Triacs are one of the most important active electronic components which are exclusively used for power switching applications, these devices are especially suited to AC mains loads, and are able to switch large currents consistently.
Triacs are the solid state replacements to mechanical relays, and come configured as static relays.
The modern triacs today are highly sophisticated with their specifications and make, one such example is the BTA41, 600B, I have explained its technical specification and datasheet from the following points:
Identifying Print Value of BTA41/600B
- BT indicates series number,
- "A" represents that the device is insulated, while B would mean non-insulated. The insulation is provided on the Tab of the device upto 2500 volts.
- 41 = 4 and "one" zero, that equals 40 Amps
- 600 is the voltage handling capacity, therefore here it's 600 volts.
- B represents the triggering sensitivity that's 50mA in this case
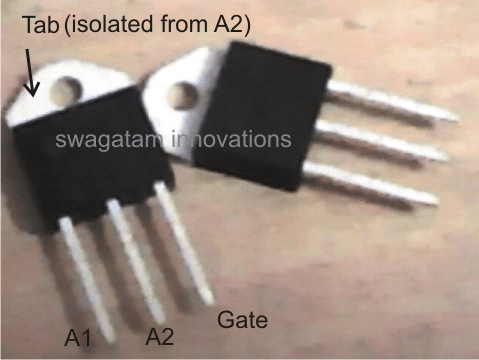
- Absolute Maximum Rating (at around 25 to 40 degrees Celsius)
- RMS, continuous current handling capacity = 40 Amps
- Non repetitive peak current = 400 Amp, only for max 20ms.
How to Connect
The pinouts are connected just as we connect other normal triacs. I have explained them yet again:
A1 should be always connected to ground. The ground doesn't have to be necessarily the neutral of the AC, it can be any one wire out of the two mains input.
The other wire will go to one of the load terminals, while the second wire of the load will go to A2 of the triac.
The gate should be connected with the desired trigger input which must be a DC, because the triac will conduct with every rising positive edge of the DC trigger.
Here the minimum triggering gate current is 50 mA.
A1 should be made common with one of the AC terminals as well as the ground of the DC trigger circuit, in case an external triggering circuit is incorporated.
Application Notes
As suggested in the above sections, the triac BTA41/600B is best suitable for applications concerning control of AC loads such heater coils, high power halogen lamps, AC motor pumps or simply motors such as in dryers, blowers and so forth.
The following circuit illustrates how the device may be utilized for controlling heater coils such as in furnaces, induction cookers etc.
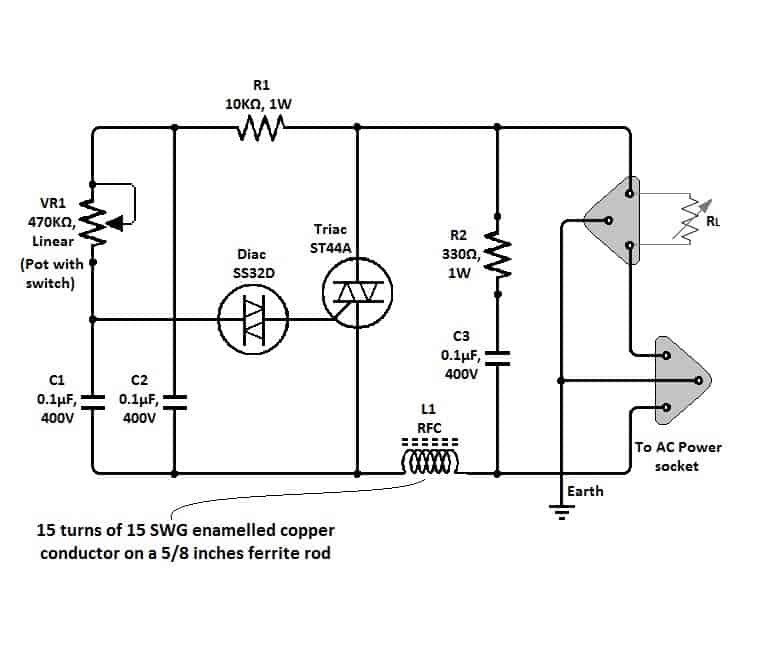
The above circuit can also be used for controlling AC motor speeds simply by replacing the heater coil with the motor wires.
The adjoining diagram depicts another application of BTA41/600 where it has been configured as a PWM assisted AC motor controller or even heater coils.
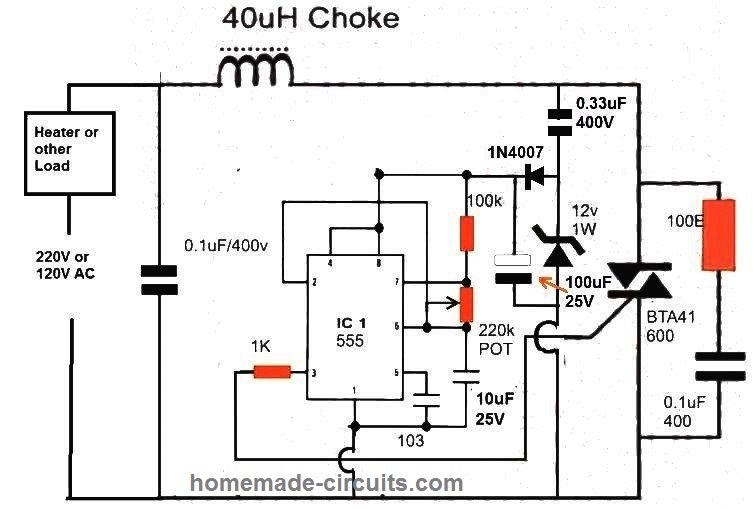
WARNING: The above circuits are not isolated from mains AC, and therefore are extremely dangerous to touch in open and powered condition.
Hello sir. Can I make without inductor. I mean only triac, diac, capacitor, resistor. Potentiometer.
Hi Sakib,
yes you can skip the 40uH coil and the left side 0.1uF capacitor, and still get the intended results, however without the LC network, the circuit will generate a lot of RF noise and interference on nearby AM radios.
Hi Swagatam,
I would like to use the second with 555 timer for making a soft starter for my submersible pump (1.5 – 2 Kw) for a community farm. Is it possible. What I do want is using a MCB to switch on then the load will be fully started after 1-5 seconds longer or more to reach full speed or power.
Changing the value of the potentiometer will make the ramping up time longer? Also the Choke, do I have to use this choke?
Please advise
Best.
Hi Dang,
Yes that’s possible. But the controlling will need to be done manually.
Meaning, initially you will have to adjust the pot at narrow PWM level and then once the load is switch ON, you can increase the PWM to maximum.
However, if you want to have this soft start fully automated then you just have to connect a 100uF capacitor between pin#5 of the 555 IC and the ground.
Hi Swagatam,
Thanks for your response. My scenario is:
MCU control the MCB with an internal small relay (to supply AC power to the coil of the MCB for it to start)One the MCB starts, the board will automatic handle the soft starting for the pump in xx seconds.So with your advise, adding a capacitor to pin 5 of the 555 to GND, it will automate the soft starting in xx seconds using the set level in the POT? In your schematic, there is already a 103 Capacitor connecting ground. From your schematic, i understood that Live and Neutral are non interchangeable! Can you advise a value for the POT to make the 10 seconds ramping up to full power?
Many thanks for your advise
Best,
Hi Dang,
Here are answers to your questions.
You can replace the 103 capacitor at pin#5 with a 100uF or a 220uF as per the desired length of the slow start.
In this situation the pot can be used to set the maximum range of the pump speed. According to me the pot must be removed and replaced with a fixed resistor so that a maximum speed can be set using the two resistors.
The ramping length can be directly set through the capacitor at pin#5.
Make sure to test the results using an oscilloscope first.
Preferably, the phase or the LIVE should be connected to the LOAD side terminal, but this is not mandatory.
Even if you reverse the L/N connections the circuit will still keep functioning normally.
Hi – I would like to use the PWM assisted AC motor controller circuit to replace the triac driver in a large carpenters plane. The present triac driver circuit is not working. What frequency range and pulse width should I consider configuring the 555 for? The 10uf cap appears to be too large for a motor driver application, as the frequency is in the 1Hz range. What should the gate drive signal look like relative to the 60 Hz line frequency? Thanks in advance for your insight.
Hi, you can try reducing the capacitor value to 0.47uF and see how it responds.
The 60 HZ would be allowed for a few milliseconds by the PWM ON cycles and then interrupted by the PWM OFF cycles.
I would also suggest you to try the first circuit which is ideally suited for controlling AC motor speeds.
Hi Swagatam
I would like to make my own version of a solar proportional immersion heater controller to use surplus electricity from my solar PV array. I assume that an appropriate circuit will use this triac which will be triggered by a current transformer on the supply to the property to provide enough load to bring down the export of electricity to zero – tested during each cycle.
I would love to make a trial version but don’t have a circuit diagram – can i use this circuit and how do i integrate the current transformer?
Thanks
Gordon Webb
Hi Gordon,
I have current transformer circuit in this blog which can be perhaps modified to suit your application.
You can try the second schematic with a buzzer. If it works with a buzzer then a triac could be used at the output to switch ON a desired load.
https://www.homemade-circuits.com/load-current-control-through-current-sensing-transformer/
Hello, I have made this circuit with 555 pwm and trying to run infrared cooker coil with triac BTA41600B. But i am getting huge ac voltage on gate and gave 1k resistance to 555 pin3 to gate and resistance just burnt.none of triac pin is sorted.Is it okey to gate high voltage in gate?three of my 555 ic is already damaged.
Hi, How is it possible to get a huge voltage at the triac gate when the 12V zener is connected?
Did you connect the 0.33uF capacitor and the 12V zener diode?
You can try using 0.22uF instead of 0.33uF and check the results.
The voltage between pin8 and pin1 of the IC should be 12V, and the same should appear across the gate and the ground of the triac.
would you have a economical power supply circuit for a diy wire edm machine
Please provide more details for the power supply.
Hello Sir, I needed a Speed Controller for Industrial DC Motors.
Is it possible to use Your above circuit with combination of a MB3510 bridge rectifier for the
DC Motor? and also what modifications i can do to above circuits for using 2 phases as input of 440V AC to feed the bridge rectifier MB3510 and later the DC output to the motor?
I have posted the more detailed message on facebook with both the motor plates, Please Kindly Check, Waiting for Your Positive Reply
Thanks 🙂
Hello AK, for operating a DC motor you can try the following circuit:
" rel="ugc">
More details are provided in the following article:
https://www.homemade-circuits.com/dc-motor-speed-controller-circuits/
Thank You very much for replying Sir, but Sir one of my DC Motor eats Four Hundred & Fourty DC Volts @ Ten point One Amperes of Current, and the another small one eats Two Hindred & Thirty DC Volts @ 8.1Amperes, how can such small circuit going to handle that much high load? and also can i by doing som adjustment i can control the speed while maintaning the torque with a external 0-10Volts DC supply?
)
I messaged on Facebook with much details earlier where You suggested me this circuit.
(" rel="ugc">
Waiting for Your Positive Reply . . . .
Thanks
Hello AK, I actually suggested you the following circuit:
" rel="ugc">
You can see that the power transistors have a separate voltage connection for feeding the motor. You can feed the 440 V to the transistors separately for controlling the motor. For this you just have to replace the transistors with appropriately rated MOSFETs.
For further discussions please comment under the following article:
https://www.homemade-circuits.com/dc-motor-speed-controller-circuits/
Good!
Thanks for good job. Can the power booster you made with this triac be used for electronic appliances, such as ac television and radio, also?
Thank you, no, the booster circuit cannot be used for powering electronic devices.
Please, can you help me, then, with a power booster circuit that can power AC electronics. I will be very grateful if you do.
Thank you very much sir.
The only way to achieve this is to build an auto-transformer or buy one auto-transformer which will allow you to adjust the output voltage to the desired levels. By the way, power cannot be boosted…only voltage can be boosted.
Hello, I am looking for a circuit to control 120 A/C volts max 10 amps motor speed aiming to keep as much torque es possible.
The AC motor is to power a spindle of a home made flight cutter for metals such as on a milling machine.
Will that circuit above do?
I
Hi, yes, you can use the above circuits for controlling the specified load. However, decreasing the speed might also cause the torque to reduce proportionately.
Hi Swag, I am repairing this Samson SX3200 amp. It has two bridge rectifiers in each channel circuit. What is bothering me is the function of the negative and positive step driver circuits. Any idea? My email address is cgachuhi@yahoo.com.
Hi Gash, The two rectifiers could be for supplying the +/- dual voltages to the amplifier circuit, because most power amplifiers require a dual voltage to operate. This is my guess, not entirely sure though.
Sir,
My name is Dr.Chris Halgryn and I am a great fan of all your circuits however Sir, the circuit I want to build now looks good it is the speed controller using a BTA41 connected in series with a 0.1uF cap…. but, at the end of the schematic it shows a device marked “100E” what is this please????
Thank you
Chris
Thank you Dr. Chris,
I am glad to help you!
100E = 100 Ohms
the letter E stands for Ohms.
Thank you Sir my goodness I at first thought it was OHMS yet I feel such a fool but Thank you again for the prompt reply I keep on following your projects, built a few all in the past….. and YES!!! They all work fine thus, everybody should be thankful for ypour projects and schematics thank you again I HIGHLY Recommend you!!!!
Thank you
Dr.Chris
PS. I need a circuit in order to control the speed of my UNIVERSAL MOTOR without LOOSING TORQUE can you assist or will the present circuit help me… please thank you in advance~~
No problem Dr. Chris, I am always happy to help! I am also glad to know that you have tried my circuits and they worked for you, appreciate your kind response!
I have a high torque motor speed controller circuit published in this blog, but the circuit can control only low current motors up to 3 amps:
https://www.homemade-circuits.com/constant-torque-dc-motor-speed-controller-circuit/
Hi….I want to make a 3-phase voltage regulator to control the voltage input of a transformer’s primary winding, so that the output voltage of the secondary winding can be adjusted. The current requirements for the primary is max 20 A per phase. Can you help me with a suitable schematic ? I am planning to make use of 3 nos. of standard single phase SCR (BTA41 600B) voltage regulators connected in a star configuration (220V INPUT) and will take the outputs of these in a delta configuration (400V OUTPUT) to the transformer’s primary. Any suggestions will be a nice gesture…. thanks
Hi, sorry. I can’t figure out how a 3 phase AC regulator can be built. It seems difficult because there’s no neutral in a 3 phase system. If there was a neutral we could have simply used 3 AC light dimmers on each phase for controlling each of the phases.
Hi Swagatam….Of course there is a neutral in the three phase system, and that’s why in the absence of a single unit of 3-phase transformer, we can connect 3 units of single phase transformers for 3 phase use. The method is known as STAR-CONNECTION. The output can be made available as a no-neutral setup (called as a DELTA CONNECTION) or otherwise.
I actually wanted a good high power (standard single phase) dimmer circuit design with symmetrical wave-forms at the gate. And I will actually use three of them for the three phases, take each one’s phase output and use them as I wish, meaning STAR (with neutral) or DELTA (without neutral).
Thank you Aditya, for the information!
After some thinking I realized that for connecting a light dimmer on each phase a neural connection may not be required since light dimmers are designed to work in series with the load. So I think you can use 3 good quality high power light dimmers and fix them in series with a DELTA 3 phase wiring.
I have a light dimmer related article which you can find in the following link. The circuit shown under “Circuit Diagram of an Improved Light Dimmer” is a good circuit which was originally designed by the elektor-electronics engineers. However, to get a symmetrical control from the 3 dimmers you may have to use a ganged potentiometer for the 3 dimmers.
https://www.homemade-circuits.com/how-to-make-simplest-triac-flasher/
Hi, I’m intending to use a BTA 41-600B pot controlled regulator circuit (common on ebay etc advertised as a 220v 4000w regulator) to power an old valve radio main circuit (separate 6.3v tube heater supply) in place of a failed transformer. I will be connecting the output of the regulator to a silicon bridge rectifier which then feeds the radios circuits. As the regulator needs to be load connected to make it regulate will the rectifier alone be enough to trigger regulation. Otherwise I was going to build a small filament lamp into the case to fire up the regulator when switching the radio on. Not to sure what current draw will be needed to make the regulator start regulating.
Thanks in advance.
Hi, using a triac dimmer with mains AC can be risky for any low voltage project, therefore I would recommend you to go for a transformer and not with a triac based power supply.
What is the best testing method for a Triac p/n BTA41600B, outside of the circuit.
Thank you
Hi, the inductance should 40 uH. The 15 turns is probably incorrect, it must be around 50 turns
The core should be a ferrite core, If you use air core then the number of turns will increase significantly.
a 2mm diameter wire should be quite enough for handling 25 amp current.
Thanks for replying, can
the ferrite core (due to poor repelability) be smaller than 5/8 of an inch?
If so, would there be problems using this coil for 25A?
Thank you
You are welcome, It may be difficult to provide the exact size of the ferrite core. You may have to find it with some trial and error to figure which core and number of turns produce minimum RF disturbance on radio
Hello sir swagatam, thanks for your electronic guidiance.I’m nosa,I have a question,is it possible to use 3kva alternator generator ac output using BTA41/600b and to power 3hp ac electric motor or higher electric motor and can it runs the ac motor continuously without damages to the BTA41/600b circuits or what kind of circuit will you recommend sir.
Hello Nosa,
since the triac is rated to handle 40 amp continuous current, it should be able to handle the 3 hp load easily. So you can try it. Just make sure to mount the triac over a large heatsink
Thanks sir,I sent you an email of the picture of such design generator I want to use the triac circuit on.
I guess dis is your email address: hitman2008@live.in.
Here is my email address: nosaglee@yahoo.com. to send me usefull information sir.
You are welcome Nosa, however, I prefer discussing only through comments so that it can be read by all of us.
Yes you can use a BTA41 triac since it is rated to handle 40 amp current, meaning 220 x 40 = 8800 watts provided i mounted on a large heatsink
OK sir,from the above diagram of bta41/600b triac,so which side to connect the triggering DC to triac diagram or how can I connect the DC 5v or 12v triggering to the same circuit with the AC bta41/600b.please sir indicate to me the place in the diagram.
Nosa, you can refer to the first diagram from the following article, which suggests exactly how a triac needs to be configured with a DC switching circuit and an AC load:
https://www.homemade-circuits.com/simple-triac-triggering-circuits-explained/
Hi Swagatam,
" alt="BT136 power supply" />
I like to replace the BT136 by BTA41 due to fail, cause of overload. Here BT136 triggered by a resistor, not a diac, does BTA41 work on this circuit?
Thanks.
Hi Awak, if your bT136 is working with a resistor gate triggering then a BTA41 will also work, but you may have to reduce the value of the R1/R2, because BTA41 needs a minimum 50 ma to get triggered.
Thank for response.This R1/R2, meaning reduce both R1 & R2 or either R1/R2?
Regards.
Try with the existing set up first, if it doesn’t work properly then you can decrease the value of R2 a bit, if it still doesn’t work properly then finally you can reduce the value of R1 and check the response
Ok thanks, I will try.
Already try to reduce R1 to 20K, not triggered; then R2 to 1.2K, not triggered; then again R1 to 18K, not triggered. Any idea what proper value for R1 & R2 so that BTA triggered? FYI, existing set up already run for soft starting my home water pump, but unfortunately it last only for 2 days & then fail. Try replaced the BT136 with same one, same, just last for 2 days. Please help
Thanks.
Keep reducing the gate resistor further step by step, it will surely work, considering the fact that it worked with a BT136, so it has to work with a BTA41 also.
Already reduce bit by bit, reducing one cicle R2 & then decrease R1 and so forth till both reach 5.6ohm, but the TRIAC does not run. Please advise. Thanks.
It is now difficult to understand, because if BT136 is working then BTA41 should also work, it is just about providing sufficient gate current to the BTA41.
BTA41 just requires 50 mA to run, and 5.6 ohm is too low, it doesn’t need to be that low for driving the BTA41 triac. Can’t troubleshoot it at this moment.
As we know transistor can double the power by parallel, any suggestion if this BT136 I make it parallel to bear the excessive?
Unfortunately, it is not possible to connect triacs in parallel, instead you can try adding an opto coupler driver in place of the BT136, and then drive the bigger triac BTA41
Thanks for suggestion. Any Iink please for optocoupler driver?
After referring to your previous diagram I could not figure out how the opto coupler could be connected, so cannot go ahead with it. You can try using a 100uF in place of the 47uF and see whether it solves the problem or not. Try increasing the 47uF value and lowering the R2 value, until the right combination is found.
It seems along with R2, C2 is also responsible for delivering the required amount of current to the triac gate
I think there are lots of detailed explanations you always offer in your tutorials.
Thanks.
However, let me ask,
I used MOC3020 to fire ON/OFF BTA41-600B. the first time I switched on, the limiting resistor in series with the current into the MOC3020 burnt immediately. I used 1K.
Can you suggest better value?
I am driving A.C MOTOR 1000W.
Thank you, where did you use this 1K, at the input side or the output side? I guess it is on the input LED side of the optocoupler. If it on the input side then it very strange, because the input side has no connection with the load side. You can try 4k7 and see if that helps!
Hi Swagatam,
Thank you for the article. I learn something new today. However, I have case and wonder if you could help. I bought a spot welder control module from Amazon. The module can also be seen on aliexpress.com. The issue is every time, I hit the trigger, my circuit breaker tripped. The module uses the “BTA100-800b” . I wonder if I could use the chip BTA41/600B to resolve this issue. My home panel is 100A max. Each breaker is 15A or 10A. Thank you very much.
Hi Dylan, The tripping is happening due to over current drawn by the welding output load. BTA100 is just a switch which is rated according to the load current, so the 100 indicates its maximum tolerable current limit which is 100, which also means that a BTA41 will handle only 41 amps. So if you replace the 100 with 41, it may quickly burn due to the excess current above its tolerance limit.
If you think the welding machine is correctly producing the 100 amp for a 100 amp output load, in that case you may have to upgrade the tripping limit of the controller from 10A to 100A or as suitable, instead of replacing the triac.
Hi Swag,
What is the consequence if I don’t use choke?
Hi Edyrakh, the circuit will still work, but will generate a lot of RF noise in the atmosphere which may create disturbance in radios or other wireless equipment.
Can I use the circuit for higher current of triac like BTA100-800b?
I need to control temperature of various length of nikelin strip that I use to cut artificial fur. Curently I use autotransformator. The voltage that I use between 5V to 70V with maximum current of 30A.
you can do it but if your load is rated at 70V then it can be risky to use this circuit with 220V input, because the 300 peak voltage from the AC can damage your load. You can use the above circuit for controlling 220V load
Hi Swagatam,
I am trying to get calculation for correct value of resistor for triac. As you guided above, look at datasheet and gate current Vgt (12V), Igt (50mA) >> R= 240 Ohm. I also found another person talking about this using the Peak current and R for the gate is calculated by R= V*SQRT(2)/Ipk = 220*SQRT(2)/8Amp=38.8 Ohm.
Actually, I will use your approach, however, the provided guideline is here (for minimum value of Ohm for gate resistor)
https://www.onsemi.com/pub/Collateral/AN-3003.pdf.pdf
Apply for the case of BTA 12, I did not see the parameter for Vg but the test sheet with applied Vg 12 (Max) Ig 50mA and this make me a bit confuse on how to calculate the required resistor value for gate.
Please take a bit of time to show me.
Using your guidance, I found the safe ohm value should be 240 Ohm also.
Thank you very much for your attention.
From Vietnam
Hi Dang, yes it is definitely not dependent on the Vg parameter, rather solely on the IGT which is the triggering current for the specific triac at a given ambient temperature.
I have discussed the subject elaborately in the following article, which you can refer below, to get a simpler idea regarding how to select the gate resistor for any triac….just by using Ohm’s law
https://www.homemade-circuits.com/triac-circuits-working-and-application/
Hi, I’m interested in building a SSFR (Solid-state fan regulator) for old model ceiling fans. I thought of using BTA41/600B instead of BT136/BT137. As BT136/BT137 gets damaged in circuit mentioned at url https://www.homemade-circuits.com/how-to-make-simplest-triac-flasher/ Please suggest suitable changes to be made in your above circuit mentioned in the url https://www.homemade-circuits.com/how-to-make-simplest-triac-flasher/.
Thanks
Hi, BT136 is also a good triac and will not blow if the load is around 200 watts and the triac is mounted on a heatsink.
BTA41 can be used for 1kv and above loads with a heatsink. No changes in the circuit would be required for this.
Hello sir swagatam,av been thinking of including a triac in my Inverter charger to control charging currents since my Inverter uses mosfets body diodes for charging and mosfets doesn’t have current control capabilities,are my thoughts right? And if so then suggest for me the best triac that can control charge current to my batteries. Av got 2 batteries rated 12/200Ah connected in series but am planning to add the batteries as time goes by. So any triac u suggest to me should be able to handle high current even if the batteries are increased. Also I’ll really appreciate if you help with aid of a diagram, thanks in advance.
Hello Evans, triacs cannot be used for controlling current with DC supplies, since they will latch permanently ON when triggered, and will not switched OfF until the supply source is switched OFF
Oh,got you sir. Do you have any in mind that I can use to control charging current in my Inverter?
Evans, current control is supposed to be implemented using the shutdown feature in the oscillator IC, if it is provided in it. If not then you can try the following concept:
Good day sir, please I want the full article for the diagram on MOSFET over current control.thanks
Seun, the explanation is very basic. When current exceeds the set threshold, the voltage across the resistor Rs at the + input of the op amp surpasses the reference level at – pin of the opamp, causing the op amp output to become high, which grounds the MOSFET gates via the BjT shutting them off
Thanks for the concept sir,the values not given any help?
for 12V battery the zener can be 3V, and the zener resistor can be 1k. The zener value becomes the Vref, which is shown in the formula for calculating the value of Rs. The value of I will depend on the desired maximum current limit
Swagatam,
Any suggestions on how to connect the Triac to a high current load. If there is a 4 sq mm wire for 25-30A AC what is a recommendation on how to connect the Triac to that.
Anshuman, If you are referring to the circuit shown in the above article, then it has to be connected where the heater is shown, while also ensuring that the associated cables are rated accordingly.
hi Swag
I really learned alot from your tutorials.
i wish to ask about BTA41, can it be driven by A.C just like others triacs?
i mean, trigger it using MOC3033 (A.C).
i asked because you said it must be trigger by D.C.
Thank you Avong, Triac Gate pin always work with a DC, while the MT1, MT2 pins work with AC. MOC also delivers a Dc to the gate of the external triac.
Sir,
thanks for share your knowledge. I have a question about the right side of the circuit,what is the function of the resistor (100 ohms) and of the capacitor (0.1 uF, 630V). I am especially refering to the difference with the similar circuit: (secod scheme of https://www.homemade-circuits.com/how-to-make-simplest-triac-flasher/).
Thanks in advance
Stefano
Stefano, it is called snubber network, which helps to safeguard the triac from high current spikes, especially when an inductive load is used.
However nowadays most triacs have this feature in built.
Sir pls I need booster for iron
Try the second circuit from this article
https://www.homemade-circuits.com/generatoralternator-ac-voltage-booster/
Thanks sir for your kind reply for using ac load for triac I have powering the timer 555 with the 5 volts want to flash 60watt bulb through triac but its burning the resistor which is placed at output of 555 timer which is 3 pin out of timer please sir you have also not answer about driving thread mill dc motor 180volt 10amp driver ckt thanks
THe pin#3 resistor must be at least 1 K rated. Please use a 1K resistor and connect the triac with the correct pinouts, and make sure the MT2 of the triac has a common connection with the IC 555 ground line.
I have already given you the link for the 180V driver circuit in your previous comment.
Thanks sir I have used 1 kilo ohm for the triac bt137 but still the square wave coming from the timer is stopping at one end of resistor help me this my project of triggering gate of triac using timer I have already used relay which is working can you please show me the calculation of gate triggering resistor for any DC supply thanks once again
Hamid, the triac gate resistor is not so critical, any value between 330 ohm and 2k2 should work. make sure you have connected the triac pinouts correctly. center pin will go to the lamp, right side pin is the gate, and the left side pin will go the lamp
Sir i have a question regarding the 555 timer output can the pin 3 of timer can be given to the gate of the triac bt 137 bt 136 in order to achieve flashing the 220 volts 60 watt bulbs a resistive load if so what are the voltage should i used to power up the timer its either 5 volts or higher what current should i used what should be the resistor value should i used to limit the gate triggering current and voltage can i use opto isolator also called as opto coupler Today i have used the 555 basic alternating flashing ckt i have constructed on veroboard i have given the the output to the triac bt137 which is having 50ma of gate triggering current but some how the ckt is not working the leds are flashing but the gare of traic is not triggering please give me proper guide lines how to trigger triac easily in experiment i have used 330ohm quarter watt resistor which indeed not working what should be the resistor value for triggering bt137 Waiting for your reply
Hamid, for the IC 555 timer you can use 12V DC. Triac cannot be ud for DC load such as LED, that is why your triac is not working. for triggering the triac a 1K resistor will be OK, but the load and its supply should be AC not DC
Thanks for your reply
Thanks
Hi Swagat Sir,
I want to control a 12v, 100 watts resistive load from a digital signal. What would be the right control element to use?
Can I use the same triac used here?
This is for my headlamp on my bike. I upgraded the bulb to 100watts from 50watts, but the switches won't take that heavy current. Can you advice me please?
Hi just humble,
triac cannot be used for controlling a DC load, you can use a mosfet for example an IRF540 for this application.
connect positive supply through your switch to the gate of the mosfet.
connect source of the mosfet with the ground line.
connect the LED negative with the drain of the mosfet.
connect the positive of LED with the positive of the battery.
also do not forget to connect a 10K resistor from gate to source of the mosfet.
I have a 2 hours power 180 volt dc motor I want to control speed control circuit if so kindly guide me waiting for your reply
Salam Sir i have recently asked you a question i want a complete circuit diagram for dc motor thread mill 180volt 2 hp you have asked about using a mosfet for controlling dc motors i need this urgently please help me in this regard
Dear Swagatham,
I have been following your work since the last few years and you are simply unbelievable…your passion and energy has not dimmed a bit all these years and posts later…how do you manage to eat, sleep and make a living?! How can you go on writing, replying(to some occasionally stupid questions too!), providing links and that too in the simplest of terms(the language is really good)…man-you are an inspiration,a one-man inspiration-army!
May the gods give you the best!
Prayers and warm wishes to you!
Dr.Niranjan
nirugnair@yahoo.com
Thank you very much Dr.Niranjan, as you rightly used the word "passion" that's exactly what helps me to keep going with the present job without tiring….and when one of the valuable viewers like you appreciates me that further boosts by inspirations.
I wish you too all the best, and may God bless you!
Hello Swagatam…It's very nice info that I get..
I've plan to make DC rectifying from 220 volt without transformer…And I need DC range from 20 to 100 voltDC..
if I use your schematic, what the suitable value of pot and resistor ?
Thanks a lot master…
thanks very much, but sorry the above concept cannot be used for controlling AC voltage levels….you will have to employ some other circuit or a variac for achieving this.
hello mr.. thanks for your fast reply.
I have think before about use variac to regulating and controlling my voltage,, but its too expensive to buy it,, hehe,,
then I try googling to find information about transformerless supply.
By the way, i've just read your "treadmill-motor-speed-controller-circuit"
and it said that
"a modified dimmer switch circuit design which can be effectively used for regulating a 180 V treadmill motor from zero to max"
may it control voltage from zero to 180 volt ?
thank a lot for your support Mr.
yes I recommended the design for treadmill motor since its spec 180V is quite near to 220V, but ideally it is not recommended to use a dimmer switch for controlling voltage.
But nevertheless you can surely try it and check whether it satisfies your application condition or not.
Dear Mr.Swagatam
I have done with it..
First one.. I connect dimmer output to bridge rectifier and 330uF Ecco..but my fuse has blown cause charging huge current.. and then I remove elco and I test it using 100watt bulb lamp..
It's great..your circuit works well.
I've upload the test run video at YouTube. "test run Dimmer circuit using triac bta41-600"
Thanks again Mr.Swagatam for your knowledge share…
Thank you dear Fira, I am really glad to hear your experience with this circuit….keep up the good work
you can probably try the following concept
https://www.homemade-circuits.com/2016/05/mini-welding-machine-circuit.html
thank you very muchh swagatamji for your support.
thank you swagatamji, my load is purely resistive in nature.
i have connected MCB at input side for heavy current trip during short circuit. the problem is when light gets fused then sometimes it get short and result in damage of triac because of short circuit.
i switch on thew light when pot was at max directly many times and still it working fine. now i am using this circuit till 4kw.
i made 2 triac in parallel but only 1 triac is working, even i gave gate input through diff diac(but from same origin). Only few times both work together. i checked current through clamp meter on each triac.
Hello Rohitji, triacs in parallel will never work since their firing characteristic will mostly, causing one of the triacs to fire before the other, therefore they will never fire together.
If a short circuit is a possibility then definitely an MCB is the right option, and it must be included.
hello Swagatamji thanks for your circuit.
Can i used this circuit for lightning application for power around 7.5kW @230V input.
And circuit to be added for short circuit protection for TRIAC.
is bidirectional Transil diode required for protection.
pls help.
Hello,
yes you can use the first circuit for your specific application. Use a large heatsink with the triac and make sure that the circuit always switched ON while the pot is set at the minimum side of the dial…onec switched ON then it could be adjusted to the required intensity.
The lights should be resistive in nature, LEDs will not work
an appropriately rated fuse could be added for the protection, other forms of protection may not be required.
hello sir
if i want to make a constant temperature control at 80 degrees celcius from second circuit above. what should i modificate from circuit or add thermistor my be
thanks
hello choirul,
if the input mains is not fluctuating then simply setting the given pot control will allow you to achieve any desired temperature level at a reasonably constant rate
salam sir i have a question in my mind That how much current is required to trigger a relay havibng 5volts 6 volts any idea How to calculate total current current required by relay
Hello Hamid,
you can get the full explanation under this article
https://www.homemade-circuits.com/how-to-make-relay-driver-stage-in/
Hi! Swagatam,
Can I use this circuit to make 110V dc from 220V rms ac after usinf triac and rectifier?
I am trying to make a 36V battery charger ofat least 6 to 7A and I am trying not to use transformer. Is it possible.
Hi Abdul, it is possible but is strictly not recommended for battery charging, because if the triac or the circuit fails at any instant, there could be an explosion in the battery and a catastrophic hazardous situation
hi! swagatam,
how do i select the heatsink for this triac (BTA41600b),
trying to switch a 4hp pump, with this.
Hi Christina, calculating it could be complicated. Better to do it by some practical experiment, in general use the largest possible heatsink to the device for providing maximum cooling…
thanks! Swagatam.
will try some available options.
can we use this bta41 circuit as a steplizer
no
Pls How Will I Calculate The Appropriate Resistors(including The Watts) And Capacitors For The Correct Amps And Volts Rating Of A Triac When Constructing
the optimal gate current of BTA41 is 50mA, at 12V.
you can Ohm law for calculating this
V= IR
12 = 0.05 x R
R = 240 ohms
any value slightly lower than this can be used as the gate resistor for the BTA41
Sir i have also experimented from the bt137 triac Can you please guide me how to trigger the gate of traic properly i have a dc supply of 9 volts i want to switch on the traic through the 555 timer is this possible if so kindly also help me in this regard waiting for your reply
Hi Hameed, you can use the following circuit
https://www.homemade-circuits.com/make-this-pwm-based-dc-motor-speed/
triac will not work for DC motors, you will have to use a mosfet based PWM driver as explained in the above link
multiply 12 x 0.05 for getting the resistor wattage
Thanks so much Engineering Genius – Swagatam . You have made engineering so easy for me, more grace to your elbow
pls sir, what about how to calculate the appropriate capacitor for BTA41
thanks Atinuke,
which capacitor are you referring to?….. the one connected between its MT1 and MT2 is not actually required because the triac is internally protected with a snubber stage.
Thanks Sir,does Bta41-600 Supply 40amps And 600v To The Appliance Wont It Damage The 2hp Motor
The specs are the maximum breakdown limits of the device, it will supply only what is consumed by the load, and as per the input power.
Hi sir, pls are scr and triac the same and do they have the same mechanism of operation. Between BTA41-600B and BTA16-800 can we say they have the maximum rating of 24,000va and 12,800va respectively. can either be used to power a 2,200va heater without damage to the heater, what will be there power consumption and their efficiency rate. can BTA41-600B be used to power a 2hp electric pump.for BTA41-600B can we say it supplies 40amps and 600v into appliance.since there are diff thyristors, what will be the criteria of choosing the appropriate one for the right rating for an appliance. Well done sir ,you have been greatly resourceful, please attend to all my questions. thanks
Hi Atinuke,
your calculations are correct according to me, but the devices will need to be mounted on substantially large heatsinks to implement those figures.
220va heater and 2hp motor can be operated using BTA41 triac
all thyristors and triacs basically work in the same way, there are distinguished by their amp and volt ratings including some other factors such as built-in snubber, and other protections…..however today most of these devices are on par with each other, so only their I and V rating needs to be considered while selecting those.
Sir one of your "Simple Dc motor speed Controller" circuit configured around ic 555
if I use this PWM circuit to drive the Triac to control heating. Is it okay
Yes it will be OK…but I would recommend an optocoupler for this, for example using a MOC optocoupler would make things extremely safe and accurate
3.bp.blogspot.com/-4dY_nPZyFGk/VXveLFjql3I/AAAAAAAAKbc/mJzqWjJt2xg/s1600/triac%2Bpwm%2Bdriver.png
Sir if I build the PWM circuit with 555 ic as designed by you and control it with a separate 12dc supply
and make these two supplies (12dc and 220 AC ) common and connect pin three to Triac gate
will it do?
Mujahid, yes that will be required for proper functioning of the triac, and is OK, but make sure you don't touch the circuit because it will be at the mains potential and extremely lethal..
Kindly explain the PULSE WIDTH MODULATION as I don.t know about it. What is its function in the above circuit
a pulse is a momentary application of a voltage for a selected duration of time, say for 1 second…if this pulse is alternately switched ON and OFF and the ON/OFF period is varied as per the user preference, then it is said to be a pulse width control…and if this ON/OFF period is varied corresponding to another signal's variation then it's called pulse width modulation since the pulse is being modulated by another signal….
a Triac can be used for three phase supply?
yes it can be used
The motor should catch its speed to its peak "Slowly & Automatically "
that.s what I want to know
What PWM stands for?
Second
sir my previous question was incomplete, let me complete it. I want my AC motor to catch its speed slowly and it should be AUTOMATICALLY. you recommeded the PWM one with ic 555. Can it be AUTOMATIC as well
Pulse Width Modulation
yes the referred circuit will do exactly that!
it'll automatically allow a slow start for the motor on every power switch ON.
What is CMOS IC ?
ICs made using CMOS technology, these ICs have the characteristic of a high input impedance, and always produce either a high (1) or a low (0), never anything else
…and always produce either a high (1) or a low (0), never anything else at their outputs, when powered
I have a 1Hp 220v AC motor. I want it to catch its speed slowly.
Is it possible with the above circuit if yes then how? And
Will it be safe?
not the above circuit…you can use the "PWM soft start motor start circuit" which is posted in this site itself.
Sir I want my exhaust fan(AC) to increase its speed as the temperature in kitchen increases and decrease its speed as the temperature decreases
is it possible with the above circuit
Mujahid, it's possible, but by including a temperature sensor with the circuit, such as a LM35 sensor or similar.
although a little different, I have a related circuit posted in this blog, you can check it here:
https://www.homemade-circuits.com/2013/01/automatic-temperatureclimate-controlled.html
If I want to trigger the Triac with the mains AC then what should be the resistor value for 220v AC for 50mA gate current
Second
The speed of a motor or heater temperature is controlled manually by increasing or decreasing resistance, sir is it possible this thing happens automatically.
I mean I want to control this resistance automatically how is it possible? So that the temperature or motor speed increase automatically without any manual work.
use Ohms law to calculate the resistor.
it's not possible to control a triac output with a variable resistor, you will require either a PWM or a phase chopper circuit for that, as explained in the article above.
Hi,
That part is very old part, And that is not available in online markets and local market. Can u please suggest any other alternative with regular make. Or suggest me for any alternative designs for 100A solid state relay.
I think you should inquire with your local spare part dealer or in the local market for knowing exactly which one may be available…or you can also Google for the same and buy it online, any 600V 100amp triac will do the job
in other alternative design too the triac will need to be 100amps as per the required specifications.
Hi Swagatham,
Am planning to design Solid State relay 100A capacity.
Voltage range is 90 to 264Ac.
Can u please tell me the part number of triac which is withstands 100A.
Hi Amar,
you can try the TSR100AA60 it's rated to withstand 100amp at upto 600V
you can do it by adding a temperature sensor with the circuit as shown here:
https://www.homemade-circuits.com/2011/12/make-simple-refrigerator-thermostat.html
the transistor emitter parts along with the triac is not required and can be removed, the power supply section can also be eliminated as we already have it in the above design
the transistor collector can then be connected with pin5 of the IC 555 and emitter to ground.
one method is to connect a 1k resistor across pin5 and ground.
next, connect a BC547 transistor and connect its emitter to pin5, collector to positive, and its base with a parallel link from positive immersed in water.
as long as water is present the BC547 will conduct and keep the heater hot, and switch OFF the IC 555 in the absence of water.
Hi Mikel,
It's possible but what would be the sensing parameter? this will need to be figured out first…
Hi Mikel,
yes you can use the designs for controlling all types of heater devices.
the 40uH is actually not required, it's included to cancel out the RF emissions or disturbances in the air, alternatively you can easily build it by winding 200 turns of 1mm copper magnet wire over an iron bolt
for the second design you can use a 100k instead of the shown 220k, but not 500k
What would be the benifit of the PWM ckt over the first Triac control ckt above?
both will vary the RMS effectively…the second circuit will provide slightly more reliable results since it's not dependent on diac's not firing issues
Hi i wanna build a power control circuit that can power 1000-2000 watts load from a 650 watts 230 voltage source.
Please Sir help me with the circuit diagram.
THANKS!
How can you obtain 2000 watts from a 650 watt source?? That's not possible.
thank you very much. I'll see if I get one locally… as the BTA41 600B is availabe so i purchased it.
Hi swagatam,
I wanted to use this triac for AC motor pump control whose load may vary from 3A to 10A. And I am quiet to new to Triacs,especially snubber circuit design,so will you please help me in designing snubber for that load? Thank you.
Hi Mrunal,
The modern triacs do not require snubbers, they have built-in protections, you can get more info about the part numbers in the following ink:
http://www.st.com/web/en/catalog/sense_power/FM144/CL1221/SC124/LN1596?icmp=ln1596_prom_sc124promo_dec2013
Hi Swagatam
How many watts do i need for resistor?
Thank you
Hi Chris,
all are 1/4 watt rated
thank you very much,
i think that circuit is good for preheater
you are welcome chris.
OK Sir Swagatam Majumdar. Very grateful for the attention and response. Did not think my question would return. I will replace the potentiometer 470K to 220K and return of the information. Hugs Celso Castro. English translated by Google.
You are welcome!
Salvador, Bahia, Brasil 24.08.2013.
Swagatam Majumdar
Como faço para modificar os circuitos do BTA 41 de 220v para 127v?
Agradeço pela atenção e se for possivel responder.
Saudações,
Celso Castro
Traduzido do Inglês para Português pelo Google
Salvador Bahia Brasil, 24.08.2013
Sir Swagatam Majumdar
How do I modify the circuitry of BTA 41 220v to 127v?
I appreciate the attention and if possible answer.
Regards,
Celso Castro
Hi Celso,
You can use the above design with 127V also, just replace the shown 470K pot with a 220K one.
Swagatam Majumdar, grateful for the guidance. I replaced the potentiometer of 470k to 220 k lin, 330k to 220k resistor.It ran on 120 volts and this perfect today. I had to get away and could not answer.
Thank you, Celso Castro – Salvador – Brazil. 06/30/2015. Google translator.
that's great Celso, I am glad to hear this…thanks for updating the info.
Hi, I'm interested in building a SSR (Solid-state relay) for use with Arduino, I thought of this uitllizar BTA41/600B
I have a circuit [api10.net/rele_diagrama.jpg] (if you can access and view, thank you). I'm using a MOC3021.
My question is: This circuit the way it is, it is safe to 40A?
Thank You
Yes it is safe, but will require good heatsinking and at least 50mA of gate current.