In this post I have explained a simple, accurate, high torque treadmill motor speed controller circuit which may be effectively installed in similar units for acquiring PWM controlled variable speed feature. The idea was requested by Mr. Samuel.
Technical Specifications
I've a treadmill whose power failed completely...it had been imported from china and it's like they can't help after negotiating with them..guarantee is only meant in their x-try.
So, am asking, how would you assist me in designing a power supply that will control speed and change of direction of the treadmill movement as well. I'm and forever will be glad for your work.
Looking into the specs of the unit, the switching relays are specified with 10A ratings. I also had a view of the motor and it was written 180Volts on it.
This is the information i got sir. They also had a cautionary notice that the T.Mill shouldn't be run beyond 2hrs continuously. I hope I've given the best for the best.Thanks sir. Stay blessed now and forever! best moments!
The Design
Here's a simple PWM based motor speed controller circuit which can be used for controlling a treadmill speed right from zero to maximum.
The circuit also provides an instant bidirectional stop and reversal of the motor rotation by a single flick of a given switch.
Another interesting feature of this circuit is its capability of sustaining and balancing optimal torque even at lower speeds ensuring a continuous working of the motor without stalling it during extreme low speeds.
The circuit of the proposed treadmill motor speed controller may be understood with the help of the following points:
Here the two 555 ICs are configured as PWM generator/optimizer for acquiring the required speed control of the connected motor.
Circuit Operation
IC1 works as a frequency generator and is rigged at around 80Hz, any other value would also do and is not anyway critical.
The above frequency from pin#3 of IC1 is fed to pin#2 of IC2 which is wired as a standard monostable. IC2 responds and starts oscillating at this frequency, forcing equivalent triangle wave frequency at its pin2/6.
The above triangle waves is instantly compared by the set potential at pin#5 of IC2 creating an equivalent level of chopped PWM at its pin#3
The preset or a pot positioned at pin#5 of IC2 forms a potential divider network for a selectable fixing of any voltage from zero to maximum supply voltage at pin5 of IC2. This level is directly translated through optimized PWMs at pin#3 of the same IC as explained above.
The PWMs are fed across two sets of NOT gates via an SPDT toggle switch.
The NOT gates which act as inverters provide the feature of instant toggling of the motors rotational direction by a mere flick of the SPDT switch.
The resultant PWMs from the selected NOT gates finally reach the transistorized bridge network that holds the motor between them for implementing all the specified features discussed above.
These transistors should be rated as per the motor specifications, and the voltage across this bridge should also be as per the motor requirements.

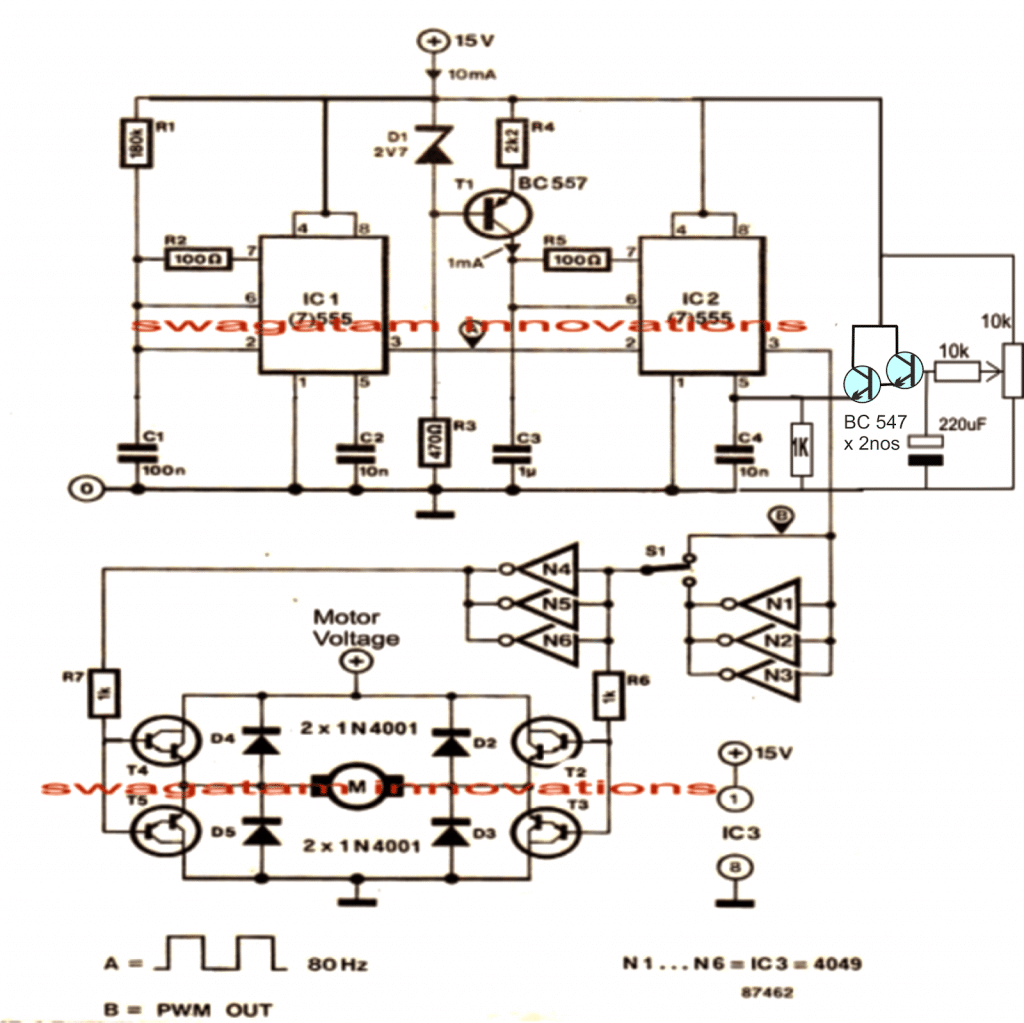
Video Clip:
Simplified Design
If you do not wish to have the reverse forward facility, then you can much simplify the above design by eliminating the lower section of the circuit entirely, as shown below:
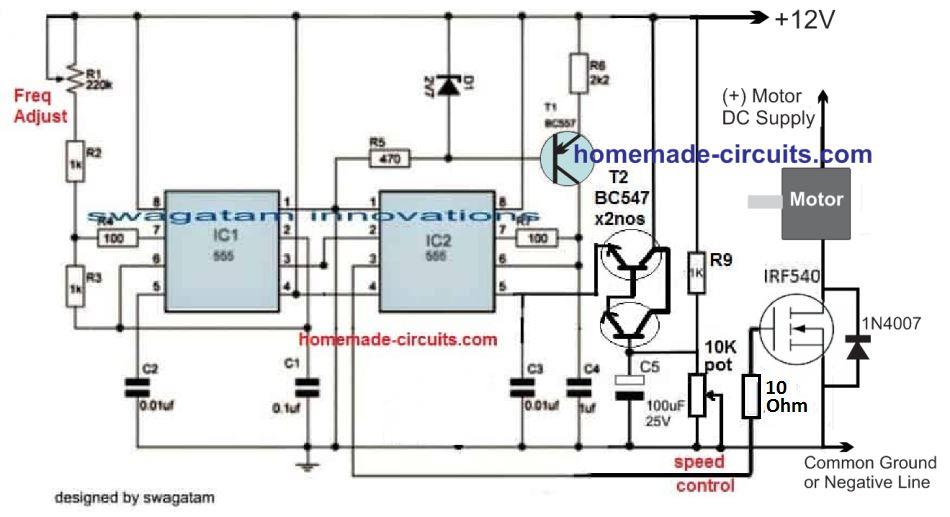
The 10K pot can be used for the speed control, while the 220uF determines the soft start feature. Increasing the 220uF value increases the soft start effect and vice versa.
Controlling Through an External Power Supply
The above design could be also modified for enabling motor speed control through an external variable power supply, as shown below.
Pin#5 can be seen driven from an external 0 to 10V variable power supply, for example from a LM317 based power supply
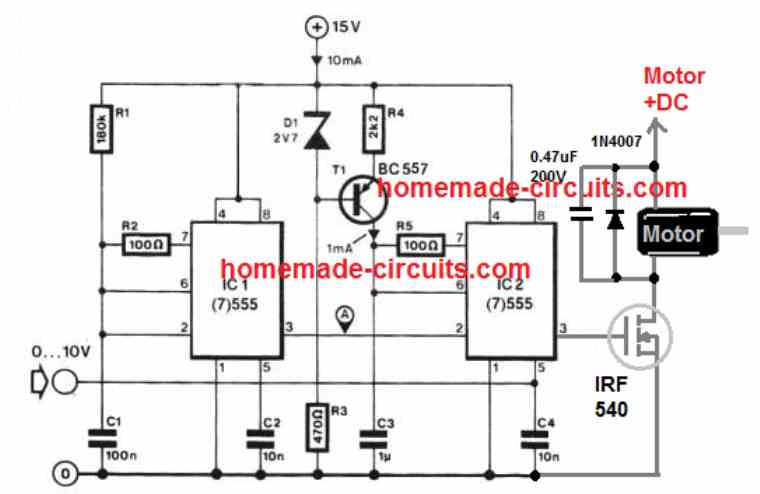
If you do not wish to use an external power supply, the above treadmill speed controller design could be simplified even further, by adding a 1k pot at pin#5 of IC2, as demonstrated below:
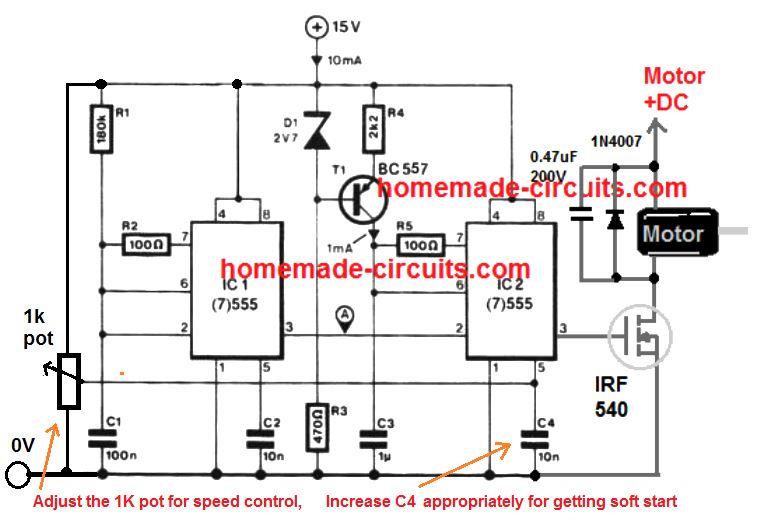
The 1k pot will allow you to adjust the treadmill speed from 10% to 90%, and the C4 value could be experimented to add a nice soft start to the treadmill motor during the switch ON.
Construction Guide
Power Supply Section
15V DC Supply:
Ensure that the input power source delivers a stable 15V DC, because it is critical for the 555 timers and the IRF540 MOSFET operation.
Use a well-filtered power source to avoid the noise interference.
Zener Diode (D1 - 2.7V):
Provides a fixed reference voltage for the base of T1 (BC557 transistor) which gives stable operation.
PWM Generator (IC1 - 555 Timer)
The first 555 timer (IC1) is configured as an astable multivibrator, to generate a pulse-width modulated (PWM) signal.
Pin Connections:
Pin 1 (GND): Connect to the ground.
Pin 8 (Vcc): Connect to +15V supply.
Pin 4 (Reset): Connect to +15V to enable the IC.
Pin 5 (Control Voltage): Add a 10nF capacitor (C2) to ground to stabilize the PWM signal.
Pin 3 (Output): Outputs the PWM signal to the base of T1 (BC557 transistor) via R4.
Frequency Control:
Use R1 R2, and C1 to set the frequency of the PWM signal.
Formula for frequency:
f = 1.44 / [(R1 + 2R2) * C1]
Where:
R1 = 180kΩ
R2 = 100kΩ
C1 = 100nF
PWM Adjustment (1kΩ Potentiometer):
The 1kΩ potentiometer varies the duty cycle of the PWM signal allowing the speed control of the treadmill motor.
Soft Start and Motor Driver (IC2 - 555 Timer)
The second 555 timer (IC2), is configured as a monostable multivibrator to implement the soft start feature.
Pin Connections:
Pin 1 (GND): Connect to the ground.
Pin 8 (Vcc): Connect to +15V supply.
Pin 4 (Reset): Connect to +15V to enable the IC.
Pin 5 (Control Voltage): Add a 10nF capacitor (C3) to ground.
Pin 3 (Output): Drives the gate of the IRF540 MOSFET.
Soft Start Capacitor (C4 - 10nF):
This capacitor determines, the ramp-up time for the soft start feature.
Larger values of the C4 increases the soft start time.
Adjust C4 using the formula:
t = 1.1 * R6 * C4
Where:
R6 = 10kΩ
C4 = Soft start capacitor
Motor Connection:
The motor is connected to the drain of the IRF540 MOSFET with the source connected to the ground.
D5 (1N4007): Protects the MOSFET from back the EMF generated by the motor.
Working Principle
PWM Speed Control:
The duty cycle of the PWM signal generated by IC1 provides the average voltage applied to the motor.
Adjusting the 1kΩ pot, changes the PWM duty cycle effectively, controlling the motor speed.
Soft Start:
When the circuit is powered ON, the IC2 gradually increases the gate voltage of the MOSFET due to the charging of the C4.
This ensures that motor starts smoothly without jerks.
Overvoltage Protection:
The 2.7V zener diode (D1) ensure the PWM output voltage doesnt exceed safe levels for the transistor T1.
Relevant Calculations
Frequency of PWM Signal (IC1):
f = 1.44 / [(R1 + 2R2) * C1]
For the given values:
R1 = 180kΩ
R2 = 100kΩ
C1 = 100nF
Substituting:
f = 1.44 / [(180k + 2 * 100k) * 0.1µF]
f ≈ 34.3 Hz
Soft Start Time (IC2):
t = 1.1 * R6 * C4
For the given values:
R6 = 10kΩ
C4 = 10nF
Substituting:
t = 1.1 * 10k * 10n
t = 0.11 ms
If a larger value for the C4 is chosen (e.g 1µF):
t = 1.1 * 10k * 1µF
t = 11 ms
Assembly Tips
Use a Heat Sink for the IRF540:
The MOSFET can heat up under heavy motor loads so Attach an appropriate heat sink.
PCB Design:
Keep the ground connections of the IC1, IC2 and the motor driver separate to avoid noise.
Testing:
Test the PWM output with the multimeter or oscilloscope before connecting the motor.
Safety Precautions:
Ensure proper insulation for all tthe high-current connections to prevent short circuit.
Using A Dimmer Phase Chopper Circuit
As rightly suggested by one of the dedicated readers of this blog, Mr. Ivan, a 180 V treadmill motor can be simply controlled through mains phase chopping concept, normally incorporated in all commercial dimmer switches for regulating home fan speed.
Shown below is a modified dimmer switch circuit design which can be effectively used for regulating a 180 V treadmill motor from zero to max:
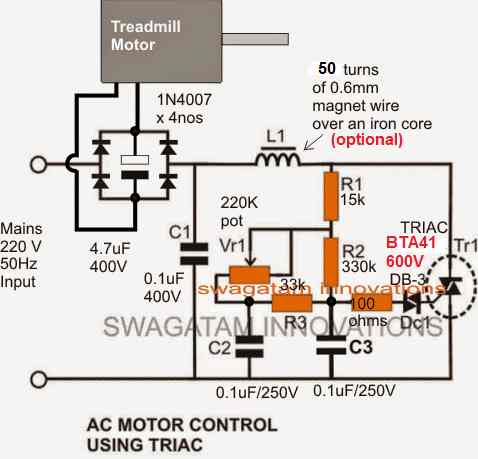
Please make sure to use a non-polar capacitor for the one shown between the bridge rectifier.
Use the following type, 10 in parallel
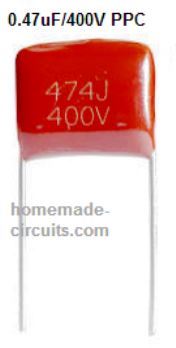
10nos of 0.47/400V in parallel will make 47uF/400V non polar capacitor which may work like a decent filter capacitor for the motor.
Saya seorang teknisi alat olahraga treadmill,sering memperbaiki modul pcb controlernya cuma saya selalu kesulitan untuk mendapatkan skema dari modulcontroler yang saya perbaiki,manakala ada modul yang sulit diperbaiki karna keterbatasan kemampuan membaca rangkaian tanpa skema
I have a proteus mtm-5600 treadmill which is now showing a e1 error and the belt does not move. The output voltage on the power board reads around 72 vdc whereas the motor needs 190 vdc. i have a picture of the board at:
" rel="nofollow ugc">
What can i test with a multimeter? i am an electronics noob but can use a multimeter and know some basics. I just want to make sure the repair guy is actually doing a decent job and not damaging the board.
Sorry, I have never used that board so it is practically impossible for me to know the exact test points.
my email: collinsmpango@gmail.com
my customers treadmill shoots to high speed upon start, I have checked the swapped the speed sensor but the [problems remains, please advise me which speed control component should i change in the circuit board,
Thank you and I will be grateful.
Collins Stuart
I understand the problem, however since I do not have any information regarding your details of the treadmill circuit board, it can difficult for me to judge the issue and suggest a solution.
Dear Swagatam,
This is Collins again:
My Motor is 200v and the motor control board is an Altatech alt-6890 mcb I have replaced all the 3 mosfet but motor still starts in high speed.
Hi Collins,
I do not have sufficient information regarding Altatech alt-6890 mcb, so it is difficult for me to solve your query.
very good your post, I have a 90V treadmill motor, but I’m having trouble with a power supply, could you help me????
Thanks, and glad you liked the post. I think you will need a 220V to 90 V transformer for the power supply
Thanks for the useful post and info. I dont really need to use the motor at low speeds so I intend to use the SCR based circuit (thanks for such a nice, concise diagram!). However, I just have a question which may be rendered moot. I understand how SCRs work but the thing I am concerned with is this:
A motor rated at, let’s say 240V DC (though it seems 180 is more common), when fed with rectified DC will be seeing +/- 340V from a 240V AC supply due to the difference between peak/RMS values. Am I missing something or is this likely to burn the motor out as it runs on 40% more voltage than it is rated for?
Thanks for your interesting question.
Yes you are right, that is why the motor is supposed to be a 310V or 340V DC motor if the input AC is 220V or 240V. For 110V AC inputs the motor is supposed to be rated at 155 V. Alternatively you can use a 240V to 150V transformer and then rectify the transformer output for the getting the matching DC for the motor
Thanks for your quick reply. I had been watching the videos and reading the web sites about this thinking people were asking for trouble just rectifying DC without taking into account peak vs RMS. I’m glad to hear someone with your skills agrees. Now I just need to work around the problem. Thanks again.
You are welcome!
I’m posting this again because after pressing the “Post Comment” button, I didn’t get an awaiting moderation message.
I have an update, I hope you got my last message, If not I will recap.
My damaged controller had a MUR3060PT ultrafast diode with following circuit across the motor.
" rel="nofollow ugc">
102K 1kV Ceramic Disc Capacitor and 470K resistor.
I bought a mosfet 23N50 500V 23A (My motor rating 180V 14A). I used this Mosfet and connected the above circuit across the motor. Treadmill is running with belt tightened. The problem I have now is with pot at minimum position the treadmill is running at RUNNING speed, I need to slow it down further to JOGGING speed and WALKING speed. I cant even get on it safely with this speed. When pot at minimum the voltage is 140V DC across load. How can i reduce it further?
Do I need an appropriate powersupply to reduce the input voltage to 180V? Can I use the one in following https://www.homemade-circuits.com/0-300v-variable-voltage-current/
Can it withstand the current rating of my motor (if not which component needs to be replaced?)
Please suggest a transformerless power supply that can be used for 180v DC motor.
Thank you
Have a great day
The diodes and the capacitor are provided only to suppress back emf from the motor.
Yes you can use the 300V MOSFET circuit, however the mosfet can get too hot at lower speeds. Therefore only a PWM based design is recommended.
How can I reduce the minimum voltage to the motor? With Pot at minimum, motor is running fast. How can i reduce the speed even further? Right now with pot at minimum position, motor is at 50% speed, How can i adjust the speed from 0 to 100%?
You will need a Pwm circuit with a pot, or a mosfet circuit with a pot for reducing the speed.
I tried the First Circit (Simplified version), I tested it with a 12v motor using a 12 volt smps, which worked fine. Then I used a bridge rectifier D35SB80 (1000v 35A) and connected a 60W bulb, which also worked. Then I connected 10 capacitor 0.47uf in parallel to the DC output of the rectifier and feed that to the treadmill. Treadmill ran at very high speed so I turned it off. The Mosfet IRFP240 (200v 20A) was short after this. Is this because I used a 200v Mosfet? DoI have to use a 400v or higher? (My motor specs is 180v 14A). I used a 200v one because you said in the previous post to choose the mosfet as per the motor specs. The bridge rectifier output is 240v DC and when using the 10 non polar capacitors in parallel raises the voltage further to 300+.
Also when using the pot, the voltage varies too qickly, which pot should I use to fine tune the voltage even further?
Thank you
Have a nice day
Glad you could build the circuit successfully! Matching the mosfet with the load specs means the mosfet rating must be considerably higher than the load, voltage rating should be 25% higher and the current rating 50% higher. Yes a 400V mosfet would be required for a 300V output, which can be actually fatal for a 180 V motor. So the supply input itself is incompatible with your motor. The mosfet can also burn due to reverse spike from the motor, so make sure to add the diode/capacitor snubber across the motor, and repeat the same across the mosfet drain/source.
You can try two 10k pots in series and use both of them to fine tune the motor output
Hello, I have an old treadmill which i bought back in 2015. It wasn’t used for a year and now it stopped working. The control board is faulty. The motor is working fine (180v dc motor). I would like to know if i can use the treadmill again with the First Circuit (Simplified version, I dont need reverse direction control). Can the First Circuit handle the load when running on the belt?
Thank you
Have a nice day
The simplified can be used for your purpose, provided the mosfet voltage and current rating the appropriately selected as per the motor specs.
Hello Mr. Swagatam,
I purchased two different dimmer switches you are speaking of to control a 3HP, 110VDC, 21A Treadmill motor. Both of those dimmer switches were defective. It said you could use 120 or 220VAC supply.
When I had them hooked up, I used a high amperage full bridge rectifier along with high power capacitor. Nonetheless the potentiometer had no effect on the AC output side or the recitified end. At the output AC before the rectifier it read 125VAC and on the DC end it read 175VDC no matter where the potentiometer was adjusted at. I got tired of it all and send them back. And the motor wouldn’t respond at all. The fact is I was reading 175VDC at all times so the potentiometer wasn’t controlling supply voltage if that is the game and the motor wasn’t doing anything. That is that. The first dimmer did respond but it was terrible and the adjustment wasn’t at all from 0 to the maximum whatsoever.
know the motor is good because I run it with a Treadmill motor controller just fine. Only that I use that controller with another motor.
So I like to just build your second circuit above, one without the reverse circuit.
What I don’t understand is the following.
1. I don’t see where the supply AC line is in the circuit and at what voltage it has to be 120 or 220 VAC? The DC output is clear.
2. I don’t know what that frequency adjuster is (R1) or how to adjust it and its value and what it looks like which seems to be external to IC1 555 timer.
3. I see 5 capacitors in total and none has 220uF value. I don’t know where the 220uF capacitor is that you are speaking of below the circuit in your commentary. You mention it is used for soft start.
4. I understand that the circuit still needs a 1K resistor paralell to that C3 capacitor.
5. I assume this is a pwm control that uses a potentiometer to control the speed of the motor which controls the voltage supply to it.
6. I want to make sure I have this right. There is one zener diode 2V7 ( D1) and one regular diode IN4007 in the circuit.
7. Will this cicruit be good enough for my motor. 110VDC, 20 A. I am certain I will never need that much power from the motor. Most likely if anything around 8 amps at best. Just for hobby usage. I won’t be running it on some Treadmill. I will use it to install a metal cutting blade, sanding, grinding, things of that nature. It won’t be pulling any 100 lb weights.
Thanks in advance for clarifying the above points. Appreciate everything you do.
Hello Mr. Ali,
I forgot to mention in the article that for a tread mill the light dimmer triac will need to be changed to a powerful one such as the BTA41/800, otherwise the normal triac can get damaged instantly. But you must always test any circuit using an incandescent lamp first just to confirm that the circuit is actually working or not?
1) The IC 555 and mosfet based schematic are for treadmills with DC motors. But you can convert them to work with AC loads by adding a bridge rectifier with the load, as shown in the following example:
" rel="ugc">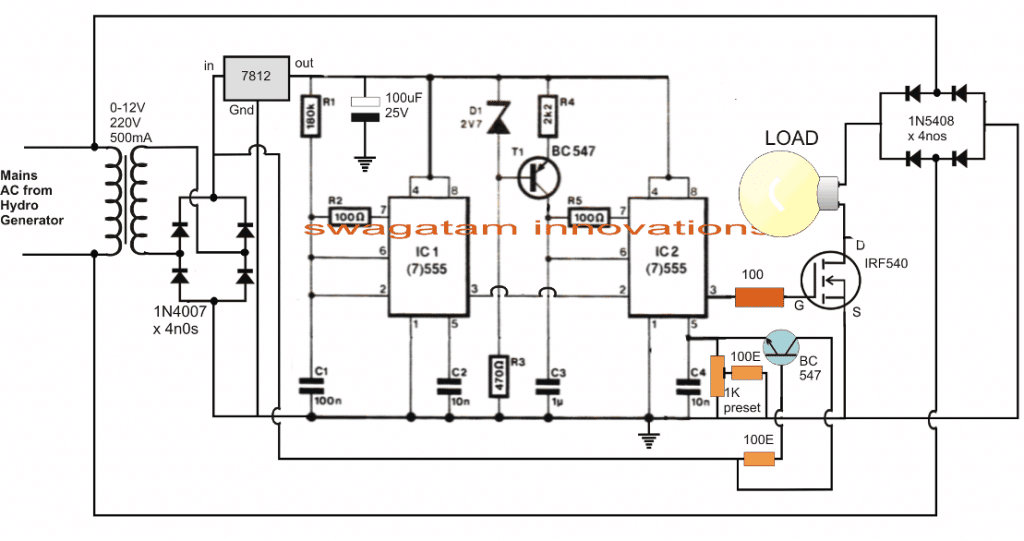
2) You can adjust the frequency to 100 Hz, by checking the frequency at pin#3 of IC1
3) The 220uF is mistakenly written for 100uF at the base of the BC547
4) That’s right.
5) The potentiometer controls the PWM which in turns causes the motor speed to vary as per the pulse widths.
6) That’s correct!
7) If Your MOSFET is appropriately rated then there shouldn’t be any problems operating your treadmill.
I would recommend adding a snubber network parallel to the motor as well to safeguard the circuit from accidental voltage spikes.
Thank you so much for being clear in your effort to cover each point.
On the first one, I believe you meant that, the schematic is for DC supply source and by adding a bridge rectifier to an AC power supply, one can use AC supply as power source.
And the schematic you included I noticed another element, a transformer.
It appears that the circuit itself require lower voltage so a transformer is needed.
I want to make sure that I have it right. The transformer is a step down to 12VAC.
Is this correct? ( I have many transformers converting 120VAC to 12VAC)
And could I use 120VAC as power supply with this circuit as these circuits seem to show 220VAC across the board?
Thank you so much.
All electronic circuits will require a small DC to run, so this circuit will also require a 12 V Dc to operate. Yes a bridge rectifier needs to be added with the load so that the MOSFET is able to work with DC while the load works with AC.
I think you are very new to electronics. Yes a transformer is a device which steps down high AC to low AC which is then converted to DC through a bridge for supplying an electronic circuit.
Your transformer primary must be rated at 120V to handle 120V AC input.
I think you must first get well versed with all the basics of electronic and only then attempt the above complex designs.
Sorry more questions.
I noticed the diagram in the link you sent me is more different looking in its details than what is in the main post here.
There are 5 capacitors in the main post’s diagram and the link you sent there are 4 capacitors.
And there is more other things involved. But the other stuff is no problem.
I just want to make it is all I need and the only thing I don’t know what it is that square box (7812) that is hooked up to rectifier IN7007. Is that a transistor or some kind of variable resistor and is that where one adjusts the frequency or the frequency is adjusted by some other device in the circuit?
I would advise you not to attempt this circuit unless you have learned all the basics of electronics otherwise there’s a 100% chance you will fail with this project. The linked circuit is little different but the function is the same, to control the load with PWM.
Hi Mr Swagatam
I’m working on a project to use a treadmill motor to drive a lathe. I’ve purchased a Motor Speed Controller Board to drive the motor and it needs an external PWM signal to vary the speed of the motor. There is a 12 pin connector socket on the board, through which the external PWM signal is connected (normally via the console). I’ve managed to find a drawing of the 12 pin connector and it identifies each pin as follows
Pin #1 +11V
Pin #2 ELV Up/Dn
Pin #3 ELV Dn/Up
Pin #4 +11V
Pin #5 Relay ENB
Pin #6 Command PWM
Pin #7 Gnd
Pin #8 Gnd
Pin #9 Speed Signal
Pin #10 ELV +5V
Pin #11 ELV In
Pin #12 ELV Gnd
I’m hoping you can help me decipher what these Pin identifiers are so that I could connect the motor speed control board to one of your PWM circuits.
Regards
Jim
Hi Jim,
I am not very sure about the terms mentioned on the pin connector?
ELV probably means Extra Low Voltage.
Relay ENB means Relay ENABLE
Command PWM could be the input for the external PWM control
Speed Signal could indicate an input for a DC level, or it could be an output to measure speed.
Hi Mr Swagatam, thanks for your reply. I think I may have to try and find out which manufacturer made the treadmill that the board came from. As a matter of interest, could you tell me what connections are necessary between a PWM controller and a motor speed control board of this type.
You are welcome Jim, A motor speed controller board as the name suggest must include a PWM generator in the board itself and must not depend on external signals. So I am not sure what kind of controller may require external signals for the control. If the broad is built only with power mosfets or transistors then an external pwm can be justified but then the board cannot be specified as motor controller board.
asslam o alaikum
i am in confusion, i am trying to make tredmil motor control circuit, which consist 1 dc motor, variable copper quile like automatic voltage stablizer, and rectifier. through variable copper quile input for example 60v after this input i given to rectifier then came to know in output 100volts. this circuit increase volts . what is matter plz guide me. thanks zameer hussain
Hello, An AVR or an autotransformer will have a range from a higher stepped-up voltage to a lower stepped-down voltage, so you AVR is giving the correct results. Check the tapping of the AVR and connect you motor with a tapping whose maximum voltage is not in the stepped-up range
It has been so many years but I still find it very interesting. My back ground in electronics is not near what yours is especially in semi conductors. My education was in the time of tubes and stopped in the infancy of semi conductors. I’m the kind of guy that wants to trouble shoot a problem and then change what ever component is bad rather than take out the entire circuit, throw it away and put in a new one. This was a little off topic but what I am needing to build is a controller that operates on 120v and operates a 90v DC motor where the field and armature are both wound. Can one of your circuits be modified for this purpose? Thank you for your help. I do have a controller but I can not find a schematic for it. There are no obvious bad components and I could and probably should check all of the components to see if I can find the bad culprit. But then again, your control sounds very interesting. Thanks again for any advice or help.
Thank you for your query, and explanation!
Yes you can use the second last circuit for powering your 90V Dc motor
Hello friend, all right, one more question about the dimmer, I’m having trouble connecting the potentiometer to control the speed. I installed the potentiometer, but the speed is not changing, can I get out of this doubt? I mean the last dimmer scheme for 180v
Hello Elias, For the dimmer, you have to build everything exactly as shown, and first test with a 100 watt lamp, if the lamp works fine then you can try it with a motor.
More information on the dimmer controller can be found in the following article:
Light Dimmer and Ceiling fan Regulator Circuit
when the problem of the triac I managed to solve, I was commenting an error, I was using a 4 ampere triac, but I had not paid attention before, doing the tests I realized that the triac was low amperage. solved that part.
OK, glad it is solved now!!
hello friend, I made the circuit according to the Scheme you sent me, the 1.2 hp 90v engine keeps burning the triac, I think the engine is shorted. I tested the scheme on the treadmill with a 1.4hp 90v motor it worked, the treadmill is working even more smoothly, I used a resistor and a capacitor in series. I leave my thanks here.
No problem friend, I hope you are able to solve the issue fast, and report back here.
thank you very much friend. could you send me a schematic for me to do this montage? I would like to thank you in advance.
You can add the snubber across the triac pins, as indicated in the following schematic:
hello friend, I did this dimmer project, but I still couldn’t understand the part of the Vr1 potentiometer, I put the potentiometer but it has no effect, how can you get me out of this doubt? I thank you already friend.
VR1 is the speed control pot, and rotating it should enable the speed control from 0 to maximum. If it is not working then your circuit is not working or maybe something is wrong in it.
Try reducing the C2, C3 to 0.047uF/250V, and use a pot rated at 220k, and see the results, if still it doesn’t then your triac is blown for sure or there maybe some other connection fault.
thank you so much friend for the return! so if i put a diode in parallel on the motor output would it work?
You are welcome Friend, no not a diode, rather a capacitor/resistor in series. You can try a 100 Ohm and 0.33uF/400V capacitor series network across the MT1/MT2 pns of the triac.
Hello Friend! the project was filet on my treadmill using the 1.4 hp 90v engine, the torque is excellent. now on another 1.2hp engine also 90v I tried to use the same project but it’s not working I used a coil with 21 awg wire with 200 volts is burning the triac transistor. my thanks friend, I really like your projects.
Thanks friend, I guess you are referring to the last circuit…most probably your triac might have burned, due to back emf from the motor….you may have
to use external snubber also, even if the triac has internal snubber. The coil has nothing to do with this issue actually.
Good night, I live in Brazil I am a hobbyist and I am looking for a PWM circuit for a 90V DC motor. and 1 Hp, I think this circuit will do, does your circuit have to have 2 supplies? 15v for the circuit and 90v for the motor (in my case)? should I connect the 90v directly to the motor where “Motor + Dc” and “0v” are? Thanks.
Yes the circuit requires two DC supplies, one from the the motor other for the circuit.
You can extract the 15V from the 90 V itself through a suitable SMPS buck converter
hello friend, I set up the project and it is already working. I made the coil with 200 turns, but it is getting very hot in a short time. What do you advise me to do? I tested with 100 laps, but it didn’t go very well in the test, 200 laps was already much better in the test, but there is only this detail to solve, I thank you for the strength and patience.
Glad to know it is working for you, I guess you are talking about the last circuit. Please try using thick wires for the coil L1, may be a 1 mm or 1.5 mm enameled copper wire should work nicely, since the motor is a high current motor.
Mr. Swagatam,
I am attempting to build the Treadmill speed control circuit, the second simplified one. Do you have a more clear picture of the circuit? Its a bit blurred and hard to read. I’m wanting to control a 2.5 HP 22 AMP 130VDC PM motor.
Also in the comments its stated to use PPC or metalized type and non polar capacitors. I have not been able to find info as to this type, are they called something different.
Do you have a parts list to go by on this diagram?, that would help a lot too.
I know enough about electronics to safely let out the smoke.
Mr.Clint,
I have updated the post with new simplified diagrams and clearer diagrams, Please check them out!
Part numbers are given in the diagram itself.
All the resistors are 1/4watt 5%
Al the capacitors are PPC type non polar 100V, except the one parallel to the motor which is rated at 200V
Mr Swagatam,
I see no change in the Simplified Design. Just as blurry.
Can you send me directly a very clear diagram.
I can’t see what the transistor number is or what the resistor is above it, barley make out some of the capacitors.
I’m a CAD drafter and would love to redraw some of you circuits for you that need a good clear diagram.
Mr. Clint, Are you seeing the following figures? They are larger and much clearer now:
" rel="ugc">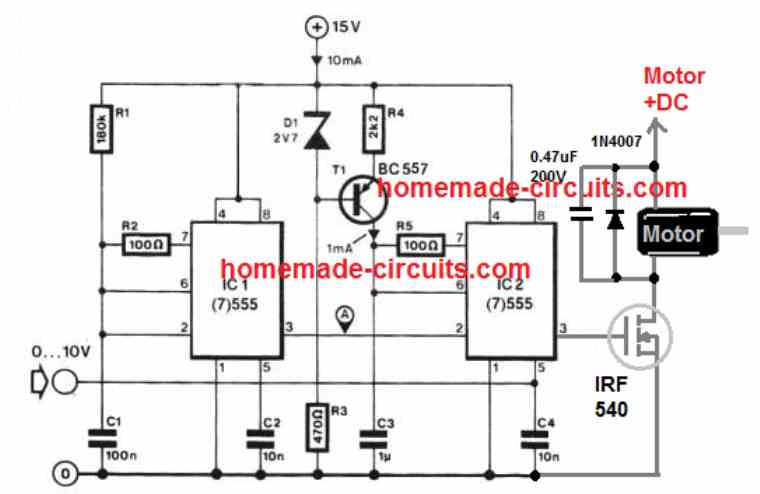
" rel="ugc">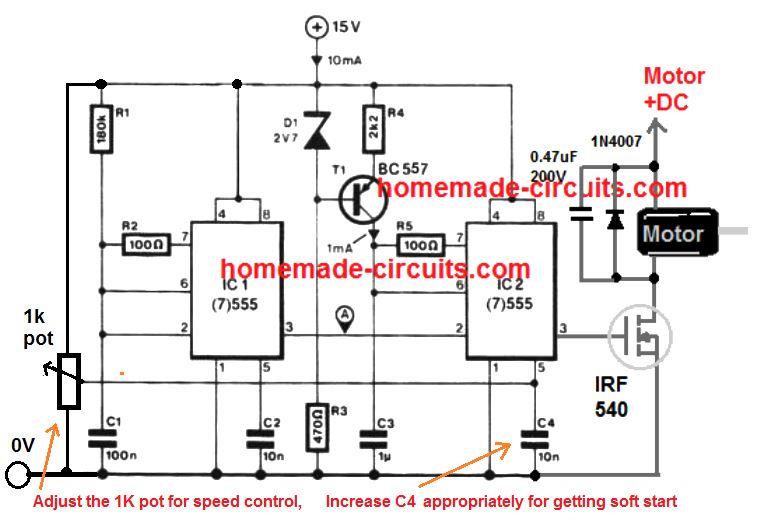
Yes those are clear but wrong circuit. Its the second circuit in that group. The one after the reversible speed control. I just want to build a one direction speed control.
I also see in both those examples a resistor marked “2k2”. Is that suppose to mean a 2k resistor? The second “2” to me is confusing.
I’ve got a background in electrical controls, so electronics is a bit of a learning curve for me.
The new designs are the simplified versions, they are not wrong!! The following circuit is the simplified version of the second one and will do exactly same like the second one:
" rel="ugc">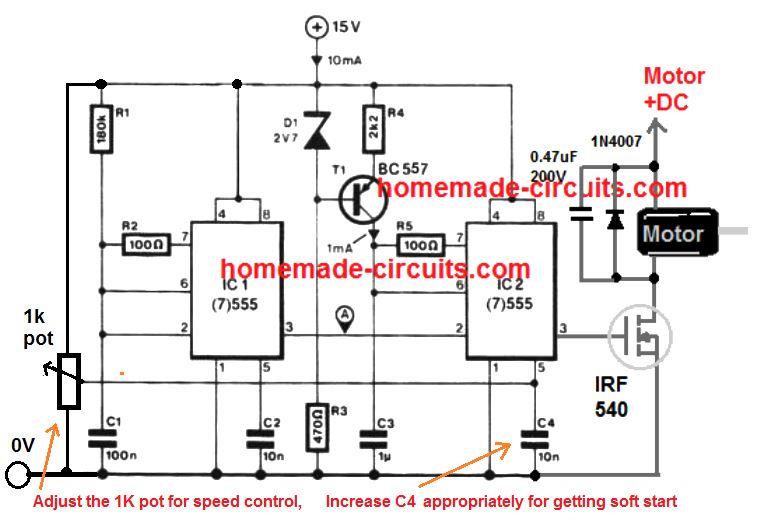
2k2 is 2.2k
I did it the way you told me about the capacitors, it was excellent. I now have a new question … about the coil; what is the ferrite size? for me to do the correct calculation. thank you very much friend.
Glad to know it is solved! The L1 and the complementary C1 are not critical, they are introduced to cancel out the high frequency RF disturbance generated due to the rapid chopping of the phase by the triac!
The coil will need to be experimented with some trial and error. Initially try any ferrite core that will accommodate 100 turns closely wound 21 SWG super enameled copper wire. C1 can be 0.1uF 400V.
Now keep an MW radio nearby and check the reduction of RF by increasing the number of turns on L1. Keep increasing until you find minimum disturbance on the radio.
I’m sorry friend !, I think I couldn’t express myself very well. I replaced the 4.7uf 400v electrolytic capacitor with 10uf and also replaced the 0.1uf400v capacitor with the 22uf non-polarized capacitor and performed the assembly in parallel, overheating still continues. I appreciate your patience in helping me.
No problem friend, I have understood it! The capacitor between the bridge rectifier, can be 4.7uF/400V or 10uF/400V but it should be strictly a non-polar PPC type, just as the other capacitors are.
The 0.1uF/400V does not need to be changed at all, which can cause other problems.
So all the capacitors in the diagram must be non-polar, and the values shown in the diagram must be exactly as it is!
hello friend, I did everything you recommended, replacing the 4.7uf400v capacitor for 10uf 400v is overheating, I put the 22uf capacitor, the heating is very little but if you continue with the 22uf capacitor and the motor will run for another 1 hour or less it can burst. do you suggest me with this situation? I configured the project as shown in the image and I have the omponetes as the project asks.
OK got it, so did you also use a non-polar capacitor as advised by me? Electrolytic cap might not work and may heat up quickly…
Good day. My degree is in Physics, NOT electrical engineering. I have a couple mc2100 board versions and a recent freebee mc1650LS Both need PWM to control motor speed since neither has potentiometer connectors. The 1650 has a 4 pin connector from the upper control board and the other boards have: an RJ45 8 pin, or the 7-8 straight pin. I have seen one mod where a PWM was connected to the 7-8 straight pin connector utilizing just 4 of these pins. While encouraging, none of these searches details, or explains how to connect the PWM generator to any of these boards. I am tempted to just use the SCR + rectifier examples – – but I would really like to utilize the treadmill controller boards. I am just a little lost/overwhelmed… Bill
Hello, I could not find a proper datasheet for the IC MC1650, so I am unable to figure out the pinout details of the IC.
Thans for trying – I ordered a PWM generator off ebay (china) so I don’t expect to see it until May. I looks like it has 4 wire connectors, would you have an idea how to connect this to a mc2100 board? Thanks again.
The MC1200 is actually an SMPS circuit for powering the treadmill motor. It requires an external varying PWM input to enable the corresponding speed variations on the treadmill motor.
You will find a connector near the end opposite to the transformer end of the board. This connector will have four wires, two black common wires which will connect with the negative of the PWM circuit, one red wire that will connect with the positive line of the PWM circuit, and a blue wire that will connect with the PWM signal output of your PWM circuit.
There’s another quick way of achieving the speed control on MC-1200 without using an external PWM. It is by replacing the small yellow colored voltage control preset existing on the MC-1200 board with an identically rated potentiometer.
Hello friend! about the dimmer is working perfectly I mounted it the way you explained to me. I have a new question, I need to set up a project to control a battery-powered 36v 700watt electric bike motor. Do you have a project like this or could you help me with this project? God bless you always my friend.
Hello Elias, glad the dimmer is working correctly now. For a e-bike control circuit you can probably try the following design
Simple E-Bike Circuit [Electric Bike]
yes friend, it is the capacitor that controls the motor. can I replace with a 22uf 450v?
No, the capacitor does not change the speed, the speed is changed by the pot VR1. The capacitor only filters the ripples.
yes 22uF will do, but it should be non-polar to ensure that it does not heat up
I am looking to use this pwm circuit on a conveyor, the engine will work with 1.4hp. 90v. 10A.
I made the circuit and tested it. the 4.7uf 400v capacitor is overheating in the 1.2 hp.90v engine. 10A 4000RPM. Should I change the configuration of this scheme? what did you suggest to me friend?
Is it controlling the engine speed? If yes then you can replace the 4.7uF electrolytic capacitor with 5 or 10 nos of 1uF/400V in parallel, these must be PPC or metalized type and non polar, like the brown one in the following image:
Hi, I am hoping to build your 2nd circuit. My motor is rated at 230 Volt DC 9.5 Amp. Will the following Mosfet be suitable?
IXFQ60N50P
Channel Type N
Maximum Continuous Drain Current 60 A
Maximum Drain Source Voltage 500 V
Package Type TO-3P
Mounting Type Through Hole
Pin Count 3
Maximum Drain Source Resistance 100 mΩ
Channel Mode Enhancement
Maximum Gate Threshold Voltage 5V
Maximum Power Dissipation 1.04 kW
Transistor Configuration Single
Maximum Gate Source Voltage -30 V, +30 V
Thank You
John
Hi, yes it should work with the specified circuit design, but first confirm the circuit operation using a 220V bulb, if it dims and brightens with the PWMs then the circuit is working and confirmed.
Hello Swagatam, thanks for all your information. Dimmer Phase Chopper Circuit, 400V 4.7uF and 1500uF 400V capacitor change possible
Hello Hasan, do you mean replacing 4.7/400 with 1500/400…??
yes that’s possible.
I have a conveyor belt that burned her control I can’t find parts for her, the engine works 1.4hp 90v. I really liked your projects. Can you give me a tip? Can I use this scheme to meet the power of this engine?
If your motor is a single phase DC, then the above circuits can be used, provided the input supply is not beyond 110V DC
Yes I wanted to regulate with 1500uF 400V
Thank you
OK!, you can do it.
thank you very much for the feedback, just one more question. on this circuit can i use a 3000W dimmer for control?
if you have a dimmer, you can use it directly to control your motor, no need of the PWM circuit?
dear Mr Swagatam,hi sir is you have Schematic design for motor speed controller treadmill 240DC/11,7 A.thanks before
aguswiryo1986@gmail.com
Dear Agus, you can try the last two circuits provided in the following article:
https://www.homemade-circuits.com/how-to-make-simplest-triac-flasher/
Make sure to use a BTA41/600 Triac
is this circuit for DC motor sir?
No, actually the linked circuit is AC….for a DC motor you can try the last circuit in the above article itself, which has a bridge rectifier with the motor
Swagatam, thank you for your input. My English is not very good and I am using Google Translate, I hope you can interpret me. I see 3 circuits in the article of this web page. To control the speed of a 120VDC 2.5 HP motor, should I use the second circuit? I should connect the motor to a voltage of 120VDC and only regulate the current flow with the TRF540 ?.
Thank you very much. Horacio from Argentina.
Thank you Horacio, if your motor is a 120 VDC then you can use the second circuit, however you will to replace the indicated MOSFET with a MOSFET rated at 200 V drain/source capacity.
Thank you Swagatam!!!
Hello Swagatam, I am thinking of building the circuit without reverse to control a 120DC treadmill motor with 2.5 HP for which I will use the IRFP250 mosfet. But I have a question. Below the circuit you indicate “The 10K pot can be used for the speed control, while the 220uF determines the soft start feature. Increasing the 220uF value increases the soft start effect and vice versa.”. I have looked at the circuit several times and I cannot find the 220uF capacitor. I also want to ask you what is the object of the 220K variable resistor in the upper left of the circuit.
Thank you very much!
I’m Horacio from Argentina.
Hello Horacio, the 220uF can be seen at the base of the BC547 pair towards the extreme bottom right of the first diagram.
It is replaced with a 100uF in the second diagram.
the 220k variable resistor controls the frequency of the soft start PWMs
Thank you Swagatam!!!
Have a nice day!!
Hi Swagatam, I have been working on the second circuit to control the speed of a 120VDC 2.5HP treadmill motor without reversing. I have changed the IRF540 mosfet to the IRFP250 mosfet. I have already used kicad to make the circuit board. But before I soldered the components I did a test on a breadboard. To simulate the engine I used an incandescent lamp. I expected the light intensity to increase linearly as I turn the 10K potentiometer, but the lamp blinks and then stays on. To power the lamp I used a 220 to 110 VAC transformer (here in Argentinda we use 220V line) that I then rectified with a KBPC3506. The negative of the 110VDC I connect it to the common 12VDC ground of the circuit, the positive I connected it to the lamp and from there to the outlet of the mosfet. I want to ask you if I am connecting the circuit wrongly?
Just in case my email is hbarrabasqui@gmail.com
Thank you very much!!
Hi Horacio, In the second diagram I forgot to show the 1k resistor across pin5 and ground line of the IC2. Did you connect that resistor?
If you did, then I would suggest you to first confirm the IC2 pin3 output response with an LED. Remove the MOSFET, connect an LED from pin3 to ground nine via a 1k resistor. The LED brightness must vary from 0 to max in response to the pot variations.
This will prove whether your IC 555 stages are working correctly or not…
Also, making it over a stripboard through soldering is more reliable than using a breadboard, which may cause loose connections
Hello Swagatam, you had already told me to connect a 1K resistor from pin 5 of IC2 to ground, which is in parallel with capacitor C3. That is already done. I will remove the mosfet and the 10K resistor and I will replace it with a 1K resistor and an LED.
I will also follow your advice and solder the components on a board to avoid bad connections.
I’ll tell you later.
Thank you very much for the quick answer.
You have a good day.
Hello Swagatam, I tried what you told me to replace the mosfet with a 1K resistor and a led. By moving the 10K potentiometer the intensity of the led increases. I have also connected the mosfet again and at its output I have placed a led with a 1K resistor with 12VdC power. When I turn the 10K potentiometer from zero to the maximum value, the voltage drop between the negative leg of the led and the leg of the resistor connected to the positive reaches 12V when the potentiometer reaches 1.2K. It appears that the load receives full tension very quickly. Do you think I’m making a mistake?
Thank you very much!!
Hello Horacio,
It seems the 2 BC547 Darlington is too sensitive to the pot movements.
Please remove the two BC547 transistors from pin5 of IC2, remove the associated parts like R9, C5, 10k pot.
Next, replace C3 with 100uF/25V
And replace the 1k at pin5 of IC2 with a 1k pot. Center leg connected to pin5, the other two legs connected to the +/- supply rails of the 12V DC
Hello Swagatam, thanks for all the information you give us. I want to build a speed controller for a 90 V dc motor, variable speed, 11 amp. I think is possible to use a controller for an Ac motor made with triac and diac and then to use a rectifier bridge to feed the motor. I really don’t know if that is possible and even more I don’t know how to handle the high starting current of the motor. Could you sugest me something?Thank you in advance for your answer.
Thanks Mauricio, It is possible since the load gets proper DC from the bridge, while the triac circuit works with an AC, again through the bridge connections. If the riac is appropriately ated it will be able to handle the initial surge. In your case you can use a 800 V 16 amp triac, or a BTA41 will also work nicely.
dear sir i also have 2 HP 180vdc treadmill motor. as mentioned in above comments i should make first circuit and to be eliminated N1 to N6 and S1 joining R6&7 to 2nd ic pin 3.
sir.
1). is it ok to connect rectified 220vac through rectifier to the given points of the motor directly?
2). IN4001 is it enough to counter that much current? should i use 6A4?
3). what are the transistors T1 to T4 should i use?
Hi Jayanth, Rectified 220 V will become 310 V DC which may be too high for the motor. Also you may have to change the transistor with 400 V transistors. You can use 1N5408 for the diodes.
Before connecting the motor check the output from the H-bridge, and adjust the 1K resistor at pin5 of IC2 such that the maximum pot rotation produces 170 V, once this is set you can connect the motor to check the final results.
thanks sir. request indicate some transistor pairs suitable for above requirement.
Jayanath, I could not find any BJTs rated at 400 V 10 amps, so I think you should try the last concept instead.
dear sir. ok but there is a problem while making coil sir. i unable to found magnet wires. any other replacement for the coil sir? thank you.
Dear jayanath, the coil is optional and is required only to reduce RF noise in the motor and in nearby radio receivers. You can insert the coil afterwards once all the testing is completed. use 100k for R1 so that the maximum voltage is restricted to below 200V
dear sir is it BT 136 capable for the load of 2HP 180vdc motor ?
Hi Jayanath, BT136 will support upto 200 watts only. For 1500 watts you may have to use a 600 V 16 amp triac
dear sir,
NPN transistors are there but PNP 400v 15A is not found. any other replacement sir? can i use MOSFET instead above sir?
dear sir,
NPN transistors are there but PNP 400v 15A is not found. any other replacement or combination sir? please indicate. can i use MOSFET or any other for instead above sir?
Hi Jayanath, yes NPN is available but PNP is not available. For MOSFET also I couldn’t find a p-channel 400 v 10 amp device.
ok sir i will make and let you know. thanks again for early replies.
Dear Sir,
I am using T308 Treadmill for home. When i disconnect magnetic sensor motor running full speed. but when i connect sensor motor will rotate one round and stops. please let me know which of the components failure in control card. I replaced magnetic sensor still same issue.
Kindly help me out in this matter. Your timely help would be highly appreciated,
Thanks & Regards
Linus Fernandez
Dear Linus, It seems the sensor system is installed to control the motor over-speed through feedback…so may be the feedback loop has some problems and it could ne latching ON and stopping the motor from rotating.
Dear Mr. Swagatam thanks for the reply. if Possible please mark and send the location on PCB. so i can check the components.
Sorry Linus, that may not be possible because I have not seen the board practically so have no idea regarding the various stages.
Dear Swagatam, Thanks for the reply.
which schematic sir,i am still confuagused?
Second last one in the linked article
hello, I made the second circuit replacing the mosfet for irfp460 to run a 180v treadmill motor, the problem is that the mosfet overheats and the motor shuts down, what would be the problem?
Hi, what is the wattage or current rating of your motor.
thanks in advanced, so i have this information, cc motor 2.0hpm 180v. when I turn on and after 5 seconds I turn off the source because the mosfet gets hot.
That’s equal to around 8 amp current, and the MOSFET is rated to handle 20 amp, so its fine. The heating may be due to high resistance RDSon value of the MOSFET which is around 0.27 ohms. So you will have to attach a large heatsink to the mosfet to control its heating, or add two mosfets in parallel, or use a 300 V 70 amp mosfet or similar which may have a much lower RDson resistance.
Hello again Sir,
I have a general question regarding dimmer circuit.
Dimmer circuits are voltage regulator and as you know it can support high currents consumer by using high amp triacs or thyrestors.(like BTA41-600E, 40A, 600V)
So i think dimmers are good choice in acheiving required AC or DC voltage. Can it be used as source of DC voltage for like treadmill motors which need high currents?
And are they suitable choice instead of transformators? Why they are not used widely as voltage regulator?
Please clear this to me.
Thank you in advance
Hello Mah, Dimmer circuit is designed to work only for AC loads not for DC loads, because it won’t regulate low DC precisely and a slight wrong adjustment will burn the DC load.
If your motor is 220V rated then you can perhaps try the last circuit.
Thanks Swagatam,
I mean to use bridge rectifier after dimmer and not for low voltages.
I ran my 220 and 180 vdc motor by using a 4kw dimmer with bridge rectifier feeding the pwm circuit and worked very well. But what i dont know is the long time effects.
Then it’s fine Mah, you can use the last circuit which has a bridge rectifier with the dimmer input. If the triac is adequately rated with internal snubber built-in then it should last for a very long time.
BTA41-600E which rated 40Amp and 600V could work properly?
Yes it should work properly for any load below 4000 watts 220V
Thanks
Is this possible to use couple of triacs in paralell in order to get higher rated amps? I mean like mosfets.
No, triacs cannot be added in parallel, because they have different working characteristics compared to transistors.
Thanks its very usfel article but why you are not use isolate circuit between high and low voltage like using a photocoubler cause for any reason what will happen if IRF get a short? Also what you think about tl494 in this case?
You can add a optocoupler if you want, but it is not necessary.
TL494 circuit will also work.
Just i think its best to isolate between circutis cause if IRF have a short it will pass 180 volt to 555 circuit and we will loss all parts.
Hello Again,
I need some clarification about the second circuit mostly for types of pars.
1) Resistors are 0.25w 5% !
2) What are C1 and C2 voltage rates?
3) Which IC’s should be selected for the circuit ; LM555J, LMC555, BCR555, ICM555CD, NE555P, NE555DR, or ICM7555CD? kindly specify the suitable type.
4) D1 is a Zener Diode 2.7v 0.5W? or?
Thank You
Hello Mah,
All resistors are 1/4 watt 5%
All capacitor rating can be equal to 2 x supply voltage or above.
Any IC 555 will work.
the zener can be a 2.7 V, 3 V or a 3.3 V zener, any minimum watt.
Hello
have a question about the schematic with dimmer. must feed 180v treadmill motor. Will the motor maintain its torque at any rpm.
No it won’t, the design does not include a torque compensation feature.
Then I can do it with a different setup. Would like to use the engine in a belt sander. Hence the question for the torque.
Hi Swag,
Your site is awesome.
I am trying to control speed of a180VDC 5.5A motor by the proposed circuit without reverse facility.
Kindly correct me about the mentioned circuit about these concerns;
1) I need to convert 220Ac to 180VDc and connect the positive to place indicated as +12VDc in the Circuit !
2) The negetive line of 180VDc goes to common which indicated “0 in circle” in the circuit !
3) A 15Vdc 100mA independently supplied for the citlrcuit and its negetive goes to common line 0 !
Thank you again for your help and sorry for lack of information
Thanks Mah,
you are right with your assumptions, however converting 220V AC to DC will result in 310 V, which can damage the motor. Therefore I would recommend the fist circuit from the following article instead:
https://www.homemade-circuits.com/0-300v-variable-voltage-current/
You can eliminate the series lamp once the motor speed control is confirmed.
Thanks Bro
The world needs more like you.
It is my pleasure Mah.
Hi
The circuit you recommend to convert 230V ac to 180V dc can do max 1A. A treadmill motor needs much more current or not?
Hi, Actually the second circuit with single diode will be more suitable, but the R2 will need to be correctly dimensioned for delivering therequired amount of current.
However, the MOSFET and the R2 can get immensely hot, and may require a large heatsink
1st of all thank you very much mr.swag for your technical explanation against my ques,
let me try as u said, and i will reply,
it is much appreciated Sincerely,
JEMS JEHAN
My pleasure Jems….
Dear sir can i buy from u dc motor controller ?
i want as follows.
1) my motor max 180VDC 300watts, i need speed controller from ZERO to 160VDC
2) another motor max 130VDC 300watts, i need speed controller from ZERO to 120VDC
Jems, you can use the second last circuit, it will work perfectly as per your required specifications.
dear sir i have one clarification,
that i have few treadmill dc motor controller, i wanted to use these dc motor controller to some other dc motor same voltage speed variable operation purpose, but there is a speed feedback sensor,
but in my project motor there is no speed sensor and also i no need to use it, so how can i deactivate the speed sensor circuit in the treadmill motor drive board, please?
my requirement is to utilise treadmill dc motor board to sensorless dc motor.
please advise me how to deactivate the sensor circuit & optocoupler circuit?
Hello Jems, you can remove the entire sensor opto stage to remove the feedback.
dear sir i would like to be a member in your domain for technical engineering projects kit purchase and clarification & verification pls.
Dear Sir,
I have a brushed motor dc 50 V 2A max.
the dimmer chopper circuit above can be used as is it, or some components should be changed. I built a similar circuit, the triac got hot, after less than 30 sec. does a triac always get hot in such circuits ? a heat sink is necessary ? I saw some circuit like this with heat sink.
A perfect smooth driving is not really necessary to me, it is used to drive a diy small flour mill.
Does a shottky across the motor (snubber ) is usefull as protection or is not necessary to this motor ?
Thank you
Massimo, if it is a DC motor, then you must use the second last circuit, because 50 V cannot be used with a 220V input or a 120 V, even with a triac chopper
Hi Swag greetings to you from the U.S., state of Wisconsin, I just got my hands on a permanent magnet, 120 volt “DC”, 2.7 H.P., 19 amp motor. It came with a flywheel that weighed half a ton, so I removed it as it is going to replace an old AC 3/4 HP single phase, capacitor start. Do you think by removing that heavy flywheel that the DC motor will ever come close to drawing that rated 19 amps? And which circuit do you recommend to build, I just am sick of moving the drive belt to change speeds, that explains the DC motor as am looking for variable speed on a single pulley. Thank you very much Swag for your time, it is much appreciated as always!! Sincerely, Michael Sakach.
Thank you Michael for contacting me! I don’t think the motor would consume 19 amps without the flywheel. Being a capacitor start motor I would recommend a phase chopper controller circuit as given in the last diagram above, but without the bridge rectifier.
The following article explains the concept in greater details. For 3 HP just make sure to replace the triac with a BTA41/600 so that it is able handle the rated current comfortably
https://www.homemade-circuits.com/how-to-make-simplest-triac-flasher/
Swag the new motor for the drill press is a D.C. Permanent Magnet motor. The old motor was the A.C. capacitor start. I got it off a treadmill and the ratings for it are; D.C. 120 Volts Permanent Magnet, 2.7 Horsepower, 19 Amperes. But I have been looking for a circuit to build a speed controller, because of the high amps and horsepower the commercial/industrial controllers are in the $400-500 dollar U.S, range. That’s way too much money, but as far as building the speed controller, I would be fine as am experienced in fabricating my own circuit boards, and probably have all the components as well. I just am unable to find a circuit that will handle that large previously mentioned D.C. specifications of the treadmill motor I now have. This motor is a beast Swag, I have never seen such a large treadmill motor!!! It is almost as large as the old A.C. 3/4 HP motor that was previously on the drill press….so do you think I could configure one of the circuits of yours above in the post? Or should I be looking at a different approach to driving that big D.C. beast?? As always thank you for all you do for the electronics community, it is sure nice to have someone always there to help people through a design or troubleshoot a problem as you do on a daily basis for the whole world….thanks Swag
Sorry Michael, I guess I misread it, no problems, you can try the following diagram, this should work perfectly:
Let me know if you have more queries!
Please make sure to Add a 1K resistor between pin5 of IC2 and the ground line, I forgot to show it in the diagram.
Hello Swag,
How can this circuit be used for 180Vdc 5.5 A motor? I mean what changes should be done to do so.
Hello Mah, you can apply the second last design without any changes, except the MOSFET which must be rated at VDs = 200V and ID = 10 amp
Thanks Swag,
If you mean to use the dimmer one, here is my experience with it.
I made the dimmer circuit as you shown here on assembly board(i mean not using soldering tools). First i put a 100w bulb instead motor. It worked properly untill i turn the pot on 40%. Then the bulb got bright like it was in wall socket without any circuit.
I ran my motor on a paid 4kw dimmer with 8A bridge rectifier. Almost like your circuit with a BTA41-600E triac. But motor sounds like wizzz.
I want to use a PWM module to control the motor. I have all part of the circuit (without reverse) stuff only IRF840PBF Instead of irf540.
You think do i need anything more to control the 180VDC, 5.5A motor?
And if i want to use the first circuit, what are T1 ~T4? Can you name a proper model for T1~T4?
Thanks always
Mah
Hi Mah, I referred you the second last design, meaning the second circuit from bottom. You only need to change the MOSFET rest everything can be as is.
" rel="ugc">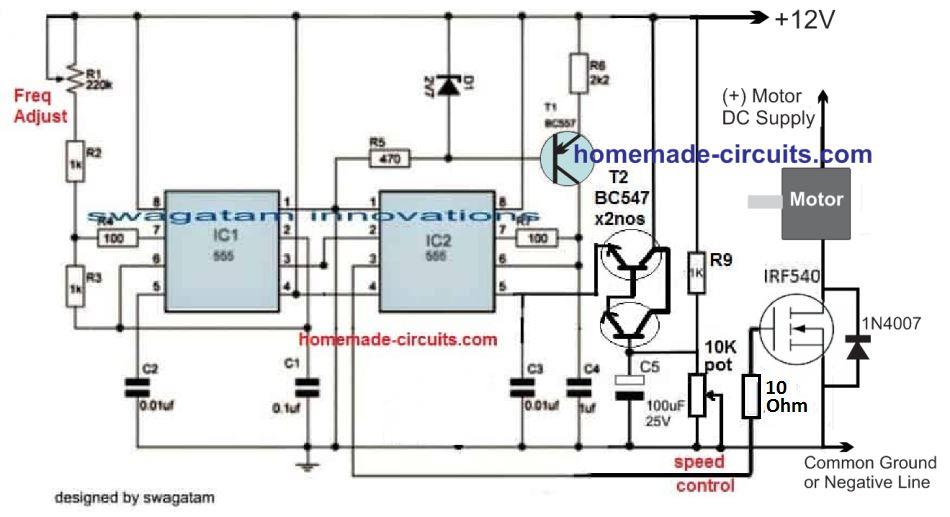
Hey Swag,
My first attempt to make the circuit as you suggest, was not successful but I am sure I will find a way to fix it ofcourse with your help. Here the summary of work;
The gate voltage of IRF840 was between 10.8 ~14.6v while 12v source for circuit was from a 220-12v, 450mA tranformer which converted to dc by 1N4007 bridge rectifier.
I should say that C1,C2,C3 rated voltage are 100V.
Thanks in advanced
Hey Mah, it is a tested design so it should work. The capacitors can be rated at 25V or above.
Hi,
I’ve been looking to build a speed controller for a 90VDC 4 amp brushed electric spindle motor on a Sherline micromill that I picked up. I was intrigued by this circuit design because of “its capability of sustaining and balancing optimal torque even at lower speeds ensuring a continuous working of the motor without stalling it during extreme low speeds.” This is necessary for milling operations. Could I possibly modify this circuit towork with this type of motor, and if so, what component modifications would be necessary?
Thanks!
Hi, yes that’s possible..you can try the modifications as presented in the following circuit
" rel="ugc">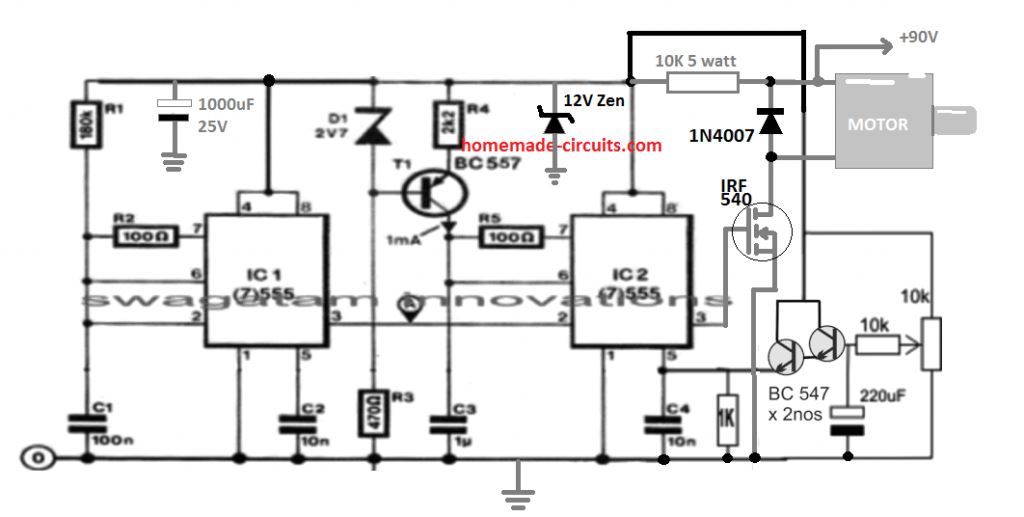
Thanks very much! I’ll give it a go…
I have a motor to treadmill 180 volt 5.5 amper , how I can made circuit to control a motor in one direction and the input
of the circuit 220 volt a.c
Eliminate everything that’s connected to the pin3 of IC2.
Connect a MOSFET with pin3. Gate to pin3, source to ground, and motor between 180V DC and drain of the MOSFET. The circuit should be supplied with a separate 12V DC, whose ground must be made common with the 180V DC ground. The MOSFET must be rated at 250V or more.
OK, how about if I use FJL6920 with TIP29C as the NPN darlington?
And I just need a forward motion, so I am going to get rid of the whole H-bridge network. Does that work?
If you want the H bridge, then Darlington may not be required. Use any 200V NPN transistor, connect its base with pin#3 of IC2 directly.
The motor can be connected across positive 110V and the transistor collector. You can also try a MOSfET instead.
make sure to apply a +12V separately to the IC positive line, and join all the negatives in common.also connect a 1N4007 diode across the motor
Hello,
Thanks a lot for teaching me so much in electronics. My motor has the following spec.
starting voltage/ current= 130vdc/16.2A
cont. voltage/ current= 110vdc/15.2A
Would you please tell me more about starting and cont. voltage/ current?
Secondly, as per the spec, could I use SC5200 /SA1943 pair instead of MJ1102/ MJ11022?
I have checked their spec. , they are having similar voltage and current max. So, what are the difference between those pairs?
Thirdly, could I use two NPN wired in parallel instead of a PNP / NPN combinations?
Thanks for your time!!
Glad you liked my site! Thanks
I am not sure what is starting voltage in your specifications, I think 110V should be the recommended voltage in any circumstances.
SC5200/SA1943 are not Darlington, so current gain and torque optimization will not be good. You can upgrade it by adding another NPN/PNP to convert it into a Darlington. The full bridge circuit shown will only work with NPN/PNP combination, no other combination will work
Dear Swagatam. I have a problem on the kind of project, i would really appreciate any assistance. I’m controlling a 180Vdc, 0.25kW PMDC motor using bluetooth, thus I can’t use 555 timer. I have been planning to use Arduino UNO, the problem is finding the relevant H-bridge driver since the PWM from the arduino is about 5V. Thanks in advance.
Hello Njabulo, you can use the H-bridge section from the above design and use it with your Arduino, a pair of anti-phase signals will be required for triggering the bJT H-bridge and the PWM could be injected at the bases of the low side BJTs.
If you are interested to use an IC, you could perhaps try the following concept
https://www.homemade-circuits.com/2014/01/simplest-full-bridge-inverter-circuit.html
Thank you, i will try it.
You can try for KSA1156 or any similar 250mA, 400V PNP BJT
my pleasure, wish you all the best!!
OK, for the PNP you could probably use MJE5852 and 2SAR340P together to form a 400V rated Darlington transistor, the configuration is simple and may e done as follows:
connect the emitter of the 2SAR with the base of MJE, connect their collectors together,
that's it, the darlington pair is ready.
use the collectors as a single collector, the base of 2SAR as the base, and emitter of MJE as the emitter for the final connection in the circuit.
I hope you got it.
Hi Rob, I tried to search for a 350V/400V 5/7 amp PNP Darlington transistor but strangely I could not find a single appropriate one. I'll do some more search and let you know soon if I happen to find one….if finally we are unable to find any, we can go for non-Darlington PNP BJTs with a supporting smaller PNP and configure the two like a Darlington
Alternatively you can also try Mosfets in place of BJTs and that would work equally good, according to me.
Hi sir, I have a DC motor which uses electromanets where Armature Voltage is 70VDC and Field voltage is 90 VDC.
Just help with a circuit diagram to power & regulate the speed, thanx
Hi Kakooza, if it's a DC motor then you can definitely use the first design which is explained in the above article.
make sure to use 12V for the circuit and 90V for the transistor bridge section.
and the transistor must be changed with suitable ones which can handle the applied volatge and current such as this one
https://www.homemade-circuits.com/2013/12/high-voltage-high-current-transistor.html
Hi Majumdar.
How are you?
I'm having a 2.5HP 180v DC Treadmill motor. I just want to make a circuit which can control its speed from zero to maximum. (No need for reverse direction)
Please guide me through simpler circuit as I'm beginner.
Please send me the Simulated File i.e Multisim or Proteous File if possible.
I'll shall be very thankful to you!!
May God bless you!
Chestno12@gmail.com
Hi Chestno,
you can try the first circuit from the above article, you can eliminate the S1 and N1—N6 stage completely, and join the R6/R7 ends together with pin#3 of IC2 for the required control.
..or you can simply use the concept explained in the following article
https://www.homemade-circuits.com/2012/05/make-this-pwm-based-dc-motor-speed.html
Hi Swagatam
In your simpler diagram depicted here:
1.bp.blogspot.com/-jONLYQ8Ehro/UkD_gzAjA-I/AAAAAAAAFSk/nt6vxMDF9RU/s1600/ELC+circuit.png
does the '+' next to the variable resistor indicate 12v Power Supply?
Also what can you recommend as the Mosfet in the circuit to drive a 180v DC motor (8 Amp) from a 250v power supply
Hi Peter, yes + indicates the +12V line of the circuit itself.
the BC547 should be actually BC557, please note this.
you can try a IRF450 for your motor application or any other similar.
Hi Swagatam
In your first diagram is there any reason you do not include a smoothing capacitor across the bridge rectifier
Hi Peter, if a capacitor is used the whole idea of PWM control would get mitigated, because adding filter capacitor would cause a constant peak voltage for the motor and stop the PWM function from controlling the motor speed.
Hi Mr. Mazumdar. Please let me know how to run a 180v dc 5400 rpm 1.5 hp motor from a threadmill with 220v ac current here in India. I'll send pictures of motor if you want to have a look. Please help me. Also let me know if this motor can be run both sides. Thank you so much for your time.
Hi Kamaal, you can try the second circuit from the above article
Thank you so much. I ll get someone who knows about circuits and I ll be in touch with you. Once again thanks for your patience and time. Have a nice time.
Dear sir, please let me know how can I run a 180v DC treadmill motor with 5400 rpm and 1.5 hp by using 220 v normal ac current in India. It would be great if I can send u pics of my motor.
I think it's already discussed in the above article and the comments…..you can preferably try the second circuit from the above article.
make sure to use a 100K resistor in series with the pot
Yes that's right! I am not sure about the torque issue, the dmmer will vary the average voltage level across the motor for the speed control, as per the pot operations.
but first make sure to test the dimmer circuit with an ordinary ceiling fan or a 200 watt bulb, before setting up the bridge and the treadmill motor
Hello Good Day,
I built this circuit for my treadmill, in AC Load (220VAC 500W) its working properly but when i connect it in 25Amp bridge type diode into the Motor my dimmer not working it continues running only but not slowing.
?oh=7ec61067d78551b101014a22e3d00e79&oe=5885D7A5" rel="nofollow ugc">
?oh=7ec61067d78551b101014a22e3d00e79&oe=5885D7A5
I thinking about to assemble your second schematic but i am not pretty sure it will work on my treadmill motor, (220VDC 1.35KW and around 8Amp) the rating of the motor.
https://www.google.com/search?q=Treadmill+speed+control&client=ms-android-asus&prmd=sivn&source=lnms&tbm=isch&sa=X&ved=0ahUKEwjRppW8jYDPAhWHOxQKHYYWA9AQ_AUICCgC&biw=360&bih=559#imgrc=Pa8o9PNgF_nwwM%3A
Can you help me with this problem sir?
Thank you very much.
Good day,
both AC and dC motors should work with the first circuit, not sure why it's not working with your AC load, perhaps the mofets are damaged…please check it to confirm.
the second circuit is also good and will work with both types of motors,…for AC motor do not use the bridge, connect it directly in place of the bridge.
make sure the triac is rated at 40 amps….use a BTA41600 type triac
Tenx for reply sir, i just reviewing my connections and Triac but its only BTA16600 only,
If i use circuit 2 of your article means i have to use BTA41600? And I will make bridging diode and not already made bridgetype diode that rated 25Amp?
Thats why its running only in AC motor and if I connect Bridgetype diode its not running.
I thinking to assemble your first schematic but can I ask for clear schematic diagram? Please and I'm Sorry because i don't know how to make it right.
you can refer to this page for the clear diagram
2.bp.blogspot.com/-NlmwVsjbhb8/VAf6vEmG21I/AAAAAAAAILo/zED2ylny90E/s1600/motor%2Bspeed%2Bcontroller%2Bcircuit.png
Ok thanks. I will let you know how it goes.
do any changes have to be made to the alternative designs for my situation? especially the 2nd alternative. The auto door control design calls for a irf540 mosfet which is rated for 100v source and my motor is 110 with rectified source being around 150v will that be a problem for that mosfet? or should replace it with a m11021 transistor instead? also the design calls for ICMM74C14 can ic4049 be used intead? The circuit looks like it is for a 12v motor. please advise if there is anything else in the auto door control circuit I must change for it to work with my 250w 110v dc motor. Thank you again for your time.
yes the existing mosfet will need to be replaced with a different mosfet having 200V/5 amp or nearby specs
4049 can be used for the design.
for operating with 110V DC, you will need to isolate the DPDT connection from the R2 point and connect it with your 110V DC source….and the circuit section will need to be powered from an external 12V DC supply.
rest all can be as is
…please make sure the negative of 110V DC joins with the 12v negative of the circuit….
Do the ic4049pins match the pins of the mm74c14? Like is 1 actually 1 and not some other pin? And Im assuming the 100kpot in the open/close door circut will be the knob I turn up and down to speedup/slowdown the motor is that correct. Also how do you suggest I isolate the dpdt switch? For some reason I was under the impression that connecting ground together from both circuits would allow high volts/current surge from the motor circuit to the controller circuit. Is that not the case? Thank you again for your time and responses.
Pinout matching of the two ICs is not important, you just have to use the 4049 gates in the appropriate locations as indicated in the diagram, you can refer to the datasheet of the 4049 IC for learning the details.
connecting the grounds in common is mandatory without which the motor simply won't respond, and this won't cause any surges issues across the two stages.
Thanks again for your prompt responses. With the isolation of the dpdt switch to the 110v motor circuit Im assuming the mosfet at Q1 as well as the diode at d3 will also be moved to the 110v line correct? If so is the zener at z1 still needed? Or would it Also be moved to the 110v circuit? Thanks again for all your help. I have ordered everything I need to build the circuit and am waiting for arrival so I will keep you updated with how it goes. Thanks
yes that's correct, D3, mosfet, DPDT all needs to be separated from the circuit and connected with the high voltage DC, as shown here
1.bp.blogspot.com/-X72f9qUy-iA/VBGuxilwsBI/AAAAAAAAIOs/yqGppAoBpGA/s1600/pwm%2Barduino.png
Z1 can be removed, it's not crucial if the 12V input is fairly constant
Ok great.. And that reminds me i forgot to mention for the 12v circuit i recall you mentioning an smps power supply however i dont know how to tell if it is a smps powersupply or not… im using a small ac to dc (wall dart) power adapter which belonged to a wireless router enclosure. It is label rated at input: 120ac 60hz. 300ma AC and output: 12v 1a DC.. When plugged in and tested with mutimeter and no load it reads 13.67v dc and it seemed pretty constant but then again it had no load. The ic4049 data sheet says the 4049 can take up to 18v and 10ma max input so i would assume my small 12v power adapter would do the job of powering the ic circuit. But i keep worrying about the smps situation so i just wanted to ask about that. Im not sure how crucial smps was to the operation of the circuit. Thanks again.
I suggested an SMPS since most smps have regulated output using zener controlled feedback.
yes 13/14V will cause no harm to the circuit although a fixed 12V is the recommended value….initially you can go ahead with your available set up, and see how it responds.
Hello sir thank you for your time and the courtesy of putting these circut designs online. I have lathe which the electronic control went bad on … its got a 250w 110 vdc motor and i want to build a circut like the first one at the top of the page to use as a speed controller. Would it be possible to build the pwm circuit excactly as shown but using a 556 timer for my purposes? secondly would it be possible to use a dpdt switch instead of the transistor h-bridge for directional control of the pwm signal or would that not work? 3rd since i plan on full bridge rectification of 110vac mains and am expecting to end up some where around 156v dc after rectification and my motor only needs 110v would i be able to use a voltage divider to create the 15v vcc input? lastly do the uf ratings of the capcitors change with the higher vaoltage needed in my circuit? Thank you for you time and your response would be greatly appreciated.
Thank you Angel
yes IC 556 will work as good as two IC555…
DPDT can be used for reversing the motor manually instead of the bridge network.
the PWM pot can be appropriately set such that the maximum output never exceeds the 110V DC for the motor.
preferably you must use a separate AC/DC adapter for the IC section, a 12V AC to DC SMPS adapter will do the job nicely
the uF rating has no relation to motor voltage.
Alternatively you could also try the following designs which looks much simpler than the above.
https://www.homemade-circuits.com/2012/05/make-this-pwm-based-dc-motor-speed.html
https://www.homemade-circuits.com/2014/09/automatic-pwm-door-openclose-controller.html
I built the DC 180v motor controller using triac, the motor starts fine for 15 seconds or so then starts fluctuating in the speed till it stops!
Any help would be appreciated.
which triac did you use? is it getting hot?….you can first test the circuit with a 200 watt bulb and make sure the bulb dims across the entire pot rotation uniformly…
Hi Mr. Majumdar, is it possible for me to reach you through mail please?
Hi Mr.Lim, I normally do not find time to respond to emails, so this place is the best place to interact with me.
". . .however for driving the MOC you'll need a PWM feed."
That's exactly what I meaned mentioning using MOC series chip, at least it combines the advantages of both circuits, presented here.
yes that correct…. it will work purely on a PWM feed and it could be entirely different from the ordinary triac dimmer concept
Mr.Majumdar as you said at the begining "Here's a SIMPLE PWM based motor speed controller circuit which can be used for controlling a treadmill speed right from zero to maximum." Your blog (which I consider very useful and interesting) is visited as you can see (at least this theme) by newcommers. If the circuit is too complicated and the people who will try to build do not have even the slightest idea of how it works and how to be checked for troubleshooting, then what is this all about? Even Mr.Samuel, the man who gave the request, did he run the circuit?
Alright, let it be so, let's forget about this . . . . How abot slowing the on threshold of the second circuit, it's the main disadvantage of it? The output starts not from the zero but from few dozens of volts. I think that it's because of the high breakdown voltage of the BD3 diac. Can something else be used instead of diac, for example something from the MOCxxxx zero-cross series? I think it will be much more comfortable for the motor starting at 20-30rpm or even less, for example instead of, let's say, 300rpm.
the word "simple" was mentioned in context to the subject….compared the complexity of the PWM concept this circuit looks easy that's was I meant to say in the article..
But even if we consider it as simple and friendly to a newcomer, so it means you could not make this simple circuit work?
as far as guidance is concerned, I am always ready and I have always been helpful to everybody in this blog, and all have shown tremendous trust in me and my work.
yes you can use a MOC3043 IC for driving your motor and I think it would make things much safer, however for driving the MOC you'll need a PWM feed.
And what's so hard in the first circuit so I must be an expert in order to run it? The only adjustable component inside is the pot?! There were much more tricky circuits I created at once. I think it's time to show you my circuit under which I created the board. It's not absolutely the same as yours because of the single way rotation needed. I'm uploading a PCB picture too. Let me know if there's something wrong with the circuit . . . .
The circuit:
postimg.org/image/fw67qv2w5/
The board:
postimg.org/image/8ex0bndd1/
when you are not able to troubleshoot a circuit then it's complicated for you.
a circuit is not about just building it exactly as shown, it's about knowing precisely how it's designed to function and troubleshoot the problems if anything goes wrong.
Can you tell me how the IC1 and IC2 together become responsible to generate the PWMs in response to the pot adjustments?? and what's the function of each of the parts??
sorry I can't verify the pics because it can be too time consuming…but I can assure you that the circuit in the first diagram is correct and has been tested by me, now it's upto you to discover the faults by checking it stage wise.
I have explained how 555 geneartes PWMs in the following article elabprately:
https://www.homemade-circuits.com/2012/12/how-to-use-ic-555-for-generating-pwm.html
Hi, mr.Majumdar, I did the first circuit. As expected, it doesn't work. I'm absolutely (120%) that it was correctly assembled. I used a light bulb as a load, because the motor is a very risky try. When the pot is at min. there's no voltage on the bulb, but when slightly opened, 207V are suddenly on it and so on until pot gets on max. With other words, there is not any stepless driving of the load – just on or off. With the scope there are pulses on the pin 3 of IC2, but it is impossible to say if their width changes or not – they are very hard to be distinguished each from other.
Hi Mr. Ivan, The first circuit has been tested by me not once but many number of times for different applications. This is one of the best PWM controller circuits I have ever seen, so it's beyond doubt that this circuit would surely work.
However the design is not simple and it's recommended only for the experts in the field who has a thorough knowledge of practical and theoretical electronics.
For the last circuit also you said the triac burnt, whereas as per the datasheet the triac is rated to handle 40 amp continuously and 200 amps in the form of short pulses, that's again extremely strange….the datasheet cannot be wrong?
". . . .such as BTA41/800 etc"
It was BTA41/600 already. Besides that, the noise from the motor becomes louder when the RPM's go down. The speed cannot be adjusted from zero (at least not in my case) and is unstable. And finally, if there's a man on the treadmills belt when the problem occurs, he will fall down, with possible injury.
Thanks for paying attention to me and my problems, will find the solution with the first circuit!
Best regards, Ivan!
OK, no problem….then you can go with the first PWM based concept, let me know if you have problems while making it…
Hello, mr.Mjumdar, I haven't been there long time ago. I finished my tests with dimmer driving of PMDC motor 8 months ago and I rate them as danger and unreliable with regard to safety and stability. Once the triac blowed up and the motor raised its RPM's to the space before the fuse interrupted the mains circuit. The idea with putting a powerful light bulb as a voltage divider is groundless because of the power it dissipates in the small area of the treadmills motor bay.
That's why I will try with the PWM concept, no matter of his complexity, not to mention that the original development used the same technology. I hope it will work much better than the previous one.
Best regards, Ivan
Hello Ivan,
if the blowing-up of the triac was the issue, in that case you try using a bigger and a higher rated triac, and also employ a fuse in series, that would solve the issue. The important thing is that whether or not the dimmer concept works and is able to regulate the motor? If it does then I think the triac issue can be corrected by simply using a more stronger or high current triac such as BTA41/800 etc.
The PWM option is also great but compared to the dimmer circuit ity looks much complicated and technically difficult.
Anyway I wish you all the best!
(repeating my posting as I'm not sure it went through…) Hi Swagatam, thanks for this. I'm trying to fix my treadmill using the dimmer + bridge rectifier option you show at the end. I have a 2000W AC dimmer, a 50A 1000V bridge rectifier and a 400V 4.7uF capacitor across the DC output. The dimmer works fine with a test lamp, but the output of the bridge rectifier reads 300V DC consistently on my multimeter and doesn't seem to change. I tried connecting it to the treadmill and it blew the fuse in the dimmer and destroyed it. Not sure if I have broken the treadmill.
Do you have any idea what I am doing wrong? Is the capacitor too big/small? Should I use a lower power bridge rectifier? Any advice or suggestions? Thanks, Nick
Hi Nick, I seem to have lost your previous comment, not sure how and where.
As for the last circuit, It looks to be technically correct, however a closer inspection shows that the inclusion of the filter capacitor across the bridge rectifier could be causing the issue, please remove it and test it once again.
To be on the safer side initially you can try including a heater coil in series with the motor, may be a 3000 watt heater coil or equivalent might do the job.
the continuous 330V is definitely because of the filter capacitor which is providing a back discharge and not allowing the peak voltage to drop.
Thanks, Swagatam. I replaced the dimmer and have now removed the capacitor. I don't have a heater coil, but I connected up a 100W bulb (40 ohms) in series with the motor to avoid drawing too much current. The bulb gets brighter and dimmer and the voltage across it varies nicely from 0V to 220V, but the motor is not moving at all.
Do you think the bulb is providing too much resistance? At 40 ohms, the max current is 4A and the motor is rated to 11A, so perhaps the motor needs more current. Or perhaps my several earlier attempts have blown the motor. Is there an easy way to tell?
Thanks again for your help.
Hi Nick, the series load should be at least 3 times more powerful than the actual load, otherwise it could completely block the actual load's functioning by introducing a much higher resistance in the path….a 100 watt is definitely not the correct match for the proposed testing….it should be at least twice the wattage of the load, although I am not aware of the actual load wattage that you are using, i assume it to be much bigger than 100 watt
Do you sell treadmill motor speed boards? I am new and lost with all your excellent info.
Robert
sorry, no I don't sell assembled boards, but anyway thanks a lot for being a part of my website, I appreciate your response.
Hi Majudar,I want to construct a motor controller based on the open source design here
https://www.dropbox.com/s/if915wxhl8ninua/osmc3-2%20sch.pdf?dl=0
I want to use the circuit to power a 180V 15A d.c motor but i don't know how to go about modifying the original circuit for this purpose.
According to the documentation provided, the circuit can handle currents up to 160A thanks to the IRF1405 mosfet in use.
Now, i know i have to change to a mosfet with a current rating of about 15A based on my motor specification but i dont know how to make the system operate at up to 180V. Do i also have to find a mosfet (or BJT) with more than 180V rating? The mosfet currently in use is rated 55V, 133A.
Also, the circuit has an HIP4081A mosfet driver, please can you briefly explain how a mosfet driver works and whether this particular mosfet driver will be appropriate based on the ratings below.
The mosfet driver is rated, High Side Voltage = 95V, supply voltage = 9.5 V ~ 15 V
Hi Folajimi,
yes the mosfet rating will need to be well over 200V, and 20 amps for safe operations.
I'll check the datasheet of the driver IC and try to update the info soon for you.
the 180V can be derived from either a step down transformer or from an smps adapter, which may be specially designed and procured for your application.
Hi Majumdar,
Thanks for the reply. It's been very helpful. I am expecting your response regarding the MOSFET driver. However, I want to add that i intend to run the motor from a 24V battery and not from mains.
Thank you.
Jimi
Hi Jimi,
if the input supply is a 24V battery then you will have to employ a boost converter circuit for acquring the required 180V, you can try the following design for the conversion:
https://www.homemade-circuits.com/2013/03/how-to-convert-12v-dc-to-220v-ac-using.html
the IC 555 supply should be protected with a 7812 IC as it's not specified to work with 24V
the simple circuit 12vdc that says dummy load connected to the mosfet
please provide the link
1.bp.blogspot.com/-jONLYQ8Ehro/UkD_gzAjA-I/AAAAAAAAFSk/nt6vxMDF9RU/s1600/ELC+circuit.png
here it is
yes you can use this set up, use 1K pot for control instead of 10k.
100 is 100 ohms, you can use lower values than this for the mosfet gate
sounds good : but on ic 2 pin 3 what dose 100 mean ?? and for the mosfet the application notes points out that the drain should be connected to a positive terminal of the supply and you say the neg – ??? thank you
which circuit are you referring too…? I can't see anything marked as 100 in the first circuit IC2 (pin3) above……. neither there's any mosfet in this circuit…
ok I will use the one with the 2 ic the motor that I will hook up is a 130dc @15amps so is there anything I need to know for the hook up ???thank you
please do exactly as shown in the first diagram, you will succeed in getting the intended results
thank you : the diagram dose not read indicated voltage, but I got it now , the circuit I am using is the one with the 556 ic I only need the single speed. thank you I will start to build it.
in the above article 555 IC are shown but if you wish you can use a single 556 instead of the shown two 555
voltage is not indicated because different users may have different voltage requirements as per their motor specs.
ok so just connect the 130dc on the plus where the motor is connected and the – to 0 rail : I don't understand how the motor would get the pluses. thank you swagatam
130 (+) to the point indicated as "motor voltage"
the pulses are applied to the respective transistor bases.
I am referring to the first circuit in the above article.
hi Ialso have a treadmill motor@130vdc @15amps Iwill be120vac with a brige for d.cv and feeding the ic with 0-18 vdc after wiring and putting in all the parts needed, my question is where dose the 130vdc come from to hook up the motor???
The 130v will come from your mains AC outlet after rectifying it through a bridge diode network, although it would become 150V after rectification, can still be used for a 130V motor considering the regulation feature available with the circuit.
…the motor connections and the voltage for the motor are clearly indicated in the first diagram.
thank you for the reply: after it is rectify I have to go throught the 556 ? but I cant the ic can only take 18vdc ,130 will fry it????
you can employ a 12v AC/DC adapter for powering the ICs separately, and make the negative common with the 130V DC
hi I am really missing something here, so the 130vdc dosent go throught the circuit, so then how is it hook up, ??? the 130vdc thank you
it's clearly shown in the diagram, the point indicated "motor voltage" should be applied with the 130V positive, and the negative to the lower rail of the bridge….all the negative or the earth symbols must be made into a common line.
Hello, I have build the diagram but when I turned it on the motor started to turn but I could not control it. I think it has something to do with the IRF840 I used. According to the datasheet of this it has a build in diode so it lets the DC power go straight thru in one direction. I've tried to put the power in the other way but then it blow out the other diode D3. Do you have any idea what to do?
Kind regards
Rookie
Hello Rookie, referring to the following circuit:
https://www.homemade-circuits.com/2014/09/automatic-pwm-door-openclose-controller.html
initially don't connect the load or the 220V AC, just power the circuit with 12V and check the gate voltage while varying the pot.
The voltage must show a corresponding 0 to 12V variation, if this does not happen would indicate either a faulty IC or connections,
the diode inside the mosfet has nothing to do with its performance, it's there for protecting the device from transients and back EMFs.
Hey Swagatam,
Excuse me for the late reply. I've checked the voltage and its varied while turning at the pot only the voltage varies between the 0.8 and 11 volts. So this part works.
But when i start the circuit at zero, i can turn it slowly to max but it won't turn down anymore. When i've done this i have to wait a few hours then i can do the same thing again.
Do you have any other suggestions?
Kind regards
Rookie
Hi Rookie, to which diagram are you referring to?? I will recommend that you build the first diagram in the above article. You can eliminate the stage that's connected after pin3 of IC2…..you can directly connect the mosfet gate to pin3 of IC2, then connect the load between the motor +V and the mosfet drain.
the source of the mosfet will connect with the circuit negative.
the +Vcc for the circuit should be applied from a 12V DC adapter.
Thank you very much, i will try to start building this weekend or maybe next week. I will let you know how it is going.
Great, You are welcome rookie!
Hello Mr. Majumdar,
I want to build this diagram for my bench lathe. Could i use it for this? On the nameplate of the lathe it says 220 Volt 800 Watt and i know that it is a DC motor. If so wat for components should i use for T2…T5 and for D2….D5?
Hello rookie,
you can rather try the following circuit which is relatively simpler and will be suitable for your application:
https://www.homemade-circuits.com/2014/09/automatic-pwm-door-openclose-controller.html
Thanks for the quick reply.
But the other diagram also includes a 12 volts dc motor and on my lathe is a 220 volt dc motor. I want to use a rectifier and a capacitor for the power supply of the motor direct from the wall outlet. If i replace Q1 for another, could i feed it directly the 220 Volt Dc? And do you have a proposal for the Q1 replacement?
yes you'll need to replace the 12V fet with a 500V fet….probably an IRF840 would do the job.
The rectified positive of the 220V will need to be applied at the junction of D3 and the switch making sure that it's been first perfectly disconnected from R2 and the 12V supply line
the negative from the rectifier will connect with the negative of the circuit.
P1 will need to be connected with an appropriately dimensioned series resistor so that the max voltage to the motor is restricted at 220V, because the rectified voltage could be well above 300V
This seem lot better? i.imgur.com/dG5wInu.png
should i change the diode to 1n4007? or is fine what it's for 130v motor?
the diode polarities inside the bridge is incorrect, it should be exactly as given in my diagram.
You can try 1N5408 instead of 1N4007
alright I appreciate your help. Would 1N4007 would do it?
where? inside the bridge?
you can try 1N5408
Alright I have become more knowledgeable with symbol. I was though different symbol at my class and realize American standard symbol and Europe symbol look very different. anyway I redraw the diagram from Proteus and wanted to have you look it over and see if i'm missing anything feel free to edit it. i.imgur.com/NHR9ug3.png
Question The VCC is 15v but wasn't sure if it's DC or AC on your schematic. I'm almost done getting all parts from ebay to put it together.
The diagram looks OK, except the transistors in the bridge…you'll need to swap T4/T5 and T2/T3 positions. meaning T5 will move to T4 and vice versa, same with T2/T3. In other words the upper transistors should be NPN and the lower ones PNP.
electronic circuits always work with DC, never with AC, so the 15V is DC…preferably use 12V DC.
Thanks for the help. Sorry i'm still learning electronic circuit. Here some more question i.imgur.com/MPDZgep.png on schematic.
My kind request to you is not to proceed with this project, you seem to be extremely new to electronics, and this project is not for the newcomers with no prior experience.
everything is clearly shown in the diagram if you are unable to read the symbols you need to study the basics first and proceed gradually.
I clearly Understand the circuit is just that some symbol look different I'm working on proteus 8 and stimulating it in order to build the circuit. here a link of my half work so far. That why i'm asking the property value and which you used for the project that work and from there I cant experiment. i.imgur.com/VP0JdCE.png
I have read all those post and many picture of schematic I have Permanent Magnet DC Motor with specs of Volts 130 , AMP 10.0 . HP 2.5, RPM 4500, Rotation CW, Duty Continuous. Which of your diagram should I use to power this motor and use 10k pot to control from 0 to max and I would like a reverse on motor can DPDT switch will do? any pointer would help. Thanks for all your time.
you can try the first diagram for your application but you should have an access to 130V Dc for supplying the motor via the transistor bridge
an ordinary SPDT switch will be enough for the reversal
couple question base on the image here the link i.imgur.com/IxaxT14.png
Appreciate your time.
diode is a zener diode
all the caps are 25V rated
N1—N6 are the gates from the IC 4049, refer its datasheet for a clearer view
Any possibility contact you in skype or phone? or txt msg i had 3 mc2100ls rev controller for treadmill <,< is fried <,< so i gonna make one my own my motor use 130v and 10amp.
i feel more comfortable interacting through my blog…
does cap on schemetic what voltage should they be on? example 10uf should it be 100v or 220v or 400v? confuse sorry still learning the symbol
in the first circuit those are 25V rated since the supply is 12 to 15V
Thanks for the example but . . . . the transistor you mentioned in the part list is "Q1 = ANY 100V, 20AMP P-channel MOSFET". Are 100V enough for Q1 in my case?
How about C3 (the reservoir capacitor) from the link? In the part list it is 100uF/100V one. I think in my case it should be at least 400V. And is 100uF capacity enough?
Thanks in advance!
No, for your application the transistor should be 300 to 400 v rated…the filter capacitor will also need to be rated at 400 V minimum….100uF is sufficient because the filtration level is not critical for the speed control functioning.
And how about a buck converter with flywheel circuit, just like in the link below?
postimg.org/image/vv40maqnj/
We already have a PWM controlled power transistor, all that remains is just the flywheel circuit (a diode, inductor and a capacitor). As long as I can see it will provide directly 180V from the 230V rectified AC grid voltage in the power line. Would you provide such circuit, mr. Majumdar? Please!
The shown design can be used for your application…you can drive the buck transistor through any high frequency oscillator configuration
an example circuit can be witnessed here
https://www.homemade-circuits.com/2014/06/solar-panel-buck-converter-circuit-with.html
just make sure that the drain of the mosfet is isolated from the R1—R5 positive line and gets separately connected with the 300 DC rectified source.
The positive line of R1—-R5 must be connected with the above 300V DC lien through a 100k resistor and a 12V zener attached across the positive R1—R5 positive and the common ground.
IC1 stage may be ignored and removed….D2 could be replaced with a 200 V zener diode.
sorry, it's not the drain rather the source of the mosfet that should be isolated and connected to the 300V DC source….
A buck converter . . . . Would you post a proper simple circuit of it for my case (which is the case of the theme at all). Embedding it into the main circuit will give it a finished look.
Thanks in advance!
there's another way of keeping the voltage under control, as shown here:
4.bp.blogspot.com/-zEbdlZt9sTo/VEoQWzsHz5I/AAAAAAAAIfs/p53qd3foLaA/s1600/voltage%2Bcontrol%2Bfor%2BIRS2453.png
the collector of the transistor should be connected with the base of the "blue" BC547 in the first diagram.
The 220k should be adjusted such that transistor in the above link just begins conducting at 190V, an additional 22k preset could be used in series with the 220 k on the input side and used as a fine control preset
in the link above a bridge can be seen, which could be replaced with a single diode from the 220k preset upper lead to the 220V DC
Yes, but the original board was also powered by 220V without any lamps or otger resisting elements. Rather I was meaning that all the circuit can be set to power the motor to 180V only no matter what the grid voltage is – with other words we have 220V, but the power transistor passes only 180 of them at maximum turn of the potentiometer.
The circuit from the link you posted is with MOSFET, there's no problem to drive it directly from the IC, but in the first circuit above power Darlington BJT's are used. I don't intend to use MOSFETs anymore.
""no matter how 220 v is rectified the result will be always dangerous for the lower rated motor….""
Why?! Do half-wave and full-wave rectification give one and the same effective value of the rectified voltage?! You said in one of your posts above:
""The 180V could be achieved through a half wave rectification using a single 6A4 diode and filtered using a 10uF/400V capacitor.""
Exactly that was my second question. That's why I want to get clear everything before start to build the circuit. Thanks!
These are PWM circuits they don't control voltage rather the RMS value… in other words it controls the average voltage by breaking the input into a calculated ON/OFF sequences, but the peak voltage always remains equal to the input, that's why it could be dangerous, initially I suggested using a single diode method considering the small difference between the motor and the mains voltage levels, but it's always good to be on the safer side and therefore the peak voltage issue must also be considered.
whether it's a full wave or half wave, the input peak again would be equal to the supply mains input.
a buck converter concept must be incorporated for dropping the voltage or the other short cut method would be to use a series 50 v lamp
I think I got the idea – the RC group together with BC547 works like a time-delay stage so the voltage change from the pot comes to pin 5 delayed depending on the values of R and C. That's smart!
I need few answers:
1. How about the power stage? Will a single MJ11022 be enough as a power stage.I am about to use a ST901T as a preamp stage and two MJ11022 as power stage.
2. The motor voltage is 180V and the grid's voltage is 230V AC. If I use a full-wave rectifier and a smoothing capacitor the rectified voltage will be above the motor's and even transistor's allowable. The other way is to use half-wave rectifier (single diode) and a capacitor behind it in order to get smoothed voltage with the value motor needs. Should I use some bigger capacitor (the original board had a 470uF/400V one). Can I use it again? As long as I know a capacitor's capacity is determined proportional to the load's current.
Please answer all my questions!
a preamp stage is not required, the power device can be directly linked with pin3 of the IC….as shown in this example design:
1.bp.blogspot.com/-jONLYQ8Ehro/UkD_gzAjA-I/AAAAAAAAFSk/nt6vxMDF9RU/s1600/ELC+circuit.png
no matter how 220 v is rectified the result will be always dangerous for the lower rated motor….one solution would be to use a 50 V lamp in series with the motor in order to absorb the extra 50V, the ampere rating of the lamp should be identical to the motor…
So, what should those R and C be? From pin 5 capacitor and resistor in sequence to the gound? What should their values be? Does the C4 (10nF) stay at it's place in that case?
Thanks in advance!
i'll try to update the info in the diagram soon…
done…please check it out
I thought the thyristor will work like half-wave rectifier together with the phase cut-off process. This is because of the voltage differences of the grid and engine (220V and 180V respectively). A lot of these circuits are widely used for motor speed controls. By the way the author of the circuit I uploaded says that the C1 capacitor's value is determined experimentally (between 1 and 10 uF) to choose less jerk and max torque (something like compromise between both). If nothing happens with my circuit, I'll do your first one.
I have another question – what will happend if the value of the pot increases rapidly when the engine goes at slow speed? By my opinion the voltage above the engine will also increase the same way and the power element (SCR, transistor) will fail immediately. I mentioned that the treadmill has opto-tachometer originally. I think it gives feedback to the controller about the current speed of the engine no matter what is the speed set by the user. The speed of the motor will equalize with the speed set by the user, but slowly which prewents this rapid change of the voltage/current. It would be great to implement the tachometer in your first circuit in order to prevent overload of the transistors when the pot shaft is rotated sharply.
Best regards, Ivan!
It would be interesting to check the second circuit also, first by confirming it with an AC bulb and then reverting with the shown bridge network
a tachometer can be avoided by simply adding a resistor/capacitor network at pin5 of IC2 which will slow down the change regardless how fast the pot or the voltage is varied
Mr. Majumdar, I didn't say anything about your first circuit, at least my was with MOSFET stage unlike yours. As for the second one, I tried alll the things you said – removing the engine and the bridge and using a 100W lamp as AC load. The result was the same. Anyway . . . . Now I found another circuit in one of our old elctronic magazines (I'm from Bulgaria). Unlike your second circuit it uses thyristor (SCR), not triac.
postimg.org/image/49kyj0io3/
It's used for drill machines and can power a engine up to 800W. The list of elements is in bulgarian, that's why I'm not posting it here. As in the circuit above, a bridge rectifier and a smoothing capacitor should give my treadmill DC motor what it needs . . . . . I hope.
Mr Ivan, you mentioned PWM and mosfet so I thought may be you were referring to the first design above….
anyway the second circuit is a very basic fan dimmer switch design that we use in our homes for controlling fan speeds or light intensity….i have tested the circuit thoroughly and have one installed in my house….so if an AC load is not working in your circuit then definitely there's something incorrect in your circuit assembly.
The image that you ahve provided will controll speeds upti 50% only and will create lot of jerk at lower speeds….i already have a similar design posted in my blog here:
https://www.homemade-circuits.com/2012/01/how-to-make-versatile-closed-loop.html
Hi, Mr.Majumdar, the dimmer circuit simply does not work, I did 3 times, the load works always at the grid's voltage (220V), no matter the potentiometer setting. All the elements are the same as required, the circuit has been checked maybe 30-40 times, everything is correct but it doesn't work. I also did a circuit with PWM and a MOSFET, the same fails everytime at nearly half turned potentiometer and the engine is even at idle.
I never imagined that controlling the speed of a DC motor can be so difficult!!!
Hi Mr. Ivan the first circuit has been tested by me and it worked right at the first shot, so it surely works, but all these can be difficult for any newcomer i can understand that.
in the second circuit, remove the motor, the bridge diodes network..verify the circuit using an AC lamp as shown in the following lamp, if this doesn't work will mean your circuit is faulty somewhere
1.bp.blogspot.com/-s2Fe-xTv4YA/T4V-Z597HLI/AAAAAAAABFk/mafeMQ6JYm4/s1600/How+to+Control+AC+Motor+or+a+Ceiling+Fan.jpg
connect a 100 watt bulb in place of the "AC motor" in the above link
Thanks, mr. Majumdar, one more question, what diameter should the iron core of L1 have?
Thanks Ivan, The diameter of the core could be such that it accommodates the 200 turns comfortably, it could be done over an iron bolt or screw…but the diameter of the wire should be more than the indicated 0.6 mm since the motor is rated to carry high currents…a 1.5 mm could be tried initially.
Your work will be highly appreciated because I'm trying to run this treadmill for 4 months. An easy-to-build and cheap solution will be more than a good result for me.
I have updated the required diagram above, please check it out.
Hello, mr Majumdar, I have something much simplier in view with respect to 180V DC treadmill motor control powered from 220V AC grid. The parameters are:
– 220V AC power grid
– 180V permanent magnet DC motor 7Amps motor
– main control element a SCR (thyristor) simultaneously acting like rectifier and control element with phase controlling circuit
– a capacitor in parallel after the thyristor acting simultaneously like smoothing element for the phase-cutted sine and voltage-raising capacitor (just like in the last circuit you offered me).
– a SCR control circuit that uses phase-cut method – cutting the sine at different angles in order to get different voltage values above the motor.
I think it will be much simpler than the two 555 timers PWM and Darlington stages.
Best regards!
Hello Ivan, yes that's a smart idea, since the load is 180 V rated using a dimmer switch circuit as the speed controller is definitely possible, the motor output will only require a bridge network and filter capacitor for the AC to DC conversion.
If possible I'll try to update the design in the above article soon.
Hi any possibility a ready made controller can be purchased. I do not have a knowledge about electronics and am desperate in powering up my treadmill.
Hi, I wish I could help by doing it for you, but I am sorry, presently that looks difficult due to lack of time.
Just a single ST901T?! I have 1640W of power which makes around 9A of current at 180V and the Icmax of ST901T is just 4A?! The motor will not be loaded at the maximum power rate but still isn't 4A too less? How about 2 or even 3 ST901T's in parallel?
sorry it won't work, I seems I missed the amp spec of the device.
you can either search for a suitable single device or connect many of these in parallel, just make sure all of these are mounted over a single common heatsink.
Sorry for my last post, I knew that this is the peak value of the voltage formed by the capacitor, but the post was already on its way. At all I intend to use this circuit:
2.bp.blogspot.com/-wJnI3vNWGoo/UoxAV_X6LyI/AAAAAAAAFxU/7NZJ4A2bg88/s1600/treadmill+motor+speed+controller+circuit.png
I have also some differences – I need one direction and have 180V DC motor at 2.2HP (that's 1640W of power). It seems that the circuit must be without those NOT gates because of the single way rotation and I'll need only 2 power transistors (in parallel oor in sequence). I don't know only what should be those Darlingtons?
Yes, you are right the NOT gates won't be required in the referred diagram.
For the transistor you can simply use a single high voltage Darligton transistor such as ST901T with pin3 of IC2 for the required implementation.
Hi, Mr. Majumdar, I did exactly as you told me – a half-wave rectifier with 6A4 diode and a 10uF/400V capacitor, but the voltage between the poles of the capacitor is 325V DC!
Hi Ivan, it's showing the peak voltage, once connected to the load the voltage will come down to the specified level, however still it could be not so safe to apply the pulsating peaks to the motor, so I think you will have to get a suitable auto-transformer designed from a transformer maker. Tell him to design a transformer which would be able to supply 150V/6amp from 220V….this output can be then bridge rectified and filtered to acquire the required 180v for your motor.
Thanks, I'll do it!
Mr. Majumdar, I have a similar problem. I have a treadmill which controller chip has failed and now i would like to build independent control of the motor. It is PMDC (Permanent-magnet DC) motor, 180V, 6.8A. I want to control it's speed from zero to max by powering it from 220V AC power grid. Can you give some circuit similar to the above one, but for 220V AC, please?
Hi Ivan, you can try the following simple design
https://www.homemade-circuits.com/2012/05/make-this-pwm-based-dc-motor-speed.html
Just make sure that the circuit supply is acquired from a 12V AC/DC adapter while the motor terminal from a 180V Dc (+) source
The (-) of the 180V must be made common with the (-) of the 12V supply or the (-) of the circuit
The 180V could be achieved through a half wave rectification using a single 6A4 diode and filtered using a 10uF/400V capacitor.
The MOSFET should be an IRF840
Thanks for the reply, Mr. Majumdar, but the circuit you offer uses PWM. How about just changing the gate voltage in order to control the drain current? Is this possible and which way is the best?
Hi ivan, It's not possible to control a mosfet drain load with a varying gate voltage, PWM is the easiest and the most ideal way of achieving the intended speed control through a mosfet.
Many thanks Sir. Now it looks very promising.
Regards,
Wes
You are welcome!!
Dear Swagatam, many thanks for your fast replies.
I’ve managed to put everything together and pluged in. Unfortunatelly when my treadmill motor (220VDC/3.5hp)
started to turn a smoke come out from one of the BJTs.
Now it looks like all four of them (mj11021pnp-mj11022-npn) has gone, cos I can’t see any reading between base-collector, emitter when testing them.
What I’ve noticed afterwards that it was a bad solder between R6 and bases of T2,T3.Virtually no connection at all. Also I’ve used 1N4744 as a D1.
What do you think Sir. Any suggestions?
Regards, Wes.
Dear Wes,
A bad solder won't cause a burning problem according to me, I think the treadmill motor could have exceeded the max amp rating of the BJTs,
Replace the circuit with new transistors and try operating the treadmill without any load, check the response,
the other reason could be wrongly configured BJTs
….1N4744 are zener diodes and will never work here, you'll have to use rectifier diodes such as 6A4 etc.
this could be an issue too
Many thanks Swagatam.
New high voltage transistors just been ordered. You're right. After closer examination it looks like BJTs were wrongly configured. This cause them to burn.
So do you think that I could use four 6A4 rectifiers in the bridge instead of 1N4001 as it is in your cuircuit?
Talking about Zenner diodes, I'm using 1N4744 instead of 2v7 as a D1 which is a Zenner diode in your circuit. I don't use them in the bridge.
Regards Sir,
Wes
OK Wes, that's good! yes 6A4 is the minimum requirement for the bridge diodes, 1N4001 will not do as these will blow of due to the high motor back emf.
I mistakenly thought that you had used the zener in the motor bridge circuit,….surely it will do in place of the shown 2.7V zener
Many thanks Sir for this publication.
I'm sorry for dump questions but I'm newbe to electronics.
Will this work with my 240VDC/12A motor?
How many of this CD4049UBE CD4049 4049 IC Hex Buffer/Converters do I need to order?
Regards,
Wes
My pleasure! yes it'll work with the specified motor, you'll need to use high voltage BJTs for it as given in the following datasheet:
https://www.homemade-circuits.com/2014/04/mj11021pnp-mj11022-npn-high-voltage.html
Only one 4049 IC is required for the above design
Thanks a lot!
im sorry one more, R4 is that 2.2k or 2002 ?
it's 2.2k
what is D1 is it a zener diode
yes it's a zener diode.
hello friend! I need to do a project to control a 36v 350watt battery powered motorcycle, do you have any projects that can help me? God bless you friend.
Yes I have a related design which can be used to control any DC motor with finger push PWM control:
https://www.homemade-circuits.com/simple-e-bike-circuit-electric-bike/
Thanks for this fantastic circuit diagram. I'm new to electronics so please excuse me if these are dumb questions. Would there need to be any programming done to make this work or does the hardware do all that automatically? Also, I wouldn't need the reverse feature and a simpler circuit would definitely be easier for a beginner like me. Could you show us what this circuit would look like without the components necessary for the reverse feature and how I could make this work using 110vac i.e. Where would the ac come in and where would it be rectified? Thanks again!
Thanks very much Michael, no programing is required for the devices all the ICs come preprogrammed, just have to wire them up in the shown manner.
If you are not interested in the reversing feature the circuit definitely becomes much simpler as shown in the following image:
1.bp.blogspot.com/-jONLYQ8Ehro/UkD_gzAjA-I/AAAAAAAAFSk/nt6vxMDF9RU/s1600/ELC+circuit.png
ignore the four diodes shown at the top which was drawn for some other similar application need.
the mosfet upper lead which is drain needs to be connected with the motor negative, while the positive of the motor will connect with the 110V DC or whatever may be the motor operational voltage spec.
The circuit would however need to be powered through a 12V AC/DC adapter specified to take the input from a 110V AC, nowadays such adapters are suited for any input right from 85V AC to 285V AC, so it won't be much of a concern
The shown pot could be used for the required speed control.
Excellent. Thanks!
Thanks for the great design! Why are the BJTs better here, as I understand BJTs are preferred for low current applications, while MOSFETs are for high power functions.
Thanks,
Matt M
If the requirement is above 30 amps mosfets could be preferred…mosfets require stricter parameters while configuring compared to BJTs therefore sometimes become difficult to handle.
however in the above design mosfets could be used since the configuration does not demand a high side driver due to the involvement of both n/p mosftes..
I'm putting together a shopping list for this project. 1/4 watt metal film resistors would work, right?
C3 is listed as 1uf, what voltage and style of capacitor should i get? The other caps I was going to buy 50VDC ceramic disc. My motor is rated at 130VDC 15A, i was going to power the motor with 110VAC thru a bridge rectifier, any ideas on what transistors to buy? IRF540 is only 100volts One last thing, what is the symbol just left of C1? I apologize for my lack of knowledge.
BJTs are easier to handle than mosfets, so it's better to use BJTs here.
Thank you for your replies. I have all the part numbers figured out and I am excited to build this circuit. This is an amazing site and appreciate the time you dedicate to helping others. Thank You.
You are welcome!
Hello
My treadmill motor is rated for 130VDC and 15a. I plan on using 120vac(line voltage) and a bridge rectifier to power the motor. What type of transistors would I use for T2-T5? I don't recognize the symbol you used. IRF540 mosfet is only 100v, I think. any advice is welcome.
Also, what is the symbol just left of C1? I apologize for my lack of knowledge.
Hello,
You can use MJ11021(PNP) MJ11022 (NPN) for the transistors
It indicates the (0) volt line or the negative volt line.
Hi, Could you explain how a constant torque at low speeds is achieved? My treadmill bogs down slightly with each step when I get below about 1.2mph.
Constant torque is achieved by the use of PWMs which prevent the devices from unnecessarily heating up yet allowing them to conduct fully during the ON states of the devices.
So it's like allowing the devices to conduct fully with full power yet only at the desired slower speeds by breaking their conduction many number of times per second.