An electrical relay consists of a electromagnet and a spring loaded changeover contacts. When the electromagnet is switched ON/OFF with a DC supply, the spring loaded mechanism is corresponding pulled and released by this electromagnet, enabling a changeover across the end terminals of these contacts. An external electrical load connected across these contacts are subsequently switched ON/OFF in response to relay electromagnet switching.
In this post I have explained comprehensively regarding how relay works in electronic circuits, how to identify its pinouts of any relay through a meter and connect in circuits.
Introduction
Whether it’s for flashing a lamp, for switching AC motor or for other similar operations, relays are for such applications. However young electronic enthusiasts often become confused while assessing the pin outs of the relay and configuring them with a drive circuit inside the intended electronic circuit.
In this article we’ll study the basic rules that will help us to identify relay pinouts and learn regarding how a relay works. Let’s begin the discussion.
How a Relay Works
The working of an electrical relay can be learned from the following points:
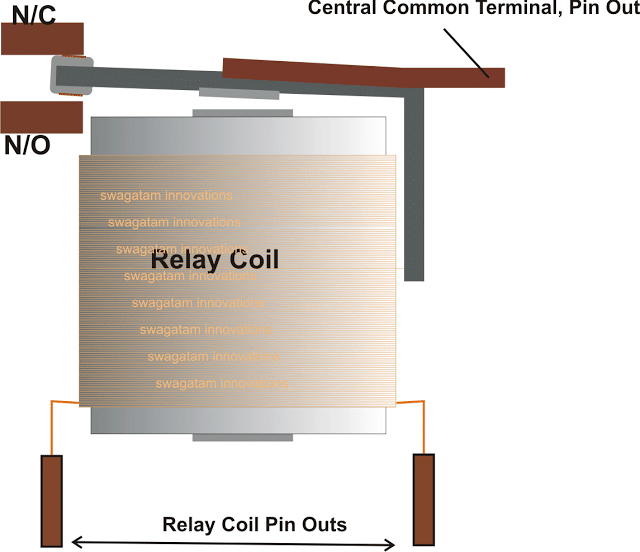
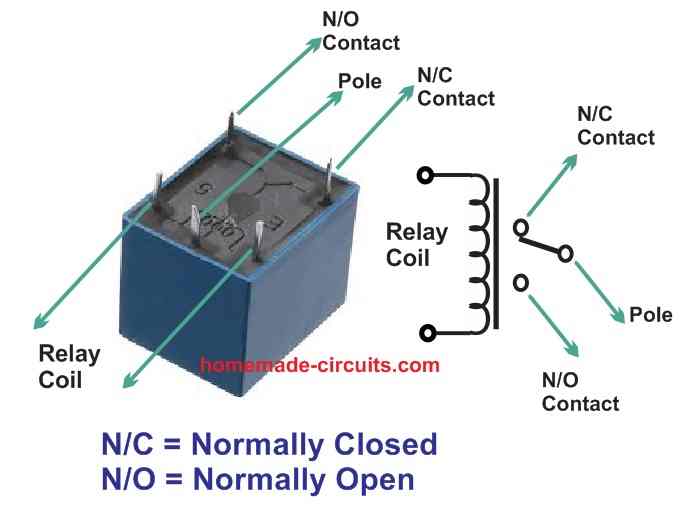
- A relay mechanism basically consists of a coil and a spring loaded contact which is free to move across a pivoted axis.
- The central pole is hinged or pivoted in such a way that when the relay coil is powered with voltage, the central pole joins with one of the side terminals of the device called the N/O contact (Normally Closed).
- This happens because the pole iron gets attracted by the relay coil electromagnetic pull.
- And when the relay coil is switched OFF, the pole disconnects itself from the N/O (Normally Open) terminal and joins itself with a second terminal called the N/C contact.
- This is the default position of the contacts, and happens due to the absence of an electromagnetic force, and also due to the spring tension of the pole metal which normally keeps the pole connected with the N/C contact.
- During such switch ON and switch OFF operations it switches from N/C to N/O alternately depending upon the ON/OFF states of the relay coil
- The coil of the relay which is wound over an iron core behaves like a strong electromagnet when a DC is passed through the coil.
- When the coil is energized the generated electromagnetic field instantly pulls the nearby spring loaded pole metal implementing the above explained switching of the contacts
- The above movable spring loaded pole inherently forms the main central switching lead and its end ts terminated as the pinout of this pole.
- The other two contacts N/C and the N/O form the associated complementary pairs of relay terminals or the pin outs which alternately get connected and disconnected with the central relay pole in response to the coil activation.
- These N/C and N/O contacts also have end terminations which move out of the relay box to form the relevant pinouts of the relay.
The following rough simulation shows how the relay pole moves in response to the electromagnet coil when switched ON and OFF with an input supply voltage. We can clearly see that initially the central pole is held connected with the N/C contact, and when the coil is energized, the pole is pulled downwards due to the electromagnetic action of the coil, forcing the central pole to connect with the N/O contact.
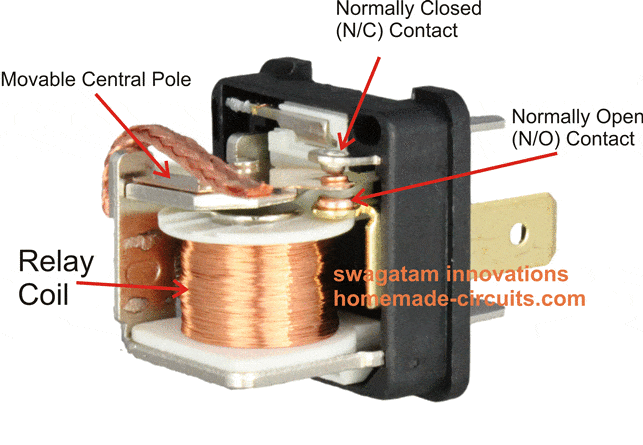
Video Explanation
Thus basically there are three contact pinouts for a relay, namely the central pole, the N/C and the N/O.
The two additional pinouts are terminated with the coil of the relay
This basic relay is also called a SPDT type of relay meaning single pole double throw, since here we have a single central pole but two alternate side contacts in the form of N/O, N/C, hence the term SPDT.
Therefore in all we have 5 pinouts in an SPDT relay: the central movable or switching terminal, a pair of N/C and the N/O terminals and finally the two coil terminals which all together constitute a relays pin outs.
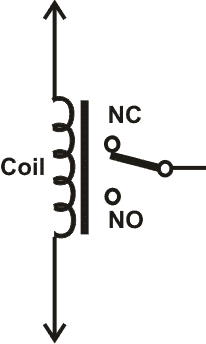
How to identify Relay Pinouts and Connect a Relay
Normally and unfortunately many relays don’t have there pinout marked, which makes it difficult for the new electronic enthusiasts to identify them and make these work for the intended applications.
The pinouts that needs to be identified are (in the given order):
- The coil pins
- The Common Pole pin
- The N/C pin
- The N/O pin
The identification of a typical relays pinouts may be done in the following manner:
1) Position the multimeter in the Ohms range, preferably in the 1K range.
2) Begin by connecting the meter prods to any of the two pins of the relay randomly, until you find the pins which indicate some kind of resistance on th meter display. Typically this may be anything between 100 ohm and 500 Ohm. These pins of the relay would signify the coil pinouts of the relay.
3) Next, follow the same procedure and proceed by connecting the meter meter prods randomly to the remaining three terminals.
4) Keep doing this until you find two pins of the relay indicating a continuity across them. These two pinouts will be obviously the N/C and the pole of the relay, because since the relay is not powered the pole will be attached with the N/C due to internal spring tension, indicating a continuity across each other.
5) Now you need to simply identify the other single terminal which may be oriented somewhere in across the above two terminals representing a triangular configuration.
6) In most cases the central pinout from this triangular configuration would be your relay pole, the N/C is already identified and therefore the last one would be your relay's N/O contact or pinout.
The following simulation shows how a typical relay may be wired with a DC voltage source across its coils and a mains AC load across its N/O and N/C contacts
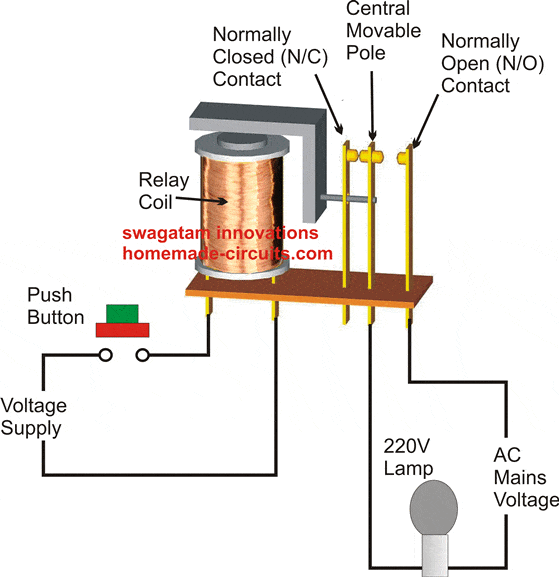
These three contacts may be further confirmed by powering the relay coil with the specified voltage and by checking the N/O side with the meter for a continuity..
The above simple procedure could be applied for identifying any relay pinout which may be unknown to you, or unlabelled.
Now since we have thoroughly studied how a relay works and how to identify the pinouts of a relay, it would be also interesting to know the details of the most popular type of relay which is mostly used in small electronic circuits, and how to connect it.
If you want to know how to design and configure a relay driver stage using a transistor, you can read it in the following post:
How to make a transistor relay driver circuit
A Typical Chinese Make Relay PinOuts
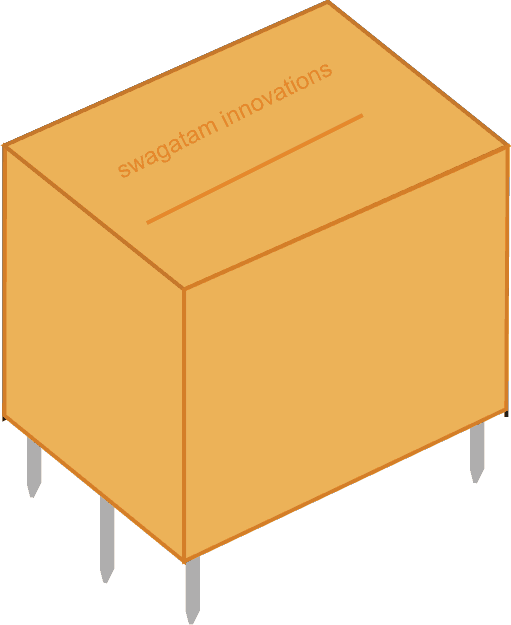
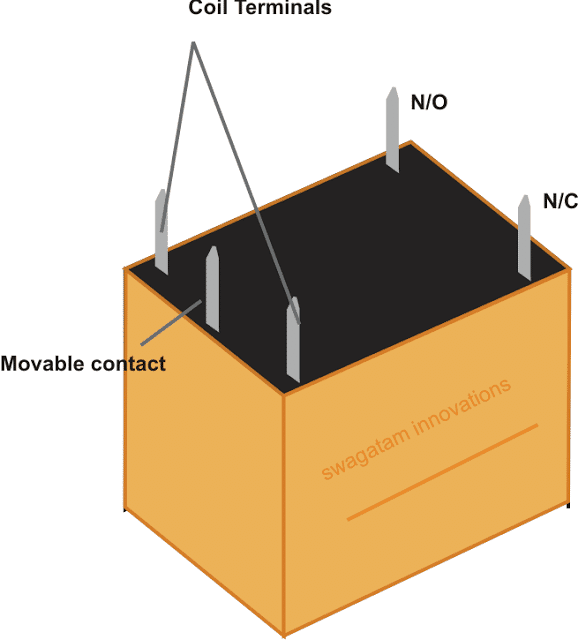
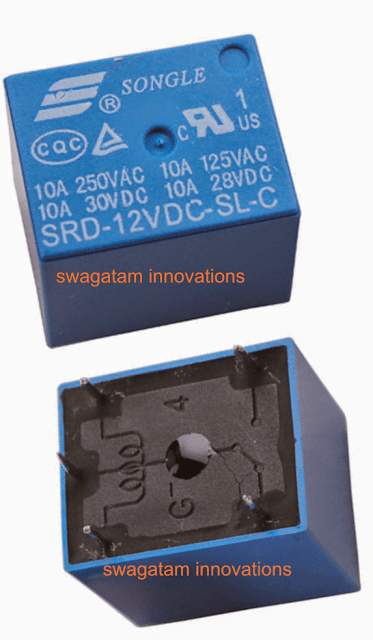
How to Wire Relay Terminals
The following diagram shows how the above relay may be wired with a load, such that when the coil is energized, the load gets triggered or switched ON through its N/O contacts, and through the attached supply voltage.
This supply voltage in series with the load may be as per the load specifications. If the load is rated at DC potential then this supply voltage could be a DC, if the load is supposed to be an AC mains operated then this series supply could be a 220V or 120V AC as per the specifications.
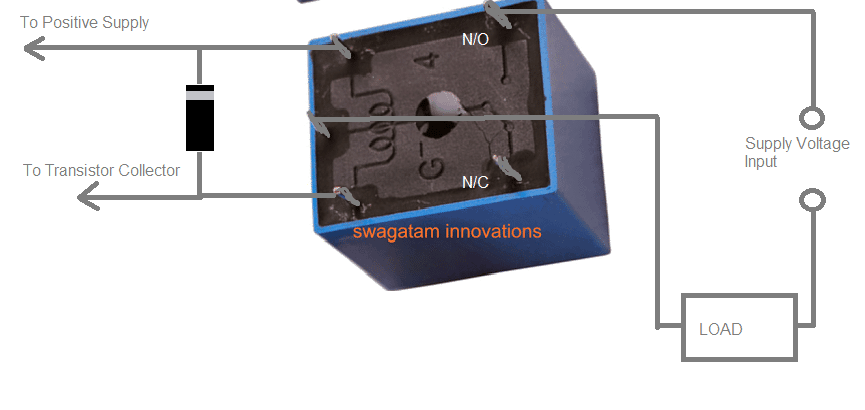
Why is a Diode so Crucial across a Relay Coil
Whenever a relay is used in a circuit, you might have noticed a rectifier diode or a capacitor compulsorily connected parallel to the relay coil.
This diode is called the flyback diode or the freewheeling diode. It is basically introduced to protect the driver transistor from the dangerous reverse back EMF of the relay coil.
You might have wondered, why is a diode always seen across a relay coil? The following section explains why a flyback or a freewheeling diode is so crucial across a relay coil.
The answer lies in the fascinating yet a potentially destructive property of inductors.
We know that, just like capacitors inductors also store electric current (DC) inside its winding. Larger the winding, larger the amount of DC voltage its stores.
A relay coil is also an inductor which has a significantly high number of turns in its winding, and therefore its capacity to store a DC voltage is proportionately huge.
When the relay transistor is switched ON, the relay also switches ON, and it stores a calculated amount of DC voltage within its winding.
Now, as soon as the transistor is switched OFF, the potential across the relay coil is removed. In this situation, the DC voltage stored inside the relay coil has to escape somehow. It tries to discharge through anything that's connected with it. This is known as the relay reverse back EMF, which may have a reverse voltage that's many times larger than the actual DC voltage fed to the relay coil.
Since the driver transistor is connected with the relay, this large reverse EMF tries to force through the transistor emitter/collector. The word "reverse" is used because this back EMF is negative in polarity. Being negative in polarity this back EMF tries to force through the emitter towards the collector, causing an instant damage to the transistor.
In order to neutralize the above reverse back EMF a flyback diode or a freewheeling diode is always connected across a relay coil. This diode can be a simple 1N4007 diode for most of the relays (upto 30 amps).
As long as the relay remains switched ON through the driver transistor, the diode remains negatively biased and has no effect on the operation of the relay. However, when the relay is switched OFF, the diode becomes forward biased for the reverse EMF kicking out from the relay coil.
This back EMF now finds an easy path through the forward biased diode and short circuits through the diode. In this way the dangerous relay coil reverse EMF is neutralized and short circuited through the diode which totally safeguards the driver transistor from any possible damage.
If a diode is not available a high value electrolytic capacitor can be also used. The capacitor can function in the same way. It allows a reverse short circuit path for the back EMF and protects the transistor from getting damaged.
What if a Driver Transistor is not used and the Relay is Operated Directly from a Power Supply?
Even in this situation a freewheeling diode must be connected across a relay coil. Because the reverse back EMF from the relay coil may still have the potential to force enter the power supply or any associated circuitry and cause damage to the vulnerable electronic parts.
How to Calculate relay Flyback Diode
This may not be easy actually, because there are no easy formulas to calculate the relay flyback diode.
However, the rule of thumb is that, the reverse EMF current can be never higher than the actual current rating of the relay coil. Although the voltage could be many times higher.
A 1N4007 fits the bill for almost all relay driver applications (below 24 V and above 100 Ohm relays)
This is because a PIV of a 1N4007 is 1000 V and the current handling capacity is 1 amp. For most applications, the back EMF from a relay coil can never exceed the above ratings of the 1N4007 diode.
Even for a massive 12V 100 ohm relay, its coil current would be:
I = 12 / 100 = 120 mA. Thus the back EMF current will be much smaller than this. A 1N4007 will be perfectly able to handle this reverse current.
Hello Swagatam,
I hope you can advise me or assist me with my camper project(hobby) with the below scenario
I want to use a timer relay off delay for my camper safety which is, 2 cameras: one is working with the reverse wire trigger, and the second with the door opening and the output is a screen monitor to be delayed off for X (amount of time).
I have used 2 timer relays delay-off, each for a camera and the mentioned triggers but the problem is the power feeds back/ interferes with the other in the output and I can’t separate the camera triggers which should be on only when triggered either reverse or door opening separately.
How do I make this project work?
timer delay off= t= x (seconds/minutes delay off)
Regards
Markus
Hello Markus,
I will have to see the schematic diagram of your design to understand the problem.
So, if possible please send the schematic diagram to my email ID, I will try to figure it out for you.
Dear Sir,
I am confused as to whether I need a 12 volt 4 pin, or 12 volt 5 pin relay.
What I want to do is to add a switched 12 volt supply on my (2008) XT250 motorcycle to feed a dual USB plug plus at the same time a feed to a TomTom Rider 550 GPS.
I believe that I need to connect a relay to the registration rear plate light to turn on the relay when the bike key is turned on.
The YouTube video also suggested using a zip-tie to attach the relay to the bike frame. Is this OK or will there be too much vibration. i.e. what should I do?
Thank you.
Regards,
Robert.
Hi Robert,
You can use a 4-pin relay but a 5-pin is better because it is easily available, and having one N/C contact in spare won’t effect anything.
If you are worried about the vibrations, do not buy the small cube type relay with 400 ohm coil resistance, buy the one which has lower coil resistance maybe around 100 and 200 ohms. Lower coil resistance would mean larger coil current and more powerful contact activation which will not be affected by the vibrations.
Dear Sir,
1) Is a Narva 68028 suitable?
2) If not, what should I buy.
Thank you.
Robert,
I would suggest you to first try a standard sugar cube type relay, and check whether it is affected by the vibrations or not.
If yes only then you can look for other alternatives.
However the Narva 68028 is not suitable, because its rating is too high, which is not required.
Yes agreed so I revaluated what the circuit is doing.
At 3500 rpm there are 3 groups of 2 magnets rotating.
the Triger for the relay is hall sensor 180° apart under the coils of which only 2 are the Triger that open and close the Relay.
So at 3500 rpm the switching time is 10,500.
With 1 rpm the Switching Time/min is 3.
Gregg
OK, thanks for the clarification, understood now.
However, at this rate I don’t think the relays would last very long.
Yes agreed, somewhere below 3000 rpm maybe a comfortable region.
But for now I will try your homebuilt 12v ssr MOSFETs, the store bought ones just don’t work with my application.
Sure, you can try it. Let me know if you have any problems.
Hi Swagatam
I wanted to ask you about the Relay Data Sheet reference to:
Iam using the 3v relay
Operation Time 10msec Max.
Release Time 5msec Max.
Max. ON/OFF Switching
Mechanically 300 operation/min
Electrically 30 operation/min
My question is, am I to understand, the relay can open and close 300 times per min?
Hi Gregg,
Yes, if the datasheet says 300 operations per minute that means closing and opening 300 times. One close/open = one operation.
That’s what I thought also, but even in there data doesn’t make sense to me, and here is why.
Operation Time 10msec Max
Max. ON/OFF Switching
Mechanically 300 operation/min
Electrically 30 operation/min
There are 100 (10msec) per sec. And 6000 per min.
In my own experiments I am getting 21000/min ON/OFF operation Switching Time/min, before the relay gets kind of hot.
Thanks for your response.
Gregg Pierce
Your calculations look correct, but how did you check 21000/min ON/OFF operations? Because 21000 number is huge.
The datasheet could be suggesting the safest range of the operation, without causing considerable stress on the relay.
Swagatam
So I did some recalculations and testing with and without the load, the load being 10 to 12v.
every time the magnet passes the hall effect the relay opens and closes and with 6 magnets that is 6 operations per rotation. Also I took the shell off so I could better understand the relay workings. I could touch and hold it while in operation and a comfortable range for my purposes was 2200 to 2500 rpm.
probably not what the relay was designed for but for now it works me, till I can build a homebuilt ssr.
Thanks Gregg
Thanks Gregg, for updating the results. Glad it is working for you at the moment. Do let us know if you happen to test the results using an ssr.
This is very similar to my circuit, which I will try to explain the best I can. But my question was to the “stackoverflow” people was all I wanted to do was to replace the 5v mechanical relay with a 2N7000 homemade circuit or just buy one. They started asking alot of questions that I could not answer or have the time for.
Anyway here is my circuits, One to operate the coil to open the N/C contacts and a separate power source to drive the load.
I have through trial and error found this works for me. The coils which are 6ea placed 60 deg. apart in a circular fashion about 4″ apart on a 6″ board. The A144 hall sensors 6ea are placed inside the coils.
There is a small rotor made of plastic that hole the neodymium magnets 12ea 6ea on top and 6ea underneath also at 60deg apart like a sandwich. A simple motor so far.
The operation is this, I hand start the rotor and the magnets S pole rotates across the coil and the A144 hall sensors all at the same time but through experimentation I find i only need two of them which are 180deg apart. When the magnets pass the A144 hall sensors that opens the N/C contacts of the relay
So I know that motor can rotate faster with an mosfet, ssr, homemade circuit.
Thanks Gregg
Thanks for sharing your experience. Yes a MOSFET based relay is always better and more efficient than an electromechanical relay.
However, I could not understand your question, or the problem you are facing.
Simply, I guess my question is replacing the mechanical relay with a mosfet.
Currently, the one I’m using is the 2N7000.
I guess I should make a drawing and send it that would be more clearer.
I have an article on this subject which explains how to use MOSFETs to build solid-state relay, here’s the link:
https://www.homemade-circuits.com/12v-dc-solid-state-relay-ssr-100-amps/
The above concept is designed to work with DC supplies only.
However 2N7000 can handle only 200mA, so make sure to replace it with a higher rated one, depending on your load current spec.
Thanks Saad, Glad you found it useful.
Thank you, glad you liked it!
I want/need a relay that is normally closed. When power, 12V , is applied to the “trigger” the relay opens.
You can try the following schematic:
https://www.homemade-circuits.com/wp-content/uploads/2023/06/PNP-relay-driver-with-switch-OFF-trigger.jpg
Can I make a toggle switch circuit with relay? I mean, By using just on/off (push button) switch to control LEDs? Ex. When I switch on a circuit, the LEDs stay lit even if I release my fingers from on/off switch and when I touch the switch again the LEDs will be turned off.
Yes you can, using the concepts explained in the following article:
https://www.homemade-circuits.com/build-these-simple-flip-flop-circuits/
I have a 5 pin relay which I would like to wire normally closed (Power to the instrument) and opened by applying a ground. Possible?
Yes, that’s possible. Use an NPN transistor to power the relay. Let the transistor be powered through a base resistor connected to the positive supply.
In this position grounding the transistor base will turn OFF the relay.
what is rectification failure relay, how it works and what are example of this?
thanks swagatam,
it is over now. Every thing is oky, the diagram illustrates the real function of a relay.
kind regards.
Godwin.
Thanks Godwin, Glad it helped!
hi, swagatam
The article was well understood. But my question is how does a relay sources a current in a circuit? As i, get you, expressed only in switching circuits.
thanks.
your friend in electronics.
Godwin.
Malawi.
Thank you Godwin,
The relay switches current and voltage through its contacts, as shown in the following GIF image:
https://www.homemade-circuits.com/wp-content/uploads/2012/01/relay-operation.gif
That’s a good presentation
Thanks
Last two days I’m watching videos on youtube trying to understand the relay. Luckily I found your valuable post on the internet and I’m really benefited from your post here. Thanks for this post from you.
Thank you, and Glad you found the post useful!
Dear Sir,
What is the transistor and diode values and I want to use this open sliding gate (Ac motor) with Fingerprint(DC 12v) device so please tell me how can do it
Thanks
Hi Chandana,
For a relay the transistor can be a 2N2222, and the flyback diode across the relay coil can be a 1N4007 diode.
Thanks Friend, welcome, I learned from your electrical site to collect electrical knowledge, I want to learn electrical knowledge from you. can Cooperation me .
Sure, you are welcome!
Good day to you
How do i wire a relay(N/C, N/O, COM) with positive and negative also on relay, to battery(+,-) and switch(COM, N/O) to make a buzzer work when switch is pressed.
Hi, The relay connections to the buzzer through N/O contacts will be like this:
Your article is very educative on relay circuits. But I have a question about what I made . Can share the video for you to see and chech why it is not working perfectly? Via email when you reply me?
You can send it to homemadecircuits @ gmail . com
Learning motor vehicle wiring
How to make your car system to charge normal
MR SWAG, I REALLY APPRECITAE YOUR EFORT ON THIS RELAY EXPLANATON, I HAVE BEEN FINDING IT DIFFCULT IN CONNECTING RELAY PREVIOUSLY BUT I NOW UNDERSTAND HOW THEY WORK N HOW TO CONNECT THEM IN A CIRCUIT. THANKS SO MUCH SIR GOD BLESS YOU.
Thank you Godspower…I am glad the post helped you!
Clearest explanation on the Internet! Thank you
Thank you for your kind feedback!
Dear sir,
Very informative, could i ask,
I have a campervan with inverter to make 240v, i have a 240v mains hookup, my question is, what sort of relay setup would i use to switch from inverter power to hookup power
automatically? would i need to switch both positive/live and negative/neutral using double pole relay (so nothing goes to inverter completely) or just the live?
regards
Paul
Thank you Paul, yes you will need a DPDT relay and a SPDT relay for the changeover action.The DPDT can be used for changing over the AC LIVE/NEUTRAL lines, while the SPDT can be used for changing the positive line of the battery
Thanks for timely reply,
I think i understand, i would like to use n/o dpdt relay that allows inverter to be main supply to fuse/sockets (that would be default 240v power to camper) control of relay action (n/o relay) would be ac coil(240v) supplied from hookup, this changes live/neutral from inverter over to hookup power live/neutral, 240v mains power. correct?
why do i need spdt relay for changing the positive line of the battery, is this to remove power that is going from 12v batteries to inverter?
I’m looking at din rail mount relay placed in enclosure with din rail 240v trip/fuses, that is auto switched from inverter to mains when hookup is pluged in.
sorry if this is a bit long winded, just a safety thing for me. ask ask ask, get it right first time.
regards
Paul
Yes your assumptions are correct for the DPDT mains connections. The battery positive also needs a changeover, since its needs to be transferred from the inverter powering mode to charging mode when mains is present.
That would stop any sort of charging, by mains hook-up feeding into inverter from batteies. correct?
what ampage relay would you suggest? I’m looking at about 25-40amp din rail dpdt relay and wire all in enclosure with the Mcb’s and rcd, the spdt relay will be 40amp? my 12v split charge circuit have 50amp trip fuses.
hope this will also be imfromative to other people out there, thinking camper van and open skys.
The SPDT relay will disconnect the battery positive from the inverter and connect it with the charger positive supply, during the mains AC presence.
The respective relay contacts will depend on the battery Ah rating or the charging current, and the transformer wattage.
Hello Mr.Swag. If a relay is 10a / 250 . can the load of a 220v 40w x 20 lamp be used?
how to calculate the load power of maximum the relay? Thanks
Hello Sarwana, yes yoo can use the relay for the mentioned load, which will consume not more than 4 amps
Hi, Swagatam. We build control circuits with 24VDC relays operated by PLC transistor outputs. Some of the PLCs have (-) 24VDC outputs and others have (+) 24VDC outputs. We have a standard 1N4002 diode across the relay coil as a snubber, which works just fine. However, we have to build two different types of circuit boards, one with the snubber diode biased one direction and the other board with the snubber diode in the other direction, depending on the PLC outputs being utilized. We want to use two zener diodes in series, reverse biased across the relay coil so that we can build one board and utilize either PLC output style without modifications. The relay coil common voltage is jumper selectable. The relay draws 5.1mA when energized. We are having trouble deciding what power rating the zeners need to be. We would greatly appreciate your expertise on this. Thank you very much.
Hi Louis, since the current rating of the relay coil is only 5.1 mA, any standard zener (400mW) should work. However for greater safety you can use 1 watt diodes which will be more than enough.
Thank you so much for the rapid reply. It is important to us that we build our boards to be as reliable as possible.
No problem, wish you all the best!
Q: why that diode is needed at all? Text missed not only explanation, but even mention that diode exists.
Diode across the relay coil helps to short circuit the reverse EMF spike from the relay coil whenever the relay is switched OFF. This helps to protect the relay driver transistor from the spike. If the diode is not introduced, the reverse EMF spike would try to force through the transistor’s emitter/collector leads, damaging the transistor permanently.
Swagatam: thanks A LOT! Very great explanation. I think this explanation MUST be in text, since it’s quite important. People CAN guess that on picture is “diode”, but WHY? You gave good answer, thanks. How I should count voltage/amps of diode? (and also interesting: why relay itself doesn’t have this diode?)
Thank you Vincent! I have added the required information at the end of the above article.
The diode is not included in a relay basically to keep the relay cost lower. Adding a diode might lead to an increased manufacturing costs and make the relay more expensive.
Another factor is that, if a diode comes connected with the relay, the relay would be forced to have a specific polarity and orientation, causing unnecessary discomfort for designing the PCB and accommodating the relay.
OK, polarity is serious reason. What about parameters of diode? What spike level I should fear?
You do not have to fear if you are using a 1N4007 diode across the relay coil, since the spike can never exceed 1000V and the 1N4007 can easily tackle upto 1000 V.
First I’d like to commend you on your patience and knowledge – you are an exleprorary teacher. Here I might add that adding the diode is especially important when switching analog signals like line level audio or the more sensitive low impeadce microphone lines for a paging system, anything that is headed for an amplifier. because the amplifier cannot sometimes discern the pulse from the program source and tends to amplify a broad spectrum of frequencies – many fold – including the ” clip,” or DC. Ive even used relays to break and ground video signals for “black out” effect in entertainment systens Without the diode to block the pulse the inputs are overloaded and these systems will blackout forever – customers complain – too much blackout effect – lololing…The emf pulse when the coil deenergizes is nasty stuff, when amplified it can cause te coils in the speakers to heat up and projectors to catch fire eve, all makes smoke – I tell custoner; No extra charge for smoke effect.. he should be greatfull;.. he is not amused. All joking aside, I learned these things the hard way in the 70’s and 80’s – the expensive way – be smarter tham me.
Thank you for the interesting and useful feedback, appreciate it very much. Please keep up the good work.
dear sir, i want to a relay to be on for desired period (say 10 seconds) and off when power supply is given and it has to be remain at off state further with availability of power supply. again it has to on after main power supply is connected after disconnection. please give instructions for that. thanks sir.
Jayanth, you can try the first circuit from this article:
https://www.homemade-circuits.com/interesting-timer-circuits-using-ic-555-explored/
replace S1 with a 0.1uF capacitor.
ok sir i will
I know very very little about circuitry. Someone told me the project I’m working on needs a “timer relay” and someone who knows controls. Thanks to this article, I think I now understand what a relay does, thank you! However, you seem like someone who knows controls, so perhaps you might be able to help more specifically. 🙂
I’m trying to make a setup where one light runs continuously during the daytime, but when a button is pushed, that light would turn off and a different one would turn on for 30 seconds. After the 30 seconds, it would go back to the normal light.
Scorpions glow under blacklight/UV light, and we want to be able to show that in an exhibit. We had a simple switch setup with on/off, so we left the blacklight on all day (controlled with simple lamp timer to turn off when we were closed) and put the “normal” light on the on/off switch, so when the switch was ON, the white light interfered with the UV and the scorpions looked black, and when OFF you could see the scorpions’ fluorescence under the blacklight. But apparently scorpion fluorescence decreases with chronic exposure to UV, so after a few months of ~12h/day of UV, they were barely glowing anymore. Instead, we want to make a setup where someone pushes a button (or flips a switch or similar interaction) to view the animals under blacklight, but it automatically goes back to the normal light after.
Usually we just use a lamp timer to set the daytime hours the normal light is on (for viewing & to give animal day/night cycle), so bonus if the system can work with that, or incorporate the day/night cycle as well.
Sorry if this is a simple question – I’m a biologist, so can tell you tons of cool stuff about scorpions and a bunch of other animals, but can’t figure out what words to enter into Google to try to find this answer!
Hi, please provide the electrical specifications of the black light and the day time timer, are these operated with 220V AC? I’ll try to figure out a suitable solution once I get these details.
Just wanted to say thanks for a great tutorial on relays.The explanations,animations and pics helped this beginner grasp relay concept and uses.Keep up the good work.
Glad you liked leo, appreciate you feedback!
Hello sir, thanks for the info.
But what about the square based 11 pin relays?
I have an inverter that doesn’t charge batteries, so I built an external 40A battery charger for my batteries.. But whenever I want to charge the battery, I’ll have to remove the inverter red and black terminals from the battery so that current will not flow from the charger into the inverter and damage it. I want something that will enable me not worry about this, with the use of those 11pin square base 40A relay so that when it is time for charging, the inverter terminals can still be on the battery, as well as the charger terminals, without current going into the inverter
Hello Jerry, you will have to find the pin diagram and internal configuration of the relay. Once you find it you can easily configure it for the required changeover and switching.
Without seeing the schematic or the pin diagram of the relay it may be difficult to judge its operational details