A self-powered generator is a perpetual electrical device designed to infinitely run and produce a continuous electrical output which is usually larger in magnitude than the input supply through which it's running.
Who wouldn't like to see a self-powered motor generator running at home and powering the desired appliances non-stop, absolutely free of cost. We discuss the details of a few such circuits in this article.
A free energy enthusiast from South Africa who doesn’t want to reveal his name has generously shared the details of his solid state self-powered generator for all the interested free energy researchers.
When the system is used with an inverter circuit, the output from the generator is around 40 watts.
The system can be implemented through a few different configurations.
The first version discussed here is able to charge three 12 battery's together and also sustain the generator for a permanent perpetual operation (until of course the batteries lose their charging/discharging strength)
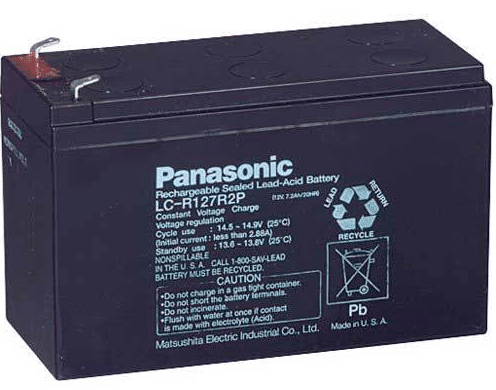
The proposed self-powered generator is designed to work day and night providing continuous electrical output, quite like our solar panel units.
The initial unit was constructed using 4 coils as the stator and a central rotor having a 5 magnets embedded around its circumference as depicted below:
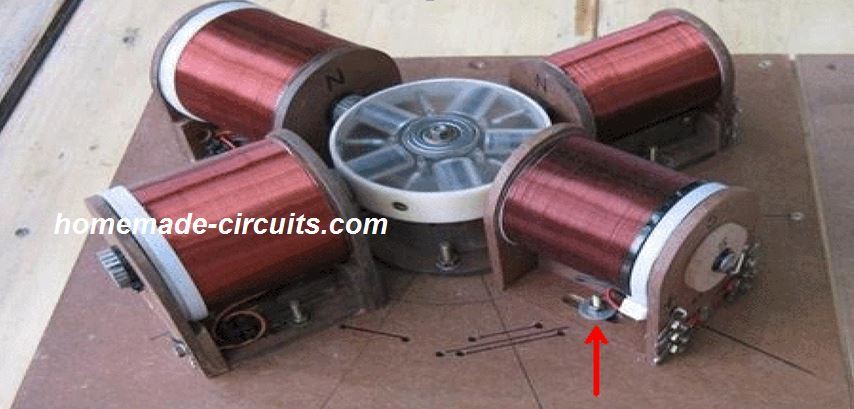
The shown red arrow tells us regarding the adjustable gap between the rotor and the coils which can be changed by loosening the nut and then moving the coil assembly near or away from the stator magnets for the desired optimized outputs. The gap can be anywhere between 1mm to 10 mm.
The rotor assembly and mechanism should be extremely accurate with its alignment and ease of rotation, and therefore must be built using precision machines such as a lathe machine.
The material used for this can be clear acrylic, and the assembly must include 5 sets of 9 magnets fixed inside cylindrical pipe like cavities as shown in the figure.
The top opening of these 5 cylindrical drums are secured with plastic rings extracted from the same cylindrical pipes, to ensure that the magnets stay fixed tightly in their respective positions inside cylindrical cavities.
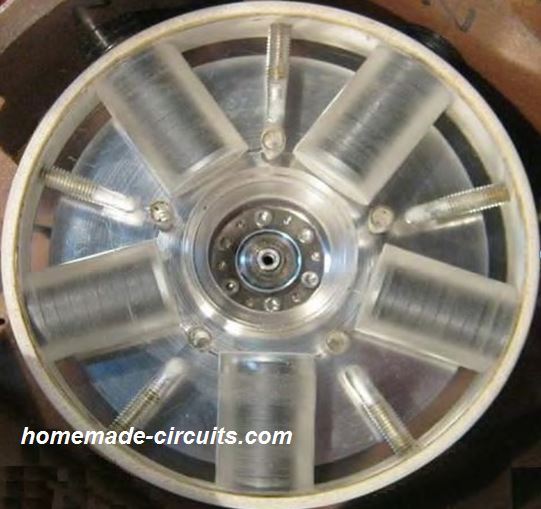
Very shortly, the 4 coils had been enhanced to 5 in which the newly added coil had three independent windings. The designs will be understood gradually as we run through the various circuit diagrams and explain how the generator works. The first basic circuit diagram can be witnessed below
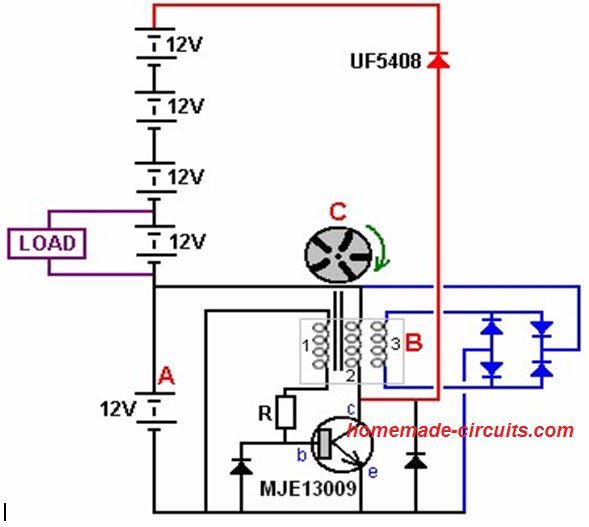
The battery designated as “A” energizes the circuit. A rotor “C”, made up of 5 magnets is manually moved pushed such that one of the magnets moves close to the coils.
The coils set “B” includes 3 independent windings over a single central core and the magnet going past these three coils generates a tiny current inside them.
The current in coil number “1” runs through the resistor “R” and into the base of the transistor, forcing it to switch on. The energy moving through the transistor coil “2” enables it to turn into a magnet which shoves the rotor disc “C” on its path, initiating a spinning motion on the rotor.
This rotation simultaneously induces a current winding “3” which is rectified through the blue diodes and transferred back to charge battery “A”, replenishing nearly all of the current drawn from that battery.
As soon as the magnet inside rotor “C” moves away from the coils, the transistor switches off, restoring its collector voltage in a short time close to the +12 Volt supply line.
This depletes coil “2” of current. Because of the manner the coils are positioned, it pulls the collector voltage upwards to around 200 volts and above.
However this does not happen because the output is connected to series five batteries which drop the rsising voltage according to their total rating.
The batteries have a series voltage of approximately 60 volts (which explains why a strong, fast-switching, high-voltage MJE13009 transistor has been incorporated.
As the collector voltage goes by the voltage of the series battery bank, the red diode commences turning ON, releasing the stored electricity in the coil into the battery bank. That current pulse moves through all 5 batteries, charging every one of them. Casually speaking, this constitutes the self powered generator design.
In the prototype, the load used for long-term, tireless testing was a 12 volt 150-watt inverter illuminating a 40-watt mains lamp:
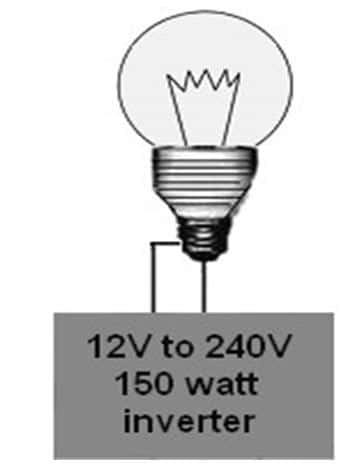
The simple design demonstrated above was further improved by the inclusion of a couple of more pick-up coils:
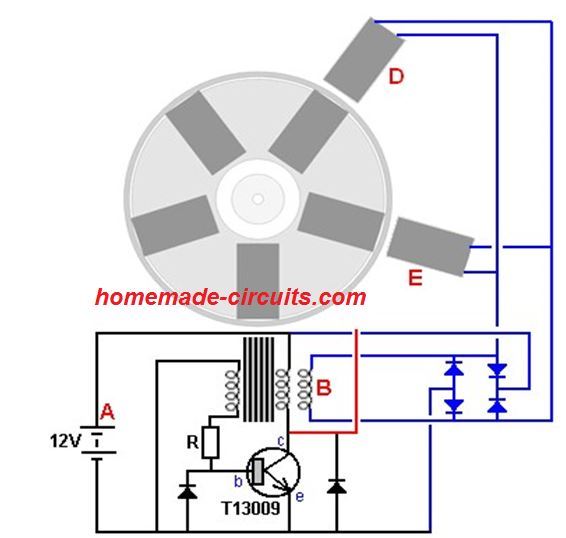
Coils “B”, “D” and “E” are all activated simultaneously by 3 individual magnets. The electric power generated in all of the three coils is handed down to the 4 blue diodes to manufacture a DC power which is applied to charge battery “A”, which powers the circuit.
The supplemental input to the drive battery a result of the inclusion of 2 extra drive coils to the stator, enables the machine to run solidly in the form of a self-powered machine, sustaining the battery "A"voltage infinitely.
The sole moving portion of this system is the rotor which is 110 mm in diameter and is a 25 mm thick acrylic disc installed on a ball-bearing mechanism, salvaged from your discarded computer hard disc drive. The set up appears like this:
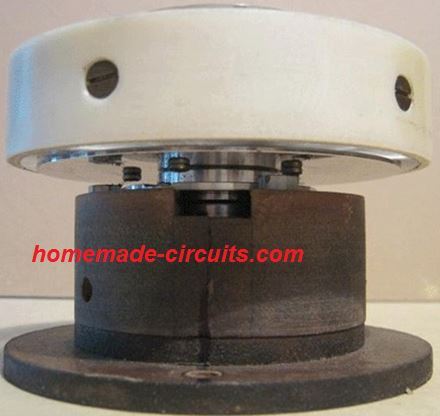
In the images, the disc appears to be hollow however in reality it is solid, crystal clear plastic material. Holes are drilled on the disc is across five equally spread out locations throughout the circumference, meaning, with 72 degree separations.
The 5 primary openings drilled on the disc are for holding the magnets which are in groups of nine circular ferrite magnets. Each of these are 20 mm in diameter and 3 mm in height, creating stacks of magnets with a total height of 27 mm long and diameter of 20 mm. These stacks of magnets are placed in such a way that their North poles project outwards.
After the magnets are mounted, the rotor is put inside a plastic pipe strip in order to secure the magnets tightly in place while the disc spins speedily. The plastic pipe is clamped with the rotor with the aid of five mounting bolts with countersunk heads.
The coil bobbins are 80 mm long with 72 mm end diameter. The middle spindle of every coil is constructed of a 20 mm long plastic pipe having an outer and an inner diameter of 16 mm. providing a wall density of 2 mm.
After the coil winding is completed, this inner diameter becomes full with a number of welding rods with their welding coating taken out. These are subsequently enveloped in polyester resin, but a solid bar of soft iron can also become a excellent alternative:
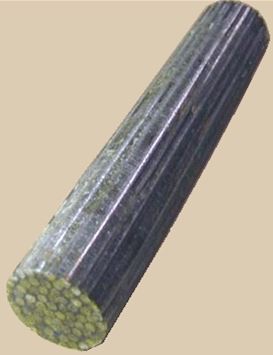
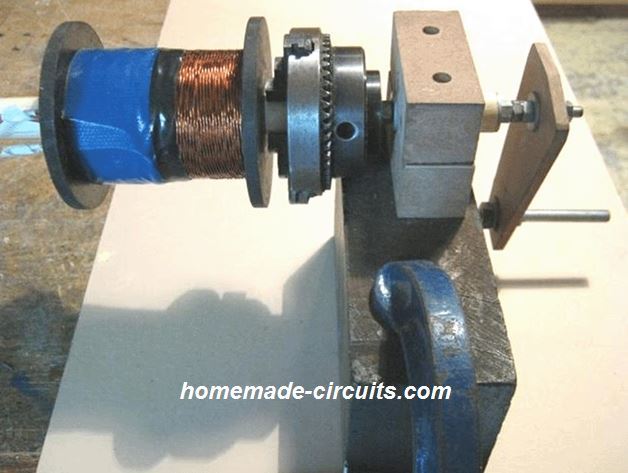
The 3 wire strands that constitute coils “1”, “2” and “3” are 0.7 mm in diameter wire and are wrapped with each other before it's wound on the bobbin “B”. This method of a bifilar winding creates a lot heavier composite wire bundle which can be simple coil over a spool effectively. The winder shown above works with a chuck to hold the coil core for enabling the winding, nevertheless any kind of basic winder can also be used.
The designer carried out the wire twisting by extending the 3 strands of wire, each originating from a independent 500 gram bundle reel.
The three strands are tightly held at each end with the wires pressing one another at each end having three metres space between the clamps. After that, the wires are fixed at the center and 80 turns ascribed to the midsection. This allows 80 turns for every single of the two 1.5 metre spans positioned between clamps.
The twisted or the wrapped wire set is curled on a temporary reel to maintain it neat because this twisting will have to be duplicated 46 more occasions since all the contents of the wire reels will be required for this one composite coil:
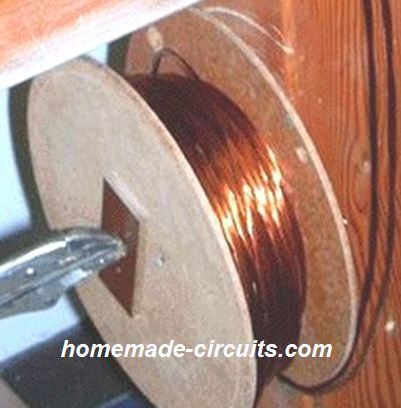
The next 3 meters of the three wires are then clamped and 80 turns wound to the middle position, but on this occassion the turns are placed in the opposite direction. Even now exactly the same 80 turns are implemented, but if the previous winding had been ‘clockwise’ then this winding is flipped ‘counter-clockwise’.
This particular modification in the coil directions provides a completed range of twisted wires in which the twist direction becomes opposite every 1.5 meters over the whole length. This is how the commercially manufactured Litz wire is set up.
This specific great looking twisted wires sets are now employed for winding the coils. A hole is drilled in one spool flange, exactly near the middle tube and core, and the start of the wire is inserted through it. The wire is next bent forcefully at 90 degrees and applied round the spool shaft to begin the winding of the coil.
The winding of the wire bundle is executed with great care next to each other across the entire spool shaft and you will see 51 no of winding around each layer and the following layer is wound straight over the top of this very first layer, going back again towards the start. Make certain that the turns of this second layer rests precisely over the top of the winding underneath them.
This can be uncomplicated because the wire pack is thick enough for allowing the placement quite simple. In case you like, you can try wrapping one thick white paper around the first layer, to make the second layer distinct as it is turned around. You will need 18 of such layers to finish the coil, that will ultimately weigh 1.5 kilograms and the finished assembly might looks something as shown below:
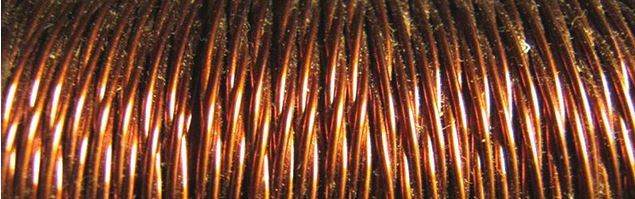
This finished coil at this point consists of 3 independent coils tightly wrapped to each other and this set up is intended to create an fantastic magnetic induction across the other two coils, whenever one of the coils is energized with a supply voltage.
This winding currently includes coils 1,2 and 3 of the circuit diagram. You don't need to to keep worrying about tagging the ends of each strand of wire as you can easily identify them using an ordinary Ohmmeter by checking the continuity across the specific wire ends.
Coil 1 can be used as the triggering coil that will switch the transistor ON during the right periods. Coil 2 could be the drive coil that is energized by the transistor, and Coil 3 could be the one of the first output coils:
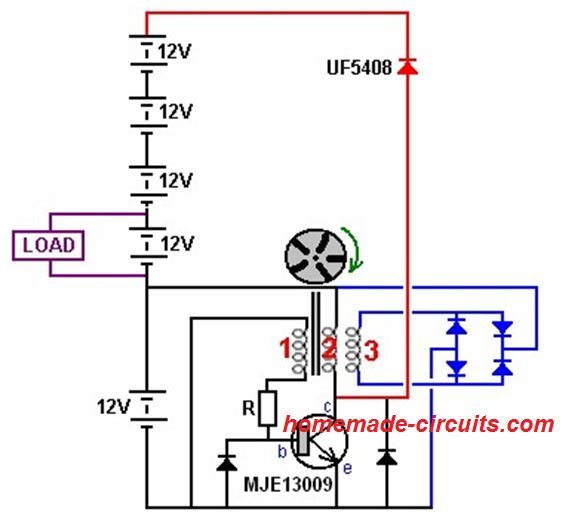
Coils 4 and 5 are straightforward spring like coils that are connected parallel with the drive coil 2. They help to boost the drive and therefore are important. Coil 4 carries a DC resistance of 19 ohms and coil 5 resistance can be around 13 ohms.
However, research is ongoing currently to figure out the most effective coil arrangement for this generator and possibly further coils could be the identical to the first coil, coil “B” and all three coils are attached in the very same manner and the driving winding on each coil operated through the a single highly rated and, fast switching transistor. The present set up looks like this:
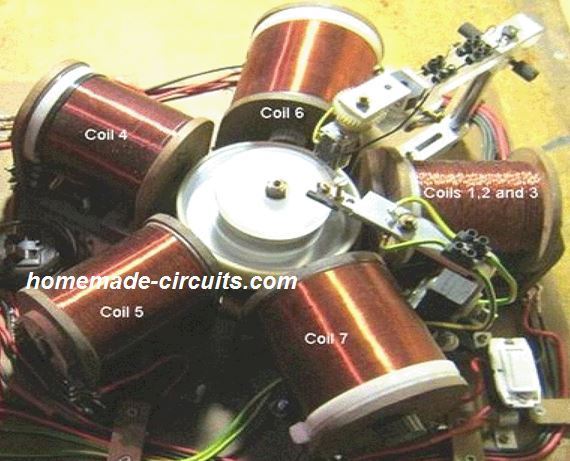
You may ignore the shown gantries since these were included only for examining different ways of activating the transistor.
Currently, coils 6 and 7 (22 ohms each) work as additional output coils attached in parallel with output coil 3 which is built with 3 strands each and with a resistance of 4.2 ohms. These could be air-core or with a solid iron core.
When tested it revealed that the air core variant performs just a bit better than with an iron core. Each of these two coils are consist of 4000 turns wound on 22 mm diameter spools using 0.7 mm (AWG # 21 or swg 22) super enameled copper wire. All the coils have the same specs for the wire.
Using this coil set up, the prototype could run non-stop for around 21 days, preserving the drive battery at 12.7 volts constantly. After 21 days, the system had been stopped for some modifications and tested again using a completely new arrangement.
In the construction demonstrated above, the current moving from the drive battery into the circuit is actually 70 milliamps, which at 12.7 volts produces an input power of 0.89 watts. The output power is approximately near 40 watts, confirming a COP of 45.
This is excluding the three additional 12V batteries which are additionally being charged simultaneously. The results indeed appear to be extremely impressive for the proposed circuit.
The drive method had been employed so many times by John Bedini, that the creator opted to experiment with John’s approach of optimization for highest efficiency. Even so, he found that eventually a Hall-effect semiconductor specifically aligned correctly with a magnet offers the most effective outcomes.
More research goes on and the power output has at this point attained 60 watts. This looks truly amazing for such a tiny system, particularly when you see it includes no realistic input. For this next step we reduce the battery to just one. The set up can be seen below:
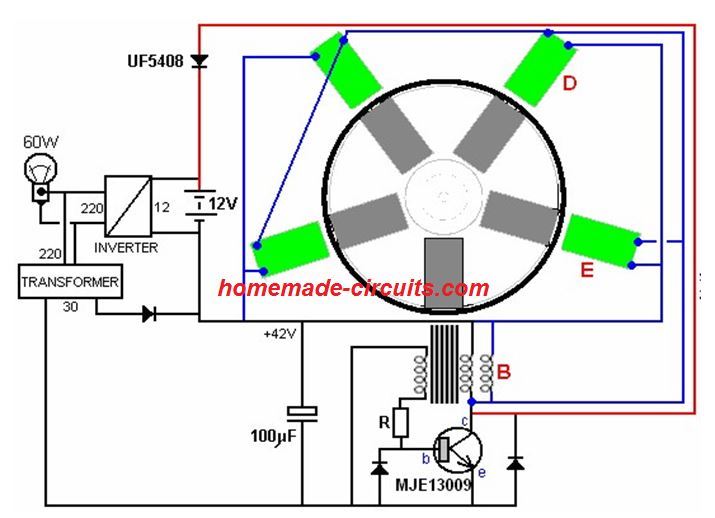
Within this set up, coil “B” is also applied with the pulses by the transistor, and the output from the coils around the rotor is now channelized to the output inverter.
Here the drive battery is removed and is replaced with a low-power 30V transformer and diode. This is in turn operated from the inverter output. Giving a slight rotational thrust to the rotor produces ample charge on the capacitor to enable the system cranking without any battery. The output power for this present set up can be seen going up to 60 watts which is an awesome 50% enhancement.
The 3 12 volt batteries are also taken off, and the circuit can easily run using just one single battery. Continuous power output from a solitary battery that by no means requires for an external recharging appears to be a great achievement.
The next improvement is through a circuit that incorporates a Hall-effect sensor and an FET. The Hall-effect sensor is arranged precisely in line with the magnets. Meaning , the sensor is placed in between one of the coils and the rotor magnet. We have a 1 mm clearance between the sensor and the rotor. The following image shows how exactly it needs to be done:
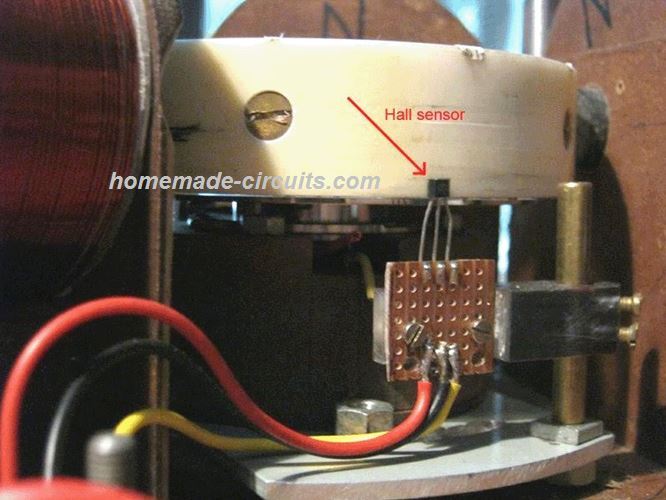
Another view from top when the coil is in the right position:
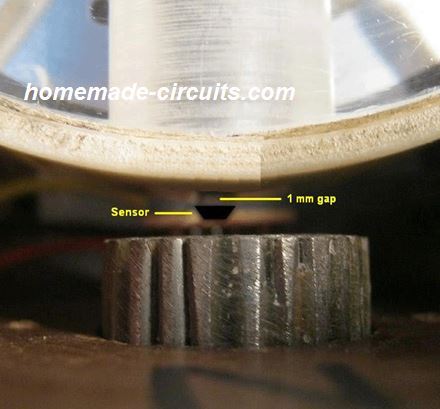
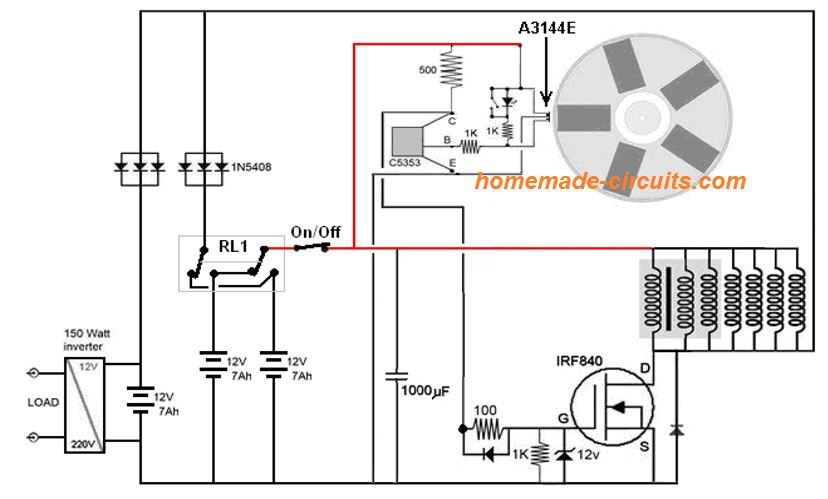
This circuit showed an immense 150 watt of nonstop output using three 12-volt batteries. The first battery helps to power the circuit while the second gets recharged via three diodes hooked up in parallel to increase the current transmission for the battery which is being charged.
The DPDT changeover switch “RL1” swaps the battery connections every couple of minutes with the help of the circuit displayed below. This operation allows both the batteries to remain fully charged all the time.
The recharging current as well runs through a second set of three parallel diodes recharging the third 12-volt battery. This 3rd battery operates the inverter through which the intended load is run. The test load used for this set up was a 100-watt bulb and a 50-watt fan.
The Hall-effect sensor switches an NPN transistor nevertheless virtually any fast-switching transistor for instance a BC109 or a 2N2222 BJT will work extremely well. You will realize that all of the coils are at this point being operated by the IRF840 FET. The relay employed for the switching is a latching type as indicated in this design:
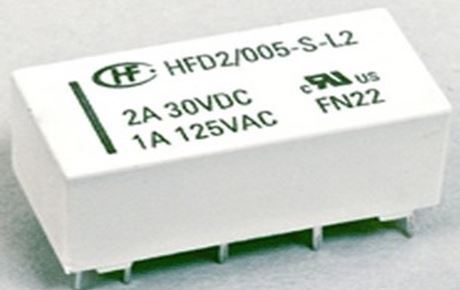
And it is powered by a low current IC555N timer as shown below:
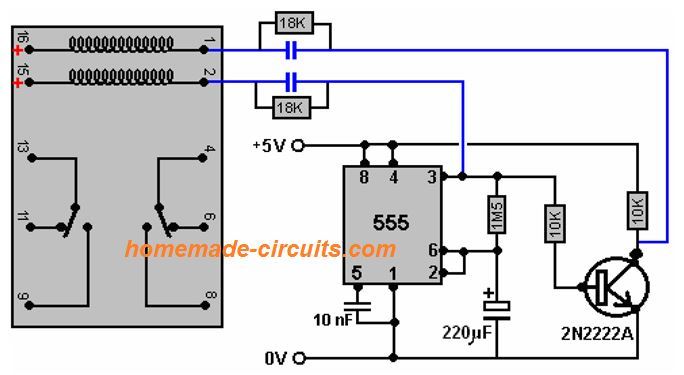
The blue capacitors are selected to toggle the specific actual relay which is used in the circuit. These briefly allow the relay to be ON and OFF every five minutes or so. The 18K resistors over the capacitors are positioned to discharge off the capacitor throughout the five minutes when the timer is in the OFF state.
However, if you do not want to have this switching between the batteries, you can simply set it up in the following manner:
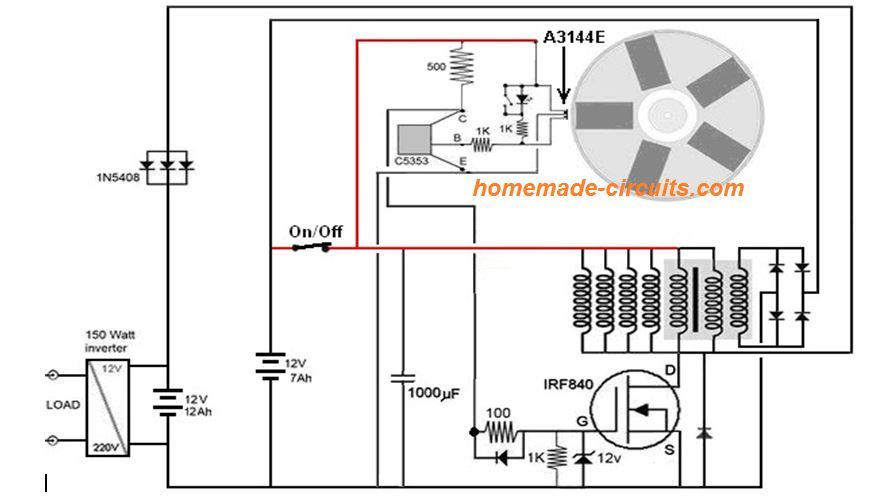
In this arrangement,, the battery powering the inverter connected with the load is specified with higher capacity. Although the creator utilized a couple of 7 Ah batteries, any common 12-volt 12 Amp-Hour scooter battery may be used.
Basically one of the coils is employed to deliver current to the output battery and the one leftover coil, which may be the part of the three-strand main coil. This is accustomed to provide supply voltage directly to the drive battery.
The diode 1N5408 is rated to handle 100-volt 3-amp. The diodes without any value can be any diode such as 1N4148 diode. The coils ends joined to the IRF840 FET transistor are physically installed near the circumference of the rotor.
One can find 5 such coils. The ones which are grey in color reveal that the extreme right three coils consist of the separate strands of the main 3-wire composite coil already duscussed in our earlier circuits.
While we saw the use of the three-strand twisted wire coil for the Bedini-style switching incorporated for both drive and output purposes, it was ultimately found unnecessary to incorporate this type of coil.
Consequently, an ordinary helical type wound coil made up of 1500 grams of 0.71 mm diameter enameled copper wire was found to be equally effective. Further experimentation and research helped to develop the following circuit which worked even better than the previous versions:
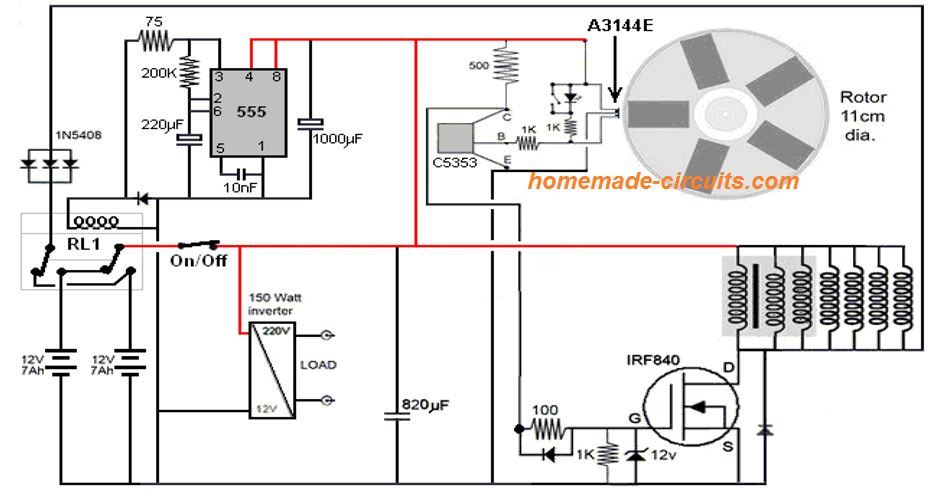
In this improved design we find the use of a 12-volt non-latching relay. The relay is rated to consume around 100 milliamps at 12 volts.
Inserting a 75 ohm or a 100 ohm series resistor in series with the relay coil helps to bring down the consumption to 60 milliamps.
This is consumed only for half the time during its operation periods because it remains non-operational while its contacts are in the N/C position. Just like the previous versions, this system too powers itself indefinitely without any concerns.
Feedback From one of the dedicated readers of this blog, Mr. Thamal Indica
Dear Swagatam Sir,
Thanks so much for your reply and I am grateful to you for encouraging me. When you made that request to me I had already fixed some more 4 coils for my small Bedini Motor in order to make it more and more efficient. But I could not create the Bedini Circuits with Transistors for that 4 coils as I could not purchase the euipments .
But still my Bedini Motor is running with the previous 4 coils even if there is a small drag from the ferrite cores of the newly attached other four coils as these coils do not do anything but they are just sitting around my small magnet rotor. But my Motor is still able to charge the 12V 7A battery when I drive it with 3.7 batteries.
At your request , I have attached herewith a video clip of my bedini motor and I advise you to watch it till the end as at the beginning the voltmeter shows the Charge battery has a 13.6 V and after starting the motor it rises up to 13.7V and after some 3 or 4 minutes it rises up to 13.8V .
I used 3.7V small batteries to drive my small Bedini Motor and this proves the efficiency of the Bedini Motor well. In my Motor, 1 coil is a Bifilar coil and other 3 coils are triggered by the same trigger of that Bifilar coil and these three coils boost the energy of the motor by giving out some more coil spikes while speeding up the magnet rotor. . That is the secret of my Small Bedini Motor as I connected the coils in the parallel mode.
I am sure when I use the other 4 coils with bedini Circuits my Motor will work more efficiently and the magnet rotor will be spinning in a tremendous speed.
I will send you another video clip when I finish creating the Bedini Circuits .
Best Regards !
Thamal Indika
Practical Test Results