In this post I have explained a high current sensorless BLDC motor controller circuit which does not depend on hall effect sensors for initiating the operations rather utilizes the back EMF from the motor for the sequential input
Overview
For proper commutation most 3-phase BLDC driver circuits rely either on a sensor based feedback or from an external 3-phase sync signal, contrary to this our present sensorless high power BLDC motor controller circuit does not depend on sensors or any external signals for operating the motor.
Instead, the circuit very simply processes the back EMFs from the motor winding to produce the required powerful synchronized rotational effect on the motor.
Coming back to our present concept, the circuit employs the IC ML4425 from Fairchild, and enables us to operate any type of BLDC motor regardless of whether the motor has sensors or not.
Most BLDC motor today have built-in Hall effect sensors which provide the necessary feedback to the controller circuit regarding the instantaneous position of the magnetic rotor with respect to the stator winding and informs the controller when the relevant power devices needs to be triggered with the precise sequence, this in turn allows the motor to rotate with perfect synchronization and maximum efficiency.
Working without Sensors
Some BLDC motors may be without sensors, and for such motors the BLDC controller is forced to employ an external 3 phase generator circuit for the required synchronized rotation of the motor.
However the present 3 phase sensorless BLDC controller eliminates all these hassles, and neither depends on sensors nor any form of external triggering, instead the system extracts the back EMF pulses from the stator coil of the BLDC motor for executing the rotational momentum on the connected motor.
This feature allows the controller to be universally used for all types of BLDC motors without going through the complications of the sensor connections or the external 3 phase generator stages.
Moreover since the full bridge circuit power devices are externally configured allows the system to be used with even high power BLDC motors without any restrictions whatsoever. One can simply change the rating of the power devices as per requirement and achieve the intended high current BLDC operation as per preference.
The following diagram shows the complete design layout of the proposed sensorless BLDC controller using back EMF as the triggering source.
Circuit Description
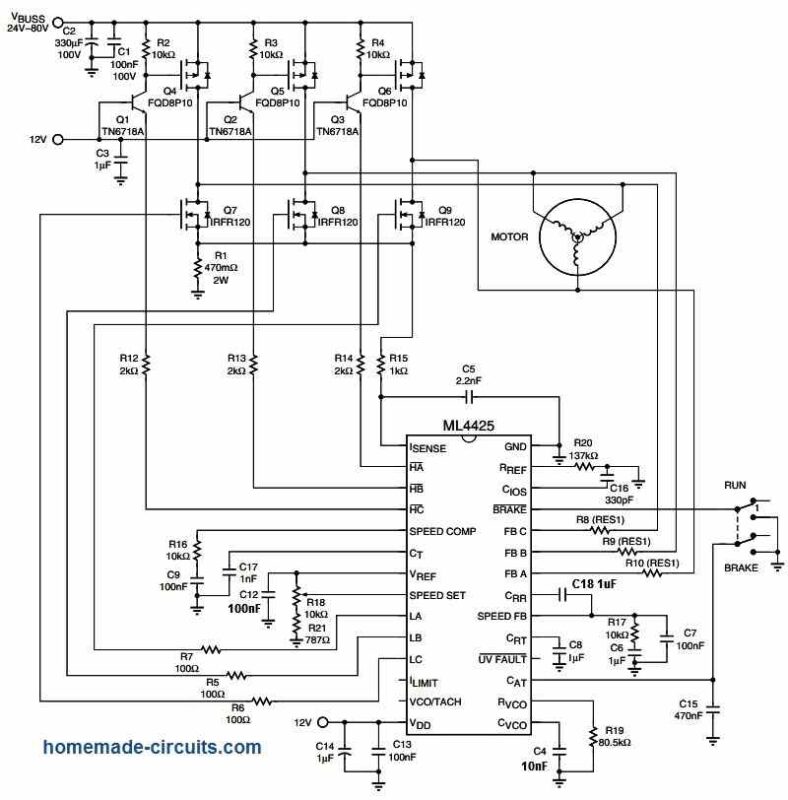
Courtesy: Mouser.com
The system looks pretty straightforward, you just have to solder the shown components in place and quickly start the BLDC operations. It is as simple as switching ON power and seeing the BLDC motor rotate with full efficiency.
The controls are also very easy to understand and implement, the RUN/BRAKE switch enables the motor to continue running as long as the switch is in the OFF position, or not grounded, while the motor is instantly stopped as soon as the switch is toggled at the ground level.
The POT R18 allows the user to control the speed of the motor linearly, simply by moving the pot knob across the specified range.
Main Advantage
The biggest advantage of this 3-phase sensorless BLDC controller is that it does not require the messy sensor based feedbacks from the motor, neither depends on a 3-phase sync signal from the an external source. As can be witnessed in the above diagram, the feedback is achieved from the motor's main 3 phase operating wires via R8/R9/R10 into the designated pinouts of the IC.
This allows the controller to be used with all types of BLdC motors whether or not a sensor is available. If sensors are available from a BLDC, those can be ignored and the motor may be configured without the sensor wires, as indicated in the above diagram.