In this article I have explained a simple electric scooter circuit design which can be also modified to make an electric auto-rickshaw. The idea was requested by Mr. Steve.
The Circuit Request
I was lucky enough to find your blog, really amazing stuff that you've managed to design.
I'm looking for a DC to DC Step Up and Controller for Electric Scooter Motor
Input: SLA (sealed-lead-acid) Battery 12V, which is ~13.5V charged
minimum voltage - cut off at ~10.5V
Output: 60V DC motor 1000W.
Have you came across a circuit like that?
I can image it will be push-pull type, but have no idea of types of mosfets (give the wattage 80-100A), driving them, then the transformer, the core type and then diodes.
Plus the minimum voltage cut off to cap the PWM's duty cycle.
I have found some more information. The motor is 3 phase brushless with hall sensors.
There are two ways to approach it, a/ leave the existing controller in place and only do 12V to 60V step up or b/ replace the controller too.
There won't be any difference in power efficiency, the controller simply switches which phase get current based on the hall sensors. Therefore, sticking with plan a.
Thank you very much,
Steve

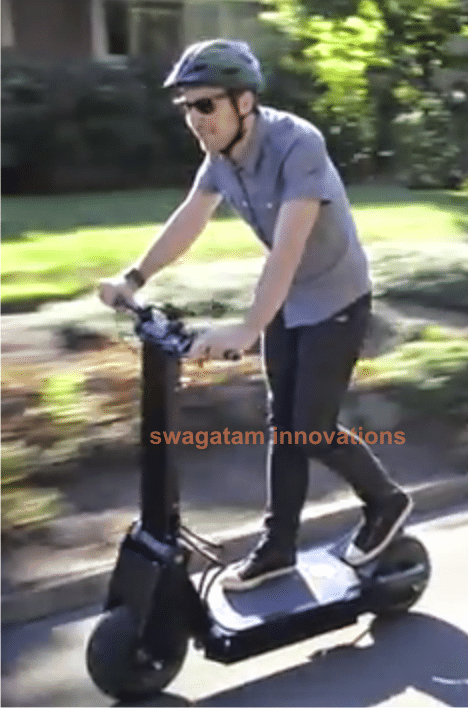
The Design
Today making an electric vehicle is much easier than it used to be earlier, and this has become possible due to two main elements in the design, namely the BLDC motors and the Li-ion or the Li-polymer batteries.
These two ultra efficient members have fundamentally allowed the concept of electric vehicles to become a reality and practically feasible.
Why BLDC Motor
The BLDC motor or the brushless motor is efficient because it's designed to run with no physical contacts except the ball bearings of the shaft.
In BLDC motors the rotor rotates solely through magnetic force making the system extremely efficient, contrary to the earlier brushed motors which had its rotors attached with the supply source through brushes, causing a lot of friction, sparking and wear and tear in the system.
Why Li-Ion Battery
On similar lines, with the advent of the much upgraded Li-ion batteries and the Lipo batteries today achieving electricity from batteries is no longer considered an inefficient concept.
Earlier we had only lead acid batteries at our disposal for all the DC back up systems which posed two major drawbacks: These counterparts needed much time to charge, possessed restricted rate of discharge, lower life, and were bulky and heavy, all these only adding to their inefficient nature of working.
Opposing to this, Li-ion, or Li-po batts are lighter, compact, quickly chargeable at high current rates and are dischargeable at any desired high current rate, these have higher run life, are SMF types, all these features making them the right candidate for applications such as electric scooters, electric rickshaws, quadcopter drones etc.
Although BLDC motors are extremely efficient, these require specialized ICs for driving their stator coils, today we have many manufacturers producing these exclusive next-generation IC modules which not only do the basic function of operating these motors, but are also specified with many advanced additional features, such as: PWM open loop control, sensor assisted closed loop control, multiple foolproof safeguards, motor reverse/forward control, braking control and a multitude of other state-of-the-art in-built features.
Using a BLDC Driver Circuit
I have already discussed one such excellent chip in my previous post, specifically designed for handling high wattage BLDC motors, it's the MC33035 IC from Motorola.
I have explained how this module may be effectively implemented for making an electric scooter or an electric rickshaw, right in your home.
I won't be discussing the mechanical details of the vehicle, rather only the electrical circuit and the wiring details of the system.
Circuit Diagram
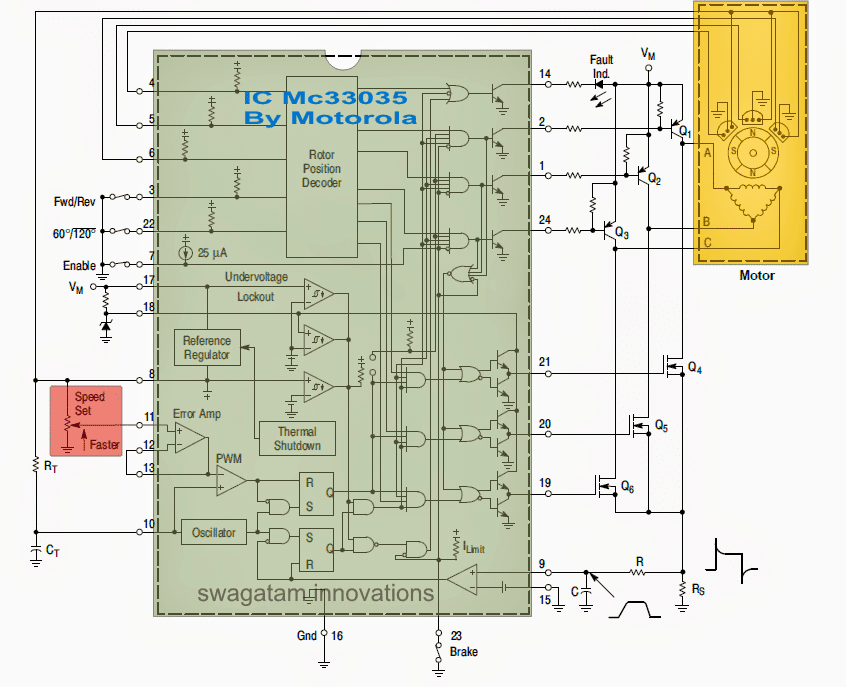
Parts List
All resistors including Rt but excluding Rs and R = 4k7, 1/4 watt
Ct = 10nF
Speed potentiometer = 10K Linear
Upper power BJTs = TIP147
Lower Mosfets = IRF540
Rs = 0.1/max stator current capacity
R = 1K
C = 0.1uF
The above figure shows a full-fledged high wattage brushless 3-phase DC motor driver IC MC33035 which becomes perfectly suitable for the proposed electric scooter or electric rickshaw application.
The device has all the basic features that may be expected to be in these vehicles, and if required the IC could be enhanced with additional advanced features through many alternative possible configurations.
The advanced features become specifically possible when the chip is configured in a closed loop mode, however the discussed application is an open loop configuration which is a more preferred configuration since it's much straightforward to configure, and yet is able to fulfill all of the required features that may be expected in a electric vehicle.
We have already discussed the pinout functions of this chip in the previous chapter, let's summarize the same and also understand how exactly the above IC may be required to be implemented for achieving the various operations involved in an electric vehicle.
How the IC Functions
The green shaded section is the MC 33035 IC itself which shows all the built-in sophisticated circuitry embedded inside the chip and what makes it so advanced with its performance.
The yellow shaded portion is the motor, which includes a 3-phase stator indicated by the three coils in the "Delta" configuration, the circular rotor indicated with the N/S poled magnets and three Hall effect sensors on the top.
The signals from the three Hall effect sensors are fed to the pin nos 4, 5, 6 of the IC for internal processing and generating the corresponding output switching sequence across the connected output power devices.
Pinout Functions adn Controls
Pinouts 2, 1 and 24 control the externally configured upper power devices while the pins 19, 20, 21 are assigned to control the complementing lower series power devices. which together control the connected BLDC automotive motor as per the various fed commands.
Since the IC is configured in an open loop mode, it's supposed to be activated and controlled using external PWM signals, whose duty cycle is supposed to determine the speed of the motor.
However this smart IC does not require an external circuit for generating the PWMs, rather it's handled by an in-built oscillator and a couple of error amp circuitry.
The Rt, and Ct components are appropriately selected for generating the frequency (20 to 30 kHz) for the PWMs, which is fed to pin#10 of the IC for further processing.
The above is done through a 5V supply voltage generated by the IC itself at pin#8, this supply is simultaneous used for feeding the Hall effect devices, it seems everything is precisely done here....nothing is wasted.
The portion shaded in red forms the speed control section of the configuration, as can be seen it's simply made using a single ordinary potentiometer....pushing it upwards increases the speed and vice versa. This is in turn made possible through the correspondingly varying PWM duty cycles across the pin#10, 11, 12, 13.
The potentiometer could be converted into an LDR/LED assembly circuit, for achieving a friction-less pedal speed control in the vehicle.
Pin#3 is for determining the forward, reverse direction of the motor rotation, or rather the scooter or the rickshaw direction. It implies that now your electric scooter or your electric rickshaw will have the facility of reversing back....just imagine a two-wheeler with a reverse facility, .....interesting?
Pin#3 can be seen with a switch, closing this switch renders the pin#3 to ground enabling a "forward" motion to the motor, while opening it causes the motor to spin in the opposite direction (pin3 has an internal pull up resistor, so opening the switch does not cause anything detrimental to the IC).
Identically, pin#22 switch selects the phase-shift signal response of the connected motor, this switch needs to be appropriately switched ON or OFF with reference to the motor specs, if a 60 degree phased motor is used then the switch needs to stay closed, and open for a 120 degree phased motor.
Pin#16 is the ground pin of the IC and needs to be connected with the battery negative line and/or the common ground line associated with the system.
Pin#17 is the Vcc, or the positive input pin, this pin needs to be connected to a supply voltage between 10V and 30V, 10V being the minimum value and 30V the maximum breakdown limit for the IC.
Pin#17 may be integrated with the "Vm" or the motor supply line if the motor supply specs matches the IC Vcc specs, otherwise pin17 could be supplied from a separate step down regulator stage.
Pin#7 is the "enable" pinout of the IC, this pin can be seen terminated to ground via a switch, for so long as it is switched ON and the pin#7 remains grounded, the motor is allowed to stay activated, when switched OFF, the motor is disabled resulting the motor to coast until finally it comes to a halt. The coasting mode may quickly come to a halt if the motor or the vehicle is under some load.
Pin#23 is assigned with the "braking" ability, and causes the motor to stop and halt almost instantly when the associated switch is opened. The motor is allowed to run normally as long as this switch is kept closed and the pin#7 is held grounded.
I would recommended to Gang-up the switch at pin#7 (enable) and pin#23 (brake) together so that these are switched with a dual action and together, this would probably help to "kill" the motor rotation effectively and collectively and also enable the motor to run with a combined signal from the two pnouts.
"Rs" forms the sense resistor responsible for checking the overload or over current conditions for the motor, under such situations. the "fault" condition is instantly triggered switching off the motor immediately and the IC going into a lock-out mode internally. The condition stays in this mode until the fault is corrected and normalcy is restored.
This concludes the detailed explanation regarding the various pinouts of the proposed electric scooter/rickshaw control module pinouts. It just needs to be correctly implemented as per the shown connection info in the diagram for successfully and safely implementing the vehicle operations.
Additionally, the IC MC33035 also includes a couple of in-built protection features such as under-volatge lockout which ensures that the vehicle is switched off if in case the IC is inhibited from the required minimum supply voltage, and also a thermal overload protection ensuring that the IC never works with over temperatures.
How to Connect the Battery (Power Supply)
As per the request, the electric vehicle is specified to work with a 60V input and the user requests for a boost converter for acquiring this higher level of voltage from a smaller 12V or a 24V battery.
However, adding a boost converter could unnecessarily make the circuit more complex and might add to a possible inefficiency. The better idea is to use 5nos of 12V batteries in series. For sufficient back up time and current for the 1000 watt motor, each battery could be rated at 25AH or more.
The wiring of the batteries may be implemented by referring to the following connection details:
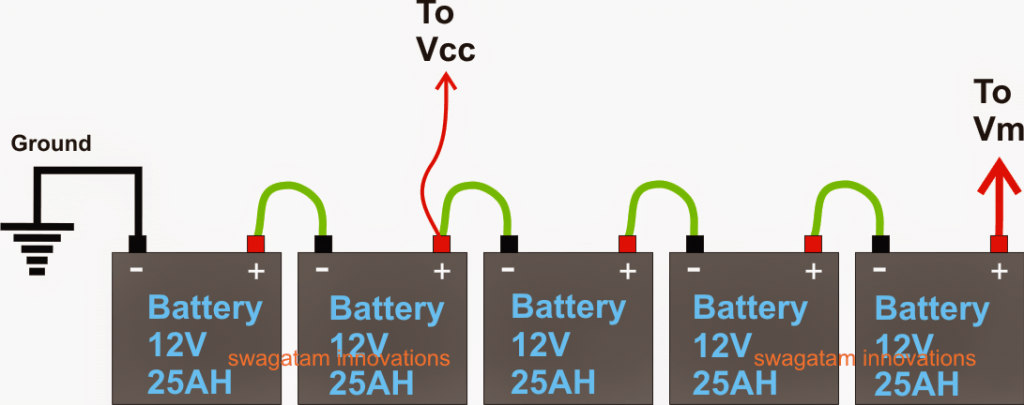
need to make up a variation of the >
https://www.homemade-circuits.com/make-this-electric-scooterrickshaw/ to make up an e-trike using 4 axial-flux sensored motors I will be building as follows:
I am making up an e-trike using 4, 250 watt, 3 phase, axial-flux motors (or perhaps 2, 500w motors since they will be connected together on the same shaft but I need to be able to disconnect 1 250w system electrically when less power is needed.) See >
https://endless-sphere.com/sphere/threads/my-homemade-bicycle-motor-version-1.30061/#p434496 <
Two axial-flux motors will be connected to each wheel to provide 500w for startup and pulling hills. When the extra power isn't needed 1 of the 250w motors for each wheel will need to be elecrally disconnected. I will need at least 1 and possibly more IC's to control the motors, preferably only 1.
👉 I need sensored, 3 phase capability,
👉 pulse width modulation,
👉 regenerative capability and 👉 if possible reverse direction capability.
The motor controller(s) need to be able to handle at least 60 volts and 250 watts for each of the 4 motor units.
I ordered some 57 amp, 100 volt mosfets and my idea is to use
the IC(s) to energize 4 circuits in order to provide enough voltage and watts to run each motor unit.
I would like to run all 4 motors using 1 IC if possible to make speed control easier.
The rear wheels will be run independently from each other, using 2 motor units per wheel on the hills and 1 motor unit per wheel on the flats which should save electricity. The motors should be synchronized to properly distribute the power.
The 4 motors will provide the 1000 maximum watts allowed in my location.
In order to qualify as an e-trike it is necessary to be able to peddle. I intend to disable the rear wheel freewheeling system so backing up and regeneration are possible and add dual freewheeling jack shafts so the pedals don't turn with the motors. The motors will be connected to the rear wheel derailer gear systems for more power if necessary. The wheels will only be connected electronicly to eliminate the necessity for a differential.
Is it possible to provide the necessary voltage and watts; the pulse width modulation; 3 phase system; and regeneration and if possible reverse direction capability using external mosfets running 4 circuits, 1 for each motor unit and if possible could you please provide the means for controlling the circuits?
Thank you for your detailed explanation,
However, unfortunately this is beyond the reach of my expertise, because this might require a very sophisticated circuitry and calculations.
You might have to refer to the existing IC datasheets which are designed specifically for these operations.
I have a electric scooter model FIEABOR 5600 watt dual motor 60volt 35amp it has 2 controller’s
controller “B” runs rear wheel has blown mosfit’s I bought new controller thru allibaba Express they sent wrong controller I need 60v 35 amp instead 60v 45amp I belive my scooter can handle the higher amp will they work on my brand of scooter mone of wires labled no wiring diagrams/schematics do you know where to purchase a wiring diagrams/schematics for my type of scooter help me
60V 45 amp controller is better than 60V 35 amp controller since it is has 10 amp more power handling capacity, so you an use the 60V 45 amp controller with the scooter motor without any issue.
Sorry, I do not have the wiring diagram of the scooter which you have specified. I am not sure where this can be purchased from.
Hello Sir…
Why IC MC33039 is to be used in such circuits as mentioned in the datasheet of MC33035.
While you did not use MC33039 in your this project sir….???
Regards….
Hello Hamid, you can use MC33039 IC also, or any other suitable BLDC driver! The main idea is to control the wheel of the vehicle through a BLDC motor
Thanks for your kind reply sir…..
HI sir i khurram shahzad from pakistan please make the (3 phase 3000waat BLDC motor control) circut and pcb make and conection componets and 1side pcb pdf file share me.
i dont understand e riksha controler.please make easy (3 phase 3000waat 60volt BLDC motor control).
just download and make this circut.i make the car but i am not afordable purchaes this controler i thankful him you make this pcb.
Hello Kurram, the BLDc circuit shown above is not difficult, you just have to purchase the IC and the other parts and then assemble them to get the results.
here’s another design that you an try
https://www.homemade-circuits.com/48v-3kv-electric-vehicle-circuit/
HI
This circuit assumes the motor coil winding is in “Delta” configuration.
Can we use this circuit for Hoverboard motors?
I believe they are in “STAR” configuration.
Possibly this is why Peter’s (initial comment) circuit blew up.
Your thoughts……
It will work for star BLDC configuration also….most BLDCs have typically star configuration.
Hi, I just tried to build this circuit and it blew up????????????.
The problem is that the components are not properly indicated and I tried to figure out but made a bomb instead of a computer. Do you mind assisting with a better design or anyone who has it figured out please assist me.
All the parts are perfectly specified in the article, and the design is by MOTOROLA. If your circuit blew then you must diagnose the fault in your circuit. Do you mean to say Motorola have designed a wrong circuit? It is a BLDC controller, and just like any other circuit this circuit must be first verified on workbench table with a proper supply.
Hello Mr Swagatam,
Please, I want to implement an e-rickshaw controller for BDC motor (24v, 4hp). Cos, in my first trial components were popping sporadically.
So, can you please suggest some a good circuit diagram for me?
Hi Sylvanus, did you try the above concept?
Alternatively you can Google for “24V BLDC driver circuit” you may come across many good pdf documents regarding this topic, which you can refer and implement for the purpose
hello there..
i want to implement e-rickshaw controller for bldc motor (48v,62 A ,850W)
so can you please suggest some ics for the same ?
hello, you can use the concept which is discussed in the above article and use it for your need…make sure to upgrade the power devices accordingly
Sir, here the ic operates on 30v max. but we are using a pair of batteries which is equal to 48v, so how can we use that 48v directly to that ic ?
Devraj, as mentioned in the article for 48V or higher supplies you may have to use a voltage regulator circuit for feeding pin#17 of the IC…you can try a TL431 based circuit for making the regulator.
https://www.homemade-circuits.com/2012/12/explaining-programmable-shunt-regulator.html
Hi swagatam thanks for the reply,could you suggest any other alternatives to the TIP36/2N2907 darlington configuration that is in single package.
thank you
Hello sir,thank you for sharing this circuit with us,i had a couple of doubts,it would be great is you could solve them:
1.Can we use IRF9540N instead of TIP147
2.Aren't almost all BLDC in star formation instead of delta,if not how will this circuit have to be modified to suit a star formation BLDC motor.
It would be great if you answered these ASAP,thank you again.
Hello, In the original datasheet BJTs are recommended so I doubt if mosfets could be replaced with them…I think you should go with BJTs instead of FETs.
for increasing the power you can try TIP36/2N2907 joined in Darlington configuration and replace with the TIP147 transistors
Sir, can you help me for pwm circuit of 0 to 5A & 0 to 30A for hho generator.
you can try this circuit:
https://www.homemade-circuits.com/2016/01/universal-variable-power-supply-circuit.html
Hi sir
can i use this from this plan for casual bicyle and what is Speed set in plan.
thanks
yes you can. speed will depend on motor specs and battery specs.
Swagatam,
I opened up the controller to see arrangements of MOSFETS.
The mosfets used are IRFB4310 which are 130A, 100V.
There are total of 15 mosfets for 3 phases! 5 for each phase !
I want to understand why 5 mosfets when one alone is sufficient to drive the motor?
I have uploaded the connection image here – postimg.org/image/as3cb8vet/
Thanks
Sachin
Sachin, looks like the upper two mosfets are in parallel, and the lower three are in parallel with each other.
And where is the load connected?
…..the parallel connections could be for tackling the switch ON high current consumption by the motor.
Swagatam,
You bring out nice things…. !
1) I want to understand what is top drive and bottom drive. Could you elaborate on this?
2) I looked into the datasheet of MC33035. It says that Top Drive Voltage max is 40V.
Top Drive Voltage (Pins 1, 2, 24) VCE(top) 40 V
Can it be used to drive motor of 48v? When batteries are fully charged, the 48v battery voltage readings are around 56v… If I connect 56v to pin14 (Vm), would it work or would it blast the IC? IC is costly, Rs.425 on RSdelivers website.. I dont want to burn it 🙂
3) I am planning to build a controller around this for Yo EXL which is 1300w continuous and 1800w peak. Is this controller IC is usable?
4) Looked into TIP147 datasheet, It has max voltage of 100v. I assume this is fine for driving 48v/60v motor. Right?
5) Collector current of TIP147 is 10A continuous, 15A peak. For driving 1300W continuous/1800w peak motor with 48v battery, the current required is around 27A continuous/37A peak. That would require 3 MOSFETs per phase(connected in series or parallel???). I am a new bee here. Please offer your suggestions on this.
Thanks
Sachin
Thanks Sachin,
for driving 3-phase motors we require high side and low side driver configuration to supply the required 3-phase signal to the motor at the specified shift angle…..it's a kind of H-bridge configuration designed for operating 3-phase loads correctly.
yes, the upper drive transistors are rated at 40V…so in order to drive higher voltage motors we could use opto coupler such 4n35 with pins1, 2, 24, this would effectively solve the issue and allow us to use virtually all kinds of motors regardless of their voltage/current specs.
according to me, this IC (with the opto-couplers) could become universally suitable for all types of BLDC motors, provided the output devices are dimensioned accordingly.
you could replace the TI147 with a Darlington combination of TIP127 and TIP36…this would allow you to drive the mentioned high wattage motors with ease.
for the mosfet you could probably use single IRF540 on each channel (adequately heatsinked) these are rated to handle 33amps at 100V
….sorry 4n35 won't work, it's too rated at 30V…you could try H11G1M
Swagatam,
I got the Mc33035 ic in hand.
The data sheet talks about using optocoupler MOC8204 for driving motors of high voltage/wattage.
Could you please provide the wiring diagram for optocoupler connectivity for all upper and lower MOSFETs?
Also, how to calculate the resistor value for overcurrent protection?
And how to calculate Rt and Ct for required max rpm?
With these info, I can immediately start testing.
Thanks,
Sachin.
Sachin,
the complete wiring detail is alerady provided in the particular diagram, in the datasheet.
you can find how the transistor leads of the opto is connected with the 1M, 4k7 and the zener diode and the fet…the LED of the opto can be seen connected a with a 1K resistor.
so this needs to be applied for all the upper three outputs for implementing the intended high voltage operation.
select the current sensing resistor Rs such that a 100mV appears across it for the desired over current value…..meaning if suppose you select 10amp as the over current limit then Rs value must be selected such that a 100mV voltage is developed across it at 10amp current
Rs = 0.001/Max current
You mean that it is one optocoupler for one mosfet pair Atop:Abottom. Right?
What is Vboost connected to pin 5 of optocoupler? What should be its value?
What is the formula for calculating Rt and Ct for a preferred maximum speed of vehicle?
In your earlier response, you asked me to use Darlington pair of TIP126 and TIP36. Could you please tell me how the connection should be?
I am troubling you a lot, and you are the source of help for me. I can do work, but i just need some right directions. Please bear with me….
Thanks
Sachin
opto coupler will be required only for the top pinouts 2, 1, and 24.
the formula for calculating Rt/Ct could be somewhere in the datasheet, you can check it out, by the way the values furnished in the above article would be generate around 20kHz frequency which you can easily alter by practically varying the Rt value and confirming the same with a frequency meter.
Darlington pair will not be required if you are using an optocoupler, as these would be replaced with FETs….for reference you can check the following article to learn how Darlington transistor are connected:
https://www.homemade-circuits.com/2014/11/48-v-inverter-circuit.html
Some Vboost is required for pin 5 on the optocoupler. There is also a circuit given in ds, fig 30. I searched for the ic given there which is MC1555. Did not find it.
Any alternatives for it?
In the h bridge, is it the top set of fets that drive forwards, or the bottom fets?
For backward movement, can same mosets be used?
-sachin
I think Vboost = Vm + 12V
I too am not sure about MC1555
the upper and the lower fets together operate the motor as per the complex sets of signals delivered by the IC.
sir, i will like to generater at list [12V—50V] DC from a coil and magnet
please ,sir help me out.
pro, you can achieve this by using any standard "555 boost circuit", but please do not anticipate any kind of free energy generation from the result…the output V x I result will be always less than the input V x I
ok,sir
look like you know what i wanted to use it for ,
i am having eletricity problem,i have got an inverter that run on 9-12V, that is why i am looking for a way to have a stable DC that i can connect to my inverter ,and my eletricity problem will be over
If you are looking for free electricity then you can install panels or wind generator set up….