The main technical function of the proposed voltage regulator is voltage stabilization. It is capable of stabilizing an input voltage ranging from 0 to 600 Vdc to an output voltage ranging from 100 to 560 Vdc, with a maximum current of 800 mAdc and maximum power dissipation of 100 W. The unit also exhibits good stability, with a stability of less than 0.1% after 15 minutes of constant input voltage, and a rejection of input ripple greater than 60 dB. By Atul Shah
Often relegated to the status of a neglected or poorly studied 'add-on component' due to lack of interest, the power supply of an electronic circuit can be a source of many disappointments. The following article reminds us of some fundamental points and proposes the designing of a versatile 600 Vdc high voltage regulator module.
The main characteristics of a power supply are the required 'voltage' and 'power', internal stability under variable load, drift over time, and noise rejection.
Power supply
The voltage and current data are quickly fixed according to the demand of the circuit. The internal impedance, on which load stability, time stability, and noise rejection depend, is often a characteristic suffered by the circuit design.
For example, a 30W class AB2 stereo tube amplifier can easily see its current vary between 100mA and 400mA. The high voltage, rectified and filtered by a "choke" coil, will see its voltage drop by several tens of volts, especially if rectified using a valve.
This means that the power supply collapses at the moment when your amplifier needs it the most! The internal resistance of a power supply represents a major key, especially as the voltage is higher.
Any passionate amateur has already experienced its effects, such as "motor boating," an oscillation that results in a slow pulsation that sounds like a boat motor noise in the speakers.
This instability is mainly caused by the power supply's internal resistance being too high.
Note also that this phenomenon is influenced by too much feedback and circuits that go too "low" in frequency.
Our study Regularly confronted with the problems described above, we have developed a high-voltage stabilizer module based on the circuit that we use in many of our projects.
With small dimensions (80 x 40 mm), it fits into most designs. Furthermore, it allows for the elimination of the cumbersome filtering choke. It can be used for the universal stabilization of any voltage between 100Vdc and 600Vdc.
Circuit Description
The 600V regulator circuit module is inserted between the ballast capacitor and the load as shown below.

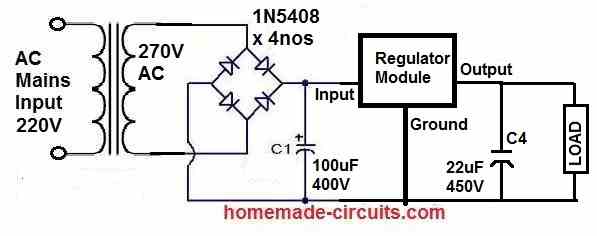
Rectification and electrolytic capacitors are external. Only four connections are required: the input and its return, the output, and its return. The two returns are connected to the floating ground of the module.
The voltage stabilization is achieved at the collector of Q1. The 10.7 V present at the two zener diode terminals biases the emitter of the PNP transistor to 10V, and a stable current of 1mA flows through resistor R2 of 10kΩ. This same current develops a stable voltage across resistors R3, R4, and P1 at the collector.
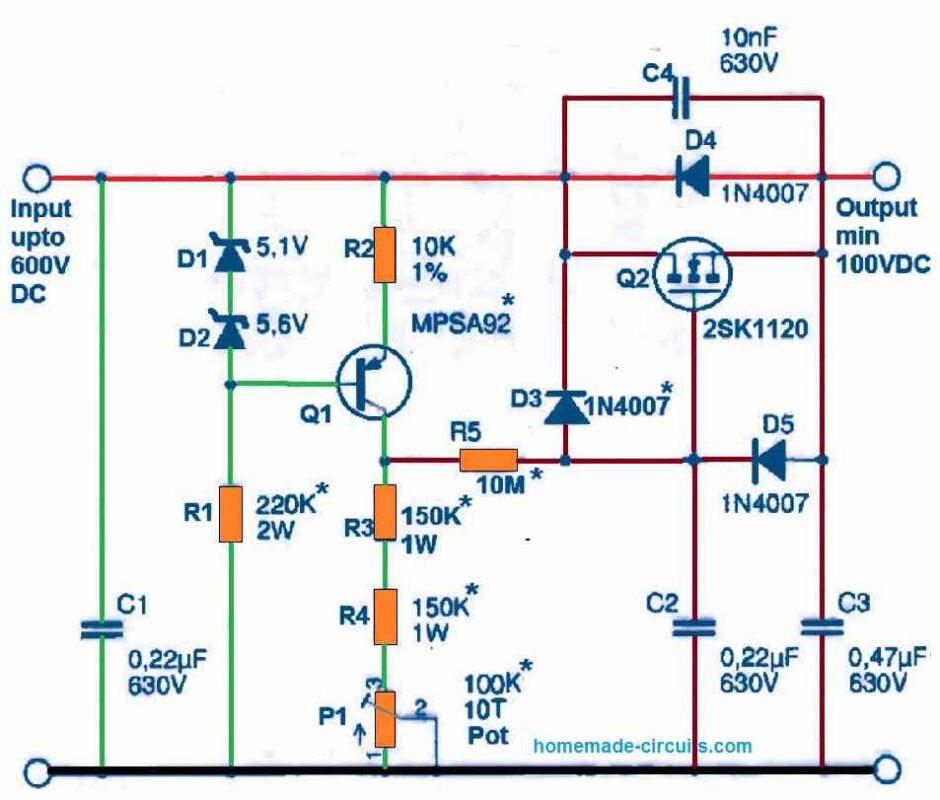
This voltage is filtered by the R5-C2 filter and biases the gate of the MOS transistor/Q2. The output voltage is taken from the "source" of Q2.
Note that the Vce voltage of Q1 can vary considerably. In fact, the input voltage is not filtered and can have a ripple of several tens of volts. Additionally, this voltage varies according to the vagaries of the sector and the variations in the output load current.
The voltages indicated on the diagram are those expected for an input voltage of 380V to 450V and a stable output voltage between 300V and 400V.
As the module accepts many other values, here are some indications to define certain components. The values of D1, D2, and R2 are invariable. The capacitor values are not critical as long as the same orders of magnitude and service voltages are respected.
Components marked with an asterisk can be changed according to needs. First of all, to ensure proper stabilization, it is imperative to maintain an input voltage that is about 20 volts higher than the output voltage. R1 must impose a current of 2mA to 3mA in the zener diodes.
Resistors R3, R4, and potentiometer P1 are calculated to develop the desired voltage based on the 1mA current that flows through them.
The PNP/Q1 transistor is an MPSA92 that supports 300V.
It can be replaced by a 2N5401 if Vce does not exceed 150 V. The R5-C2 filter allows for a 70 dB rejection of the ripple at 100 Hz, but the high voltage takes about twenty seconds to settle. By replacing R5 with a value of 1 MSS, the voltage settles immediately and the ripple rejection is still 50 dB.
It should be noted that with a typical choke, the attenuation of residual ripple is about 20 dB. Additionally, the choke adds a resistance of several tens of ohms to the internal resistance of the power supply.
Finally, the chosen transistor Q2 is a 2SK1120 from Toshiba. We chose this one because our BUZ305 became unavailable.
The 2SK1120's TO-247 package has two advantages:
- The length of the leads is 20 mm (15 mm for the BUZ305)
- The top surface and the mounting hole are insulated, eliminating the need for an insulating sleeve.
However, it is possible to replace it with a 2SK1489 with a maximum power dissipation of 200 W.
The regulator circuit module operates from an input voltage of around a hundred volts that can be raised to a maximum of 600 Vdc. It must deliver a minimum current of 20 mA and can easily reach 1 A, provided that the MOSFET's dissipation limits are respected.
Heatsink Specifications
The heat sink also has a thermal resistance with respect to ambient air, which can be reduced to very low values by using a fan. These thermal resistances must be taken into account as they cause a shift in the graph towards lower values.
Practical example: suppose the ballast transistor consumes 30 W, is insulated by a 0.85°C/W spacer, and is mounted on a 1°C/W heat sink. The heat sink removes the heat, and the temperature rise will be 30°C, plus the 25°C ambient temperature, totaling 55°C.
The transistor temperature will be even higher, by 25.5°C (30 x 0.85), due to the thermal resistance of the spacer, making it 80.5°C. This is still within the safe range, as the maximum allowable dissipation at 85°C is still 80 W.
Different mechanical mounting configurations have been provided. The first is mounting on an aluminum block of 40 x 80 x 6 mm with a spacer for integration into a closed chassis. If the aluminum block is screwed onto the chassis or an external heat sink, the module can dissipate up to 40 watts, which is more than enough for most audio applications.
The second possibility is external mounting. For this purpose, the module is placed on an aluminum base of 84 x 70 x 5 mm, fixed to the chassis, and protected by a transformer cover of type E184. The allowable dissipation is also around 40 watts.
The third option involves mounting the transistor without a spacer. The electrical insulation will be between the aluminum block at the input HT potential and the heat sink.
The thermal interface is located between the 40 x 80 mm aluminum block, which has an area of 32 cm², and the heat sink.
The thermal resistance of the insulation will be around 0.08°C/W. With a fan-assisted heat sink, it is possible to dissipate 120 watts, which is mainly applicable for laboratory power supplies.
Use & Technical Specifications
This 600V high voltage circuit module integrates all the essential elements for stabilization and can be mounted far from the voltage source and its use.
All tests have been carried out with 50 cm leads between the ballast capacitor and the module, as well as between the module and the loads, without any instability problems. The module's own internal resistance is around 5 Ω at constant input voltage.
However, this resistance is influenced by the transformer's power. For our test, we use a 110 VA transformer, a bridge rectifier, and a 100 pF buffer capacitor. The internal resistance of the entire setup is then established at 13 Ω.
When integrating the module into a design, it is advisable, in the first instance, to protect the module with a quick fuse and a hundred ohms resistor to ensure that the output current is limited to an acceptable value.
With such a low internal resistance, any short circuit in the output line will be fatal to the ballast. The stability of the output voltage is measured by varying the input voltage. A variation of 330 Vdc to 400 Vdc at the buffer capacitor, equivalent to a ±10% mains variation, produces a 2 Vdc output variation.
After stabilization for ten minutes with a constant input voltage, the output voltage remains within a range of 0.1%.
The rejection rate is the ratio between the input ripple voltage and the output voltage. For a current consumption of 200 mA, the input ripple voltage is 6 Vac, and the output ripple is 2 mVac, resulting in a ratio of 3000 or 70 dB.
The table of technical specifications shown below reflects the various possibilities in voltages and currents. We must not forget that the values of the voltages, currents, and powers are intimately linked by the relation:
(Vin - Vout) x I = P.
Technical Characteristics | Specifications |
---|---|
Maximum Input Voltage (*) | 600 Vdc |
Output Voltage (`) | 100 - 560 Vdc |
Current (*) | 0 - 800 mAdc |
Maximum Power Dissipation (*) | 100 W |
Stability for Uin +/- 5% | 41-0.5% |
Stability for constant Uin | <0.1% after 15 min |
Ripple Rejection (*) | >60 dB |
Residual Ripple (I=250 mAdc) | <3 mVac |
Static Internal Resistance | <10 Ω |
Internal Impedance | >100 Hz <10 Ω |
Dimensions (LxWxH) | 80 x 40 x 40 mm |
Weight | 100 g |
muito bom o seu circuito vou utlizalo como fonte em meus amplificadores valvulados.muito obrigado e parabens por seu trabalho.
You are most welcome! Glad you found it useful! Let me know if you have any further questions or doubts!
bonjour mr swagatam je realisé un circuit qui permet de transformé une tension 220Vac a une tension 127Vcc 1A est ce que vous pouvez m’aidé pour le realisé merci d’avance
Hello Mr. Swagatam, I want to create a circuit that converts 220V AC to 127V DC at 1A. Can you help me with its design? Thank you in advance.
Hello Charaf,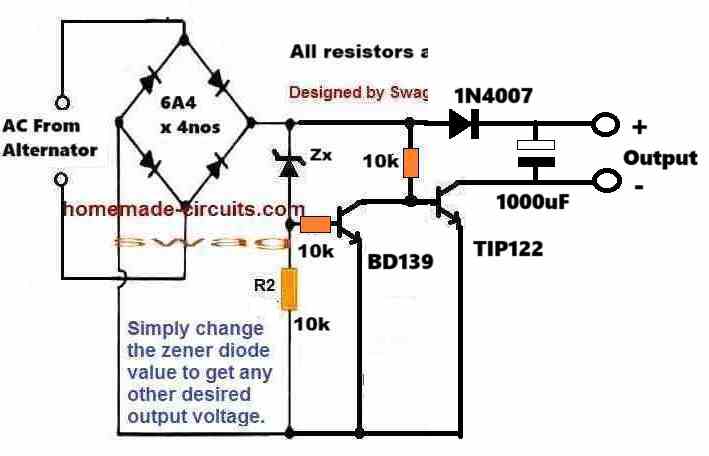
You can try the following concept:
" rel="ugc">
Just make sure to include a 22uF/400V PPC capacitor in series with the input mains supply.
And replace the BJTs with MJE13005 or equivalent, and use a 150V 1 watt for the zener diode. The resistors must be 2 watt rated.
And also note that this circuit is not isolated from mains AC, so be extremely careful while handling it.
Have a 918W 310V DC motor as generator, I want this to make a 80V constant DC output to charge my bike battery with max amp it produces. since generator cannot provide constant 310 at the time of start so i need variable input from 100-280-310 but need 80V constant output, can i use this circuit to make so?
I would rather recommend the second design from the following article, because it is a tested circuit:
https://www.homemade-circuits.com/0-300v-variable-voltage-current/
can it handle 5-10amp since my generator is 918 watt and if dropped to 80V then amp can be roughly 10+. is it fine to handle such? you mentioned 100mA max in output.
Current output can be increased by modifying the R2 value in the previous circuit, and also by changing the MOSFET accordingly.
R2 = 0.6 / Max Current Output
However, stepping down 310V to 80V with a linear regulator would cause huge dissipation and heat generation by the MOSFET.
In that case I would recommend using a buck converter circuit instead.
Yes, buck will be my 2nd project however this time I’m planning to use LM2596 buck to replace your transistor feedback since there need 10.4 v as per your design, hopefully it will work. I’m just concern on the amp output. am using 40T321 IGBT even higher than that, lets see.. do you mind if I get your mail address, i need to be connected with you, mine is kazinuraalahi@gmail.com
There’s no feedback transistor in my previously linked diagram. The BC547 is used as a current controller, to limit the output current to the load.
" rel="ugc">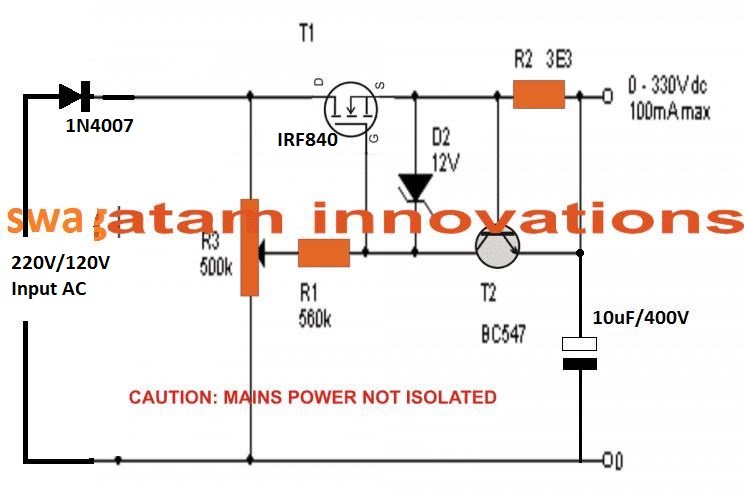
I am not sure how the LM2596 buck converter can be used in this circuit to minimize dissipation, it cannot be used according to me.
A buck converter designed to handle 350V – 80V must be connected directly to the input 300V DC source for ensuring maximum output efficiency.
You can feel free to discuss the issue here, I will try my best to solve it for you…
Hi- I’m sorry, i was talking on the earlier design not this. anyways, would you please discuss how this circuit can stable the output to 80V dc with 10A current regardless the input between 100-310V, I’m really confused. 547 is not capable in handling such current. i just simulated earlier circuit, at the output giving 250-270V dc and the P1 V/R not functioning any. I’ll simulate this also lets see..
The BC547 does not handle the current directly. When current exceeds the set limit, the BC547 conducts and short circuits the MOSFET gate/source to stabilize the output.
The circuit is tested practically by me and it works perfectly. Please do not simulate, instead understand the functioning, and build it practically…. because as you can see your simulation is giving wrong results.
I will try to design the buck converter for the 300V to 80V DC, and let you know.
well thank you so much. ill wait for that buck converter. As i understood from the given circuit- it is driving gate voltage with voltage divider using 500K pot which will vary depending on input voltage meaning if input varies then gate voltage will vary and output will vary accordingly thus providing a variable voltage in output, not fixed. I need fixed output 80V, hope it makes you understand the scenario.
In the previous circuit the output can be fixed by simply adding a 85V zener diode between MOSFET gate and ground,, but the MOSFET will heat up a lot at over 100V input. The MOSFET can be safeguarded by adding adequate heatsink to it…if that is OK then you can try the previous circuit…
thank you so much for your time. ill be in touch with you, see you.
Sure, no problem!
Hi- in my circuit if it gives output as much it gets in gate voltage. Meaning if gate voltage is 8 it gives 8, if 80 it gives 80 using linier voltage. Now I need a simple circuit which will provide stable 80v from 12v, please help. I tried to use pwm of booster circuit from market but MOSFET gets super hot and damaged.
Hi, If the circuit is not regulating the input voltage then I think your MOSFET could be malfunctioning, or there may be some other fault in the circuit.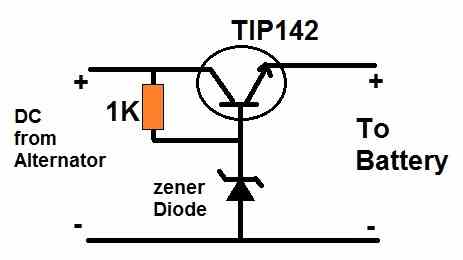
PWM cannot be used for getting a constant DC output, because then the output peak voltage will be always equal to the input voltage peak.
You can try the following simple design, the transistor must be relaced with a MJE13005 transistor.
The zener diode value must be 1V higher than the desired output voltage across the emitter and ground:
" rel="ugc">
thank you, let me try with this.
OK, no problem!
Hi- i have a problem, input from 40-140V variable ac to 82V constant regulated DC. can you please help in providing some circuit to solve this.
Please specify the required maximum current output also, I will try to figure it out…
Hi-10A max. Basically need one buck converter with input range 40-140V DC and output 82V please.
OK, I have explained the entire procedure in the following article. You just have to recalculate the inductor value by replacing the parameters in the given equations:
https://www.homemade-circuits.com/calculating-inductor-value-in-smps/
For the transistors, just make sure all are rated at above 150V, and the TIP127 is replaced with a 200V 20 amp power transistor
Hi- BC546, C E voltage 50 max, how can it handle 140V DC input to provide 6V using Zener to 555, am confused. output can get from inductor other end and high voltage filter needed. this astable timer used as PWM?
Yes, that’s why I suggested you to change all the BJTs and make sure they are rated at above 150V. Instead of 6V zener you an use a 12V zener.
I did not understand what you meant by “high voltage filter needed”
The 555 is used as a PWM astable with duty cycle control.
Hello Swagatam.
Thank you for the presentation of this configurable circuit and the functional description.
There are similar suggestions, but I haven’t seen it like this before. Simple and yet very effective.
As a radio amateur I was looking for an anode voltage stabilization for the preamplifier of a 630m tube power amplifier. The simulation in LTSpice for 250V/60mA with IRF820 and 2N5401 looks excellent.
Thank you very much!
Olaf, DL4SA
Thank you Olaf, glad you found the above post useful.
I hope it works for you.
If you have any issues with the circuit, please let me know.
What similar ic cd4035 pwm 3 phase
Sorry, there’s no equivalent for this IC.
Dear Swagatham,
In the above circuit, the mosfet is used a source following.
The Gate-Source voltage of the said Mosfet is only +-20v
[Maximum Gate-Source Voltage |Vgs|: 20 V]
in my experiments, what I have seen is , output at source is almost equal to the gate voltage.
Can we give more than the specified Vgs voltage ? obviously we cannot get outputs like 100v without providing 100V at gate. But how ? is my understanding wrong ?
I have blown many mosfets trying to get about 80v at the source of the mosfet. I am trying to figure out why it is blowing off ?
another strange thing is with gate open , if I connect 80 v at source, it is fully available at gate, instantly damaging the mosftet. No load was connected at the drain and gate too was not connected. why this behavior ?
Your ideas are most welcome.
Dear Suresh,
In a source follower MOSFET configuration, you can use any voltage higher than Vgs at the gate of the MOSFET, by clamping the gate voltage to 12V or 15V through a 12V or a 15v zener diode connected across the gate and the source of the MOSFET. You can find an example design in the following article.
https://www.homemade-circuits.com/0-300v-variable-voltage-current/
It is not recommended to connect a supply DC input from the source side to a N-channel MOSFET. The supply voltage to an N-channel MOSFET is supposed to be from the drain side. I am not sure what would be the result if the supply input is applied from the source side??
Dear Swagatham,
“ by clamping the gate voltage to 12V or 15V through a 12V or a 15v zener diode connected across the gate and the source of the MOSFET”
by doing this , will it not amount to restricting the gate voltage to that of zener , effectively bringing the gate voltage within the Vgs rating ? is there something , I am missing ?
“It is not recommended to connect a supply DC input from the source side to a N-channel MOSFET” This is confusing ! as the name signifies , “source” should be power source (input) and “Drain” should be the power draining out – output.
Just like the collector and emitter of a bjt signifies.
this beats me!
Thks once again for your insights.
Dear Suresh,
Connecting zener to gate/source will not affect the source voltage output, connecting the zener from gate to ground line of the circuit will affect the source voltage.
understood. thks
Dear swagatham,
I am facing a strange issue. Hope you can help.
As discussed earlier, I am using mosfet IRF640 to control the voltage.
I had connected two of them in parallel.
It was working reasonably well , getting 0-70v unregulated output.
I was testing led keeping the voltage at 1.5v. I increased the voltage to know at which voltage blows it off. As I increased the voltage it not only god burned , but damaged the power supply too. one of the mosfet got shorted along with the 2n2222 short circuit protection.
I changed all both. Now is the new problem. as I connect any load, the output drops to zero. Both mosfets are good.I removed the protection, still the same. I was using a 500K pot with one end connected to the input + and the other end connected to the ground. The center control is connected to the gate with a 5k resistance in series (tried direct connection too).
when I disconnect one mosfet it worked , but the lowest I could manage to reduce was around 15v. with one mosfet. Some how I was getting high voltage at the drain even when the gate was zero. So I connected a 10k resistance across drain and gate in parallel to the zener. This solved some issue. However when I connect the load, the output was droping. when I increase the gate voltage above 12v , it worked like a on of switch. Voltage was getting low and coming back. To make it steady I connected a 10nf cap at the gate. This stopped the voltage dropping to zero – But INCREASED with load. The output goes from 12 to 40 volt. and further the digital meter reads as if there is high speed switching going on. I don’t have an oscilloscope to check this behaviour. I use what I made using raspberry pi pico and scoppy mobile app. It can take max 3.2 volt as input and I am scared that it might get damaged.
Can you guess what might be happening ?
Dear Suresh,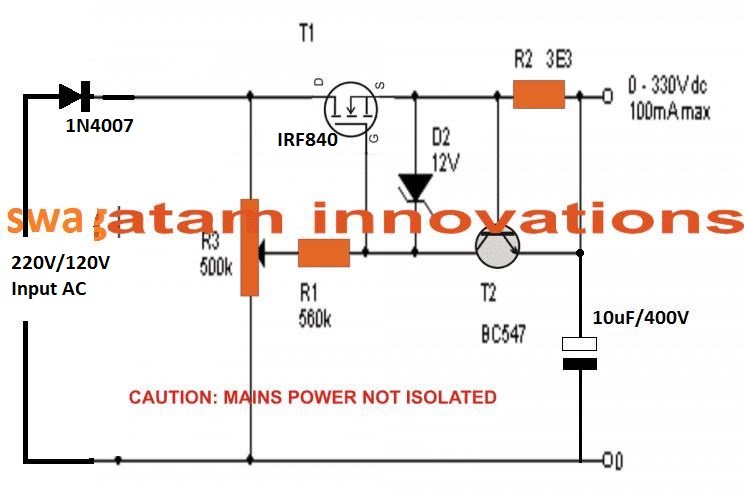
What is the value of the current limiting resistor which is associated with your 2N2222 current controller stage.
When the LED got shorted, it might have shorted the source of the MOSFEET to ground causing heavy current to flow though the MOSFET.
However, if the current limiting resistor and the 2n2222 are configured correctly with the MOSFET then this should not happen.
And where did you connect the 12V zener diode? It should be connected across GATE and SOURCE, not GATE and DRAIN.
Please configure the current limiting stage and the zener diode exactly as shown in the following diagram, and check again:
" rel="ugc">
Dear Swagatham, The circuit is as shown in the diagram. The resistor value is 0.6 ohms 25 watts. Zener is connected across GATE & SOURCE .
I used a 15v zener instead of the 12v you had recommended. I think this is ok considering the Vgs to be +-20v , so within the limit . or it be within Vgs-Vgs(th) ? :- 20-4 =16v ?
without the capacitor, when connected a 12v dc motor (0.5 amp) , it works like a square wave fashion – when supply to motor is beyond 13v ; like switching on and off. What is happening is voltage drops to almost zero and rises again. When the cap is connected , instead of droping, it shootsup wild from 13 to anything above 30v. longer the motor stays connected, higher is the voltage and current too increases.
I can’t figure out what changed and it’s present behavior.
Thanky you Suresh, in that case it is difficult you understand why the mosfet blew. I have tested the same circuit with 220v ac and a 220v bulb, it worked perfectly well, I could dim the bulb until the filament was barely glowing, and then I could increase the brightness to full 220v level….I did not have any current limiting stage in my circuit. I think it is better to go with a BJT instead since MOSFETS can be too sensitive and unpredictable.
Dear swagatham,
You had mentioned about clamping the gate by connecting a zener from source to gate. However in the above circuit though a normal rectifier diode is connected so, there is no zener connected.
does that mean, the gate is supplied with less that 20v through the collector of q1 & 10M resistance ?
Dear Suresh,
The above diagram was referred from a popular magazine and I am not sure why a zener diode is not used across its gate/source terminals.
According to me the D5 diode must be replaced with a 15V zener otherwise the MOSFET should get damaged quickly.
The Q1 is included to supply a 600V constant current supply to the gate of the MOSFET, while the pot is included to adjust this 600V to any desired lower level voltage.
Dear Swagatham,
I tried both methods with two IRF640 mosfets connected : drain & source in parallel while gate through a 1K resistance & 2 independent diodes across the gate – source of each mosfets
1) zener diode between gate & source : Mosfet stays good
2) In4007 as shown : fried both
BTW , do you think TVS diode might be a choice here ? or use both in parallel be any better ?
Thank you Dear Suresh for confirming the results, although I am sorry you had to sacrifice two MOSFETs for this.
So, it proves that for high voltage MOSFET power supplies, the gate/source voltage of the MOSFET must be restricted below its maximum tolerable limit.
No, TVS diodes are not relevant here, only a 12v or a 15V zener diode will work in this situation.
Dear Swagatham,
Actually only one was lost. That is strange.
What I have noticed is that when mosfet switches on, the resistance between Drain & Source is different in every mosfet. I wonder if this was the reason only one was lost out of two connected.
I completed the project with a 15v 1 watt zenner diode as discussed. I had purchased tvs diode too but thought of trying out with zener for a few days and with various types of loads. So far it is good with the same load as tried previously.
I combined the short circuit protection with 2N2222 also.
just a thought : with the other type using TIP 42 c – which is a darlinton pair. However all these are current driven , which means requires large current at the base – ending up burning pots.
to overcome this issue, why not combine a mosfet and a BJT , making a darlinton pair. Mosfet is voltage driven and can supply the required current to BJT.
I want to try this , would love to hear from you.
thanks & rgds
.
Thank you for the update Dear Suresh!
The resistance across drain and source of a MOSFET will be in milliohms and the difference will be also in milliohms, so i don’t think it is easy to differentiate between such small resistance values. I am wondering how you measured this difference?
And I don’t think this resistance difference will cause a MOSFET to blow. If one MOSFET was good it probably means the above circuit is equipped to keep the MOSFET gate safe even without a zener diode, although I cannot figure out how this is done in the circuit?
However using a zener diode between gate and source is still recommended and I am glad this method has worked for you so far.
Yes BJTs are current driven and require larger current at their base compared to MOSFETs but TIP142 can work with relatively lower current at its base since it is a Darlington transistor. Darlington transistors are high gain devices which can work with minimal base current yet drive high current loads at their collectors.
Using a MOSFET to drive a BJT would be an overkill, since the MOSFET is alone capable of handling the load without the BJT.
Dear Swagatham,
as you pointed out the resistance is only 0.18 ohms for irf640.
on the digital multimeter, diode test mode, I was getting 1.6~ ohms when the mosfet was at ON-State. this value is different with each mosfets. I know this is wrong since the document says it will be only 0.18 ohms. However the point is there might be some difference with each mosfets. This could also be due to the simple fact that we might be getting 2nd or 3rd quality products.
Funny, websites like elements14 list the price @ 39.87 for 1000+ quantity and I get it for 22/- per piece locally. Obviously there could be quality issues.
Mosfet is capable of handling the load. I totally agree. But it less forgiving than BJT’s when it comes to transient surges or even short circuit situations, I think. This is the only reason why I am thinking of such a design.
Thank you Dear Suresh,
I don’t think using the diode range is the correct way of determining resistance value, it will simply show the continuity or the forward voltage drop, not the resistance value.
Yes, although BJTs are less efficient than MOSFETs, they are more reliable and predictable in terms of getting damaged.
However, using a MOSFET to control the base of a BJT looks awkward and is mostly not recommended.
Instead you can make the TIP142 even more sensitive by adding a third transistor (2n2222) in the Darlington format so that the potentiometer value can be increased to a 100K pot and the base resistors can be also increased to 100K. This will keep the potentiometer much safer and prevent from getting burned.
Dear Swagatham,
Thanks a lot for your valuable insight. I shall definitely check this method too.
rgds
No problem Dear Suresh, all the best to you.
dear Swagatam
I understand that P1 should be 1W of power. Is Not more practical to replace it by a transistor and put a trimpot to adjust the voltage output?
Thank you Emerson, for the suggestion,
However I am not sure how a transistor circuit can be replaced with the P1 trimpot.
Hi Swagatam,
I’m trying to copy your design using an NPN transistor to replace Q1. Is there any way that I can send the schematic for your review?
Btw, may I understand the purpose of R3, R4 and P1 as the voltage divider with Q1? From my understanding, you take the output from Q1 collector. Can you explain how you use Q1 output to drive Q2 for the regulation?
Thanks and look forward to your reply!
Thank you Kevin,
The R3, R4, P1 are positioned for regulating and feeding a proper voltage for the MOSFET gate, so that it does not exceed 20 V or 25 V. Because the MOSFET gate volatge exceeds 25 V it get destroyed.
This means I can increase either the Q1 current drawing or the value of R3, R4, and P1 to make the circuit stands for even higher input voltage, correct?
For higher input voltages you will have to upgrade Q1, Q2 appropriately, and also adjust the R3, R4, P1 values appropriately.
R/Sir,
Is it possible to increase its current upto 25 amp? If possible then what changes should be required?
Regards
Avdhoot
Hello Avdhoot, Yes you can increase the current to any limit, simply by upgrading the IGBTs accordingly.
Good morning sir,
Thanks for quick response.
1. Can I use KGF25N135NDH – 1350V 75A N-Channel IGBT instead of 2SK1120?
2. Is it required to change the MPSA92 PNP High Voltage Transistor? If yes please suggest type or model name.
Thanking you Sir.
Avdhoot
Good Morning Avdhoot,
1) You can use the mentioned IGBT if your load is also rated at around 1000 V otherwise you can use an IGBT or a MOSFET whose maximum voltage capacity is not more than 100 V higher than the load voltage.
2) If you are not able to find the MPSA92 transistor, you can replace it with any 300 V 1 amp PNP transistor
Very very thankful
Ok sir I will be check igbt.
MPSA92 is available so I can use it.
Once again thanks.
No problem, let me know if you have any more questions.
R/Sir,
I have 2 more issues one is this circuit related and another is VFD related
1. For this circuit required 0.22uf 630v/ 0.47uf 630v / 10nf 630v each capacitor but I have only two type capacitor available apart from 0.22uf 630v so can I take 0.47uf 630v instead of 0.22uf 630v ? If yes then it will be 2 in parallel or a single one?
2. For VFD The H-Bridge Driver Circuit I am going to use IRS2110 03 Nos instead of IRS2330 IC and for the whole project all components are available accept 10uf/1kv capacitor. I have 47uf/250v capacitors so it is possible to replace the 47uf/250v(4 capacitors in series) with 10uf/1kv.
Apart from these two components all material is available for my both projects.
Plz advise.
Regards
Avdhoot
Hi Avdhoot,
1) You can use a 0.47uF/630V for C2 instead of 0.22uF/630V, it should work. A single one should be enough.
2) for the VFD circuit you can use 4 series connected 47uF/250V that will do the job.
All the best to you.