In the following post I have explained two straightforward dummy load circuits: the first one can be used for testing high current power supplies, and the second design can be used for testing large power amplifiers.
Suppose you have a 10 amp power supply and you want to confirm the 10 amp output through some sort of dummy load which can absorb 10 amp current. For this, you would have to build a 10 amp current sink using many high watt resistors connected in series and parallel. This arrangement could be hugely cumbersome and bulky.
Instead, an adjustable transistorized dummy load circuit could do the job more efficiently by sinking the 10 amp current from the power supply and help the user to confirm that the power supply is actually able to deliver the intended 10 amp current.
In this circuit, the high power transistors could be optimized and adjusted to sink or shunt the power supply current at some specific rate, which could be adjusted through a potentiometer, thus making the procedure very smooth and accurate.
You can test power supplies and related devices at maximum peak output current without resorting to arrays of power resistors, using this dummy load circuit, which is nothing but a simple transistor current sink circuit.
Without the need of costly non-inductive resistors, an adjustable current sink permits the load to be adjusted fast across a large range, irrespective of the voltage source. And thus removes the need to fiddle with power resistors each time the voltage and/or output current characteristics of the power supplies or devices under test are changed, for example during the testing of power supplies.
How the Circuit Works
The current load is shared by transistors QL1 and QL2, which are balanced by their emitter resistors R1 and R2, whose quantities should be in the.2 ohm to.1 ohm range.
Therefore, simply by connecting power transistors QL1 and QL2, we may raise the circuit's current-load capacity to whatever we want, restricted by just the transistors' absolute limits.
A few common junkbox-type load transistors, like for example NPN 2N3055s, may come with a VCE of 60 volts, an Ic at about 15 amps, and power dissipation of 115 watts.
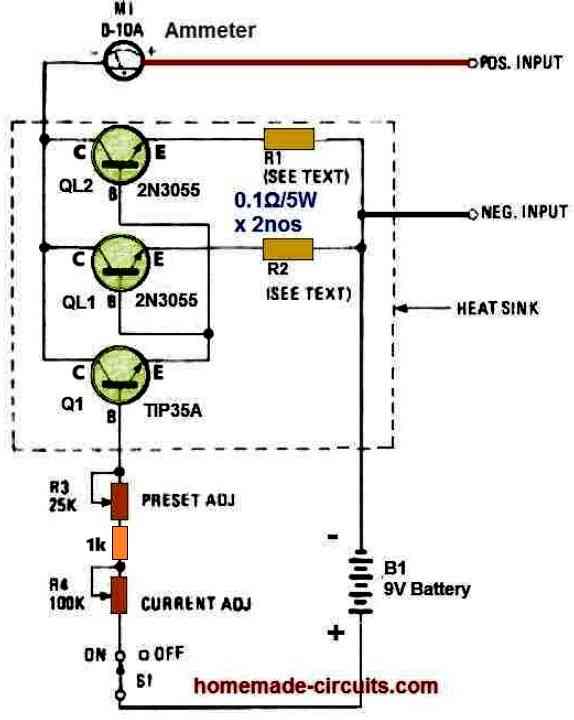
Thus, everything else being identical, while assessing low-voltage supplies, power dissipation is the most important characteristic to consider.
For instance, you may be able to handle 30 volts at 20 amps constantly by connecting four ordinary junkbox 2N5885s in parallel with four 0.1 ohm, 5 watt emitter resistors. 2N5885s have similar characteristics to 2N3055s, although with a power dissipation in the 200-watt range, and with a collector current Ic of about 25 amperes.
Furthermore, high-voltage power supply could also be tested if transistors having high VCE specifications are incorporated.
In either circumstances, the bases of the load transistors (QL1 and QL2) are governed by a predetermined "adjust" current through a battery or DC power. This preset current regulates the current flowing via Q1, that controls the base current of load transistors QL1 and QL2.
PRESET ADJ., potentiometer R3, controls the highest allowable current draw, whereas CURRENT ADJ., potentiometer R4, sets the current range.
Transistor Q1 is a typical TIP35A, an NPN silicon power transistor that may withstand voltages up to 350 and also has a rated collector current of one amp.
In this dummy load circuit, any NPN silicon power transistors featuring a hfe of 50-150 would suffice. 2N5682 is yet another possibility for Q1.
How to Setup
The setting level of the PRESET potentiometer, R3, is defined by the beta of the transistors employed, and the higher-load threshold is decided by the load transistors.
The maximum load is adjusted by potentiometer R3, and the current level is readily adjusted if an optional ammeter or external ammeter is installed. To begin with, tweak the current PRESET potentiometer R3 to maximum and the CURRENT ADJ. potentiometer R4 to the lowest resistance.
Next, measure the current consumed from an appropriate power source hooked up to this active dummy load and adjust the current-preset to achieve the maximum load you intend to implement; and that's all there is to it!
The maximum power dissipation required is determined by the number and kind of load transistors employed.
Therefore, if you drive a lot of voltage at an excessive current for an extended length of time, don't exceed their maximum power dissipation otherwise you might fry your load transistors.
Alternatively , if you allow your load transistor temperature to normalize for a short amount of time, it might perhaps allow you to exceed their continuous power dissipation limit.
Try implementing a moderate duty cycle which does not go beyond their optimal working temperature.
This project does not provide a components list since doing so would undermine the objective of the project, which is to be made from junk box parts. A 9-volt transistor battery was selected since it works like an optimum control power source which is electrically isolated-while lowering expenses to a bare minimum.
Calculations and Formulas
In the circuit the TIP35A transistor (Q1) combined with the two 2N3055 transistors (QL1 and QL2) forms a Darlington configuration which greatly increases the current gain, as the overall current gain of a Darlington pair is approximately the product of the individual current gains of the two transistors.
Darlington Configuration in the Circuit:
TIP35A (Q1) acts as the driver transistor.
2N3055 transistors (QL1 and QL2) serve as the power-handling transistors,, sharing the load current.
Current Gain in Darlington Configuration:
The effective current gain (h_FE(total)) of the Darlington pair can be approximated as:
hFE(total) ≈ hFE(Q1) × hFE(QL1)
Where:
hFE(Q1) is the current gain of the TIP35A (typically it is around 20 at high currents).
hFE(QL1 or QL2) is the current gain of the 2N3055 (typically this is around 20 at high currents).
So the overall current gain becomes:
hFE(total) ≈ 20 × 20 = 400
This means that only a small base current is required to drive the Darlington configuration to handle large load currents.
Base Current Calculation for TIP35A (Q1):
Since the Darlington pair has a very high current gain, the base current required for Q1 is:
IB(Q1) = ILoad / hFE(total)
For a maximum load current of ILoad = 10A:
IB(Q1) = 10A / 400 = 0.025A (25mA)
This is significantly smaller compared to the base current required for individual 2N3055 transistors without the Darlington configuration.
Resistor Calculations:
R3 (base resistor for Q1):
The voltage across R3 remains VR3 = 9V - VBE(Darlington).
In a Darlington configuration the base-emitter voltage is approximately:
VBE(Darlington) = VBE(Q1) + VBE(QL1)
Typically each of the base-emitter junctions has a voltage drop of around 0.7V therefore:
VBE(Darlington) ≈ 0.7V + 0.7V = 1.4V
The voltage across R3 is:
VR3 = 9V - 1.4V = 7.6V
To allow IB(Q1) = 25mA:
R3 = VR3 / IB(Q1) = 7.6V / 0.025A = 304Ω
You can choose a standard resistor value: R3 ≈ 300Ω.
Power Dissipation in the Transistors:
In a Darlington configuration the TIP35A (Q1) specifically handles the small base current for the 2N3055 transistors and thus its power dissipation is much lower.
The 2N3055 transistors share the majority of the load current (5A each for a 10A load).
For each 2N3055:
PQL = VCE × IC
Assuming VCE = 5V and IC = 5A:
PQL = 5 × 5 = 25W
Both the 2N3055 transistors need to dissipate 25W each which means appropriate heat sinks are critical.
Finalized Component Values for Optimal Dummy Load Operation
- R1, R2: 0.1Ω, 5W (to balance current sharing between the 2N3055 transistors).
- R3: 300Ω, 1W (limits the base current for the TIP35A).
- TIP35A (Q1): Acts as the driver in the Darlington pair.
- 2N3055 (QL1, QL2): Handle the main load current, requiring good heat sinks.
- Power Source: A 9V battery powers the base circuit.
- Load Current: Up to 10A, shared equally by the two 2N3055 transistors.
- This ensures that the Darlington configuration works efficiently to drive the high current load using minimal base current.
Dummy Load for Testing Power Amplifiers
The following dummy load circuit can be effectively used for testing large power amplifiers with 8 ohm speaker specifications.
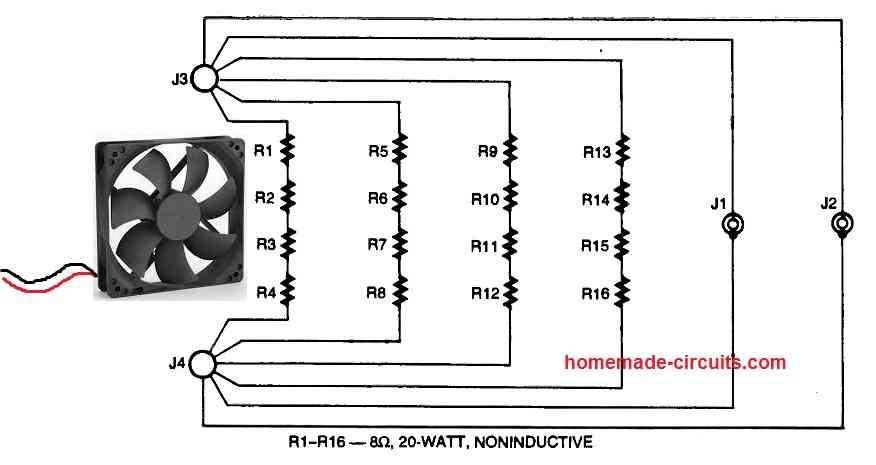
The circuit is quite easy to build, but after building it, and before testing make sure to check the following conditions carefully:
Check the fan, make sure it spins correctly and produces optimal breeze, when switched ON.
Using an OHM meter check across J1, J2, you must see 8 ohms on the meter. Do the same across J3, J4, and the result should be the same, that is 8 ohm reading on the meter.
To test a power amplifier with this dummy load, you must connect the amplifier output across J1, and J2. Preferably, connect the ground side of the amplifier output with J2.
Connect a distortion analyzer meter across J3, J4.
Connect a 1 kHz oscillator frequency to the input of the amplifier.
Switch ON the fan, and then switch ON the amplifier and the 1 kHz oscillator.
After this you can check the amplifier distortion response on the distortion analyzer meter.
Make sure to use a cooling fan which effectively keeps the dummy load resistors cool for at least 5 minutes.
Testing the dummy load over 5 minutes is not recommend, otherwise it may cause damage to the resistors.
Remember to use resistor which are not wire-wound type, because wire-wound resistors can become inductive and produce wrong results on the distortion analyzer meter, and may cause the resistors to over heat.