A step down transformer is a device which reduces a higher AC potential to a lower AC potential as per its winding ratio and specifications.
In this article we are going to discuss how to design and construct a basic step down transformer which are typically applied in mains-operated power supplies.
Introduction
This will likely help electronic hobbyists to develop and build their very own transformers based on their particular demands.
Within the next pages, a simplified layout method is presented in order to achieve satisfactorily developed transformers. On the other hand, the design process may be a subject of some experimentation.
The tables I have I have explained in this article trim computations short which help the designer to find the appropriate size of wire or even core lamination.
Exclusively pertinent data and calculations are supplied here to ensure that the designer is absolutely not baffled by unwanted details.
Here we will specifically discuss about transformers which possesses 2 or more winding of insulated copper wire around an iron core. These are: one primary winding and one or maybe more secondary winding.
Each winding is electrically isolated from the other however are magnetically connected by using a laminated iron core.
Small transformers possess a shell style structure, i.e. the winding are encircled by the core as demonstrated in Fig. 1.
The power supplied by the secondary is in fact transmitted from the primary, although at a voltage level dependent on the winding ratio of the a pair of winding.
Video Interpretation
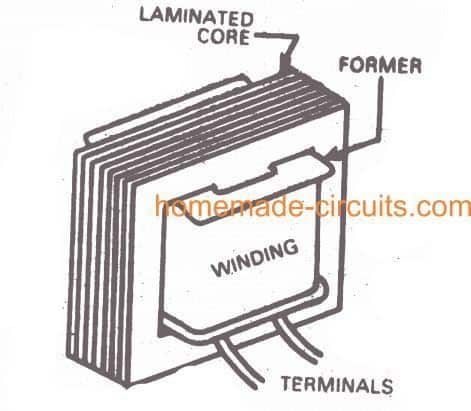
Basic Transformer Design
As the initial phase towards the design of a transformer, the primary and secondary voltage evaluations and the secondary ampere rating has to be distinctly expressed.
After that determine the core content to be employed: ordinary steel stamping or cold rolled grain oriented (CRGO) stamping. CRGO features a greater allowable flux density and reduced losses.
The best possible cross-sectional part of the core is roughly assigned by:
Core Area: 1.152 x √(output voltage x output current) sq cm.
With regard to transformers having several secondaries, the sum of the the output volt-amp product of each winding needs to be considered.
The quantity of turns on the primary and secondary winding is determined using the formula for turns per volt ratio as:
Turns per volt = 1/ (4.44 x 10-4 frequency x core area x flux density)
Here, the frequency is usually 50Hz for Indian household mains source. The flux density could be considered as approximately 1.0 Weber/ sq. m. intended for ordinary steel stamping and approximately 1.3 Weber/ sq. m. for CRGO stamping.
Calculating Primary Winding
The current in the primary'winding is presented by the formula:
Primary Current = Sum of o/p Volt and o/p Amp divided by Primary Volts x efficiency
The efficiency of small transformers can deviate between 0.8 to 0.§6. A value of 0.87 works extremely well for regular transformers.
The appropriate wire size needs to be determined for the winding. The wire diameter is dependent upon the current rated for the winding and also the permitted current density of the wire.
The current density could be as tall as 233 amps/ sq. cm. in small transformers and as minimal as 155 amps/ sq. cm. in big ones.
Winding Data
SWG | Max. current capacity (Amp) | Turns per sq. cm. |
---|---|---|
10 | 16.60 | 8.7 |
11 | 13.638 | 10.4 |
12 | 10.961 | 12.1 |
13 | 8.579 | 13.6 |
14 | 6.487 | 21.5 |
15 | 5.254 | 26.8 |
16 | 4.151 | 35.2 |
17 | 3.178 | 45.4 |
18 | 2.538 | 57.3 |
19 | 2.013 | 72.3 |
20 | 1.313 | 106.0 |
21 | 1.0377 | 132.7 |
22 | 0.8183 | 167.4 |
23 | 0.6383 | 210.9 |
24 | 0.5046 | 265.9 |
25 | 0.4004 | 334.9 |
26 | 0.3284 | 415.0 |
27 | 0.2546 | 523.0 |
28 | 0.2024 | 659.0 |
29 | 0.1608 | 830.0 |
30 | 0.1558 | 881 |
31 | 0.1364 | 997 |
32 | 0.1182 | 1137 |
33 | 0.1014 | 1308 |
34 | 0.0858 | 1608 |
35 | 0.0715 | 1902 |
36 | 0.0586 | 2286 |
37 | 0.0469 | 2800 |
38 | 0.0366 | 3542 |
39 | 0.0284 | 4838 |
40 | 0.0225 | 5595 |
41 | 0.0197 | 6543 |
42 | 0.0144 | 9337 |
43 | 0.0113 | 11352 |
44 | 0.0090 | 14392 |
45 | 0.0079 | 17147 |
46 | 0.0059 | 20223 |
47 | 0.0047 | 25397 |
48 | 0.0037 | 31605 |
49 | 0.0029 | 40160 |
50 | 0.0010 | 81242 |
Typically, a value of 200 amps/ sq. cm. may be considered, according to which Table#1 is created. The amount of turns in the primary winding is presented by the formula:
Primary Turns = Turns per Volt x Primary Volts
The room consumed by the winding is determined by the insulation density, technique of winding and the wire diameter.
Table#1 provides the estimated values of the turns per square cm. through which we are able to calculate the window area consumed by the primary winding.
Primary winding Area = Primary turns / Turns per sq. cm from Table#1
Calculating Secondary Winding
Considering that we have the assumed secondary current rating, we are able to determine the wire size for the secondary winding simply by going through Table#1 directly.
The quantity of turns on the secondary is calculated in the identical method when it comes to primary, but around 3% excess turns should be included to reimburse for the internal drop of secondary winding voltage of the transformer, upon loading. Hence,
Secondary turns = 1.03 (turns per volt x secondary volts)
The window area necessary for secondary winding is identified from Table#2 as
Secondary window area = Secondary turns / Turns per sq. cm. (from Table#2 below)
Calculating Core size
The principal qualifying measure in picking the core could be the total window area of winding space accessible.
Total window area = Primary window area + sum of secondary window areas + space for former & insulation.
A little extra space is necessary to support the former and insulation in between winding. The specific quantity of extra area may differ, even though 30% could be considered to begin with although this may need to be customized later on.
Table Dimension of Transformer Stamping
Section 1
Type No. | Tongue width (cm.) | Window area (sq. cm.) |
---|---|---|
17 (E-I) | 1.270 | 1.213 |
12A (E-I) | 1.588 | 1.897 |
74 (E-I) | 1.748 | 2.213 |
23 (E-I) | 1.905 | 2.723 |
20 (E-I) | 1.905 | 3.230 |
15 (E-I) | 2.223 | 3.230 |
31 (E-I) | 2.588 | 3.230 |
11 (E-I) | 2.540 | 4.839 |
35 (E-I) | 2.540 | 4.839 |
14 (E-I) | 2.461 | 5.645 |
33 (E-I) | 2.461 | 5.645 |
11 (E-I) | 2.540 | 7.259 |
35 (E-I) | 2.540 | 7.259 |
3 (E-I) | 3.810 | 7.562 |
Section 2
Type No. | Tongue width (cm.) | Window area (sq. cm.) |
---|---|---|
9 (U-T) | 2.223 | 7.865 |
9A (U-T) | 2.223 | 7.865 |
4A (E-I) | 3.810 | 10.484 |
4 (E-I) | 3.810 | 10.484 |
16 (E-I) | 3.810 | 10.891 |
13 (E-I) | 2.381 | 15.865 |
7 (E-I) | 2.540 | 15.865 |
6 (E-I) | 3.810 | 15.865 |
5 (E-I) | 3.810 | 19.305 |
8 (E-I) | 5.080 | 49.803 |
The perfect core sizes possessing a more substantial window space are generally determined from Table#2 taking into consideration the gap between lamination while stacking them (the core stacking element may be taken as 0.9), we now have
Gross core area = Core Area / 0.9 sq cm. In general, a square central limb is preferred.
For this, the width of the tongue of lamination is
Tongue width = √Gross core area (sq.cm)
Now refer to Table#2 once again and as a final point find the appropriate core size, having adequate window area and a nearby value of the tongue width as calculated. Modify thel stack height as needed to acquire the intended core section.
Stack Height = Gross Core Area / Actual Tongue Width
The stack must not be a lot under the tongue width rather should be more. However, it must not be greater than 11/2 times the tongue width.
Core Assembly Diagram
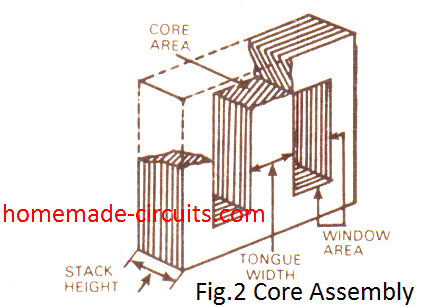
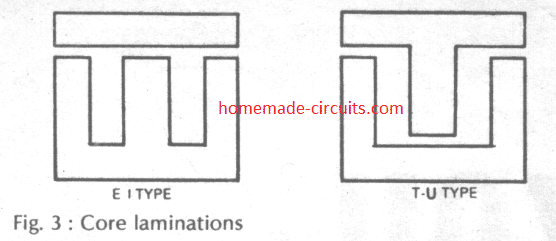
How to Assemble the Transformer
The winding are done over an insulating former or bobbin that fits on the middle pillar of the core lamination.
The primary is generally wound first, and next it is the secondary, keeping an insulation between the two layers of the winding.
One last insulating layer is applied on top of the winding to safeguard all of them from mechanical and vibration deterioration.
Whenever thin wires are employed, their particular ends needs to be soldered to heavier wires in order to bring the terminals outside the former.
The lamination are usually put together on the former by alternate lamination reversed in set up.
The lamination has to be tightly bound together through an appropriate clamping framework or by using nuts and bolts (in case through holes are supplied within the lamination assembly).
How to Apply Shielding
This can be a wise idea to utilize an electrostatic shielding between the primary and secondary winding to circumvent electrical interference from moving across to the secondary from the primary.
The shield for step down transformers can be constructed from a copper foil which can be wound between the two winding for somewhat more than a tum.
Insulation has to be presented across the entire foil and proper care taken in order that the two ends of the foil never come in contact with each other.
Additionally a wire could be soldered with this shielding field and connected with the ground line of the circuit or with the lamination of the transformer which may be clamped with the ground line of the circuit.
For Torroidal Transformer designing, you can refer to the following pdf document:
https://www.homemade-circuits.com/wp-content/uploads/2021/04/torroidal-transformer_compressed.pdf
Additional Useful Information Regarding Transformer Winding
The following useful data related to transformer winding was kindly shared by Mr. Constantinos Mermygas. I hope the readers will find it very helpful.
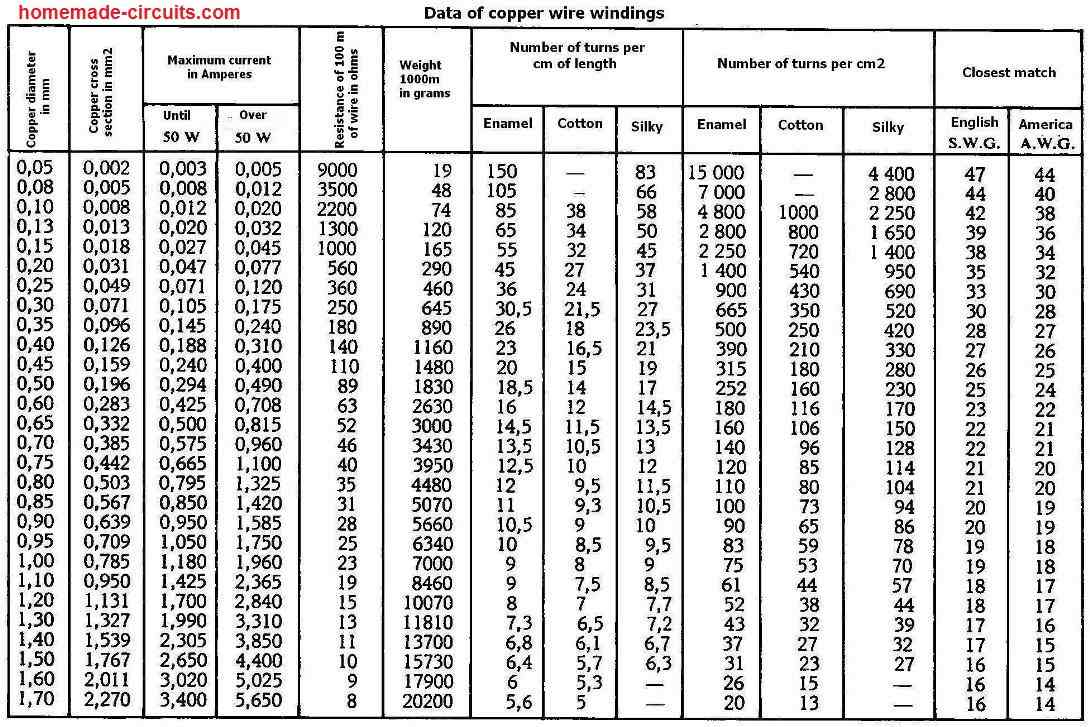
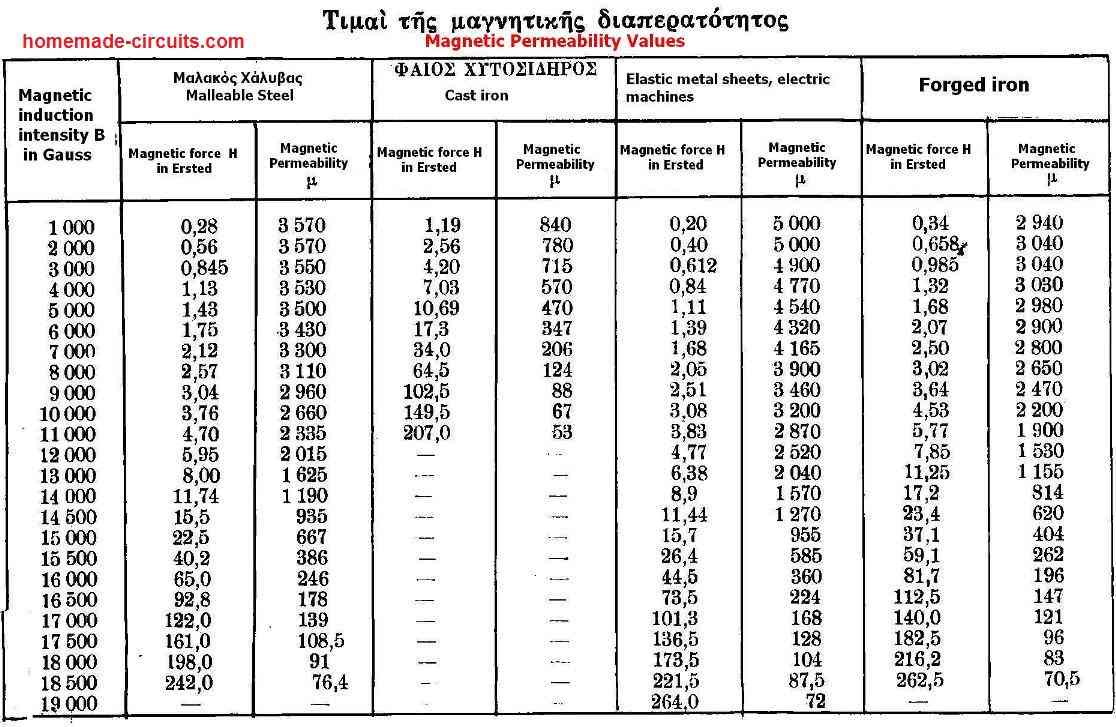
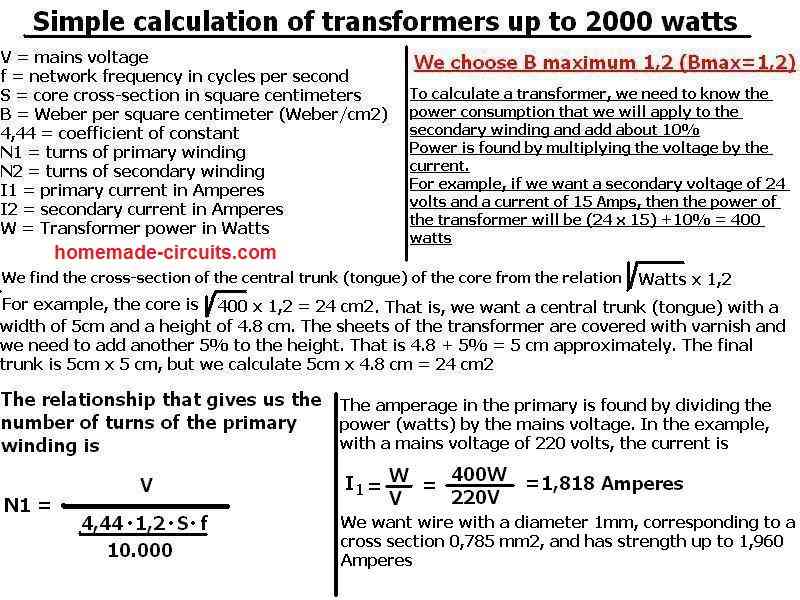
Simple Calculation of Transformers Up to 2000 Watts
Parameters:
- V = Mains voltage
- f = Network frequency in cycles per second
- S = Core cross-section in square centimeters
- B = Weber per square centimeter (Weber/cm²)
- 4.44 = Coefficient of constant
- N1 = Turns of primary winding
- N2 = Turns of secondary winding
- I1 = Primary current in Amperes
- I2 = Secondary current in Amperes
- W = Transformer power in Watts
Calculation Notes:
- Choose Bmax = 1.2 (maximum flux density).
- To calculate a transformer, determine the power consumption on the secondary winding and add approximately 10%.
Power Calculation Example:
- Secondary Voltage: 24 volts
- Current: 15 Amps
- Transformer Power: (24 * 15) + 10% = 400 watts
Core Cross-Section Calculation:
- Example:
Core cross-section: √400 * 1.2 = 24 cm²
Central trunk (tongue): - Width = 5 cm
- Height = 4.8 cm
- Add 5% for varnish, total height ≈ 5 cm
Primary Winding Turns Calculation:
- Formula:
N1 = V / (4.44 × B × S × f / 10,000)
Primary Current Calculation:
- Formula:
I1 = W / V
Example:
I1 = 400W / 220V = 1.818 Amperes
Wire Calculation:
- Example:
- Wire Diameter: 1 mm
- Cross Section: 0.785 mm²
- Current Strength: Up to 1.960 Amperes