In this post I have explained a circuit which controls a submersible borewell motor by operating its red (Start) and green (Stop) buttons, in response to low level, high level water conditions, and also in a condition where the motor may experience a dry run situation. The idea was requested by Mr. Vamsi.
Automatic Start/Stop Controller for Borewell Contactor
Hi sir, i'm an electronics hobbyist and a regular viewer of ur blog , also a very big fan for U sir... 🙂 i have learned very much from YOU. and THANK YOU VERY MUCH SIR... 🙂
Sir, can u pls suggest me, i need the circuit design of fully automatic water overflow controller cum dry run protector circuit with showing level indicators.
The circuit needed for the borewell starter like generally all of the borewell starters will have a GREEN and a RED push type buttons. manually we will start up the motor by pressing the GREEN for 1sec. and 1sec. for shutting OFF as the same way, the design i need is, the controller works with Dual Relay ( 2 individual Relays) one is for starting winding.
i.e Relay1 activates for 1 sec. to START motor and the other Relay2 is to STOP the motor activates for 1 sec. respectively and the main thing is we can not drop sensors such a lengthy to the ground level of the deep wells
so, all i need is in case if there is less water in the bore well, the sensor in the OHT is connected to upper water pipe which falls in the tank,sensors should activate and energise the Relay2 which in turn shutting OFF the motor if water discharges very low. the water which discharges from the pipe will take atleast 15sec. so, it will be needed ON time delay for at least 20 sec.(relay1 activates and wait for water discharge up to mentioned time.)
Now the motor should works in these conditions:
1.when water low level in OHT, Relay1 gets energized for 1sec & switching ON the motor.
2 Relay2 should activates in two conditions: a) when water filled up in OHT activates for 1sec. shutting OFF motor , and b) when borewell DRY RUN, time delayed for at least for 20sec and activates the Relay2 for 1sec to shut OFF the motor.
The circuit need to works in 12v dc. and also if possible need a RESET push button, when the water in the OHT is suppose a half of the tank, if we need to make tank full, the motor should start by pressing RESET button.
This is my brief explanation. i tried very much for this desired circuit design. but i'm not such expert to say but i have a technical, logical and basic knowledge in this field. i hope that u understand my request. Pls do the needful Sir, Hopefully awaiting for ur valuable reply. For posting the circuit diagram, my ID : [email protected]
Thanks and Regards
Vamsi Krishna
The Design
In a couple of my earlier articles, I discussed about a similar circuit concerning a semi-automatic submersible pump controller circuit, however the design utilized an ordinary moisture sensing metal probes for the detection and activation.
The present design relies on a reed/magnet based float switch operation, which not only makes the operations easier but also a lot reliable.
The proposed submersible borewell motor starter controller circuit may be understood by referring to the following diagram:
Circuit Diagram

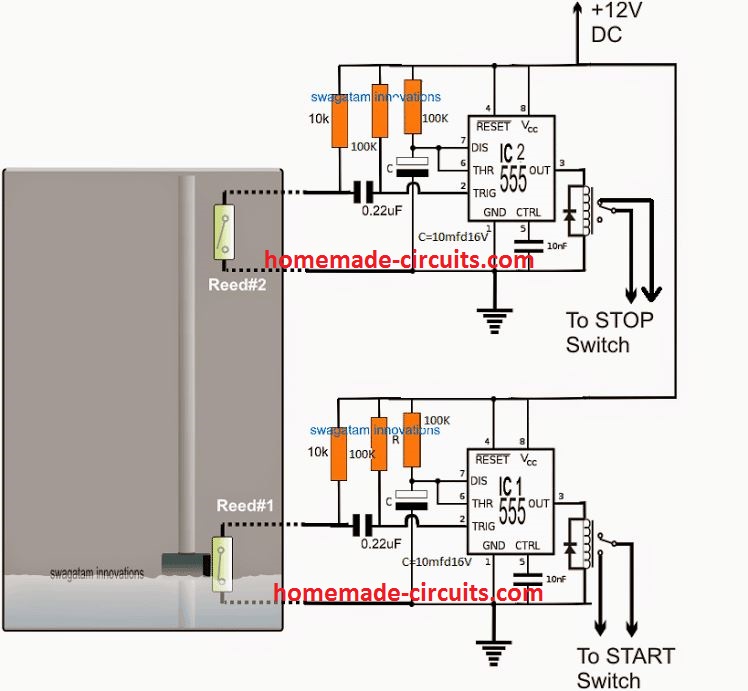
The diagram above shows a very straightforward set up using a couple of identical IC 555 monostable stages.
The IC2 stage forms the submersible pump starter circuit, while the IC2 stage is positioned to stop the pump switch.
Both the circuits work with reed switches (float switch) which may be seen positioned inside the overhead tank, one at the bottom, the other at the top of the tank.
The bottom reed closes when the water level is near the bottom threshold, and parallel to the reed switch, while the upper reed switch closes when the water level reaches at the level where its been installed.
Assuming the water level to be near the bottom reed switch, the reed switch closes, triggering the IC1 stage, which in turn momentarily clicks the associated relay.
The relay being wired across the START button of the submersible pump, the motor gets initiated and it starts pumping water to the overhead tank.
The water level in the OHT now begins rising, and when it reaches near the upper reed switch reed#2, it closes triggering the IC2 relay for a moment activating the STOP switch of the motor. The motor now stops and discontinues the pumping of water inside the OHT.
Motor Dry Run Protection
As requested, the STOP circuit also needs to be signaled in case a dry running of the motor is detected.
In the absence of water to pump, the motor may be subjected to a "dry run" situation which in turn might heat up the motor to dangerous levels.
A simple heat sensor thus can be introduced to sense the rising heat of the pump motor and signal the IC1 stage so that the STOP button is instantly activated on time and the motor is saved from burning.
A simple yet very effective heat sensor circuit may be witnessed below. It ensures the vital dry run protection for the borewell motor and also facilitates the action externally without
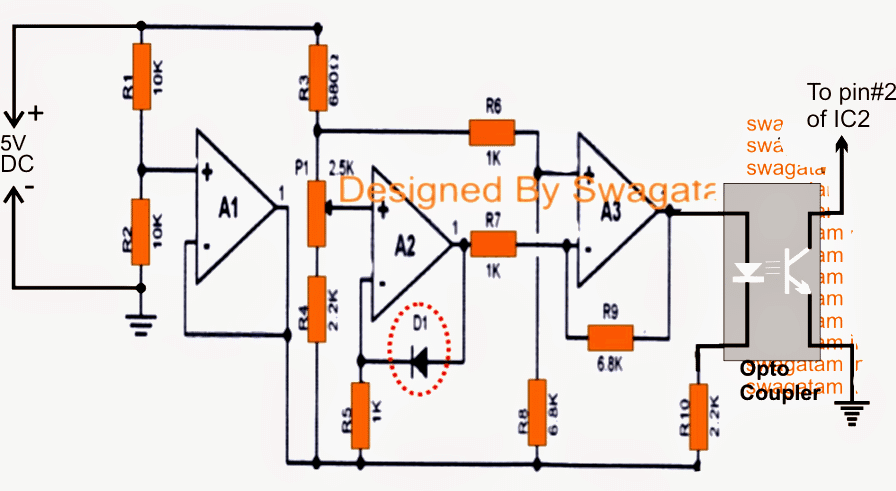
Using 3 opamps from IC LM324
The circuit is configured around three opamps (LM324 or three separate 741 ICs), where A2 forms the temperature sensor through D1.
D1 which is a 1N4148 diode is used as an effective heat sensor, and is supposed to be glued to the motor body for the sensing.
P1 is set such that when the motor tends to heat up, the output of A3 becomes high enough to trigger the opto transistor into conduction, therefore in case a motor goes through a dry run situation and begins getting hotter, D1 detects this triggering the connected opto coupler (4n35).
Now since the collector of the opto coupler is attached with the pin#2 of IC2 (STOP relay), the IC2 responds to this and quickly initiates the relay and halts the motor.
The motor gradually cools down, which causes the opto coupler too to shut down and the situation reverts to normal and in the original state.
The IC 555 based START/STOP circuit explained above was successfully built by one of the avid readers of this blog Mr. Chandan. The tested values of the R and C components as shown in the figures are for producing a 2 sec ON delay for the relevant start/stop switches. The values were suggested by Mr. Chandan.
Hi Sir I had connected only the START circuit on breadboard. At first the circuit operated fine but after 5 to 10 times movement of float switch, the relay is getting stuck in the ON position only until I disconnect the supply..
Can you please help me..
Hi Sagar, that should not happen unless your IC 555 is not working. Check the operation manually by grounding the 0.22uF end to ground, and see if the timer works correctly or not. Also replace the 100k resistor with 10k, so that the 0.22uF can discharge properly.
I would recommend building the circuit by soldering on a stripboard, and not on breadboard
Which circuit do you prefer for submersible pump Auto On/Off….?
IC 4049 based or IC 555 based…?
Which is more reliable for long term usage (maybe more than an year)..?
IC 555 is easier to make for a newcomer, so IC 555 circuit is good…both are extremely reliable.
Regarding the Dry Run Protection, is it a circuit that senses motor load or is it a sensor that is put in the motor & going down hundreds of feet into the earth. In such case additional wiresfrom the sensor to circuit would be required. Could you comment on this from a non-engineer’s view.
The dry run protection here involves the sensing of the rising temperature of the motor due to absence of water! Even if it is installed deep down, it won’t require any extra wiring. The supply of the motor itself can be used for powering this circuit and switching the motor through an associated relay.
If you wish to have the circuit over the ground, you can use current sensing circuit which is described in this article:
https://www.homemade-circuits.com/watercoffee-dispenser-motor-dry-run/
I cannot get reed switch in my local. Any other can i use in this circuit.
Hi, wonderful article, i have a similar setup in my house but its single phase and 3 hp.I tried using a single relay to start but it switches off immediately maybe a single relay cannot hold the load. The ampere rating when its switched on is around 18-20Amps. Please guide me sir.
Thanks, I am glad you liked it…your problem is not due to the 3 HP motor because I assume the relay contacts are rated at 30+ amps.
the problem is probably due to the sudden switch ON transient that's rattling the IC 555, to correct this you can increase the pin#5 capacitor to some higher value, may be at around 1uF…and additionally connect a 1000uF capacitor right across the relay coil….do these and check the response.
Thanks for your suggestion. i tried adding a capacitor(1000uF) across relay contacts and i saw a drastic voltage drop in the circuit. The leds became dim till the relay triggered and then it was fine. I'm using a micro-controller instead of a 555 timer, the micro-controller froze after the motor got switched off from the stop relay and i had to restart the mcu then tried again and faced the same problem. Please share your thoughts sir.
connect the positive pin Vcc of the MCU IC through a diode 1N4148, and connect a 220uF or any high value capacitor right across the (+)(-) pins of the IC.
Thanks for your suggestion sir. VCC pin of the mcu should connect to negative of 1n4148 and positive of 1n4148 to gnd? I have put 220uF across vcc and gnd of mcu.
yes that's correct, cathode of the 1N4148 will connect with the Vcc, anode with the supply (+), and 220uF across Vcc/GND pins of the IC
Sir should I add a snubber to relay contacts? The problem seems to occur once in a while.
Vipin, if you have implemented the above suggestion and still the problem is happening occasionally, then you can try increasing the 220uF capacitor value….a snubber might not help because a snubber is intended for suppressing relay contact sparking and RF interference and transients….it won't correct the low voltage condition due to sudden motor switch ON consumption.
in the first figure their is a resistor 1M ohm below that their a capacitor C, the value of capacitor is not indicated.
what is that value of C
the 1M and the C value determines the time for which the relays remain activated….you can calculate the values using the first software as given in the following link:
https://www.homemade-circuits.com/p/ic-555-calculator.html
Dear Swagatam, For a borewell motor driven by a microcontroller, should I be most likely using a 9 V relay or a 5 V relay. Kindly suggest. Thanks Rajesh
Hi Rajesh, you can use a 9V relay, but make sure it is operated through a separate 9V power supply
Hi, I came across your site when googling smart starters for 3 phase submersible pumps.
Found your site more informative and great.
I will be very thankful ,If you can share any info of vendor or product that send alert message to mobile when anything goes wrong in 3 phase pump starter.. Thanks .. Id- [email protected]
Hi, I think you could use the following concept for your requirement
https://www.homemade-circuits.com/2016/09/gsm-fire-sms-alert-circuit-using-arduino.html
if anything goes wrong with the motor the first thing that could happen is the motor getting hotter, and this unit will sense it quickly and inform the user regarding it in his mobile.
Brother i need a reset button for ic 555, where i want to insert in this circuit?
Brother, the above circuit is for those sub-motors which have a contactor start/stop system….the 555 are configured to actuate these start stop buttons through the relays, only for a second, and then release.
what exactly are you trying to make??
I cannot understand why you need a reset button for the 555 because the 555 IC are only momentary activation, they do not stay switched ON permanently.
Brother i need a push button switch to start the motor again when the water is empty, until it is in off condition, so where i can put the switch?
Brother, if you are referring to the above circuit, then simply remove the lower 555 section completely.
and use your motor's start button to initiate the motor whenever you wish to start it.
Hello sir is it possible to use 8051 or pic cu instead of 555 ic and use steel rod as water level sensor for 3 phase bore well submersible motor.please help.
Hello Pranab, when an ordinary IC 555 is able to accomplish the mentioned application, an MCU will easily be able to implement the same, so yes it is possible.
Hi sir. Do you have any simulation model for that. Like multisim
Hi, I do not have a simulation model for this design
Dear Swagatam,
Thank you for publishing such a useful circuit.
I have done some modifications in your circuit and achieved the 3 second timer effect which is sufficient to trigger on and off the submersible pump switch.
1. Replace 10K resistor attached to pin2 with 100K resistor
2. Value of R should be 100K
3 Value of C should be 10mfd 16 V
4. the stop relay should have wiring connection between NC and common points of relay which should be connected parallal to Manual off switch.
The modified diagram is also being sent.
https://drive.google.com/file/d/0B5sZwo7bpwR1RVVRUTNtZjVZNVk/view?usp=sharing
Thank you so much dear Chandan,
I am sure this will help the readers a lot, and all will appreciate this valuable info.
looks like the image is not in the "sharing" mode, therefore it's not opening here, please do the needful so that it becomes accessible to all.
Sir I think the C value is not 10mfd. May be it’s 10uf . I can’t find 10mfd 16v capacitors. Please cross check it once again
Sagar, 10mfd and 10uF are one and the same! You can use 10uF/16V or 25V or 63V………. any voltage level higher then 25 V will work without any issues.
Why can’t we use stainless steel probes instead of reed switches?? Is there any problem
stainless steel or any other metal will overtime develop a layer of oxide which will prevent electrical conduction and sensing…
Dear sir,
Hello again. sir, can u pls clarify my doubt, what is the min value of polarised capacitor which shown in the above circuit diagram. in the place of that capacitor, i kept 22uf 25v capacitor. is it OK…? if so, i tested by putting that capacitor. for suppose the water in the OHT falls to the lower float switch, the float switch will be in contact until the water fills a little bit higher level to the lower float. that means the time will be taken to fill the water and contact open for lower reed is minimum 2 to 3 mins. right…? according to that way. i make the reed wires in contact for 1 min. and the relay is energised for 34 sec. actually here i need for 1 sec. because we will press the motor starter button just for 1/2 sec. or 1 sec. so i tested like as the above said procedure for 2 , 3 times to count how much time relay is energising. and then i kept a 1k resistor in parallel with 10nf. then relay energises for 10 to 12 sec. again changed with 680 ohms. energising for 3sec. finally kept 100 ohms. energising for a little bit more than 1 sec. i tested with 100 ohms for some times by making reed wires in contact for 1 min. and releasing. it work very fine. and after that the ic get damaged. i found this problem through changing the ic with new once. and the new one also damaged in same way. why like this….?
The resistor 100 ohms which i connected in parallel to 10nf is wrong….?
and the capacitor value 22uf which i kept is wrong…?
this is my brief explanation. if it's wrong, can u please suggest me the solution for this. which resistor or capacitor value i should change now. thank you…
Dear Vamsi,
I could not understand your folowing statement clearly
"…the float switch will be in contact until the water fills a little bit higher level to the lower float. that means the time will be taken to fill the water and contact open for lower reed is minimum 2 to 3 mins. right…?"
, I am assuming that you are confused whether the reed closing determines the relay ON time, and the relay might remain closed as long as the reed remains closed??…no that's not how it works.
No matter how long the reed may remain closed, the relay is supposed to trigger just for a second only….you must dimension the referred resistor R and the capacitor C correctly for this to happen.
22uF will do, but select the corresponding resistor R accordingly so that it generates the 1 sec timing pulse for the relay.
please always provide space after every sentence just as I am doing, for a stress free reading.
pin#5 has absolutely no relation to the relay timing, please do not try anything random that will only make things worse.
it's so simple, just go on reducing the R/C values until it gives the 1 sec relay ON time, and vice versa…
Dear Swagatam,
I have tried making the circuit. But, the time delay ffr which the relay remains energised is only fractions of a second, consequently, an effective switching on and off is not possible. Can you suggest modifications to the circuit so that the relay remains energised for at least 2seconds.
Thanks
Dear Chandan, the relay can be made to remain ON even upto 1/2 an hour…you just have to increase the values of the concerned resistors, and/or the capacitors for altering the delay.
The resistors can be increased to mega Ohm range for this…
Dear sir,
can u pls suggest me the circuit like power ON time delay for 1min. that means when the power is off,then later if water empty in the tank,then motor will be ready for start. as soon the power reached mean while motor get starting. due to sudden inrush current i think the motor and the device may get damage.
so, the circuit i need is to work at ( INPUT 12V DC and OUTPUT the same 12V DC ).my idea is to connect it in between transformer 12v 500ma with bridge converting DC and before the water level controller INPUT.
i checked all time delay circuits which u published so many stuffs. but i think here instead of relay operation, the same INPUT power supplied OUT through TRANSISTOR is better. coz, here suppose the transformer is already feeds power to time delay circuit. and relay will ON continuously. and controller circuit relay also should function from the same transformer. so i think here transformer take much load due to both circuits.
Dear Vamsi, the following circuit can be effectively used for the delay action…the N/O relay contacts can be wired with the water level controller circuit for providing the 12V supply to it after the set delay.
https://www.homemade-circuits.com/2013/02/make-this-simple-delay-on-circuit.html
Dear sir,
THANK U VERY MUCH for the RPLY. can u suggest me, if i put the level indicator sensors along with the waterlevel controller circuit sensors in the same tank. is there any interruption occur to the both circuit…? coz, the both circuits works with 12v only.
Dear Vamsi, you can put level sensors in the same tank without problems, but it should be with reference to the common positive supply dipped in the tank water.
the code of diodes which u said here is 1N4007. is it 1N4007 or IN4007.
it's 1N4007
Dear sir,
Hello again. can u tell me the value of estimated minimal resistances of resistors R2,R5 and the minimal value of polarised capacitors C1,C2 and C3. THANKS.
Dear Vamsi,
you will have verify the values through some trial and error, I don't have the formula….may be you can try a 10k for the resistors and a 22uF/25 for the capacitors to begin with
Dear sir,
i REALLY VERY APPRECIATE and THANK YOU VERY MUCH for the HELP and the earlier response. Sir, i like to ask about here in this circuit instead of using float switch, is there any other option through modifying the circuit to use with steel probes or cable lugs as sensors..? and for the dry run protection can't we make this circuit as similar to the circuit which u have posted in ( https://www.homemade-circuits.com/2013/07/underground-water-pump-motor-dry-run.html ) coz, we can not fix the heat sensor as such deeper our bore well depth is more than 600 feet and i think it is expensive and too difficult to do. so, can u design the circuit accordingly the above requirement along with showing 4 level indicators to this circuit. if it's possible kindly i request u pls modify the needful.
THANKS & REG.
VAMSI KRISHNA
Dear Vamsi,
I'll try to design the new circuit as per your mentioned requirement, it might take a couple of days, though…
Thank you sir…:)
here the new design:
https://www.homemade-circuits.com/2015/09/automatic-submersible-pump-contactor.html
Hello sir, can i use a ups transformer to design an inverter
yes you can use it…