In this post I have explained an induction cooker/heater design which may be powered from a solar panel voltage. The idea was requested by Mr. Vamshee
Technical Specifications
My name is Vamshee and i am from hyderabad , India I am a small time entrepreneur looking to promote and sell new age products into the market .
Right now really interested in renewable energy resources .
After reading your blog and being following it from a while I would really appreciate your interest being hired by me if you are interested in the project about induction cooking with solar panel at a very very cheaper cost .( would like to introduce it to the poor ) with the help of govt schemes here in my state .
Specs what i was looking was about
180w solar panel
transformerless inverter ( built inside the induction cooker)
max output of 500W induction stove ( Coil type )
Usage for : heating water,milk , make one time meal in a day .
I am sorry if the specs i gave you might be wrong as i am not from a science background ,but just some calculations reading from the internet . so i have no idea about this , but just have the concept and can sell the product .
I have gone through 12v cooking pans and stuff like those on google but in vain to find any solutions .
I hope to hear from you soon about this project and make it prospective to talk about a bright future .
Regards
Vamshee
Simple Method: Just Hook up any Standard Induction Heater with a Calculated Solar Panel! That's all!
Step #1: I would recommend purchasing a standard 500 watt Induction heater, rather than building yourself at home.
The specification of the induction heater can be 12V 500 watt. This would mean the induction heater would require a maximum current of 500/12 = 41.66 amps or 42 amp current.
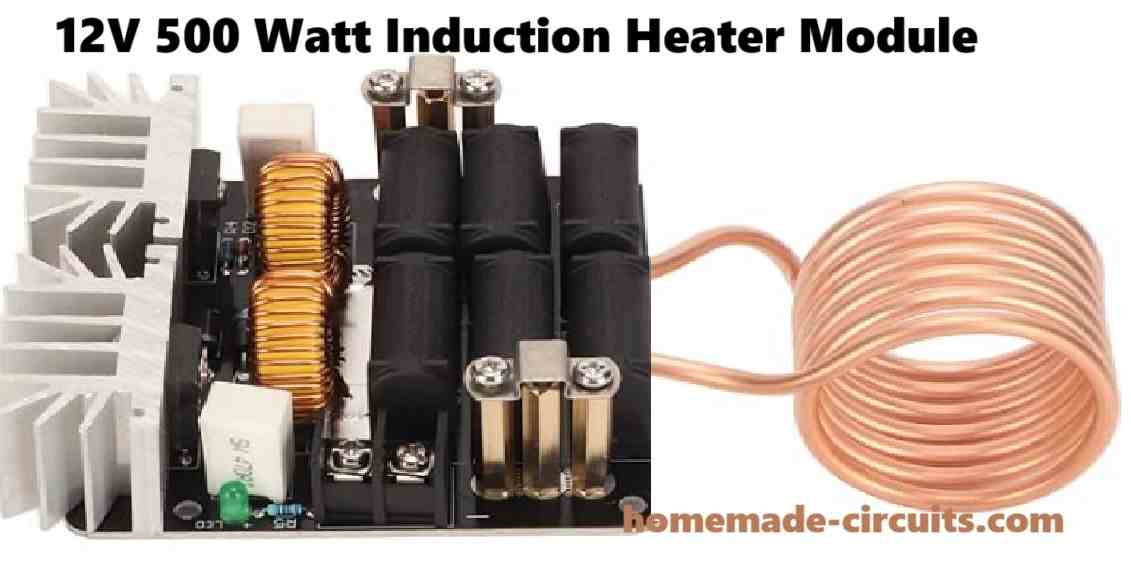
Step #2: Buy a solar panel rated at 500 watt. I would recommend getting a 60 V panel. So, 500/60 = 8.33 amps. That means the solar panel needs to be 60V, 10 amp rated.
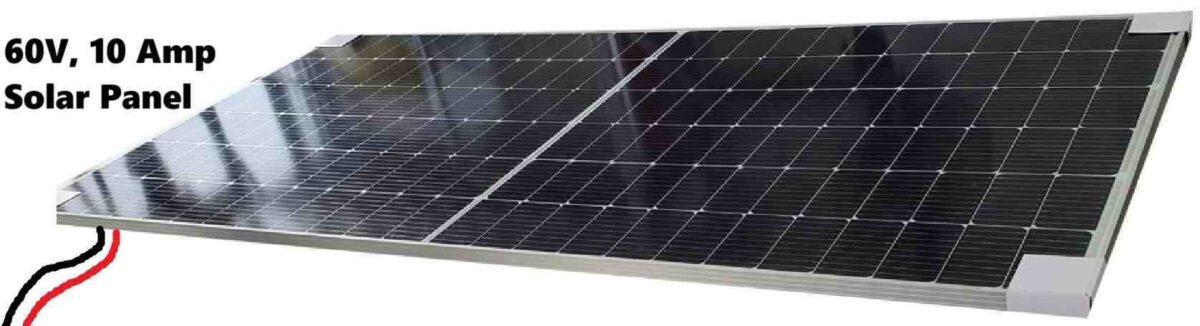
Now, this solar panel output needs to be stepped down to 12V for the induction heater., so we need a buck converter for this.
Step #3: Buy or build a Buck Converter rated to handle 100V input and produce adjustable output.
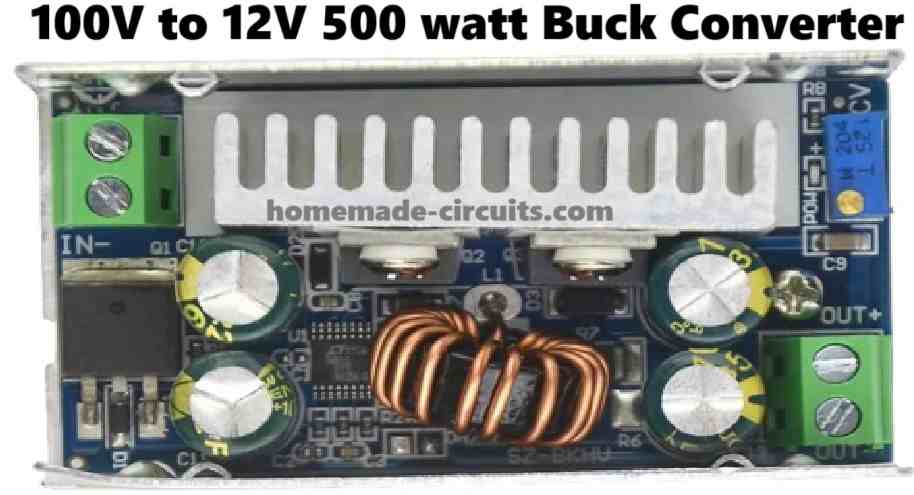
If you want to build your own buck converter circuit, then can very easily build and customize it, as per the instructions provided in this article.
Step #4: Hook Up the buck converter with your solar panel output and adjust the buck converter output to match the operating voltage of your induction heater.
Step #5: Connect the induction heater with the set output from the solar panel integarted buck converter, and that's it! You have now completed your solar induction heater circuit and are ready to cook anything you want with this set up.
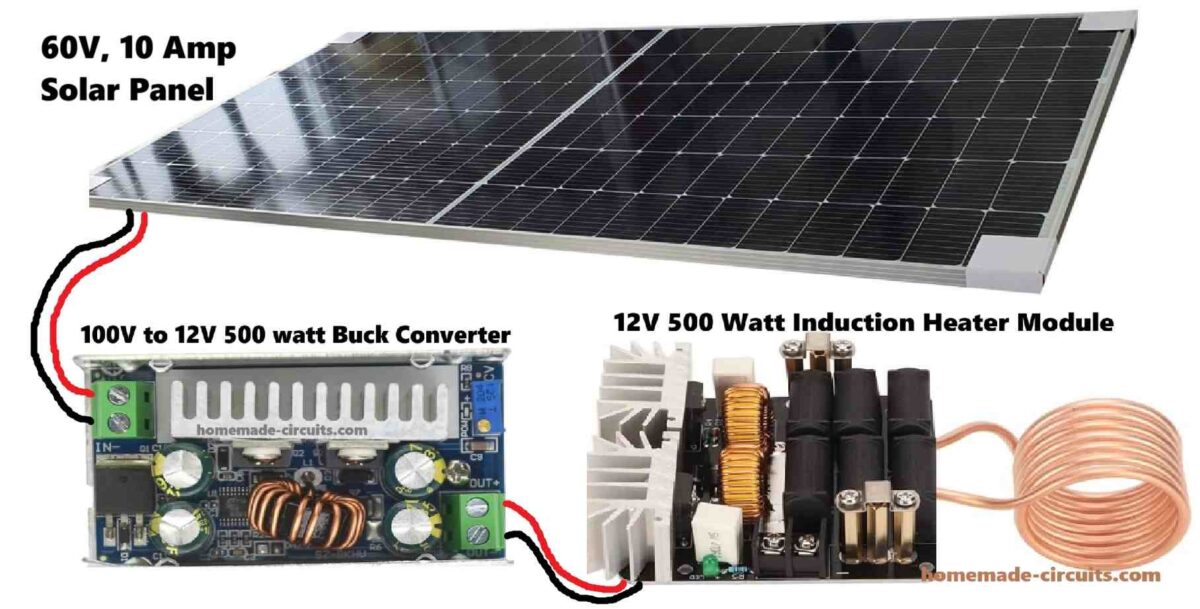
Using IC IR2155 Oscillator
As per the specifications a 500 watt output is intended to be achieved from a 180 watt solar panel which may not be feasible in the practical world, therefore the correct solar panel parameter for the proposed solar induction heating system should be approximately 600 watt, or two 180 watt panel in parallel can also be tried for optimal results, this won't be cheap, though.
The panel specs could be anywhere from 30 to 44 V and the amp rating between 20 and 10 amps, and will require a buck regulator in order to step down the voltage to the required levels for the induction heater circuit.
A suitable induction heater circuit can seen below which uses a half bridge driver topology, the schematic is pretty straightforward and may be understood as follows:
Circuit Diagram
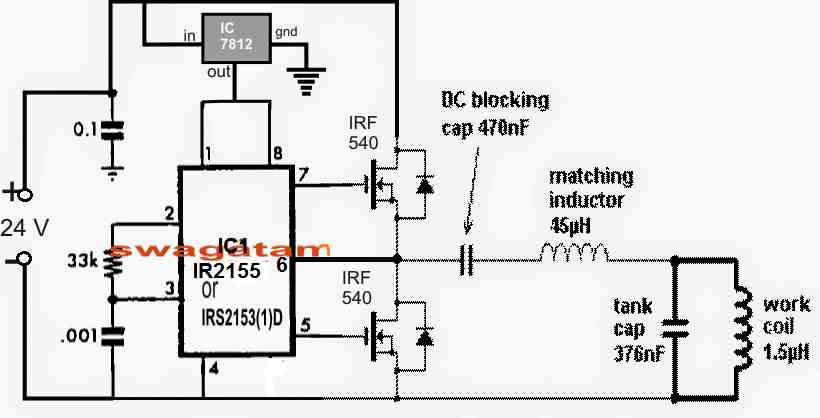
The circuit is driven from a 24 V DC supply, at current ranging up to 15 amps. A 7812 voltage regulator drops the input voltage to 12V for the driver IC which is a standard half bridge driver IC IRS2153 or any other similar.
The push pull output from the IC drives a pair of mosfets which in turn forwards the oscillations to the main work coil of the induction heater via a DC blocking capacitor and an impedance matching inductor.
The blocking capacitor prevents excessive current from passing through the work coil and stops damaging the mosfets while the inductor makes sure no disturbing harmonics get into the line and induce inefficiencies into the system.
The 376 nF tank capacitors are used to achieve a resonance with the work coil at about 210 kHz frequency which is set by the R/C network across pin2 and pin3 of the driver IC. The 33k resistor could be made variable for fine tuning or optimizing the resonance effect.
The Work Coil Size
The work coil dimensions and the resonant capacitor arrangement are provided in the image below:
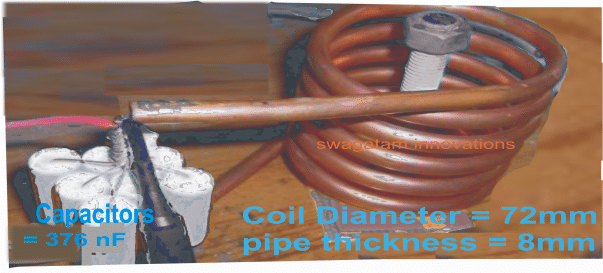
Buck Converter Specifications
A buck converter for converting the panel high voltage to the required 24 V for the induction heater may be built with the help of the following diagram:
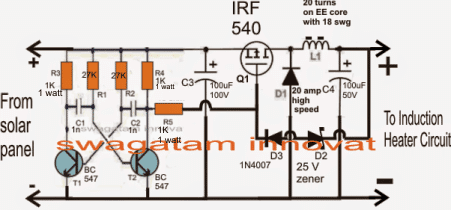
T1, T2 together with C1, C2 and the associated resistors form a classic astable multivibrator (AMV) with a set frequency of around 30 kHz.
The panel volatge is fed to the above AMV and oscillated at the said frequency before feeding it to the buck converter stage made by employing a mosfet and an associated diode, inductor stage.
During the switch OFF periods an equivalent amount voltage is delivered from L1 in the from of back EMFs which is appropriately filtered and supplied to the connected induction heater circuit across the output terminals.
C4 makes sure the converted bucked voltage is free from any ripples and helps in producing a cleaner DC for the induction heater circuit.
The regulated 24 V DC at the outputs may be achieved by roughly winding the correct number of turns for L1 through some trial and error and also by the incorporation of D2 which ultimately stabilizes the output voltage to the required levels.