The 6 unique designs below explains us how an ordinary single IC 555 astable multivibrator could be used effectively to make an inverter without involving complex stages.
No doubt IC 555 is a versatile IC which has many applications in the electronic world. However when it comes to inverters, IC 555 becomes ideally suitable for it.
In this post we'll discuss 5 outstanding IC 555 inverter circuits, from a simple square wave variant to slightly more advanced SPWM sinewave designs, and finally a full fledged ferrite core based DC to DC pwm inverter circuit. Let's begin.
The idea was requested by Mr. ningrat_edan.

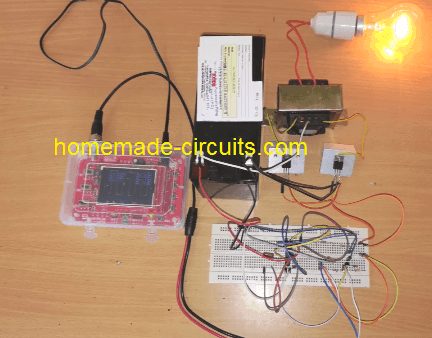
The Basic Design
Referring to the shown diagram, a single IC 555 can be seen configured in its standard astable mode, wherein its pin#3 is used as the oscillator source for implementing the inverter function.
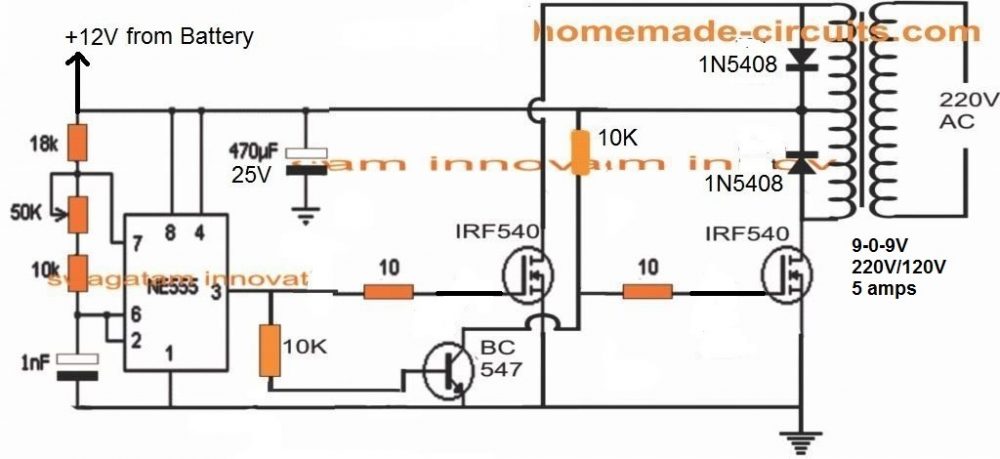
NOTE: Please replace the 1 nF capacitor with a 0.47 uF capacitor for optimizing 50 Hz at the output. It can be a polar or a non-polar.
How it Works
The working of this IC 555 inverter circuit can be understood with the following step wise analysis:
The IC 555 is configured in an astable multivibrator mode, which allows its pin#3 to switch a continuous high/low pulses at a particular frequency rate. This frequency rate depends on the values of the resistors and capacitor across its pin#7, Pin#6, 2 etc.
Pin#3 of the IC 555 generates the required 50 Hz or 60 Hz frequency for the MOSFETs.
As we know that the MOSFETs here are required to run alternately for enabling a push-pull oscillation on the attached transformer center tap winding.
Therefore both the MOSFET gates cannot be connected to pin#3 of the IC. If we do this both the MOSFETs would conduct simultaneously causing both the primary winding to switch together. This would cause two anti-phase signals induced at the secondary causing a short circuit of the output AC and there would be a a net zero AC at the output, and heating up of the transformer.
To avoid this situation, the two MOSFETs needs to be operated alternately in tandem.
The Function of BC547
To ensure that the MOSFETs switch alternately at 50 Hz frequency from pin#3 of the IC 555, we introduce a BC547 stage for inverting the pin#3 output across its collector.
By doing this we effcetively enable the pin#3 pulse to create opposite +/- frequencies, one at pin#3 and the other at the collector of the BC547.
With this arrangement, one MOSFET gate operate from pin#3, while the other MOSFET operates from the collector of the BC547.
This means when MOSFET at pin#3 is ON, MOSFET at the BC547 collector is OFF, and vice versa.
This effectively allows the MOSFETs to switch alternately for the required push pull switching.
How the Transformer Works
The working of the transformer in this IC 555 inverter circuit can be learned from the following explanation:
When the MOSFETs conduct alternately, the relevant half winding is supplied with the high current from the battery.
The response allows the transformer to generate a push pull switching across its center tap winding. The effect of this causes the required 50 Hz alternating current or the 220 V AC to be induced across its secondary winding
During the ON periods the respective winding store energy in the form electromagnetic energy. When the MOSFETs are switches OFF the relevant winding kicks back its stored energy on the secondary mains winding inducing the 220V or 120V cycle on the output side of the transformer.
This keeps happening alternately for the two primary winding causing an alternating 220V/120V mains voltage to develop on the secondary side.
The Importance of the Reverse Protection Diodes
This type of center tap topology has a downside. When the primary half winding throws the reverse EMF, this is also subjected on the MOSFET drain/source terminals.
This can have a devastating effect on the MOSFETs if the reverse protection diodes are not included across the primary side of the transformer. But including these diodes also means precious energy being shunted to ground, causing the inverter to work with a lower efficiency.
Technical Specifications:
- Power Output: Unlimited, can be between 100 watt to 5000 watts
- Transformer: As per preference, Wattage will be as per the Output Load wattage requirement
- Battery: 12V, and Ah rating should be 10 times more than the current selected for the transformer.
- Waveform: Square Wave
- Frequency: 50 Hz, or 60 Hz as per country code.
- Output Voltage: 220V or 120V as per country code
How to Calculate IC 555 Frequency
The frequency of IC 555 astable oscillator circuit is basically determined by an RC (resistor, capacitor) network configured across its pin#7, pin#2/6 and ground.
When IC 555 is applied as an inverter circuit, the values of these resistors and the capacitor is calculated such that the pin#3 of rthe IC produces a frequency of either around 50Hz, or 60 Hz. 50 Hz is the standard value compatible for 220V AC output while 60Hz is recommended for 120V AC outputs.
The formula for calculating the RC values in a IC 555 circuit is shown below:
F = 1.44 / (R1 + 2 x R2) C
Where F is the intended frequency output, R1 is the resistor which is connected between pin#7 and ground in the circuit, while R2 is the resistor in between pin#7 and pin#6/2 of the IC. C is the capacitor found between pin#6/2 and ground.
Remember F will be in Farads, F will be in Hertz, R will be in Ohms, and C will be in microFarads (μF)
Video Clip:
Waveform Image:
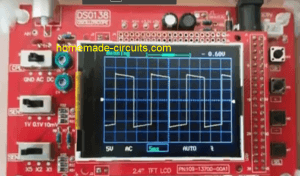
Using BJT instead of MOSFETs
In the above diagram we studied a MOSFET based inverter with center tap transformer. The design made use of 4 transistor in all which appears to be a bit lengthy and less cost effective.
For hobbyists who may be interested in building a IC 555 inverter using a couple of power BJTs only will find the following circuit very useful:
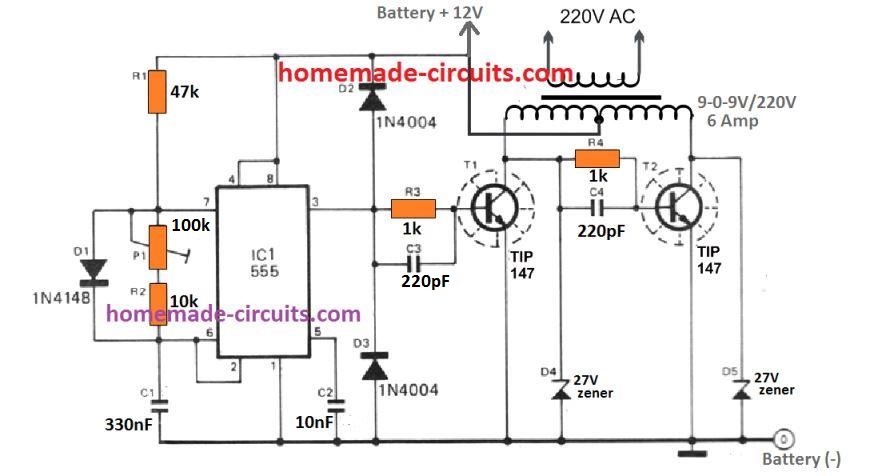
UPDATE: Did you know, you could make a cool modified sine wave inverter simply by combining a IC 555 with IC 4017, see the second diagram from this article: Recommended for all dedicated inverter hobbyists
2) IC 555 Full Bridge Inverter Circuit
The idea presented belowcan be considered as the simplest IC 555 based full bridge inverter circuit which is not only simple and cheap to build but is also significantly powerful. The power of the inverter may be increased to any reasonable limits y suitably modifying the number of mosfets at the output stage.
How it Works
The circuit of a simplest full bridge power inverter explained requires a single IC 555, a couple of the mosfets and a power transformer as the top ingredients.
As shown in the figure, the IC 555 has been wired as usual in the an astable multivibrator form. The resistors R1 and R2 decides the duty cycle of the inverter.
R1 and R2 must be adjusted and calculated precisely for getting a 50% duty cycle, otherwise the inverter output may generate unequal waveform, which may lead to unbalanced AC output, dangerous for the appliances and also the mosfets will tend to dissipate unevenly giving rise to multiple issues in the circuit.
The value of the C1 must be chosen such that the output frequency comes to about 50 Hz for 220V specs and 60 Hz for 120V specs.
The mosfets can be any power mosfets, capable of handling huge currents, may be upto 10 amps or more.
Here since the operation is a full bridge type without any full bridge driver ICs, two batteries are incorporated instead of one for supplying the ground potential for the transformer and in order to make the transformer secondary winding responsive to both positive and negative cycles from the mosfet operations.
The idea has been designed by me, however it has not been yet tested practically so kindly take this issue into consideration while making it.
Assumably the inverter should be able to handle upto 200 watts of power easily with great efficiency.
The output will be a square wave type.
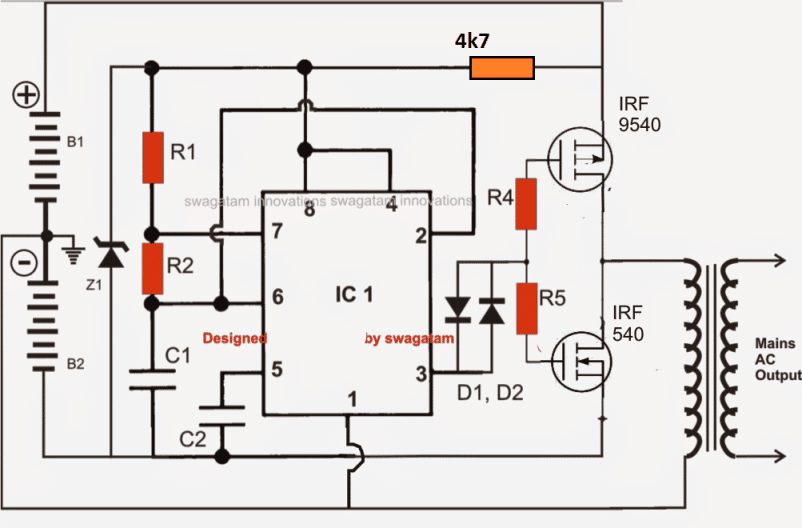
Parts List
- R1 and R2 = See Text,
- C1 = See text,
- C2 = 0.01uF
- R3 = 470 Ohms, 1 watt,
- R4, R5 = 100 Ohms,
- D1, D2 = 1N4148
- Mosfets = see text.
- Z1 = 5.1V 1 watt zener diode.
- Transformer = Asper power requirement,
- B1, B2 = two 12 volts batteries, AH will be as per preference.
- IC1 = 555
Another Full Bridge 555 Inverter
Another full bridge 555 inverter using a 2 wire transformer is shown in the following diagram. Unlike the above design this inverter does not depend on two batteries rather works with a single battery.
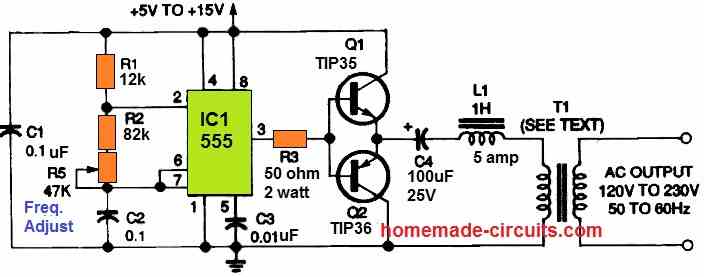
The IC 555 again is rigged as a simple astable multivibrator circuit whose output frequency can be adjusted to a precise 50 Hz or 60 Hz. The frequency is fed to push pull power transistor network using TIP35 and TIP36 configuration, which provides a high current oscillation into the connected power transformer.
A series resistor/inductor network using C4 and L1 ensure an over current protection for the transistors, and allows a controlled running of the full bridge inverter.
The transformer can any ordinary step-down transformer such as 12-0-12V/5 amp, if the supply voltage is 15V. Alternatively a 9-0-9V transformer can be also tried for a 12V battery operation.
3) Pure Sine wave SPWM IC 555 Inverter Circuit
The proposed IC 555 based pure sine wave inverter circuit generates accurately spaced PWM pulses which imitates a sine wave very closely and thus can be considered as good as its sine wave counter part design.
Here we use two stages for creating the required PWM pulses, the stage comprising the ICs 741 and the other comprising the IC 555. Let’s learn the whole concept in details.
How the Circuit Functions – The PWM Stage
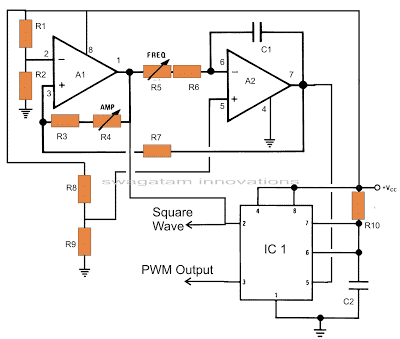
The circuit diagram can be understood with the following points:
The two opamps are basically arranged to generate the required sample source voltages for the IC 555.
The couple of outputs from this stage is responsible for the generation of square waves and triangular waves.
The second stage which is actually the heart of the circuit consists of the IC 555. Here the IC is wired in a monostable mode with the square waves from the opamp stage applied to its trigger pin #2 and the triangular waves applied to its control voltage pin # 5.
The square wave input triggers the monostable to generate a chain of pulses at the output where as the triangular signal modulates the width of this output square wave pulses.
The output from the IC 555 now follows the “instructions” from the opamp stage and optimizes its output in response to the two input signals, producing the sine equivalent PWM pulses.
Now it’s just a matter of appropriately feeding the PWM pulses to the output stages of an inverter consisting of the output devices, the transformer and the battery.
Integrating PWM with the Output Stage
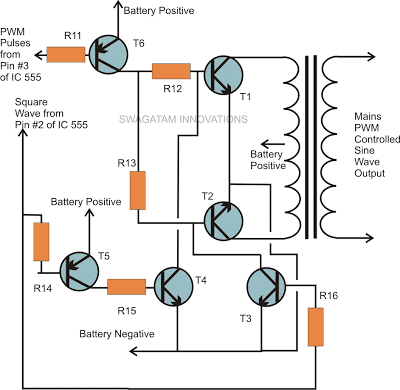
The above PWM output is applied to the output stage as shown in the figure.
Transistors T1 and T2 receive the PWM pulses at their bases and switch the battery voltage into the transformer winding according to the duty cycles of the PWM optimized waveform.
The other two transistors make sure that the conduction of T1 and T2 takes place in tandem, that is alternately so tat the output o from the transformer generates one complete AC cycle with the two halves of the PWM pulses.
Waveform Images:
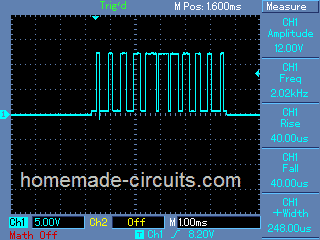
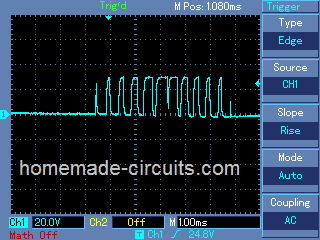
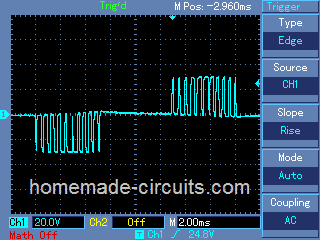
(Courtesy: Mr. Robin Peter)
Please also see this 500 VA modified sine wave design, developed by me.
Parts List for the above IC 555 pure sine wave inverter circuit
- R1, R2, R3, R8, R9, R10 = 10K,
- R7 = 8K2,
- R11, R14, R15, R16 = 1K,
- R12, R13 = 33 Ohms 5 Watt,
- R4 = 1M preset,
- R5 = 150 K preset,
- R6 = 1K5
- C1 = 0.1 uF,
- C2 = 100 pF,
- IC1 = TL 072,
- IC2 = 555,
- T1, T2 = BDY29,
- T5, T6 = TIP 127,
- T3, T4 = TIP122
- Transformer = 12 – 0 – 12 V, 200 Watts,
- Battery = 12 volts, 100 AH.
- IC 555 Pinout
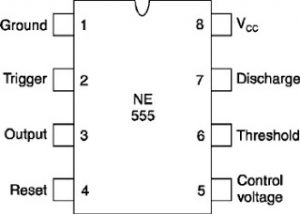
IC TL072 Pinout Details
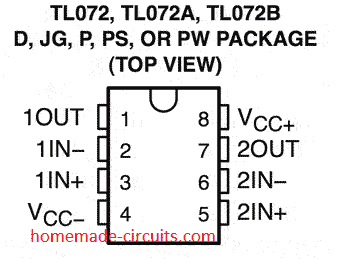
SPWM waveform stands for sinewave pulse width modulation waveform and this is applied in the discussed SPWM inverter circuit using a few 555 ICs and a single opamp.
4) Another Sine wave Version using IC 555
In one of my earlier posts we elaborately learned how to build a SPWM generator circuit using an opamp and two triangle wave inputs, in this post we use the same concept to generate the SPWMs and also learn the method of applying it within a IC 555 based inverter circuit.
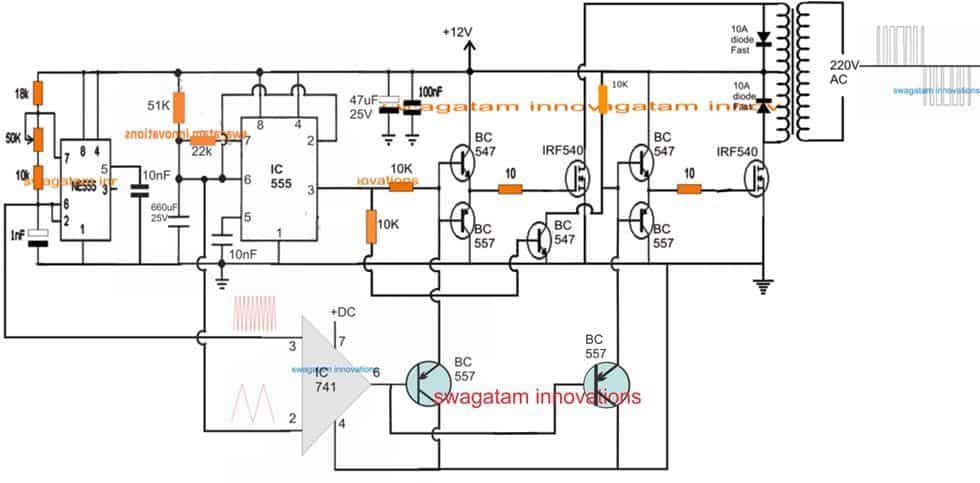
Using IC 555 for the Inverter
The diagram above shows the entire design of the proposed SPWM inverter circuit using IC 555, where the center IC 555 and the associated BJT/mosfet stages forms a basic square wave inverter circuit.
Our aim is to chop these 50Hz square waves into the required SPWM waveform using an opamp based circuit.
Therefore we accordingly configure a simple opamp comparator stage using the IC 741, as shown in the lower section of the diagram.
As already discussed in our past SPWM article, this opamp needs a couple of triangle wave sources across its two inputs in the form of a fast triangle wave on its pin#3 (non-inverting input) and a much slower triangle wave at its pin#2 (inverting input).
Using IC 741 for the SPWM
We achieve the above by using another IC 555 astable circuit which can be witnessed at the extreme left of the diagram, and use it for creating the required fast triangle waves, which is then applied to the pin#3 of the IC 741.
For the slow triangle waves we simple extract the same from the center IC 555 which is set at 50% duty cycle and its timing capacitor C is tweaked appropriately for getting a 50Hz frequency on its pin#3.
Deriving the slow triangle waves from the 50Hz/50% source ensures that the chopping of the SPWMs across the buffer BJTs is perfectly synchronized with the mosfet conduct ions, and this in turn ensures that the each of the square waves are perfectly "carved" as per the generated SPWM from the opamp output.
The above description clearly explains how to make a simple SPWM inverter circuit using IC 555 and IC 741, if you have any related queries please feel free to use the below given comment box for prompt replies.
5) Transformerless IC 555 Inverter
The design showing below depicts a simple yet very effective 4 MOSFET n channel full bridge IC 555 inverter circuit.
The 12 V DC from the battery is first converted into 310 V DC through a ready made DC to AC converter module.
This 310 VDC is applied to the MOSFET full bridge driver for converting it into a 220 V AC output.
The 4 N channel MOSFETs are appropriately bootstrapped using individual dide, capacitor and BC547 network.
The switching of the full bridge section is executed by the IC 555 oscillator stage. The frequency is around 50 Hz set by the 50 k preset at pin#7 of the IC 555.
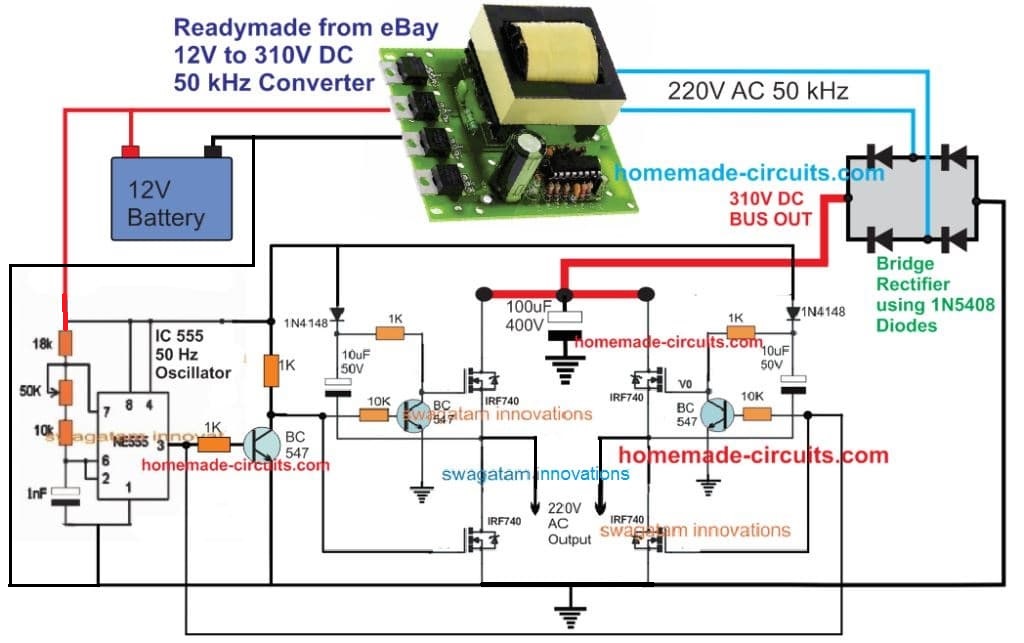
6) IC 555 Inverter with Automatic Arduino Battery Charger
In this 6th inverter design we use a 4017 decade counter and a ne555 timer Ic are used to generate a sinewave pwm signal for the inverter and an Arduino based automatic high/low battery cut-off with alarm.
By: Ainsworth Lynch
Introduction
In this circuit what actually happens is that the 4017 outputs a pwm signal from 2 of its 4 output pins which is then chopped up and if the proper output filtering is in place at the secondary side of the transformer it takes the shape or close enough to the shape of an actual sine wave form.
The first NE555 feeds a signal to pin 14 of the 4017 which is 4 times the required output frequency that you need since the 4017 switches across its 4 outputs, in other words if you need 60hz you would need to supply 4*60hz to pin 14 of the 4017 IC which is 240hz.
This circuit has an over voltage shutdown feature, under voltage shutdown feature and a low battery alarm feature all that is done by a microcontroller platform called the Arduino which needs to be programmed.
The program for the Arduino is straight forward and has been provided at the end of the article.
If you feel that you won’t be able to complete this project with the micro controller added it can be omitted and the circuit will work just the same.
How the Circuits Works
This IC 555 Inverter with Arduino Hi/Low Battery Shutdown Circuit can work from 12v, 24, and 48v going to 48v an appropriate version voltage regulator would have to be selected and the transformer sized accordingly also.
The Arduino can be powered with 7 to 12v or even 5v from a usb but for a circuit like this it would be good to power it from 12v as not to have any voltage drop on the digital output pins which is used to power a relay which turns on the Ic in the circuit and also a buzzer for low voltage alarm.
The Arduino will be used to read battery voltages and it only works from 5V DC so a voltage divider circuit is used I used a 100k and a 10k in my design and those values are plotted in the code that is programmed in the Arduino chip so you have to use the same values unless you made modification to the code or write a different code which can be done since the Arduino is an open source plat form and its cheap.
The Arduino board in this design is also connected up with an LCD display 16*2 to display battery voltage.
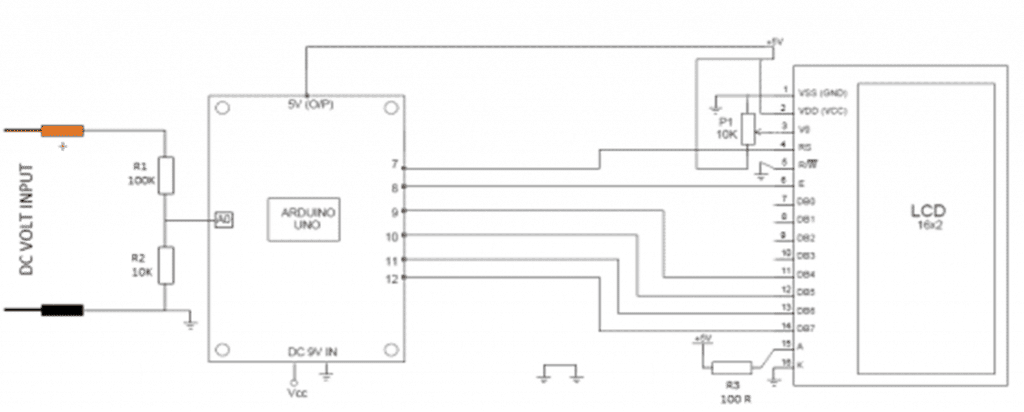
Below is the schematic for the circuit.
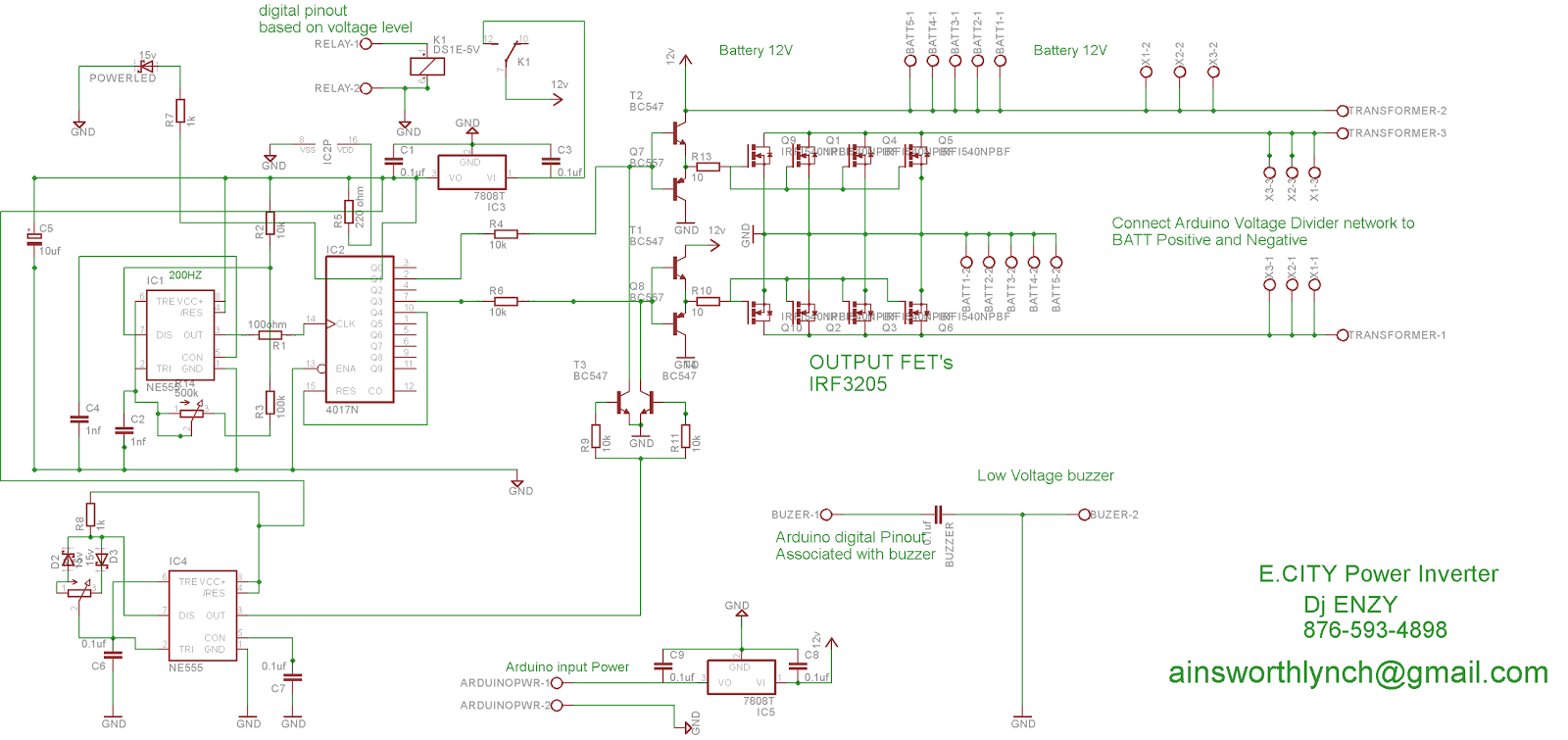
Program for the Battery Cut Off:
#include <LiquidCrystal.h>
LiquidCrystal lcd(7, 8, 9, 10, 11, 12);
int analogInput = 0;
float vout = 0.0;
float vin = 0.0;
float R1 = 100000.0; // resistance of R1 (100K) -see text!
float R2 = 10000.0; // resistance of R2 (10K) - see text!
int value = 0;
int battery = 8; // pin controlling relay
int buzzer =7;
void setup(){
pinMode(analogInput, INPUT);
pinMode(battery, OUTPUT);
pinMode(buzzer, OUTPUT);
lcd.begin(16, 2);
lcd.print("Battery Voltage");
}
void loop(){
// read the value at analog input
value = analogRead(analogInput);
vout = (value * 5.0) / 1024.0; // see text
vin = vout / (R2/(R1+R2));
if (vin<0.09){
vin=0.0;//statement to quash undesired reading !
}
if (vin<10.6) {
digitalWrite(battery, LOW);
}
else {
digitalWrite(battery, HIGH);
}
if (vin>14.4) {
digitalWrite(battery, LOW);
}
else {
digitalWrite(battery, HIGH);
}
if (vin<10.9)) {
digitalWrite(buzzer, HIGH)
else {
digitalWrite(buzzer, LOW
lcd.setCursor(0, 1);
lcd.print("INPUT V= ");
lcd.print(vin);
delay(500);
}
For more info you may feel free to express your queries through comments.
Have Questions? Please Leave a Comment. I have answered over 50,000. Kindly ensure the comments are related to the above topic.
Thanks for your reply Sir.
I have made inverter using 555 timer and bc547 B transistor
Sir, I used 24-0-24 ,230V transformer I m getting 50 V output instead of 230 is it because I have not used 9-0-9 transformer?
Hi Dweep, yes that’s exactly why you are getting a reduced voltage output, please make it 9-0-9v, or at least 12-0-12v
Hi there! I love these circuits, they’re close to something I need. I have a range of 6V, 9V, 12V DC wall power adaptors… one of my devices needs a 9V AC adaptor, so I’m trying to find a simple 555 circuit that will produce about 9VAC, up to 300mA. All of the circuits I’ve found include a transformer to convert to 110-220V which is too much.
Do you have a circuit that could do low voltages AC?
(than kyou)
Hi, you can try the following design for converting 9V DC to 9 V AC
Thank you! I will give this a go.
Thank you too for replying very promptly. Have a great day
I am 73 and been in electronics for 50 years built my first 8080 based system in 1978. 2 deg’s aeronautics and computer science. Been in software most of life. done lots of repair work but have some UPS system that need repair, APC, Tripp-lite, and have not a clue what part of the basic block dia. to look for the most likely failure point. Have used logic probes on digital circuits before, does not help here. I know from previous experience that there is always a single part of failure that is higher probable then others, ie. power supply’s for most electronics. I am sure given more time I could find the problem but hoped you could give a hint where to look first. Feel I should have known this. Spent many years building ranch, training horses, and building barns, houses, etc. So time has been short for Hobbies (HaHa). Designed and build Ham Radio Equip. So some experience.
Thank you for sharing your experience in the field of electronics. I appreciate it. I truly wish I could help you, however without checking the entire circuit configuration of the UPS it may be quite difficult for me to suggest the exact fault.
Thanks sir, regarding your last comment, after connecting the diodes individually to each mosfet gate say for example we used 6 mosfets, 3 each separately are we going connect the whole diodes from each gate together through a common wire and take it singly to the Bc547 collector or are we going to connect the diodes together as they’re in threes and get two common wires to connect to the Transistor collector, sir pls if possible use a diagram to show us this
Then lastly sir, can we use this feedback circuit in any inverter using n channel mosfets or npn transistors because the article said that it’s applicable only to inverters with N channel or NPN transistors. Thanks.
Individual diodes will be necessary only if you are using separate resistors on each gate. So the anodes of the diodes will connect with respective mosfet gates, and the cathodes of all the diodes will join together and connect with the collector of the BC547 transistor of the inverter correction.
The feedback circuit can be used with all inverters having N channel mosfets.
Hello sir, good day I have gone through the write-ups you sent to me and I must confess that they are very helpful.
I have gotten the ones I need and joined them with the relevant inverter circuits and I want you to pls help me confirm that they will work so that I won’t make costly mistakes.
http://www.dropbox.com/s/gafkpcs5hpt27r3/inverter-output-voltage-corrector-circuit-1.png?dl=0
http://www.dropbox.com/s/f61n6zzcyh79mwy/screenshot_20211224-142052.png?dl=0
I sent you two circuits diagrams the first is an inverter circuit using irfz44 mosfets and TIP41C transistor. The second diagram is the diagram of the automatic feedback control circuit I integrated with the inverter circuit. Pls I want you to help check if joining both circuits together appropriately is okay and will work fine producing 50hertz and 220v A.C. I will give a detailed explanation on how I joined the two circuits for you to understand.
From the first diagram the points out for mosfets were connected to the gates of the two set of the IRFZ44 mosfets of the inverter ( diagram 2).
Then the sides out for 12v d.c. + and minus in diagram 1 were connected to the inverter’s ( diagram 2) 12v +& – terminals.
Then lastly the points out for the transformer from diagram 1 were connected to the output side ( 220v) of the inverter ( diagram 2) transformer. Pls check if these arrangements will work fine and if the inverter will sine wave a.c. Thanks.
Michael, I have explained the entire process and the connection details in the relevant article, if you are facing any problems you can ask me, I will tell you how to do it.
For multiple mosfets you will have to connect individual diodes from each mosfet gate to the BC547 collector.
Sir I have resent the message, pls check your spam folder. Thanks.
http://www.dropbox.com/s/oowqvbiddeskn4a/screenshot_20211224-142052.png?dl=0
http://www.dropbox.com/s/sjniqm8m3ie0cok/screenshot_20211223-161034.png?dl=0
http://www.dropbox.com/s/gox0rr8334ju7bg/screenshot_20211223-161200.png?dl=0
http://www.dropbox.com/s/xpq0sdacbfbahxu/screenshot_20211223-161121.png?dl=0
Sir I signed up on Dropbox, afterwards downloaded thier app and uploaded the images there, but you can view them using chrome. The third and fourth links are same circuits.
Like I wrote to you in my previous comments, all I want you to do is to help me to add the pure sine wave or modified sine wave and automatic feedback control circuits parts or diagrams to the circuit images I sent to you. Thanks and remain blessed as you do this. Compliments of the season ✨
Michael,
I already have all these information posted in this blog.
You can refer to the following post for learning how to convert an SG3525 inverter into pure sinewave……you can also get the feedback design in the 3rd circuit diagram from top:
https://www.homemade-circuits.com/sg3525-pure-sinewave-inverter-circuit/
For 4047 you can refer to the following post
Pure Sine Wave Inverter Circuit Using IC 4047
for general purpose feedback control, you can refer to the following article:
Automatic Inverter Output Voltage Correction Circuit
Ok sir, so sorry for the inconveniences, let me reduce it to three circuits only, pls sir how am I going to send the links to you and you will get them and they will be opening, because it’s giving me a lot of trouble here trying to find a way to send them to you and they will work. Thanks
You can upload it to any free image hosting site online, and provide the link here, if it is easy and feasible for me I will try to solve it for you.
Please remove the https while sending the links.
Ok sir, thanks, I have sent 6 different links for 6 inverter circuits just before this particular comment. you can view them using chrome or drive. The fifth and sixth circuits are same but they aren’t joined together, that’s why I made two different links for them
Sir pls all I want you to do is to help me to make these circuits pure sine wave inverters especially the first one and then add automatic feedback control to each of them if you can make the first one a pure sine wave inverter and others modified sine wave, I will be grateful for it, but if you can have time to make all the circuits pure sine wave, I’d be more grateful ????????????????, I know you’re a very busy person. Thanks again for doing it. Pls join the diagram of the pure sine wave/ modified sine wave and automatic feedback control circuits to each of them ( the inverter circuits below) so that I can understand it well
Concerning the second circuit link, pls it looks like this a modified sine wave inverter, am not sure, if it’s not pls help me to convert to pure sine wave/ modified sine wave like the others.
Thanks very much sir for getting out time to do this
Hello Michael,
first of all the links are not working because they are not shared.
Second thing is that I cannot join them because that would be a lot of work and time consuming for me.
Sir pls I have sent multiple replies, I don’t know if you have gotten any of it, if not pls send me your email lemme send the message directly through it. Thanks
Michael, I prefer discussing through comments, so you can send the details here, I will try to figure it out.
Sir I have sent you the for the circuit diagram as you requested using same email am using to send this message
Sorry Michael I did not get any email. Alternatively, you can upload it to any free image hosting site and provide the link here. Make sure to remove the https from the link.
Hellow Mr swagatam.,
how can I add LC pass filter to the 4th sine wave inverter before the transformer output in a half bridge inverter.?
Hi Micheal, according to me there’s no need to connect an inductor, because the transformer secondary itself acts like an inductor. You can simply add a 3uF/400V PPC capacitor across the output wires and that will transformer the SPWMs into pure sine wave.
Thank you very much Ing… .. I made the simplest square wave inverter and it works very well, from a probe and it works, then I will add it to be a sine wave…
http://1.bp.blogspot.com/-z9RRPSTi8zs/UbR4uKyuLRI /AAAAAAAAESo/rGu-sAhOqio/s1600/IC%204047%20inverter%20circuit.jpg I
ask: I don’t have an oscilloscope for now
. on pin 10 and 11 = 50 hz and on
pin 13 = 100 hz. del ic = 4047… .service ,, leave there .. ??
2- To adjust the frequency of 2 khz in pin 2 of ic2 555, I can adjust with a Digital multimeter .. ??
3- I wind my transformers, could I increase my 220vac turns to compensate for the voltage drop when adding the load, .. at what voltage could I increase in my calculation…?
Glad you could make the inverter successfully.
pin#13 can be left open.
you can adjust the frequency by keeping the meter probe pin10 and ground, or pin11 and ground
you can increase the secondary turns to increase the output voltage, but increasing voltage will reduce current which will again lead to voltage drop if the load is high.
Muchas gracias Ing….creo que me exprese mal,,,
Hice el inversor de onda cuadrada más simple y funciona perfecto, luego lo agregaré para ser onda sinusoidal….pero necesito saber para proseguir ,,se que para ver la forma de onda es imprescindible
1- Puedo ajustar con un Multímetro Digital la frecuencia en el pin 10 y 11 con respecto a tierra.del 4047..?? de hecho así ajuste el 1er inversor que mencione..o debería hacer con Osciloscopio..?
2- Como queda para ajustar la frecuencia de 2 khz en el pin 2 del ic2 555, puedo ajustar con un multímetro digital..?? o para esta zona debería hacer con Osciloscopio..?
Yes, You will need an oscilloscope to confirm the waveform.
1) To adjust the frequency you can use a multimeter (set at frequency range), across pin10 or pin11 and ground. Oscilloscope is not required.
2) For iC 555 also you can use a multimeter (set at frequency range) to adjust the frequency at pin#2. Oscilloscope won’t be required here too.
Mil….Gracias..Ing….. pregunto..para avanzar ,,cada ítem por favor !
1- Puedo ver la forma de onda con el programa Goldwave..en mi pc.
2-Cómo le inyectó la señal al MIC (Micrófono)., a través de qué.? transformador con baja espira 1Vac, sería señal alterna. o le aplico señal del integrado al la entrada de MIC (Microfono)..
3- Antes de usar el Goldwave para ver la señal del inversor,, podría probar para ver la señal de un transformador 220Vac -en el secundario le agrego 1 a 3 espiras q me de 1 Vac o menos..
You are welcome!
1) yes, Goldwave can be used for seeing the waveform.
2) Sorry I did not understand the use of MIC with an inverter?
3)Yes 220V transformer secondary can be checkd in any pc software through a high value resistor.
Ing,mil gracias y disculpe la falta de comprensión,,Pregunto,,para ver la ,forma de onda con el programa Goldwave.,
Cómo le inyectó la señal a la entrada del Micrófono de mi pc,,.?
1- segun entendi, antes de meter señal a la entrada del Micrófono de mi pc debo usar con una resistencia de alto valor, así verificare la señal de cualquier secundario de transformadores de 220 V y de paso ya veré la salida de mi transformador inversor,,,,
2- Para ver la forma de onda de los 555 uso resistencia,,?,o es directo sin resistencia..? que valor será ..?
As far as I remember, the input voltage to the PC MIC socket for operating Goldwave should be 1 V peak to peak.
So you may have to use a potential divider and step down the AC voltage to 1V and then feed it to the MIC socket, for sending the signal to Goldwave.
EXELENTE SITIO….podrías decirme Ing..cual de los 6 circuitos u otro , me recomendaría usar para encender tubos fluorescentes tengo desde 5w a 40w necesito circuitos para 12Vdc y 220Vac
Thank you and glad you liked the concepts. You will have to use a sine wave inverter for operating a fluorescent tubelight, so that it works without noise. You can make the 555 sine wave version of the inverter, or you can also go with the second 4017 schematic from the following article, which is much easier modified sine wave inverter and will give fairly good results:
https://www.homemade-circuits.com/modified-sine-wave-inverter-circuit-2/
Sir swagatam,about first basic design circuit, what size of mosfet can be use to get a 5000w ac output?
Luis, MOSFET is a secondary thing, first you will have to dimension the transformer ad the battery appropriately, then the MOSFET can be selected accordingly:
Calculate Battery, Transformer, MOSFET in Inverter
ok thanks for the answer sir
Dear Sir,
In your no 4 sign wave inverter circuit (Another sign wave version using ic 555) where you used two 555 timer ic one 741 opamp and two irf540 power mosfet, what will be its max watt if I use 12-0-12 5 amp transformer ? Can I use four 540 mosfet and same transformer for more watt and what will be its interchange of components ? If possible then plz send me the same circuit diagram.
Thanking you.
Hello Sekhar, MOSFETs are like switches, they only switch power they don’t increase power, the wattage or power is determined by the transformer and the battery…the MOSfET must be rate according to their max power. A 12V 5 amp will produce only 50 watt of power at the output
Dear Mr. Swagatam,
Do you recommend connecting transformers in parallel for use in an inverter application, since i have on hand two 500VA transformer units procured from old UPSes, both same in size, weight, input/output voltage and power.
The transformers have PRI 2 in pins and SEC 2 out pins.
My questions are:
1. Can i connect them in parallel with the idea of having a 1000VA power from it.
2. I have noticed that on paralleling the windings, the resistances of both stages drops down to much less than half of what each transformer had.
(To clarify: pri to pri and sec to sec together).
Still, for safety I never applied mains energy to the transformer setup i made.
3. Do paralleling two transformers for more output power dangerous for the inverter circuit either being made by hand or getting ready-made procured inverter cards.
4. Is this something sensible we can do or try? what about the heat distribution between them, if we setup the sufficient spacing and ventilation between them?
I do prefer making circuits from your site since i trust them from a great long time.
Dear Sherwin,
If the specifications of the transformers are reasonably equal then you can connect the primary sides in parallel in an inverter application.
But I won’t recommend connecting the secondary or 220V side in parallel, due to the risk of opposite polarity connection, and a slight mismatch in the specs might result in wastage of power.
So the primary DC side can be connected in parallel to the inverter, and the secondary side could be individually connected to separate loads.
Thank you for trusting my circuits, It’s my pleasure!
Sir.. One question from me.. If i can use 7ah 12v battery in any inverter cricuit like 200w or 500w then how much current flow to the
two point of transformer primary connection… If we have 12-0-12 transformer.. Please give me write current value sir..
Apurva, with 7Ah you can drive only upto 100 watt loads, if you exceed this then that will be harmful for the battery.
Divide the wattage with the battery voltage that will give you the current flowing through the wires.
Ok fine… One more thing also explain sir if i used 12-0-12 5amp transformer and the cricuit will made by 2 mosfet with pulse generators ic then how much wattage will give in output ac Current. if battery will have 7ah 12v…and also explain me how much current comes to the connection two point of the transformer into the cricuit??? …can i find that point maximum current to the battery amp.. Aur less…??
Multiplying 12 with 5 will give you the approximate output power from the inverter. But practically it could be much less than this result due to transformer inefficiency and false labeling.
Divide the wattage of the transformer with the battery voltage to get the approximate current flowing into the transformer winding
Current flowing into the winding of transformer will rated actual to amp of the transformer or different? Means if i have 300w transformer then the current will be 25amp into the transformer with a 12V battery?
In your example the 25 amp will be the maximum capacity of the transformer, but the actual current will depend on how much the battery can deliver into the transformer. And it will also depend on the load. smaller load will draw smaller current from the transformer, higher load will draw higher current, but this will ultimately depend on the battery capacity.
It means If the battery will be 7ah 12v and 10amp transformer then it’ll generate 120watt only. But this phenomenon does not occur with my ups. Because my computer ups glows 2 100w bulb for 15min and the transformer used in the ups is not more than 10amp because the core is (1inch) and bobbin size(1.5 sq inch) So how it is possible I cant understand.
I have already explained you that if you operate more than 100 watt with 12V 7Ah, the battery will get damaged, so it is not recommended.
the transformer that you are referring to could be a ferrte based transformer and not iron based therefore it looks smaller but could be rated with more capacity.
can i use 10amp transformer for 12v 7ah battery with any inverter circuit (where 2 or four mosfet will used)… Which give output power above the 200 watt or more for few min like 10 or 15 min can it is possible sir??
That can be never possible, a 10 amp 12V transformer will never produce 200 watts. Please respect the calculations and please do not give vague explanations.
Then how my computer ups gives above 200watt?
Did you verify the current and voltage with meter?
According ur last comment.(30 dec) i do and the result would be ok… Means led glow flashing type.. It means it is correct and and the voltage will vary like up and down in any point of cricuit like gate pin of both mosfet … But after connecting the transformer 12-0-12 then one mosfet will be heat in bc547 side and no ac power produced in output by tranformer… I cant understand why it is occur… Than i think mosfet will be damage but i check it… It will be ok.. And sir i used irf44n mosfet… Sir i ask one more question how much amp.. Tranformer used in this project… Please recommend me sir..
Apurva, It can be very difficult to know what mistake may be present in your assembly without checking it practically, so I cannot suggest anything from here.
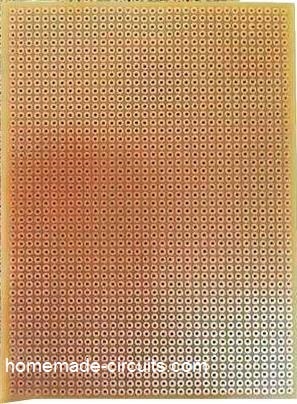
what have you used for joining the parts, is it a breadboard?…in that case remove the parts and build it again using strip-board like this one:
I could draw my project in ur given image of board.sir but can’t understand where it is occur problem.. And one also suggest me how much amp.. Transformer used in this project min and maximum both..
I suggested you to build it by soldering not to draw anything…the amp of the transformer can be 1amp to 5 amp.
I cannot troubleshoot your circuit because it will need practical checking
Yes sir i can draw by soldering.. And i could check it after the point come from pin 3 to all cricuit like bc547 pin,mosfet pin, every place by multimeter(setting the regulator into voltage)… Sir.. But cant understand why mosfet will heat.. Even one side… Please suggest me sir where i left to determine my fault..
Then don’t use mosfets, replace it with transistor like TIP31 or any similar
Then how it is connect sir.. Base emitter, and collector.. And can i use
mje 3055t transistor which are npn power transistor.. In place of it… And one more thing is both transistors are npn aur one npn and other is pnp… Give me a connection and suitable transistor name sir..please
I will try to update the diagram tomorrow, I think you should also try the first design from this article:
https://www.homemade-circuits.com/2018/06/7-simple-inverter-circuits.html
In ur pervious comment can i use tip31 transistor because it is available in my market…
yes you can, put heatsinks also on it
Sir.. In second diagram the resistance which are attached to zener diode what its value..10k aur 10ohms…which one is… Please comment me…
They are 10 Ohms 1/4 watt
Thanks sir…
You are welcome Apurva!
Sir in ur second diagram the 7v generates by the pin 3 of ic555 passes through the 10ohms and 9.v zener diode it show in gate of mosfet is 2.33v and other side 10k resistance it show 0. 33v which are connected to the base of bc547… But sir it not any effect on transformer and not any ac output generate in secondary side of transformer.. Please solve my problem sir…
Apurva, you can remove the zener diodes, I introduced them to create a separation between the conduction of the two mosfets….but basically you can remove it, and replace them with a wire link. I hope you have connected the diodes across the transformer winding as shown in the diagram. You can use 1N4007 initially
you can try this circuit also:
http://danyk.cz/menic230.gif
Sir can i do this one or second cricuit diagram because some component are different in ur given diagram and second cricuit diagram… Which one i do this… And one more thing can i remove zener diode from the cricuit and place IN4007 in place of IN5408… Then its work properly yes ya no… Please rply me sir…
Apurva, you can do whichever you feel easy, both will work. you can remove the zener diodes, and also you can use 1N4007 across the transformer winding.
Sir i do according ur comment but problem is that.. Is the one mosfet will be heat and the voltage on gate will be same as pin 3 voltage of ic 555 and another mosfet where bc547 where connected there are no any voltage show on gate pin of their mosfet… Why it is occur please shot out this problem sir… I remove both zener diode and in 5408 in place of 1n4007…
It means your IC 555 is not oscillating. First make a simple iC 555 flasher to confirm whether it is oscillating or not. disconnect everything from pin#3 of the IC and connect an LED from pin#3 to ground through a 1K resistor.
Also replace the pin#6/2 capacitor with a 10uF
now the led should blink, if not then your IC 555 circuit has some fault….first confirm this.
Sir i use irfz44n mosfet in place of irf540n… I think no problem from that… Please rply me on both comments sir…
yes it will also work…
Ok sir i’ll do it!
Can i use full bridges pwm inverter cricuit digram in my project… Where transformer is without centertape..in ur second cricuit diagram….
do you mean 3rd diagram from top?
Yes where heading is (ic 555 full bridges inverter cricuit)… Can i use it my project without any doubt…
Apurva, yes this is much easier, but you will required two batteries.
And also rply me sir.. why ur msg not come in my email id… Which are used in the email box below the comment, name box
Please check your spam folder, or junk folder of your email….and let me know whether the emails are reaching you.
Rply me sir can i do with single12v 7ah battery…
Please see the diagram there are two batteries.
Rply me sir can i do with single battery.. Aur any modification in cricuit for single battery system… Please help me sir
Single battery will not work, and no other modification is possible in this design for single battery operation.
BUT how dose the ofset Adjust work in the given link and how to adjust it ?
you can correct the offset null issue by connecting a 10K preset across pin#1,5,4 of the IC, connect the outer leads of the preset with pin# 1 and pin#5, and connect the center lead with pin#4
OK SIR THANKS
Good day sir,
Please the circuit shown above for 555 timer inverter if I convert it DC TO DC Boost, by replacing with ferrite transformer, and make it at 12v input to achieve 310v output, sir you can see at the time of running the H-bridge inverter the input voltage to dc to dc will ten to decrease to say 11v, likewise the rectified DC of 310v will ten to decrease also, so in this case how do I make a feedback voltage with 555 to increase the pwm automatically to achieve exactly 310v at the state of 11v decrease from 12v input to dc to dc boost?
Kabir, you may have to employ the concept which is used in the last diagram from this article
https://www.homemade-circuits.com/simple-solar-mppt-circuit-using-ic555/
build the IC1, IC2 and the 741 stage only, and replace this over the existing IC 555 pwm in the above article.
the pwm from pin#3 then can be used for controlling the inverter output.
the 741 input can be acquired by creating a resistive divider across the inverter 220V output such that around 12V is sent to the 741 input and this must correspond to 220V across the inverter output, now if the 220V tends to rise, the PWM will be forced to get narrower and vice versa.
Dear Swagatam,
Thank you so many for your prompt answer, and for all you do in this site. Are you saying that the output of the second circuit is a square waveform? (you wrote in the description of the circuit that it generates a sine waveform, which I interpret as a PWM image of a sine waveform) ?
Dear Michael,
PWM is standard digital method for creating pure sinewave in all sinewave inverters. But ideally it is an SPWM which interprets into perfect sinewave at the output.
However that may be true only if a transformer is used or through the use of inductors and capacitors.
Having said this, even without inductors or filters When an SPWM is used the load will ultimately interpret the input as a sinewave, although a slightly crude one.
Therefore, the second circuit should ideally have an SPWM input instead of a uniform PWM, as shown in the diagram.
Dear swagatam,
In the second circuit, I don’t understand how the IC 555 can causes the circuit to generate a pure sine wave, that is, how it generates the correct PWM. Can you explain that?
Dear Michael, since no trafo is used a pure-sine would be difficult to obtain, however you can add an LC filter across the output to actually carve the waveform into a sinewaveform, you can refer to the following similar concept which will help to understand the waveform transformation at the trafo output side.
https://www.homemade-circuits.com/modified-sine-wave-inverter-circuit-2/
Please tell how zener diode works to achieve dead time.
zener diode ensures that the transistor conducts only once the trigger voltage crosses the zener value, until then the transistor remains switched OFF
Thanks for your very prompt reply. Your circuit are very useful and helpful. Your ideas use simple circuits but it does very fantastic job.
You are most welcome satyavijay, I’m glad you found it useful
Dear Swagatam,
Thank you so much for your reply. Yes, you are so right. The lift didn’t go to to the top floor before, but now my H-bridge light is finally switched on.
Regards, Reitz
You are most welcome Reitz!
Dear Swagatam
I have a question about the centre tap of the primary winding. I understand how and why the transformer is working. Noting the following from your design explanation:
” The zener diodes at the gates of the mosfets introduce a slight delay time or dead time between the mosfet conduction and inhibits any possibility of both mosfets getting engaged together even for a fraction of a second.”
As the mosfets cannot conduct together, would it then be possible to use this circuit on a coil without a centre tap, connecting the drains of both the mosfets to one side of the coil and the other side of the coil to +12V? I’m asking because I’m contemplating a 12VAC circuit to drive a de-magnetising/degaussing coil. I have a core from a old 12VDC auto solenoid handy which I want to use. Probably would have to up the frequency somewhat.
Thank you for a great site. I learned a lot from reading the comments and your replies
Reitz
Thank you Reitz,
The method that you have imagined can be simply applied using a single mosfet and a single output oscillator such an IC 555, however that will not produce a push-pull effect, which becomes rather the main purpose of using full bridge networks.
by using a single mosfet, single winding topology you can eliminate the center tap mess, but the output from the secondary will be a one-sided waveform, and not an AC waveform.
I hope you got the point.
THE PWM 555 IN THE LOWER DIAGRAM, WHICH HELP THE IC IRS2453D TO PRODUCE SINE WAVE
It should be set to minimum 200Hz, 55Hz will not give correct result
Sir what is the effect if to say I leave it around 50Hz to 55HZ for the 555 timer at pin3 and the IC IRS2453D kept at 50HZ?
Kabir, which 555 IC you are referring to? the first 555 or the PWM 555 in the lower diagram?
Sir,
I have change the 1k and c2 and successfully achieved 50HZ; but the problem is that the frequency is not staying at 50HZ fixed, its fluctuating to 55HZ When ever power is switch off and switch on again, when you measure again you will see it change from 50HZ to around 55Hz. therefore you have to reset it again. Help.
Kabir, where did you measure the frequency? please check it at the 555 IC pin#3….or you can replace the preset with a fixed resistor for permanently fixing the value.
Sir,I have refer to the link; If I replace the zener with 15v, does the resistor 10k 1/2watt need to be change or not? or that 9v 1watt zner will give me 15v out put?
Kabir, the output voltage at emitter will be around 0.6V less than the zener value.
the 15K can be used for 15V zener also….this resistor determines the emitter current and a safe operating current for the zener.
Sir, how can I get 12v out of 60v from solar panel to drive my circuit, as you used 33k 10watt R in the full bridge side and get 15v? I have used 33k 10watt but the supply voltage is 60v, therefore I got 15v out, when I connect to the circuit the voltage dropped to 1v and the circuit did not function, I suspect the supply voltage differences that result in to this, Help.
Kabir, you can do it using a BC546 emitter follower transistor as shown in the following figure:
https://www.homemade-circuits.com/2014/11/48-v-inverter-circuit.html
Good day sir, pls I want to share some circuit diagrams with you for you to help me to answer some questions on them, pls how am to share it or send them to you. Thanks.
Michael, sorry there’s no image upload facility in this comment section, so at the moment it is not possible to discuss external diagrams. You can try google drive sharing, however sending any sort of link through comments here will cause the comment to go into the spam folder.
Thank you sir for your reply sir but pls can I upload them directly from my email app for you to see pls.
You will have to provide me the link here so that I can check it out. After posting the link write another comment informing me about it so that I can retrieve it from the spam folder.
Sir, so at which frequency for the 555 timer suppose to give to the full bridge state for acquiring 5HZ output?
It will be the same frequency, that is 50Hz which needs to be set for the IC 555, preferably at a 50% duty cycle.
this duty cycle can be changed for adjusting the RMS value of the output AC
Kabir, both the pots are for PWM setting, the adjoining 1K resistors and the C2 cap can be tweaked for adjusting frequency.
Sir,
in the full bridge side, there is 2 pot, please which one is for setting the frequency, and how to set the other one for duty cycle? already I have frequency meatre .
May Allah bless you and protect you from unforeseen menace amen.
Thank you Very Much.
you are welcome, and may God bless you too!
SORRY FOR MY TOO MUCH QUESTION .
CAN I USED BUCK CONVERTER TO MAXIMIZED THE OUTPUT CURRENT AND STABILIZED THE VOLTAGE TO THE REQUIRE VOLTAGE LEVEL OF MY FERRITE CORE BEFORE FEEDING IT TO FULL BRIDGE SECTION?
buck converter is not required, reduce the output winding appropriately…..
THANKS FOR YOUR REPLIES :And That is very correct Sir.
I have change the Zen diode from 7v to 3.5v, and it successfully drive my IRFP450, and for the Trf winding I have change the SWG to 30swg 10 (strand) 5o tune for primary and made 40 tune 5 (strand) for the secondary with thinking that the output voltage will reduce, but nevertheless the voltage remained as its (230v dc WHEN I APPLY 12V INPUT) And if I move to 24v the output increase to 430. and my intention is to Apply direct 60v from solar panel.that is at this stage when I apply 60v the output will be up to thousand voltage. but in your 555 timer booster, your primary tune is 50 and the secondary tune is 200. and that is exactly for my first winding and achieve 320v dc when I apply 12v, that is why I change the secondary winding to 40 tune with intention to reduce the voltage. HELP
the primary winding should be preferably equal to the supply voltage…for 60V you must use 60 turns. for reducing the output voltage you can reduce the the turns in the output winding.
Thank you Sir,
Sir, if I change the capacitor value at the output of my Ferrite trsf,that is from 22uf/400 to 2200uf/450 What will be the effect of my output; its capacitance change or there should be a modification in the output load?
Kabir, The output response will improve if the filter capacitor value is increased, but the output voltage might increase because of this which will need to be corrected using the PWM adjustment. the output load will not require any change.
Sir, I have noticed my problem, that IRF547 In the circuit, I have replaced it with IRFP450, which prevent the circuit to work; later I just refer back to your 555 timer DC to DC boost converter, I just eliminated that 10k and 9v z from the circuit and the circuit is now working perfectly. But I tested it with 12v battery and achieved 320v DC out put. Sir my question is when I use 60v input from the solar panel, the output voltage will change or not? My ferrite core primary winding is 50 tune with 5 strand 20swg and the secondary 200 tune with single 20swg. You can see that I have altered your specification OF SWG in the circuit; this is because I determined the output load of my inverter and maximum current for the wire gauge, that 0.5mm seem like can not carry high load of current, and that 1.00mm can not carry high input current. But if I when wrong base on my assumption please correct me.
Hi Kabir, the 9V zener could be reduced to some lower value, say 4.7V etc because the zeners help to achieve a dead time which is important for the inveter's safe functioning…anyway for a 60V input, the tafo will need to be dimensioned accordingly and the winding could be altered to get any desired output from the design.
instead of using single thick wire it's better to use many thin wires in parallel for a much efficient response….instead of 20SWG, try a few strands of 30SWG in parallel.
….and make sure that the IC 555 gets 12V for operating and not 60V.
rest everything may be OK.
instead of 5 strands of 20SWG try 10 strands of 30SWG etc…
please sir help me as urgent,
I have build the first circuit but before testing i will like to insure the curret polarity of the zener diode, as you said the mosfit will conduct base on the negative and positive pulse of the 555 timer, so by looking at the circuit you can see that the zener diode is facing positive all of them to the mosfit, that is at a positive pulse one of the mosfit will not conduct. or the are as it is. Help
Kabir, the zener diodes in the first circuit are correctly placed.
the positives from the emitters of the BC547s will enter through the zener cathodes and reach the mosfet gates.
zener diodes do not work like rectifier diodes.
thanks for ur reply sir, hope u r doing well.i have some questions .which circuit should i use ? what is the transformer & battery ratings ? is that a sine wave or square wave inverter??
if you integrate the second circuit, then it will become a sinewave.
transformer and battery rating can be as per your inverter power requirement…
sir, i have made this on proteus but haven't got the desired output yet could u check it plz ?? i have to make an 100 watt inverter for my university project .need ur help sir
asad, sorry I cannot verify a software interpretation, but I can guarantee that this inverter will perform as specified when built practically without errors..
Hello sir, can you pls help me with 12v dc to 60v dc 100w circuit diagram please. Thanks
Hello ERic, you can try the second circuit concept from the following article
https://www.homemade-circuits.com/2014/05/generating-electricity-from-road-speed.html
hello sir,
Best wishes
sir, can you help me make an inverter circuit with an ac voltage pulsed out of 500watt, so if out burdened by 500watt light the lamp may blink and blink rhythm can be set using a potentiometer with a frequency of at least 50Hz maximum out 100hz.
thank my regards
hello ningrat, sorry I could not properly understand your requirement and the application need of the circuit
Sorry sir if it is so contrary to you due to certain factors, actually I wanted to create a series of electrofishing to output a pulsed ac voltage, …
once again please forgive me if my request is contrary to your
my regards
Ningrat, you mean to say you want a 220V generator circuit having a variable frequency adjustment??
Chucks, you can use 2N2222 in place of 2N3053