In this article I have explained how to design your own customized, simple LED driver circuits at home. We will learn how to calculate specific LED configurations for applying the LEDs with appropriate LED driver power supplies. In these driver power supplies I have explained two concepts one by using SMPS boards and the other by using capacitive power supplies.
What is an LED Driver
An LED driver is an electronic circuit specially designed to drive or illuminate a set of LEDs safely through controlled current and voltage output, as per the specifications of the LEDs.
Since LEDs are vulnerable semiconductors devices, they must be driven using a regulated current and voltage power supply. Thus, we can also say that LED drivers are basically power supplies, specially designed to operate or illuminate LEDs through controlled parameters, so that the LEDs illuminate optimally without the risk of an over voltage or an over current.
This implies that an LED driver must feature a constant voltage and a constant current, ensuring that the LEDs are never subjected to abnormal voltage or current conditions, and they never burn or deteriorate overtime.
The biggest enemy of LED is overheating, which can cause a thermal runaway situation in LEDs. Overheating may be caused due to over current or over voltage, and this is exactly why these two parameters must be strictly regulated in any given LED driver circuit.
LED Parameters
Before we start learning LED driver circuits, it would be important to understand a few of the LED specifications which are crucial to designing drivers for them. These are, LED forward voltage rating or the VF rating, and LED forward current rating or the IF rating.
LED Forward Voltage Rating (VF): It is basically an optimal voltage rating of the LED which is supposed to be supplied by the driver or the power supply to illuminate the LED with optimal brightness. This voltage must never be increased to ensure proper safety to the LED.
LED Forward Current Rating (IF): It is the maximum operating current of the LED, exceeding which can cause a deterioration or even permanent damage to the LED.
For example a standard 1 watt LED has a forward voltage rating of 3.3 V, and a forward current of 0.303 Ampere. Exceeding the forward voltage of 3.3 V can cause an increase in the current consumption exceeding its maximum tolerable IF rating of 0.303 amps. This may result in overheating of the LED so that it ultimately burns and gets permanently damaged.
The forward current can be calculated by dividing the LED wattage by its forward voltage. For the above example, this is IF = 1 / 3.3 = 0.303 Amps
While designing an LED driver it must be ensured that it provides the LEDs with the correct amount of VF and the IF parameters, so that that the LEDs are able to illuminate optimally without any risks of damage.
Now we will see how the VF and IF parameters, as explained above, can be correctly implemented using the right LED configuration and by calculating the LED resistor correctly.
LED Configuration
While designing LED drivers the LED configuration must be correctly matched with the voltage output of the driver, such that the driver voltage is equal to the forward voltage spec of the LED configuration.
This ensures that the correct amount of forward current passes through the LEDs. However it is always not possible to match the driver output with the available LED configuration.
In case the driver output does not exactly match with the forward voltage spec of the LED then we use series current limiting resistor to adjust the voltage and current of the driver with the LED.
Example#1
For example, let's say, the output voltage of the driver is 12 V DC (with 1 Amp current), and we want to connect a 3 watt LED with this DC output. Assume we have 3nos of 1 watt LEDs with forward voltage specification of 3.3 V each.
We want the forward voltage of the LEDs to match as closely as possible with the 12 V spec of the driver.
Therefore we add the 3 LEDs in series, so that the total forward voltage of the LED string becomes 3.3 + 3.3 + 3.3 = 9.9 V. This is close to 12 V but still not precisely equal.
If we connect this 3 LED string directly with the 12 V supply of the driver, that would cause each LED to be subjected to a forward voltage of 12 / 3 = 4 V. This looks too high for each of the LEDs, and this would instantly burn the entire 3 LED string.
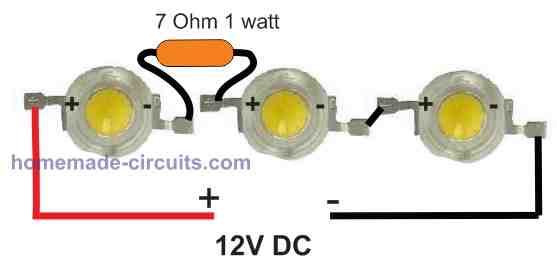
To prevent the above issue, and to ensure that the 3 LED string works correctly with the 12 V from the driver, we add a series resistor with the LED string. The resistor value is calculated by considering the total forward voltage of the LED string, the maximum current spec of the LED string, and the supply input voltage from the driver.
R = Supply Voltage - Total LED forward Voltage / LED Current.
R = 12 - 9.9 / 0.303 (All the 3 LEDs will have 0.303 amp current since they are connected in series.)
R = 6.93 Ohms or 7 Ohms.
Therefore, we would need a 7 Ohm series resistor to ensure that 12 V can be safely used with the 3 LED string.
The wattage of the resistor can be calculated using the formula:
W = (Supply Voltage - Total LED forward Voltage) x LED Current.
W = (12 - 9.9) x 0.303 = 0.63 watts, or simply a 1 watt will do.
Example#2
Let's consider another scenario where we want to configure a 6 watt LED to a 12 V, 1 Amp driver output. Assuming we have 6 nos of 1 watt LEDs, we want to make sure that the total forward voltage of the LEDs is as close as possible to the 12 V DC output.
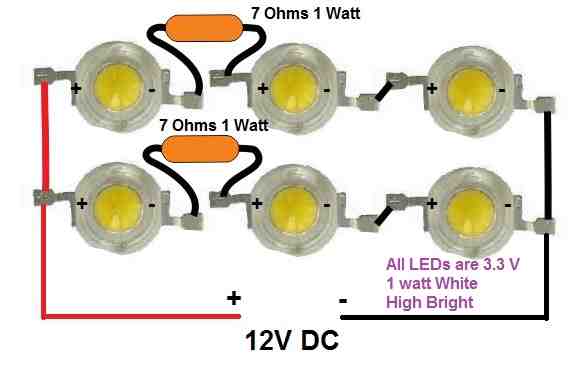
Just as the previous example, putting 3 LEDs in series provides a total forward voltage of 3.3 + 3.3 + 3.3 = 9.9 V. Since we have 6 LEDs, means we have to create two such strings having 3 series LEDs on each string.
Once the two strings are created, the next step is to calculate the current limiting resistor for the two LED strings. As calculated in the previous example, we have to connect a 7 ohm 1 watt resistor in series with each of the two LED strings, and then simply join the two LED strings in parallel.
This parallel combination then finally could be attached to the 12 V supply for getting a matching configuration with the supply.
Example#3
In the above two examples the calculations were pretty easy since the LED numbers were even. Now let's consider an LED combination which is not even.
Let's imagine we want to connect a 7 watt LED to the driver's 12 V supply.
Let's assume we have 7 nos of 1 watt LEDs for the 7 watt LED configuration.
We implement the same procedures as above.
We first create two strings of LEDs having 3nos of 1 watt LEDs each, along with a 7 ohm 1 watt series resistor on the each of the strings.
We connect the above two strings in parallel, as before.
For the above configuration we use 6 LEDs , and find that we have still have one LED left with us, which also needs to be included in the design.
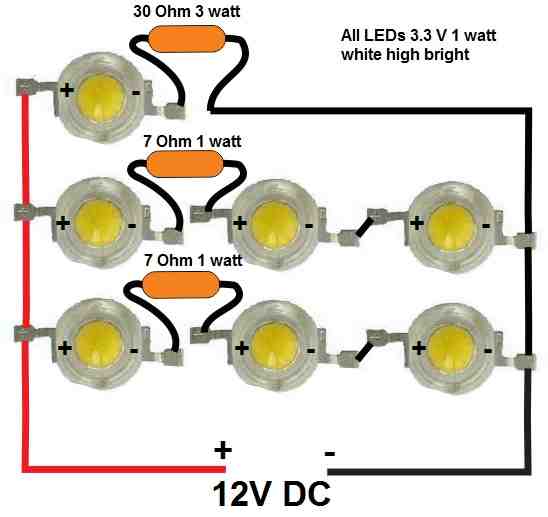
We have no other option but to connect this single LED parallel to the two strings.
However, this single LED will also need a resistor so that its 3.3 V forward voltage could be matched with the 12 V supply.
We use the same formula as above to calculate the limiting resistor for this single LED string:
R = Supply Voltage - Total LED forward Voltage / LED Current.
R = 12 - 3.3 / 0.303 = 28 .71 Ohms, or simply a 30 Ohm will do.
Wattage = 12 - 3.3 x 0.303 = 2.63 watts or simply a 3 watt will do.
Using the above methods, it is possible to configure any number of LEDs in series/parallel combination to suit any specific power supply output.
Now coming back to our LED driver subject, in this post I will elucidate two simple methods of designing LED drivers, 1) SMPS method, 2) capacitive power supply method.
Warning: Circuits I have explained below are not isolated from mains AC, and therefore are extremely dangerous to touch in the powered and open condition. You should be extremely careful while building and testing these circuits, and make sure to take the necessary safety precautions. The author cannot be held responsible for any mishap due to any negligence by the user.
SMPS LED Drivers
SMPS LED drivers are built using SMPS technology or switch mode power supply technology, which are by far the most efficient type of power supplies due to their low dissipation and reduced wastage of power.
However, designing SMPS power supplies is not easy and requires a lot of calculations, so new hobbyists can find this aspect of an SMPS undesirable, and inefficient.
Therefore it may seem that designing SMPS LED drivers can be indeed a complex affair, and most electronic enthusiasts or professionals may find this not so preferable.
That said, there is an easy workaround through which cheap and quick SMPS LED drivers could be created.
It is by procuring ready-made, cheap SMPS power supplies from the market, and then configuring an LED stage at its output, through a current control circuit.
A cheap 12 V 1 amp SMPS board example can be seen in the following image:
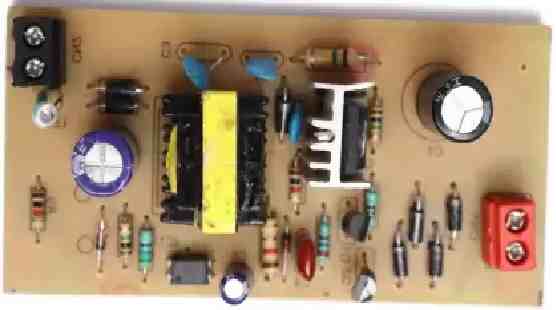
These modules will produce 12 V DC 1 amp output, with a capacity of 12 watts. We can easily attach appropriately configured LEDs strings at the output through a current controller stage for converting these SMPS boards into easy and safe LED drivers.
Why do we Need a Current Controller Stage
We need a current controller to ensure that the current to the LEDs does not increase above the tolerable limit of the LED specifications.
A current controller becomes essential only for high wattage or high current LEDs, typically for LEDs that have a current specifications of above 100 mA.
For low current LEDs below 100 mA a current controller stage may not be necessary, and the current can be controlled simply through a calculated series resistor.
You may be wondering why a current controller may be needed for high a watt LED, despite of having current limiting resistor attached in series with the LEDs?
It is because of the significant amount of heat generated by the high watt LEDs. Low wattage or low current LEDs do not emit too much heat and therefore the series resistor becomes sufficient for controlling the current.
In high watt or high current LEDs, despite of a series resistor there's a very high amount of heat generated which causes the current draw of the LED to increase proportionately. This in turn causes more heat to be generated, and more current draw.
The situation finally becomes uncontrollable causing the LED to eventually burn. This is known as thermal runaway situation, and is commonly seen in power transistors also.
A current controller stage ensures that the current draw by the LED can never increase beyond a set limit. This limit is usually the highest tolerable current specification of the LED.
Along with a current controller stage, we also need the high watt LED to be mounted over a heatsink to ensure that its temperature never becomes too high, which may otherwise cause the life of the LED to deteriorate.
Simple 6 Watt SMPS LED Driver Circuit
The following design depicts a simple 6 watt driver example using a cheap commercial SMPS board.
Simply by adding a current controller stage between the SMPS and the LEDs, we transform the SMPS circuit into a fully compatible LED driver module for the 6 watt LEDs.
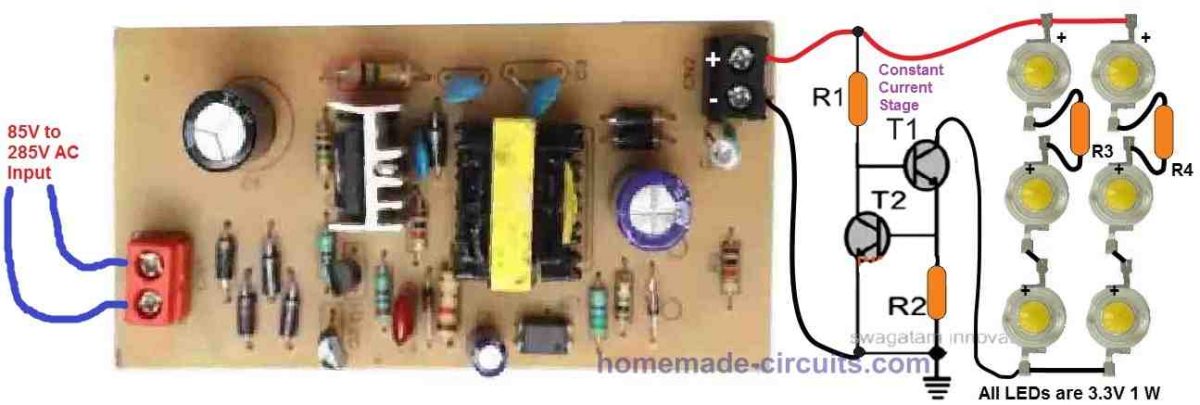
Parts List
T1 = TIP122
T2 = 2N2222
R1 can be calculated using the following formula:
R1 = (Supply Voltage - BJT forward base voltage) BJT HFe / Collector load Current
= (12 - 0.6) 1000 / (0.303 x 2) = 18811 = 18 K approximately.
So R1 = 18 K
Wattage = P = V2 / R = 122 / 18811 = 0.0076 watts. This means a 1/4 watt resistor will be sufficient.
R2 = 0.6 / Max Constant Current = 0.6 / 0.606 = 0.99 Ohms, or a 1 Ohms will work fine.
Wattage = 0.6 x Max Constant Current = 0.6 x 0.606 = 0.36 watts, or a 1/2 watt will do the job nicely.
R3, and R4 are already calculated previously in Example#2 above.
12 watt SMPS LED driver Circuit
Using the same steps a explained above, a 12 watt LED could be designed as shown in the following schematic:
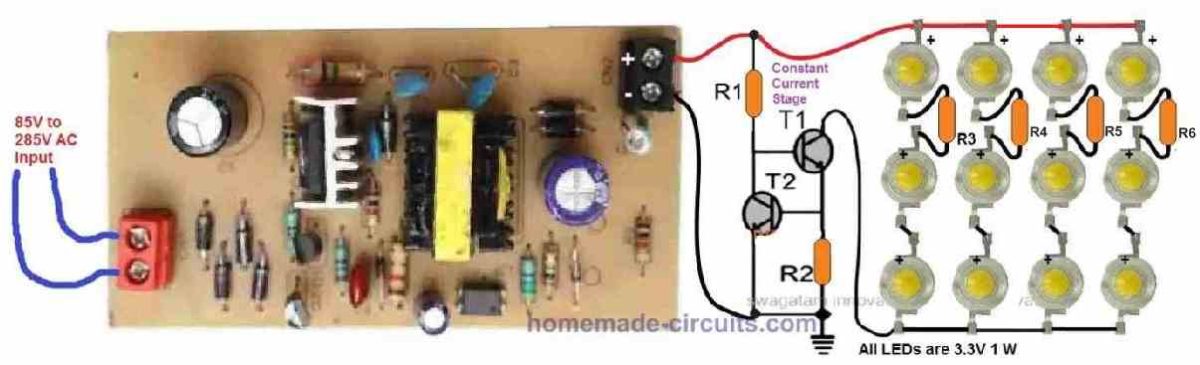
The resistors can be calculated in the same way as done for the previous 6 watt example. The current control transistors will remain the same since TIP122 can handle well above 1 amps.
Since the indicated SMPS board has a maximum specifications of 12 watts ( 12 V x 1 A), a maximum of 12 watt LED can be configured at its output. For applying higher watt LEDs the SMPS module might need to be upgraded accordingly.
The above examples shows us how any ready made standard SMPS board procured from the market can be easily converted into a full fledged working LED driver by appropriately configuring the LED circuit along with a transistorized current control stage.
However, for those who do not wish to use ready made SMPS boards, rather want to build the entire SMPS circuit discretely can follow the following links and try the designs provided therein.
2 Compact 12V 2 Amp SMPS Circuit for LED Driver
7 Watt LED Driver SMPS Circuit – Current Controlled
Make this 3.3V, 5V, 9V SMPS Circuit
32V, 3 Amp LED Driver SMPS Circuit
SMPS 50 watt LED Street Light Driver Circuit
12V, 24V, 1 Amp MOSFET SMPS Circuit
5V, 12V Buck Converter Circuit SMPS 220V
Cheapest SMPS Circuit Using MJE13005
Capacitive LED Driver
A capacitive LED driver can be built through a capacitive power supply, which is also popularly known as transformerless power supply.
It consists of a high voltage capacitor connected in series with one of the input mains terminals for limiting the current to the desired lower levels, depending on the rating and the configuration of the LEDs.
The stepped down AC is rectified using a bridge rectifier, and a filter capacitor, just as we do with any other standard AC to DC power supply circuit.
However there are a couple of serious issues with capacitive power supplies.
- Although the current is limited, the output of a capacitive power supply always produces the peak levels of the AC RMS. Meaning, if the input is 220 V AC, then the output DC from the capacitive power supply will be 310 V DC.
- Whenever capacitive power supply is switched ON, a high surge current is generated at the output which can instantly fry any LED connected at its output.
- The current from a capacitive LED driver has to be on the lower side, because higher current results in a proportionately higher surge current during power switch ON. Typically, the output current specs should be kept below 100 mA while designing capacitive LED driver circuits.
Adding Zener Diode to Control Voltage
The above two issues can be resolved by using appropriately rated zener diodes across the output of the power supply. But adding a zener also means unnecessary heat dissipation, and wastage of power.
Suppose we have an LED configuration whose total forward voltage is 24 V, then we may incorporate a zener diode to restrict the power supply output to 24 V, by using a 24 V zener diode.
However this would mean dropping the 310 V DC to 24 V DC which may result in a significant amount of power getting wasted through zener diode dissipation.
This simply means that there's no easy and efficient way to step down the output voltage from a capacitive power supply to lower levels. Therefore, it seems we do not have any other choice but to make use of the full 310 VDC from the power supply and configure the LEDs to match this 310 V DC.
To do this we first divide the 310 V with the forward voltage drop value of the LED.
310 / 3.3 = 93.93. Rounding it off gives us 94 numbers of LED for the configuration.
To allow some margin for a low voltage situation, we reduce the number to 90 LEDs approximately.
Calculating the Limiting Resistor
We use the same earlier formula for calculating the limiting resistor:
R = Supply Voltage - Total LED forward Voltage / LED Current.
R = 310 - (90 x 3.3) / 0.02 amps (Using 5 mm 20 mA LEDs for the configuration)
R = 650 Ohms
Wattage = 310 - 90 x 3.3 x 20 mA = 0.26 watts
To ensure better safety against switch ON surge currents, we can upgrade the resistor to a 1 watt wire wound resistor.
The final configuration would be like as shown in the following figure. A zener is added to guarantee increased protection against voltage fluctuations, and NTC ensures reinforced protection against switch ON surge current.
How it Works
In general, a 1uF/400V capacitor will generate 50 mA of current. So C1 here is 1uF/400V which can handle upto 50 mA load, with its 310V DC output.
Initially, the capacitor C1 is fully discharged and acts like a momentary short circuit, until it gets fully charged and stabilizes.
As soon as power is switched ON, the NTC controls the initial current surge, and after some milliseconds, the LEDs illuminate with full brightness. By this time C1 is already stabilized and the short circuit surge current is eliminated.
However, in a different scenario, if the NTC is unable to control the current surge, the zener diode switches ON at 300 V, which causes C1 to charge instantly and this stabilizes the current surge through it, safeguarding the LEDs and the zener diode.
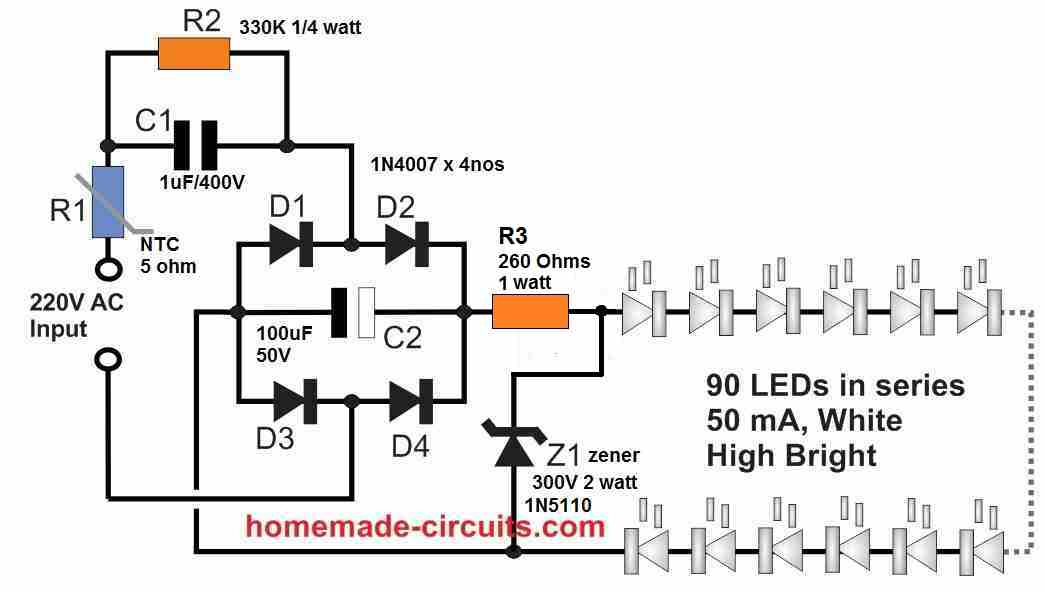
From the above discussion we understand that for capacitive LED drivers, the ideal situation would be to use an LED configuration whose total forward voltage matches the peak output DC from the power supply.
However, if efficiency is not important, then other LED configurations with much lower forward voltage can be used, with appropriate zener diodes for controlling the peak DC from the capacitive power supply.
An example design can be seen in the following figure.
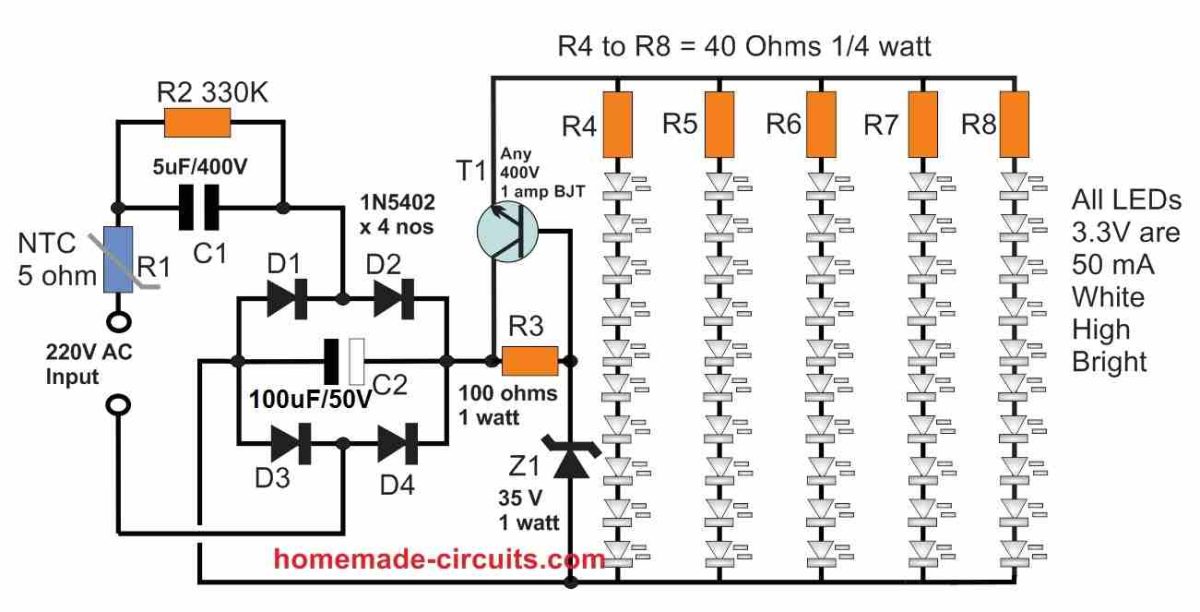
How it Works
In the above high capacitive LED driver circuit, we can see 5 parallel strings of LEDs each having 10nos of 50 mA LED hooked up in series.
This means the total consumption of the LED network is 50 x 5 = 250 ma.
As described previously, considering a 1 uF/400 V can produce 50 mA current, for getting 250 mA we will need C1 to be 5 uF/400 V.
However, a 5 uF/400V capacitor might also generate a substantial amount of switch ON current, which could easily destroy the LEDs, along with the zener diode.
Keeping this issue in mind we have introduced a transistorized voltage controller, which will keep the output voltage stabilized and in turn prevent an over current surge across the LEDs.
R3 will need to be experimented a bit to ensure that the transistor is able to deliver the required 250 mA to the LED strings.
Overall the above circuit looks good, however, it can be highly inefficient due to the high heat dissipation by the transistor.
Increasing the number of LEDs in the series strings will proportionately increase the efficiency of the circuit. However for this the series resistor, the transistor, the zener value all will need to be modified appropriately.
An Interesting way to Control Surge Current in Capacitive LED Driver Circuits
As discussed in the above paragraphs, the main issue with high current capacitive LED drivers is the switch ON surge current, which can instantly destroy the connected LEDs.
An easy way to suppress the above issue is by using a zener diode, however a zener diode being a semiconductor device itself may be prone to getting burned during a catastrophic switch ON voltage surge in a capacitive power supply.
A novel way to tackle this problem is by incorporating a mini low current relay, and switching the LEDs through the relay contacts.
This provides a couple of benefits to the overall design. First the relay coil absorbs all the initial switch ON current surge, and additionally it switches ON the LEDs with a slight delay further safeguarding from the initial surge current.
The complete schematic of the relay delay switch ON surge current protector for capacitive LED drivers can be seen in the following figure.
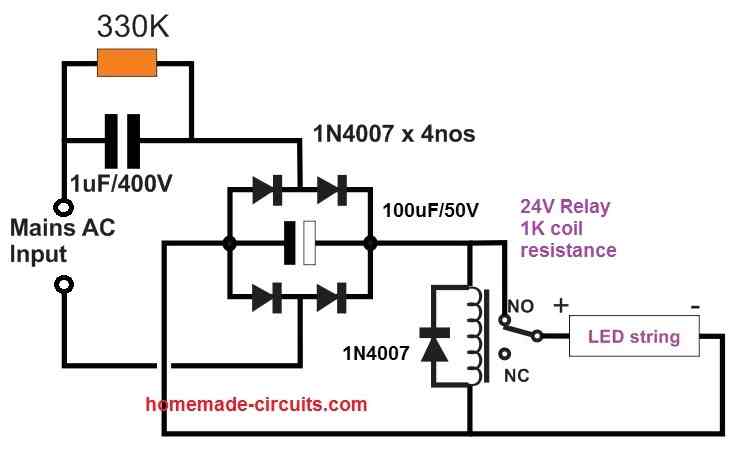
Make sure the relay is rated at a minimum of 24 V with coil resistance of 1K or higher. The 24 V mini SPDT or SPST type relays will work great in the above application.
Simple Zero Crossing Controlled Transformerless Surge Free LED Driver Circuit
As we know, even if the input capacitor is calculated optimally, switch ON current surge can become a major issue with capacitive transformerless LED driver circuits. Due to this LEDs often burn unpredictably. Although this can be eliminated using zener diode, a high current LED driver becomes possible only when a perfect zero crossing is implement, and without a zener diode.
The simple circuit diagram of a zero crossing assisted surge free transformerless LED driver is shown in the following diagram:
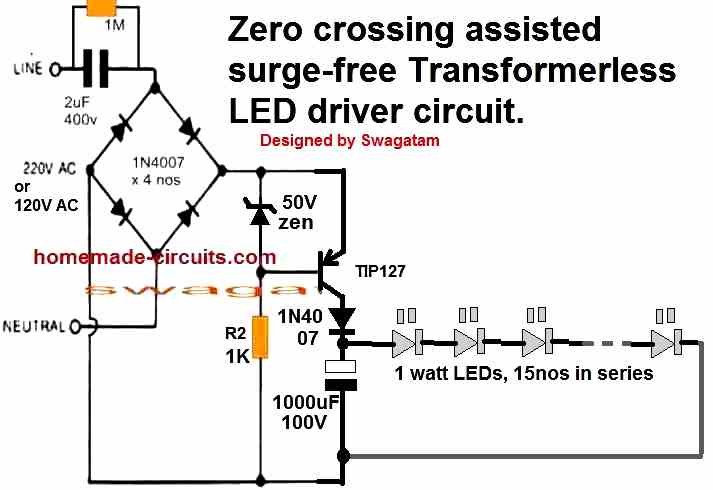
How it Works
This circuit works in the following way:
The TIP127 PNP transistor makes sure that it never turns ON as long as the AC input cycle is above 50 V.
The 50 V cut off is determined by the 50 V zener diode. You can other zener values to get any other desired output voltage, as per the number LEDs in series.
Each time the peak AC drop below 50 V, the TIP127 instantly conducts and allows the instantaneous 50 V to get stored inside the 1000uF capacitor.
This stored energy is then used to illuminate the connected LEDs safely without any concerns of an abrupt switch ON surge current burning the LEDs.
In the next rectified AC cycle, the process continues and the LEDs seem to remain illuminated continuously without being affected by any sporadic surge current issues.
Over to you
So what do you think about the above detailed description regarding simple LED driver circuits? Do you have any specific questions or any other simple LED driver design that you would like to share in this article? Please feel free to express your valuable thoughts and ideas through comments below.