An electronic incubator thermostat circuit shown in this article is not only simple to build but is also easy to set and acquire exact tripping points at various different set temperature levels. The setting may be completed through two discrete variable resistors.
How Incubators Work
An Incubator is a system where bird/reptile eggs are hatched through artificial methods by creating a temperature controlled environment.
Here the temperature is precisely optimized to match the natural incubating temperature level of eggs, which becomes the most crucial part of the whole system.
The advantage of artificial incubation is faster and healthier production of the chicks compared to the natural process.
Sensing Range
The sensing range is quite good from 0 to 110 degrees Celsius. Switching a particular load at different threshold temperature levels doesn’t necessarily need complex configurations to be involved in an electronic circuit.
Here I have explained a simple construction procedure of an electronic incubator thermostat. This simple electronic incubator thermostat will very faithfully sense and activate the output relay at different set temperature levels from 0 to 110 degree Celsius.
Drawbacks of Electromechanical Thermostats
The conventional electromechanical temperature sensors or thermostats are not very efficient due to the simple reason that they cannot be optimized with accurate trip points.
Normally these types of temperature sensor or thermostats fundamentally use the ubiquitous bimetal strip for the actual tripping operations.
When the temperature to be sensed reaches the threshold point of this metal, it bends and buckles.
Since the electricity to the heating device passes through this metal, it’s buckling causes the contact to break and thus power to the heating element is interrupted - the heater is switched off and the temperature starts falling.
As the temperature cools, the bimetal starts straightening to its original form. The moment it reaches its previous shape, the electricity supply to the heater is restored through its contacts and the cycle repeats.
However, the transition points between the switching are too long and not consistent and therefore not reliable for accurate operations.
The simple incubator circuit presented here is absolutely free from these drawbacks and will produce comparatively high degree of accuracy as far the upper and the lower tripping operations are concerned.
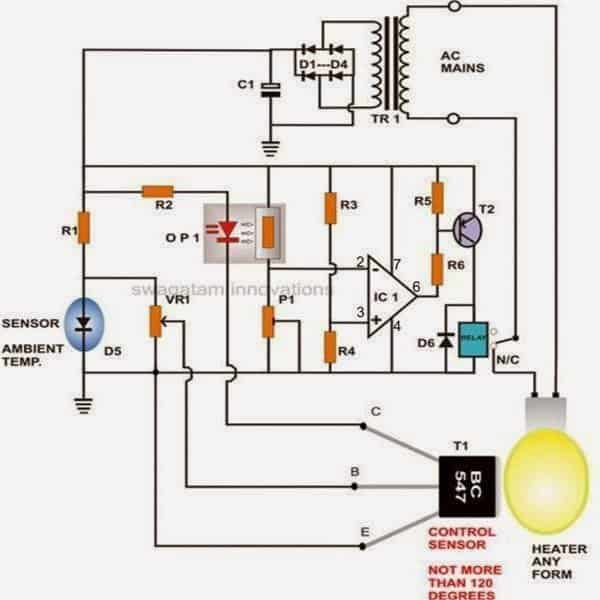
Parts List
- R1 = 2k7,
- R2, R5, R6 = 1K
- R3, R4 = 10K,
- D1---D4 = 1N4007,
- D5, D6 = 1N4148,
- P1 = 100K,
- VR1 = 200 Ohms, 1Watt,
- C1 = 1000uF/25V,
- T1 = BC547,
- T2 = BC557,IC = 741,
- OPTO = LED/LDR Combo.
- Relay = 12 V, 400 Ohm, SPDT.
Circuit Operation
We know that every semiconductor electronic component changes its electrical conductivity in response to the varying ambient temperature.
This property is exploited here to make the circuit work as a temperature sensor and controller.
Diode D5 and transistor T1 together form a differential temperature sensor and interact greatly with each other with changes in the respective surrounding temperature.
Also since D5 acts as the reference source by staying at the ambient temperature level should be kept as far as possible from T1 and in open air.
Pot VR1 may be used externally to optimize the reference level set naturally by D5.
Now assuming D5 is at a relatively fixed temperature level (ambient), if the temperature in question around T1 starts rising, after a particular threshold level as set by VR1, T1 will begin to saturate and gradually start conducting.
Once it reaches the forward voltage drop of the LED inside the opto-coupler, it will start glowing correspondingly brighter as the above temperature rises.
Interestingly as the LED light reaches a particular level, further set by P1, IC1 picks this up and instantly switches its output.
T2 along with relay also respond to the IC’s command and respectively actuate to trip off the load or the heat source in question.
How to Make an LED/LDR Opto-Coupler?
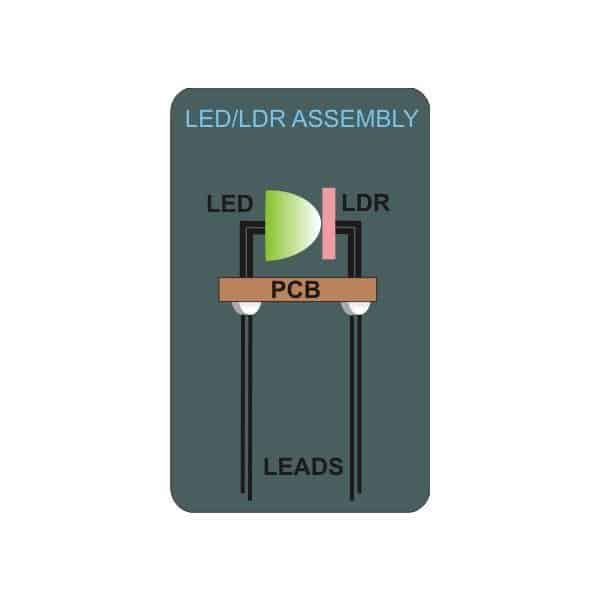
Making a homemade LED/LDR opto is actually very simple. Cut a piece of general purpose board about 1 by 1 inch.
Bend the LDR leads near its “head.” Also take a green RED LED, bend it just as the LDR (See figure and Click to Enlarge).
Insert them over the PCB so that the LED lens point is touching the LDR sensing surface and are face to face.
Solder their leads at the track side of the PCB; do not cut off the remaining excess lead portion.
Cover the top with an opaque lid and make sure its light proof. Preferably seal off the edges with some opaque sealing glue.
Let it dry. Your home made LED/LDR based opto-coupler is ready and may be fixed over the main circuit board with its leads orientations done as per the electronic incubator thermostat circuit schematic.
Update:
After some careful investigation it became evident that the above opto-coupler can be totally avoided from the proposed incubator controller circuit.
Here are the modifications which needs to be made after eliminating the opto.
R2 now directly connects with the collector of T1.
The junction of pin#2 of IC1 and P1 hooks up with the above R2/T1 junction.
That's it, the simpler version is now all ready, much improved and easier to handle.
Please check-out the much simplified version of the above circuit:
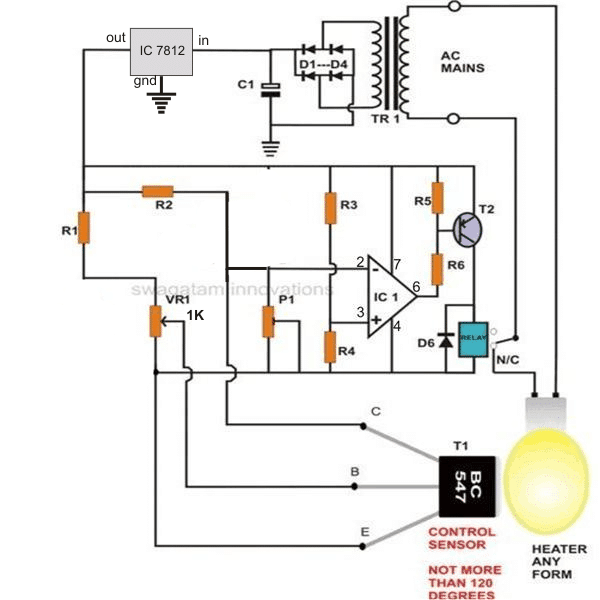
Adding a Hysteresis to the above Incubator Circuit
The following paragraphs describes a simple yet accurate adjustable incubator temperature controller circuit which has a special hysteresis control feature.
The idea was requested by Dodz, let's know more.
Technical Specifications
Actually, I have a little request to make and I hope this does not burden you that much. I have been researching on analog thermostat for my homemade incubator.
I learned that there are probably dozen of ways of doing it using different sensors such as thermistors, bi-metallic strip, transistors, diodes, and so on.
I want to build one using either of these methods but I find the diode method as the best one for me because of the availability of the components.
However I could not find diagrams that I am comfortable experimenting with.
The present circuit is good but could not follow much regarding setting the high and low temp levels and adjusting the hysteresis.
My point is I want to make thermostat with sensor that is diode-based with adjustable hysteresis for a homemade incubator.
This project is for personal use and for our local farmers that venture into duck and poultry hatching.
I am an agriculturist by profession by I studied (vocational very basic course) electronics as a hobby. I can read diagrams and some components but not very much.
I hope you can make me this circuit. Lastly, I hope you can make simpler explanations especially on setting the temperature thresholds and the hysteresis.
Thank you very much and more more power to you.
The Design
In one of my previous posts I have already discussed an interesting yet very simple incubator thermostat circuit which uses an inexpensive transistor BC 547 for detecting and maintaining the incubation temperature.
The circuit includes another sensor in the form of a 1N4148 diode, however this device is used for generating the reference level for the BC547 sensor.
The 1N4148 diode senses the ambient atmospheric temperature and accordingly "informs" the BC547 sensor to adjust the thresholds appropriately.
Thus during winter, the threshold would be shifted on the higher side such that incubator stays warmer than during summer seasons.
Everything seems to be perfect in the circuit except one issue, that is the hysteresis factor which is completely missing there.
Without an effective hysteresis the circuit would respond fast making the heater lamp switch at rapid frequencies at the threshold levels.
Moreover adding a hysteresis control feature would allow the user to manually set the average temperature of the compartment as per individual preferences.
The following diagram shows the modified design of the previous circuit, here as we can see, a resistor and a pot has been introduced across pin#2 and pin#6 of the IC.
The pot VR2 can be used for adjusting the OFF time of the relay as per the desired preferences.
The addition almost makes the circuit a perfect incubator design.
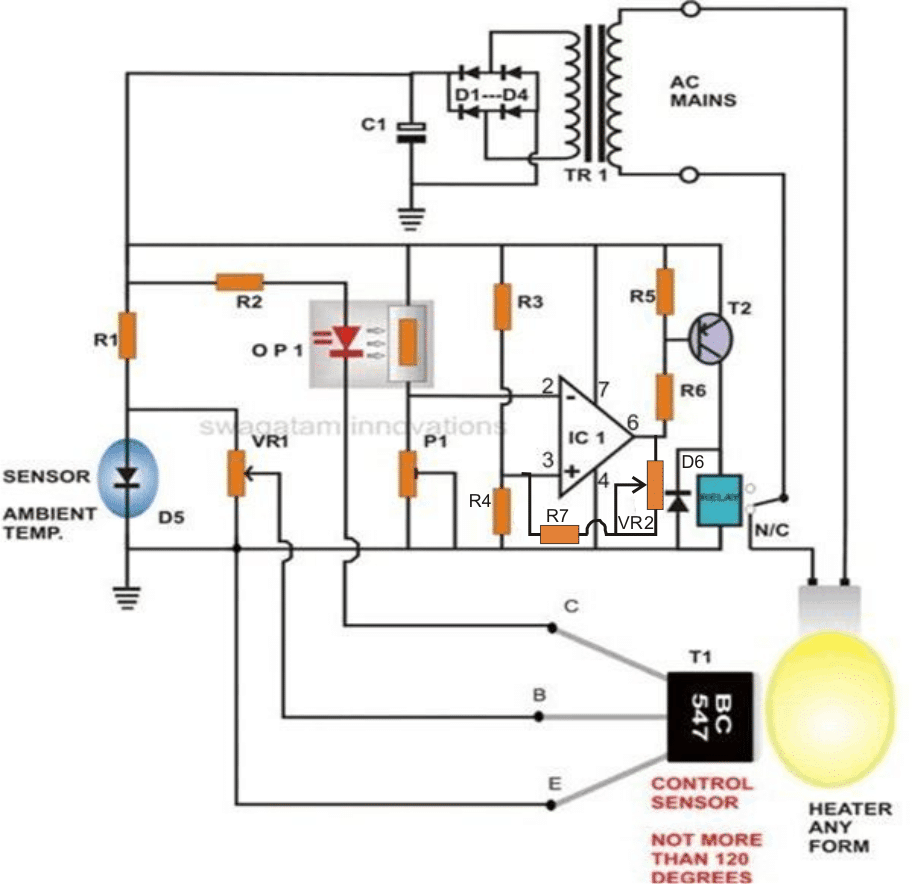
Parts List
- R1 = 2k7,
- R2, R5, R6 = 1K
- R3, R4, R7 = 10K,
- D1---D4 = 1N4007,
- D5, D6 = 1N4148,
- P1 = 100K,VR1 = 200 Ohms, 1Watt,
- VR2 = 100k pot
- C1 = 1000uF/25V,
- T1 = BC547,
- T2 = BC557,IC = 741,
- OPTO = LED/LDR Combo.
- Relay = 12 V, 400 Ohm, SPDT.
Incubator Thermostat using IC LM35 Temperature Sensor
A very simple egg incubator temperature controller thermostat circuit using LM 35 IC is I have explained in this article. I have explained more.
Importance of Temperature Controlled Environment
Anybody involved in this profession will understand the importance of a temperature controller circuit which should be not only reasonably priced but also have features like precise temperature control and manually adjustable ranges, otherwise the incubation could get hugely affected, destroying most the eggs or developing premature offspring.
I have already discussed an easy to build incubator thermostat circuit in one of my earlier posts, here we'll learn a couple of incubator systems having easier and much more user friendly setting up procedures.
The first design shown below uses an opamp and a LM35 IC based thermostat circuit and indeed this looks quite interesting due to its very simple configuration:
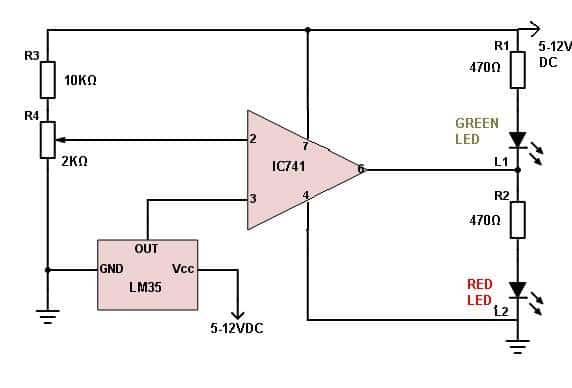
The idea presented above looks self explanatory, wherein the IC 741 is configured as a comparator
with its inverting pin#2 input pin is rigged with an adjustable reference potentiometer while the other non-inverting pin#3 is attached with output of temperature sensor IC LM35
The reference pot is used to set the temperature threshold at which the opamp output is supposed to go high.
It implies that as soon as the temperature around the LM35 goes higher than the desired threshold level, its output voltage becomes high enough to cause pin#3 of the opamp to go over the voltage at pin#2 as set by the pot.
This in turn causes the output of the opamp to go high. The outcome is indicated by the lower RED LED which now illuminates while the green LED shuts off.
Now this outcome can be easily integrated with a transistor relay driver stage for switching the heat source ON/OFF in response to the above triggers for regulating the incubator temperature.
A standard relay driver can be seen below, wherein the base of the transistor may be connected with pin#6 of the opamp 741 for the required incubator temperature control.
The Relay Driver Stage for Switching the Heater Element
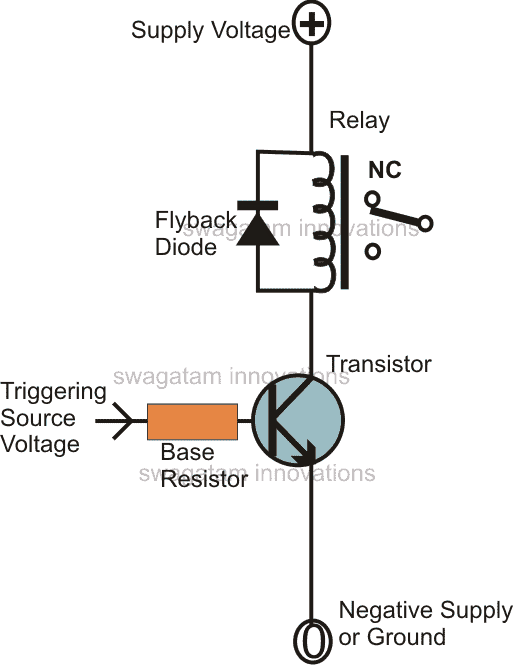
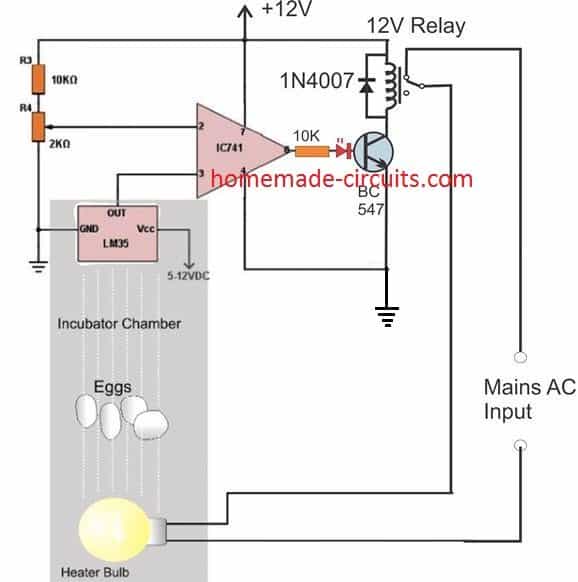
Incubator Temperature Controller Thermostat with LED Indicator
In the next design we see another cool incubator temperature controller thermostat circuit using an LED driver IC LM3915

In this design the IC LM3915 is configured as a temperature indicator through 10 sequential LEDs and also the same pinouts are used for initiating the ON/OFF switching of the incubator heater device for the intended incubator temperature control.
Here R2 is installed in the form of a pot and it constitutes the threshold level adjustment control knob and is used for setting up the temperature switching operations as per the desired specifications.
The temperature sensor IC LM35 can seen attached to the input pin#5 of the IC LM3915. With rise in temperature around the IC LM35 the LEDs begin sequencing from pin#1 towards pin#10.
Let's assume, at room temperature the LED#1 illuminates and at the higher cut-off temperature the LED#15 illuminates as the sequence progresses.
It implies that pin#15 may be considered the threshold pinout after which the temperature could be unsafe for the incubation.
The relay cut-off integration is implemented according to the above consideration and we can see that the base of the transistor is able to get its biasing feed only upto pin#15.
Therefore as long as the IC sequence is within pin#15, the relay remains triggered and the heater device is held switched ON.
However, as soon as the sequence crosses over pin#15 and lands on pin#14, pin#13 etc. the transistor biasing feed is cut off and the relay is reverted towards the N/C position, subsequently switching OFF the heater..... until temperature normalizes and the sequence restores back below the pin#15 pinout.
The above sequential up/down drift keeps on repeating in accordance with the surrounding temperature and the heater element is switched ON/OFF maintaining almost a constant incubator temperature as per the given specifications.
Solar Powered Egg Incubator Circuit
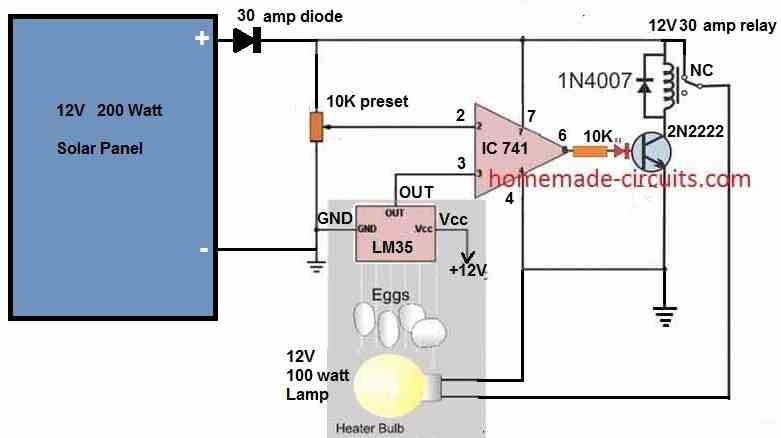
The solar-powered incubator circuit described uses an op-amp configured as a comparator to control the operation of a heater bulb for eggs. The working of the circuit can be understood from the following points.
Solar Panel: The circuit is powered by a 12V 200W solar panel, which provides the required operating power to the circuit and the lamp.
LM35 IC Heat Sensor: An LM35 temperature sensor IC is connected to the non-inverting input of the op-amp (741) to detect the heat generated by the heater bulb. The LM35 provides an output voltage proportional to the temperature it senses.
10K Preset: A 10K preset resistor is connected to the inverting input of the op-amp. This resistor sets the reference voltage for comparison with the LM35 output.
By adjusting the preset resistor, the desired temperature threshold can be set.
Op-Amp (741) Comparator: The op-amp (741) is configured as a comparator. The IC the voltages at its inverting and non-inverting inputs.
As soon as the voltage at the non-inverting input goes above the voltage at the inverting input, the output of the op-amp becomes high.
Transistor Relay Driver: A transistor relay driver circuit is connected to pin 6 (output) of the op-amp.
The relay driver provides the necessary current to activate a relay when the op-amp output goes high.
Relay: The relay acts as a switch that controls the power supply to the heater bulb. When the op-amp output goes high, the relay is activated, turning off the bulb.
Conversely, when the op-amp output goes low, the relay is deactivated, turning on the bulb.
Circuit Description
The functioning of the circuit is as follows:
Initially, the heater bulb is turned on, and the LM35 measures the temperature.
The op-amp compares the LM35 output voltage with the reference voltage set by the 10K preset resistor.
If the measured temperature exceeds the set threshold, the op-amp output goes high, activating the relay and turning off the heater bulb.
As the temperature decreases below the threshold, the op-amp output goes low, deactivating the relay and turning on the heater bulb again.
This cycle repeats continuously, maintaining the temperature within the desired range.
I need a stable solar powered circuit, for my 12V 300watts solar panel, which can power 2 smart phones and a dc 19V, 3.42amp driven laptop during the day only, so that it doesn’t need any battery.
You can try the first boost converter circuit shown in the following article:
https://www.homemade-circuits.com/high-power-dc-to-dc-converter-circuit-12-v-to-30-v-variable/
Please comment under the above article if you have any questions regarding this circuit.
In the Solar Powered Egg Incubator Circuit, does it work at night? If no, can you, please, modify it to also function during the night
It will not work at night.
How do you want to power the lamp at night? using 12V or mains AC?
Using 12V Sir
You can connect the 12V DC with the supply lines of the circuit, in this way it will work during daytime through solar power and at night it will work using 12V DC from your external source…or you can also use a relay to alternately toggle the two supplies during day and night.
Sir, please, what type of diode is at the base of 2N2222 in the “Solar Powered Egg Incubator Circuit” and what is it’s value?
Hi Lisborn, that is a RED LED, rated at 3.3V, 20mA.
It’s 1:22am in Nigeria, good morning dear SWAG. I am very grateful for your good job on Solar Powered Egg Incubator Circuit, I love it – more grease to your elbow.
Please, I want to ask these questions:
1) How do I make up for the fluctuations of the sun during the day?
2) How do I increase the output power with the output voltage remaining at 220V?
Good Morning Lisborn,
You can stabilize the solar output by using a high voltage solar panel and then stepping it down using a buck converter, then the buck converter output can be adjusted to provide a fixed voltage.
Power can never be increased, you can increase either the voltage (by reducing the current) or increase the current (by reducing the voltage).
l am interested in simple incubators and l want to learn more about simple circuits.l would like to hatch eggs at home.
You can try the following simple design:
https://www.homemade-circuits.com/wp-content/uploads/2024/09/simplest-egg-incubator-circuit.jpg
Let me know if you have any doubts regarding the circuit…
So the question basically says this:
An amplifier is required to amplify a signal that varies from OV to 1V to an output potential of
OV to 5V as per the following diagrams
a) Using no more than three components develop and test a circuit using these diagrams as a starting point.
I can’t however post the diagram here cause it doesn’t allow me to paste it.
I am not really sure what amplifier it is.
Thank you
You can try the following circuit:
https://www.homemade-circuits.com/wp-content/uploads/2016/01/Li-Fi.jpg
The 2 ohm resistor and the LED can be removed.
The amplified output can be acquired across the transistor collector and the positive line.
Thank you so much. I managed to make the circuit work.
No problem! I am glad it worked.
Hello and thank you for your help I am really struggling to design the circuit diagram of incubator that is designed to be at the constant temperature of 49 degrees, it must contain the heat lamp that is automated if the temperature gets to low and it turn off when the temperature gets to high. Also you can set it to desired temperature and the output driver must include a MOSFET
Can you please help me with this circuit diagram if possible
Hello, no problem, I will help you to succeed with your incubator project.
Please try the following circuit, it will surely work. Please make sure to keep the LM35 IC close to the bulb, at a touching distance.
https://www.homemade-circuits.com/wp-content/uploads/2016/08/incubator-circuit.jpg
Thank You for Your reply, do You have any tutorials where amplifier is used? I need to develop circuit where an amplifier is required to amplify a signal that varies from 0V to 1V to an output potential of 0V to 5V, and where no more than 3 components are used excluding the amplifier.
Do you mean an audio amplifier or boost converter? Please explain more….
In the work sheet I have it only says amplifier to amplify the signal. I can send the picture of original sheet that I need to follow with basic draw of the circuit I need to complete.
Thank you
The signal to be amplified is constant DC, or is fluctuating?
Basically is it an audio amplifier that you need or a boost converter?
I kindly requesting for a precise drawing of a laboratory incubator circuit
In the laboratory incubator I can add temperature control and humidity control but not CO2 control, will that be Ok?
Ok,but my request was a complete circuit. Just proceed
How is a precise laboratory incubator circuit look?
Please provide detailed specifications about your requirement, i will try to figure it out.
Ok,but my request was a complete circuit
Pleade Provide specifications.
An embryo incubator circuit
What features do you want in the circuit?
The switches,thermal regulators,resistors
You can try this concept:
https://www.homemade-circuits.com/incubator-using-arduino-with-automatic-temperature-and-humidity-control/
Thank you so much
You are welcome.
Hello swagatam, I’m again back to you, requesting you to please design an incubator that can use solar or dc electricity
Thanks Rashid, I will try to upgrade the last circuit with solar panel and DC lamp.
If possible please specify the solar panel voltage and current specifications.
You are the father of technology, so I kindly request you to design it in dc way, let’s say for example let it be using 12v dc batteries and it can incubate more than 500 eggs so that it can help in the villages.
Please swagatam you are the one to decide what is very easy to make and very cheap and can incubate very many eggs so that it can can help in the villages, thanks
Thank you Rashid, for your kind words.
I have updated the circuit diagram at the end of the above post, you can check it out.
However, I am not sure what should be the power of the bulb to incubate 500 eggs, you will have to dimension the bulb and the batteries according to the necessary specifications.
The solar panel can be replaced with a 12 V 200 Ah lead acid battery.
Hi swagatam;
Pls can you explain to me what is P1 in the circuit?
Hi Abdulrahman, P1 is a preset or a trimpot.
I would recommend you the following circuit which is more easy to build:
https://www.homemade-circuits.com/wp-content/uploads/2016/08/incubator-circuit.jpg
Hi Swagatam;
I think the stable humudity should be necessary for the incubators. Please advise how we can control it and if there is any sensor like LM35 to control the humudity. Best Regards
Hi Suat,
Here’s one circuit which can be used for implementing humidity and temperature both:
https://www.homemade-circuits.com/incubator-using-arduino-with-automatic-temperature-and-humidity-control/
Dear Swagatam,
Is it possible increase the temperature sensing range up to 250°c?
We want to use same circuit for one of our hating project, where we need the cutoff range 250°c.
best regards
Prakash Srivastava
Dear Prakash, it is possible by safeguarding the BC547 with a 5mm thick coating of epoxy, so that 250 degrees on the heater corresponds to 100 degrees on the BC547
Sir please tell me what is the temperature range with 2k resistor of Thermostat that based on Lm35 temperature sensor. I am talking about second last circuit diagram of this page….
And my second question is which is best last or second last by accuracy because i want to add high temperature alarm in incubator because some times temperature goes high…. Please answer me…
Asad, you can adjust up to 80 degrees C. But it also depends on the distance of the LM35 from the temperature source.
The second last is easier than the last one, but the last one has the feature of 10 step LED temperature indication.
Please guide me by Making What changes i control temperature on 37.5 ?????….please tell me
Asad, Keep the pin2 preset to positive level. You will find the relay is switch OFF, and the RED led OFF.
Now bring a 38 degree heat source very near to the LM35, and slowly adjust the preset until the relay just switches ON.
That’s all, the circuit is set now. Make sure to use the pole and the N/C contact of the relay for the load and mains connections
Sir please tell me what do you mean by positive level????
At first rotate the preset with screwdriver until the center pin of the preset or the IC pin2 becomes equal to positive supply. Now the relay will be OFF (RED LED OFF)
After this bring a 38 degree heat near LM35, and again rotate the preset on the opposite direction (very slowly) until the point when the relay just switches ON (RED LED ON)
Very Thankyou Sir…… My Last question about this project is… Is this thermostat is durable? ????
No problem Asad, yes LM35 is very reliable and durable below 125 degrees C.
Sir, can i use LM3914 instead of LM3915 for your precious circuit Incubator Temperature Controller Thermostat with LED indicator.
I was very happy to see your circuit and explanation. But problem is LM3915 is dificult to find for me. I was very sorry for my broken english thank alot.
Thank you Patea, yes you can use LM3914 in place of LM3915.
A pleasant day sir.
I had a question about the incubator using IC LM35 on post.
I am done wiring it but it doesn’t turn off & on the bulb.
I follow the circuit you’ve posted.
I am just worried it doesn’t turn off.
Thank you in advance! 🙂
Hi Jonathan, it will surely turn ON and OFF as required, but before that you will have to check and do some precise adjustments. Please tell me what is the voltage range that you are getting across the “out” and “ground” pin of LM35 at normal temperature, and when the temperature is increased to the threshold level? I’ll try to troubleshoot.
please sir, what will happen if the circuit can not trip but functioning. and what component will cause that please, am using the second circuit sir. thank you
the BC547 will burn, and the lamp will never switch OFF, you can add a timer based function in that case
Hi swag, am Michael an electrician from Kenya and follower of your website. Ave built the simple incubator circuit using BC 547 without opto coupler and I politely ask you to guide me on how to set up the output of op amp to trigger relays OFF/ON at my desired temperature
Hi Michael,
for easy results, remove R4 completely so that pin3 remains connected only with R3. Remove P1 also.
Connect an LED in series with R2 to indicate the temperature change.
Now switch ON and check the response. As soon as the LED begins illuminating the relay must click.
Thanks
Sorry Sir,in our stores i can only see 12v 10A relay, can i use it in this circuit?
check its coil resistance, if it is higher than 200 ohm, it will be fine
thank you sir swag..! ill try to do that.. but my multitester is defective so i cant get accurate reading specially for ohms..for now i cant afford to buy a digital one..maybe sir ill try to look for presets at stores and use different names like trimmer or trimpot.. im not sure sir if their just the same. and if i found presets will it stabilize the thermostat?
rhamram
Hi rhamram, yes a good quality preset will be more accurate than a pot, and especially if it is glued with an acrabond kind of adhesive after setting it up.
sir swag,
good day! thank you for this very useful circuit. im done making mine and enjoying it now. but this past few days, i’ve noticed that the circuit became unstable with temperature ranging from 34-44 degrees so i need to make adjustments every 10 cycles i think.. but the problem is im not home all day..i think its the pot that gives the problem here. presets are very hard to find in my place which is a very small town so i used pots for the adjusters.
can i use fixed resistors instead if pots? any suggestion sir? thank you in advance!
Hi rhamram, yes it could be due to pot’s internal setting getting slightly disturbed due its sensitive nature.
you can use fixed resistors by carefully measuring the pot resistance values, and then replicating them with fixed resistors.
Thank you sir.
please sir, can i add computer fan to it. sir please i have choose this as my final project so help me and do you need to add any small hole on your incubator
Adu, you can connect a fan with this circuit, but make sure you proceed with proper understanding and steps, because this circuit will need some critical setting up procedures…
gud day sir!! i really want to build your circuit but 400 ohms relay is not available..can i use 320 ohms instead? tnx alot!!
Hi Rhamram, you can use a 320 ohm relay
thank you so much sir swagatam!!!:)
you are most welcome!
Hi Swagatam,
I´ve built this circuit based on the second schematic, and I´m having some problems setting the temp trip point. After re-reading your explanation I realized that there is no D5 in my circuit. Is it missing from the second schematic or not necessary?
Thanks,
Dan
Hi Dan, D5 provides a reference level for T1, they both interact with one another and decide the collector voltage of T1.
but I thought that since 7812 is already there, the T1 preset would be enough to provide the reference level for the collector, and therefore removed D5…you can try putting it back or you can also try replacing the area with a 4k7 preset.
hi sir im confused because how can check that we adjust 8 hour or 9 hour etc kindly reply me thanks
Mohammad, which circuit are you referring to? The above design has no timer circuit in it??
Please tell me If I can Use a small coli heater instead of the lamb in this circuit?
I am aiming to get heat in the range of 45 deg. to 50 deg in my small Incubator.
and if possible, please provide me the coli type.
And im really sorry for bothering you,
I need more information on how I can do my small project.
thanks..
you can use any kind of heater you like instead of the lamp.
you coil power will depend on the area of the chamber.
both are working, you can try any of the two…..
And is the diagram working sir? T.y
You help a lot sir . what diagram is better one the first or second? If I use second what are the part change?
thank you sir for your help……can I make this circuit cut of at 38C and start at 36C (I want sensitive thermostat
yes you can set it at any desired point within 100 degree range, the inclusion of the opamp makes sure that the cut-off is sharp and accurate
sir which is better bc547 or 2n3904 or 2n3906 to use as a sensor ????….thank you very much for all circuit…
اوس النعيمي
any of those will do, but BC547 is the recommended one.
2N3906 will not work because it is PNP
thank you for your help……can i make it cut at 39C and work at 35C???
Sir bc547 can I place nearby lamp?
Or other places
Dinesh, the BC547 needs to be placed near the heat source for the detection.
Sir can I use 12v ,1A transformer?
yes you can use it
adjust the given presets to trigger the relay at 40 degrees that's all, I have already explained the procedures elaborately in the earlier comments
LM35 will not work in the above set up, the configuration will need to be changed for that…BC547 is used as a heat sensor here
Please, concerning the buzzing sound, which of the transistors are you referring to??
Hello sir, is the preset resistor 10k or 100k.
Hai Swagatam,
I have few queries could you please explain
1.how to set the minimum and maximum temperature of the circuit.
2.can i use 24vdc as input voltage for incubator Thermostat Circuit (cause in input side we have used a 7812 IC on that additionally 0.33micro farad capacitor as input and 0.1 micro farad capacitor as output side).
3.In relay you have connected 2 pin is input side and output side also connected 2 pin only one pin is remaining in o/p side,can you please explain that relay connection.
4.Transistor Bc547 Emitter terminal line is ground connection am i right.
Hi Udhayakumar,
the above circuit will switch ON/OFF sharply within 2 degrees range, meaning if it's set for tripping at 50C then it will keep toggling ON/OFF within the range of 50C and 52C, for setting the range apart you may have to include a resistor across pin2 and pin6 of the opamp, as explained in the previous comment.
24V will do if 7812 is employed in the circuit.
in the relay the blue box ends correspond to the relay coil, while the unused contact represents N/O
BC547 emitter is connected to ground or the negative line.
Hi Swagatam,
Thanks swagatam for your valuable comments also i am need your help please help me on this,
I have tried the second circuit(without opto LED/LDR compo),on that am used a 24vdc as input to the Ic 7812 circuit used 12v and my load is 24v dc.
Now switch on the input and checked with the multimeter across input of IC 7812(+) and relay centre pin(-) am getting 24v, also heated the BC 547 more than 60degree but cut-off function not working.
at the same time check the voltage with respect input of IC 7812(+) and circuit ground as(-) am get the zero voltage of load, i don't know where is the mistake please help me on this.
Hi udhayakumar,
It will be difficult for me to explain the same procedures again and again to each member individually.
please go through the above comments to exactly understand how the circuit needs to be handled.
unless you thoroughly understand how an opamp works and how the temperature indicator stage needs to be integrated with the opamp circuit you would find succeeding with this design extremely difficult.
Hello Sir Swagatam , i have some doubts in this design
for my project
1. i want to control the temperature cutoff at 75 celsius and on the voltage at 45 degree celsius . how i can adjust the cutoff and on temperature
2. i want maximum temperature at 75 degree celsius for that which resistor i want to change and what range i want change the resistor and same as for minimum temperature as 45 degree celsius
Hello Guru, please see the previous comment, I have answered your question already.
Hello Sir Swagatam , i have some doubts in this design
for my project
1. i want to control the temperature cutoff at 75 celsius and on the voltage at 45 degree celsius . how i can adjust the cutoff and on temperature
2. i want maximum temperature at 75 degree celsius for that which resistor i want to change and what range i want change the resistor and same as for minimum temperature as 45 degree celsius
Hello Unknown,
the 75 degrees can be set by the P1 preset, and for setting the 45 degrees, you will need to connect a 220K preset across pin6 and pin2 (hysteresis control, this preset can be used for adjusting the 45 degrees restoration.
or alternatively you can use another opamp with its PIN#2 connected with pin3 of the existing opamp, and PIN#3 configured with a separate preset but attached to the same points as the existing opamp preset pin2.
the output of this opamp then can be connected with the base of the transistor for the cut off action, with its PIN#3 preset adjusted for cutting off at 45C.
thank u for your reply
i have some query about your reply
1. how to set p1 as 75 degree . when we set the preset value of the resistor before or after the power supply given.
2. if we use 220k preset for setting 45 degree then if we want to set our minimum temperature as 35 degree then which resistor value we want to use. Is there any special formal for setting resistor preset
Actually I have already explained the procedures in the earlier comments, I'll repeat it briefly for you.
initially do not insert the LED with the LDR.
heat the BC547 at 75 C and adjust VR1 until the LED illuminates jut moderately, once VR1 is set now you can seal this LED with the opamp LDR.
after this repeat the heating procedure and now adjust P1 until you find the relay just clicking…seal P1 now…the circuit is now set for 75 C.
repeat the procedure to confirm the activation threshold.
do this without connecting the 220K preset.
first confirm this result, afterwards we can go ahead with the 220k integration.
Sir Swagatam, Thank you so much for your help, your replies were very helpful. This is an awesome website, Excellent work sir.
Thanks Christian, The pleasure is all mine!
Sir Swagatam, Thank You so much for your continuous help, I wrote the details of the point where the relay clicks when the sensor is being heated inside the incubator, but I'm curious at some point, for example if the sensor is heated and the relay clicks at 7v so the moment that the voltage at pin2 increases up to 7V the heat source will turn off, and it slowly cools the sensor which makes the voltage at pin 2 dropping, so the moment that it drops the voltage below 7volts the heat source will again turn on, This will make the desired temperature disturbed, is there a way that the heat source will just turn on again when the voltage at pin2 reaches the initial point? If the sensor is being heated I can notice easily the change of voltage at pin 2 but when the time of cooling comes, it takes too long for the heat source to turn on again, By the way the relay creates a sound like buzzing and the heat source starts to dim continuously before it turns on/off. What should I do, Is this normal?
Chritian, leave it on the sensor, because he sensor will switch ON the load only when it cools down itself at the earlier point or when the ambient temperature goes below the set temperature by 2 to 3 degrees, that is what the sensor is supposed to do and it will do this correctly.
In order to force the BC547 to cool quickly you can attach a small aluminum strip over it, so this might help to heat it faster and cool it faster…
connect a 100uF/25V capacitor right across the relay coil to prevent its buzzing at the thresholds
I'll definitely do that Sir Swagatam, uhmm Relay Coil do you mean to the rails of the N/C and the Central Common Terminal? or to the rails of the pins who went to the collector and the ground? And which rail should I put the positive and negative of the 100uf/25 capacitor?
connect the capacitor between collector and ground of the T2, or in parallel with D6
positive to collector, and negative with ground
alternatively you can connect a 10uF/25V capacitor across base emitter of T2 for getting the same results
….positive to emitter and negative to base
Hi Sir Swagatam, I want to ask if what I did was correct, I put a 10k resistor in series with the LDR and P1 and 100k POT namely the "Rf" to the rail of pin 2 and pin 6, I saw in the book that the Inverting op amp has a resistor and Rf for the voltage output at pin 6 so I thought that maybe I could try to calculate and put a resistor there for the output voltage to drop, when I tweaked the POT namely the "Rf", the voltage at pin 2 also changes, but as I tweak it again the relay did click and the heat source turned off, So I tried to learn the adjustments, however I'm having trouble with the variable resistors, what I did was, I tried to adjust the P1=100k and it gives me a change in voltage at pin 2 like how the "Rf" does, the only difference between them was if I tweak the "Rf" theres a bit of a change at the output voltage at pin 6, so I set up a fix point of P1, and focused on the "Rf", I wrote every details of what I observed, if I tweak the "Rf" and the voltage at pin 2 increases, the voltage at pin 6 drops and vice versa, so when I tried to find the point where the relay clicks, for example when the output voltage at pin 2 increases up to 7V and the output voltage at pin 6 drops from 12v to 10v the relay clicks and the heat source turns off. So when I found the point where the relay clicks at 7V I adjusted the "Rf" slightly down to turn on the heat source like about 6.5V, but when I introduced the controlled heat to the Sensor, the voltage at pin 2 increases, but when it reaches the 7V where I assumed that the heat source should turn off, it sadly didn't, so in other words the relay clicks when I adjust the "Rf" to 7V, but when I let the sensor do it on its own to reach the voltage at 7V, the relay won't click, please tell me that I didn't ruin the entire circuit.
Hi Christian, all these are not required.
you are unnecessarily making a simple concept too complex.
previously you said that pin2 voltage was rising above pin3 in response to heat…so that is correct.
but if the above response is not making pn6 low then the IC is faulty ….I also told to connect an LEd in series with base of the transistor for getting an indication…may be you did not do that as well.
you can refer to the following article to learn how an opamp works like a comparator:
http://www.technologystudent.com/elec1/opamp3.htm
Sir thanks for this project
I have followed all the steps you gave carefully but i am still having problems with setting of the thresholds
When I connect red LED in series with R2 the relay doesn't on/off
What can be the problem
Patrick, if you have followed everything correctly then it should have worked.
everything's pretty straightforward.
Initially do not seal the LED LDR.
first set P1 such that the LED just lights up at the preferred heat (below 100 degree).
once the optimal glow is achieved you need to seal P1 with some glue.
Next seal the LED with the LDR carefully inside a lightproof box.
After this just do stepwise as suggested to Mr. Christian in the above comments.
correction:
first set VR1 such that the LED just lights up at the preferred heat (below 100 degree).
……once the optimal glow is achieved you need to seal VR1 with some glue.
Thank you for your responses
sir which of the circuit is advisable to be build
the first diagram or the second diagram
thank you.
both are good, but the first one allows you to set the heat level by looking at the LED glow….but it involves the hassle of making the LED/LDR assembly.
for newcomers I recommend the first one but the LDR/LED sealing is crucial.
sir I want to find out must the whole unit
be inside the incubator box or
only the bc547 should be in the box?
thank you
preferably only the BC547 should be near the heat source rest of the circuit should be positioned in the normal ambient atmosphere.
Hi Sir Swagatam, I've got another problem, since there's no regulator, the voltage at pin 3 goes up to 7 to 7.2 voltage instead of 6 due to the Voltage Divider so I tried making the voltage at pin 2 slightly near below the voltage at pin 3 at around 6.8 volts hoping for the op amp output to be low and for the relay to operate.
As I use the multimeter, when I introduced the controlled heat to the sensor BC547, The voltage at pin 2 unexpectedly increases instead of dropping, what causes the increasing of voltage at pin 2 as I introduce the heat to the sensor?
Hi Christian, replace R4 with a 6V zener diode, that will take care of the unstable reference at pin3.
I am sorry I told you the opposite by mistake….pin2 should witness a rise in voltage as soon as heat is introduced near the sensor.
that means your circuit is working perfectly as per the expectations.
so the moment pin2 voltage goes above pin3, the relay is supposed to switch ON (pin6 should go low)….you just need to confirm this now…
Okay so I removed the R4 and replaced it with a 6V zener diode, now the Voltage at pin 3 is now stable at 6 volts, I set the voltage at pin 2 slightly near below 6 volts, I did set the voltage by adjusting the P1. When I set a LED glow I didn't touch the VR1 anymore, I just set the voltage at pin 2 by adjusting the P1, however, when I introduced the heat to the sensor, The voltage at pin 2 increases but as soon as I checked the voltage at pin 6 which is the output of the op amp, The Voltage was at 15 volts and doesn't show even just a slight dropping of voltage, considering the 15 volts as 12 volts if its regulated, I can't figure out the problem so please tell me my mistake.
touch and remove the pin2 with the positive rail manually and simultaneous check the pin6 voltage it should switch from 0 to 12V/15V each time this is done…if this not happening then your IC may have gone faulty.
Excellent work sir. I want to set the temp at 100 degree F(37 degree celsius),then what will be the vallue of p1?
thanks Roshan, the value of P1 will remain the same for all temps between 0 to 100 degrees
Sir Swagatam, did you mean that when I remove the pin 2 along with the positive rail manually, the pin 6 voltage should switch from 12/15v to 0? I tried to do it, and you're right sir, I think the IC may have really gone faulty, When I removed the pin 2 along with the positive rail, the voltage at pin 6 still remains at 12V/15V. So I replaced the IC with a new one and tried it again but still the problem remains the same, However, As I checked the voltages. I discovered a new problem and maybe its the real problem that causes the Relay not to operate. When I checked the voltages of the pins that were not included in the circuit, The voltage at pin 5 remains at 0, the voltage at pin 8 is steady at 14V, and the Voltage at pin 1 goes to 13V, the interesting part is when I introduced the heat to the sensor I simultaneously checked the voltages. The voltage at pin 2 increases but the moment that the voltage at pin 2 goes above pin 3, the voltage at pin 1 suddenly goes to 0, but when the voltage at pin 2 goes back below the voltage at pin 3 the voltage at pin 1 goes back also to 13V the others voltages remains the same, The Pin 6 should be the one doing this not the pin 1.
I really need your help sir, I'm just a student trying to finish this circuit as my project in Electronics.
Christian, I meant to say that without disturbing any connections just short circuit pin2 with the positive rail, this should instantly turn pin6 from 12V to 0V, and on removing the situation at pin6 should revert from 0 back to 12V.
The other pinouts of the 741 IC are irrelevant and should not be considered, only pun3/2/6/7 and pin4 are the ones that are used here, the rest must be ignored.
Pin6 is the one that must change its response to the pin2 pin3 voltage differences, if this is not happening there could be something seriously missing or wrong n your IC connection.
just verify the above accordingly. Connect an LED in series with the base of the transistor to get an instant indication regarding the pin6 response…LED anode should be connected to the base, and the cathode to the resistor junction.
Sir can u please tell me how to connect the relay it got a total of 5 pin, (2 and 3 on opposite sides).And what spdt signifies.
Sir, I designed and built everything using the first circuit, I even followed how the assembly of the Led or Ldr should be, when you say sealed is there a proper way for the Led and Ldr to be permanently stick with each other? When I adjust the VR 200ohms, the glow in the Led also changes. I don't think that the Relay was even turned on because when I tried to put the BC547 near the heat source, still nothing has changed, It doesn't turn off. When I touch the IC it does produce heat, but not even a single reaction from the relay, What might be the problem? Is it the wattage in the resistors? I just used a 0.25 watts resistors. Or is it the P1? Im a little bit confused about that, because when I bought the variable resistors the 200ohms Variable resistor is a little blue and white preset with a number indicated 202, and when I looked at the P1 100k it is the same little blue and white preset but the number indicated is 104, so I was thinking if it was just 100ohms, and not 100k ohms, its confusing because there is no name indicated unlike the pot. What might be the problem that the heat source doesn't turn off.
Christian, I told you to first set the LED glow at the preferred heat level and after that you need to seal it, by sealing it means that the assembly should be protected from the ambient light…this is clearly mentioned in the article…did you follow this??
Once you set and seal the LED/LDR in a lightproof enclosure VR1 must NOT be touched anymore, otherwise the LED glow (temp setting) will get disturbed and you will get wrong results.
The relay will operate when the opamp output goes low, and this in turn will happen only when its pin2 voltage gets slightly lower than its pin3.
after integrating the LED/LDR assembly to pin2 of the opamp, introduce the controlled heat to the sensor BC547 and simultaneously check the voltage at pin2, you will find it dropping and stabilizing at some point, now adjust the pin2 preset such that this voltage is still reduced slightly below pin3 voltage…which will immediately cause the relay to click.
If this
to confirm the preset value you can use an DMM and measure the resistance from its end to end leads….it must show a 100k value or whatever may be its value.
Sir iam Sonal can u please tell me how to connect the relay in this circuit i got the one with a total of 5 pins and what did spdt signifies.
the blue box is the coil of the relay….you can refer to the following article for knowing the details:
https://www.homemade-circuits.com/2012/01/how-to-understand-and-use-relay-in.html
Hi Sir iam Rishabh,can you please tell me where is spdt is used in this circuit bcuse it is in part list.
SPDT is referred to the relay contacts specs. it means a relay with a single pole and a pair of N/C, N/O contacts.
My comment was posted twice, I'm new to blogs, I didn't know that the first one was published. Anyway thank you, I'll make sure to keep that in mind. I'll design a new one using the first circuit where the D5 and the T1 interact with each other as the sensor.
Hi sir! Im trying to do the the simpler version of this circuit. The one that doesn't need the OPTO coupler. However I'm having trouble knowing the use of the Variable Resistors. You said that the P1 and the VR1 are both presets. But my teacher said that we should use the P1 as a Rotatory Potentiometer. So I bought a 100k Potentiometer and used that as the P1 and a 200 ohms preset as the VR1. Is there going to be a problem in the circuit? Or is it just the same? However we designed and applied the simpler version using the P1 as the potentio meter and the VR1 as the preset it turned out that the Heat source doesn't turn off.
Hi sir! Im trying to make the simpler version of this circuit. The one that doesn't need the OPTO coupler. However I'm having trouble at the Variable Resistors, you said that the P1 and the VR1 are both presets but my teacher said that we should make the P1 as the Rotatory Potentiometer. So I bought a Potentiometer 100k as the P1 and 200ohms as the VR1. Is there a problem that might occur in the circuit? Or is it all the same? However We tried to design the simpler version that we considered the P1 as a potentiometer and the VR1 as the preset. And the source heat doesn't turn off.
P1 should be a preset because a pot can be too sensitive and cannot be held tightly in a set position, this can make the circuit unstable.
The simpler version is not practically verified and might need some practical measurements and adjustments for getting proper results. and remember while testing if the BC547 is heated too much it might get damaged permanently, therefore things could be slightly difficult with the simpler version unless you exactly know how to proceed, so I would recommend you to go for the first circuit and build it as it's shown, because this circuit has the facility of an LED lamp which gives a direct indication of the BC547 response to heat.
Therefore it becomes possible to first fix the amount of glow on the LED by correctly adjusting VR1 at the specified heat level and after that it can be sealed with an LDR for the relay activation.
…in the simpler version the relay is supposed to be switched ON initially without heat application,
when heat is applied and it crosses above the required threshold, the pin2 voltage is supposed to go just below pin3 to cause the relay to just switch OFF…
the above will strictly depend on the precise setting of P1 at the specified heat threshold which should not be above 90 degree C max
no, it's not recommended for this application
Can i use adaptor transformerless?
Please help
Sir I need help on how to construct a DC thermostat with LCD display , which can equally trigger on a fan at 50degree centigrade ….. Pls this is my project … I need urgent help … Any link or help will be highly appreciated …
Ekenekk@gmail.com
Hi Ekene, I'll try to publish it soon, do keep in touch.
Sir … I really need help on how to construct a DC thermostat with LCD display ….. With can trigger on a fan at 50centigrade only … .. Any link or help will be appreciated
Ekenekk@gmail.com
can u give me info..about 12v dc motor
12v DC works on 12V DC power
Good day Sir Swagatam, i will be making this projet and i will base on your circuit as a reference =) I only have samome basic concepts questions.
What will happen to the Light (heater) if the heat goes up in the sensor? Will it dim or will it turn off?
Which pots are assigned to set the temperatures from 0-120? Can it be made in a way that it that if (assuming) i set the min temperature to 20 degrees it will light up and shine brighter if lower temperatures are achieved? And 35 degrees it will dim?
Or i got it all wrong? Hehehe sorry for asking a lot of question. I'm kinda new to these.
Good day Lloyd, the heater will shut off for a moment if the heat exceeds above the set high threshold, and will switch ON back as the temperature falls below the lower threshold.
The setting up adjustments could be done in the following manner:
connect a RED LED in series with R2, and adjust VR1 until this LED begins glowing at the required high temperature from the heater (not to exceed 100 degrees C), ignore the relay response during this setting.
the heater should not be connected through the relay rather directly through a manual switch
Now once the above position is reached, carefully adjust P1 so that the relay just deactivates, if it's already in a deactivated position, force it to activate by adjusting P1 and immediately adjust it back to deactivate it, all these must be while the red LED is still glowing bright.
your setting up procedure is complete now, connect the heater via the relay contacts as shown in the diagram, check and enjoy the automatic response as per the above settings.
…for a dimming and brightening type of response you may refer to the following design:
https://www.homemade-circuits.com/2013/01/automatic-temperatureclimate-controlled.html
Hi Sir, I don't know if my comment have been published. But just to be sure, i want to thank you again and i appreciate it very much for replying to my questions!
I cannot find any way to private message you so i will put my request here to you..
I changed my mind, instead i wanna make a 12v dc temperature controlled fan.
I want it to make as such, it will turn on at 20 degrees and it will turn off below 20 degrees. If it reaches 20 degrees above, the speed of the fan will go faster aswell. The heat source will be the surrounding. And can we possibly add a LED, that will glow brighter aswell? I need as an example of a closed loop feedback control system. Please..
Thank you again sir! I'll wait for your reply. Regards! (my gmail is here : rreddmallari@gmail.com)
Hi Lloyd, you can try the following circuit:
1.bp.blogspot.com/-YmlmSYSqUTU/U7UWfVEzlHI/AAAAAAAAHcc/E6Uh_aI7rpA/s1600/solar+ater+heater+regulator+for+drip+irrigation.png
Replace the heater with the fan, and the 9v supply with 12V
Connect a red LED in series with the base of the transistor for the indications.
Adjust P1 precisely so that the fan triggers at 20 degrees approximately.
Can 230VAC/350watts rated heating element be made to run on dc power. If yes how will the configuration of the circuit look like. For instance using a 12v step down transformer.
You will need a 400 watt DC to AC inverter to operate the 350 watt load through a 12V battery. The transformer current will need to be 33 amps.
Ok thanks. But it was thinking of running it direct with 12v dc power supply not by inversion possibly with a transformer of up to 33amps since the heating element load is resistive load. I was thinking it should be independent of the type of supply (whether dc or ac). So I thought what is most important there is the power rating of the element. Is it not really possible that way.
Yes, AC or DC dose not matter but voltage matters. For 220V element the voltage has to be 220V AC or DC.
Ok thanks
in fig 2 R1 isnt grounded ……. am i ri8???
no, it's correctly shown in the diagram, R1 and the pot form a potential divider for the transistor base
….yes it should not be grounded
sir, i have a temperature controller built-in-type, in its user guide denote that use a snubber circuit for long life of relay of temperature controller, how can select the values of resistor and capacitor which involved in snubber circuit? i'm waiting for your suggestion….
Khalid, that'll depend on many factors, you'll need to calculate it through an online snubber calculator software.
tanx a lot sir for the quick reply,,, maybe i can try the adjustment by next week coz i am out of town right now….i will follow the adjustment you say and update here the result ,,,
OK!
hello sir swagatam, i already made the simplified version of your design, but it wont turn off the heat source ,,, if i adjust the vr1 manually, it will initialize turn on/off the relay but it wont turn off/on automatically to my desired temp, will you email me the step by step procedure in setting up my desired temp, cut-off,, tanx in advance
hello Oliver, i am sorry it's not that easy.
you can include an LED immediately after R2 and in series with it.
Allow the transistor BC547 to heat up to around 70 degrees, and adjust VR1 to just make the LED glow.
At this point you can try adjusting P1 for the required switching of the relay, or if it's already switched ON adjust P1 to just switch it OFF and then readjust to just switch it ON back.
The circuit is set now and will repeat the actions every time the temp reaches the set threshold
I hope you got it.
how many eggs would the box contain to do the process 😀
will depend on the size of the heat source.
hie bro the infrared light a 250watt rating and what is the most desired heat source
It will depend on the egg hatching specifications, you can get the information online regarding the right temperature required for hatching eggs. Then you can adjust the above circuit for maintaining the particular temperature range, throughout.
l want to use any area of 5m by 1.5m so is one infrared light ok as a heat source
thanks bro you are helping so much .is it proper to use one heat source for a 5m by 1.5m area and the heat source is an infrared light
I have neve rused an IR light for heating purpose, how much heat does it produce?
ok bro so for one individual circuit what is the capacity then how many eggs per circuit are we looking at
It will depend on the area used, and the wattage of the heat source, it can be dimensioned to any desired range as per requirements.
HIE SIR THANKS BUT MY QUESTION IS TO WHAT CAPACITY DOES THIS CIRCUIT HOLD IN TERMS OF NUMBER OF EGGS IN THE INCUBATOR AND HOW LONG DOES IT TAKE TO HATCH
Hi Ngoni,
It will depend on how many heat sources you are using, for each heat source you will have to incorporate an individual circuit.
Hatching period is not known to me.
Hey sir..
I was the one who said 8/10 egg's
hatched, please read that
comment again before answering
this.
i did 4 boards with the modified
circuit with the following
modifications
1. gave LED in series with 10k.
2.hyst 100k preset in series with
10k resister.
3. A capacitor across base and
positive.
Done everything as yu said.
Still problem is'nt solved, all
boards giving same problem.
It works good and fine first day
(completely accurate), but after a
day the temp on/off range
changes again.
Sometimes it never turns OFF or
ON, couldn't findout what is the
prob.
i think the room temperature
again affecting its behaviour.
Hi Rithesh,
Remove the 100k hyst preset link, we do not need it at all because the heat will never rise or fall quickly, so a hysteresis feature is not required.
Did you try the last circuit as given in the above article??
Make it exactly as it's given…don't forget to use a 7812 IC with the circuit.
Use good quality preset for both VR1 and P1.
Make the above mods, it will work.
With 1N4148 removed room temperature will not affect the circuit in anyway.
In future you could think of replacing VR1, P1 with fixed resistors.
Please are the D5 and D6 diodes some heat censors?
D5 and T1 are the sensors….T1 is the main sensor which needs to be kept near the heat source to be measured.
to the pin4 rail of IC741
It basically depends on Ub (supply voltage), R1 and R2.
R1 and R2 may be selected with the following formulas:
R1 = (Ub – 0.6)/5 (kohms)
R2 = (Ub – 1.5)/15 (kohns)
these are the only computations available.
you can use soldering iron to heat the transistor…but be careful not to overheat BC547
Connect an LED in between R2 and collector of BC547…..keep pin2 of 741 disconnected with R2.
Switch ON power and heat BC547 slightly at about 60 degree and adjust VR1 such that the LED starts glowing dimly…that's all your circuit is set.
Now connect pin2 of 741 back in position, repeat the procedure and adjust P1 to activate relay at any desired temperature within 110 degree.
pin4 line of 741 is the ground
….correction: for second diagram VR1 = 1k, P1 = 100k
for second diagram P1 = 1k,
BC547 is the only sensor near heat source.
keep P2 at center, set VR1 roughly to activate the relay at about 70 degree temp, after this only P2 may be used for getting other desired thresholds.
altanative of bc557 transistor
if you don't get these, you won't get the other alternatives also for sure, consult the dealer, he will know better.
hi sir in my place there is no an IC 741 and 4060 what are their altenertive
altenative of 741 IC
connect one LED from pin6 to positive, another from pin6 to ground, both LEDs should have individual series 10k resistors.
one of them will indicate ON, the other one as OFF.
That's great, if you look carefully you will find that actually the 1N4148 is not required, so you can simply remove it, and make VR1 into a 1K preset. Finished, now adjust the 1K preset for the desired actions.
However in this case your power supply must be regulated, so add a 7812 IC after the bridge for making the supply stabilized.
The blue part is the relay coil……please click the diagram to enlarge and check the details.
The BC547 is used as the heat sensor here and therefore must be kept near the heat source.
Thanks!
VR1 may be used for setting-up the cut off threshold, which must not exceed 110 degree Celsius (max), while P1 may be used for fine tuning the set cut off point.