A simple high voltage generator circuit is explained here which can be used to step up any DC level to about 20 times or depending upon the transformer secondary rating.
Circuit Operation
As can be visualized in the shown high voltage arc generator circuit diagram, it employs a standard transistor blocking oscillator configuration for generating the required stepped up voltage across the output winding of the transformer.
The circuit may be understood as follows:
The transistor conducts and drives the associated winding of the transformer via its collector/emitter the moment power is applied to the center of the transformer.
Circuit Diagram
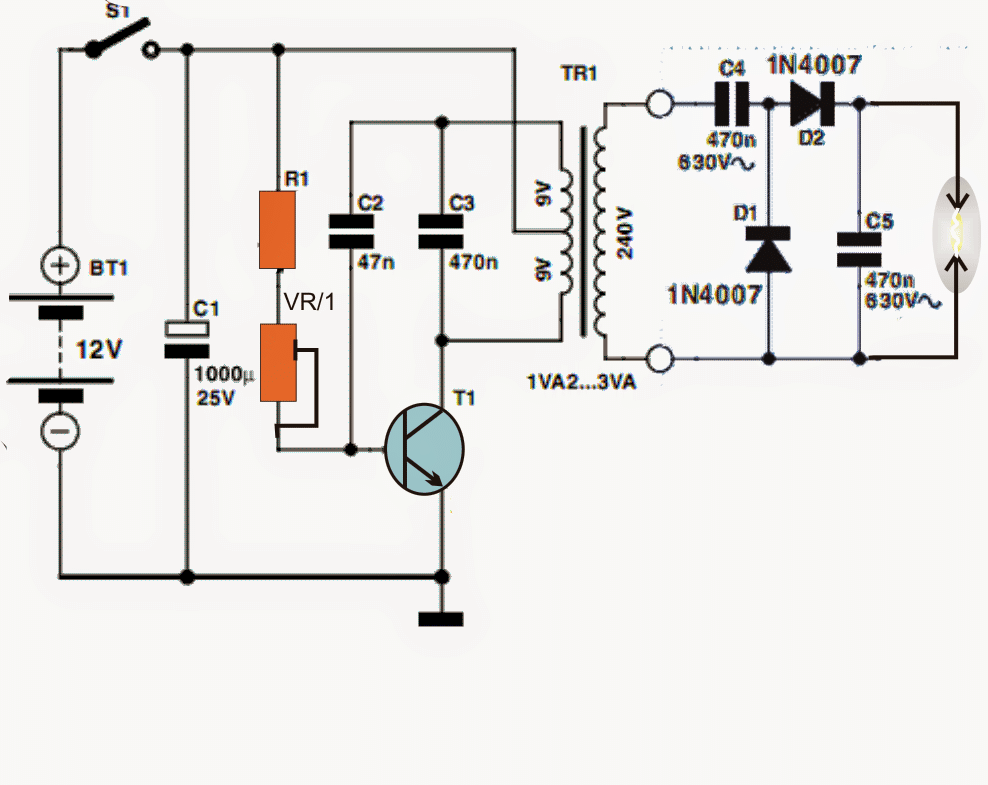
The upper half of the transformer winding simply provides a feedback to the base of the transistor via C2 such the T1 stays locked on to the conduction mode until C2 charges fully, breaking the latch and forcing the transistor to begin the conduction cycle afresh.
R1 which is a 1K resistor is positioned to limit the base drive for T1 to safe limits while VR1 which is a 22k preset may be adjusted for obtaining an efficiently pulsating T1 frequency.
C2 may be also fine tuned by trying other values until the highest possible output is attained at the trafo output
The transformer could be any iron-cored step down transformer (500mA) normally used in transformer type AC/DC adapter units.
The output right across the transformer output would be at the rated secondary level, for example if it is a 220V secondary, then the output could be expected to be at this level.
The above level could be further amplified or stepped up through the attached diode, capacitor charge pump network akin to cockroft-walton generator network.
The network raises the 220V level to many hundreds of volts which may be forced to spark across an appropriately positioned end terminals of the charge pump circuit.
The circuit can be also used in mosquito swatter bat application by replacing the iron cored transformer with a ferrite core counterpart.
High Power 10 kv Generator Circuit
If powered with a 30 V power input, the circuit detailed below can provide a high voltage which range from 0 to 3 kV (type 2 an even provide from 0----10 kV. NAND gates N1----N3 are wired like an astable multivibrator (AMV), which powers the darlington transistors T1/T2 with a 20kHz souarewave frequency.
Because of the reduced current circulation (decided by R4 via the transistors, they are not able to get saturated, leading to a quick switch-off. The incredibly rapid switching of the transistors generates a pulsating signal of around 300 V across the primary winding of Tr1.
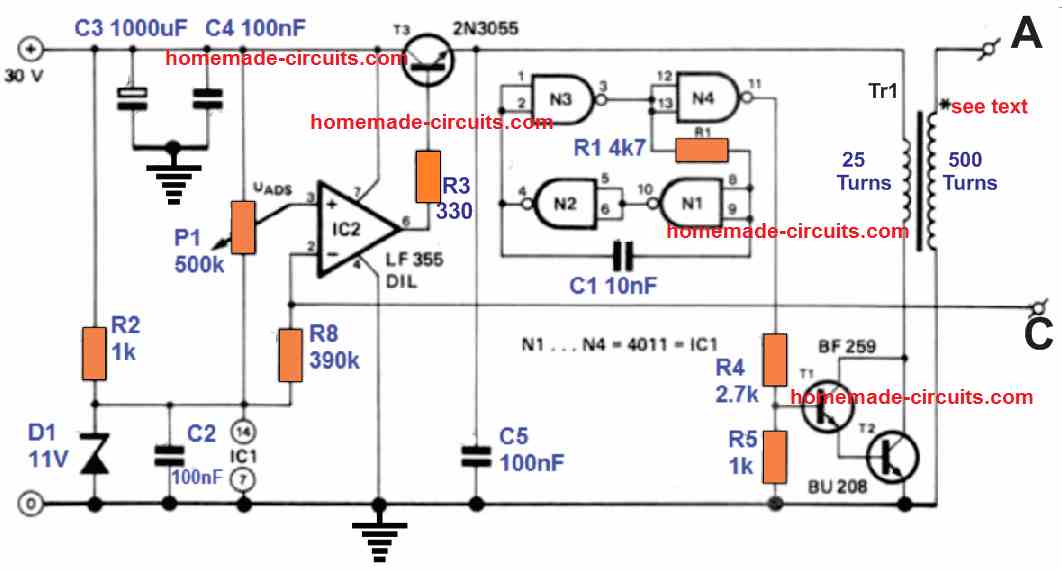
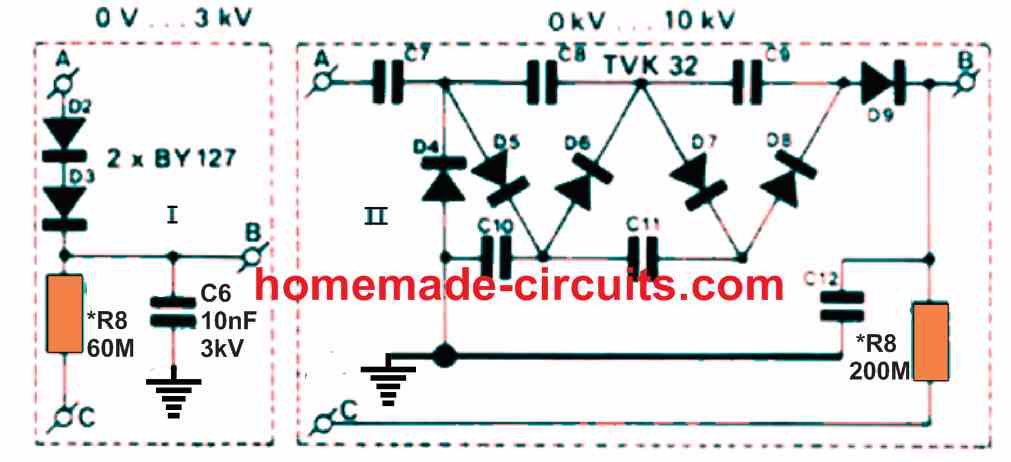
This voltage is subsequently boosted and stepped-up proportionately as per the turn ratio of the secondary windings. The 1st variation (type 1) of the circuit employs half-wave rectification. Version 2 is actually a cascade rectifier salvaged from an old T.V. set.
Variation 2 provides a voltage 3 times greater than version 1 since the cascade rectifier functions like voltage multiplier (3X). IC2 controls the output voltage.
The opamp compares the voltage created across the P1 preset with the voltage existing at the voltage dividers R6/R8 or R7/R8 junction.
In the event the output goes higher than the preset voltage level, IC2 may cut down the supply voltage towards the output by using T3.
The main section of the circuit is the transformer. Eventhough it is pretty vital, its design isn't that critical.
A range of E, EI ferrite cores with a diameter of 30 mm might work extremely well pretty effortlessly.
The core must not include any kind of air gap, an AL value of 2000 nH will be just appropriate.
The primary winding includes 25 turns of 0.7 mm 1 mm super enamelled copper wire and the secondary is built using 500 turns of 0.2 … 0.3 mm super enameled copper wire.
The primary and secondary windings needs to be effectively insulated from one another!
Dependent upon the high voltages, the user must be careful about the following points:
Capacitor C6 should have the ability to handle a minimum of 3 kV. R6 in version 1 includes six 10 M resistors connected in series. R7 is a 10 M resistor, built by using 10nos of 1M in series.
This is implemented to counteract spikes from the output. Both circuit takes in around 50 mA with no load attached, and 350 mA while ensuring 2 … 3 W to a load.
Transistors T2 and T3 may demand heatsinks.
9V to 300V Generator Circuit
The use of voltage multipliers to generate larger output voltages is typically less expensive only when the desired voltages are lower than 6 times the supply voltage.
Other circuit configurations are advised when hugely large step-up ratios are necessary (e.g., hundreds of volts supplied through a 12-volt supply).
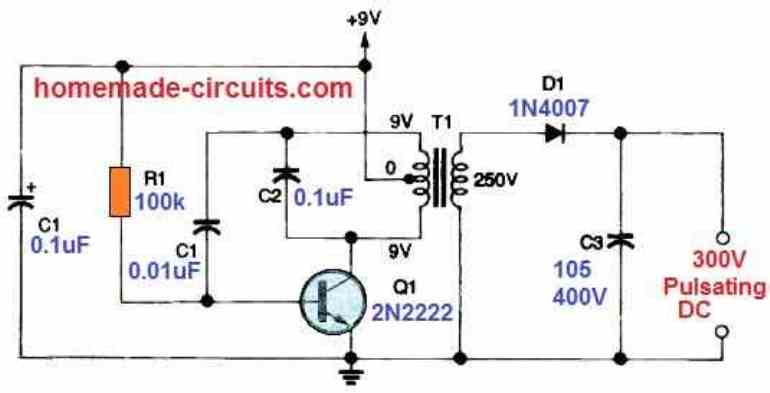
As shown in the above diagram, the output of a cheap low-voltage oscillator or square wave generator may generally be used as the input of an appropriate step-up voltage transformer (an ordinary step-down transformer connected in reverse).
The transformer's secondary winding produces the desired high AC/DC output voltages.
With a simple DC-to-AC converter, this AC power could be quickly converted back to DC. A DC-to-DC converter circuit as depicted above is able to create a 300-volt DC output out of a 9-volt Dc power supply.
The Hartley inductive-capacitive (LC) oscillator is formed by transistor Q1 and its accompanying electronics in this design. The primary winding voltage, which varies from zero and nine volts, is fed to the 250-volt transformer T1.
The inductive component in the LC oscillator is the main inductance, that is adjusted through capacitor C2. At the secondary of T1, the voltage level is boosted up to roughly 350 volts peak.
Diode D1 half-wave rectifies this output, which charges capacitor C3. The capacitor has the potential to deliver a strong yet non-lethal electrical shock with minimum loading on C3.
With a load current of a few milliamperes, the output decreases to around 300 volts when a permanent load is connected.
High Voltage Generator Using a Single IC 555
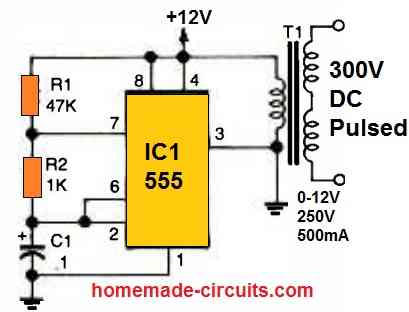
A simple low power high voltage generator can be built using the IC 555 and a step down 0-12V transformer.
The IC 555 is wired as a high frequency oscillator which switches the 0-12V side of the transformer with a 12V/200mA supply.
This induces an equivalent high voltage pulsating DC on the other side of the transformer to generate around 300 V pulsating DC at the output.
Using Ignition Coil
The next circuit we'll look at is a solid-state negative ion generator. This circuit, depicted in Fig. 6, is pretty much the easiest to design and use.
A low-frequency pulse is generated by a 555 timer IC, which drives the gate of Q1, a power HEXFET. In turn, the IRF511 transmits a high-current pulse into the primary of the automotive ignition coil T1.
The secondary winding generates many thousand volts, which are rectified by diode string D1—-D35 and used to charge C3.
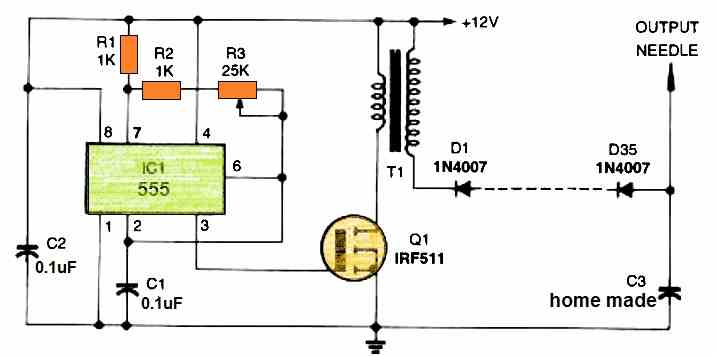
One or more sharp needles blasts the ions into air. C3 can be created at home or obtained from market.
Set the frequency of IC 1 with potentiometer R3 to the maximum output voltage with the minimum input current.
To get the highest output and circuit efficiency, you can tinker about with R3.
12V to 600V Generator Circuit
A 12 V battery will allow this high voltage converter circuit to produce a voltage of around 600 volts.
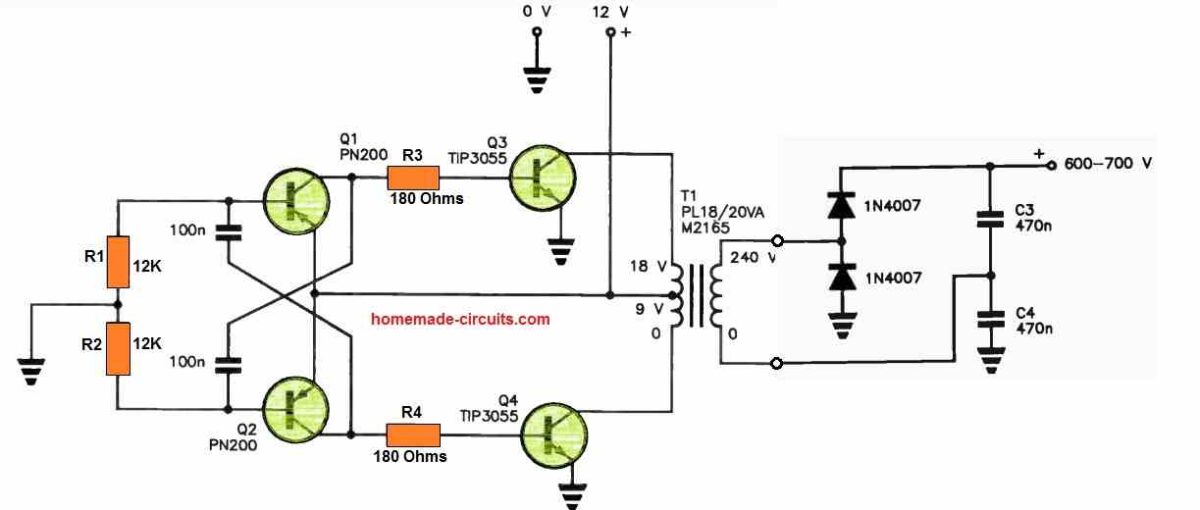
There is no need for an special inverter transformer. T1 is only a standard mains transformer with two 9 V windings or an 18 V secondary that is center-tapped.
Base drive is provided to switching transistors Q3 and Q4 by a flip-flop oscillator employing Q1 and Q2.
The 12 V supply is switched across each half of the 9 V windings alternately by these power transistors, which act as the primary winding in this application.
As the secondary, the 240 V mains winding powers a full-wave voltage-doubler rectifier.
The transformer continues to function well when the oscillator is operating at a frequency of roughly 1 kilohertz.
The rectifier doesn't require any electrolytic capacitors, which saves space, lowers costs, and increases dependability. Only 400 V rated polyester caps [greencaps] are required for C3 and C4.
Because switching transistors have some collector-emitter voltage loss, nine volt transformer windings are utilized instead of 12 volt ones.
It is important to note that Q3 and Q4 should be installed atop a heatsink.