In this article I will try to explain the making of a 1500 watt simple heater controller circuit at 25 amp current rate using an ordinary triac based dimmer switch circuit
Using Advanced Snubber less Triacs
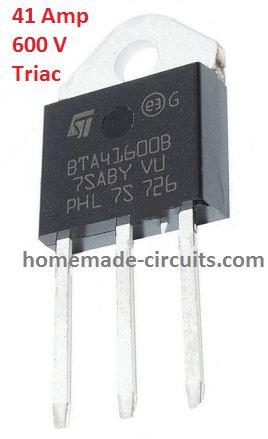
Controlling heaters rated as high as 1500 watt requires stringent specifications with the controlling unit for safe and effective implementation of the intended operations.
With the advent of advanced snubber-less Triacs and Diacs making heater controllers at massive watt levels has become relatively easier today.
Here we study a simple yet entirely suitable configuration which may be utilized for making a 1500 watts heater controller circuit.
So I have explained the given circuit diagram with the following points:
How the Triac/Diac AC Controller Works
The set up of the circuit is pretty standard as the the wiring is very similar to the ones which are normally employed in ordinary light dimmer switch circuits.
The standard triac and diac set up can be seen for implementing the basic switching of the triac.
The diac is a device which switches current across itself only after a certain specified potential difference is reached across it.
The following network resistors and capacitors associated with the diac are chosen such that they allow the diac to fire only as long as the sine curve remains below a certain voltage level.
As soon as the sine curve crosses the above specified voltage level, the diac stops conducting and the triac is switched OFF.
Since the load or the heater in this case is connected in series with the triac, the load also switches OFF and ON in accordance with the triac.
The above conduction of the triac only for a specified section of the input sine voltage curve, results in an output across the triac which has the AC chopped into smaller sections, making the overall RMS of the resultant drop to a lower value, depending upon the values of the relevant resistors and capacitors around the diac.
The pot which is shown in the figure is used for controlling the heater element which initiates the above explained procedure.
The greater the resistance, the longer it takes or the capacitor to charge and discharge whih in turn prolongs the firing of the diac/triac pair.
This prolongation keeps the triac and the load switched OFF for a longer section of the AC sine curve which results correspondingly lower average voltage to the heater, and the heater temperature remains at the cooler side.
Conversely when the pot is adjusted toward to produce a lower resistance, the capacitor charge and discharge at a faster rate making the above cycle rapid which in turn keeps the average switching period of the triac at the higher side, resulting a higher average voltage to the heater.
The heater now generates more heat due to the increased average voltage developed across it via the triac.
Circuit Diagram
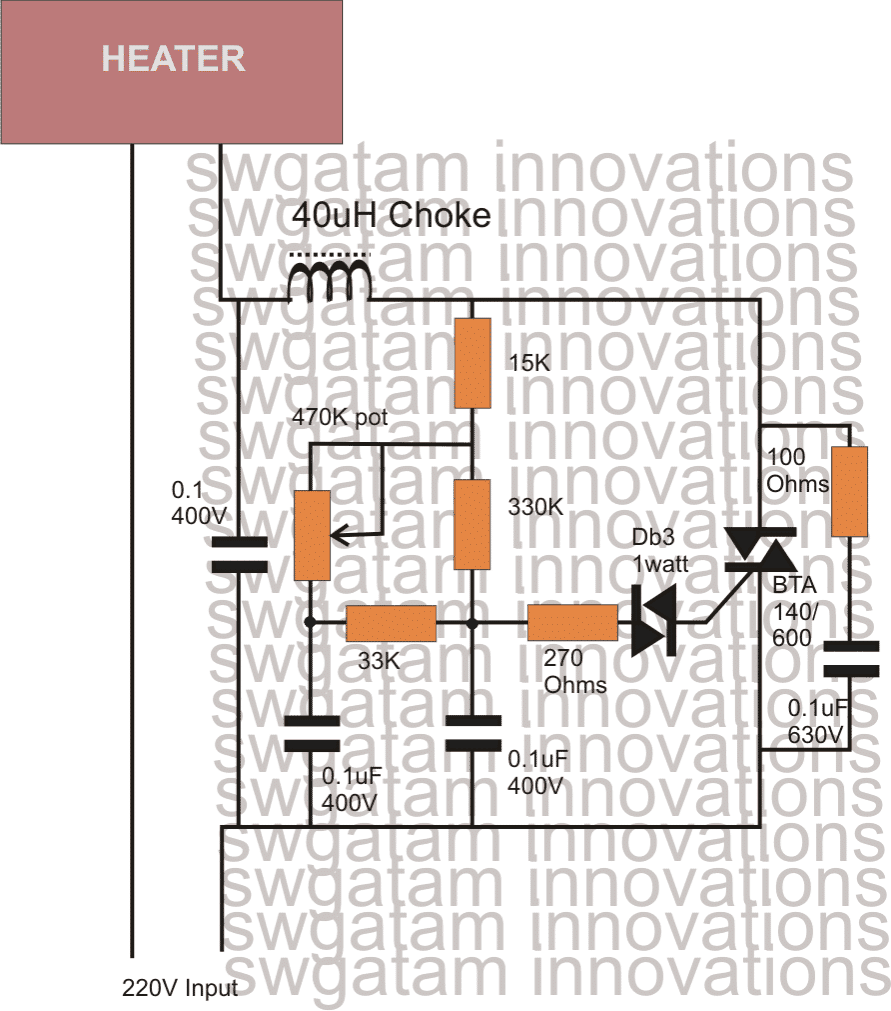
Parts List
Resistors 1/4 watt 5% CFR
- 15k = 1
- 330k = 1
- 33k = 1
- 270 ohms = 1
- 100 Ohms = 1
- Potentiometer 470k linear or 220k linear
Capacitors
- 0.1uF/250V = 2
- 0.1uF/630V = 2
Semiconductors
- DB-3 = 1
- Triac = BTA41/600
Inductor 40uH 30 amp (optional)
Controlling through Arduino Pwm
The above simple 220V dimmer switch control can be also effectively implemented using an external Arduino PWM feed through the simple method shown below:
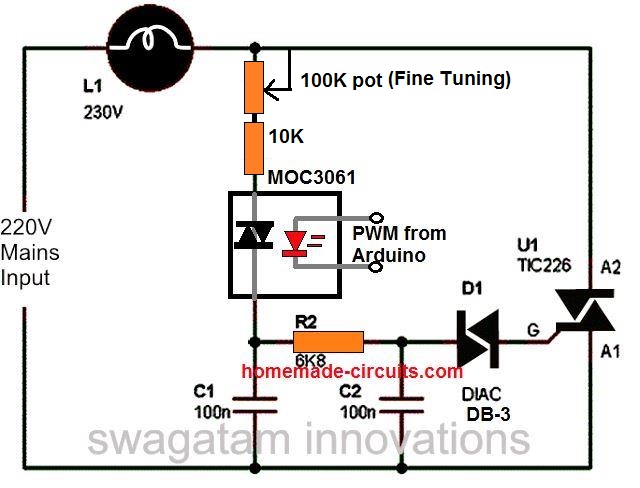
Advanced Heater Controller with Snubber and RFI Elimination
As soon as the voltage around C2 increases over approximately 30 volts (during any phase cycle), the Diac (D1) breaks over and produces a trigger pulse for the gate of the Triac (TR1).
This leads to the Triac switching ON and it applies the entire AC line voltage to the load hooked up to SO1.
Adjusting the potentiometer R2 varies the phase (timing) of the trigger pulses applied to the Triac and therefore modifies the average power level going to the heater load.

Resistor R5 along with the capacitor C3 works like a a snubber network over the Triac to safeguard it from the reverse EMF voltages spikes created by inductive loads every time the Triac is switched OFF.
Inductor L1, which is a 50 µH choke, and capacitor C4 are configured like an interference suppression filter, that enables the elimination of the RF noise commonly generated by this type of light dimmers or heater controllers.
The preset R3 adjusts the minimum starting range of the heater temperature, and helps the user to ensure that the power to the heater always starts from the minimum power when R2 is moved to the minimum position, and the heater gets maximum power when the R2 is moved to the maximum adjustment point.
PCB Design
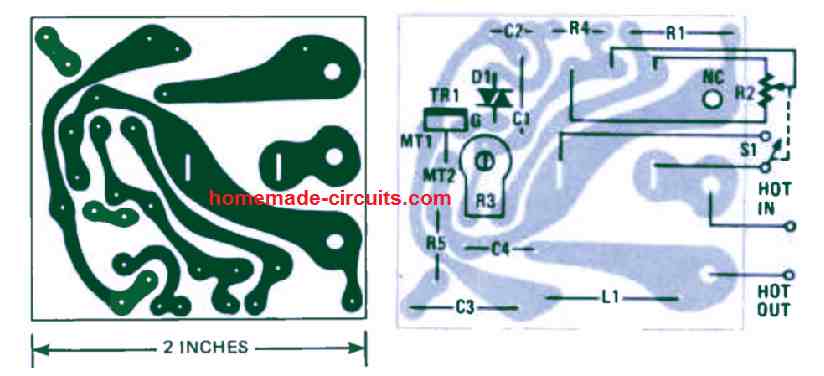
1000 watt Light Dimmer
Nearly all light dimmers that you can get from the common electrical products stores can simply manage pretty small electric power.
A few hundred watts is normally the handling capacity. The straightforward dimmer circuit demonstrated below is designed to control a power as high as 1 kW.
There is nothing much to be explained regarding the details of the circuit.
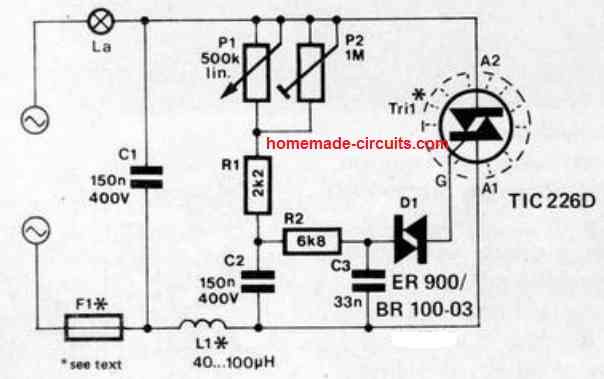
This high power light dimmer includes one triac, a single diac and an RC network where the period of the charging and discharging of capacitor C2 could be fixed using potentiometer P1.
Noise disturbances and transients are kept under control through capacitor C1 and the inductor L1.
How to Set up
Setting up of the circuit requires adjusting the pot P1 so that it reaches its maximum resistance, and then preset P2 must be tweaked until the attached lamp is just at the verge of shutting down.
In case a lamp higher than 100 W is utilized the triac should be attached to a heatsink having a heat transfer specification rate of about 6 °C/W.
When the circuit is used like a 1000 W dimmer, suppressor coil L1 should be rated to handle a current of 5 A with an inductance value that may be up to 40uH, while fuse F1 must be rated at 6.3 amps.
Heater using Transistors and Resistors
This unique heater circuit which involves transistors and resistors for the heat dissipation instead of a heater coil was designed by Mr. Norman, but he faced an issue with the circuit.
The problem and solution for the design can be understood from the following discussion:
Problem:
I designed a small heater using LM7812 voltage regulator and Tip31c transistors and resistors.
I tested it over several hours and found a problem. The last two 56R resistors got extremely hot and burned and scorched the pcb. I am attaching a schematic.
I couldn't find a similar project on your website, so I am trying to contact you through this contact point. Thanks!
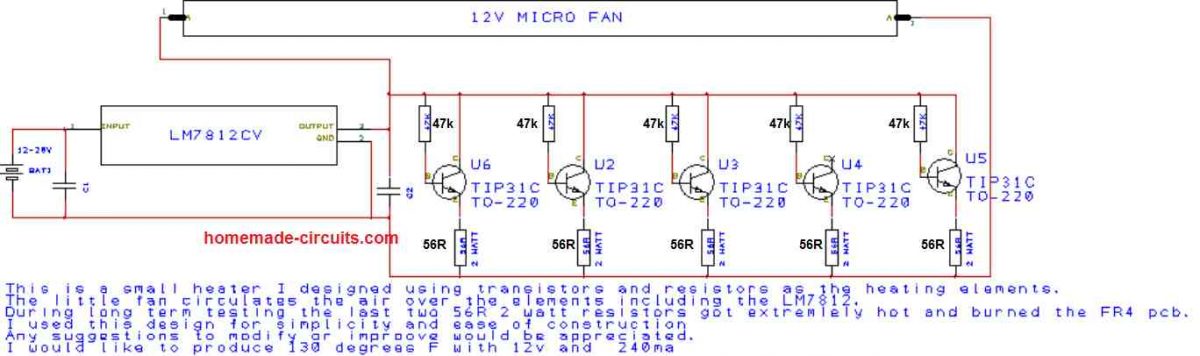
The Solution:
That looks very strange because the 56 ohm resistors at the emitter of the transistors should force the transistor to dissipate the heat equally among the resistors and the transistors.
The last two 56 ohm resistors getting hotter means that the last two BJTs are conducting more freely than the remaining transistors.
The easiest way to tackle this problem is to mount all the transistors over a common aluminum strip, so that the transistor exchange their body dissipation uniformly with each other and thus all the transistors conduct and dissipate equally.