In this post I have explained how to make small homemade induction heater circuit for laboratories and shops for carrying out small scale heating jobs such as melting ornaments, or boiling small quantity of liquids using electricity or battery The idea was requested by Mr. Suni and Mr. naeem
- Circuit Objectives and Requirements
- Our challenge is to make an induction circuit for use from 12 V to 24 V with a flat spiral that can get half a liter of water to boil in as little time as possible.
- The primary goal is to get induction circuit to work but there are other challenges that are described below.
- The container in which the water should be boiling is of double-walled stainless steel and is insulated and the distance between the outer and the inner container where the induction works is about 5-7 mm.
- We have chosen induction in order to protect the electronic components from the heat of a conventional spiral heater coil which is possible when the tank is insulated.
- The outer container has a diameter of Ø 70 mm and the space for the electronic components is 20 mm high, so another challenge is to see if we have space for the components.
- In connection with the power supply there is connected a tilt switch which cuts the power to the induction loop in case the container is tilted 15 degrees or more. When the power to the induction circuit is interrupted this triggers an audio buzzer.
- Further, the induction loop is connected to two thermostats. One thermostat that interrupts power to the induction circuit when the water reaches boiling point and another thermostat that takes over to keep the temperature of the water at about 60 degrees - do not know if this will require a programmable circuit. I would also like to know if there are any infrared thermostats available.
- I know that this is a lot at once, but as mentioned, the primary aim is to get the induction circuit to work. Is it possible for you to send us a list of the necessary components and a diagram of the circuit.
- Looking forward to hear from you!
- Yours sincerely Súni Christiansen
- hello sir, i need a Induction Heater circuit diagram for our shop we have a silver jewelry shop
- so i want to silver melt and sometimes gold but if u send small circuit with transformerless power supply that will be good for me.
- I saw on internet very small project for induction heater but i cannot found power supply tansfomerless can you help me if u send both project Induction Heater and his power supply transformerless
The Design
In one of the earlier posts I have explained the basic method of designing a customized induction heater circuit by optimizing the resonance of the LC tank circuit, here we are going to apply the same concept and see how the proposed homemade induction heater circuit can be built for using in laboratories and jewellery shops.
The following figure show s standard induction heater design which can be customized as required by the user, as per their individual preferences.
Circuit Diagram
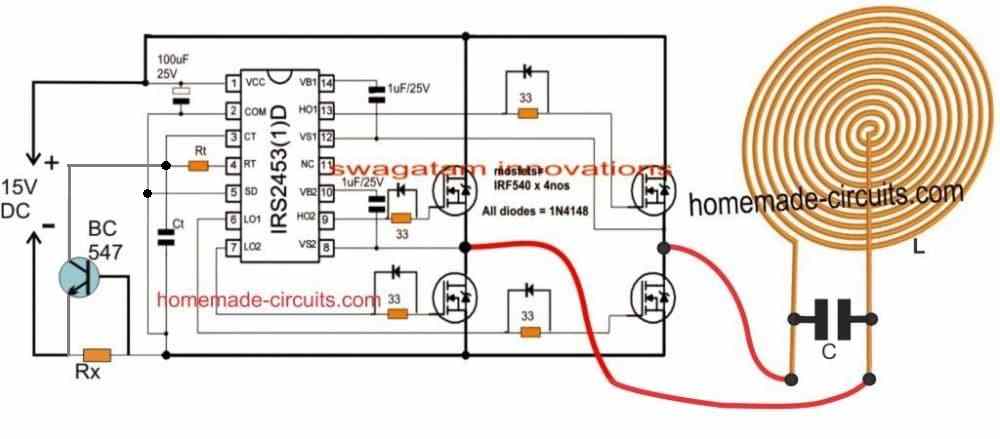
Circuit Operation
The entire circuit is configured around the popular full-bridge IC IRS2453 which indeed makes designing full bridge inverters extremely easy and foolproof. Here we use this IC for making a DC to DC induction heater inverter circuit.
As can be seen in the design the IC employs nothing more than 4 N-channel mosfets for implementing the full bridge inverter topology, additionally the IC involves an in-built oscillator and a bootstrapping network ensuring an extremely compact design for the inverter circuit.
The oscillator frequency can be adjusted by altering the Ct, and Rt components.
The mosfet H-bridge is loaded by the LC tank circuit using a bifilar coil which forms the induction work coil along with a few parallel capacitors.
The IC also incorporates a shutdown pinout which can be exploited for shutting down the IC and the entire circuit in case of catastrophic circumstances.
Here we have employed a current limiter network using BC547 transistor and configured it with the SD pin of the IC for ensuring a current controlled safe implementation of the circuit. With this arrangement in place, the user can freely experiment with the circuit without the fear of burning the power devices during the various optimization operations.
As discussed in one of the earlier articles, optimizing the resonance of the work coil becomes the key point for any induction heater circuit, and here too we make sure that the frequency is accurately tweaked in order to enable the most favorable resonance for our induction heater LC circuit.
It doesn't matter whether the work coil is in the shape of a spiral bifilar coil or a cylindrical coiled winding, as long as the resonance is correctly matched the result can be expected to be be optimal from the selected design.
How to Calculate the Resonance Frequency
The resonance frequency for the LC tank circuit can be calculated through the formula:
F = 1 / 2π x √LC Where F is the frequency, L is the inductance of the coil (with magnetic load inserted), and C is Capacitor connected parallel to the coil. Make sure to put the value of L in Henry and C in Farad. Alternatively you can also use this resonance calculator software for determining the values of the various parameters in the design.
The value of F can be selected arbitrarily, say for example we can assume it to be 50kHz, L can then be identified by measuring the inductance of the work coil, and finally the value of C can be found using the formula above, or the referred calculator software.
While measuring the inductance L make sure to keep the ferromagnetic load attached with the work coil, with the capacitors disconnected.
Selecting the Capacitor
Since a significant amount of current could be involved with the proposed induction heater for the lab works or for melting ornaments, the capacitor needs to be rated appropriately for the high current frequency.
To tackle this we may have to employ many numbers of capacitors in parallel, and make sure that the final value of the parallel combination is equal to the calculated value. For example if the calculated value is 0.1uF, and if you have decided to use 10 capacitors in parallel, then the value of each capacitor would need to be around 0.01uF, and so on.
Selecting the Current Limiter Resistor Rx
Rx can be simply calculated by using the formula:
Rx = 0.7/Max Current
Here, the max current refers to maximum current that may be permissible for the work coil or the load without damaging the mosfets and for optimal heating the load.
For example, if the optimal load heating current is determined to be 10 amps, then Rx could be calculated and dimensioned for restricting anything above this current, and the mosfets must be selected to handle in excess of 15 amps.
All these might require some experimentation, and Rx can be initially kept higher and then gradually lowered until the right efficiency is achieved.
Cooling the Work Coil.
The work coil can be built using a hollow brass tube, or a copper tube, and cooled by pumping tap water through it, or alternatively a cooling fan can be employed just below the coil for sucking out the heat from the coil from the reverse end of the enclosure. Other suitable methods can also be tried by the user.
Power Supply
The power supply unit required for the above explained induction heater for labs and shops can be built using a 20 amp, 12V transformer and by rectifying the output using a 30 amp bridge rectifier and a 10,000uF/35V capacitor.
Transformerless power supply can be unsuitable for an induction heater since that would require a 20 amp smps circuit which could be extremely costly.