In this post I have explained the construction of a 5000 watt inverter circuit which incorporates a ferrite core transformer and therefore is hugely compact than the conventional iron core counterparts.
Block Diagram

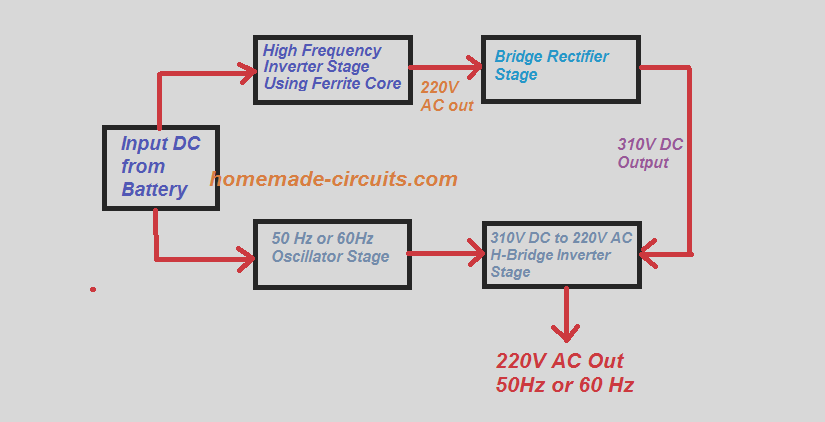
Please note you can convert this ferrite core inverter to any desired wattage, right from 100 watt to 5 kva or as per your own preference.
Understanding the above block diagram is quite simple:
The input DC which could be through a 12V, 24V or 48V battery or solar panel is applied to a ferrite based inverter, which converts it into a high frequency 220V AC output, at around 50 kHz.
But since 50 kHz frequency may not be suitable for our home appliances, we need to convert this high frequency AC into the required 50 Hz / 220V, or 120V AC / 60Hz.
This is implemented through an H-bridge inverter stage, which converts this high frequency into output into the desired 220V AC.
However, for this the H-bridge stage would need a peak value of the 220V RMS, which is around 310V DC.
This is achieved using a bridge rectifier stage, which converts the high frequency 220V into 310 V DC.
Finally, this 310 V DC bus voltage is converted back into 220 V 50 Hz using the H-bridge.
We can also see a 50 Hz oscillator stage powered by the same DC source. This oscillator is actually optional and may be required for H-bridge circuits which do not have its own oscillator. For example if we use a transistor based H-bridge then we may need this oscillator stage to operate the High and low side mosfets accordingly.
UPDATE: You may want to jump directly to the new updated "SIMPLIFIED DESIGN", near the bottom of this article, which explains a one-step technique for obtaining a transformerless 5 kva sine wave output instead of going through a complex two-step process as discussed in the concepts below:
A Simple Ferrite Cote Inverter Design
Before I have explained the 5kva version here's a simpler circuit design for the newcomers. This circuit does not employ any specialized driver IC, rather works with only n-channel MOSFETS, and a bootstrapping stage.
The complete circuit diagram can be witnessed below:
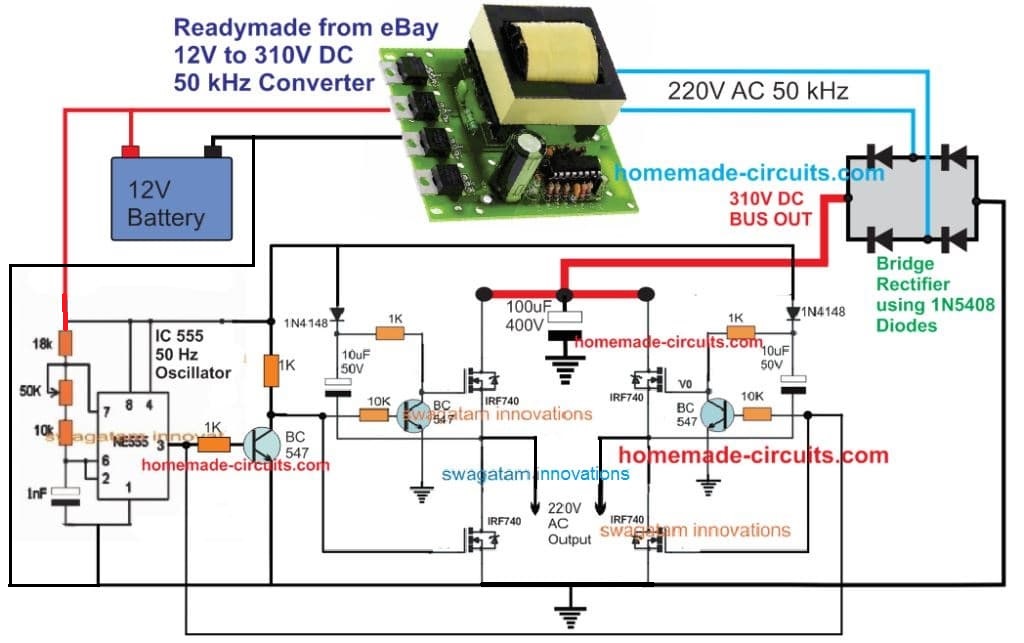
400V, 10 amp MOSFET IRF740 Specifications
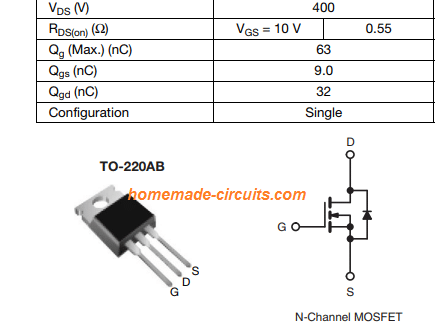
In the above simple 12V to 220V AC ferrite inverter circuit we can see a ready made 12V to 310V DC converter module being used. This means you don't have to make a complex ferrite core based transformer. For the new users this design may be very beneficial as they can quickly build this inverter without depending on any complex calculations, and ferrite core selections.
5 kva Design Prerequisites
First you need to find 60V DC power supply for powering the proposed 5kVA inverter circuit. The intention is to design a switching inverter which will convert the DC voltage of 60V to a higher 310V at a lowered current.
The topology followed in this scenario is the push-pull topology which uses transformer on the ratio of 5:18. For voltage regulation which you may need, and the current limit – they are all powered by an input voltage source. Also at the same rate, the inverter expedites the current allowed.
When it comes to an input source of 20A it is possible to get 2 – 5A. However, the peak output voltage of this 5kva inverter is around 310V.
Ferrite Transformer and Mosfet Specifications
In regard to the architecture, Tr1 transformer has 5+5 primary turns and 18 for secondary. For switching, it is possible to use 4+4 MOSFET (IXFH50N20 type (50A, 200V, 45mR, Cg = 4400pF). You are also free to use MOSFET of any voltage with Uds 200V (150V) along with least conductive resistance. The gate resistance used and its efficiency in speed and capacity must be excellent.
The Tr1 ferrite section is constructed around 15x15 mm ferrite c. The L1 inductor is designed using five iron powder rings that may be wound as wires. For inductor core and other associated parts, you can always get it from old inverters (56v/5V) and within their snubber stages.
Using a Full Bridge IC
For integrated circuit the IC IR2153 can be deployed. The outputs of the ICs could be seen buffered with BJT stages. Moreover, due to the large gate capacitance involved it is important to use the buffers in the form of power amplifier complementary pairs, a couple of of BD139 and BD140 NPN / PNP transistors do the job well.
Alternate IC can be SG3525
You may also try to use other control circuits like SG3525. Also, you can alter the voltage of the input and work in direct connection with the mains for testing purpose.
The topology used in this circuit has the facility of galvanic isolation and operating frequency is around 40 kHz. In case if you have planned to use the inverter for a small operation, you don’t cooling, but for longer operation be sure to add a cooling agent using fans or large heatsinks. Most of the power is lost at the output diodes and the Schottky voltage goes low around 0.5V.
The input 60V could be acquired by putting 5 nos of 12V batteries in series, the Ah rating of each battery must be rated at 100 Ah.
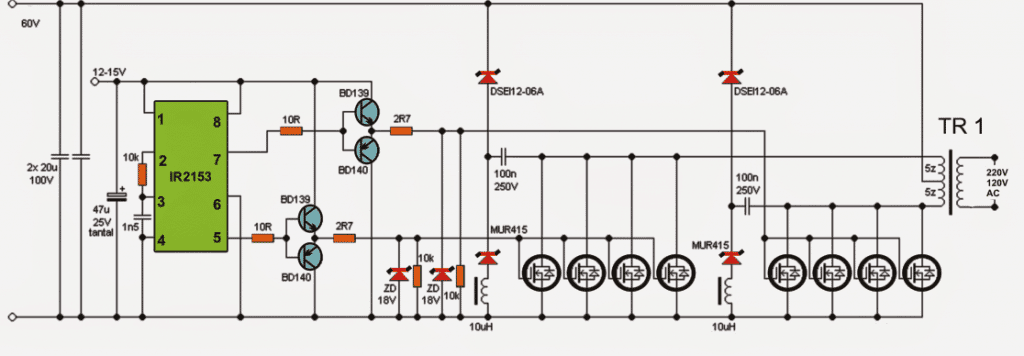
High Frequency 330V Stage
The 220V obtained at the output of TR1 in the above 5 kva inverter circuit still cannot be used for operating normal appliances since the AC content would be oscillating at the input 40 kHz frequency.For converting the above 40 kHz 220V AC into 220V 50 Hz or a 120V 60Hz AC, further stages would be required as stated below:
First the 220V 40kHz will need to be rectified/filtered through a bridge rectifier made up of fast recovery diodes rated at around 25 amps 300V and 10uF/400V capacitors.
Converting 330 V DC into 50 Hz 220 V AC
Next, this rectified voltage which would now mount up to around 310V would need to be pulsed at the required 50 or 60 Hz through another full bridge inverter circuit as shown below:
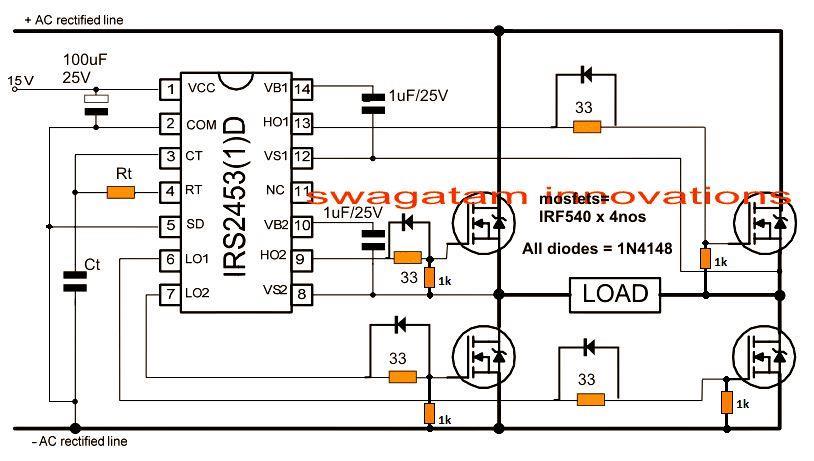
The terminals marked "load" could be now directly used as the final output for operating the desired load.
Here the mosfets could be IRF840 or any equivalent type will do.
How to Wind the Ferrite Transformer TR1
The transformer TR1 is the main device which is responsible for stepping up the voltage to 220V at 5kva, being ferrite cored based it's constructed over a couple of ferrite EE cores as detailed below:
Since the power involved is massive at around 5kvs, the E cores needs to be formidable in size, an E80 type ferrite E-core could be tried.
Remember you may have to incorporate more than 1 E core, may be 2 or 3 E-cores together, placed side by side for accomplishing the massive 5KVA power output from the assembly.
Use the largest one that may be available and wind the 5+5 turns using 10 numbers of 20 SWG super enameled copper wire, in parallel.
After 5 turns, stop the primary winding insulate the layer with an insulating tape and begin the secondary 18 turns over this 5 primary turns. Use 5 strands of 25 SWG super enameled copper in parallel for winding the secondary turns.
Once the 18 turns are complete, terminate it across the output leads of the bobbin, insulate with tape and wind the remaining 5 primary turns over it to complete the ferrite cored TR1 construction. Don't forget to join the end of the first 5 turns with the start of the top 5 turn primary winding.
E-Core Assembly Method
The following diagram gives an idea regarding how more than 1 E-core may be used for implementing the above discussed 5 KVA ferrite inverter transformer design:
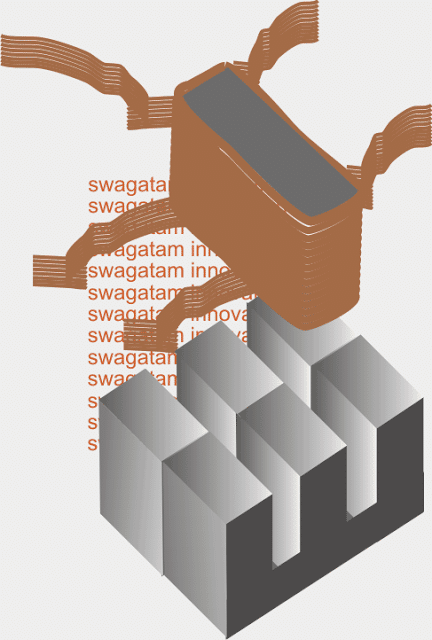
E80 Ferrite core
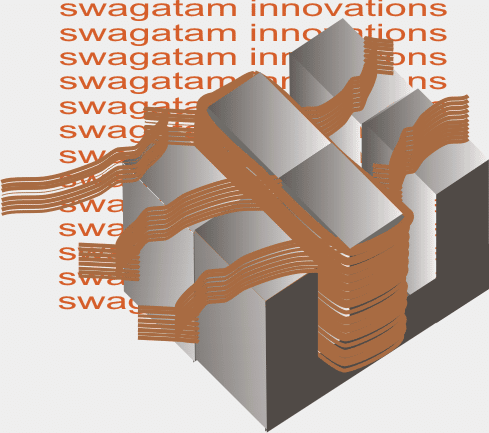
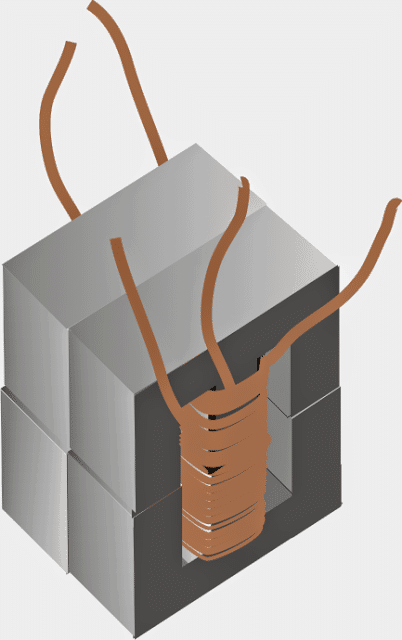
Feedback from Mr. Sherwin Baptista
Dear All,
In the above project for the transformer, i did not use any spacers between the core pieces, the circuit worked well with the trafo cool while in operation. I always preferred an EI core.
I always rewound the trafos as per my calculated data and then used them.
All the more the trafo being an EI core, separating the ferrite pieces were rather easy than doing away with an EE core.
I also tried opening EE core trafos but alas; i ended up breaking the core while separating it.
I never could open an EE core without breaking the core.
As per my findings, few things i would say in conclusion:
---Those power supplies with non-gaped core trafos worked best. (i am describing the trafo from an old atx pc power supply since i used those only. The pc power supplies do not fail that easily unless its a blown capacitor or something else.)---
---Those supplies that had trafos with thin spacers often were discolored and failed quiet early.(This i got to know by experience since till date i bought many second hand power supplies just to study them)---
---The much cheaper power supplies with brands like; CC 12v 5a, 12v 3a ACC12v 3a RPQ 12v 5a all
Such types ferrite trafos had thicker paper pieces between the cores and all failed poorly!!!---
In FINAL the EI35 core trafo worked the best(without keeping air gap) in the above project.
5kva ferrite core inverter circuit preparation details:
Step 1:
- Using 5 Sealed Lead Acid batteries of 12v 10Ah
- Total voltage = 60v Actual voltage
- = 66v fullcharge(13.2v each batt)voltage
- = 69v Trickle level charge voltage.
Step 2:
After calculation of battery voltage we have 66volts at 10 amps when full charged.
- Next comes the supply power to ic2153.
- The 2153 has a maximum of 15.6v ZENER clamp betwen Vcc and Gnd.
- So we use the famous LM317 to supply 13v regulated power to the ic.
Step 3:
The lm317 regulator has the following packages;
- LM317LZ --- 1.2-37v 100ma to-92
- LM317T --- 1.2-37v 1.5amp to-218
- LM317AHV --- 1.2-57v 1.5amp to-220
We use the lm317ahv in which 'A' is the suffix code and 'HV' is the high volt package,
since the above regulator ic can support input voltage of upto 60v and output votage of 57 volts.
Step 4:
- We cannot supply the 66v directly to the lm317ahv package sice its input is maximum of 60v.
- So we employ DIODES to drop the battery voltage to a safe voltage to power the regulator.
- We need to drop about 10v safely from the maximum input of the regulator which is 60v.
- Therefore, 60v-10v=50v
- Now the safe maximum input to the regulator from the diodes should be 50 volts.
Step 5:
- We use the regular 1n4007 diode to drop the battery voltage to 50v,
- Since being a silicon diode the voltage drop of each is about 0.7 volts.
- Now we calculate the required number of diodes we need which would buck the battery voltage to 50 volts.
- battery voltage = 66v
- calc.max input voltage to regulator chip = 50v
- So, 66-50=16v
- Now, 0.7 * ? = 16v
- We divide 16 by 0.7 which is 22.8 i.e., 23.
- So we need to incorporate about 23 diodes since the total drop from these amounts to 16.1v
- Now, the calculated safe input voltage to the regulator is 66v - 16.1v which is 49.9v appxm. 50v
Step 6:
- We supply the 50v to the regulator chip and adjust the output to 13v.
- For more protection, we use ferrite beads to cancel out any unwanted noise on the output voltage.
- The regulator should be mounted on an appopriate sized heatsink in order to keep it cool.
- The tantalum capacitor connected to the 2153 is an important capacitor that makes sure ic gets a smooth dc from the regulator.
- Its value can be reduced from 47uf to 1uf 25v safely.
Step 7:
- Rest of the circuit gets 66volts and the high current carrying points in the circuit should be wired with heavy guage wires.
- For the transformer its primary should be 5+5 turns and secondary 20 turns.
- The frequency of the 2153 should be set at 60KHz.
Step 8:
The High frequency ac to low frequency ac converter circuit using the irs2453d chip should be wired appropriately as shown in the diagram.
Finally completed.
Making a PWM Version
The following posting discusses another version of a 5kva PWM sinewave inverter circuit using compact ferrite core transformer. The idea was requested by Mr. Javeed.
Technical Specifications
Dear sir, would you please modify its output with PWM source and facilitate to make use such an inexpensive and economical design to World wide needy people like us? Hope You will consider my request. Thanking you.Your affectionate reader.
The Design
In the earlier post I introduced a ferrite core based 5kva inverter circuit, but since it is a square wave inverter it cannot be used with the various electronic equipment, and therefore its application may be restricted to only with the resistive loads.
However, the same design could be converted into a PWM equivalent sine wave inverter by injecting a PWM feed into the low side mosfets as shown in the following diagram:
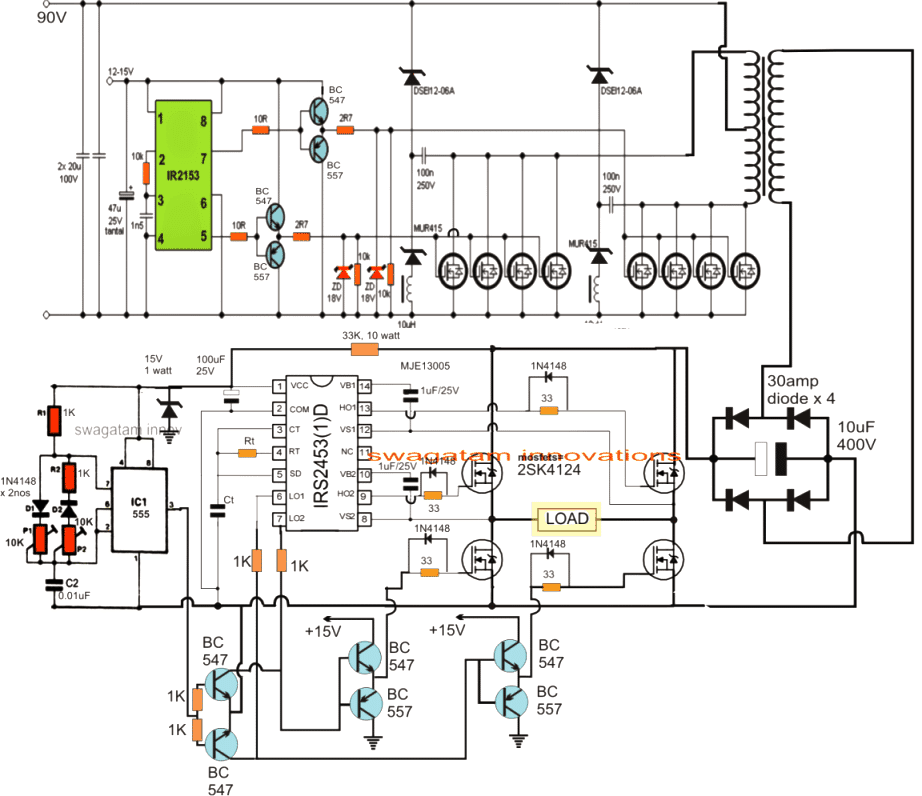
The SD pin of IC IRS2153 is mistakenly shown connected with Ct, please be sure to connect it with the ground line.
Suggestion: the IRS2153 stage could be easily replaced with IC 4047 stage, in case the IRS2153 seems difficult to obtain.
As we can see in the above PWM based 5kva Inverter circuit, the design is exactly similar to our earlier original 5kva inverter circuit, except the indicated PWM buffer feed stage with the low side mosfets of the H-bridge driver stage.
The PWM feed insertion could be acquired through any standard PWM generator circuit using IC 555 or by using transistorized astable multivibrator.
For more accurate PWM replication, one can also opt for a Bubba oscilator PWM generator for sourcing the PWM with the above shown 5kva sinewave inverter design.
The construction procedures for the above design is not different to the original design, the only difference being the integration of the BC547/BC557 BJT buffer stages with the low side mosfets of the full bridge IC stage and the PWM feed into it.
Another Compact Design
A little inspection proves that actually the upper stage does not need to be so complex.
The 310V DC generator circuit could be build using any other alternate oscillator based circuit. An example design is shown below where a half bridge IC IR2155 is employed as the oscillator in a push pull manner.
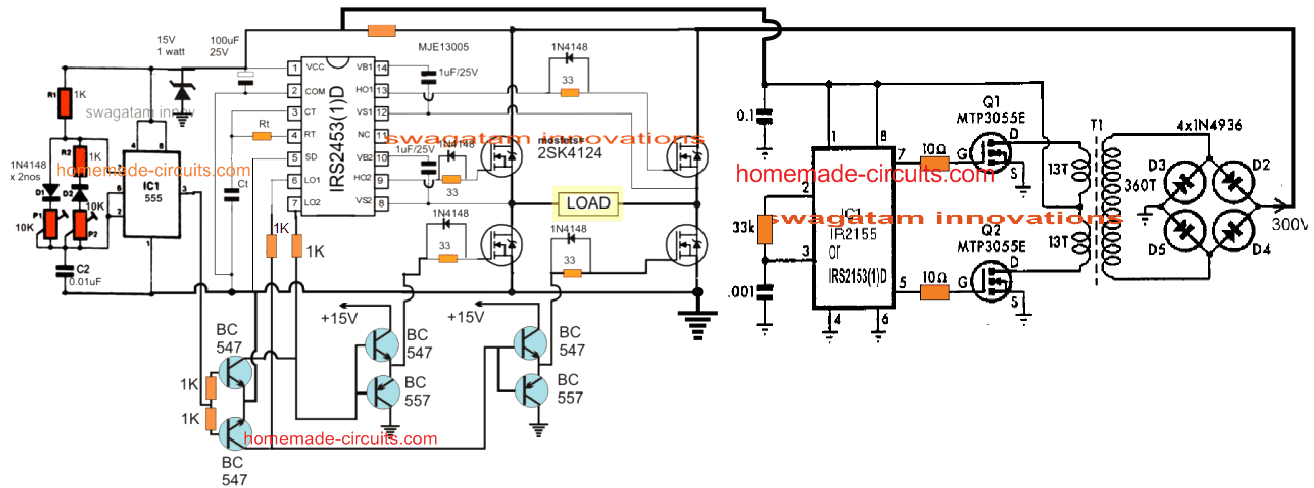
Again, there's no specific design that may be necessary for the 310V generator stage, you can try any other alternative as per your preference, some common examples being, IC 4047, IC 555, TL494, LM567 etc.
Inductor Details for the above 310V to 220V Ferrite Transformer
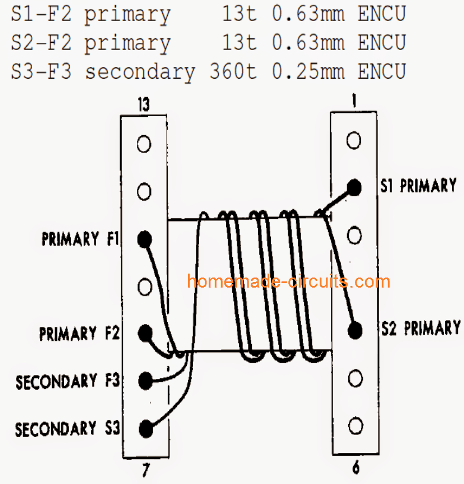
Simplified Design
In the above designs so far we have discussed a rather complex transformerless inverter which involved two elaborate steps for getting the final AC mains output. In these steps the battery DC is first needed to be transformed into a 310 V DC through a ferrite core inverter, and then the 310 VDC has to be switched back to 220 V RMS through a 50 Hz full bridge network.
As suggested by one of the avid readers in the comment section (Mr. Ankur), the two-step process is an overkill and is simply not required. Instead, the ferrite core section can itself be modified suitably for getting the required 220 V AC sine wave, and the full bridge MOSFET section can eb eliminated.
The following image shows a simple set up for executing the above explained technique:
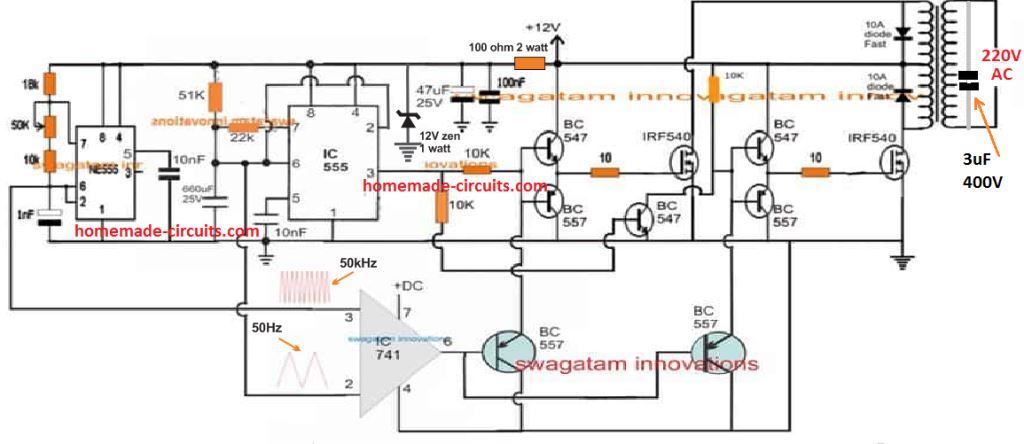
In the above design, the right side IC 555 is wired to generate a 50 Hz basic oscillatory signals for the MOSFET switching. We can also see an op amp stage, in which this signal is extracted from the ICs RC timing network in the form of 50 Hz triangle waves and fed to one of its inputs to compare the signal with a fast triangle wave signals from another IC 555 astable circuit. This fast triangle waves can have a frequency of anywhere between 50 kHz to 100 kHz.
The op amp compares the two signals to generate a sine wave equivalent modulated SPWM frequency. This modulated SPWM is fed to the bases of the driver BJTs for switching the MOSFETs at 50 kHz SPWM rate, modulated at 50 Hz.
The MOSFEts in turn, switch the attached ferrite core transformer with the same SPWM modulated frequency to generate the intended pure sinewave output at the secondary of the transformer.
Due to the high frequency switching, this sine wave may be full of unwanted harmonics, which is filtered and smoothed through a 3 uF/400 V capacitor to obtain a reasonably clean AC sine wave output with the desired wattage, depending on the transformer and the battery power specs.
The right side IC 555 which generates the 50 Hz carrier signals can be replaced by any other favorable oscillator IC such as IC 4047 etc
Ferrite Core Inverter Design using Transistor Astable Circuit
The following concept shows how a simple ferrite cored inverter could be built using a couple of ordinary transistor based astable circuit, and a ferrite transformer.
This idea was requested by a few of the dedicated followers of this blog, namely Mr. Rashid, Mr, Sandeep and also by a few more readers.
Circuit Concept
Initially I could not figure out the theory behind these compact inverters which completely eliminated the bulky iron core transformers.
However after some thinking it seems I have succeeded in discovering the very simple principle associated with the functioning of such inverters.
Lately the Chinese compact type inverters have become pretty famous just because of their compact and sleek sizes which make them outstandingly light weight and yet hugely efficient with their power output specs.
Initially I thought the concept to be unfeasible, because according to me the use of tiny ferrite transformers for low frequency inverter application appeared highly impossible.
Inverters for domestic use requires 50/60 Hz and for implementing ferrite transformer we would require very high frequencies, so the idea looked highly complicated.
After some thinking I was amazed and happy to discover a simple idea for implementing the design. Its all about converting the battery voltage to 220 or 120 mains voltage at very high frequency, and switching the output to 50/60 HZ using an push-pull mosfet stage.
How it Works
Looking at the figure we can simply witness and figure out the whole idea. Here the battery voltage is first converted to high frequency PWM pulses.
These pulses are dumped into a step up ferrite transformer having the required appropriate rating. The pulses are applied using a mosfet so that the battery current can be utilized optimally.
The ferrite transformer steps up the voltage to 220V at it output. However since this voltage has a frequency of around 60 to 100kHz, cannot be directly used for operating the domestic appliances and therefore needs further processing.
In the next step this voltage is rectified, filtered and converted to 220V DC. This high voltage DC is finally switched to 50 Hz frequency so that it may be used for operating the household appliances.
Kindly note that though the circuit has been exclusively designed by me, it hasn't been tested practically, make it at your own risk and on;y if you have sufficient confidence over the given explanations.
Circuit Diagram
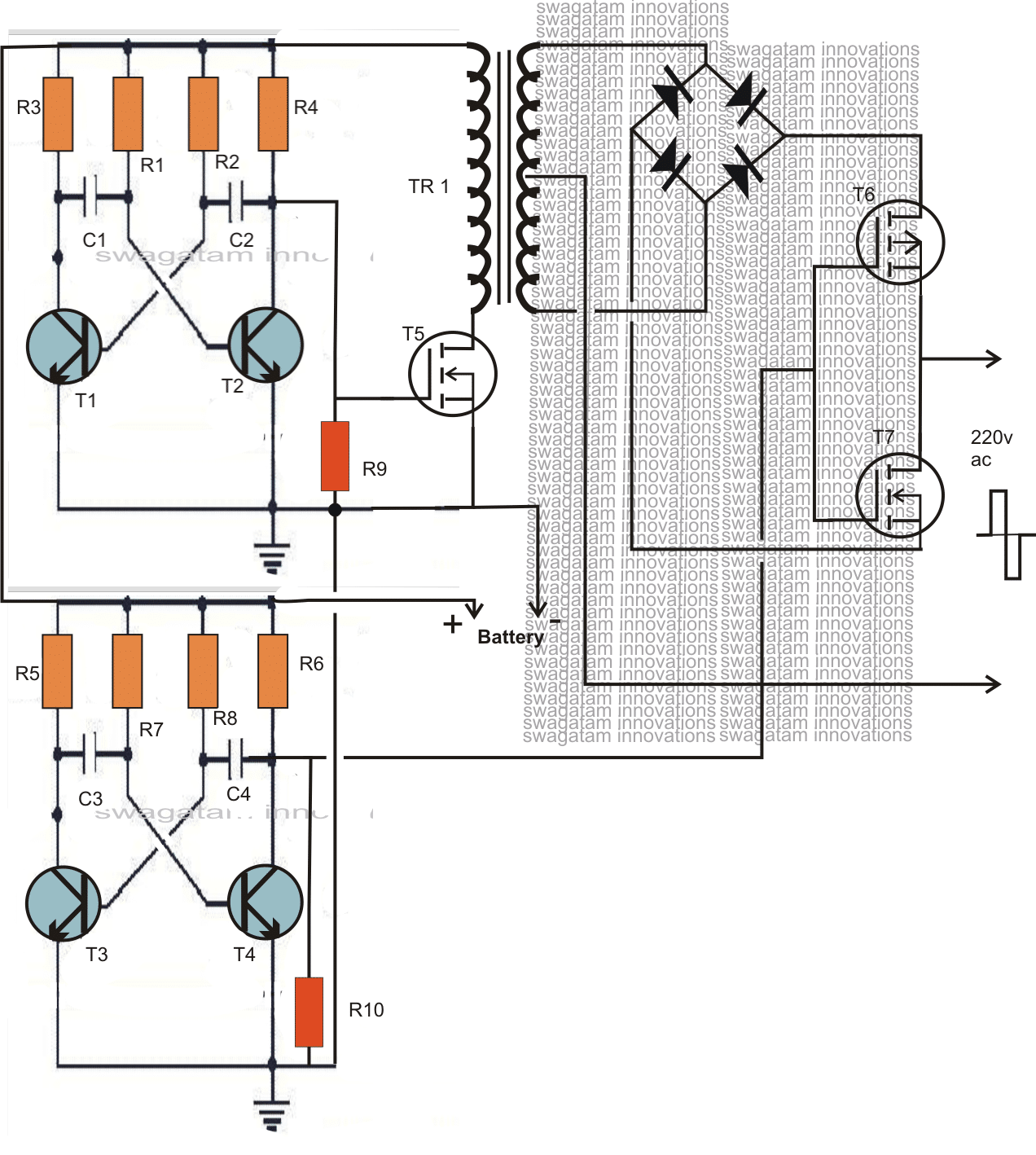
Parts List for 12V DC to 220V AC compact ferrite core inverter circuit.
- R3---R6 = 470 Ohms
- R9, R10 = 10K,
- R1,R2,C1,C2 = calculate to generate 100kHz freq.
- R7,R8 = 27K
- C3, C4 = 0.47uF
- T1----T4 = BC547,
- T5 = any 30V 20Amp N-channel mosfet,
- T6, T7 = any, 400V, 3 amp mosfet.
- Diodes = fast recovery, high speed type.
- TR1 = primary, 13V, 10amp, secondary = 250-0-250, 3amp. E-core ferrite transformer....ask an expert winder and transformer designer for help.
An improved version of the above design is shown below. The output stage here is optimized for better response and more power.
Improved Version
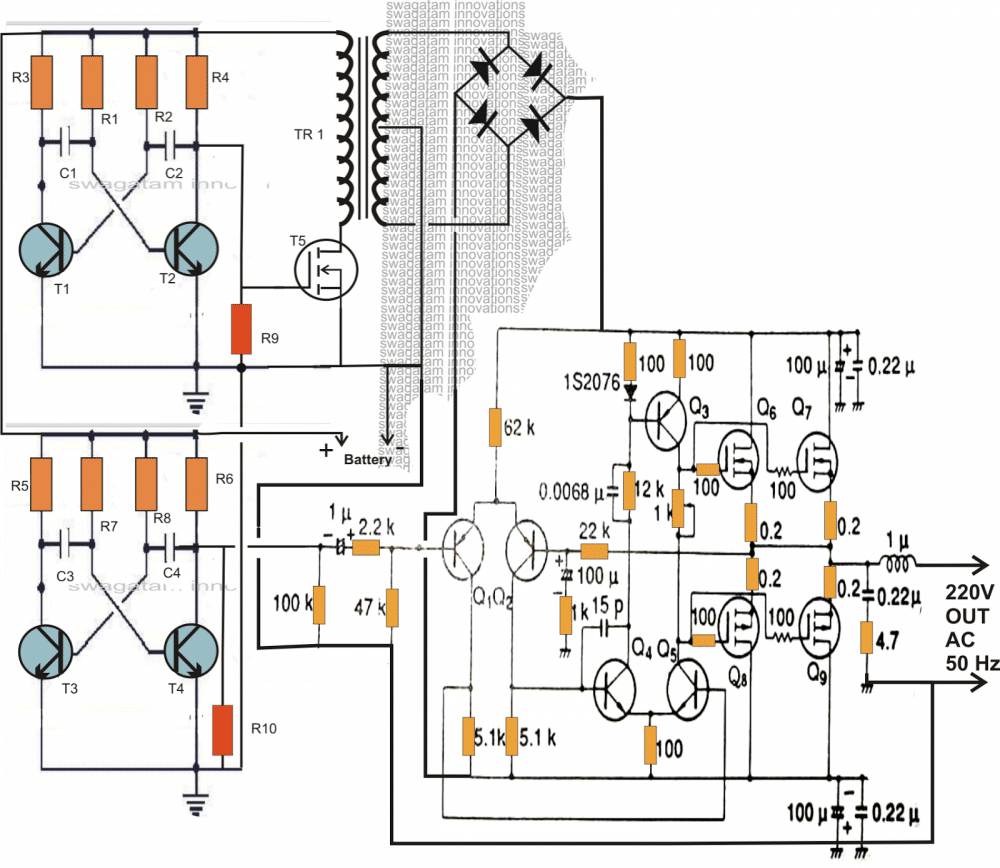
sir pls can I use a toroidal ferrite transformer for this inverter?I have few of them laying around may b I can put them to use
Hi Abubakar,
Yes, you can use any ferrite type core for this project…
hello swagatam, nice work you’re doing here. but most of the Ic’s you used here are not available here. do you have a much more simplier desgn? and secondly i’m still still new in this high frequency ferrite core inverter, and what i have available is a 12vdc do you have a design for 12vdc battery?
Thank you Christopher, I appreciate your kind words.
The first design is the simplest one you can have. It may not be possible to create a simpler design that the first concept…
The first design uses a readymade converter module so the ferrite transformer does not need to be built by you…
Hi Swagatam, thanks for your response. I’ve got every other thing here for the first design except the reaadymade converter module. Can’t I build the converter module or something similar to it myself? if yes, please give me a guide or link to one that will be compatible with first design.
secondly, how many watt does this your first design deliver?
thirdly, what waveform does it produce at the 220vac output? can this be used with loads like fans etc?
please I’m still new to this type of design , so forgive my plenty questions.
thank you.
Hi Christopher,
I understand your problem, but unfortunately it may not be possible to build the top converter circuit for you or any newcomer because of the presence of the ferrite core transformer, which requires high expertise to build and optimize the winding and the core.
The first design is only a basic concept which can be upgraded to any required power level just by modifying the converter power output, battery and the number of MOSFETs in parallel.
It is a square wave design, fan will humming noise with this design.
thank you for your explanation and response. actually, I’m a bit familiar with winding the ferrite core transformers. I’ve got a couple of EE’s and ED core types that I can rewind.. it’s just that I had never thought I’d be interested in building a ferrite core inverter until now. So if there’s any circuit to replace the reaadymade converter module, I’ll really appreciate, as that is the main challenge i have now. Thank you Swag 😎
I completely understand Chris, that you want to build the transformer yourself, and you have some experience in this field, but winding a ferrite transformer requires elaborate calculations. If you can do those calculations then you can certainly rewind one using the available data, as suggested in the following article:
https://www.homemade-circuits.com/how-to-design-and-calculate-ferrite-core-transformers-for-inverters/
Thanks for responding so far. since the issue of the ferrite core transformer has been settled. how about the circuit diagram for the 12vdc to 310vdc converter?
Sure, here is an article which you can refer to for building a boost converter from the scratch:
https://www.homemade-circuits.com/how-to-make-simple-boost-converter-circuits/
Sir how Irs2453 voltage feeback work I can’t fine vb pin
Hello Islahuddin,
To add a feedback voltage control to Irs2453 IC, you will need to configure either its CT pin or the SD pin with the feedback transistor or the opamp…..the Vb pin is not required.
Good day sir
I love your work, please how can I get the GERBER PCB FILE OF THE PROJECT
THANKS
Thank you Russell, however, sorry I do not have the GERBER files for this project. I would rather suggest you to try the project on a strip-board first, and test the results, before designing a PCB.
Hello Mr Swagatam how much would it cost to order components from your country to Maseru Lesotho. Most of the components I need to build my projects are not available in my country.
Hi Poloko, sorry, I have no idea how much it would cost to procure parts from India to your country, you may have to inquire this with the part supplier.
Hi there! That is a very interesting circuit that I intend to try soon after locating the elusive high power, adequately sized ferrite transformer. Here clarity is not given for winding the transformer for running the unit off 24v (2X12/150A, a very common battery combination in many households.) as this info wasn’t available although it was suggested. One suggestion worth examining is that you’ve used a high wattage resistor to create 15v to power the low voltage section from high voltage Dc. A more elegant solution is to use a common 12v wall adaptor that are used in many applications can be taken apart and the Hi voltage Dc can be connected across the Hv Filter cap that is on the unit. The 12v Dc output can now be connected instead of the previous arrangement although 15v is suggested I feel it should be satisfactory or a 15v adaptor could be used. This is more efficient and will give out much less heat also.
Hi, thanks for the feedback!
A 24V DC would call for a huge amount of current from the transformer and the battery. To be precise we would need around 5000/24 = 208 amps, that is why 60V source is selected to minimize the current spec as far as possible.
The article provides the transformer details for a 60 V ferrite transformer.
Yes, the 12V or 15V DC can be obtained from an SMPS source or from a buck converter circuit such as the following design:
https://www.homemade-circuits.com/simple-220v-smps-buck-converter-circuit/
Hello how r u
I want to know that transformerless 5 kva circuit will work satisfy or just for ..
It will work satisfactorily if you build it correctly.
Block diagram and its function
Thank you very much for the kind information, appreciate it.
Hi Seagatam,,,I built a tl494 circuit,,,I made use of z44,,,,,but they keep getting hot with or without load
Hi Md, read the following article, and try implementing them as required:
https://www.homemade-circuits.com/mosfet-protection-basics-explained-is/
IN IRS2453 CIRCUIT FOR 50HZ WHAT IS RT AND CT
Rt is the timing resistor and Ct is the timing capacitor, these parts determine the output frequency.
Rt,100k ρυθμιζόμενο ct100n ,όλα εντάξει αλλά τα ,hz παρά πολλά.
Your detailed step by step teaching is awesome and simply top notch! Keep up the good work!
I will need your advice on two things
1. Need to purchase a low power variable single phase high frequency AC supply. Can you recommend one for me please?
2. I need already built inverters with the high frequency intermediate state as shown in your design. I need your recommendation please.
Kind Regards
Hi, Thank you and Glad you liked the post!
Sorry to say this, but since I have not used any readymade VFD or inverter so suggesting a specific brand may not be possible for me.
Thanks very much Swagatam. I really do appreciate your sacrifice of time. Please I will need your support to deliver on this project. even if it is for a fee. You have my email address, do message me privately please.
You are welcome Achor! I above circuit is recommended only for the experts in electronics, not for the newcomers. If yu are well versed with electronic circuits and ferrite inverters then you can try this circuit.
Thanks very much. With respect to the 5Kva system , on no load condition, please what amount of power loss do we incur on the ferrite core with the high frequency(50-100khz) input supply?
I am not exactly sure about it, but the efficiency should be around 90% for the above designs without a load or with load.
OK, thanks very much. That gives one an idea of the power loss.
Kind Regards
No problem!
Thanks a lot Swagatam for your good works. I’ll appreciate if you can give me a circuit to convert my 110 VAC 5kva Colman inverter to 220 VAC. And I’ll also like to get a circuit design for 12 VDC car battery charger. Thanks once again.
phanyessence@gmail.com
Thank you Epiphany,
You will need an external 100V to 220V transformer for converting your 110V to 220V.
For the battery charger you can investigate the circuits provided in the following articles:
https://www.homemade-circuits.com/opamp-low-high-battery-charger/
https://www.homemade-circuits.com/high-current-10-to-20-amp-automatic/
Good details…i like your work..I am interested in making an altenator using microwave transformers iron core,by welding them in multiple together to form three octagons from those cores and join them together, then winding as many turn of copper as possible to produce lets assume around 310v with frequency higher than 50/60hz as the rpm of neodymium magnet inside the core shall be aim high to increase the output….then rectify it to high Vdc…and then inverting it to 220v ac at 50hz…Asking for any assistance and guidance to best approach ….thanks
Thank you for your question. Please let me know what help exactly you need from me, if it is possible I will surely try to solve it for you.
Swagatan, well-done and thank you for your services and contributions to the spread of knowledge in electronics. I was designing a 3KVA inverter using SG3524 as PWM pulse generator and 2N7000 for the driver stage. I discovered that the biasing resistor one side of the driver stage was always getting hot. Initially I used 1/4watt resistor and later changed it to1/2watt resistor but the result was still the same. Kindly advise me on what to do. Thank you.
Thank you Oyekan,
That is very strange because 2N7000 is a MOSFET and MOSFETs have a high gate impedance, which means the bias resistor connected with the gate have negligible flow of current through it.
It seems your MOSfET is burned or faulty, otherwise the gate should provide a high impedance to the resistor and it shouldn’t become hot under any circumstances.
Try replacing the MOSFET with some other mosfet and check the response.
a narrow width and a large width when passed through photochromic retainers, while passing through ferritic transformers do not retain the essence, so the project using ferrite transformers will not be successful because when smoothing it doesn’t produce a sine wave
đã ai thử thành công biến tần ferít chuyền trực tiếp sin pwm qua biến áp sung ra 220v sin cho mình tham khảo với. Mình đang muốn áp dụng đối với biến tần hòa lưới.xin chân thành cám ơn
bạn có thể chạy giả lập mạch biến tần ferit xem có hoạt động được không. dang tín hiệu sau khi làm mịn có thành sóng sin thuần túy không cám ơn bạn nhiều mọi người rất quan tâm điều này
Can you design a grid-tied inverter using arduino, won’t it help people to make their own small-capacity grid-tied inverter at a reasonable price, thank you very much
Sorry, My Arduino knowledge is not good, so it won’t be possible for me to provide the mentioned design
Can you tell me if the inverter uses a ferrite transformer to produce a sine modulation using a 3 mf loc capacitor to flatten out to 50hz is it possible. I can apply this to the grid-tied inverter IC 555 on the right, replace it with 50hz of grid power, ic 555 on the left, create 50khz and mix with 50hz to produce sine pwm to put into load-coupled power through the ferrite transformer
No, none of the above circuits uses a capacitor to flatten the 50 Hz….but if you want you can try it.
mình thấy có mạch này " rel="ugc">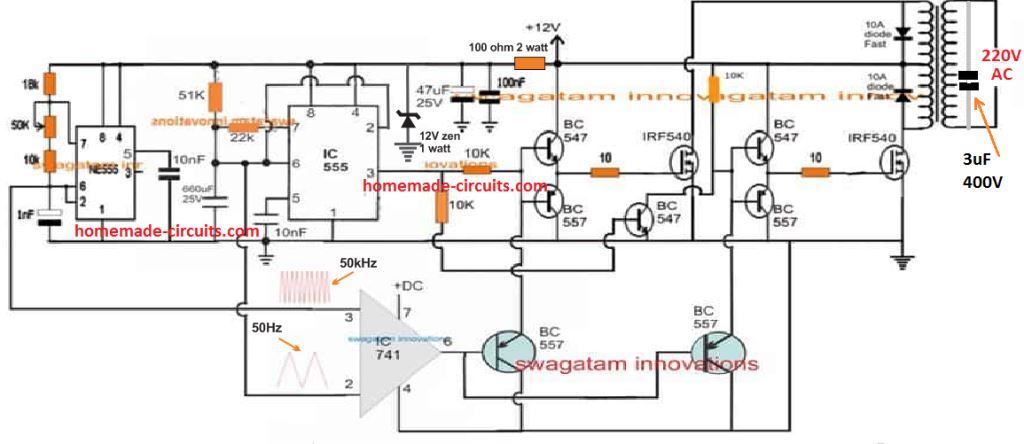
It is supposed to be a pure sine wave inverter, therefore the output capacitor is placed to smooth the SPWM into pure sine wave.
I made a post but I did not see it, anyway I have a different perception. I need some insight on the following design. I plan to connect 12, 48v solar panels in series which is 576VDC max. Therefore, I want to design an inverter with 600v input. A pure sine wave might not be that important because it will only be feeding resistive loads. Meaning water heaters, hot plates, solder irons, stoves etc. I can convert the AC output to my desire. I can place a sensing circuit to turn off when the power drops certain value. I will not use a battery backup, therefore, this is a standalone unit. It should shut off or turn on as the power drops to a certain threshold or when the sun rises the the next day. If 2, 300v inverters are better with 6 panels in series, please recommend that design.
Since resistive load is involved you can drive them easily DC supply also, why do you need an AC inverter? If you connect the 576V DC to the load they would still operate.
Thank you for your reply. Can you explain how can I connect the 576VDC to a hot water heater that uses 240VAC. I will connect 6 panels each in series, therefore, I will have two 288VDC and 8amps per phase. I am afraid that is too high for equipment that uses 120VAC per phase. I believe that I will not need a voltage sensing circuit, because the equipment will cool down when the power drops. Do you think that a restive load with low voltage or low current can harm a circuit. A circuit that reduces the voltage to a manageable level is the only device I might need.
You can reduce the number of series solar panels so that the DC becomes around 260 V for the heater. You can make some arrangement through which you can quickly adjust the number of panels in series or parallel to suit a particular device.
To reduce voltage you can try adding the following simple shunt regulator circuit
" rel="ugc">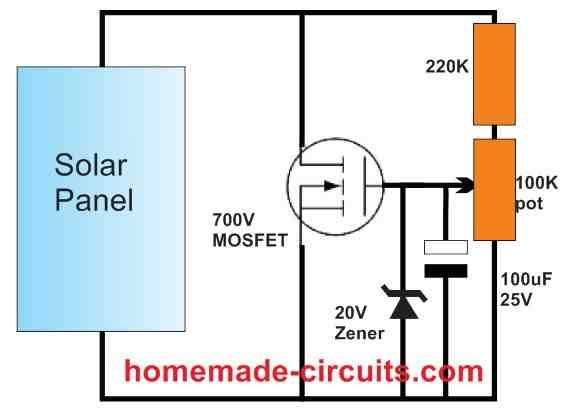
Thanks a million my brother, I finally have a plan to provide free energy to my relatives. In a couple of years, I plan to install an inverter to provide a clean sine wave. I will observe how this system work before I do any changes, anyway from me and my relatives, we appreciate your expertise.
I am glad you found my suggestions useful. I wish you all the best with your project!
I tested it with a 3-phase H-bridge because the motor is 3-phase AC . I will test next week with a single phase H-bridge . It would be great if I got +/- 12 V, ie V (p-p) = 24V from DC 12 V, I would basically have a voltage doubling. I am interested in getting 400 V DC from 100 V DC, so 2 H-bridge and filtering rectifier circuits would be enough, which is much simpler than that transformer. I want to thank you for your time and I will let you know the progress of the tests next week. Have a wonderful day !
For a 3 phase driver the case is different, and it will require 620 V peak as suggested by you in your earlier comments. It is because normally we use 440V RMS for a 3 phase load.
Presently I cannot figure out how 400V can be achieved from a 100V supply through a H bridge circuits…let’s hope it works.
I wish you all the best!
Congratulations on your impressive work ! However, after 7 years since you published the project, someone tells you that you made wrong calculations, it seems that no one has practically made this design. From the 310 V DC voltage you cannot get an AC voltage of 220 V but only 110 V with the H-bridge. You need 620 V DC to get 220 V AC. You can get 620 V DC from 220 V AC with a simple scheme with 2 diodes and 2 capacitors. If I manage to make the transformer, I want to make the part of 330V DC .
P.S. The same error is true for other H-bridge inverter schemes.
Congratulations, you are partially correct. For a square wave generator the output will be 115V from a 310V DC but if the H bridge is SPWM sine wave, then the output will be 220V from 310V DC
Actually NO….the AC output for a square wave will be equal to its peak value….in H bridge for a 310V DC, the output will also be 310 V AC.
I am also an electronics engineer since 1990 but I work in the IT field, electronics being a hobby. Recently I decided to make a VFD circuit to control an AC motor and I studied the theory again, when I found out that I need 650 V DC to get 230 V AC and I said wow, it can’t be possible … I can’t attach images that would be suggestive but we have this: the AC mains voltage has V(rms) 230V (for me), the peak voltage V(pk) = 325 V and the peak to peak voltage V(p-p) = 650 V. The V(p-p) voltage produced by the H-bridge cannot exceed the voltage V(p-p) from the power supply, so if V(p-p) = 310V then, after the H-bridge, we will have V(p-p) = 310V (maximum, real 300 V or less) , V(pk) = 155 V and V(rms) = V(pk)/1,414 = 110 V (sine) or V(rms) = V(pk) = 155V (rectangular). I wish I was wrong, but ….
I am afraid you are wrong. I don’t know what results you got from your VFD experiment, I just want to explain in a very simple term.
How does the H bridge function?
It simply switches the 310V DC supply alternately to the load. Meaning for one positive cycle the load gets the 310V DC, and for the next cycle the load gets -310V DC. So at any instant the load is getting the fully 310V DC, this means the peak and the RMS are both 310V for the load.
The 1.41 value does not apply for square wave AC, it applies only for sinusoidal wave AC.
Just rectify the output from the H-bridge through a bridge rectifier and check the voltage on a meter, that will tell you what RMS exactly are you feeding to the load.
I have already tested this with a 12V powered H-bridge and an oscilloscope. I invite you to do this. We’re not talking about a charge pump.
P.S. I wrote above: sine wave (sine) – 110 V and rectangular wave – 155 V.
Your scope may be giving wrong results, or your H bridge may be faulty….it is straightforward calculation….no scope is required. You must investigate why you are getting this result for a single phase H bridge??
for a 310V Dc bus, A Single phase H-bridge will produce 310V DC on one direction and then 310V DC on the other direction to create one positive half cycle of 310V peak and a negative half cycle of 310V peak, there’s nothing complicated in that.
The H bridge will not cancel or terminate any part of the DC for a square wave output….for sinewave some portion of the DC will be cancelled or chopped of that is why we have to consider the 1.41 factor.
650v để ra 220v soay chiều thì phải dùng mạch nửa cầu h không phải toàn cầu h điện áp lấy ra ở giữa 2 tụ và giữ nửa cầu h
sir,the third circuit with two 555timer and a ferrite transformer at the output,my question is can that work for domestic appliances because,to me ferrite core works at high frequence to turn on.or how can they work with home appliances at just single stage?please sir,i want to be clear with this.looking forward to your quick answer
Eniola, if you build everything correctly, then this circuit can be used for any electronic domestic appliance. The 555 circuit is a 50Hz circuit…with 20kHz PWM…so it will ultimately produce 50 Hz at the output
Okay, also the ferrite transformer will be calculated at what Khz? when calculating the turns ratio.
The frequency of the fast triangle waves which is fed to one of the op amp inputs
Please sir i need further explanation on ready made 12v to 310v to 5kv please thank you.
sir, thank you for the lecture .I don’t know what to do my 5kva 48 inverter when connected its will be working normal all of the sudden the out put voltage will just go up and burn some light what should I do to rectify it. Thanks
Isaiah, I think it may be due to malfunctioning of the feedback control, which may not be regulating the output voltage correctly. Or may be the there’s no feedback control present in your inverter…
hey how do you calculate the transformer for the first circuit with h bridge at the output? I mean by the some core information or inductance of the windings
Sorry I do not have the inductance value for the winding, I only have the number of turns, as mentioned in the article.
Good schematics dear swagatam
Isn’t it easier to put 19 12 V batteries in series to add up to 228 V and put them in the oscillator that creates the 50 or 60 Hz frequency? You protect the whole installation with automatic fuses and you have as many kw as you want.
That is what we usually do in most high voltage inverters, however, maintaining 19 numbers of batteries may not be easy.
Please sir how can I increase the power of my inverter up to 10000 watts
by upgrading the transformer, mosfets and the battery accordingly.
Hello sir khalid here how are you sir hope you well our prays with you. Sir i need help sir i change the winding of ferrite transformer i am using 3+3 EE80 cores now i am getting 145dc from from output and the frequency is 450khz before there zero volt and frequency was very as i said i am using 10k pot the frequency not decresing it is in last point still it can be incresed but not decreasing to get 50 htz what modification required with ic to get 50htz please need help sir.and now the transformer is giving output sir thankyou very much you are my teacher sir please reply i will try to get success by your help please waiting for your reply i will back with result thaks sir plesae take care.
Hello Khalid, the frequency of the first SMPS should be below 100 kHz, 450kHz is very high.
I think you should try the 555 IC version instead, which is much easier and will fulfill the same results:
" rel="ugc">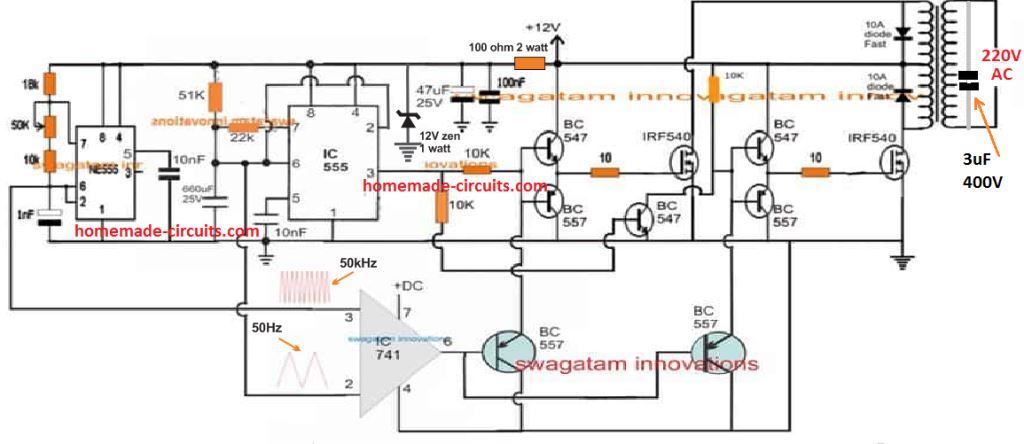
Hello sir thank you very much for teply sir the osdilater is working its giving from 890.5 to 990 .5 kilo htz i checked with digital multimeter it has frequency reading option. Before joing the circuits all i was checked seperately it was working then i was joined together . Now i checked osdilater is working. The winding i did on bobbin i made by hand with plastic sheet.the voltages going but output not coming from transformer so we have to make another winding or what .please reply sir i am waiting your help thank you very much for your help and cooperation i will be back with result. Please take care .khalid.
Hello Khalid, 990kHz looks very high, almost 1MHz, I don’t think the IC is configured too produce this much frequency. It should not be more than 100 kHz. In the article it is clearly written the max frequency as 40 kHz, You should read the article fully for understanding its working.
Hand winding will not do, it should wound with machine and with great accuracy. The e-cores must have a paper gap between the edges. Please get it done from a professional transformer winder
As I cautioned you earlier this circuit is for people who are well versed with the basics of SMPS, it is not recommended for a newcomer.
If you are new to this, you must first try smaller SMPS circuits and study their working by experimenting with their transformer winding and the effect of frequencies on the number of turns.
Hello sir khalid here how are you sir i did the 5kva above reffering to 60v i got ferrite cores and i did it complete as it is in the drawing and for testing i used 14 o 14 v transformer it is 28 i used 4 diodes and 2500 uf capacitir after capacitor it is showing 40 volts and i am also using 22 diodes to reduce volt from 60 to 50 because i am using 317 ic to supply 12v to ic irs2453 after testing sucessfully i will use 60v supply but now i am using transfoer 28v so i adjust the supply to 12v for ic irs2453 its ok and also i am using same 12v to transisters pwm insertion which is plus 15 mark is there . Now every thing is good but the ferrite transformer is not giving outputi remove the connection from 30 amps diode and checked no output but another with centre tap i gave the supply ot is showing 40v but no output the tonnes and guage and strands i make all as you said 5+5 and 18 but no output what will be problem and the supply to pwm insertion transister with same 12v with ic irs2453 i connected so is this good or we have to connect different 12v. And the transformer i have change the again or what .please reply me about this two problems. Thank you very much for your help. And take care. I will be back .
Hello Khalid, solving a ferrite core SMPS problem can be very difficult without checking the circuit practically. So I cannot troubleshoot it correctly from here.
There are few basic things that must be checked.
Is your oscillator circuit oscillating correctly, and with what frequency?
Is the ferrite transformer correctly wound with a small gap between the ferrite core edges?
Are the MOSFETs conducting optimally?
So basically you must check all the stages for ensuring that they are working with perfection.
You must also have an ammeter connected with the supply to check if the current consumption to circuit is getting affected.
Even with a slight mistake your MOSFETs can blow and create more confusions.
Hi Swagatam,
Thank you for looking but that is not the one I was looking for.
I’ll keep looking.
Tom Kenefick
No problem Tom, hope you are able to find it quickly!
On thing I haven’t seen on youtube or your site (I hope I searched adequately) is a tutorial on how to smooth distortion from the typical brushed gas generators that people buy just about everywhere.
I saw one such video on youtube that smoothed the output by running it through an AC/DC charger, to a battery bank, on finally to a sine wave inverter. Not really what I would consider a video on “smoothing” gas generator output.
Any interest in giving this a few minutes with pen and paper? 🙂
You have a great site, BTW. Your efforts are much appreciated!
Thanks
Doug
I guess the intended output is a DC? In that case the output can be smoothed using a filter capacitor? A battery is also great compensator, and will smooth just about any form DC ripple and fluctuations, while also getting charged through those ripples.
So a large capacitor across the battery terminals along with the generator output connected across the same battery terminals can assure a clean and a smooth DC for the inverter.
Hello sir how are you hoping you well.khalid here thankyou for help your guide and and reply . After success of simulater circuit .now i recieved ee80 cores for 5kva inverter the circuit before was made but the ee80 core was not found but now i got from online and make bobbin i wanted to verify the bobbin from you buy sending the photos so how could i send the pictures. And i rapped 5tones primary and cut the wire after secondary 18 tonnes i will make another 5tonnes but i want to send the bobbin picture.and after completing complete transformer i will send again picture to you after assembling .so please reply .thankyou very much please take care i will back.
Hello Khalid, I appreciate your interest in this circuit, however it is duty to caution you that this is a complex SMPS circuit and is not recommended for newcomers in the field. Because if you are building it for the first time without prior knowledge SMPS and ferrite transformers, then you could run into problems, and it can be difficult for me to understand the fault and troubleshoot it through comments.
So I advise you to proceed with caution, if possible start with a smaller design first, gain some experience and then try this design.
You can send the pics to my email, which is given in the CONTACT page.
Hello Swagatam I am Kallol Bhuiya. I want the output 50 Hz 220 v AC will be pure sine wave. so kindly give me this type of circuit. it will be very helpful to me. (load approx 10kv max)
The circuit output mosfit transistor n channel or p channel?
Good sir. Please what is the power rating of the “simple ferrite inverter” designed above for the new comers..
It is around 100 watts
Hi Swagatam,
I am wondering why you don’t directly low pass filter the output of the high frequency transformer using a LC filter to obtain the 50Hz sine wave.
What is the point in rectifying the transformer output and then subjecting the DC obtained to an AC conversion. Why not just filter out the HF components at the Ferrite transformer output itself to obtain the sinusoid?
Regards
Ankur
Hi Ankur, I am not sure how an LC filter can be used to convert a 220 V 50 kHz signal to 220 V 50 Hz at 5 kva, please explain in more detail
Hi Swagatam, A PWM (eg. carrier at 100KHz) signal modulated by a 50Hz sinusoid will produce a spectrum with a peak at 50Hz along with its attenuated harmonics. These harmonics when filtered out by an LC filter at the HF transformer output will result in a 50Hz wave.
A ternary (3-level) PWM will have further attenuated harmonics.
Regards
Ankur
Thanks Ankur, that makes sense! If time permits I’ll try to update the design in the above article.
Dear sir, according to the schematic whether the 310VDC High frequency inverter has been tested and works well in providing 5KVA power, with 8 mosfets. this source determines the reliability of the inverter. if the DC supply from the battery available is 120v, it is necessary to calculate the number of primary turns of the HF transformer.
Regards,
Widiatmono
Dear Widiatmono, yes it is tested, but it is recommended only those who are experts with SMPS and flyback designs. Yes it is strictly necessary to calculate the ferrite transformer under all circumstances.
Dear Swagatam,
If you don’t mind, please correct the calculation for the number of turns of the inverter that I built, with a DC voltage of 120volts according to the formula, N = 120×100000000 / 4x50khzx1500x2.1 (etd59), the result is 20turns so that the primary is made CT 2x20turns. for mosfet using 8x IXFH50N60P3 and is being considered using igbt
Thank you for your help, I really appreciate it
Widiatmono hersan
Indonesia
Hi Widiatmono, It looks OK to me. Using MOSFET will be a better option initially, since they are cheaper than IGBTs and their datasheet is more familiar.
Hi. please can you help me. I use sg3525 ,I choose rt=22k, ct 1nf, rd=56ohms.which gives oscillator frequency at 64khz. so each mosfet switching at 32khz. My question is during calculation of primary turn of ferrite transformer, which frequency (F) I have to consider in the formula (vinx10^8/4×FxBmaxxAc) ? 32khz or 64khz? Many thank’s man
Hi, it is 32kHz which must be taken into account while calculating the primary turns
He sir khalid here hpe you are fine.i recieved irs2453 from online i did other corcuits completed for 5va inverter now H bridge i am doing i want to ask the caps connecter to ic irs2453 from pin 8 to 10
12 to 14 is this polarised or non polarised .and another doubt we can give directly 60 v to ic irs2453 as through 33k resister as shown in diagram no problem or is there any problem please im waiting for reply thanks .but now only remaing EE80 core online not avaluable also.but im in search may i can get until i finish the complete circuit.i am waiting for reply i will back take care.
Hi Khalid, those can be polar or non-polar, it is not critical.
you can also try the following circuit which is simpler than IRS2453
" rel="ugc">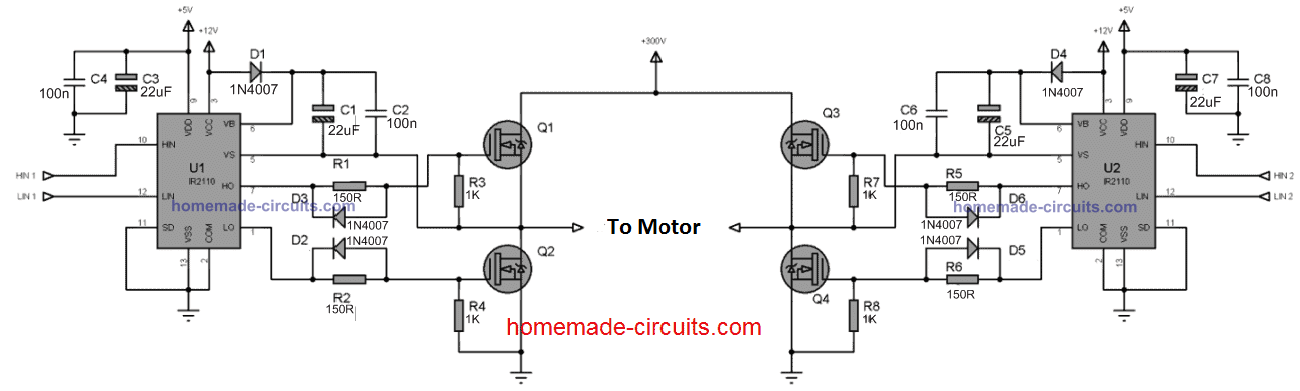
Hi Swagatam,
We’re working on solar-powered air conditioning and need a board similar to the one you have here. It’s up to 380v solar DC input or 120v alternating current input, and then it supplies 310v DC to the electronics in the air conditioner (compressor and fan motors). Is this anything you can help with, or can you advise who you can refer me to for this?
Thanks,
Dave
Hi David, A ferrite based transformer might require some serious calculations and some practical experimentation, so it can be difficult to suggest without doing these analysis in a lab, which may not be possible for me due to lack of time. Sorry, I do not have anybody else who may be willing to do the job for you.
Great design, Please confirm that this is a pure sine wave design .What changes is to be made if we are building a 1000w circuit ?. How can we include a EGS002 module into the design .
Thank you, it is not a sine wave design. For 1000 watt you will have to upgrade the transformer and the mosfet specs accordingly
Pls I need you help with these. Thanks in advance, you are the best.
1. How to incorporate a changeover/charger circuit to this existing circuit
2. How to incorporate a low battery shutdown circuit.
Thank you Chris, However, I would suggest you to build the unit successfully first, once you complete it then we can proceed with the further enhancements.
Wow, wow wow. Thanks a million Swagatam. You are the best
Good day sir, thanks for the informative article, I attempted building the inverter, I used sg3525 to generate a frequency of 50khz, I used mosfets irpf3205 in a push pull topology, I wound a ferrite core transformer 3 turns (twice to form center tap) on primary side using 6 strands of 0.45mm wire and I made 96 turns on secondary using 0.45mm wire..my challenge is that once I connect the center tap to my 12v 100AH battery, the battery voltage drops quickly and the negative trace of the circuits burns off causing a open circuit, I have rewound another ferrite core transformer but am getting same problem,the oscillator and mosfets work well without transformer but once I put the trasformer the negative rail melts and battery voltage reduces rapidly and stabilises back to 12v when the track is melted….pls sir how can I correct this.
Daniel, your described inverter is completely different to the one which is explained above. Moreover, ferrite inverters are always difficult to optimize, because they need many calculations and sophisticated gadgets to test, so it can be difficult for me to judge your design problem.
The IR2155 inverter section explained in the second last design is an easy option which you can probably try. You can replace the IC with sg3525
Dear Swagatam,
Am highly astonished at your knowledge of electronics circuits. Really grateful to come across your post. Under the section ” Making a PWM Version” I have a few questions;
1. How easy is it to incorporate to this existing circuit an input changeover/charger circuit?
2. How easy is it to incorporate a low battery shutdown circuit.
3. Lastly, to increase the duration the inverter can provide the power, can I cascade 12VDC batteries say four(4) together with this circuit ?
Looking forward to your anticipated response.
Thank you Dear Dyani, all those features can be easily included in the design, however making the inverter section is the most difficult part. Other features can be easily added once the inverter is built successfully and thoroughly tested.
Thanks ok but only confusion with negative lead of capacitors .negative will connect up or down side this i wants know .thank you very much sir for reply i am waiting.
Khalid, Capacitor negatives are connected with the MOSFET sources
Thanks a lot for reply sir khalid here. i want to ask the capacitor which is connected pin 10 and 14 of irs24531d where the negative leg to be connected please reply thanks .
they should connect on the spot where the black dots are shown…
Thankyou very much for reply sir i forget to ask where the negative leg shold be connected of cap
Ic ok but if ee80 not found so what other number of ee core mathes for this particular 5kva circuit please reply thanks. Khalid.
the full bridge circuit negative/positive will connect with bridge rectifier output. The bridge rectifier should be connected with TR1 output
the core should e such which comfortably accommodates the total winding of the transformer…
this circuit is for the EXPERTS ONLY, so please proceed with caution.
Hello sir hiw are you khalid here i got ic irs2453d but in diagram it is irs24531d is this ok and second thing in full bridge circuit 1uf 25v is this polarised or non polarised .please let me know i will be thankful. Now i got components but still EE80 not found inshallah until my circuit is complete i can get .only ee80 is required or we can use ee85 for the same data.thanks.
Hi Khalid, it is one and the same and will work.
1uF/25V can be polarized, but please try 10uF/25V instead which is more suitable for 50 Hz frequency. If the rating of the diodes are the same then you can use them.
Hai sir khalid here thank you for reply i have one question for 5kva inverter i am referring to 60v circuit . For high frequency circuit i used irf 740 as you mention but for full bridge inverter in irs24531d circuit can i use irf 640n 4pcs because it is avaluable with me. and for rt what value of potentio meter i can use plesae reply i will be thankful waiting for reply.
Hi Khalid, whenever you are in doubt about a MOSFET, you should check the datasheet of the device, and confirm whether its VDS (drain/source voltage) and ID (drain/source current) matches the supply voltage and load current respectively or not. If the datasheet specifications are higher than the required specifications, then the MOSFeT is OK, otherwise not.
Thanjs fir reply sir so i can use 10uf 50v non polarised instead of 1uf 50v is this ok please reply thanks because in circuit both legs showing black of 1uf 50v thats why i confused polarised or non polarised.
You can use polarized or non-polarized both will work.
Hello sir khalid here again hope you are fine.i have question. I make the circuit high frequency and oscillator but not tested because i am waiting for ic irs24531d may be i can this week online 1st question can i use different mosfets in full bridge side means 2 irf7460 and 2 irf 640n or should be all four same. And 2nd what is rt and ct value and if i want us a pontentio meter what should be value please i am want to the value of capacitor and resistor ct and rt of full bridge ic irs24531d .thanks waiting for reply.
Khalid, you can use any MOSFET as long as its rating matches the required output voltage and current specifications.
The Rt Ct formula is given in the following article, or you can also experiment it through trial and error using a frequency meter.
https://www.homemade-circuits.com/simplest-full-bridge-inverter-circuit/
Hai any have made this 5kva inverter because i cannot find EE80 F core and irs2453 ic in india and also online so please if got success making the circuit wheather same with the ic and F core or any substitute if suceeded please send the details of substite ic and Fcore please send picture and details o wil be thankfull to swagatam sir and others thanks.
Thanks Khalid, the above design is a tested one, but it was tested by other members not by me, so it can be difficult for me to provide precise suggestions.
Please can you help me with pic16f877a inverter Code + Simulation + PCB + Schematics + Gerber Files
You can refer to the following article…
https://www.homemade-circuits.com/sinewave-ups-circuit-using-pic16f72/
It is all that I have in this website…
Plz sir can I get the PCB details file for the 3kva ferrite based inverter? Thanks so much for your supports
I don’t have the PCB details at this moment, if possible I’ll try to update it in near future.
Good day sir…How can I generate a sinewave using this microcontroller 18f26k22?
Sorry Shilex, I have no idea about it…
Good day,
This is a great article. I’m interested to utilise the circuit to drive a 3kw load.
My energy source are PV solar panels.
My planned configuration is 6x320W panels in series (1920W rated energy, practical power is about 80% at 1536W)
with another 6 in parallel. The open circuit voltage is about 200V and under full load falls to about 180V at 8.5A.
With 2 sets in parallel its 180V at 17A.
If the input DC power from the solar drops, due to clouds or sunset/sunrise, what will be the effect on the primary boost phase? Will the circuit at maximum PWM just not be able to reach 310Vac@50kHz, causing the amplitude of the output to drop below 230Vac rms at 50Hz?
The transformer winding calculation resulted in 25 primary and 45 secondary turns. Are the number of turns still practical or won’t it fit on a ee80 core given the wire guage required to transfer 17A?
Hi, thanks, and glad you liked it…if the solar voltage drops, the output would also drop proportionately. I am not sure about the winding data, because it’ll need to be done with some calculations or with some trial and error.
Hi Swag, Thanks for all your interesting projects. I would like to know whether it would be possible to use two of these modules in tandem to produce a 1000 watt inverter. Also the input voltage must be 24v instead of 12 volts. Could you please give slow and understandable instructions and maybe a sketch to a guy like me who is not so smart in electronics? It would really be appreciated. Eric Smith.
Hi Eric, you can try that by modifying the transformer differently. I would recommend the 3rd circuit from bottom. Instead of 13+13 turns at the primary you can try 10+10 turn, using 2 numbers 20 SWG super enameled copper wire in parallel. For secondary you can use 24 swg 250 turns.
Build and test each section separately and stage-wise….having said that, this circuit is no way recommended for any newcomer, so please proceed with caution.
Dear Mr. Swagatam,
While making the ferrite core transformer I was using a cutting knife blade or a #180 sand paper to remove enamel coating of winding wires. This is tedious and time consuming. have you got a better way of doing it?
Thanks.
Hi Gamini, you get a special solution (chemical) for cleaning the super enamel of copper wires, you can inquire it online for the details.
Ok sir thank you very much i am reffering to pwm 90 supply volt seond circuit is resistor type 10uh inductor ok for it or not .and i bought diode of 40 amps because 30 amps not avaluable its good or not. And ds812 06a zener not avaluable so is there any equivalent for it.and ic ir2453 1d still not found but i am trying for ic may i can found. And ee80 ferrite transformer core i not found i am trying also for this.but for diodes and inductor i want your answer please reply and also the number ds812 06a zener is this number correct.iam waiting for answer thanks.
For the diode you can use the following:
https://www.digikey.bg/product-detail/en/ixys/DSEI12-06A/DSEI12-06A-ND/241965
yes the small resistor type induct0r will do
Hello sir thanks for reply.i bought inductor 10uh it is resister type not ferrite ring it will be ok or not or require ferrite ring type please reply thanks
Hello Khalid, which circuit are you exactly referring to? Please note that this circuit is very complex and is intended only for experienced engineers and needs to be built with sophisticated measuring equipment like oscilloscopes and digital meters, so please proceed with caution.
Ok Thank you very much but mosfets required to fix with mica between heatsink and mosfets to protect short with mosfets and heat sink or we can fix the mosfet without mica on heat sink . This is my question please let me know .thanks
Mica is recommended if you use a single common heatsink, if you use separate heatsinks then no need…
Hello sir khalid here i bought some components for 5kva inverter i am trying to build each circuit seperate one by one my questio is all resistors are 1 / 4 or any different watts available if there is which please tell me.and 2nd question is all bjt’s should be fixed with mica on heat sink or can be fixed without mica on heat sink please let me know .as i make the circuit i will send the picture each circuit thak you very much for your cooperation and help to us.
Khalid, yes all the resistors are 1/4 w 5%.
Only the MOSFETs will need to be mounted on heatsinks, not the BJTs.
Always use a heavy duty bulb in series with the MOSFET drains, this will ensure that the MOSfETs are never burned due to a mistake or some other fault.
Hai khalid here thanks gor reply i have some questions. If i am going the last circuit of 5kva with 360 tons inductor i want to the connecting points for batteries and the charger points from grid and if i suppose to make solar so where the connecting ponts please.and i saw your dual charger if that we wants to connecte how to be connected and what chages the dual charge circuit requirwd please this is the question .i am gathering parts if i get success i will send the images and result.thanks again.
Hello, this circuit is for the experts in SMPS projects, so please proceed only if you have prior knowledge and experience with ferrite based SMPS concepts, otherwise you may find it extremely difficult to succeed. Please first make the initial basic design successfully, afterwards we can discuss the other parameters.
Hai sir i am planing to make this inverte as you said in in the article the readymade module if we use it will be very easy the module i saw on net it is 500watts is this ok it operates only on 12 vots please reply.
Hi Khalid, if it’s rated at 12V then it must be operated with 12V only. It is OK to use it
Hello sir you are helping alm over the world its really a great help to us
Thank you khalid!
Dear Swagatam
May the almighty reward you for teaching the world free of charge. Ive been your student since 2014.
I will suggest you should establish an online electronic university which awards degrees so that you reward yourself rather than relying on peanuts from Google. Think about it.
I’ve some question as per the above 5kva inverter .
https://www.homemade-circuits.com/5kva-ferrite-core-inverter-circuit/
1. Stacking of two ee80 ferrite cores for larger power , how do I design the bobbin that will fit the winding? Or do I wind on the center arm of the core directly without bobbin ? Please explain.
2.If no ee80 cores available, How many ee55 cores can be stacked together to obtain such intimidating KVA?
3. Can you give me a link online where I can get more information on stacking of cores together for obtaining monster power ? I’ve googled my eyes out without any
Thanks.
Thank you Dear Davidson, I appreciate your thoughts.
As we know, ferrite transformers are not easy to calculate, so estimating something without calculations can be difficult.
Here, I am not sure how many of them can be stacked up, and even whether it is recommended or not.
For experimenting you can try 3nos of ee55 and check whether that satisfies the requirements or not.
You can create a hand made bobbin using a cardborad wrapped up on the center limb of the e core.
you can try this link for reference:
https://electronics.stackexchange.com/questions/96435/making-a-bigger-transfomer-core-by-stacking-multiple-smaller-cores
hello Sir,
Please do I need to design additional feedback control circuit for the low frequency oscillator which switches the 310VDC to 220VAC or will the output AC be automatically 220VAC due to the 310VDC rms?
Hello Kingsley, A feedback can be added for better output regulation. You can try the last concept discussed in the following article:
https://www.homemade-circuits.com/load-independentoutput-corrected/
The transistor collector can be connected to the Ct pin3 of the full bridge inverter IC.
Thank You Dear Swagatam.
Please I want to ask these question(s) that keep confusing me about the high frequency ferrite core inverter.
I want to know if the rectified high frequency 310Vdc will share the same GND with the H-bridge MOSFET in the 50Hz low frequency AC switching side? Again, will the GND of the two oscillators (the low frequency and the high frequency oscillator) connect together as common GND with the battery negative? Please help me I am using high frequency SG3525 oscillator to drive the ferrite transformer and everything works fine; the high frequency 310Vdc is obtained without trouble but each time I connect the obtained high frequency rectified 310Vdc to the common drain and common Source of the H-bridge MOSFET on the low frequency side, I ended up getting nothing at the AC output. I tried placing the digital multimeter at the +ve and _ve of the rectified 310Vdc to observe if the voltage remains the same after the connection and only find out that the voltage withdrwas to zero. This process has burnt My H-bridge MOSFETs on the low frequency side a couple of times and once i insist on checking the fault, it even get some of the MOSFETs on the high frequency push-pull side burnt too without separating the two(2) oscillators. I am using IR2110 * 2 to drive the H-bridge MOSFETs and have connected all the GNDs together including the GND of the rectified high ferquency 310Vdc, GND of the two(2) oscillators, and GND of battery. In the rectification, I used UF5408 ultra fast diode rated at 3Amps each.
Please help me sir. Thank you in anticipation of your response.
Hello Kingsley,
yes all the grounds or the negative s need to be joined in common. This is necessary so that the bootstrap capacitors associated with the IC is able charge through the low side MOSFETs while they are ON. If the grounds do not connect the bootstrap cap won’t respond and the circuit will fail to work
just make sure to connect a 1K across all the gate/source of the MOSFETs.
Thank You Sir. I already connect 10K from gate to source and 10R from gate to driving signal through IR2110. I used to do so for push-pull low frequency inverter that i have been designing for long and it works well there. Though I don’t know if that is the problem with the h-bridge counterpart associated with the high frequency.
Hi Kingsley, please make it 1K instead of 10K for fast discharging of the MOSFET capacitance
OK Thank you.
Please what is the acceptable range of values for the bootstrap capacitor? I am using 47uf. is that value acceptable or do I still have to reduce it?
Hi Kingsley, you can use any value between 0.1uF and 1uF if the frequency is above 20kHz
47uF is too high for 20 kHz and above, it may be OK for 50 Hz application
Hello sir, how do you determine the values of those components, say for example resistor and capacitor values for an arbitrary power output of a given design. For instance if I want to design a 5kva inverter
Hello Ken, it depends on which component it is being used, and under what V and I conditions. It will be different for a BJT, a capacitor, a MOSFet an IC etc…
1) actually sir i want to make half bridge with four mosfets each pulse with two mosfet without heating . i only have problem with two mosfets on single pulse that’s getting hot. how to solve the problem?
2) another problem is that once i have used two 47N60 super fet. each mosfet with single pulse of IR2110 they are not getting hot but also the smps not getting started and both pulse voltage of IR2110 dropped. i don’t know why the pulse dropped and the mosfet not turned on?
3) sir is it possible to make full bridge or half bridge with uc3843? as in the 555 inverter circuit diagram where single output drive full bridge with necessary transistor etc?
Hi Sheraz, connect a 1K resistor across gate source of each mosfet and check the response.
47N60 seems to have a separate source for the gate driver input, so make sure to use this separate source with the bootstrap capacitor of the high side MOSFETs.
You can try building a full bridge using any oscillator by using separate bootstrap stages for the external n channel mosfets, as shown at the end of this post:
https://www.homemade-circuits.com/simplest-full-bridge-inverter-circuit/
the 555 output pulse with bc547?
IR2110 is a half bridge driver IC, it must be used with two mosfets, single is not recommended. Use a 1K resistor across its gate/source and see if that stops heating of the IC.
Hi sir! dear sir i have the problem with driving two mosfet 20n60 with a single pulse of IR2110 driver. one mosfet get extremely hot. i made an IR2110 based smps it works fine with single mosfet on each pulse but can’t drive two 20n60 or 13n60 with single pulse. i have not added the buffer stage as shown in your IR2153 inverter circuit diagram. how can i drive multiple 20n60 or 13n60 mosfet with single pulse???. i connect two mosfet with single pulse of IR2110 with single 10R resistor at the gate pin but they getting hot and the pulse dropped not starting the smps. but fine with single mosfet. how to solve this problem?
Hi Sheraz, you must use the driver stage as suggested in the first diagram, otherwise the MOSFETs may heat up an blow. so please use the push pull stage and check again.
Dear Swagatam
Firstly very very thanks to you for your quick response.
Now my question is:-
01. Can I connect negative terminal of my home wall socket/grid line to output line of inverter’s any
one 220 VAC output line?
It might create a short circuit, because the LIVE from the inverter will try to short itself with the Grid neutral.
Thanks Swagatam, for your option.
I understand that it’s not possible to wiring China inverter’s
output line with mix to my home wiring.
But one thing I would like to inform you that, In my home IPS/UPS/Inverter system there is also two output line but when I check boths output line it shows one +VAC and another one is -VAC terminal.
My question is any difference is there for designing circuit for China Inverter System and other inverter/IPS/UPS system which is regularly used for backup system of power failure.
Dear Zahirul,
the UPS could be having an arrangement for a dedicated neutral line which allows the output to show 0V for the neutral wire, unlike ordinary inverters which do not have a special arrangement for the neutral.
Yes there will be a difference in the transformer winding specs and the switching specs.
The neutral line is basically a reference line, which enables the load to respond to the +220V and -220V alternating phases with reference to the neutral line…so the neutral by itself does not generate any current and therefore stays neutral.
So nice Swagatam, I understand all the matter.
My next topics is:-
I have two 1000 VA UPS which are run by two 12 VDC battery i.e input voltage is 24 VDC.
Now I want to convert this system to 12 VDC input system. If I use 12 volt transformer instead of 24 volt transformer for inverter system but circuit board is same as before then it will work or not?
If it is needed to convert circuit board also then how I convert the circuit board to 12 VDC input system.
Give me tips and topics
Thanks Zahirul, yes a 24V inveretr will work with 12V if the battery and the transformer are replaced with 12V equivalents. Changing the board may not be required but if it has 24V relays they also will need to be changed with 12V.
Awasom! I am very very please to you for your support.
Now I would like to know one thing is- if I make my inverter system is 12 VDC input system instead of 24 VDC by replace Transformer, Battery and Realys (if needed) then inverter’s VA/Watt rating will decrease or not?
My question to you-
01. If VA rating decreased then, Can I increase Watt/VA by adding more
MOSFET to circuit board?
02. Can I make 12v-0v-12v transformer by taking one connection from
between 24v and 0v of 24v-0v-24v transformer?
Swagatam, for your kind information I would like to inform you that-
I am making this type of inverter system for reduce the battery cost, why not already I have a one 12 Volt 160AH battery but my UPS required two battery. If I purchased more one battery then I have to spend more USD 150, now a time this is not possible for me. That’s why I am taking your suggestion for done the job nicely and correctly. Don’t fill boring.
Thanking you
Always, I will be stay with you.
Hello Zahirul,
The output wattage will depend on the input wattage.
The wattage is calculated by multiplying the transformer voltage with its current rating.
This transformer wattage must be satisfied by the battery otherwise the transformer will not be able to produce the rated power.
Mosfets are only like ON/OFF switches, they don’t generate power, they only switch power across the connected parameters. But they must be rated according to the transformer V and I rating otherwise they will burn.
The battery will need to be selected as per the required power output and the transformer wattage.
For a 160 Ah battery the typical wattage of the transformer can be 12 x 16 = 192 watts or 200 watts. Meaning the transformer primary must be rated at 12V, 16 amps or 20 amps.
Hello sir khalid here hope you well.sir now i assembled the circuut for rt i used 10k potentiometer is this ok and for ct from which value i should try and second thing it is electrolytic type or pf type please let me this 2 things .i will be waiting for reply and i will be back thanks please reply sir.
Hello Khalid, you will have to find the values either using the formula or with a frequency meter, Ct will be non-polar and a small value capacitor.
Hi I need u r help
Dear Sir
I am from Bangladesh. In my china 300 watt inverter system there is two ware for AC 220 out.
But problem is both two AC out line shows positive/alive (both wire light up the AC tester) that is I can not identify which one is positive terminal and which one is negative terminal. Why not I want to connect my inverter output to my home wiring because for power backup when grid line is off. For this purpose I will use auto cutoff relay system only for positive terminal of both grid and inverter system.
I need help from you for this problem.
Technical observation myself:-
When I check inverter circuit board I seen both VAC out line come out from two different MOSFET pairs
Source Pin.
Dear Zahirul, normally inverters do not have a neutral as our mains AC have. Inverters operate in a push-pull way which causes their output wires to swap between LIVE an Neutral alternately, therefore you may find LIVE on both wires since it is alternating across the output.
In utility mains, the distribution transformer has a common neutral and +310V/-310V phases which alternate with respect to the neutral producing positive cycle and negative cycles with respect to the neutral which always stays at zero potential.
What about using arduino to generate sinewave and voltage controller
Pls an you modified it to modified sine wave inverter
modified version is not possible because it will require modifying the dead time, which is not possible here.
Hi,
Thanks for this. It is very educative.
I am attempting to build an inverter of this capacity for everyday home use. The sources of power include AC mains (220v), Solar Panel (12-48v) and Lead Acid batteries. The most preferred source will be the solar panels, which can both charge the batteries and supply power at the same time. The next preferred will be to discharge the batteries when the solar panels don’t supply again; and then charge and supply power with AC mains should both initial sources are depleted.
I would be very grateful if you can give me a circuit for this. Thanks a lot!
Hi, please provide the details regarding the inverter wattage, battery voltage and Ah rating, and load rating, if possible I’ll try to help!
Thanks,
I’m looking at maximum of 5000watts inverter with multiple 12v 200Ah battery (the number of batteries will be flexible, but typically between 1-5 batteries of that rating), load will be between 1000 – 3000watts. Should be able to include one or two refrigerators (about 0.8-1A current rating, 220v) in the load, considering their starting power. Other appliances will be bulbs, TV set, laptop chargers, etc.
I would really be grateful for this!
Thanks for providing the details. The circuit provided in the above article is for experienced engineers, so I would rather recommend buying one from an online store and then configuring it through changeover relays and a battery charger.
Making the battery charger and the changeover stage can be constructed at home with my assistance.
I can attempt to build the above circuit, but my questions: the PWM version has 90v input according to the circuit diagram, can I use a 20A dc/dc converter and use with a 12v battery?
I also have a 1.5kva sine wave inverter, can I increase the capacity by changing the transformer and increasing the number of power transistors? What othe components of the circuit do I need to replace?
For a 5kva if you use 12V then the current will be 5000/12 = 416 amps which looks impracticable, that’s the reason why 90V and above is suggested for this design.
You can put many 12V batts in series for getting 90V or 60V
I am not sure whether it would be a good idea to modify a ferrite transformer of an existing inverter, because ferrite transformer require proper calculations for the turns and the core size, so I can’t suggest much on this.
In this circuit the rms voltage is 220v . It is aligned with preset
Yes that’s right!
Hi sir , I have seen your 5kwatt transformer less inverter circuit . I tried it using ic 3525 (because i can’t get ic 2453 ),gate ic 2110 and igbt kgf40n120kda with snubber of 10ohm 5watt and 10kpf 2kv.i have solar cell for 350v DC and it is used for input for this circuit. For stablized output , feedback also given through opto isolater 4n35. It’s all refered from your circuit. It’s good for up to 1.5 hp motor .
But, in case of electronic loads
TV get harmbars , tube light chokes gets fault ,phone charger,etc,.
Please reply me the solution sir .
Hi Sageyu, for sensitive electronics you will need to employ SPWM so that the output is turned a pure sinewave. I have many examples published in this website related to SPWM inverter which you can refer to for more info.
Hi sir good afternoon
Sir ,in some of your circuits additional pwm is given instead of spwm. Is it good for motor and electronic appliances. But its output (after filter),i have seen is not sinusoidal on CRO.
Sir do you have any camparator circuits for spwm.if you have please send me the http.
Good afternoon sageyu, yes constant pwm will only help to control the RMS, it won’t create perfect sine wave like SPWM.
You can check out this link:
https://www.homemade-circuits.com/?s=SPWM
Hi sir ,I have referred your circuits and then i design pure sine wave circuit using EG 8010 with drive ic IR 2110 . Input dc bus voltage 400,High side pwm frequency 24 khz,Transistor 47N60C3.
High side transistor faults frequently but the load is below 5kwatt .what we have do for increase the wattage of circuit .
Can i use IRGPS 60B120KD for higher wattage
What buffer ic is used For increasing the signal from ic 2110 .
Can I use IC TC 4452 for buffer purpose.what is the difference between soft switching and hard switching
Hi Sageyu,
Power will depend on the transformer winding rating and the battery rating. The product of battery voltage and Ah should be at least 5 times more than the required output wattage.
Buffer will not work and is not required because MOSFETs have high impedance gate, so current is irrelevant. It can switch optimally even at microampere, but the gate voltage should be around 12 V.
The product of MOSFET ID and VDDS must be much higher than the intended output wattage for safe operations.
You can add a couple of more 47N60C3 in parallel to increase the current handling capacity of the MOSFETs
Make sure to add a 1K resistor across gate/source of each MOSFeT. This is not compulsory, but it guarantees better safety to the MOSfeTs.
Thanks so much for this.
however, I am a little bit confused about how to wind the ferrite. what exactly did u mean by “5+5 turns using 10 numbers of 20 SWG?” pls pit me through.
Thanks Izzuna, It means 10 continuous turns with a center tap extracted from the 5th turn, so that we get a winding with 3 wire output
Sir,
Speaking of a low power version i also tried the 12V 15A SMPS power supply which i purchased from a thrift store in my area.
1. What i did was directly removed the transformer from the unit carefully.
It had 2 pins each for primary, auxiliary and secondary windings.
2. I seen on the secondary side there were plenty of smaller wires, being 10 nos. wound in parallel.
On an approx. 1.5A output per strand of wire is my assumption…….
3. I did not modify the transformer and used it as a whole in the inverter circuit.
4. I concerned more for the secondary side of the trafo since it had sufficient parallel windings(i counted them) to provide me upto 180 Watts of max power on 12V output.
Next, i built a 555 inverter circuit……selected the 50% duty cycle schematic(the one in your article) which worked smoothly…..used one mosfet since secondary being a two wire design……
The transformer became a right match with 50KHz from 555 (50.03 on freq. meter upon direct measurement on mosfet drain) and worked well.
I tried the incandescent lamps initially for loading purpose…..a 100w was the maximum i tried……it worked nicely….
To conclude…..i can say that the very popular 12v 15a smps gets its best in the above circuit by using its transformer without changing its winding specifications…..but only for a low power application…..even a 12v 10a smps could be tried for this purpose for a 100w design.
Thank you Sherwin for your research and observations, I am sure the readers will benefit from it greatly!
Hello sir,
Just last week I tried the high power version of the circuit using 5pcs —EI33 core for the transformer. At 1000W of continuous power, i could sustain 400W load carefully.
Here I knew overloading upto 500W and more could consume more current from the battery and drain it pretty fast. Battery power is 24V at 840Watt hours to be perfect.
So at 400W continuous battery would just last 2 hours to be precise.
Here was the point where the IC 2453 just popped out even without any load connected on the output. Why did this happen? I were shocked even after doing it multiple times and re-engineering it carefully.
That was the time i didn’t share the results with you. Just because something which was not conformed carefully by me and i didn’t want to share something that is dangerous and not practically conformed and tested thoroughly after repeated attempts to do the same.
Users and readers must take note of this that on building high power versions of this inverter is not difficult if built carefully but the second circuit becomes weak at a certain power stage if crossed at some point of time and stops working.
Thank you Sherwin for the enlightening the users with your experience regarding the subject, appreciate it a lot!
Dear Mr. Swagatam,
I’m a little afraid of building the high power version as you mentioned only because the second circuit doesn’t stay calm.
The IC 2453 just blows OFF. I don’t understand why this is happening. I tried building it multiple times but the IC burns out.
With three EI cores in parallel nothing has still happened yet, I am able to get continuous 600W power. The second circuit is working presently but with danger. I am afraid anytime it will pop out.
I carefully converted the output to DC using appropriate fast recovery diodes and filtered everything but still the 2453 blows out. This happens after working after a couple of minutes nicely.
I also took reference of the COKE CAN INVERTER which rated 150W continuous and 180W max. It had both of the above circuits but used TL494 as the control circuit(both for PWM processing and full bridge circuits) which was mounted on a vertical board.
It was complex with many components surrounding it. i couldn’t understand anything.
On the end of the board there were 4 IRF830 mosfets, and they didn’t use heatsinks for the 4 mosfets.
This circuit worked nicely. The transformer here was quiet complex with the winding data.
But unfortunately this chinese inverter also popped when there was a loose connection from the battery side.
I need some help from your side with the second circuit; maybe i’m missing something very important in the circuit.
The second circuit is not safely conformed from my side, i’m afraid and unable to say anything!!!.
Hi Sherwin,
Your efforts are commendable. I understand your concerns and aware regarding how vulnerable and delicate mosfets can be.
That’s the reason I created the following article which explains how mosfets must be configured to minimize fatality of the devices.
https://www.homemade-circuits.com/mosfet-protection-basics-explained-is/
Please see the 4rth point which recommends the use of resistor across gate/source….this resistor ensures that whenever there’s an absence of a gate voltage even for a microsecond the mosfet is instantly switched OFF, preventing all possibility of a damage or burning of the device.
Hello Sir,
Today i built another transformer, this time i used 3pcs — EI33 ferrite cores in parallel. Keeping in mind the power i could get is 200 watts per core on full load on just being WARM.
This is now finalized such that as i increase the loading above 200W (when tested with single EI core) continuous the ferrite core starts to become HOT.
Also with due respect to the SPACING between the CORES; I’ve seen a great difference in power by adjusting them. I never removed the original spacing component as that was factory set to the working dimensions of the core pieces.
I took care that the trafo core didn’t get much hot when loaded after adjusting the frequency carefully. frequency was 55Khz(54. 23 on low and 54.71 on high being meter readings of 2153).
I kept the inverter running at 24V 35Ah SLAB this time during tests.
So, three pcs EI33 in parallel gives about 600W watts on continuous and 750W at maximum.
Now, i carefully loaded the system at 300W and the trafo stays cool as expected.
Till here I’ve succeeded for now. The load I’ve used were a multiple High Powered INCANDESCENT lamps.
Regards…,
Hi Sherwin,
thanks very much for your continued interaction with this website. Appreciate it a lot!
Could you please try the same using 110V DC. If 24V is able to support 750 watt, then 110V could easily handle upto 3kva.
For your mentioned experiment which you have finished, if possible please send a small video clip to my email, just a 10/20 second clip will be great
Please sir, am working on my school project which is construction of 500watts ferrite core inverter, I have ETD54 ferrite core, but I don’t know the working frequency, and the equivalent value of mosfet 2sk4124, I want to use sg3524n and irf3205 for the dc to dc converter, please tell me the frequency of ETD54 ferrite core, the equivalent value of 2sk4124, and if possible the circuit diagram using the parameters mentioned above. Please help me sir.
Ezeolisa, frequency is more related to the number of turns and the voltage specifications. You can take the help of the following schematic and match the specs with your specs and proceed:
https://www.homemade-circuits.com/compact-ferrite-core-transformerless/
Respected sir,
My self a student of science & independent innovator I have study about my own project for bldc motor, actually sir I want to run a 20kw bldc motor through a invertar ,
So u kindly please suggest me how much power invertar & battery it will requreid.
Regards; Azad (INDIA) 9693247248.
Hi Azad, can you please specify the voltage rating of your motor, I’ll try to help!
Good article.
I have a confusion. I read somewhere that the ferrite transformer should be wound for 313V, but your article says 220V. I would love to comprehend the discrepancy. Also, I read some articles where the H-bridge is switched at a frequency of 16KHz. How does this finally translate to the 50 or 60 Hertz frequency of the output voltage.
Thanks.
310V will be available after bridge rectification, whereas 220V is the RMS or the average value of the 310V output after it is pulsed with a calculated PWM, so here the 220V value is considered since this value is the one which will be used ultimately by the appliances at the output
..the second circuit is used for pulsing it at 50Hz, although the output would be still 310V, unless it is processed with a PWM
good day Sir …engineer Swagatam pls help me with a ferrite core step down power supply circuit diagram use for charging 12v battery……. 230v input to 14v output power supply thanks
Hi Sunshine,
you can try this link
https://www.homemade-circuits.com/12v-5-amp-transformerless-battery/
Please, can I replace IRS2453 and IR2153 with CD4047 because it’s difficult to find it in my country or can I use another CI capable to gernerate the needed frequencies, thank you man
sorry that cannot be possible, however one way of achieving the same could be by employing two batteries in series….
Dear Guru,
Although the EI33 datasheet says at 50KHz it can provide 125 Watts maximum and 100KHz it can provide 179 Watts, but after winding the transformer by hand results were different;
After multiple tests and trials, i have found out that a single EI33 ferrite core is able to provide 200 Watts of Continuous power and 250 Watts is the Maximum Limit it can provide.
I used 50KHz frequency to drive the core.
This was possible only after winding 2 wires together, i could increase the output power to almost double.
The moment i tried winding more wires in parallel, heating issues suddenly started and i fried few mosfets unnecessarily.
At that moment i were power hungry and tried to see how much maximum power i could get from a single EI core. Just for being greedy i paid the price for the mosfets. I had to replace four of them since i paralled two on each side.
In Conclusion, i can firmly say that a single EI33 ferrite core can provide up to 250 Watts Maximum power, i cannot go beyond that unless i parallel cores for more power.
Till 68Khz all tests and results are fine with regard to transformer, mosfets and 2153.
I never tried 100KHz and more from 2153 although being possible to get, i didn't want to overrun its switching parameters.
In the market the 2153 is 10 times more compared to price of 555 in rupees so i decided to ensure double safety to the 2153 chip by not exceeding certain parameters in its working.
Thanks
Dear Sherwin, thank you so much for this awesome insight, I am sure the readers visiting this page will be immensely benefited and enlightened through this invaluable data and your practical efforts. appreciate it a lot!
Dear,
There are lots much to say and discuss regarding this post.
I wish to put out a lot of changes in this design since I've noticed errors in certain places.
I don't know that whether i should join the forum for the discussion or just comment in this section directly.
Thanks
Dear Sherwin, since you have worked hard on this project you have all the right to point any corrections or modifications that may be required in the proposed design, please feel free to post it here, I may further on transfer the data in the main article so that the readers are able to view it easily while reading the article itself…
Great,
Hi Sherwin, thanks for this great effort to design this high power circuit. It will be much appreciated if you please post corrections and any other thing which can help us designing error free inverter. also would be much better if you can add pure sinewave conversion section.
Hi Saqib,
Firstly i would suggest you to build a low power version of this design say 150/200W which would require a single EI core transformer.
This could give you a good experience at the beginning stage and then later you may upgrade to high power.
I got the specifications of the transformer if you wish to build as i suggested.
I could help you with other stages of the inverter also.
Just take note of this:
The 5KVA design would be more difficult to accomplish since it will require a lot of complicated checking and inspection at every single stage of the complete design.
The transformer gets more complicated….You will have to stack many cores side by side to get the proposed power output.
You will require large heatsinks and cooler fans for power devices, in order to keep them cool during operation.
The full bridge section of this design will heat up if not implemented correctly and managing them at such massive power(5kva) would be really difficult.
You may face problems of power devices burning or cracking if something goes mistakinly wrong.
I don't wish to dissuade you from doing anything but based on your level of expertise on this field with regard to this project, you may think appropriately how to go ahead with this design.
Thanks
Thank you Sherwin, for this valuable advise!!
Hi Swagatam,
I am going to buy tranformer EI cores. Can you or anyone in your group send me required specs of cores for 5kva or more. as I read somewhere. should E80 type core is suitable for this? please I need all calculations to prepare the transformer like core dimensions including inductance and density and winding wire thikness and turns. Will be really thankfull to you guys.
Hi Saqib, I do not have the exact calculations or the inductance data for the transformer, the idea was thoroughly tested by Mr. Sherwin, you can go through all his posted comments and try to grasp the details.
Or better even 24vdc to 800vac
What If I wanted to use this circuit to step up from 12v to 400v how much turns would that require on each side of the transformer?
you can use 12 turns on each half, and 400 turns on the other side
Dear,
I wish to know what software you use to draw circuits since i wish to design some circuits myself,
I have never done so till now so please help.
Thanks
I use CorelDraw for drawing my schematics.
Dear,
some more wonderful things,
1. I managed to attach two EI cores side by side in order to attain more power output from the transformer.
2. I took both E's first, stuck them firmly with electric tape on each vertical legs.
3. I then made the windings fit firmly on the E's such that they don't exceed the length of the middle leg of the E-core, finally applying tape on the finished windings.
4. Next, i placed the i's on the e's and THIS TIME ADDED PAPER GAP BETWEEN THE CORE PIECES.
5. I finally taped the whole transformer firmly and assured:
a. that the e's and i's are not lose,
b. that the pri and sec windings have proper isolation between each other,
c. that the winding does not have direct contact with the ferrite pieces which would cause a short.
On completing the transformer, i googled the datasheet of the EI33 core and took a note of its maximum power output with respect to the working frequency given in the table.
The datasheet says at 50KHz it can output 125 Watts of power.
So the total power i calculated for combined ee and ii cores is 250 Watts at 50KHz.
But here i tuned the 2153 to produce 66KHz and powered the transformer through four mosfets irf3205 on each channel.
Now i am getting 300 watts of continuous power from the transformer and after rectification got 330volts DC(329.6 on meter).
I got the 300 watts from driving the ferrite inverter from 24volts 20amps of battery power (2 * 12V 20AH sealed lead acid battery).
Making this transformer was somewhat a difficult and challenging task but i successfully completed it.
Regards,
Thanks
H Sherwin, that's very interesting and valuable information, thanks for sharing, I am sure the new hobbyists will love reading this.
is it ok to use IRL640A in the high frequency section these are what I found to buy. ( I was wondering if the Rds on if its low enough).
please check its max drain/source voltage and current specs….
its 200v 18amp
I checked for some 600v 20amp fets for the H bridge side
Dear,
What i have learned and understood by doing this ferrite core inverter circuit is:
1. By increasing the oscillator frequency, the turns count in a transformer can be reduced resulting in the use of much smaller transformer which can still give good power output.
2. Rewinding transformers without keeping AIR GAP between CORE PIECES, worked the best giving full power.
According to me, the EI core transformers were easy to open and rewind without breaking the core.
Till now, i've rewound 10 such transformers and all worked best giving full power output.
I finally attained success building lightweight inverters (only upto 200W continuous, 300W peak) only after cracking the HF trafo winding theory!!!
As for now i've done the inverter circuits to operate with 12V, 24V and 60V with 10 amp/hour rating SLA battery,
But kept my power output limited to 200w continuous 300W peak only.
Thats it,
All done well with careful inspection and good knowledge about electronic components and their various
uses in circuits…….keeps me on the go…….
Regards…….Thanks…….
Thanks Sherwin, I appreciate your efforts.
your first point is correct and it's the standard principle applicable for all ferrite based inductors, however getting good results without keeping air gap or a paper gap across the core surfaces looks strange….because without paper gap the cores could get saturated and start malfunctioning.
Anyway thanks a lot for the inputs, keep posting and good wishes to you!
Sir does a Ferrite core transformer outputs the voltage in terms of pulses ?
i have a circuit of LED street lamp with me .. one ferrite core transformer is used at the output stage of the circuit… 230 V ac is first being converted into DC voltage ( about 310 V ) filtered and fed to the ferrite core transformer after some componets ( including one IC ).. the output of this transformer is then diverted to a dual ultrafast soft recovery rectifier ( BYQ28E )… and finally the output is taken from the output pin of this ic and the ground terminal.. but the problem is the leds are flashing continously…. turning on and turning off then again turning on turning off automatically…. when i have checked i came to know that the voltage between the output terminals varies in between 20 V to 100V … what is the cause for this sir ?.. i am sending you a picture of the board for reference into your hitman inbox… plz check it out and reply as earlier as possible
RT, it could be because the load is not compatible with the SMPS output specifications, therefore it is being forced to go in the shut-down mode, reduce the number of LEDs or use a resistors in series to possibly correct the issue
Dear,
What would you suggest in order to prevent iron core transformers from catching corrosion on their body?
Hi Sherwin, to prevent corrosion and rust, the iron core should be coated with a thick layer of varnish, and then after drying, it should be applied with additional layers of thick good quality oil paint
Hi swag sir,I need 5kva 310volt dc to 220 volt ac circuit please guide me how can I buy from u through ebay I m in karachi pakistan (also price detail)Thaks
Hello Gulab, you can type the exact words on Google search “5kva 310 volt dc to 220 volt ac module”, if it’s available from any vendor, you will be ale to find the address online.
Sir plz am new here, I sincerely do find your tutorials interesting although being new in this field, I do find it difficult to understand. Expecially in the area of the ferrite based inverter. Also when it comes to the mosfet, I do get confused about if both the n channel and the p channel is applied. Sir plz I really want to learn.
Hi Prayer, keep reading and understanding the concepts with patience and slowly you will begin grasping them. Apart with this website you may also find plenty of online tutorials that you can refer to gain expertise
Thanks alot sir. Sir plz I want an ATS circuit that can operate a 120kva Diesel generator. In such a way that once the grids mains goes off the fuel pump will be turned on the the generator will be crank for about 5 seconds depending on what is safe and once it is successful the the crack will be stopped and about 5 minutes delay the power will go to the load and again once the grids main comes on the power will be on the generator for 5 seconds before it moves to the grids power without any idle time before the generator will be turned off. Thanks once more sir
Prayer, I already have this circuit in this website, please use the search box and type ATS.
Sir,
i rewound an EI35 core trafo from a PC power supply,
1. Battery i used 12v 10AH as my input voltage, making another inverter circuit keeping the components as is.
i set the 2153 to 40KHz perfectly using a trimmer.
2. the ixfm series mosfets were quiet costly so to save on bucks, i decided to parallel four 3205 mosfets which mounted to 55v 440amps.
i used four on each 2153 outputs.
3. for the transformer, this time i wound pri.8+8 turns and sec.20 turns.
Now, my circuit ran quiet fine and i could power a 100W filament bulb at full brightness.
One thing, the rewound trafo was humming enough to give me a headache, so i decided to clip off unwanted noise by adding ferrite inductors at each outputs of 2153 and filtered with 10n caps.
After that the hum were completely gone.
One good thing is that using 8+8t in pri, the trafo was barely warm on full load.
Comparing it with the 5+5t trafo that i rewound previously it got hot on full load.
_______________________________________________________________________________________
4. I cracked the turns idea by thinking in this manner:
Input is 12v keeping in mind this is peak dc of an unknown ac voltage.
I divided this with root 2 and removed its AC equivalent voltage and got 8.48v
5. So 12V DC = 8.48V ACrms i decided to wind 8 turns and finally cracked the high frequency trafo winding theory!!!
THIS TIME I'M REALLY REALLY THANKFUL TO YOU FOR PROVIDING ALL YOUR SUPPORT. CHEERS TO YOU!!!
That's amazing Sherwin, in fact we are the ones who are really thankful to you for verifying the design and improving it with such determination and accuracy.
We all appreciate the in-depth info that you have so far provided to enlighten the many needy enthusiasts reading this article.
keep up the good work, and keep posting….. thanks very much.
Sir,
for any oscillator when programmed to output a particular waveform, eg., square wave here and when seen on an oscilloscope we see the square waveform but with some (sort of disturbance) noise on the generated waveform,
my question is: How to suppress this noise and get a proper square wave?
you can suppress it by adding an optimized inductor in series with the relevant signal output
Hello sir,
i have a powersafe600 series UPS, its rating being 600va/360w
Just thinking that the trafo were a stepdown type…
1. on the primary side there were 4 wires.
2. on the secondary were 2wires (heavy guage copper coil).
i tested this trafo seperately feeding AC correctly on the primary side and on the secondary i got 6.2v AC.
Now what i wish to know is:
1. How much is the secondary coil current rated for, and which factor should i take, is it the watts or the volt-amps?? and then divide it by 6.2??
Now, taking the watts and dividing with sec.voltage i get 58 amps
and taking the volt-amps, dividing with sec voltage i get 96.7 amps
here, which factor is proper in consideration??
Hello Sherwin,
use volt x amps, it will give you the most appropriate results
Ok then I will use the 555, you didnt get back to me about the tl072 puresinewave generator found in your forum, what If I wanted a clean sinewave wave out wouldnt that be better even though I know its less effecient.
I am buying up some parts now so just want to make sure of everything.
saw some diodes (RURG3060) was thinking about using those in the rectifier stage also I would just get 8 irfz444n for the high frequency stage and use 4 more for the H-bridge stage also.
I see on the IRS2453D that there is Ct and Rt what value resistor and capacitor should go there?
you will need to build the circuits stage wise, otherwise troubleshooting if any can get difficult…so first build the 300V stage with success and then we can proceed for the sinewave processor section either by using iC555 or an opamp, whatever suits best.
you can use any value for the Rt, Ct and then check the frequency for those values, once you get the frequency, you can calculate the required values for 50Hz through cross multiplication.
Ok then Ill try the 6 amp diodes I have and use the irfz44n's but since the minimum I require is 1000 watts ill go for 24v primary then. I forgot to ask I cannot get any 10mh inductors presently can it be replaced by resistors or can I use copper wire and make a coil to replicate it, if so what should I do.
OK will do,
the inductors are 10uH not mH….you can build them by winding a few turns of magnet wire over a ferrite bead or any suitable ferrite core
Ok I was wondering Can I use irfz44n Fets instead of the fets used in this schematic in the ir2153 section since I am using 12v supply, also I have some 6amp shottky diodes can I use those to replace the 4 amp general purpose diodes? The 47uf 25v capacitor connected to ir2153 did you mean to write tantalum?
yes IRF44z can be used.
the specified diodes can be used at the indicated places.
the 47uF cap should be a tantalum type preferably.
12V will not allow more than 500 watts output
I know that it works from high frequency and I didn't mean I would connect it to the circuit in this article immediately after wrapping, I'm not an expert at electronics but I don't know all things especially about ferrite cores because Information on it is hard to find.
What I was asking you really was if it's possible for me to test it like test the voltages without connecting it up in the inverter circuit, if not it's ok… I just though I could test it like how I would test an iron core if I wrapped it.
It is not hard to find about ferrite cores on the net, there are plenty of articles regarding ferrite core transformers, basically it comes under "power electronics", so you can obtain all the info under this subject.
there's no other way to test a ferrite transformer other than using high frequency
https://www.dropbox.com/sh/x5ueeohjkvy6njr/AABhmnjnhVj4PBuZ904FobVKa?dl=0
This is the core and wires
Just doing 1 wrap for 12v and 9 wraps for 120v out.. After that can I test it by hooking it up to my power companies ac supply of 115v?
yes, only if you want to see a big explosion, fire and blown fuses.
ferrite cores work with high frequencies in the range of 20kHz to 100kHz…..the home AC is specified only at 50Hz or 60Hz.
the above project is strictly for the experts who are well versed with all the basics of power electronics.
I forgot that I ordered an E-80 core, I have some copper wire I was wondering if I should wrap take around the inside part of the core before I start to wrap.
Should I place paper underneath the ends of the core to prevent them from touching and also I was planning to use tape to tape it together.
Since to core is separate should I wrap all the turn on one side them put the top section on to the half that I made the wrap on, or place then together tape it up then start to wrap?
you will need to wind it over a hard plastic or a similar non-conductor bobbin, and then gently insert the bobbin winding assembly inside the E-core as shown in the image.
this project is strictly for the experts.
you can tell them about the winding specs…or the voltage, current and the frequency specs, that would be more than enough for anybody to design the trafo
ok thanks, for some reason I have been searching the internet to find information on ferrite core transformers to me it seems its not so popular with english speaking countries I cant even source it online I was trying to see if I can get 1 to buy at 12v to 120v but no luck unless there is something that I dont understand about them.
ferrite inverter transformers are never available ready made…they need to be made to order
Also is this a square wave, if so it wont be able to run electronic circuits, I think I saw you with a modified version with a pwm feed, can I have the link and would it be able to run the most common electronics like smart tv, radios, fridge ect?
the following modifications might help to convert the above design into a reasonably good sine wave version:
https://www.homemade-circuits.com/2016/02/pwm-sinewave-5kva-inverter-circuit.html?m=0
Ill be using 120v out from the 1st circuit so ill be feeding 160v to the second circuit, where it says load on the second circuit I hope it doesnt require a iron core transoformer there, just testing between those 2 points marked load, will I get 120vac 50hz? since thats what I desire from it. Adding a transformer there would defeat the purpose of using this design so I hope I dont need one there.
when the first circuit is already creating 160V then obviously there would be no need of any other form of step-up transformer, so yes the load can be directly connected across the indicated points.
you are supposed to get around 120V across these points if the first circuit is correctly generating 160V DC
Ok thanks, looking at the inverter in this article I always wondered what was missing but I realize that you didnt add a circuit for the rectifier stage, how much capacitors would should I use in parallel for this circuit for the rectifier stage.
you may refer to the following article for all the required details:
https://www.homemade-circuits.com/2016/02/pwm-sinewave-5kva-inverter-circuit.html?m=0
Ok thanks that was straight forward, I dont want to take up too much of your time, I would like to know if you have a specific article I could read up on them where It concerns understand how they work I can seem to find out about the turn ratio, I actually want to give ferrite core design a try now that I realize that to get high power inverters its better to use ferrite core, I would like to know what types of cores I could by and how to wrap them to get for example 12 t 120v from it or if I was to order it what would I look for in terms of turn ratio since thats how I see them listed.
ferrite core allow you to get high power in compact sizes, that's the only main advantage of a ferrite core trafo over an iron core counterpart
you can refer to this article which explains the basic winding formulas for ferrite core transformers:
https://www.homemade-circuits.com/2015/07/turns-and-voltage-ratios-total-voltage.html
for educational purpose for me I would like to know within an inverter using ferrite core why is it necessary to use high frequency, based on what I understand is that you would feed 12v from your battery to FETS, then an Ic would pulse the Fets to send out a high frequency dc to ferrite core transformer, so what I always wonder is if that same 12v dc were to be chopped up at 50 or 60hz and sent to the ferrite core wouldnt it be the same, since generally the ferrite cores are low wattage.
50/60Hz may be suitable for iron core trafos, but ferrite core trafos can work only with high frequencies in the range of 20kHz and above for producing efficient results.
Sir,
i found a new formula for calculating capacitors in series, here goes it:
Suppose we have four capacitors, all non polar type rated at 440v and having 2.5uF capacity.
Now, my formula is;
Total value of capacitors divided by number of capacitors square.
so we get,
2.5 + 2.5 + 2.5 + 2.5 = 10
no.of capacitors = 4 sq
so, 10/16 = 0.625uF i.e., 625nF
Sir please think over it and tell me that is such a formula correct??
Thanks
Sherwin, I'll let you know after confirming it.
…it will work only if the values are identical, not with nonidentical values.
Sir,
in one of your previous comments you mentioned to me;
Instead of writing such interesting facts in comments, you should publish them as posts for this site and contribute to this site.
Dear, how do i do so??
Thanks
Sherwin, please refer to this page:
https://www.homemade-circuits.com/p/submit-and-earn.html
for further questions you can email me at the given address.
dear sir,would please modify its output with PWM source and facilitate to make use such an inexpensive and economical design to World wide needy people like us? Hope You will consider my request.Thanking you.Your affectionate reader.
Dear Javeed, I'll try to update the design possibly soon…
Dear Sir Majumdar, thanks for your kind service to we electronic hobbyists and man kind.My request is, please let me know,whether the Inverter is purely sine wave? And appliences like refrigerator,airconditioner,plasma TV etc…..can be undoubtedly operated through this non re-payable gifted Inverter by You selfless personification so.Wish You cheerful happy new year and never ending Ideas to you from Almighty God Creator.
Thank you dear Javeed, wish you too a very happy new year!!
The above circuit is a ordinary square wave inverter you will have to insert a PWM feed in order to convert it into a PWM sine wave version which can eb a little complex.
dear Mr Swagatam Majumdar thanks for the donated circuit.can 1500wt air conditioner be run on this 5kva Inverter ?
dear javeed, 5kva = 5000 watt approximately…. so yes 1500 watts can be operated through it.
Sir,
i made another transformer ready for the inverter circuit,
1. i prepared another circuit today and kept the oscillation frequency of 2153 at 50khz.
2. the ferrite trafo primary i wound 7+7 turns using 3 wires in parallel and for secondary i used 2 in parallel with 20 turns.
3. mosfets on each section were 2 irf3205 in parallel, gate resistances were 12 ohms 2w resistors.
4. i converted the hfac o/p of trafo to dc. this time i got 330v on my multimeter(reading 329.7)
i prepared till this point and stopped.
my question,
now with this peak voltage can i directly operate the cfl lamp or an incandescent else there is danger of explosion??
Thanks
Sherwin, this peak voltage appears to be within the normal working range of all 220V RMS rated appliances, so according to me it's fine, you can go ahead with this peak level.
Sir,
what is the actual function of a bleeder resistor in power supply circuits??
a day before i were doing a study over an old computer smps, on each dc output rail there were resistors connected after the capacitors.
I calculated their values based on the color dressings:
1. 12v output had 270ohm 1watt, i calculated the current through ohms law and got 44ma.
2. 5v output had 100ohm 0.5watt, calculated current is 50ma.
3. 3.3v output had 15ohm 1watt, current is 220ma.
before i proceed, are these calculations right??
my thought,
i noticed the resistor at the 12v output rail it were 270ohm 0.5w MFR and it burned such that it made the pcb black at that spot. fortunately its color dressing were identifiable thats how i got to know its value.
my question,
while making a power supply circuit, should i include a resistor after the capacitor stage and is it really important to have one in circuit??
Thanks
Sherwin,
It's a calculated dummy load which becomes essential for most SMPS topologies in order to keep the circuit stable even during a "no load" condition.
When there's no load connected this resistor load acts as the minimum specified load for the SMPS and prevents it from getting unstable and from a possible damage.
your calculations are correct.
Sir,
when we rectify the mains 230v ac into dc, we get 325v dc,
my question: is this rectified voltage equal to ac mains peak voltage?
coming to the ferrite core trafo in the above circuit, we have
5=5 turn in pri and 18 in sec,
the voltage induced in the 18 turns is 220v at 40khz,
now this voltage cannot be measured by a multimeter due to such huge frequency.
After rectifying this 220v high frequency voltage i get 311v on my multimeter.
Can this voltage (311v) be called the peak value of the High Frequency rectified voltage??
Now if i divide the 311v with root2 i get 220v.
HERE, can i call this 220v as the high frequency RMS voltage at the output of the ferrite transformer??
Are my above calculations proper??
Thanks
Sherwin, yes 325V is the peak value of the measured mains AC.
311V is also the peak voltage that you have measured for the ferrite trafo., because after rectification, the reading will be always equal to the peak value.
220V after dividing with roo2 is also correct, it'll be the RMS value
so all your calculations look correct to me.
hi
i understand.please give an example for(mosfets V and I should be twice of the required voltage and current spec of inverter.)
current rating mosfet is 17 amper and voltage rating is 550 volt.if out put current inverter is 3 amper and trensformer is 12 to 220 volt.and battery is 12 volt 500AH.
thank you
The output wattage is not relevant, it's the battery consumption at any instant which must be considered…if the battery voltage is 12V and max current consumption is 50amps by the inverter, then the mosfets could be rated anywhere around 30V, 40V, 50V at 100amp, 70amp, 80amp etc.
hi
(The battery AH rating must be 10 times that of the required watt/volt from the inverter).why???????
thank you
because lead acid batteries should always be charged or discharged at around 10 times less current than their AH value, for preventing damage to the battery.
hi
if iput voltage is 12 volt 500 amper, input power is 12*500=6000watt.(p=vi).but if battery is 12 volt 70amper input power 12*70=840 watt and output power is about 700watt.it is true or fulse?
and How do I calculate the amount of MOSFETs needed?
thank you
It's AH, which is ampere-hour and is different from ampere…it means if you discharge at this rate it will last for 1 hour….but practically it will be not more than 20 minutes.
mosfets V and I should be twice of the required voltage and current spec of inverter.
hi
So if I use the 4 to the transistor 5r199p.and battery had 12 volt 70 amper.i can,how much power will be in out put?and What is transformer details.and do battery 12 volt 500AH produce 5000watt or 1000w?
thank you for attention
I don't know about the specs of 5R199P please confirm it from the datasheet…
The battery AH rating must be 10 times that of the required watt/volt from the inverter.
so ideally a 500AH would be able to handle only 600 watts
hi
current rating is 17 A and VDS=550 volt.and i want inverter output is 1000 watts .out put current is 4.5 amper.and input voltag is 12 volt.ishoud I use How many of these transistors 5r199p.
thank you
mosfets will not produce watts for the inveter, it's the battery power first which must be correctly rated, and then the transformer, and lastly mosfets can be considered…
at 12V, the current from the battery must be 1000/12 = 83 amps…so the battery will need to be around 12V 500AH
hi
Can I use transistor 5r199p instead ixfh50n20 .and i use 4 transistor 5r199p.and also use 12 volt instead 60volt.and i want to design transformer again.
what's the voltage and current rating of 5R199P??
how much current do you intend to acquire from the inverter?
thanks for the circuit, but i need to know, wont there be a need for output voltage correction circuit or with the H-bridge, there is no need, cos i know in inverters, output voltage drops when loaded
that's a secondary circuit and can be included if one requires, here the main thing is to make the ferite inverter successfully, afterwards other add-ons can be included….
by way what actually brings the frequency so high is it the ferrite core itself or is it the circuit feeding it?
if its not the circuit that mean putting a normal 12v -120v iron core transformer at the end of the first circuit would give me 50hz at 120v
it's the IC that's responsible for generating the frequency, as per the core requirement…the parts associated with pin2 and 3 can be altered to reduce the frequency to 50hZ and an then iron core trafo can be employed instead of the ferrite core….
Sir,
I tried to use the salvaged transformer from the coke can inverter.
but before that i protected the inverter circuit with a 12v 20w incandescent lamp.
i would give a detail of the winding of the coke can ferrite trafo:
CONSIDER: PRIMARY 4 PINS CONSIDER: SECONDARY 3 PINS
A E
B F
C G
D
The primary data:
From pin A two wires feed inside the trafo,
One of the two wires connected from pin A ends at pin B.
From pin C one wire enters feeds inside the trafo
At pin D two wires end.
The secondary data:
At pin E one wire feeds into trafo and end at F
At pin F another wire feeds into trafo and end at G
Coming to how this trafo was connected to the coke can circuit:
firstly, the oscillator circuit were designed in a push pull config. where i also seen 2 irf3205 mounted on seperate heatsinks.
The outputs were connected to the trafo as follows:
a. drains of 3205's were connected respectively to pins a and d
b. trafo's b and c were shorted connecting to + battery……………………the primary side
c. pins e and g of trafo connected to the rectifier circuit which consisted 4 pieces of M7 diode and one 6.8uF 400v capacitor.
These were the details of the trafo connection to pcb.
And YES the salvaged trafo worked with your blog's circuit that i prepared.
Here, i rectified the above trafo's secondary output i got 321.6 volts dc.
The toroidal trafo that i made i got 315.7 volts dc at secondary rectification.
I also checked for any unwanted heating of components after attaching the salvaged trafo on the inverter circuit, none were there and everything worked normal.
For final confirmation i attached the incandescents that i did previously, all worked well, brightly using the salvaged trafo.
Once again the 'salvaged' victory that i attained!!!
Thanks
That's great Sherwin, I really appreciate your cool head and intelligence.
I think instead of writing such interesting facts in comments, you should publish them as posts for this site and contribute to this site. That will also allow you to earn a handsome passive income from me.
thanks I think ill also try one for myself also for learning purposes.
question 1) I realise that the core has 2 sides based on pics above, after winding the coil and placing the 2 sides together would I have to tape the outside of the core itself to keep it firmly together because it seems it would fall apart to me.
2) based on the first schematic the transformer looks like it has a center tap so if i was to wrap 5 turns then insulate it with tape then wrap 18 turns then insulate it with tape then wrap 5 more turns how would I get that middle leg going to the battery positive? Is it that ill join 1 set of the 10 strands of the first winding to 10 strands of the second winding then use that as the center leg?
3) If I was going to use 10 strands of wires to make 5+5 turns I would end up with 20 strands of wires so would i just terminate each side of 10 wires to a terminal block then send 2 wires out from each side?
4) since I will be using 120v how much turns will I need to make for the secondary?
The "start" of the outer 5 turn winding will join with the "finish" of the inner 5 turns and this joint will become the center tap.
treat the 10 strands as a one wire and wind them together, and join the outer and inner start and finish points to amke the center tap, as explained in the above sentence.
use 9 turns instead of 18 for getting 120V
make sure to separate the upper and lower core surfaces which join each other face to face with paper or with the insulation tape itself
its automatically ticked and not even the reply you just gave I haven't received in my email and I normally receive them there, anyway ok I understand what your saying but my second question that I have been asking, in my country I use 120v using 12v as the suply ignoring the wattage what output voltage should I get from the ferrite core I am asking if it should be 120v or is it 160v because I want to know what to tell the person who is wrapping it to what I need from it and also I need 50hz to operate my load
It's 120 that you need to tell the winder…after rectification this might become 160V
This is the first reply I got since you told me so why not boost the 12V to 120V directly. and I sent a schematic asking you if that can work whic was basically an inverter with a power supply converter the 120v ac to 120v dc and I was saying how I would change the transistors to fets for higher power, basically I want to know if that can work and I step it up to 120v would the ferrite core would be primary 120v secondary 160v or should the secondary be 120v also because at the end of the circuit I need 120v ac to my load at 50 hz
you are supposed to get all the replies in your email, if you are ticking the "notify me" box before publishing your comments.
with a 12V supply you will have to use 400 amp current for achieving 5000 watts, there's no way of escaping this requirement regardless of what technique you may employ.
yes that's correct, but I have replied to all your comments and then deleted it afterward, so I hope all the replies are still stored in your email, you can check it out.
I keep posting but I am not seeing it here, is it because I posted a link of the other circuit?
The idea behind making this whole project is to make known to the viewers how effectively one can convert battery power into mains ac to use their intended household appliance, without making use of bulky iron core transformers in circuits.
The ferrite core trafo is complicated in design in terms of winding data, wire guage size, type of bobbin used, the core size, etc.
But for me all these was just a piece of cake!
I knew the difficult part in the inveter circuit is the ferrite core trafo itself, so i prepared myself thoroughly into making it and sourcing the raw materials for building the trafo. was not at all difficult rather easy since all materials were readily available in the market.
Thats it, everything done well.
That's indeed commendable Sherwin, we all appreciate your efforts and wish you all the success for your future projects too.
Sir,
I built the ferrite inverter circuit shown in your blog and it was very easy. I made it such a way that i got results in a first shot.
The chinese inverter that i bought its circuit were far more complicated.
What i did was;
1. i removed the fer.trafo to study its winding schematic. It was an EE trafo and had 4 pins on the primary and 2 on the secondary
2. Moreover, i didn't open the trafo and inspect the winding to see how the pri and sec were wound, its turns,etc. since its core pieces were glued tight.
3. I kept this trafo aside and may attach it to your ferrite invt.circuit in the blog and see how much it can output.
To make things clear, i made the circuit which is in your blog and it worked well, on the other hand i had a chinese trafoless inverter and i seen how they made it.
You may have wondered that i made a replica of their circuits by looking at them and making it on a veroboard.
NO NO IT IS NOT SO
I just opened one of their make to see what components they used. Nothing else. Now i'm planning to use their circuits' trafo only and connect it to your circuit shown in your blog.
OK Sherwin, thanks for the clarification, however the salvaged trafo might not work with the above circuit, because inverter transformers are specifically designed and matched for their own specific circuits, so you'll need to be careful while doing it.
Sir,
The current consumption of the inverter are as under;
3.56 amps for a 25w bulb
3.88 amps for a 40w bulb
4.05 amps for a 60w bulb
3.65 amps for 25w soldering iron
Even a 100w bulb worked! circuit drew almost 4.8amps(~4.77).
Sir,
This experiment happened sucessfully only since i happened to buy a cheap trafoless chinese inverter and studied their circuit.
These inverters were rated something like;
Input-12v
Output-150w continuous 180w maximum
Few of these came in the market, old and tattered in fashion, some were good and their shape was in a coke can type, and also had few nice features.
I brought one home and connected a 100w incandescent at its output.
The moment i powered them, i was shocked the way the bulb glew, i wondered damn what circuit they have used.
I will give you the details of the coke can inverter circuit as i am free.
Sherwin, sorry I am confused, which circuit did you build? The one which is shown in the above article or the Chinese inverter circuit??
and how the above circuit and the Chinese inverter circuit be related?? please let us know about it?
Dear,
Yet to tell you the CURRENT CONSUMPTION of the inverter circuit at different loads, i will do so as i get time.
Once again,
THANKS
sure!…many thanks to you.
Sir,
The bulb 60w is glowing at full brightness similar to driving even on ac mains.
Indeed, my ferrite inverter circuit got completed at the first shot, since i did so by inspecting every stage of my unit.
I tested for possible shorts between all connecting points in the circuit.
I tested for the output frequency it were 60KHz(i set it manually).
One thing is i connected diode between pin1 and pin8 of ic, here the above circuit showed pins 1 and 8 short being connected to positive,
I did dummy test on breadboard of the ic 2153 only,
shorted pin1 and pin8 of ic, then connected the oscillator components and added bypass tantalum cap,
HERE I WAS NOT GETTING OUTPUT PULSES INSTEAD IT WAS A SHORT CIRCUIT, IC WAS GETTING HOT.
Then i realized the importance of the diode between the ic pins.
After connecting this diode, only then the ic began oscillating smoothly here and i set the frequency at 60KHz
Now there is no heating.
Once i began to connect the ic outputs to the rest of the circuit, my circuit then worked properly,
I finally then checked whether or not i'm getting frequency at the final respective mosfet drains, here everything worked normal and output frequency was 60.08KHz.
i finally connected the transformer, proceeding with connecting a 60w light bulb. Here the bulb glew instantly,
on the other hand i was shocked to see the way the bulb lit,
Indeed, credit goes to you for providing all circuit details, i am really thankful for that.
I am looking forward to even help other newcomers in building this project since this project was very easy to me.
Regards,
THANKS
Hi Sherwin, thanks for updating all the info, all these look very impressive.
However the diode across pin1 and pin8 does not have much significance according to me, because connecting the diode will make pin8 just 0.6V less than pin1…so if pin1 is 12V…pin8 will be rendered 11.4V with the diode…so this doesn't look like something crucial that would alter the circuit's performance
but anyway I appreciate your efforts a lot….and hope to see more from you.
Sir,
I'm done with the winding of the trafo, here i did some changes;
1. i used 5+5 turns in primary and 20 turns in secondary
2. i had the ei core trafo on hand but still preferred the toroidal core.i used two core pieces.
3. i unwound those cores, glued them with fevikwik and kept aside.
4. once both core attained firmness, i covered the cores with yellow adhesive tape.
5. i then begun winding the core.
6. after finishing i attached the trafo with cable ties and then covered with tape.
7. i tested for shorts between windings and then connected to the inverter circuit.
as stated in previous comment i used two mosfets on each outputs of 2153.
Now the whole circuit is ready.
i then connected 60w incandescent bulb.
i then attached my 12v 7ah battery,
WOOOOOOW the bulb glew at full brightness, i couldn't imagine
ONE THING frequency finally was set at 60KHz.
I'm finally done with this project.
i appreciate your kind replies to every comment stated by me.
Regards,
Thanks.
That's amazing Sherwin, I wonder how you could succeed at the first attempt since you are a newcomer in this field.
anyway that's a great achievement…..congrats to you…and keep up the good work.
Thats exactly what the manufacture just told me. I actually need 120v ac from the output of the inverter so I told him the output should be about 160v from the ferrite core instead of 220v, also is it possible for me to actually input 12vdc from the source and use a dc-dc converter to step up the 12v to 60 volts or higher to feed the circuit so that I can use smaller wires to achieve higher power.
if you use a DC to DC converter that would again demand 400amps for the 12V for boosting the value to 60V at 83 amps…then feed this 60V / 83 amps to the above inverter to get 120V @ 40amps…
so why not boost the 12V to 120V directly….
Ok kool I did that before but I got 416.6 amps I was just wondering if a ferrite core would really push that much amp, and I thought the amps would be lower than that on the ferrite core and then stepped out at the output of the second circuit by the output fets, but thanks for the info Ill pass it on t them and then get back to you if anything.
the calculation is correct, but the value looks impractical…..that's the reason the voltage needs to be more…even 60V will require 5000/60 = 83 amps, which is huge
the fets and the trafo together have to handle this massive current in order to produce the output wattage
Sir,
some day i happened to salvage a toroidal core from an old computer power supply i purchased second hand. Its specs are;
Core color is white/yellow
The outer diameter measures: 1.06”
The inner diameter measures: .57”
The height is: .44”
are the given specs. enough for winding up the core and building the transformer.
Just want to keep the toroidal core as an alternative.
OK great. thanks for the update
Okay,
now i will build the trafo as you described in the article, but will use 2 strands of wire together for winding the pri and sec.
also, the circuit part has almost got completed, yet to attach fuse and heat sinks.
I will tell you the results within a day or two.
sure, all the best to you.
hope you succeed with the project, because this design is strictly for the experts and you are fairly new in the field.
I would aim for the same 5000 watts but because i am using 12v supply i am wondering what curreent ratting would I need to tell them to make the ferrite core at
if you divide 5000 with 12 you will get the required amperage value for your transformer.
Sir,
the 5kva schematic needed 10 wires to be wound simultaneously while winding the primary;
but since i am trying the low power version i want the circuit to give 100w at the output only.
1. for 100w output, while winding the trafo how many wires would i need in parallel in primary and sec.
2. would 2 mosfets be sufficient on each channel of the ic outputs for 100 watts of power.
Thanks.
Sherwin,
I don't have the calculations, you will need to do it with trial and error.
two mosfets (IRF540) would be more than sufficient for 100 watts…..or even 1000 watts.
Sir,
I am making a LOW POWER version of 100 watt only, here i need your help.
1. For the trafo to oscillate at 40khz, would i need to configure the 2153 outputs to a bit higher frequency say 45khz, since i think there could be a frequency drop after connect the trafo to the circuit.
Is that changing necessary here.
2. I got the ferrite trafo ready for this inverter circuit, but it is an EI core. salvaged from an old pc power supply.
3. Should i need to add spacers between the core pieces? if you suggest some please specify me which material.
4. I noticed in some ferrite trafos, manufacturers add a copper sheet between the windings, what purpose does it serve? should i add it when rewinding the trafo?
5. For resistors what does the tolerance value mean, i have heard of 1% and 5% tol.and which type is best? at what wattage are the 2r7's rated at?
6. What diodes are dsem2-06a in the diagram, picture represents a zener type, there is no google response for the above value, any substitutes?
7. What is the purpose of the coil in series with the diode?
I am building this circuit from today so please help
Thanks
Sherwin, the answers are as follows:
1) the frequency will not drop, but anyhow the 40kHz value is not critical, it can be little here and there.
2) EI core will do.
3) use paper pieces as spacers between the EI contact surfaces.
4) it's for an increased isolation and suppressing noise, but PVC insulation also works equally well and offers good isolation.
5) tolerance refers to the slight value difference between the actual measured value against the printed value
6) refer to this datasheet:
datasheet.octopart.com/DSEI12-06A-IXYS-datasheet-14472.pdf
7) It's for protecting the diodes from switching transients
ok makes sence, so finally ill as because in the info about the build of the inverter its changing the DC voltage of 60V to a higher 220V at a lowered current im not sure how low the current would be.
so my question is a manufacture may ask me what input current or output current do I expect to get from the transformer what would I tell them? (remember in my case I would be using 12v supply what would the current be for that voltage range, secondly what would the current be for 60v in case I want to try that also.)
what is your requirement? how much watt do you intend to acquire at the output?
So if i want to use the ferrite core I would have to use 60v from my batteries as input nothing lower for that specific circuit?
I want to try ferrite core so I would like to give the manufacture specs to work from to build it, would I just let them know that I need the primary to handle 60v and the secondary should produce 220v at 40khz or should I tell them to wrap 5+5 turns on the primary and 18 turns on the secondary.
You can use any desired voltage and current as per your preference, by just modifying the primary side of the inductor…please see your previous comment for the answer
the calculation is very linear….for 60V if it's 5 turns, then for 12V it becomes 60/12 = 5/z = 1 turn
or 1 + 1 turn @ 40 kHz
Sir,
for the above circuit what should be the ideal frequency output of the ic to drive the ferrite transformer?
secondly, i wish to build a low power version of this ferrite inverter say 100w and input to circuit will be 12v.
for 12v input how many turns would i require at the primary of the ferrite trafo and how many in the secondary?
Thanks
Sherwin,
it's given in the article as 40kHz, the number of turns decide the frequency and vice versa.
use 2 + 2 turns at 40kHz, secondary will be as is.
1) if I use 12v battery source to power this circuit will I need to change anything for example to ferrite core transformer?
2) if not will it step up the same 12v dc to 220v dc at 40khz?
3) Suppose I decided to use the 50v center tap transformer you said we could use in place of the ferrite core would it still be a 50v center tap transformer if I used a 12v battery supply?
4) And using a iron core transformer would it still produce the same 40khz or would I have t get a iron core transformer made specifically for 50v ct and that can operate at that frequency?
yes the primary winding 5 turns will get smaller with a 12V supply
since the secondary winding will be 220V so the output will also be 220V
the battery voltage and the trafo primary should match, for a 12V batt you will need to use a 12-0-2V iron core trafo or a9-0-9V iron core trafo
for iron core trafo the frequency will need to be changed to 50Hz for 220V output and you won't require to build the last circuit
Dear sir,
In the ir2153 ic connection, certain circuits has a diode placed between pin1Vcc and pin8Vb pins, in your circuit you have shown pins 1 and 8 shorted. what is the function of that diode ?
If i set the oscillator components to output a 50Khz, will pins ho and lo show 50Khz or half frequencies on both pins?
Again, how to buffer the high and low outputs into a single clock output?
Thanks
Dear Sherwin,
The diode is placed when the Vcc and the high voltage line are joined together via a resistor, but here both the lines are separate, and Vcc is powered from a different power source.
it will be 50kHz for both the outputs….this is what I assume
the outputs cannot be made into a single…and it doesn't make sense..
Dear,
i am doing a 555 inverter project,
currently i sucessfully built a low power inverter 50hz using 12v 60w trafo. i could light up one 20w cfl only.
battery used was 12v at 7ah capacity.
now, i have a 100w transformer rated at 12v in a 2wire primary and secondary config.
IC 555 datasheet says something like this,
"high output current can source or sink 200ma"
that means a single 555 can output 200ma current at pin 3 (i am referring to astable config. only), am i right.
so i though if i need more current, i should parallel 2 555 ics. i.e.,i could get upto 400ma at pin 3, am i sensible? should i do this?
OR should i go in for sophisticated driver ics like 2153 at least in my 100w inverter project?
if i plan to use the 2153, it has 2 outputs, how should i buffer the outputs into a single output so i can pass it to a 2wire trafo.
please help me.
Thanks.
Dear, that doesn't make sense, the IC 555 is an oscillator, timer IC, it cannot be used like a power device…and anyway it would never be possible to parallel them for an inverter application.
so you must go for a professional driver IC, may be by connecting two half bridge ones…. or a single full bridge IC..as shown in the following links
https://www.homemade-circuits.com/2013/09/half-bridge-mosfet-driver-ic-irs21531d.html
https://www.homemade-circuits.com/2014/01/simplest-full-bridge-inverter-circuit.html
…just Google "half bridge inverter circuit" you'll get the required design online
please give the detail of L1 such as truns, core size,wire gauge etc
salut ! imi poti spune te rog cate spire trebuie in primar si secundar pentru o tensiune de 12v in loc de 60v pentru un transformator de ferita, seria EE70. Multumesc !
sir please can you provide me the connection diagram for wireless power transfer using high frequency transfer….and about high frequency transformer(220v,50hz as input to 12v,40khz output)….
Ashutosh, presently I do not have this circuit, I'll try to investigate and let you know if I happen to find any…
I read up about both converters and understand them.
if I plan to build this inverter could I buy the ferrite core transformer if so what specifications would I ask for how could I identify the transformer by specs?
with this exact circuit could I use a 12v dc input with the ferrite core? if so then I would assume the output voltage would be 120v in my case but the frequency would be lower than 40khz, if I am correct about that then would changes have to be made to the lower circuit to then get 50hz at 110vac?
I don't think these would be available ready-made, you'll have to get it wound from a transformer winder or simply do it yourself with the help of a winding machine.
for acquiring a 120V RMS the output from the first circuit will need to be around 160V DC, so the transformer will need to be wound as per this value.
the lower circuit can be kept as is for a 160V input and 60Hz frequency
Well first I have to understand how those transformers work, normally I expect to get for example 6v between 2 leads to go to an iron core transformer and the battery making the third, with a ferrite core I don't see a voltage rating, so I don't know how to apply it to a normal circuit or any circuit at all
just Google "how buck/boost converters work", you'll get plenty of articles explaining the concept online
ok then, so I guess I have to figure out how those transformers work, and so far they seem more complex that iron core transformers. It seems as if the circuits have to e designed to use ferrite core and it cant be replace with a iron core.
in fact these are much easier to wind than iron core trafos, the only disadvantage is that you cannot get 50Hz or 60Hz frequencies directly from ferrite topologies, rather will need to process the output through a bridge driver network for achieving it.
Hello Swagatam, yes i did sent the mail. hope to hear from you soon on that.
sure Tonyben, it's in the que, will try to finish it soon….
Hello Swagatam, did you get my email on the design idea ?
Hello TonyBen, I received an email from Mr.McAnthony Bernard, I believe it was sent by you.
Let me assess the requested design, I'll try to figure out an appropriate circuit diagram for the same and post it for you…soon.
I would think so, I think those transformers normally have some yellow plastic covering the coil windings, so if I wish to achieve those results are you saying I would have to use ferrite core transformers?
yes all battery operated compact inverters rely on ferrite transformer, there's no other option…
Hello Swagatam, thanks for the good work you doing.
Can i have your email? i want to discuss a design idea with you to see what input you could make to it.
Thanks Tonyben, my email ID is admin@162.240.8.81
Hello Swagatam , you recommended IRF3205 to be use at the output of the H bridge stage that has rail voltage of 310v. Can that mosfet handle such high a voltage.?
Hello Tonyben, IRF3205 will not work since it's rated to handle only upto 55V….instead IRF840 would be more suitable for the mosfet bridge network circuit
I have done the required correction in the article, thanks…
I realize the ready made inverters dont carry big transformers not even for something like a 3000 watt, is there anyway I could do a transformer setup to give me powerful wattage of 3000watts and above without getting custom made transformers?
what you are referring to are inverters using ferrite core transformers, exactly similar to the one discussed in the above article.
is it possible to get 3000-6000 watt transformers for inverters, like 12v or 24v- 100v ac, because I can never find transformers like that.
no not possible, these will need to be made-to-order
can i use 60v 7ah battery for this circuit? can it power the inverter and make it function well? i am asking this question because i want to connect 12v 7ah in series. Thanks waiting for reply
yes 60V 7AH will work and will provide around 120 watts of power….
Dear sawagatam
second circuit what is CT and RT value please explain
Tks
chandana
Dear Chandana,
It decides the frequency of the inverter, you can select it appropriately for fixing 50Hz at the output
ok sir i want to ask you again if yes if2110 can replace the two circuit wha t can i do or nothing will going to change? 2110 and irs2453 and ir2153 are they the same pins?
please check the datasheet of the IC, yes the pinouts will be almost the same, but better to confirm from the datasheet
ok sir thank you ,has this circuit tested?
sir this circuit need another 60v dc? sir please can i ir2110 in place of the two ics? thank you
Not yet tested but I am sure the design is 100% correct technically and will work if built correctly…
yes ir2110 will do..
ok sir,please sir in the first circuit there is diodes can you please tell me any common diode can 1n4148 or any value of zinner diodes? these are the diods MUR415,DSEM2-06.any replacement of it?
please Google and find the datasheets of the indicated diodes…then check at what voltage and current these are specified…once you know this you would be able to identify and determine a suitable equivalent for the same…..1N4148 will not do.
hi sir it been a while thank for the good circuit im interesting in this circuit but there is one thing do not understand and it will be difficult to get it,the two circuit should connect together or it separate? can you please give me any equivalent type of the ic irs2453? or can i replace it with sg3525,TL494?
hi daniel, IRS2453 is a specially designed high side H-bridge driver IC, it cannot be replaced with 3535 or 494 ICs…it can be replaced with another full bridge high side driver only
the output voltage from the first circuit becomes the supply voltage for the H-bridge of the second circuit
Good day Sir, what about the construction of the charging section in the circuit diagram?
Good day Muhammed, I have many battery charger circuit posted in this blog, any one of them can be suitably used with the above circuit for the required operations.
Good day to you Sir Swagatam,
Would like to ask you about the symbol load in the diagram.
Does it mean the consumer side already?
Thanks and best regrads,
Radley
Good day Radley, load indicates the appliance you would be interested to operate from the inverter….it's the final output from the inverter which could be used for operating the intended gadgets and appliances.
Good day Sir Swagatam. Hope you're feeling great today. could i ask you for some expert's advice? Which is better to use a Pure sine wave or the pulse width modulation invereter? And also, do you a PWM design which has a capacity of 5kva?
Thanks and best regards,
Radley
Hi Radley, both the counterparts are good, but PWM based are cheaper and more efficient.
Presently I do not have a 5kva PwM based design, if I find one will let you know.
Dear Sir Swagatam,
Thank you very much for the information.
More power to you and may you always be in good health.
Best regards,
Radley
Thanks Radley! It's my pleasure!
Good day Sir,
Do you other design about a 5kva inverter that has a transformer without center tap.
Thanks and best regards,
Radley
You can try the second circuit separately for your application. Ignore the first circuit.
Connect the mosfet common drains/sources with +/-24V, and connect the transformer primary across the points shown as "load"
Hello again Sir,
My transformer is 24V-0V. without center tap.
is it still possible for me to use the above circuit.
Thanks and best regards,
Radley
Good day Sir.
Is it possible to connect the IC to the battery which is 12 Vdc. Since, I'll be using 4 pcs of 12V. 2pcs connected in series and then connected in parallel with the other 2.
Thanks and best regards,
Radley
Good day Radley, yes that would do, but use the battery which has its negative connected with the circuit negative.
Good day Sir.
I would like to ask your help again if this circuit is applicable also to 24V input voltage. cause i already have a 24V/220V transformer.
Thanks and best regards,
Radley
Good day Radley,
yes a 24V transformer/battery could be used in the above design, but make sure the IC gets a 12V regulated supply only
Good day Sir.
Is it possible for me to have a detailed list of materials for the inverter.
Thanks and best regards.
Radley
Good day Radley,
Please click the diagram to enlarge it, all the numbers are appropriately labelled beside the individual parts, you can easily note it from there.
But d concept is different, in d link homemadecircuitsandschematics.blogspot.com/2012/09/making-200-watt-compact-pwm-inverter.html?m=1 high and low frequencies were used, but d configuration in dis 5kva transformer is just like a normal iron core Transformer(no high frequency).
please check the article, now it includes the low frequency stage also….
Ok… But please am really interested in the ferrite transformer design because of its efficiency and light weight.
you can try it as per the given instructions.
Pls…. is dis circuit tested and trusted. Has Dhrubajyoti Biswas
Already tested it to work? Thanks
yes it is a tested design, but the ferrite transformer will need to be designed correctly.
Alternatively a 5kva iron core transformer could be used with primary 50-0-50/100amps and secondary 220V or 120V
Please am seeing two different diagrams here, where will the second diagram be?
Please sir Can you give me the list of everything needed to run circuit?
Hello sir khalid here thank you very much for reply . How are you sir hope you are fine.sir now i got 50 htz frequency from ir2153 now i set to 50htz .iam using 24v transformer for supply and getting 35v after diode and 2200 capacitor for safety i was using series bulb of 100w now i am getting 123 output from ferrite transformer so dew to the series or input only 35v thats why it is half means 123v only what will be the reason because the design is for 60v but using only half supply may this is the reason we are 123v output may the ferrite transformer not good what do you suggest sir. Before the frequency was very high now i modified so got good. Now i set to 50htz but output only 123v dc what could be the problem sir please reply i think we very near to the success. Please reply waiting for your reply thank you very much sir i am still very happy because any failure i got some success by your help thanks please reply i will back with result .
Hello Khalid, the smps frequency should be around 50 kHz, not 50 Hz, …..yes lower input voltage will cause the output voltage to be lower proportionately.
Hello sir how are you thank you very much for reply thank you very much you spreading the skills to us peoples me in the world sure we will become a technician through your site thanks. Sir i got 60v transformer i connectect 5kva inverter circuit and set the frequency to 50khz but when i put on the frequency goes megha htz and i checke the voltage by dmm on high amps diode output is 265 to 280 but still i not connect hbride section. So why the frequency going to meha htz this is first? And second ? How much should be the voltage at high amps diode side .please need your thankd help waiting for reply.please take care i will back with result.
Hello Khalid,
which high amp diode are you indicating? Is it the dsem2-06a diode?
You should check the voltage only at the secondary side of the transformer, and nowhere else!
Regarding the MHz issue, I have no idea, I guess you must verify the frequency with an oscilloscope….a small scope will cost only $30.
Hello sir thank you very much for reply how are you sir .i am pointing 30amps where secondary connected and senond thing 60v transformer i am using i connect 4diodes supply reduced 4 to 6 volts but when i swith on the voltages becomes 80volts output from ferrites tr shows 270 to 280v dc and the frequency goes in megha htz befire swith on i set to 50khz .these are 3questions i need your help please reply waiting for reply thank you very much i will be back with result. Please take care khalid.
Hello Khalid, You will nee an oscilloscope to test the frequency, and voltages accurately, without a scope it can be impossible to understand what’s going on in the circuit.
you can see the example of a small oscilloscope in the following article:
https://www.homemade-circuits.com/1500-watt-pwm-sinewave-inverter-circuit/
Hello Mr.
Hope u r fine
May i ask u
How we can put a feedback to control the output voltage in this circuit?
Thank u a lot
Hello, feedback can be added through an op amp circuit, whose input pins can be configured with the inverter output through bridge rectifier, and the op amp output can be connected with pin3 of the oscillator IR2153IC.
Please sir is it possible to buy China made modified sine wave inverter and convert it to pure sine wave inverter
Dadid, it may be possible if the mosfet gates are accessible for integrating with an external SPWM