In this post I have explained the construction of a DC UV germicidal lamp ballast circuit which can be used for driving any standard 20 watt UV lamp through a 12 V DC source.
Although, the proposed ballast design was originally meant for illuminating a regular 20 watt fluorescent tube light, this can be also used for operating a 20 watt UV lamp, for the intended germicidal effects.
The following image shows the main features and image of a compatible 20 watt UV lamp.

Lamp Features
- Short-wave UV radiation having a peak wave-length of 253.7 nm (UVC) effective for disinfection purposes against all types of bacteria and viruses.
- Specially created glass material of the lamp filters out the harmful 185 nm ozone building rays
- Inside protective covering guarantees practically constant UV output throughout the entire life span of the UV lamp.
- A Warning sign printed on the tube signifies that the lamp is designed to generate UVC.
Main Applications
- Deactivation of bacteria, viruses as well as other forms of microbes
- Domestic drinking water purification units.
- For purifying Fish aquarium water units.
- Disinfection of In-duct air treatment equipment.
- As Standalone air purifier systems.
How the Circuit Works
Transformer T1 along with the transistors Q1 and Q2 work like a self-oscillating inverter stage. The operating frequency of the circuit is determined by the core material, the amount of primary winding and the supply voltage.
As described, the inverter is wired to oscillate at around 2kHz frequency when the input supply is provided from a 12.5 V source.
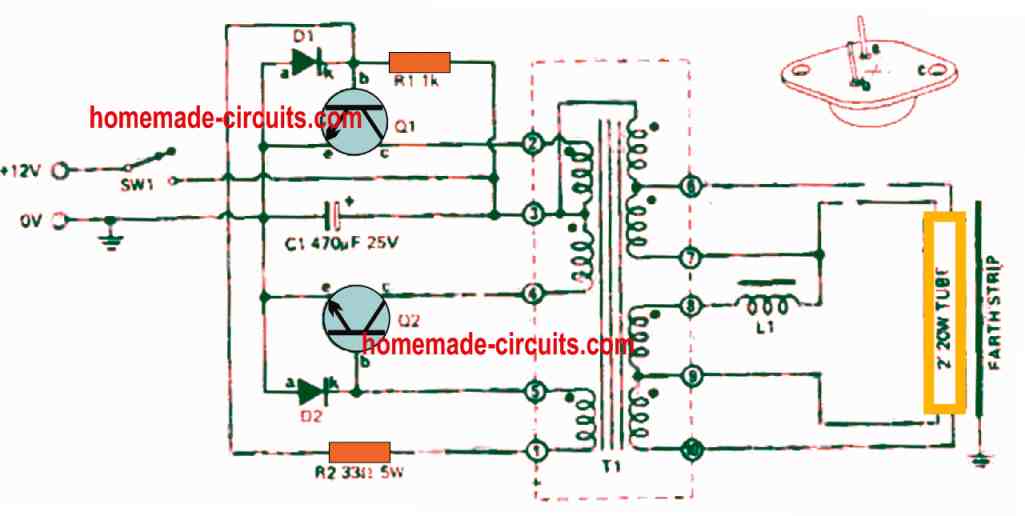
Parts List
Quantity | Component | Description |
---|---|---|
1 | R1 | Resistor 1k, ½ watt, 5% |
1 | R2 | Resistor 33 ohms, 5 watt, 5% |
1 | C1 | Capacitor, 470 µF, 25V, electrolytic |
1 | Q1 | Transistor 2N3055 |
1 | Q2 | Transistor 2N3055 |
1 | D1 | Diode, EM401, 1N4005, or similar |
1 | D2 | Diode, EM401, 1N4005, or similar |
1 | T1 | Transformer, see Table I |
1 | L1 | Choke, see Table II |
The secondary side winding of the transformer includes a couple of 4V windings to preheat the tube filaments, and also a 80 V winding to provide the discharge current supply across the tube and a 240V winding to generate a initial static voltage for starting the tube conduction.
Choke L1 can be seen connected in series with the 80 V winding of the transformer, in order to control the current through the tube.
Besides providing the current limit for the tube, the choke L1 also provides stabilization of the tube current for the supply voltage fluctuations.
When the input supply voltage rises, the inverter frequency also increases proportionately forcing the choke impedance to rise and vice-versa.
This automatically adjusting L1 impedance helps to keep lamp current steady in response to the variations in supply voltage between 10 V and 15 volts.
Construction Hints
The circuit schematic of the full UV lamp driver ballast circuit can be witnessed above. The winding info of transformer T1 and choke L1 are presented in Tables 1 and 2.
The winding for the transformer T1 is implemented over a 12mm x 12mm former or bobbin. The precise winding is easy to understand, yet somewhat laborious. The entire winding has to be done very uniformly; or else the whole winding may not accommodate well over the former.
Both the primary windings must be wound in a bifilar manner as explained in the following image.
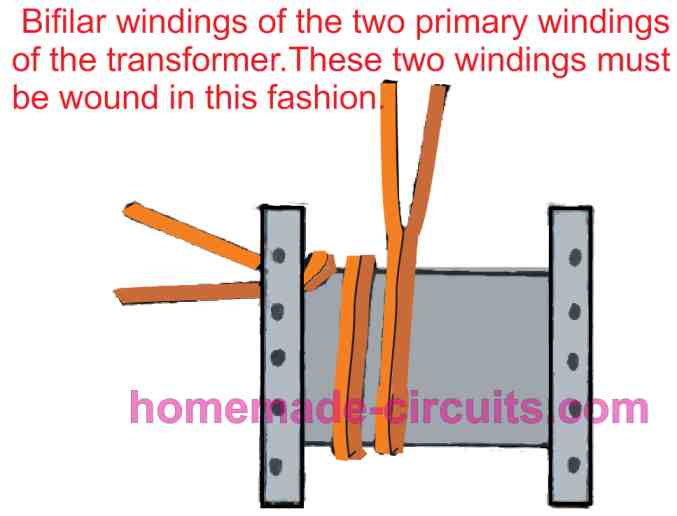
This means that you must hold the wires for both the winding together and then begin winding the primary 1 and primary 2 simultaneously to make sure they are laid together in a combined way. This also implies that both these winding are laid down in perfectly adjacent with each other all through the length of the winding.
The other windings for T1 can be implemented in the regular fashion, but you must make sure that each of these winding is wound in the identical direction and also their start points and finish points are soldered to the appropriate terminals, as suggested in Table 1 below.
Table#1
Winding | Start | Finish | Turns | Diameter | Notes |
---|---|---|---|---|---|
Primary 1 | Pin 2 | Pin 3 | 28 | 0.8 mm | Bifilar wound |
Primary 2 | Pin 3 | Pin 4 | 28 | 0.8 mm | Bifilar wound |
Feedback | Pin 5 | Pin 1 | 20 | 0.4 mm | 0.005" insulation |
Secondary | Pin 8 | Pin 9 | 200 | 0.4 mm | |
Filament 1 | Pin 9 | Pin 10 | 10 | 0.4 mm | |
Filament 2 | Pin 6 | Pin 7 | 10 | 0.4 mm | 0.005" insulation |
Starting Winding | Pin 3 | Pin 6 | 600 | 0.125 mm | 0.005" insulation |
After finishing the winding process, you may insert the pair of 'E' cores into the bobbin slots, and secure the whole construction firmly together using sticky tape or an appropriate metal clamp being careful that the metal clamp doesn't cause a short circuiting across any of the turn.
How to Wind the Choke
The choke L1 winding specifics are listed in Table#2 below:
Table#2
- Core: As shown in the following image or any similar contemporary pot core:
- Coil former: as shown in the image (in yellow):
- Note: cores should be clamped with each other through 3/16" brass bolt and nut- a 3/16" brass washer can be accustomed to create an air gap.
- Winding: 250 turns of 0.4 mm thick wire.
After the above steps, the winding are clamped between a pair of Mullard FX2242 cores as shown in the table#2 images. It is important to introduce a thin brass washer is interposed between the two cores, in order to create an air gap.
Wiring Layout
Wiring details of the parts and other aspects of the UV ballast circuit are demonstrated in the following figure. However, this exact component layout is actually not critical.
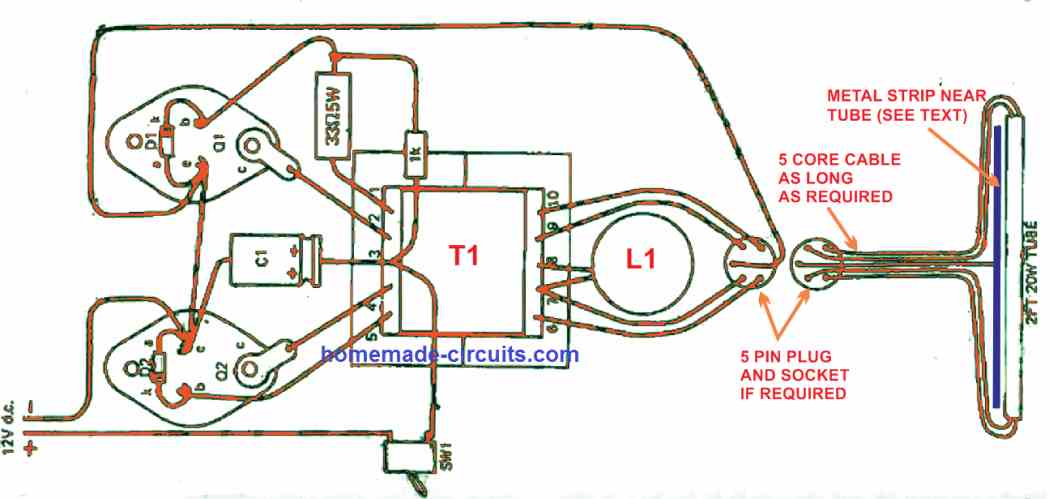
The transistors Q1 and 02 needs to be installed over an appropriate heatsink, which must have a minimum dimension of around 4" by 6".
Insulation washers should be applied to keep both the transistors well isolated from the heat sink. All the parts now can be casually hooked up and the full system attached to a 12V source.
Be careful not to touch the transistors or the transformer output side terminals because all these elements will be at fairly large voltage which could give you a painful electrical shock.
Current Adjustment
With the UV tubeligt switched ON, measure the current consumed by the circuit through the 12V supply. You should find this to be around 2.5 amps ± 0.2 amp.
In case you see this beyond this spec, you can try varying the air gap air of the choke until the issue is fixed to the specified limit. You will find that extending the the gap causes an increase in the current consumption and vice-versa.
Once the working and setting up are confirmed and tested, remove the transformer and immerse it into varnish in order to coat it with a layer of insulation, and let the varnish solidify across the winding and core. Once the transformer is entirely dried up, reconnect all the components for finalizing the UV lamp driver ballast circuit.
Since this UV lamp driver functions with 2 kHz you may hear slight noise around this frequency through the transformer and choke. This can be minimized by enclosing the key components inside heavy rigid box, or by covering the transformer and choke with epoxy resin coat.
220 V UV Lamp Driver Circuit Diagram
The design represents a 220 V operated simple UV lamp driver circuit, which can be effectively used to illuminate a UV lamp with minimum components.
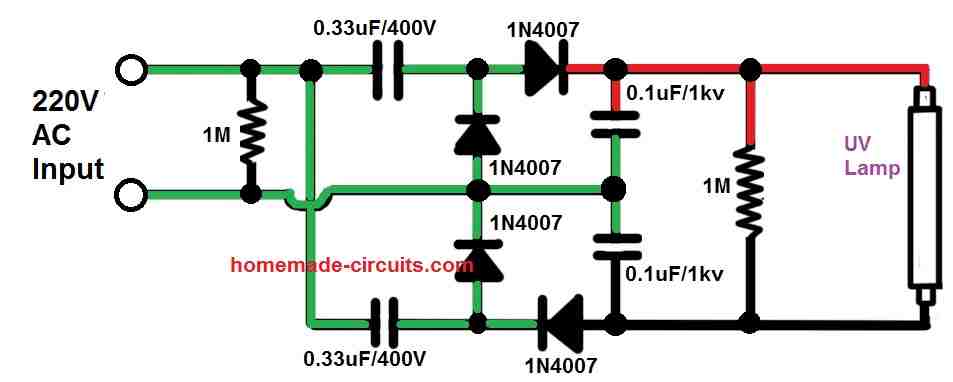
The circuit is basically a voltage doubler circuit. The horizontal 1N4007 diodes along with 0.33uF capacitors cause the input 220 V to become double at the output, across the UV lamp.
The peak voltage of 220 V RMS input is = 220 x 1.41 = 310 V.
After the voltage is doubled this 310 V turns into a massive 620 V peak to peak which is enough for driving any standard UV lamp brightly.
Warning: The circuit ideas were contributed by one of the dedicated members of this blog, the circuits are not practically verified by the author.