The common problem with many low cost inverters is their incapability of adjusting the output voltage with respect to the load conditions. With such inverters the output voltage tends to increase with lower loads and falls with increasing loads.

The circuit ideas explained here can be added to any ordinary inverter for compensating and regulating their varying output voltage conditions in response to varying loads.
Design#1: Automatic RMS Correction using PWM
The first circuit below can be considered perhaps an ideal approach of implementing a load independent auto output correction using PWM from a IC 555.
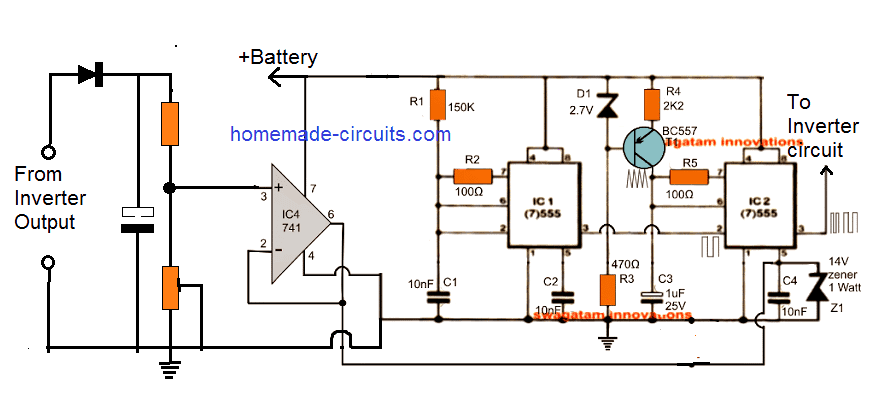
The circuit shown above can be effectively used as an automatic load triggered RMS converter and could be applied in any ordinary inverter for the intended purpose.
The IC 741 works like a voltage follower and acts like a buffer between the inverter output feedback voltage and the PWM controller circuit.
The resistors connected with pin#3of the IC 741 is configured like a voltage divider, which appropriately scales down the high AC output from the mains into a proportionately lower potential varying between 6 and 12V depending upon the output status of the inverter.
The two IC 555 circuit are configured to work like modulated PWM controller. The modulated input is applied at pin#5 of the IC2, which compares the signal with the triangle waves at its pin#6.
This results in the generation of the PWM output at its pin#3 which varies its duty cycle in response to the modulating signal at the pin#5 of the IC.
A rising potential at this pin#5 results in the generation wide PWMs or PWMs with higher duty cycles, and vice versa.
This implies that when the opamp 741 responds with a rising potential due to a rising output from the inverter causes the output of IC2 555 to widen its PWM pulses, while when the inverter output drops, the PWM proportionately narrows at pin#3 of IC2.
Configuring the PWM with Mosfets.
When the above auto correcting PWMs is integrated with the mosfet gates of any inverter will enable the inverter to control its RMS value automatically in response to the load conditions.
If the load exceeds the PWM the inverter output will tend to go low, causing the PWMs to widen which will in turn cause the mosfet to turn ON harder and drive the transformer with more current, thereby compensating the excess current draw from the load
Design#2: Using opamp and Transistor
The next idea discusses an op-amp version which can added with ordinary inverters for achieving an automatic output voltage regulation in response to varying loads or battery voltage.
If you don't want to read the following description, you can watch this video instead:
The idea is simple, as soon as the output voltage crosses a predetermined danger threshold, a corresponding circuit is triggered which in turn switches OFF the inverter power devices in a consistent manner thereby resulting a controlled output voltage within that particular threshold.
The drawback behind using a transistor could be the involved hysteresis issue which could make the switching fairly over a wider cross section resulting in a not so accurate voltage regulation.
Opamps on the other hand can be immensely accurate as these would switch the output regulation within a very narrow margin keeping the correction level tight and accurate.
The simple inverter automatic load voltage correction circuit presented below could be effectively used for the proposed application and for regulating the output of an inverter within any desired limit.
The proposed inverter voltage correction circuit can be understood with the help of the following points:
A single opamp performs the function of a comparator and a voltage level detector.

Circuit Operation
The high voltage AC from the transformer output is stepped down using a potential divider network to about 14V.
This voltage becomes the operating voltage as well as the sensing voltage for the circuit.
The stepped down voltage using a potential divider corresponds proportionately in response to the varying voltage at the output.
Pin3 of the opamp is set to an equivalent DC voltage corresponding to the limit which needs to be controlled.
This is done by feeding the desired maximum limit voltage to the circuit and then adjusting 10k preset until the output just goes high and triggers the NPN transistor.
Once the above setting is done the circuit becomes ready to be integrated with the inverter for the intended corrections.
As can be see the collector of the NPN needs to be connected with the gates of the mosfets of the inverter which are responsible for powering the inverter transformer.
This integration ensures that whenever the output voltage tends to cross the set limit, the NPN triggers grounding the gates of the mosfets and thereby restricting any further rise in the voltage, the ON/OFF triggering continues infinitely as long as the output voltage hovers around the danger zone.
It must be noted that the NPN integration would be compatible only with N-channel mosfets, if the inverter carries P-channel mosfets, the circuit configuration would need a complete reversal of the transistor and the input pinouts of the opamp.
Also the circuit ground should be made common with the battery negative of the inverter.
Design#3: Introduction
This circuit was requested to me by one of my friends Mr.Sam, whose constant reminders prompted me to design this very useful concept for inverter applications.
The load independent/output corrected or output compensated inverter circuit explained here is quite on a concept level only and has not been practically tested by me, however the idea looks feasible because of its simple design.
Circuit Operation
If we look at the figure we see that the entire design is basically a simple PWM generator circuit built around the IC 555.
We know that in this standard 555 PWM design, the PWM pulses can be optimized by changing the ratio of R1/R2.
This fact has been appropriately exploited here for the load voltage correction application of an inverter.
An opto-coupler made by sealing an LED/LDR arrangement has been used, where the LDR of the opto- becomes one of the resistors in the PWM "arm" of the circuit.
The LED of the opto coupler is illuminated through the voltage from the inverter output or the load connections.
The mains voltage is suitably dropped using C3 and the associated components for feeding the opto LED.
After integrating the circuit to an inverter, when the system is powered (with suitable load connected), the RMS value may be measured at the output and the preset P1 may be adjusted to make the output voltage just suitable enough for the load.
How to Set Up
This setting is probably all that would be needed.
Now suppose if the load is increased, the voltage will tend to fall at the output which in turn will make the opto LED intensity decrease.
The decrease in the intensity of the LED will prompt the IC to optimize its PWM pulses such that the RMS of the output voltage rises, making the voltage level also rise up to the required mark, this initiation will also affect the intensity of the LED which will now go bright and thus finally reach an automatically optimized level which will correctly balance the system load voltage conditions at the output.
Here the mark ratio is primarily intended for controlling the required parameter, therefore the opto should be placed appropriately either to the left or the right arm of the shown PWM control section of the IC.
The circuit can be tried with the inverter design shown in this 500 watt inverter circuit
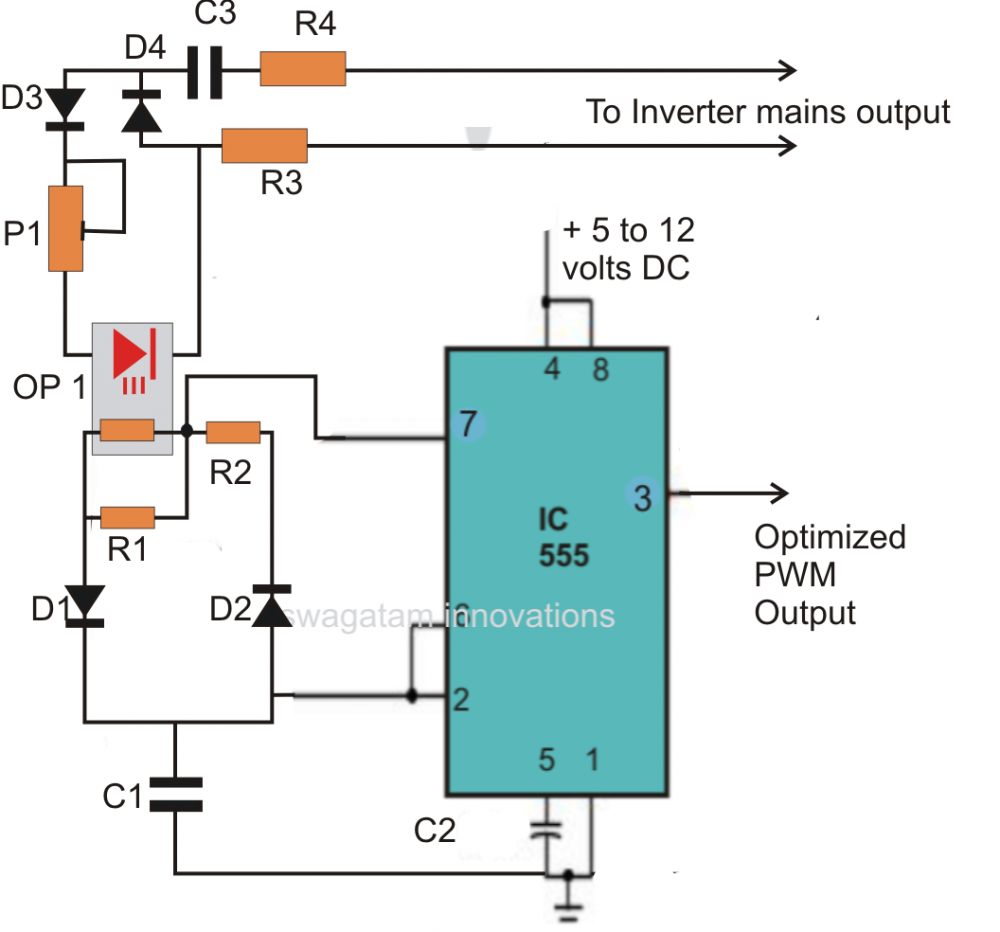
Parts List
- R1 = 330K
- R2 = 100K
- R3, R4 = 100 Ohms
- D1, D2 = 1N4148,
- D3, D4 = 1N4007,
- P1 = 22K
- C1, C2 = 0.01uF
- C3 = 0.33uF/400V
- OptoCoupler = Homemade, by sealing an LED/LDR face to face inside a light proof container.
CAUTION: THE PROPOSED DESIGN IS NOT ISOLATED FROM INVERTER MAINS VOLTAGE, EXERCISE EXTREME CAUTION DURING THE TESTING AND SETTING UP PROCEDURES.
good day sir I tried the circuit and it works fine..
I want to add an overload protection to the output side, please how do I go about it ?
Thank you Hillary,
The above circuits are designed to control overcurrent and overload both….
Dear swagatam,
Trust you good?.
My problem is still about the feedback control circuit. Please I need your help. Now, I have designed the arduino sine wave in your description and it is working perfectly. For the last time please where should I connect the output from the feedback control? Thanks in advance for your help.
Thank you Jonathan, glad you could build the inverter circuit.
The connection details of the feedback control circuit with the Arduino inverter is provided under the same Arduino inverter article. Please check it again, and let me know if you have any difficulty understanding it.
https://www.homemade-circuits.com/arduino-pure-sine-wave-inverter-circuit/
Thanks for getting back to me. I will design it soon and when I’m done I will send you a full working picture and a video.
Sure, no problem, all the best to you!
One more question. Please I have 5 mosfets at the low driver side. And if I’m to connect the cathode of the diode directly to the 5 mosfet gates, should I also connect the 50ohms to each of the gates or only one 50ohms to all the gates? Thank you
An H-bridge low side is supposed to have 2 mosfets only, why have you used 5 mosfets, and how are they configured? please let me know…
Swagatam please I said I did full bridge not half bridge. Thank you
H-bridge refers to full bridge….how can you have 5 low side MOSFETs in an h-bridge or a full bridge topology?
Dear swagatam. Please I have made full bridge inverter with egs002 module and I need to control the voltage. Could you please show me which of the circuit to use and where to connect the circuit output to the inverter?. Waiting for your response sir.
Hi Jonathan I would recommend the second schematic using 741 ic and bc547 transistor. You can attach the diodes cathode with the gates of the low side mosfets….make sure that the mosfets have around 50 ohm gate resistors connected with the EGS002 board.
Though it is working but the gates of the mosfets are connected with 4.7ohm so I connected 100ohms from the cathode of the diode to the 4.7ohms of the low side of the inverter. Could this cause a problem?. Thank you for your time
Sorry, that will not work, because 100 ohm is too large compared to the 4.7 ohm resistor therefore the grounding will not happen when the BC547 conducts.
You must replace the 4.7 ohm with 50 ohm, and remove the 100 ohm resistors entirely.
Thank you for your time. It stopped working. Please what about the high mosfet gates too, should I replace the 4.7ohms with 50ohms?. And also I connected 10kohm to the gates and the source of the mosfets should I remove that one too?. Thank you
Only the low side MOSFET gate resistor needs to be replaced with a 50 ohm resistor, the high side resistor can be also changed to 50 ohms but it is not necessary. The 10k across gate and source is recommended, however if you don’t want them you can remove them, it is not crucial.
Much love swagatam. ❤ thank you
You are welcome Jonathan!
Last question. Please where exactly so I connect the cathode of the diode to the gates? Should it be connected after the 50ohms resistor to the gate or before the 50ohms resistor to the gate? Thank you
The 50 ohms are connected between the low side IC outputs and the low side MOSFET gates. The automatic correction circuit diode cathodes must be connected directly to the gates of the MOSFET.
The setup of the second circuit you recommended to me. How is the setup done? And does it need a variable power supply before connecting to the transformer output of inverter? Thanks.
You will have to arrange a 230V or 240V AC source which can be fed to the 220K end of the circuit after which the preset will need to be adjusted until the BC547 just conducts. You can replace the 3 V zener with an LED for the switch ON indication. The 230V or 240V is the desired cut off range at which the circuit should activate and begin deactivating the mosfets for the automatic cut off.
Yes sir I was asking if the setup needs a variable power supply before connecting to the transformer output of an inverter. Or how is the the setup done. Thanks
Preferably you will need a variac for this, or if you have any other method of producing the high level voltage of 230V or 240V or whatever cut off level you require.
So I first apply the 220v or 240v ac to the circuit then slowly trim the preset until the red light illuminates and glue it at that point. That means the setup is complete and ready to feed to the inverter output?
Thanks
Yes, you are absolutely correct.
hello sir, it seems there is a problem in your website because am not getting your latest responses. I was asking after i have paralleled all gate resistors with in4148, i do connect again a common in4148 each side to the bc transistor in the second diagram you had referred to me?
Hello Morris, the 1n4148 you connected parallel to the gate resistors are for protecting the MOSFET from voltage spikes, it has nothing to do with the second circuit explained in the above article.
Yes, you will have to connect the 1N4148 diodes with the BC547 transistor as shown in the second diagram above.
The anodes of these diodes will connect with the LOW side MOSFET gates.
Make sure your MOSFET gate resistors are at least 100 ohms.
Thank you very much sir
You are welcome Morris…
Hello Morris, would love to connect with you if you don’t mind ..
Hae Nik what’s up✋
Hello Swagatam, I first applied 220ac main to the second design before loading it to inverter. I then slowly tweaked the preset but the led I used instead of 3v zena diode was not illuminating. Secondly. I applied again 220ac whn the circuit is connected to a12v batteries and tweaked the preset. The led is still not illuminating. What should be done sir being this circuit is very simple and I wonder why it’s not working.
Hello Morris,
The LED polarity will be opposite to that of the zener, meaning if you use an LED in place of the zener diode, then the cathode must be towards the base and anode towards the the 10k resistor.
If still it does not illuminate please check the voltage across the 10uF capacitor, across pin#3 and ground, pin#2 and ground.
The LED will illuminate only when the pin#3 voltage exceeds pin#2 voltage.
Do I feed only 220 ac or 12v must also be fed to the circuit?
Thanks.
It should be exactly as shown in the diagram, the IC 741 Vcc pin will require a separate +12V DC.