The 4 simple car voltage current regulator circuits I have explained below is created as a immediate alternative to any standard regulator and, although developed principally for a dynamo it will function equally effectively with an alternator.
If the functioning of a traditional car alternator voltage regulator is analyzed, we find it amazing that these kinds of regulators is often as trusted as they are.
While most contemporary cars are furnished with solid-state voltage regulators to regulate the voltage and current output from the alternator, you may still find countless earlier cars installed with electromechanical type of voltage regulators that happen to be potentially unreliable.
How Electro-Mechanical Car Regulator Work
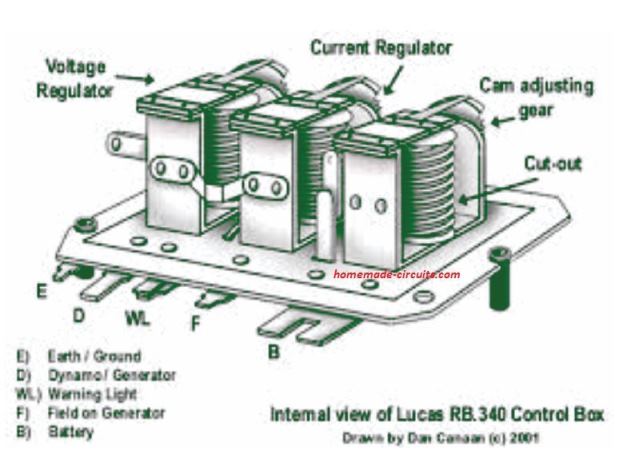
The standard functioning of a electro-mechanical car alternator voltage regulator can be as I have explained below:
Once the engine is in the idling mode the dynamo starts getting a field current through the ignition warning lamp.
In this position the dynamo armature remains unattached with the battery since its output is smaller compared to battery voltage, and the battery starts discharging through it.
As the speed of the engine begins increasing, the output voltage of the dynamo also begins rising. As soon as it surpasses the battery voltage a relay is switched ON, connecting the dynamo armature with the battery.
This initiates the charging of the battery. In case the dynamo output goes up even more an additional relay is activated at around 14.5 volts which cuts off the dynamo field winding.
The field current decays while the output voltage begins dropping right up until this relay deactivates. The relay at this point consistently switches ON/OFF repeatedly, sustaining the dynamo output at 14.5 V.
This action safeguards the battery from overcharging.
There's also a 3rd relay containing its coil winding in series with the dynamo output, through which the entire dynamo output current passes.
Once the safe output current of the dynamo gets dangerously high, may be due to over discharged battery, this winding activates the relay. This relay now detaches the field winding of the dynamo.
The function ensures that just the fundamental theory, and the specific circuit of the proposed car voltage current regulator may have different specs depending on a specific car dimensions.
1) Using Power Transistors
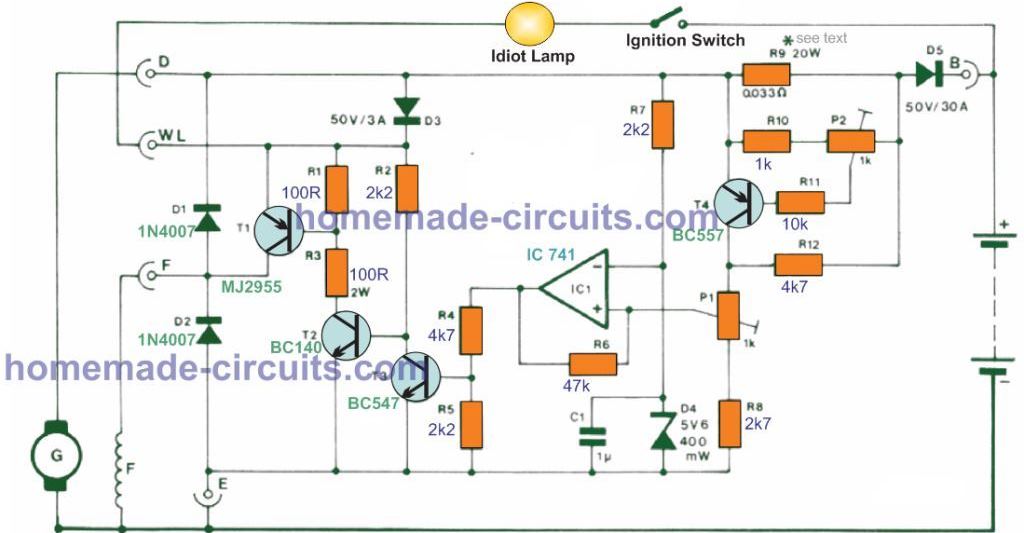
In the indicated design the cut-out relay is substituted by D5, which gets reverse-biased as soon as the dynamo output drops below the battery voltage.
The battery as a result is unable to discharge into the dynamo. If the ignition is started up the dynamo field winding gets current through the tell-tale light and T1.
Diode D3 is incorporated to avoid current becoming drawn from the field coil due to the reduced armature resistance of the alternator. As the speed of the engine increases the output from the dynamo proportionately rises, and starts delivering its own field current by means of D3 and T1.
As the cathode side voltage of D3 goes up the warning light gradually dims until it fades off.
When the dynamo output reaches to around 13-14 V the battery begins charging again. IC1 works like a a voltage comparator which tracks the dynamo output voltage.
As the dynamo output voltage increases the voltage on the op amp inverting input is at first greater than at the non-inverting input, hence the IC output is held low and T3 remains switched off.
As soon as the output voltage goes higher than 5.6 V the inverting input voltage is regulated and controlled at this level by D4.
When the output voltage goes past the specified highest potential (set through P1), the non-inverting input of IC1 becomes higher than the inverting input, causing the IC1 output to change into positive. This activates T3. which switches OFF T2 and T1, inhibiting current to the dynamo field.
The dynamo field current now decays and the output voltage begins dropping until the comparator reverts back again. R6 supplies several hundred millivolts of hysteresis which helps the circuit to work like a switching regulator. T1 is either toggled harder ON or is cut off such that it dissipates fairly low power.
Current regulation is impacted through T4. Once the current by means of R9 is higher than the selected highest level, the voltage drop around it results in T4 to switch on. This raises the potential at the non-inverting input of IC1 and isolates the dynamo field current.
The value selected for R9 (0.033 Ohm/20 W, made up of 10nos of 0.33 Ohm/2 W resistors in parallel) is suitable to get a optimum output current as high as 20 A. If larger output currents is desired, R9 value could be reduced appropriately.
The output voltage and current of the device must be fixed by appropriately setting up P1 and P2 to meet the standards of the original regulator. T1 and D5 should be installed on heatsinks, and must be strictly isolated from the chassis.
2) A Simpler Car Alternator Voltage Current Regulator
The following diagram shows another variant of a solid state car alternator voltage and current controller circuit using minimum number of components.
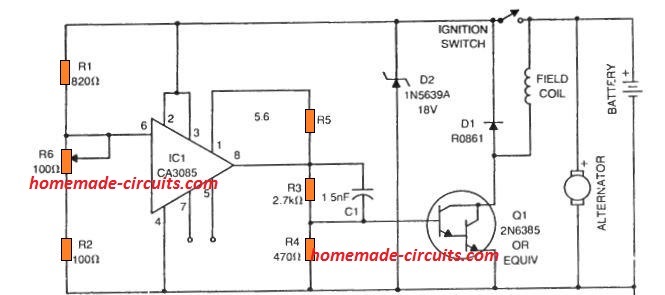
Normally while the battery voltage is below, the full charge level, the regulator IC CA 3085 output remains switch OFF, which allows the Darlington transistor to be in the conducting mode, which keeps the field coil energized, and the alternator operational.
Since the IC CA3085 is rigged as a basic comparator here, when the battery charges to its full charge level, may ba 14.2 V, the potential at pin#6 of the IC changes to 0V, switching OFF the supply to th field coil.
Due to this the current from the alternator decays, inhibiting any further charging of the battery. The battery is thus stopped from overcharging.
Now, as the battery voltage drops below the CA3085 pin6 threshold, the output becomes high once again, causing the transistor to conduct, and power the field coil.
The alternator begins supplying to the battery, so that it begins charging again.
Parts List

3) Transistorized Car Alternator Regulator Circuit
Referring lo the nest solid-state alternator voltage current regulator diagram below, V4 is configured like a series-pass transistor which regulates the current to the field of the alternator. This transistor along with the two 20 amp diodes are clamped on an external heatsink. It is intriguing to see that dissipation of V1 is not really very high even during the maximum field current, rather merely within 3 amps.
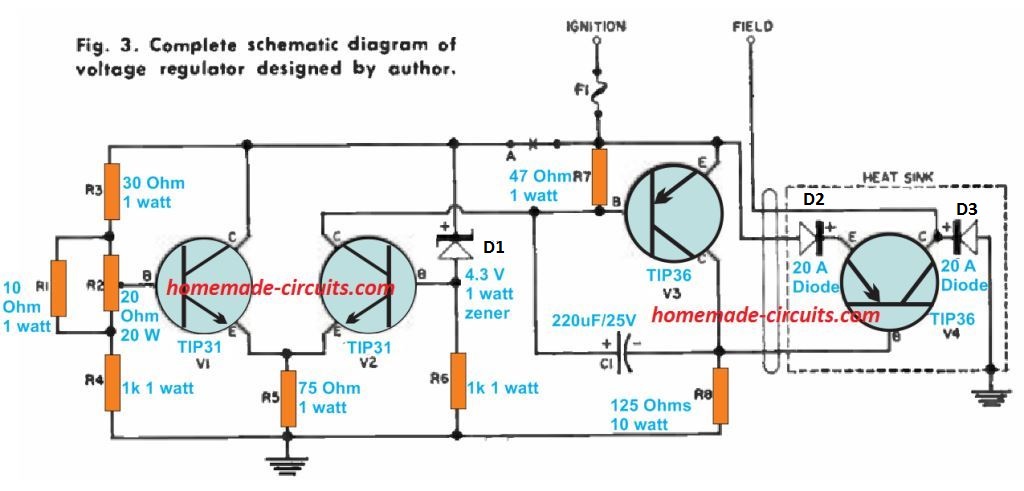
However, instead of the mid-range at which the voltage drop across the field is corresponding to that of transistor V1 causing a highest dissipation of not more than 10 watts.
Diode D1 provides protection to the pass transistor V4 from the inductive spikes generated within the field coil any time the ignition switch is switched off. Diode D2 which transfers the entire field current supplies extra working voltage for driver transistor V2 and guarantees that the pass transistor V4 could be cut-off at large background temperatures.
Transistor V3 works like a driver for V4 and a base-current swing of 3 ma to 5 ma upon this transistor allows total "on" to full "off" switching of V4.
Resistor R8 offers a route for the current during excessive temperatures. Capacitor C1 is essential to protect against oscillation of the regulator because of the high gain loop that is created around the the system. A Tantalum capacitor is recommended here for increased precision.
The primary element of the control-sensing circuit is enclosed within the balanced differential amplifier consisting of transistors V1 and V2. Special concern had been provided to the layout of this alternator regulator is to make sure there is no temperature drifting issues. To achieve this most linked resistors must be wire-wounds types.
The voltage control potentiometer R2 deserves specific consideration as it should never move away from its settings due to vibrations or temperature extreme conditions. The 20-ohm pot employed in this design worked ideally well for this program however nearly every good Wirewound pot in the rotary style might be just fine. The rectilinear trimpot varieties must be avoided in this car alternator voltage current regulator design.
The zener reference diode is important. Not just because it sets voltage reference but also because it controls system temperature coefficient. So the differential amplifier is made temperature-stable to stop drifting. It uses known diode coefficient about -0.04% per degree centigrade.
Now how it works is simple. When engine speed goes up then battery voltage also goes up. This makes charging current increase.
If field current stays same at start then higher battery voltage increases base current of transistor V₂. Then base current of V₁ also increases but less than V₂. This happens because of resistor network R₁ R₂ R₃ and R.
Ok… since collector current of V₁ goes down and V₂ collector current goes up, something interesting happens. Current in resistor R stays about same because it comes from V₂ collector current and V₁ base current. So when V₂ collector current increases, it must make V₁ base current smaller. This also reduces alternator field current.
Because of this alternator output voltage comes back to almost same as before. How close depends on regulator gain. In this case gain is very high.
Now about the setup. Transistors V₁ and V₂ are put on heat sinks. Not because they need cooling but to keep them strong.
Best if they stay close together so no temperature difference happens between them. The reference zener CR has its own place.
4) IC 741 Car Alternator Voltage Current Regulator Charger Circuit
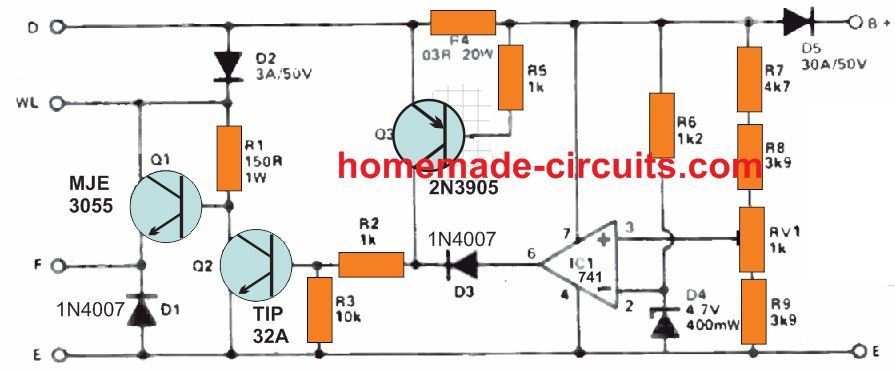
This circuit offers solid-state management of battery charging. The alternator's field winding is in the beginning stimulated through the ignition light bulb just as in a traditional method.
Current moving across the WL terminal travels via Q1 to the F terminal then finally on the field coil. As soon as the engine is powered, current from car's dynamo moves through D2 to Q1. The ignition tell-tale lamp fades out since the WL terminal voltage exceeds than that of the battery. Current likewise moves through D5 towards the battery.
At this point, IC1 which is rigged as a comparator detects the battery voltage. When this voltage on the non-inverting input becomes higher than the inverting input (clamped at 4.6 volts via zener D4) causes the output of the op amp to go high.
Current subsequently passes via D3 and R2 towards the Q2 base and instantly switches it ON. This action as a result grounds the Q1 base switching it off and removing the current applied on the field winding. The alternator output now drops, causing battery voltage to also drop correspondingly.
This procedure ensures that the battery voltage is always held constant, and is never allowed to be over charged. The battery full charge voltage can be tweaked through RV1 to roughly 13.5 volts.
During cold weather conditions while starting the car, the battery voltage may drops significantly low. As soon as the engine has ignited the battery's internal resistance also become quite low, forcing it to pull too much current from the alternator and thus leading to a possible deterioration of the alternator. In order to restrict this high current consumption, resistor R4 is introduced within the primary power terminal from the alternator.
The R4 resistance is selected making sure that at highest possible current (Commonly 20 amps) 0.6 volts is generated across it which causes Q3 to turn ON. The moment Q3 activates current moves through the power line through R2 towards the Q2 base, switching it on, which then, shuts off Q1 and cutting off current flow to the field winding. Due to this the dynamo or the alternator output now drops.
No modifications need to be made to the original wiring of the alternator in the car. The circuit could be encased within an old regulator box, Q1, Q2 and D5 must be attached to an appropriately dimensioned heat sink.