In this post I have explained the construction details of a triac based push-button dimmer circuit which can be used for controlling incandescent, and fluorescent lamp brightness through push-button pressing.
Another feature of this dimmer is its memory, which retains the brightness level even during power outages, and provides the same lamp intensity after power is restored.
By Robert Truce
Introduction
Light dimming circuits are easy to operate, simply assembled and use a rotary type potentiometer for controlling lamp brightness.
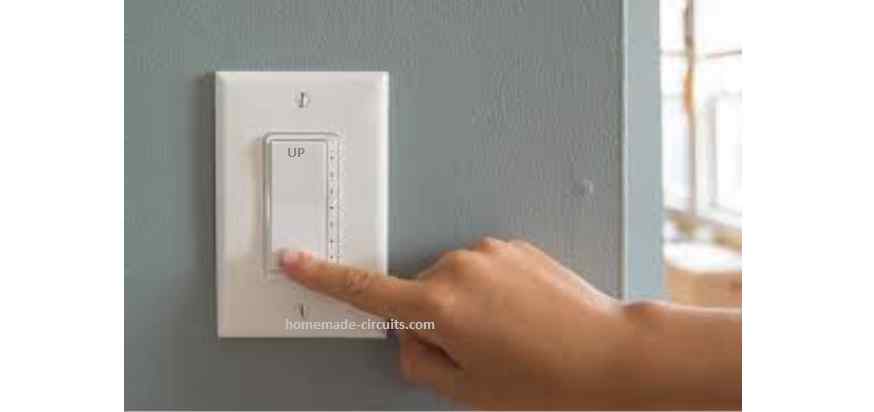
Although such circuits are fairly simple, there can be a need for more complex dimming situations.
The appearance of a regular light dimmer circuit is not the best as it has a dull-looking knob with which light intensity is adjusted.
Furthermore, you can only determine the illumination level from the fixed position where the dimmer is installed.
In this project, we are talking about a push-button type dimmer with better aesthetics and more flexible in terms of mounting locations. Be it on either side of the door or bedside tables, the dimmer discussed in this article is exclusive.
This part equips an on/off toggle switch with a pair of push-buttons – one to increase the light intensity gradually over 3 seconds and another to do the exact opposite.
While adjusting the knob, the light level can be fixed at the desired level and maintained for 24 hours without any alterations.
This dimmer is suitable for incandescent or fluorescent lights that are rated until 500 VA with a particular heatsink. When installed a larger heatsink, you can even go up to 1000 VA.
Construction
By referring to tables 1 and 2, prepare the choke and the transformer. Take extra precaution to ensure sufficient insulation is provided between the primary and secondary windings of the pulse transformers.
The construction will be extremely simple if the following recommended PCB is utilized.
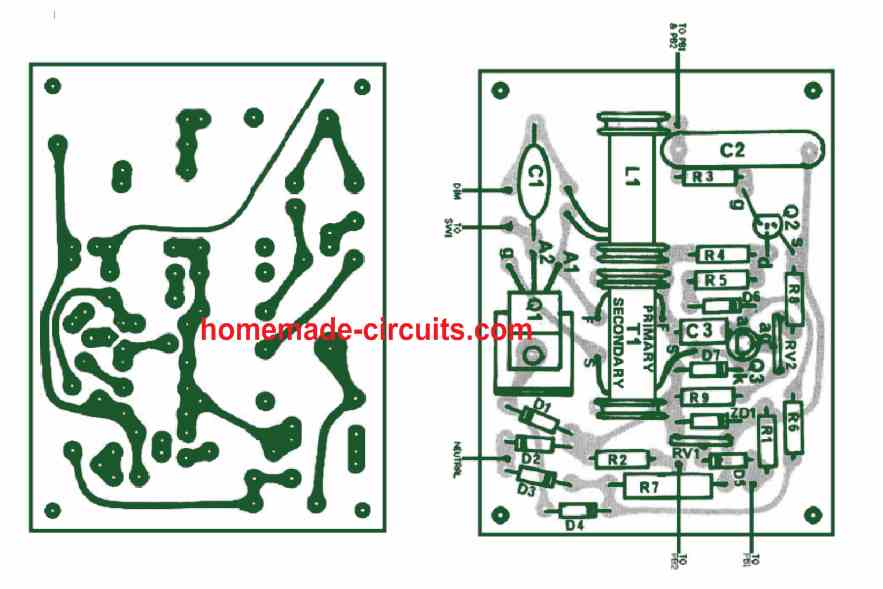
Firstly, place all the electronic components on the PCB by referring to the parts layout. Be sure to pay attention to the diodes polarity and transistors’ orientation before soldering them.
For the heatsink, grab a tiny piece of aluminium (30 mm x 15 mm) and bend it 90 degrees in the middle of the long side. Place it under the Triac and your heatsink is ready.
The pulse transformer and the choke are placed using rubber grommets and tightened into position using tinned copper wire around the grommets. Then, they are soldered into the existing holes.
Check if all the components are soldered and the external wires are linked. Upon verification, flip the PCB to reveal the underside and use methylated spirits to rinse it. This process removes any built-up flux residue which could cause leakage.
The PCB must be fixed on washers into a metal box with earthing connections. After that, you need to place a 1-mm thick insulation material beneath the board to avoid any long component leads from contacting the chassis.
It is recommended that a 6-way terminal block is selected to connect all the external wiring.
Setting up
Ensure that all setup and configurations are made using plastic or thoroughly insulated tools.
This push-button light dimmer circuit will contain the mains voltage when switched on and hence it is extremely important to take the precautionary measures.
Adjust potentiometer RV2 to get the desired minimum light illumination while holding the down button.
Next, tweak potentiometer RV1 to get the maximum light intensity while holding the up push-button. Do this just until you obtain the maximum level and not more.
Extra precautions are necessary if the lamp loads are of fluorescent type when you are making the adjustments. Moreover, you must redo the adjustment if the fluorescent loading is altered.
When changing the maximum light illumination on a fluorescent load, gently increase the light level just until the lamps begin to flicker.
At that moment, turn RV1 back until there you see a drop in light intensity. This elevated setting difficulty is because of the inductive characteristics of the fluorescent loads.
If the needed minimum light level cannot be reached within the range of RV2, you must swap resistor R6 with a bigger value. This will deliver the lower light level range. If you use a smaller R6 value, the light level range will be higher.
Table 1: Choke Winding Data | |
Core | A long piece of 30mm ferrite aerial rod with (3/8” diameter) |
Winding | 40 turns 0.63 mm diameter (26 swg) wound as double layers with each having 20 turns. Close wound utilising the centre 15 mm of only the core. |
Insulation | Utilise two layers of plastic insulation tape over complete winding. |
Mounting | Utilise a rubber grommet with 3/8” diameter over each end and attach to the PCB using tinned copper wire in the provided holes. |
Table 2: Pulse Transformer Winding Data | |
T1 Core | A long piece of 30mm ferrite aerial rod with (3/8” diameter) |
Primary | 30 turns of 0.4 mm diameter (30 swg) close wound on the centre of the 15 mm of the core. |
Insulation | Utilise two layers of plastic insulation tape over primary winding. |
Secondary | 30 turns 0.4 mm diameter (30 swg) close wound on the centre 15 mm of the core. Pull the wire out on the opposite side of the core to the primary. |
Insulation | Utilise double layers of plastic insulation tape over complete winding. |
Mounting | Utilise a rubber grommet with 3/8” diameter on top of each end and attach to the PCB using tinned copper wire in the provided holes. |
How the Circuit Works
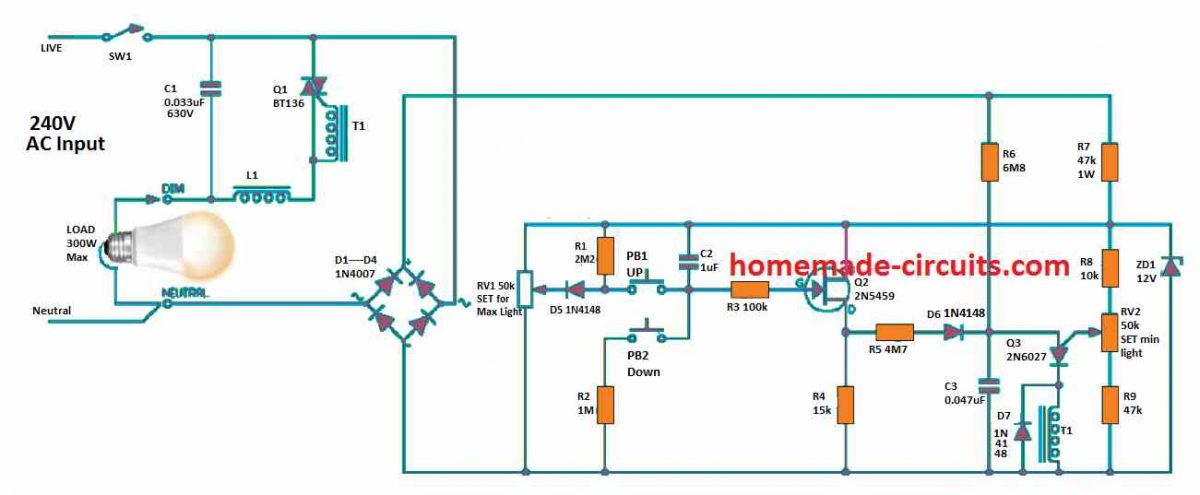
We used a phase-controlled triac for power control just like the recent dimmers.
The triac, is switched on by a pulse at a pre-decided point in each half cycle and turns off by itself at the end of each cycle.
Traditionally, dimmer use a standard RC and diac system to produce the trigger pulse.
However, this dimmer works with a voltage-controlled device. The 240 Vac from the mains is rectified by D1-D4.
The full-wave rectified waveform is trimmed at 12 V by resistor R7 and Zener-diode ZD1.
Because there is no filtering, this 12 V will fall to zero during the last half millisecond of each half-cycle.
To deliver the right timing and the energy needed to drive the triac, a programmable unijunction transistor (PUT) Q3 is used with capacitor C3.
Furthermore, the PUT operates like a switch in the following way. If the anode (a) voltage is more than the anode-gate voltage (ag), a short-circuit is developed in the anode to cathode (k) path.
The voltage on the anode-gate is determined by RV2 and is usually around 5 to 10 V.
Capacitor C3 is charged through resistor R6 and when the voltage across it increases than the “ag” terminal, the PUT begins discharging C3 using the primary side of the pulse transformer T1.
In return, this creates a pulse in the secondary section of T1 which gates on the triac.
When the voltage supply to resistor R6 is not smoothed, the voltage rise on capacitor C3 will experience a scenario called a cosine modified ramp. This provides a more proportional change in light level versus the control voltage.
The moment capacitor C3 is discharged, the PUT may either stay on or switch off depending on the individual part.
There is a possibility that it might fire again if it turns off because capacitor C3 charges swiftly. In either situation, the operation of the dimmer remains unaffected.
Moreover, if C3 fails to charge to the PUT’s “ag” voltage before the end of the half-cycle, the “ag” potential will drop, and the PUT will fire.
This crucial part of the operation ensues synchronization of the timing to the mains voltage. For this important reason, the 12 V supply is not filtered.
To regulate the charge rate of C3 (and eventually the time it takes to turn on the triac within each half cycle) a secondary timing network of RS and D6 is used.
Since the value of R5 is lower than R6, capacitor C3 will charge faster using this path.
Let’s say we set the input to RS to around 5 V, then C3 will quickly charge up to 4.5 V and slows down due to the value of R6. This type of charging is known as “ramp and pedestal”.
Because of the initial boost given by RS, the PUT will fire in the beginning and the triac will switch on earlier while distributing more power to the load.
So, by regulating the voltage at the input of R5, we can attempt to control the output power.
Capacitor C2 functions as a memory device. It can either be discharged by R1 using PB1(up button) or charged with R2 using PB2 (down button).
Since the capacitor C2 is connected from the positive terminal of the 12 V supply, the moment the capacitor is discharged the voltage will shoot up with respect to the zero-volt line.
Diode D5 is there to avoid the voltage from rising beyond the value set by RV1. The capacitor C2 is attached to the input of Q2 using resistor R3.
There is also a Field Effect Transistor (FET) Q2 which holds a high input impedance. Therefore, the input current is practically zero and the source trails the gate voltage at several levels. The definite voltage variance depends on the specific FET.
As a result, if there is a change in the gate voltage, there will be also changes in the voltages on C2 and RS.
When either PB1 or PB2 is pressed, the capacitor voltage which triggers the triac firing point and the power delivered to the load may be diverse.
When the push-buttons are released, the capacitor will “hold” this voltage for an extended period of time even when the power is turned off!
Elements Affecting Dimmer Memory
However, the memory time relies on several factors as shown outlined below.
- You should use a capacitor with a leakage resistance of more than 100,000 megaohms. Furthermore, choose a decent capacitor with a voltage rating of at least 200 V. You may choose different brands.
- The push-button switch must be rated for 240 Vac operation. These kinds of switches have better separation and that means greater insulation between the contacts. You can identify if the push-button is the cause of low memory times by physically dismantling it.
- When there is leakage across the PCB board, it is a problem. You might notice there seems to be a path travelling from the source of Q2 and looks like going nowhere. This is a guard line that prevents leakage from high voltage components. If you are adopting a different construction approach, ensure to establish the junctions of R3 and Q2, and R3 and C2 through mid-air joints or by high-quality ceramic standoffs.
- By itself, the FET equips a finite input resistance. Countless FETs were tried and all of them worked. Still, ensure to check and not overlook the possibility.
You can control the dimmer from multiple stations by simply making parallel connections to the sets of push-buttons.
There is no damage done if both the up and down buttons are pushed simultaneously.
However, bear in mind that increasing the number of control stations may compound the chances of leakage and subsequent loss of memory time.
Always ensure to fix the dimmer and push-button in a dry-dusted position.
At all costs, avoid using this dimmer or push buttons in a bathroom or kitchen because moisture will corrupt the memory of the circuit.
PARTS LIST
RESISTORS (All 1/2W 5% CFR)
R5 = 4k7
R6 = 10k
R4 = 15k
R7 = 47k 1W
R9 = 47k
R3 = 100k
R2 = 1M
R1 = 2M2
R6 = 6M8
RV1,RV2 = 50k trim pot
CAPACITORS
C1 = 0.033uF 630V polyester
C2 = 1 uF 200V polyester
C3 = 0.047uF polyester
SEMICONDUCTORS
D1-D4 = 1N4004
D5,D6,D7 = 1N914
ZD1 = 12V zener diode
Q1 = SC141D,SC146DTriac
Q2 = 2N5458, 2N5459 FET
Q3 = 2N6027PUT
MISCELLANEOUS
L1 = Choke - see table 1
T1 = Pulse Transformer - see table 2
6 -way terminal block (240V), Metal Box, 2 Pushbutton
Switches, Front Plate, Power Switch