Whenever PWM is employed in an inverter for enabling a sine wave output, inverter voltage drop becomes a major issue, especially if the parameters are not calculated correctly.
In this website you might have come across many sine wave and pure sine wave inverter concepts using PWM feeds or SPWM integrations. Although the concept works very nicely and allows the user to get the required sine wave equivalent outputs, they seem to struggle with output voltage drop issues, under load.
In this article I have explained how to correct this through simple understanding and calculations.
First we must realize that output power from an inverter is merely the product of input voltage and current that's being supplied to the transformer.
Therefore here we must make sure that the transformer is correctly rated to process the input supply such that it produces the desired output and is able to sustain the load without any drop.
From the following discussion we'll try to analyze through simple calculations the method to get rid of this issue, by configuring the parameters correctly.
Analyzing Output Voltage in Square Wave Inverters
In a square wave inverter circuit we will typically find the waveform as shown below across the power devices, which deliver the current and voltage to the relevant transformer winding as per the mosfet conduction rate using this square wave:
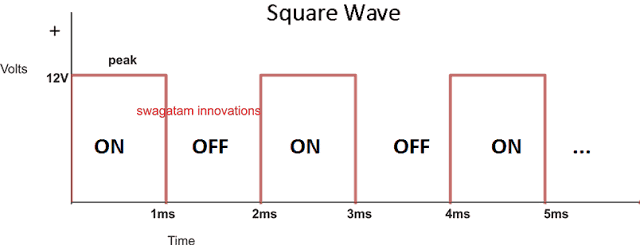
Here we can see that the peak voltage is 12V, and the duty cycle is 50% (equal ON/OFF time of the waveform).
To proceed with the analysis We first need to find the average voltage induced across the relevant transformer winding.
Supposing we are using a center tap 12-0-12V /5 amp trafo, and assuming 12V @ 50% duty cycle is applied to one of the 12V winding, then the average voltage induced within that winding and MOSFET drain can be calculated as given below:
12 x 50% = 6V
This also becomes the average voltage across the gates of the power devices, since the 50% duty cycle are applied to the MOSFET gates from the oscillator
For the two halves of the trafo winding we get, 6V + 6V = 12V (combining both the halves of the center tap trafo.
Multiplying this 12V with the full current capacity 5 amp gives us 60 watt
Now since the transformer actual wattage is also 12 x 5 = 60 watts, implies that the power induced at the primary of the trafo is full, and therefore the output will be also full, allowing the output to run without any drop in voltage under load.
This 60 watt is equal to the actual wattage rating of the transfomer, i.e. 12V x 5 amp = 60 watts. therefore the output from the trafo works with maximum force and does not drop the output voltage, even when a maximum load of 60 watt is connected.
Analyzing a PWM based Inverter Output Voltage
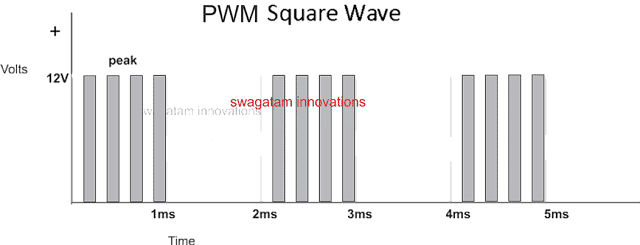
Now suppose we apply a PWM chopping across the gates of the power mosfets, say at a rate of 50% duty cycle on the gates of the mosfets ( which are already running with a 50% duty cycle from the main oscillator, as discussed above)
This again implies that the previously calculated 6V average is now impacted additionally by this PWM feed with 50% duty cycle, reducing the average voltage value across the mosfet gates to:
6V x 50% = 3V (although the peak is still 12V)
Combining this 3V average for both the halves of the winding we get
3 + 3 = 6V
Multiplying this 6V with 5 amp gives us 30 watts.
Well, this is 50% less than what the transformer is rated to handle.
Therefore when measured at the output, although the output might show a full 310V (due to the 12V peaks), but under load this might quickly drop to 150V, since the average supply at the primary is 50% less than the rated value.
To rectify this issue we have to tackle two parameters simultaneously:
1) We must make sure that the transformer winding matches the average voltage value delivered by the source using the PWM chopping,
2) and the current of the winding must be accordingly specified such that the output AC does not drop under load.
Let's consider our above example where the introduction of a 50% PWM caused the input to the winding to be reduced to 3V, to reinforce and tackle this situation we must ensure that the winding of the trafo must be correspondingly rated at 3V. Therefore in this situation the transformer must be rated at 3-0-3V
Current Specs for the Transformer
Considering th above 3-0-3V trafo selection, ans considering that the output from the trafo is intended to work with 60 watts load and a sustained 220V, we may need the primary of the trafo to be rated at 60 / 3 = 20 amps, yes that's 20 amps which the trafo will need to be to ensure that the 220V is sustained when a full load of 60 watt is attached to the output.
Remember in such situation if the output voltage is measured without a load, one might see a abnormal increase in the output voltage value which might appear to be exceeding 600V. This might happen because although the average value induced across the mosfets is 3V, the peak is always 12V.
But there's nothing to be worried about if you happen to see this high voltage without a load, because it would quickly settle down to 220V as soon as a load gets hooked up.
Having said this if users find it rattling to see such increased level of voltages without load, this can be corrected by additionally applying an output voltage regulator circuit which I have already discussed in one of my earlier posts, you may effectively apply the same with this concept also.
Alternatively, the raised voltage display can be neutralized by connecting a 0.45uF/600V capacitor across the output or any similarly rated capacitor, which would also help to filter out the PWMs into a smoothly varying sine waveform.
The High Current Issue
In the above discussed example we saw that the with a 50% PWM chopping, we are forced to employ a 3-0-3V trafo for a 12V supply, forcing the user to go for a 20 amp transformer just to get 60 watts, which looks quite unreasonable.
If 3V calls for 20 amps to get 60 watts, implies that 6V would require 10 amps to generate 60 watts, and this value looks quite manageable....... or to make it even better a 9V would allow yo to work with a 6.66 amp trafo, which looks even more reasonable.
The above statement tells us that if the average voltage induction on the trafo winding is increased, the current requirement is decreased, and since the average voltage is dependent on the PWM ON time, simply implies that to achieve higher average voltages on the trafo primary, you just have too increase the PWM ON time, that's another alternative and effective way to correctly reinforce the output voltage drop issue in PWM based inverters.
If you have any specified queries or doubts regarding the topic, you can always make use of the comment box below and jot in your opinions.