for batteries upto 50 AH, however you may have much higher rated batteries in the order of 100 AH, 200 AH or even 500 AH.
These might require charging at the respective higher current rates which a single LM338 might not be able to suffice.
To remedy this one can upgrade or enhance the IC with more ICs in parallel as shown in the following example article:
In the above example, the configuration looks little complicated due to the inclusion of an opamp, however a little tinkering shows that actually the ICs can be directly added in parallel for multiplying the current output, provided that all the ICs are mounted over a common heatsink, see the below diagram:
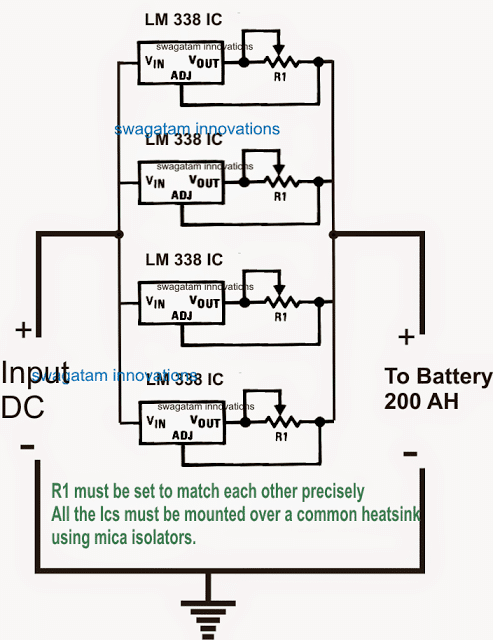
Any number of ICs may be added in the shown format for achieving any desired current limit, however two things must be ensured in order to get an optimal response from the design:
All the ICs must be mounted over a common heatsink, and all the current limiting resistors (R1) must be fixed with a precisely matching value, both the parameters are required to enable an uniform heat sharing among the ICs and hence equal current distribution across the output for the connected battery.
So far we have learned regarding how to customize constant voltage and constant current for a specific battery charger application.
However without an auto cut-off a battery charger circuit may be just incomplete and quite unsafe.
So far in our battery charging tutorials I have explained how to customize constant voltage parameter while building a battery charger, in the following sections I will try to explain how to implement a full charge auto cut off for assuring a safe charging for the connected battery.
Adding an Auto-Cut 0ff in Battery Charger
In this section we'll discover how an auto cut-off may be added to a battery charger which is one of the most crucial aspects in such circuits.
A simple auto cut-off stage can be included and customized in a selected battery charger circuit by incorporating an opamp comparator.
An opamp may be positioned to detect a rising battery voltage while it's being charged and cut off the charging voltage as soon as the voltage reaches the full charge level of the battery.
You might have already seen this implementation in most of the automatic battery charger circuits so far published in this blog.
The concept may be thoroughly understood with the help of the following explanation and the shown circuit GIF simulation:

NOTE: Please use the relay N/O contact for the charging input, instead of the shown N/C. This will ensure that the relay does not chatter in the absence of a battery. For this to work, also make sure to swap the input pins (2 and 3) with each other.
In the above simulation effect we can see that an opamp is been configured as a battery voltage sensor for detecting the over charge threshold, and cutting off the supply to the battery as soon as this is detected.
The preset at pin (+) of the IC is adjusted such that at full battery voltage (14.2V here), the pin#3 acquires a shade higher potential than the pin (-) of the IC which is fixed with a reference voltage of 4.7V with a zener diode.
The previously explained "constant voltage" and "constant current" supply is connected to the circuit, and the battery via the N/C contact of the relay.
Initially the supply voltage and the battery both are switched off from the circuit.
First, the discharged battery is allowed to be connected to the circuit, as soon as this is done, the opamp detects a potential that's lower (10.5V as assumed here) than the full charge level, and due to this the RED LED comes ON, indicating that the battery is below the full charge level.
Next, the 14.2V input charging supply is switched ON.
As soon as this is done, the input instantly sinks down to the battery voltage, and attains the 10.5V level.
The charging procedure now gets initiated and the battery begins getting charged.
As the battery terminal voltage increases in the course of the charging, the pin (+) voltage also correspondingly increases.
And the moment the battery voltage reaches the full input level that is the 14.3V level, the pin (+) also proportionately attains a 4.8V which is just higher than the pin (-) voltage.
This instantly forces the opamp output to go high.
The RED LED now switches OFF, and the green LED illuminates, indicating the changeover action and also that the battery is fully charged.
However what may happen after this is not shown in the above simulation. We'll learn it through the following explanation:
As soon as the relay trips the battery terminal voltage will quickly tend to drop and restore to some lower level since a 12V battery will never hold a 14V level consistently and will try to attain a 12.8V mark approximately.
Now, due to this condition, the pin (+) voltage will again experience a drop below the reference level set by pin (-), which will yet again prompt the relay to switch OFF, and the charging process will be again initiated.
This ON/OFF toggling of the relay will keep on cycling making an undesirable "clicking" sound from the relay.
To avoid this it becomes imperative to add a hysteresis to the circuit.
This is done by introducing a high value resistor across the output and the (+) pin of the IC as shown below:
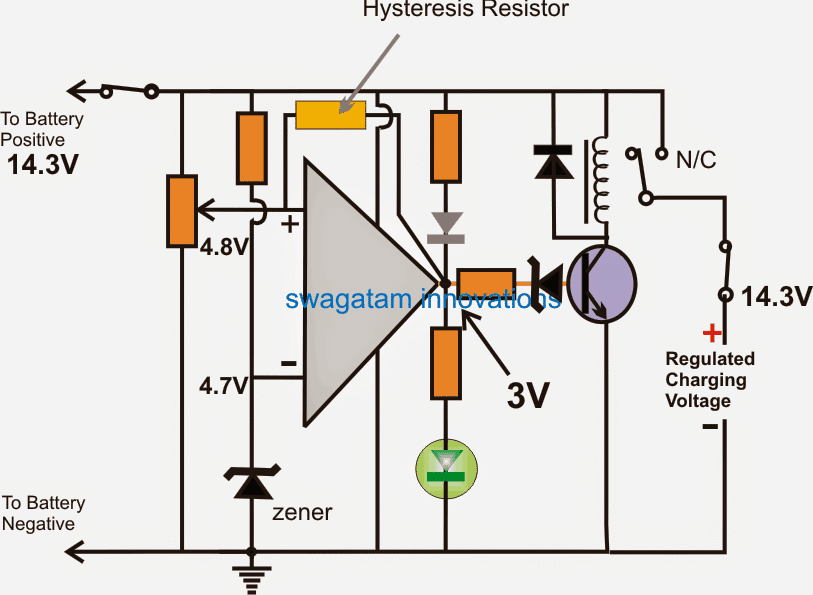
Adding Hysteresis
The addition of the above indicated hysteresis resistor prevents the relay oscillating ON/OFF at the threshold levels and latches the relay up to a certain period of time (until the battery voltage drops below the sustainable limit of this resistor value).
Higher value resistors provide lower latching periods while lower resistor provide higher hysteresis or higher latching period.
Thus from the above discussion we can understand how a correctly configured automatic battery cut-off circuit may be designed and customized by any hobbyist for his preferred battery charging specs.
Now lets see how the entire battery charger design may look including the constant voltage/current set up along with the above cut-off configuration:
So here's the completed customized battery charger circuit which can be used for charging any desired battery after setting it up as explained in our entire tutorial:
- The opamp can be a IC 741
- The preset = 10k preset
- both zener diodes can be = 4.7V, 1/2 watt
- zener resistor = 10k
- LED and transistor resistors can be also = 10k
- Transistor = BC547
- relay diode = 1N4007
- relay = select match the battery voltage.
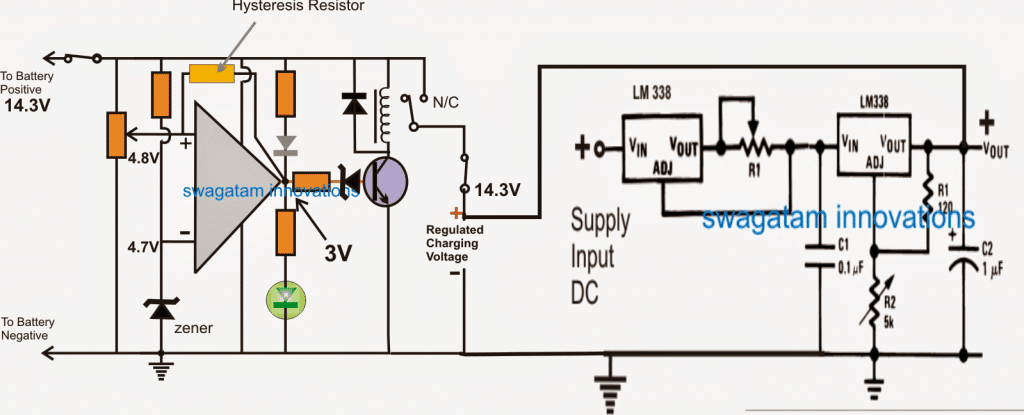
How to Charge a Battery without any of the Above Facilities
If you are wondering whether it is possible to charge a battery without associating any of the above mentioned complex circuits and parts?
The answer is yes, you can charge any battery safely and optimally even if you do not have any of the above mentioned circuits and parts.
Before proceeding it would be important to know the few crucial things a battery requires to charge safely and the things that make "auto cut off" "constant voltage" and "constant current" parameters so important.
These features become important when you want your battery to be charged with extreme efficiency and quickly. In such cases you may want your charger to be equipped with many advanced features as suggested above.
However if you are willing to accept the full charge level of your battery slightly lower than optimal, and if you willing to provide a few hours more for the charging to finish, then certainly you wouldn't require any of the recommended features such as constant current, constant voltage or auto cut off, you can forget all these.
Basically a battery should not be charged with supplies having higher rating than the battery's printed rating, it is as simple as that.
Meaning suppose your battery is rated at 12V/7Ah, ideally you must never exceed the full charge rate above 14.4V, and current over 7/10 = 0.7 amps.
If these two rates are correctly maintained, you can rest assured that your battery is in safe hands, and will never get harmed regardless of any circumstances.
Therefore in order to ensure the above mentioned criteria and to charge the battery without involving complex circuits, just make sure the input supply that you are using are rated accordingly.
For example if you charging a 12V/7Ah battery, select a transformer which produces around 14V after rectification and filtration, and its current is rated at around 0.7 ampere.
The same rule may be applied for other batteries also, proportionately.
The basic idea here is to keep the charging parameters slightly lower than the maximum permissible rating.
For example a 12V battery may be recommended to be charged upto 20% higher than its printed value, that is 12 x 20% = 2.4V higher than 12V = 12 + 2.4 = 14.4V.
Therefore we make sure to keep this slightly lower at 14V, which may not charge the battery to its optimal point, but will be just good for anything, in fact keeping the value slightly lower will enhance the battery life allowing many more charge/discharge cycles in the long run.
Similarly, keeping the charging current at 1/10th of the printed Ah value makes sure that the battery is charged with minimum stress and dissipation, rendering a longer life to the battery.
The Final Setup
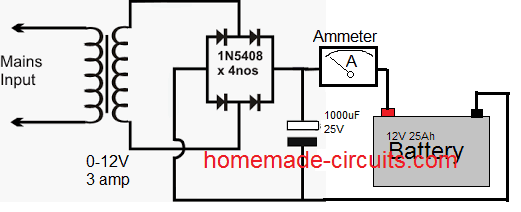
A simple set up shown above can be universally used for charging any battery safely and quite optimally, provided you allow sufficient charging time or until you find the needle of the ammeter dropping down to almost zero.
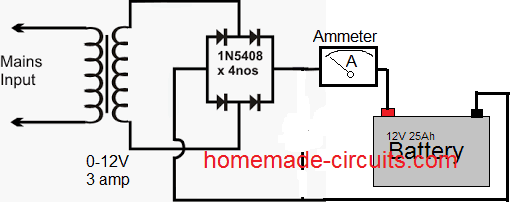
The 1000uf filter capacitor is actually not needed, as shown above, and eliminating it would actually enhance the battery life.
Have further doubts? Do not hesitate to express them through your comments.
Source: battery charging
hi bro , I am designing ev bike in that i have a 72v battery and 12v auxiliary battery …..the 72v battery is charged by charger in need to charge a this 12v auxiliary battery from 72v with 1A-2A…. can you suggest me it help me a lot
THANK YOU
Hey Ganesh,
This one appears to be the best design suitable for your application:
https://www.ti.com/lit/ds/symlink/lm5164.pdf
bro, I need to charge 12v auxiliary battery with 72v battery with 1A-2A
Hi Ganesh,
You will need a regulated buck converter for this application:
https://www.homemade-circuits.com/calculating-inductor-value-in-smps/
we are a battery Start-up and have developed a new type of battery with a different chemistry. we want to develop a battery charger for this battery which would be used for charging the battery packs of different types of electric vehicles having different voltage requirement like 12×4=48v for erickshaw, 12×5/6=60/72v for 2-wheelers, 12×8/10/12=96/120/144v for cars/trucks/trailers etc.
we need the charging at 0.5c to 4c for battery capacities ranging from 50AH to 500AH.
could you please guide us to develop simple, low cost & reliable battery chargers with functions to adjust the voltage & current as required.
We also need auto cut-off plus a temperature sensor & controller by limiting/reducing the input current if the battery temperature starts increasing beyond a particular limit.
please contact at the below mentioned email ID mohindersinghwahi1967@gmail.com or directly on whattsapp number +917385081488
Hello Mohinder,
If your battery is able to accept charging current at 4C rate, then that’s an outstanding feature and that also means it can be quickly charged within 15 minutes.
I can definitely provide you with a simple yet highly efficient and effective BMS type charger circuit for your battery.
Just give me one day, I will get back to you soon with the circuit idea.
If possible please provide more technical details about your battery, so that I create a new article on this with your credentials which might help you to get more potential customers.
Sir, Namaskar I have a 3.7v, 3Amps chargeable 18650 type battery. Please tell me a transformer less circuit to charge it. I would be grateful to you.
Hello Ashu,
For a 3 Ah Li-ion battery the optimal charging current will need to be 1.5 amps, which is not feasible and not appropriate with a capacitive power supply, so you will need an SMPS circuit for this.
I would recommend using an existing mobile charger for this, by adding a 4.1V voltage regulator at the output.
Let me know if the idea works for you, or if you have any further doubts…
Sir, kya ye voltage regulator zener diode hi hai,ya kuchh aur kripya sujhaye aur yadi zener hai toh isse kaise connect karein
Ashu, you can use the following voltage regulator circuit example at the output of the mobile charger:
" rel="ugc">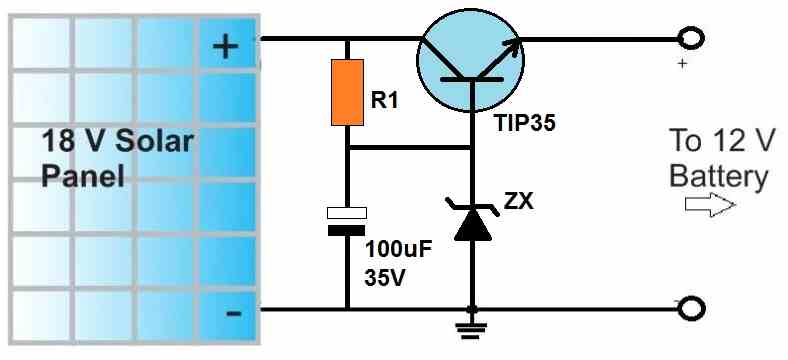
Please do the following modifications in the above circuit:
1) Replace solar panel with your mobile charger supply input
2) Replace the TIP35 with TIPP3055 (although TIP35 will also work)
3) Replace R1 with 330 ohms 1 watt
4) Replace the zener diode ZX with 5.6V 1 watt zener diode.
5) The 100uF can be a 100uF/25V capacitor or any nearby value will work.
Hi Swagatam;
I need a circuit which may control / limit not only DC voltage but also ampere between 1 – 30 Volts and maximum 15 Amperes. So please advise which circuit I may use.
Best Wishes.
Hi Suat, You can try the practical design from the following article:
https://www.homemade-circuits.com/how-to-design-a-stabilized-bench-power-supply-circuit/
Instead of using two transistors for the main pass transistor, you can replace it with the following single Darlington transistor.
https://www.homemade-circuits.com/50-amp-transistor-mj11032-mj11033-datasheet-pinout/
sir i need battery charger circuit to charge four lead acid batteries in series 130 -180 ah capacity.
regards
You can try the following circuit: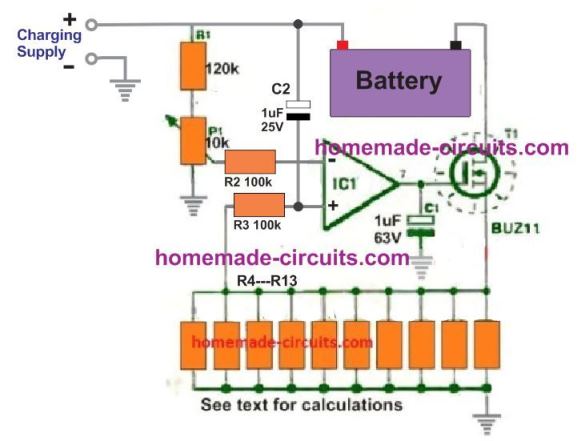
" rel="ugc">
More information on this can found in the following article:
https://www.homemade-circuits.com/high-current-10-to-20-amp-automatic/
Good day Sir, I used my fridge on 150ah battery with 1.5kva inverter but not very cold as compared with someone’s 200ah(very cold).
Please how can I salvage this to use it with my 150ah battery.
Thanks Swag.
Hi Seun, it simply means that the 150 Ah is not able to provide sufficient current to the fridge which is bad for the fridge and the battery also. You must check the current using 150 Ah battery and with 200Ah battery, that will help to understand the problem. The current consumption should not be beyond 15% of the battery Ah rating
Thanks Swag, if supplementary solar panels are added, what will be the optimum current drawn?
The current consumption will depend on the load. The load decides how much current it needs to draw.
I meant if the load draws 10amps from battery only but if added solar system supplies 3amps, will only 7amps be drawn from the battery invariably.
Yes that’s’s correct!
Good day Sir, Swagatam, I have a few questions on battery charging.
1. I noticed a trafo charger was charging without rectifier, any effect?
2. It is a common practice to put capacitor to charger, but you recommended not to use, any effect? I even saw some using 10000uf.
,3. I noticed preset settings for auto cut off for 40ah battery and 100ah is different, why is it so. Is there a way to have a standardised settings for these sizes.
Hi Seun,
It is dangerous and impossible to charge a battery directly from transformer without a rectifier.
You can use a filter capacitor after the bridge for charging a battery, it is fine. But without a filter capacitor the battery is charged with 100 Hz ripple voltage which helps to prevent sulfation on the battery plates.
According to me the full charge voltage preset setting should be the same for all batteries. However the current (amp) setting of the charger must be changed according to the battery Ah spec.
Thanks Sir Swag, between 1000uf and 10000uf capacitor which is better and why?
Hi Seun,
10000uF will allow the battery to charge faster than 1000uF. However DC without filtration is better for charging lead acid batteries.
Thanks Sir, I appreciate.
Can desulfator help if capacitor is used.
Capacitor will prevent the desulfator from working normally and producing the intended results.
Making it faster, does it increase voltage or current?
Please do you have any circuit or component that boost charging current.
As the capacitor value increases the current and voltage both increase, but not beyond what the power supply can produce.
For boost charging you can refer to the following post:
Make this Fast Battery Charger Circuit
Hello Swagatam, in this post I saw another automatic cut off Goff explained. You have said for it to work, the input pins 2 and 3 should be swapped with each other. What do u mean with the “swap?”……joining together???
Hello Morris, swapping means interchanging the pinouts with each other.
Sir referring to the fig of CC,CV battery charger circuit using LM 317/ 338, you have used the CC stage first and then the CV stage using the second regulator chip.My doubt is ,can we connect the other way round also,viz CV stage first and then the CC stage? Does this affect the circuit performance in any way? Also pls let me know whether this circuit helps in accidental short circuit protection
Binoj, yes you can put CV first and CC next, no problem with that. You can connect them anyway round, no issues. The ICs are internally fully protected against overload and short circuit.
At the end of the article you say:
“The 1000uf filter capacitor is actually not needed, as shown above, and eliminating it would actually enhance the battery life”
How would removing it enhance the battery life?
That capacitor would smooth out the DC from the rectifier. Surely that’s better for the battery? Isn’t it?
Just trying to understand.
Thanks in advance.
A pulsating DC is probably better for a battery since it prevents the internal plates of the battery from sulfating, and thus helps to keep the battery healthy and long pasting.
If I have a 12 v 7 amp battery and I use a 12 Volt 1 amp transformer or precisely a 750 ma transformer then will it be safe to forget the peak output voltage which may be 20 volts without using any regulator ics ?
12V transformer will produce around 17 V,and not 20 V after full bridge rectification…and it would be fine to provide this peak level provided the charger is equipped with a 14.3 V auto cut off
Hi Swagatam, i found out that by using the 12V 2A adapter charger, the boost converter voltage need to set above 18.1V then the current output will be regulated. From 18.1V onwards no matter how much voltage that is above 18.1V then output current will be regulated in 0.72V. How do i solve this?
Hi Jason, the output power of any power supply should be equal to V x I, therefore at 12V 2 amp, the power output ofyour boost converter is 24 watt. This power output must be available throughout the entire voltage range of the boost converter, if this is not happening, then the boost converter may not be OK. The problem cannot be solved externally.
If I use a voltage regulator Lm317 to charge 12 Volt 7 Ah battery by setting exact 14.4 v along with transformer rating 1 or 2 Ampere, will it apply 0.7 A or the full 2 Ampere to the battery ?
The maximum current from the LM317 can be 1.5 amps provided it is perfectly cooled, otherwise it will limit the output current as soon as its temperature gets higher than the specified limit.
Thanks for reply. But if I use a 12 Volt 1 ampere transformer to charge a 12 Volt 7.2 A battery, then is it a constant voltage or a constant current charger ? Since most low cost chargers available in market use this technique along with an ammeter to charge batteries so I want to know ?
It will work like a constant voltage. For applying a constant current you can add a transistor stage to the circuit as explained in the following article:
https://www.homemade-circuits.com/how-to-make-current-controlled-12-volt/
Hi, would like to know if i am building a charger for 12V 7.2Ah battery charger, which my power supply is DC 12V 2A :
1. I am planning to use a boost converter to boost the voltage into 14.1V and connect the boost converter to the circuit limiter circuit and limit it to 0.78A which is 0.1C. Is it okay if i use the current limiter circuit stated above?
2. About the CC & CV stage, when the voltage of battery rise to the the input voltage that i set which is 14.1V the current will automatically decrease slowly? or i have to create a pwm signal to control the current.
Hi, yes you can do that!. If your power supply is an SMPS you may find a preset adjustment built-in which you can use for increasing the voltage to 14.1V….if not then you can use the 555 boost circuit I have explained below:
https://www.homemade-circuits.com/how-to-make-simple-boost-converter-circuits/
you can use the 2nd IC 555 circuit. For the coil you can use 50 turns, and adjust the feedback preset to adjust the output to 14.1 V.
For the current you can use an LM317 current limiter as explained in the following article:
2 Best Current Limiter Circuits Explained
Dear Sir,
Thank you for you reply. But the output of LM317 is 2A right? Says if i am using a LM317 to calculate R1 , the formula will be R1 = Vref/current, so the output current that i need is 0.78A therefore i will calculate the R1 resister by 1.25/0.78 = so the R1 value will be 1.60ohm. Am i right?
2. How about the voltage since i will be using a boost converter board to boost my voltage up to 14.1 and connect it to the current limiter circuit. Is there any effect in value of voltage from the output of current limiter circuit?
Hi Jason,
your calculations are correct.
No, the current limiter will not have any effect on the 14.1 V, except the current.
Hi Swagatam,
I actually connected did the circuit with boost controller connect with the current limiter circuit to get 0.72A however, when I vary the voltage in my boost controller the current output varies too I’m not using a smps power supply I’m using a 12V 2A adapter. what could be the problem here?
Hi Jason, if your boost circuit is varying the current from its source then the output current will also vary. You can try a variable SMPS power supply or a transformer based variable supply which can provide a variable output from 3 V to 15 V, this will make it clear whether the current reduces with voltage or not.
Alternatively you can try a 6 V 2 amp fixed power supply, you will find the current supply to be intact, as set by the LM317
Hi im currently building a 12V 7.2Ah lead acid battery, would like to ask a few question if my power supply is 12V 29A is it possible to use this circuit without any error or damage in the equipment?
Is there any reference that I could follow for the constant voltage 17% and 18% higher also for constant current 1-2 of 10? because I need it in my research. I would appreciate if you could help with.
The data provided in the article are standard specifications for a lead acid battery. You can refer to “Battery University” website for comprehensive details regarding batteries.
Hello Sir,
Thanks for the valuable information. I am working on a project where I have to generate electricity from a 12V DC motor using anticlockwise and clockwise rotation one after another and save the power generated in a 9V battery.
Sir, it would be a great help if you pls tell me how can I make the system work! How can I make the circuit to save the generated electricity inside the 9V battery! I am at a loss and really confused because neither constant current nor constant voltage condition can be achieved in this case.
Hello Arnab,
You can use a bridge rectifier using 1N4148 diodes for rectifying the motor output AC to DC for charging the battery. The output voltage level will decide which battery can be used for the charging process.
Dear Swag
Thank you for helping!
I am looking for the easiest way to use a photovoltaic panel with USB output (without battery) to provide power for an outdoor remote temperature sensor that I cannot access except for one or two weeks each year. Which exceeds the lifetime of the alcaline batteries (2x AA).
I would like to use two AA NiZn cells (instead of NiMH because the temperature may reach -20°C in winter) and was wondering if a constant voltage supply at 1.65V would suffice, and if any more complex solutions make any sense at all due to the fact that the charger will reset each morning anyway.
Looking forward to you reply!
Have a nice day
Pascal
Dear Pascal,
can you tell me the mAh value of the cell. It is actually very easy to get these cells charged with a solar panel quickly, just like a Li-on batteries.
There a good information available in the below link, regarding the charging specs of these batteries
https://en.wikipedia.org/wiki/Nickel%E2%80%93zinc_battery#:~:text=of%20discharge%20used.-,Advantages,1.5%20V%20alkaline%20primary%20cells.
Hello, Swagatam Sir
This is the perfect one I was looking for. Sorry for any inconveniences but I want a pre conditioning trickle charging in this project. How can I add one in this?
Thank you Yash, for trickle charging you can keep a permanent high value resistor attached between the positive of the battery and the positive of the charger supply. This resistor will ensure that even when the charging supply is cut off, the battery keeps getting the required amount of float charge and self discharging is prevented.
Hey Swagatam,
I am currently designing a battery charger circuit for 25.2V 6S LiPo battery packs (4.2V Cells). Our charging requirements are 7A constant current. Was wondering how I could adapt this design to meet my needs. Or if you had a better idea of how to go about this design? Hope you could bring some insight to my problem.
Best,
Joe
Hey Joe, you can try the first option as described in the following article:
https://www.homemade-circuits.com/battery-current-indicator-circuit/
You can replace LM338 with LM196 for increasing the current output
Thank you for the quick reply. However, wouldn’t the LM196 limit my charging voltage to 10 Volts though since these regulators are only rated for working up to 70W?
Yes you are right, in that case you can use 2 LM338 in parallel. Just connect their similar pins together and mount them over a single common heatsink
Good day Swagatam,
I have implemented the constant voltage constant current charger as described above. I am however charging a 55ah battery. After consulting the battery’s datasheet I have found that my battery is optimally charged at 8amps. I then implemented the circuit as such in order to have a max of 10 amps. After numerous testing on smaller batteries (7ah) I manage to charge these batteries but my maximum current is only 0.2amps. When switching over to the larger battery I only manage to charge at less than 1amp. My current remains constant, but is still very small. What could the reason for this be and how can I increase my charging current? I have been looking into the lm338 datasheet as well and have implemented some of their circuits which all work well, but the current remains very small. Is this maybe due to my supply not giving enough amps? I am using 8amp solar pv’s in parallel thus 36V 16amp supply?
Thanks.
Hi Johan, if you have wired LM338 IC correctly shown then you will definitely get a maximum current of 5 amps from a single IC, provided the IC temperature is kept below 50 degrees.
Yes, the input current should be at least equal to the current that is required by the load, if not more. Please make sure the solar panel output current is over 8 amps, by connecting an ammeter across the panel terminals.
…For current over 5 amps, the current control resistor won’t be required, and the IC itself can be used as a constant current source.
Hello Swagatam,
Read your article and all the comments, I am still facing problem and want to ask you questions.
I am designing a battery charger circuit for li-ion 5V and 2.1A battery. According to instructions I have selected R1 and R2 resistors for voltage and current regulator functions. Relay selection is also dependent on battery, I have done that. And hysteresis resistor is hit and trial process. My questions are:
1) If I can use the same parts other than which I have selected?
2) If answer to 1) is no, then please tell which zener diode (specification), zener diode resistor, relay diode, led and transistor resistor, preset resistor, transistor IC, and which Diode I should use. You can also share formula related to any part.
I am unable to find way on how to select these parts.
Your response will help a lot.
Hello Aryan,
1) Yes you can use the same parts for the op amp circuit, except the zener diode.
2) you can use a 3V zener, since using a lower value provides a greater range for the preset setting.
3) Relay diode can be 1N4007, since it will be enough to handle the back EMF from most relay coils.
The resistors are used for dropping voltage and current depending on the associated semiconductor device’s voltage and current specs.
It can be a long explanation which cannot be accommodated here, but all these are thoroughly explained and addressed through many articles in this blog.
A big thanks for your reply. I will look for those articles having that information.
Also, I want to make the charging start automatically while the input supply is connected all the time.
Do I need to adjust the potential which op-amp detects (here 10.5 V) and the rest of the circuit all same? Or any component needs to be replaced?
Waiting for your reply.
Yes you will have to adjust the sensing potential through the given preset carefully, as explained in the above article. You can also refer to the following article for more circuits that might be suitable for your application:
Op amp Battery Charger Circuit with Auto Cut Off
I will refer to that article. Big thanks to you.And can the presets value be confirmed in circuit simulation software? If yes then please suggest software which can do that.
The preset values are not critical, they can be any value from 1k to 100k, because the op amp input pins have high impedance, so only the ratio of the potential divider created by the preset adjustment matters, not the value. I actually do not use simulation software, instead I depend on and trust my knowledge and experience.
Hi, thank you for all the wonderful circuits you provide and in advance for any help with my 2 questions. First for the current limiting section of the battery charger I need a constant current of 500ma I’ll be using an lm317 with a fixed R1. So question 1 is how do I determine the wattage requirement of R1? The input voltage will be approximately 14.5 volts provided from an automotive style alternator. Second question, since I will be using an alternator as voltage input should I still use the capacitor in your schematic shown prior to the LM 338 (lm317) (1000uf 25v)?
Hi, The R1 wattage can be calculated by multiplying the reference value 1.25V with the maximum current limit value.
If the supply input is from an alternator, then you will not only have to use the filter capacitor but also a bridge rectifier for filtering the alternator AC to DC.
Thank you very much for your help. The alternator has a built in rectifier so output is in DC, I’ll add the capacitor anyway as I don’t think it can hurt anything. Once again thank you very much for the response and how fast you replied.
No problem! Wish you all the best!
Hello sir,
if i have two 6v/4.5Ah batteries and i connect them in parallel, what will be the value of charging voltage and current?
Hello Safaa, charging voltage will be 7.1V, current can be 500 mA
sorry, current should be 1 amp, since two are in parallel
Hello sir,
I need your help sir. I am having a ups transformer with 15 volt 7amp (D.C.) tapping. I want to use it for charging 12volt 25ah battery using lm338. I am also using the same transformer for inverter circuit using sg3525 published by you sir. I understand that lm338 can handle only up to 5amp. In this case how can the current of 7amp be reduced to bellow 5amp, so that LM338 circuit is safely handled.
thanking you sir,
leelesh.
Hello Leelesh, you can add a current limiter through a simple BC547 transistor as shown in the following article;
https://www.homemade-circuits.com/how-to-build-solar-panel-voltage/
Thank you sir.
Good night.
Leelesh
Sir,
I referd your article on ‘Solar penal voltage regulater ‘ and understood that the bc 547 will keep the output current constant or restrict it below the threshold limit fixed by R3. But in my case the input to LM 338 itself is 7amp, wherein it allows only max 5amp.and hence the bc 547 will force the IC to shut down. Therefore is it ok, if a suitable resister is connected between input of lm338 and power supply to limit the current to 5amps. Pl.clarify sir.
Thanking you sir,
Leelesh
Leelesh, your battery is 25 Ah so the max current should not be more than 3 amps. So R3 must be selected to limit the LM338 at 3 amp.
Thaks sir
Hi. If i want to charge a 12V/50AH battery i understand that the current have to be limited to 5A witch is also the rating of the LM338… Referring to the above “Schematic for CC and CV Controlled Battery Charger” can i use just one lm338 configured as voltage regulator and ignore the second lm338 configured as current limiter (the left side one) ?
If yes can i use the same circuit to charge another battery rated 12v/90AH even if it will take longer time to be charged.
NB: I’m using a transformer rated 20VAC / 8A.
Thanks.
Hi, yes you can use only the voltage regulator circuit using LM338, and skip the current controller, because the IC is itself internally protected at 5 amp max current.
You can use the same circuit for charging a 90 Ah battery at 5 amp which might take up to 24 to 30 hours for the battery to charge fully. Just make sure the IC is attached with a large heatsink and do not use any filter capacitor after the bridge rectifier for the input supply.
Thanks a lot for clarifying this out. As for the input supply filter capacitor is it ok to skip it even if i will use the auto cutoff circuit based on the lm358 and the relay coil witch, i think, have to be fed with dc current??.
You can put a filter capacitor at the output side of the LM338, a 470uF/25V should be enough.
Thanks a lot for answering.
As far as charging phases of a lead acid battery are concerned i’ve read everywhere this statement :
” constant current is the phase where the voltage is varying (rising) and current is constant with time. Approximately 70% of the battery is charged in this phase and this is the fastest charging phase.
constant voltage is the phase where the voltage is constant with time and current is varying (falling). In this phase rest of the 30% battery is charged and this is the slowest part of charging phase.”
Since with the lm358 (or the 741 ic) auto cut-off design the charging process is stopped as soon as the voltage reaches it’s maximum charging value (14.3v for instance) does this mean that with this design the constant voltage phase (ie 30% of the charging process) is not executed ?
Yes that is correct, if you wish you can add a float charging by adding a permanent resistor across battery positive and the supply source from LM338. This resistor can be any high value resistor such as 470 ohm approximately.
Hello Swagatam,
I would like to use this circuit with added hysteresis resistor to charge a 3.6V 12000mAh NiMH batteries. Maybe with 1.1A carging current. My question is if it is possible to use this circuit and what should i use instead of the 4.7 zener.
Thank you
ina.ses
Hello ina, yes that is possible, in fact you can use the above designs for charging any type of battery by suitably adjusting the involved circuit parameters.
You can replace the zener with a couple of 1N4148 diodes in series, with cathode towards the ground.
Hello Swagatam, thank you very much for your fast reply! I am a beginner in electronics so i find your articles very helpful. So for my parameters I have chosen
Battery to be charged is 3.6V
Upper cut off point 4.29V
Lower point 3.3V.
So after this explanation:
https://www.homemade-circuits.com/universal-battery-charger-circuit/
i set Vcc to 3.5V and reference of OP amp to 3.5V using 5x1N4148, is this right?
So for comparator the threshold is VH 2.14V and VL is 1.65V?
Thank you in advance
Hello Ina.ses, IC 741 will not work with 3.5 V, so the circuit cannot be used for your application.
Hello Swagatam,
thank you for your answer and sorry to bother again. Input DC of circuit is 5V then im using lm388 to achieve a constant voltage of 4.3V. Then l i could use ic 741 if i use a vcc of 5V or use something like lm358 which works with 3V?
Thank you
Hi ina.ses, LM358 can be used, since it will work with 3 V. You can also use LM321 IC
Hello Swagatam,
a big thank you for answering my questions!
I have ordered the parts and because i can´t get relais to match my battery voltage i am building this circuit with TIP122 as switch:
https://www.homemade-circuits.com/universal-battery-charger-circuit/
My last question is what is the use of the 1K resistor between pin 7 of op amp and supply voltage in this circuit? Is it to limit current?
Sounds great ina.ses, wish you all the best! Yes the 1K is for limiting current to the zener diode
sir, I want to charge my car battery 12 V 60 AH (used in my Maruti swift Dzire Diesel car). I have 15-0-15 volt 2 amp step down transformer with which after rectifying it, I can get 14V D.C., with 2 amp current using LM338. Can I use it to charge the car battery? Even if it takes longer time to charge, can I use it below the required current of 6 amp?
Hi NA, yes definitely you can do that, in fact charging at low current and for longer periods will ensure an enhanced life for the battery.
Dear Mr.Swagatham, Thanks for your prompt reply. Your article is very nice. It is like teaching in a science in school/college, very useful for electronic hobbyists like me. Keep continuing articles like this. Thanks a lot. Dr.Jayavelan
Thank you so much Dear Dr. N.A.Jayavelan, I am glad you liked my articles. Please keep up the good work.
Greetings dear Swang,
I have sought to study your topics very well, very well oriented here. But some things still have difficulties. If you can help me, I’ll be very grateful again.
I have a solar panel Power (NP): 20; Νmax (v): 17.90; Im (A): 1.24; Voc (V): 21.76; ISC (A): 1.32; Efficiency (%): 11.1; Cell Type: Polycrystalline; Number of cells per module: 36.
And 3 small of 6V / 1W.
1 PMW 12V / 10A charge controller
1 Stationary 12V / 12 Ah lead acid battery, 18 cells 1.2V NiCd, some 18650 and several 3.7V Li-ion batteries.
I do not have a power grid, but my consumption is little. Only lighting, sound and smartphone.
I would like to maximize what I have.
This custom charger circuit using the LM 338, LM 741 and BC 547 seemed to me quite versatile and fit my design given the variety of my batteries. Am I right?
* I intend to acquire more powerful solar panels
1º – As the current need would be low, can I replace the LM338 with the LM317?
2 – Can I use the LM833 (which I have in the trash) instead of the LM741?
3º – With the configuration of this circuit I could work in the range of 6V up to 12V?
4º – In this range from 6V to 12V, if possible, what would the hysteresis resistor look like? Could it replace with a variable resistor of 1K?
5 – Could R1 be a variable resistor of 1K? (I have many)
6th – A 6V relay could work with batteries in series forming 12V?
7th Later, if more current is needed, can I add a TIP42C in BYPASS?
I suppose my doubts must be tiresome to you, but to me your lessons are treasures.
Very good sir.
Thank you Dear Marcelo, for reading my articles so keenly.
Yes definitely you can use the LM338 and the op amp based circuit for your application, although it won’t give the kind of efficiency a buck converter based design would give. Nevertheless, since the design is much simpler than a buck converter, I would recommend this design.
You can use LM833, but to fix the hysteresis resistor you may require some trial and error operations. You can start with 1K, and check at what lower voltage the relay clicks back, and in this way you can increase a bit and check again, to finally set the right threshold.
LM317 can be used instead of LM338 if the battery Ah rating is less than 10 Ah.
A 6V relay can be used to charge two 6V batts in series but separately, one by one.
For more current I would recommend using LM338, because adding an an outboard transistor may required some calculations and adjustments.
Many thanks for your time dear Swag,
But my English is not very good and in the translation of google a part I do not know if I understood. In the use of 6V relay, would you have to use a relay for each 6V battery connected in series?
OK understood, you can use a single 6V relay for charging the two batteries, but it cannot be charged together, you will have to charge them one by one separately…or use a 12V relay to charge the series with 14V together.
Good morning dear Swag and thanks for the clarifications.
Still breaking his head around here. Trying to make an arrangement with what I have, what I need, and what I know.
As I know little, I need your help again.
Since I have low power panels (6v / 1w), would it be possible to connect 2 of these panels in parallel, to increase the current produced and be able to charge 5 cells of 1.2v / 1000mAh NiCd connected in series?
If so, which circuit would you recommend? I have the 555, LM317, BC547, TIP 31, 41 and 42, LM833, LM431 and some mosfets.
I thought of this circuit here, as I told you, but I do not know if it compensates in this arrangement with low power panels.
Thanks in advance for your kind help
PS. Can I use the Shottky 1N4148 diode to protect these panels?
Good Morning Marcelo,
Charging 5 cells may not be possible. Even if you add one more panel, the total wattage will be 2 watts, dividing this with 6 gives 0.33 amps, which may be just sufficient for charging 4 cells in series. At his minimal rate you won’t require any charge controller…you can just put one 1N4007 diode in series with panel and start charging the 4 cells in series….optionally you can connect an ammeter in series with the positive line to check when the meter reads zero, which will mean the cells are fully charged.
Very thankful Lighted Swag.
Your information always brings knowledge. Is the supplied amperage also divided equally into a parallel connected load?
With a panel of 6v / 3w and three of 6v / 1w each I could connect in parallel and serial respectively, without damage to them to generate 12v / 3w?
Is not the use of Schottky diodes (for less loss) a necessary protection for the panel, since its loss is less than that of silicon diodes?
Just a single diode in a serial or parallel arrangement, or one diode per panel?
Once again I thank you for your goodwill and wisdom for sharing your knowledge. May there always be light in your ways.
A big hug.
Thanks Marcel,
Yes you can connect 3 nos 6V/1 watt in parallel and connect this parallel combination in series with the 6V 3 watt panel.
Diodes hardly drop 0.7V, so if you want to save this 0.7V then you can use a Schottky diode.
For the 12V series panel, you connect just one diode with the positive line of the panel.
Wish you all the best! 🙂
Hi swag..
I have 12v 6ah and 5amp trasnformer along with lm317 set to 14.2v
How to know if the battrery is fully charged?
Thanks.
Hi Candra, limit the current to 600mA, and voltage to 14V, and keep the charger connected. Occasionally check the voltage across the battery terminals, when it reaches 14V , you can consider it almost fully charged.
thanks..
looking at your lm338 current limiter what is value for R1?
candra, you can refer to this article for the details:
https://www.homemade-circuits.com/universal-high-watt-led-current-limiter/
how to be a current variable rather than fixed?
for example from low to 3A max current
thanks.
you can change the resistor values or use a pot in its place for changing the range
Iout = Vref/R1 thats mean R1 could not be zero am I right? or is there any explanation
thanks.
yes it cannot be zero, because any conductor will have some resistance
What if R1 is removed? Or it should not be omitted? Because if i use pot at max that’s mean R1 will 0 or no resistance between out and adj?
Theoretically R1 can be never zero. As I said previously, even a shorted R1 will have some resistance, it could be in 0.00000xyz but it will have some value.
it means even if R1 is 0.00000xyz max current will around 5A?
yes that’s what we are supposed to get if there’s hardly any resistance, we’ll have the full current from the source.
ok. thanks swag
I’ve just figured it out…
Hello,
I am planning to charge a 12V lead acid battery with your circuit.
I have tried your circuit in a bread board ,but it had some problems.
First off all,what is the value of hysteris resistor i need to again start auto charging when the battery charge becomes, say 30%.??
And as shown in the above simulation the red led doesnot light up. Only the green lights up all the time.
And at what value should i set the 10k preset to charge 12V lead acid battery.?
hysteresis resistor will need to be found through trial and error by experimenting with different resistors and increasing or decreasing the values proportionately until the right cut off is achieved.
you can change the LED positions as shown in the following diagram for correct response, because IC 741 is not an efficient opamp and has a large offset voltage which may keep the green LED permanently On,
https://www.homemade-circuits.com/make-6v-4ah-automatic-battery-charger/
initially keep the 10K preset at pin#3 of the opamp to ground, switch ON input power, adjust the the LM338 pot to 14.3V, and finally next adjust the 10K preset until the green LED just lights up, this will set the upper full charge cut off.
remember to remove the green LED from the shown position and place in series with the transistor base or you can also replace it with the base zener of the transistor
sir thanks for cheering your precious time with me, but is 3amps enough for the gate of a 600v 1200 amps igbt assuming i use the tip31 and tip32 you recommended for me sir for switching the igbt on and off fast or sir can you direct me to any efficient and simple igbt gate driver for novice like me
Abioye, IGBT gates do not require high current to operate, just like mosfets they too can work with minimal current across their gate/emitter, but they are better than mosfets because they can be operated with minimal voltages also, and have lower On time resistance than mosfets
sir i have a cpu power stage that i tweak it setting to produce (+18v %-18 volt ) instead of (+12v & -12 volt) but i want the negative output to be (-9 volt ) in stead of (-18 volt) please can you kindly refer me to a circiut i to use it as a dc to dc converter for the gate driver circiut to drive igbt for electric car
And sir i think BD140 and BD139 is capable of 3 or 2amps is there any transistor that that as the similarities of BD140 and BD139 but can give up to 6 or 5amps
Abioye, may be you can try adding the following circuit, but preferably use a pot instead of the shown rotary switch
https://www.homemade-circuits.com/dual-power-supply-3v5v6v9v1215v-with/
for 2/3 amp it is better to go for TIP31/32 transistors, BD139/140 will not be able to handle that much current
thank you in advance
Hello sir swagatam , i made the circuit but when i connect my battery to the circuit it does not charging showing but voltage across battery terminal is same as applied , i did not decrease .
1. what does it mean?
2. Is my ciruit wrong ? If it is then what should it do to correct it? and
3.Iam unable increase my voltage regulator output to applied voltage
i.e.,if i apply 12v at input iam getting maximum of 7 volts output (by changing the 5k pot).
Hello Kranthi,
Please use a 10K pot, and set the output to 14V, and for this you will need an input of at least 18V.
Please do this and check the response again.
When you connect the output with your battery, the voltage must immediately drop to the battery’s existing voltage level, and then begin rising slowly as the battery charges.
and Make sure to select the current control resistor correctly.
If you are using a transformer or the input supply source with a current rating 1/10th of your battery Ah, in that case the current control stage can be eliminated….
Hello sir Swagatam,
Thank you so much for the published article. I have few questions:
I want to use the schematic to charge four 7AH batteries connected in parallel, which gives a total of 28AH.
1. How do I set R1 to match the correct output current which is about 2.8A? If I want use fixed resistor for R1, how do I make the calculation?
2. If I want use a fixed resistor for R2, how do I make the calculation in order to achieve 14.8V, which is the required voltage for charging?
3. What is the function and value of the zener diode connected to BC547?
4. Can I use LM358N as the opamp?
5. Will the two LM338 require heat sinks for the said purpose?
6. How do I calculate the value of the hysteresis resistor for the said purpose?
Anticipating your usual prompt response. Thank you sir.
Thanks Godson, for a 28 AH battery, you can set
R1 = 1.25 / 3 = 0.41 ohme, 5 watts
for R2 you can try the following software
https://www.homemade-circuits.com/lm317-lm338-lm396-calculator-software/
the zener is used to prevent leakage voltage from opamp output to get into the transistor base, instead of zener you can use a 1K resistor across base/emitter
you can use any other opamp, all will work, LM321 can also be tried
for calculating hysteresis resistor you can study the following article
https://www.homemade-circuits.com/universal-battery-charger-circuit/
Hello sir Swagatam,
Thanks a lot for the reply. Regarding using fixed resistors for R2, what will be the power rating of the resistor? What will be the power rating of the 120ohm resistor connected between the “output” and the “adjust” pins of th LM338?
Hello Godson, whenever it is not specified, it is always 1/4 watt CFR or MFR, CFR will be cheaper.
Hello sir Swagatam,
Thanks a lot for the reply. Please I would like you to help me with the following info:
1. If I want to obtain 12V from a 12V transformer based power supply, can I simply connect a 12V zener diode across the filter capacitor? I want to use it to run the cooling fan for my inverter which is rated 12V DC.
2. I need a schematic diagram of a transformerless power supply that can conveniently run an IC and can deliver between 100mA and 200mA.
Your reply will be appreciated sir.
Hello Godson,
the zener will burn and create a short circuit if the input is from a transformer because the transformer will have much higher current than the zener rating, a series resistor can be used with the supply to prevent but that would also reduce the current output to a very low level, insufficient for the fan.
the correct way would eb to use a 7812 IC, or a transformerless power supply will also work, but will not be isolated from mains and may cause fatal electric shock if touched in powered condition.
you can try the following design:
https://www.homemade-circuits.com/cheap-yet-useful-transformerless-power/
use 5uF/400V for C1, use 5 watt zener (1N5349B) for the zener, and replace the 50 ohm with a 22 ohm resistor
hi sir, help me please,
i wont to build 70 volt 100ah lead acid battrey. where is schemstic match with my charger?
thank before.
i use 5 battery serial. asumed 14volt x5 70v charger
Hi Yulianto, you can try the 4rth circuit diagram from the following article:
https://www.homemade-circuits.com/high-current-10-to-20-amp-automatic/
Hello
I would like know if is possible regulate voltage and current just with one lm317.
Example. I would like 4.2V just with 150mA.
I cant to place 2 regulator because cost project will be stay very heigh. So for me is very import know if this is possible.
Best Regards
Hi, yes that’s definitely possible, you can refer to the following article for the details:
https://www.homemade-circuits.com/how-to-make-current-controlled-12-volt/
Hello
I would like know, if I can do a charger circuit for battery lipo just with a CI LM337 with current constant.
and a AMPOP, how voltage comparator para turn off when to be 4.2V
I would like let my circuit without voltage constant because i know that only current constant the CI lM317 do this to work voltage regulator for the current.
I would like know if is possible charger battery lipo this way ?
Best Regard
congratulation for blog perfect in subject.
Hello, yes definitely you can build a Li-po battery charger using a simple LM317 circuit as shown below,
https://www.homemade-circuits.com/how-to-make-current-controlled-12-volt/
however make sure to adjust the output of the LM317 to 4.1V and not 4.2V, this will never allow your battery to become fully charged, and safeguard it from over charge.
Thank you for the answer.
Just for confirm your answer. I have a littel doubet that cause a confusion in my understand.
When you say adjust output for 4.1V, you say adjust the LM317 for this output or adjust the cut AMPOP for 4.1V.
Because always in circuit when seen in internet is build with current and voltage constant. Setuping first LM317 how constant current and second LM317 how constant voltage.
I would like eliminet the second LM317 with constant output, and let this job all to the first LM317 that control current e voltage. And who will control the cut output is AMPOP.
thank you
4.1 V should be adjusted using the LM317 preset to get a constant 4.1V out for the battery, please see the first diagram in the link which I referred, it has only a single LM317 IC based design, with a BC547 stage for the current control
please can help me with comprehensive design and construction of four level automatic battery charger incorporating a digital progress indicator that is capable of charging a 12v,24v,36v and 48volt design analysis and circuit design .
You can try the following design, however a digital indicator may not be feasible…only 4 LEDs can be incorporated for the charging steps
https://www.homemade-circuits.com/fast-battery-charger-circuit/
HI sir,
i want to ask that some other topic’s question.”To get 2amp power output can i use two lm7805 in parallel in circuit?”
Hi Abhishek , it is possible, just make sure to attach them both over a single common heatsink.
Dear Sir,
I have recently purchased 2pcs of 6V 4.5Ah SLA and 1pc of 12V 12Ah battery but currently i am not using them.
I will be using them in the near future as and when i need them.
I don't want the newly purchased batteries to self discharge, so i wish to keep them on continuous charging system i.e., 24Hrs non-stop.
What i wanted to know was how much current and at what voltage should i need to apply continuously on the batteries?
Also is a continuous charging system dangerous to the battery OR one can implement it freely without any issues?
Thanks
Hi Sherwin,
to keep the battery healthy you can keep it trickle charged using an automatic battery charger.
you can charge it at a constant current rate which may be at 1/10th of its AH rating and then float charge it with a 1/50th AH rate…. this figure is not too critical but lower current is preferred for the float charge.
Hi sir,
Your blog is very much interesting.
Sir I need some help to build CONSTANT VOLTAGE OUTPUT,
As I have 1kw alternator, It gives 0-50vdc output, but it's fluctuating & will be varied from 0 to 50vdc….I need constant voltage for battery charger, so that I can connect FAST BATTERY CHARGER CIRCUIT to that output…..Can I use LM338?………Please suggest me. Your help will be very HELPFUL.
THANK YOU
Thanks Kaustubh,
LM338 will take not more than 38V at the input, so it might not be possible to use this IC.
You can try using the following voltage regulator concept and see the response….you can reduce the number of transistors as per your amp requirement:
https://www.homemade-circuits.com/2015/03/100-amp-variable-voltage-power-supply.html