In this project we are going learn how to make a simple unipolar stepper motor driver circuit using 555 timer IC. Apart from 555 timer we also need IC CD 4017 which is a decade counter IC.
By Ankit Negi
Any unipolar motor can be connected to this circuit for performing specific task, though you need to do some small changes first.
Speed of the stepper motor can be controlled from a potentiometer connected between discharge and threshold pin of 555 timer.
Stepper Motor Basics
Stepper motors are used in areas where a specific amount of rotation is required, not achievable using ordinary d.c motors. A typical application of stepper motor is in a 3D PRINTER. You will find two types of popular stepper motor: UNIPOLAR and BIPOLAR.
As the name suggests unipolar stepper motor contains windings with common wire which can be easily energized one by one.
Whereas bipolar stepper motor does not have a common terminal between coils due to which it cannot be driven simply by using the proposed circuit. To drive bipolar stepper motor we need an h-bridge circuit.
COMPONENTS:
1. 555 TIMER IC
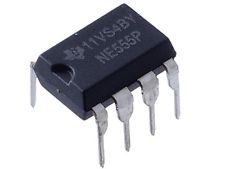
2. CD 4017 IC
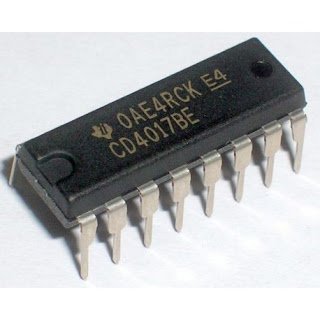
3. RESISTORS 4.7K, 1K
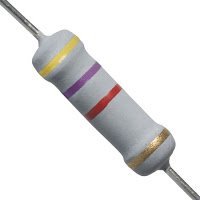
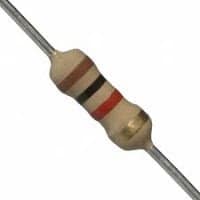
4. POTENTIOMETER 220K
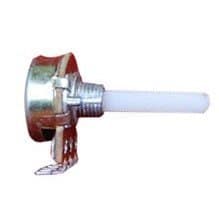
5. 1 uf CAPACITOR
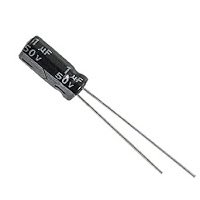
6. 4 DIODES 1N4007
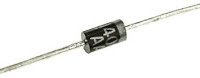
7. 4 TRANSISTORS 2N2222

8. UNIPOLAR STEPPER MOTOR
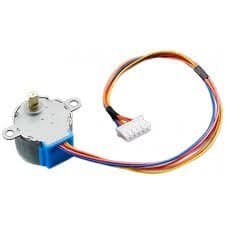
9. DC POWER SOURCE
PURPOSE OF 555 TIMER:
555 timer is required here to generate clock pulses of particular frequency (can be varied using 220k pot) which determines the speed of the stepper motor.
IC 555 Pinout details
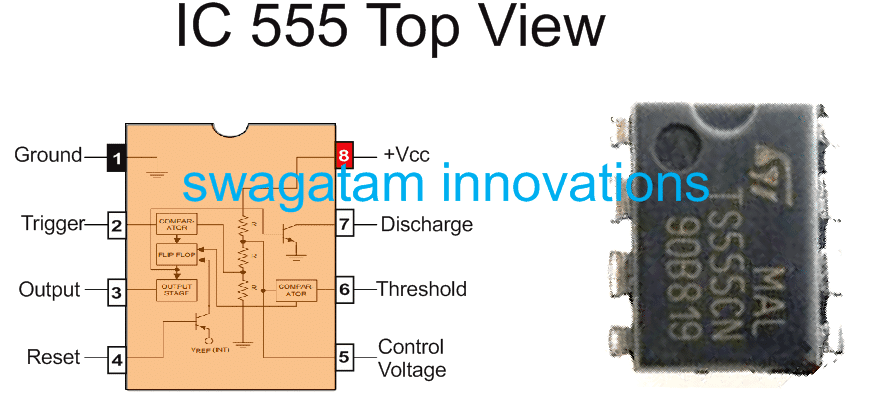
PURPOSE OF CD4017:
As already mentioned above, it is a decade counter IC i.e., it can count up to 10 clock pulses. What make this IC special is that it has its own inbuilt decoder. Due to which you do not have to add an additional IC to decode binary numbers.
4017 counts up to 10 clock pulses from 555 timer and gives high output corresponding to each clock pulse one by one from its 10 output pins. At a time only one pin is high.
PURPOSE OF TRANSISTORS:
There are two purposes of transistor here:
1. Transistors act like switches here, thus energizing one coil at a time.
2. Transistors enable high current to pass through them and then motor, thus excluding 555 timer completely as it can supply very little amount of current.
CIRCUIT DIAGRAM:
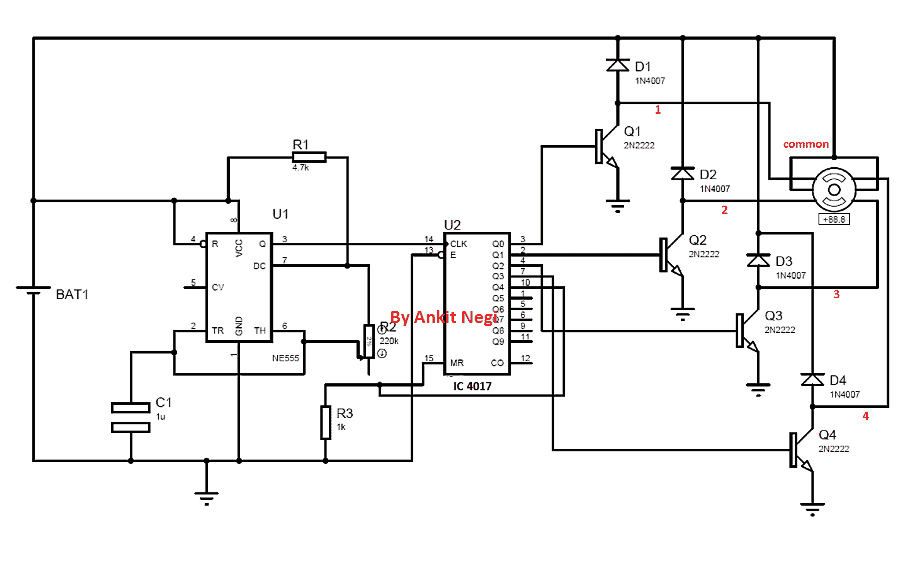
Note: Please make sure to add a series 1k resistor with the bases of each transistor, otherwise the transistors may quickly burn.
Make connections as shown in figure.
1. Connect pin 3 or output pin of 555 timer to pin 14 (clock pin ) of IC 4017.
2. Connect enable pin or 13th pin of 4017 to ground.
3. Connect pins 3,2,4,7 one by one to transistors 1,2,3,4 respectively.
4. Connect 10 and 15th pin to ground through a 1k resistor.
5. Connect common wire of stepper motor to the positive of supply.
6. Connect other wires of stepper motor in such a way so that coils are energized one by one to complete one full revolution properly.( you can look into datasheet of the motor provided by the manufacturer)
WHY OUTPUT PIN 10 OF IC 4017 IS CONNECTED TO ITS PIN 15 (RESET PIN)?
As already mentioned above 4017 counts clock pulses one by one up to 10th clock pulse and gives high output on output pins accordingly, each output pin goes high.
This causes certain delay in rotation of motor which is unnecessary. As we require only first four pins for one complete revolution of motor or first four decimal counts from o to 3, pin no. 10 is connected to pin15 so that after 4rth count IC resets and counting starts from the beginning again. This ensures no interruption in the motor’s rotation.
WORKING:
After making connections properly if you switch on the circuit motor will start rotating in steps. 555 timer produces clock pulses depending on the values of resistor, potentiometer and capacitor.
If you change value of any of these three component frequency of clock pulse will change.
These clock pulses are given to IC CD 4017 which then counts the clock pulses one by one and give 1 as output to pin no 3,2,4,7 respectively and repeats this process continuously.
Since transistor Q1 is connected to pin 3, it switches on first then transistor Q2 followed by Q3 and Q4. But when one transistor is on all other remain off.
When Q1 is on it acts like a closed switch and current flows through common wire to wire 1 and then to ground through transistor Q1.
This energizes coil 1 and motor rotates at some angle which depends on clock frequency. Then same thing happens with Q2 which energizes coil 2 followed by coil 3 and coil 4. Thus one complete revolution is obtained.
When potentiometer is rotated:
Let’s say initially position of pot is such that there is maximum resistance (220k) between discharge and threshold pin. Formula for frequency of output clock pulse is :
F = 1.44/(R1 + 2R2)C1
It is clear from the formula that frequency of clock pulses decreases as value of R2 increases. Thus when R2 or pot’s value is maximum, frequency is minimum due to which IC 4017 counts more slowly and gives more delayed output.
As value of resistance R2 decreases, frequency increases which causes minimum delay between outputs of IC 4017. And hence stepper motor rotates faster.
Thus value of potentiometer determines speed of the stepper motor.
SIMULATION VIDEO:
Here you can clearly see how speed of the motor varies with resistance R2. Its value is first decreased and then increased which in turn first increases and then decreases speed of the stepper motor.

Stepper Motor Driver Circuit using BJT and MOSFET H-Bridge Configuration
The following diagram was drawn and contributed by Mr. Thiệu, who is a dedicated reader of this blog and an avid electronic enthusiast. I am thankful to him for his kind contribution to this blog.
The complete circuit diagram for the stepper motor driver using IC 555, IC 4017 and MOSFET H-bridge is shown in the following figure.
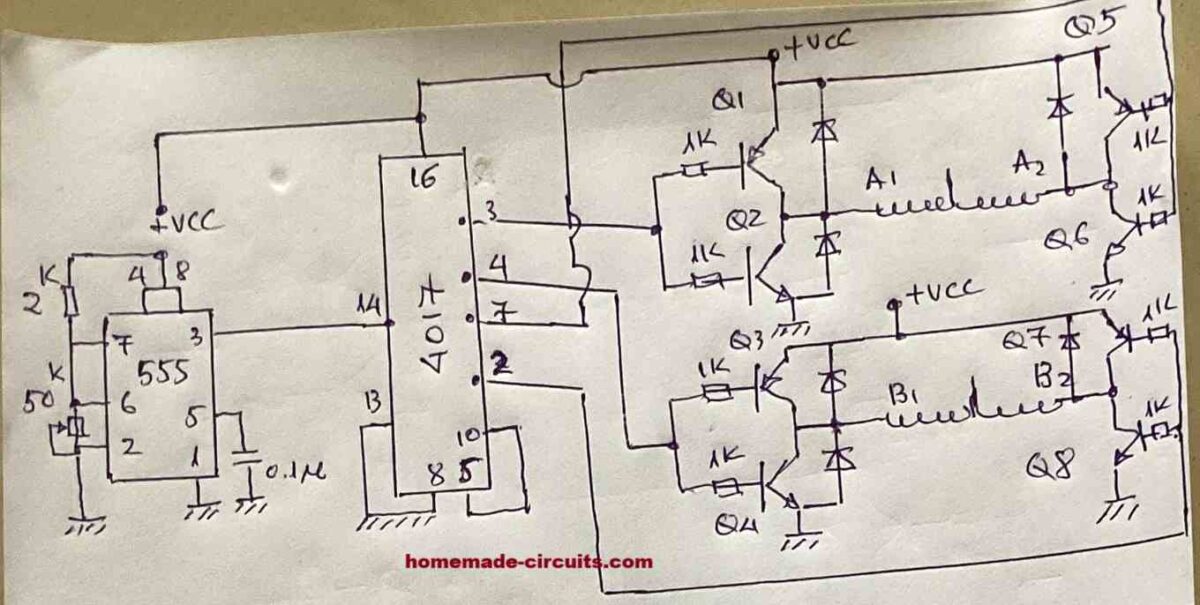
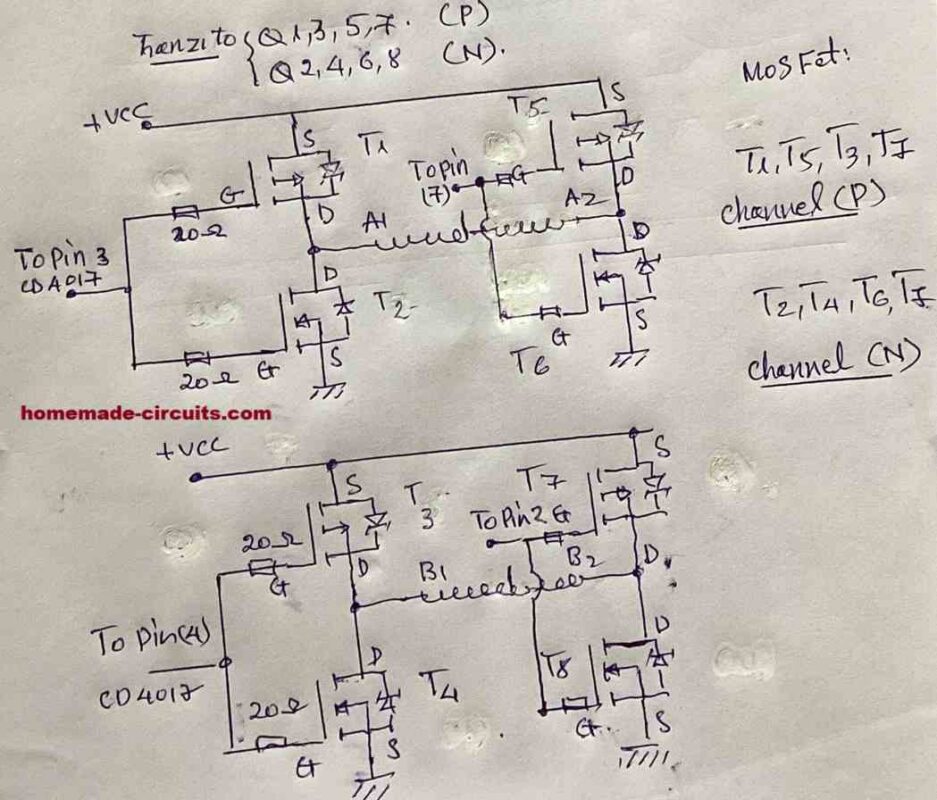