A fast battery charger circuit charges a battery with enhanced speed so that it is charged in less time than the specified period. This is usually done through a step wise current optimization or control.
While looking for a fast charger circuit that would charge a battery quickly, I came across a couple of designs which were not only useless but misleading too. It seemed that the concerned authors had no idea what a fast charger actually needs to be like.
Objective
The main objective here is to accomplish rapid charging in lead acid batteries without causing any harm to its cells.
Normally, at 25 degrees Celsius atmospheric temperatures , a lead acid battery is supposed to be charged at C/10 rate which would take at least 12 to 14 hours for the battery to get fully charged. Here C = Ah value of the battery
The objective of the concept presented here is to make this process 50% quicker and enable the charging to finish within 8 hours.
Please note that an LM338 based circuit cannot be used to boost the charging rate of a battery, while it is a great voltage regulator IC, enhancing the charging rate requires a special step wise changeover in current which cannot be done using an LM338 IC alone.
The Circuit Concept
When we talk about how to charge a battery quickly we obviously are interested to implement the same with lead acid batteries, since these are the ones which are used extensively for almost all general applications.
The bottom line with lead acid batteries is that these cannot be forced to charge rapidly unless the charger design incorporates an "intelligent" automatic circuitry.
With a Li-ion battery obviously this becomes quite easy by applying the full dose of the specified high current to it and then cutting off as soon as it reaches the full charge level.
However, the above operations could mean fatal if done to a lead acid battery since LA batteries are not designed to accept charge at high current levels continuously.
Therefore in order to pressure current at a rapid pace these batteries need to be charged at a stepped level, wherein the discharged battery is initially applied with a high C1 rate, gradually reduced to C/10 and finally a trickle charge level as the battery approaches a full charge across its terminals. The course could include a minimum of 3 to 4 steps for ensuring maximum "comfort" and safety to battery life.
How this 4 Step Battery Charger Works
For implementing a 4 step fast charger circuit, here we employ the versatile LM324 for sensing the different voltage levels.
The 4 steps include:
1) High Current Bulk Charging
2) Moderate Current Bulk Charging
3) Absorption Charging
4) Float Charging
The following diagram shows how the IC LM324 may be wired up as a 4 step battery voltage monitor and cut off circuit.
Circuit Diagram
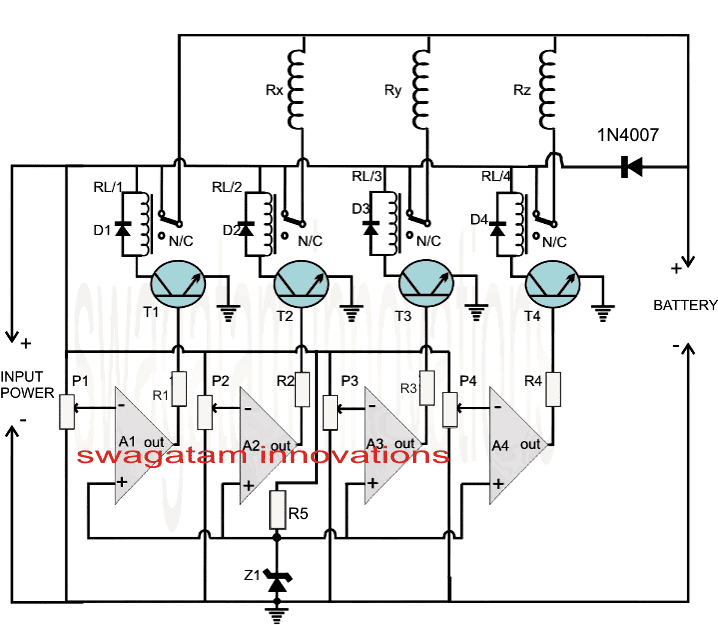
NOTE: Battery must be connected first before switching ON the input, to ensure that the circuit works correctly.
The IC LM324 is quad opamp IC whose all the four opamps are used for the intended sequential switching of the output current levels.
The proceedings are very easy to understand. opamps A1 to A2 are optimized for switching at different voltage levels during the course of the stepped charging of the connected battery.
All the non-inverting inputs of the opamps are referenced to ground through the zener voltage.
The inverting inputs are tied with the positive supply of the circuit via the corresponding presets.
If we assume the battery to be a 12V battery having a discharge level of 11V, P1 may be set such that the relay just disconnects when the battery voltage reaches 12V, P2 may be adjusted to release the relay at 12.5V, P3 may be done for te same at 13.5V and finally P4 could be set for responding at the battery full charge level of 14.3V.
Rx, Ry, Rz have same values and are optimized to provide the battery with the required amount of current during the various charging voltage levels.
The value could be fixed such that each inductor allows a current passage rate that may be 1/10th of the battery AH.
It may be determined by using ohms law:
R = I/V
The values of Rx, alone or Rx, Ry together could be dimensioned a little differently for allowing relatively more current to the battery during the initial stages as per individual preferences, and is tweakable.
How the circuit responds when switched ON
After connecting the discharged battery across the shown terminals when power is switched ON:
All the opamps inverting inputs experience a correspondingly lower voltage levels than the reference level of the zener voltage.
This prompts all the outputs of the opamps to become high and activates the relays RL/1 to RL/4.
In the above situation the full supply voltage from the input is bypassed to the battery via the N/O contacts of RL1.
The discharged battery now starts charging at a relatively extreme high current rate and rapidly charges upto a level above the discharged level until the set voltage at P1 exceeds the zener reference.
The above forces A1 to switch OFF T1/RL1.
The battery is now inhibited from getting the full supply current but keeps charging with the parallel resistances created by Rx, Ry, Rz via the corresponding relay contacts.
This makes sure that the battery is charged at the next higher current level determined by the the three parallel inductor net value (resistances).
As the battery charges further, A2 shuts down at the next predetermined voltage level, switching OFF Rx and rendering Ry, Rz only with the intended charging current to the battery. This makes sure that the amp level is correspondingly reduced for the battery.
Following the procedures as the battery charges to the next calculated higher level, A3 switches OFF allowing only Rz to maintain the required optimal current level for the battery, until it gets fully charged.
When this happens, A4 finally switches OFF making sure that the battery is now gets completely switched off after attaining the required full charge at the specified fast rate.
The above method of 4 step battery charging ensures a rapid charging without harming the battery internal configuration and makes sure the charge reaches at least at 95%.
Rx, Ty, Rz may be replaced with equivalent wire wound resistors, however it would mean some heat dissipation from them compared the inductor counterparts.
Normally a lead acid battery would need to be charged for about 10 to 14 hours for allowing at least 90% of charge accumulation. With the above rapid battery charger circuit the same could be done within 5 hours of time, that's 50% quicker.
Parts List
R1---R5 = 10k
P1---P4 = 10k presets
T1---T4 = BC547
RL/1---RL/4 = SPDT 12V relays 10amp contact rating
D1---D4 = 1N4007
Z1 = 6V, 1/2 watt zener diode
A1---A4 = LM324 IC
PCB design
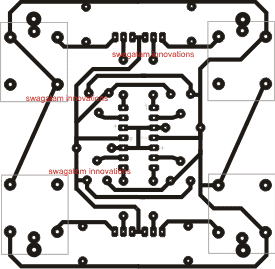
This the original size PCB layout, from the track side, the high watt resistors are not included in the PCB design.
Simplest Single Op amp Fast Charger Design
The following diagram shows how a single op amp can be used to create a decent fast charger circuit for a 12V battery.
A discharged battery will be initially charged at a high current rate using the 13V supply, through the N/C contact of the relay. This will allow the battery to be charged quickly at the 13V mark within a few hours.
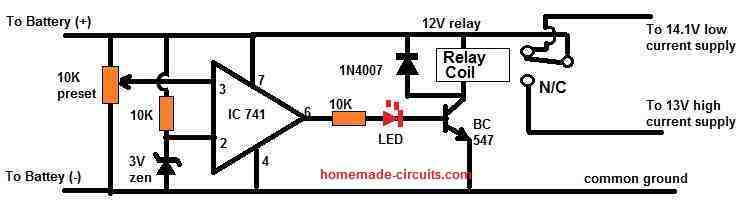
When the battery is charged up to 13V, the relay will changeover to the 14.1 V supply and the battery will start charging through the 14.1 V low current charging supply, until it is fully charged.
How to Set
- Initially keep the 10k preset wiper to the ground level.
- Connect a 13V fixed DC supply with the pin7 and pin4 supply lines of the IC.
- Next, adjust the preset until the relay just clicks ON from N/C to N/O, and the red LED turns ON.
- That's all, this single op amp fast charger circuit is all set now.
Simplest 2-Step Fast Battery Charger Circuit
In this section I will discuss a very simple yet effective battery charger circuit, which will charge your battery at a relatively faster rate than the normal charging methods.
This battery charger circuit can be used for fast charging of all types batteries, however make sure to adjust the current and the voltage of the charger according to the specifications of your battery.
That said, this fast charger circuit employs a step-charging process and therefore is specifically suitable for lead acid batteries and SMF batteries, since these batteries strictly require a step-charging method for implementing the fast charging effect. Li-ion batteries have no such restrictions, and can be quickly charged directly through a relatively high current input, and therefore do not strictly depend on step charging.
Now, let's understand how the circuit is designed to work.
How the Circuit Works
If you do not want to read the explanation below, you can simply watch this video instead:
Referring to the circuit diagram below, we can see that is basically a two step battery charger circuit, which will allow an initial high current charging for a lead acid battery, until the battery voltage has reached around 75% of its full charge level, wherein the circuit will switch the current to a lower level and continue the charging process until the battery attains the full charge level.

Here, the circuit is configured for fast charging of a 12 volt lead acid battery.
The NPN transistors works like a voltage sensor.
The Zener diode at the base decides at what voltage threshold the transistor needs to switch ON.
Here, the Zener diode is fixed at a 13.5 volt level, which means that the transistor will turn ON when the battery has charged up to the 13.5 volt level.
When the transistor turns ON, the connected relay also turns ON, causing its contacts to shift from its initial N-C contact to its N-O contact.
Initially, while the voltage level of the battery is below the 13.5 volt changeover threshold, the battery is allowed to charge with a relatively high current through the N-C contacts of the relay.
With this initial high current, the battery starts charging at a faster rate and quickly reaches the 13.5 volt level, wherein the transistor switches ON and causes the relay to changeover from its N-C contact to its N-O contacts.
The N-O contacts of the relay can be seen configured with a current limiter stage which consists of a high watt resistor, whose value determines the amount of current that needs to be reduced for the last phase of the charging process.
The battery now continues to charge but with a reduced current until finally it reaches its full charge level.
Please note that here the full charge level for the 12 volt lead acid battery must be restricted to a maximum of 14 volt which is around 0.3 volt lower than its actual maximum full charge level of 14.3 volts.
This reduced full charge level of 14 volt is intentionally chosen to ensure that the battery never reaches its highest 14.3 volt level, which in turn allows the battery to be connected with the reduced supply current indefinitely, without the need of an automatic cut off mechanism.
For a 12 volt lead acid battery, the initial high current charging may be done by using a maximum current which could be around 30% of its A-h rating.
For the current limiting, the above current may be reduced to around 7% of the battery A-h rating.
Calculating the Current Limiting Resistor Rx
The current limiting resistor must be calculated accordingly, using Ohm's law, as shown below:
Rx = V/I = (14 - 13.5)/Ah * 10%
Remember, the initial charging current which is selected here as 30% of the battery A-h must be thoroughly examined. If you find your battery warming up significantly with a 30% initial charging rate, you must reduce this level until the warming of the battery reduces to an acceptable level.
If you have any further questions regarding the above design please feel free to comment below with your queries.