In this post I have explained how the internal body diodes of MOSFETs could be exploited for enabling the charging of battery through the same transformer which is being used as the inverter transformer.
In this article we will investigate a full bridge inverter concept and learn how the in-built diodes of its 4 MOSFETs could be applied for charging an attached battery.
What is a Full Bridge or H-Bridge Inverter
In few of my earlier posts we have discussed full bridge inverter circuits and regarding their working principle.

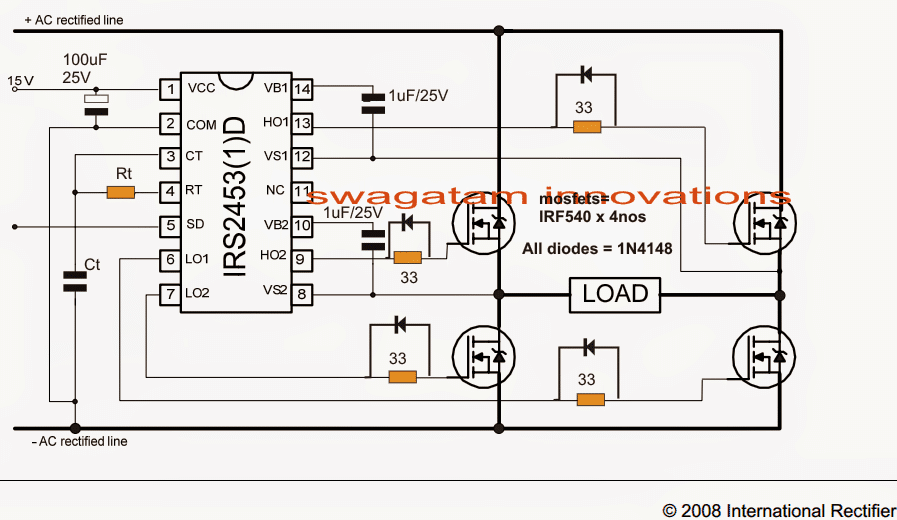
As shown in the above image, basically, in a full-bridge inverter we have a set of 4 MOSFETs connected to the output load. The diagonally connected MOSFET pairs are alternately switched through an external oscillator, causing the input DC from the battery to transform into an alternating current or AC for the load.
The load is normally in the form of a transformer, whose low voltage primary is connected with the MOSFET bridge for the intended DC to AC inversion.
Typically, the 4 N-channel MOSFET based H-bridge topology is applied in full bridge inverters, since this topology provides the most efficient working in terms of compactness to power output ratio.
Although using 4 N channel inverters depend on specialized driver ICs with bootstrapping, yet the efficiency overweighs the complexity, hence these types are popularly employed in all modern full bridge inverters.
Purpose of MOSFET Internal Body Diodes
The internal body diodes present in almost all modern day MOSFETs are primarily introduced to safeguard the device from reverse EMF spikes generated from a connected inductive load, such as a transformer, motor, solenoid etc.
When an inductive load is switched ON through the MOSFET drain, electrical energy gets stored instantaneously inside the load, and during the next moment as the MOSFET turns OFF, this stored EMF is kicked back in the reverse polarity from MOSFET source to drain, causing a permanent damage to the MOSFET.
The presence of an internal body diode across the drain/source of the device thwarts the danger by allowing this back emf spike a direct path through the diode, thus safeguarding the MOSFET from a possible breakdown.
Using MOSFET Body Diodes for Charging Inverter Battery
We know that an inverter is incomplete without a battery, and an inverter battery inevitably requires charging frequently to keep the inverter output topped-up and in the standby condition.
However, charging a battery requires a transformer, which needs to be a high wattage type to ensure optimal current for the battery.
Using a additional transformer in conjunction with the inverter transformer can be quite bulky and costly too. Therefore finding a technique in which the same inverter transformer is applied for charging the battery sounds extremely beneficial.
The presence of the internal body diodes in MOSFETs fortunately makes it possible for the transformer to be switched in the inverter mode and also in the battery charger mode, through some easy relay changeovers sequences.
Basic Working Concept
In the diagram below we can see that, each MOSFET is accompanied with an internal body diode, connected across their drain/source pins.
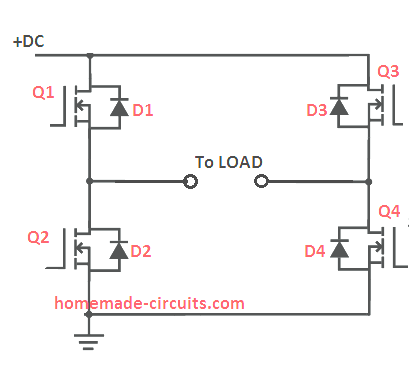
The anode of the diode is connected with the source pin, while the cathode pin is associated with the drain pin of the device. We can also see that since the MOSFETs are configured in a bridged network, the diodes also become configured in a basic full-bridge rectifier network format.
A couple of relays are employed which implement a few quick changeovers for enabling the grid AC to charge the battery via the MOSFET body diodes.
This bridge rectifier network formation of the MOSFET internal diodes actually makes the process of using a single transformer as an inverter transformer and charger transformer very straightforward.
Current Flow Direction through MOSFET Body Diodes
The following image shows the direction of current flow through the body diodes for rectifying the transformer AC to a DC charging voltage
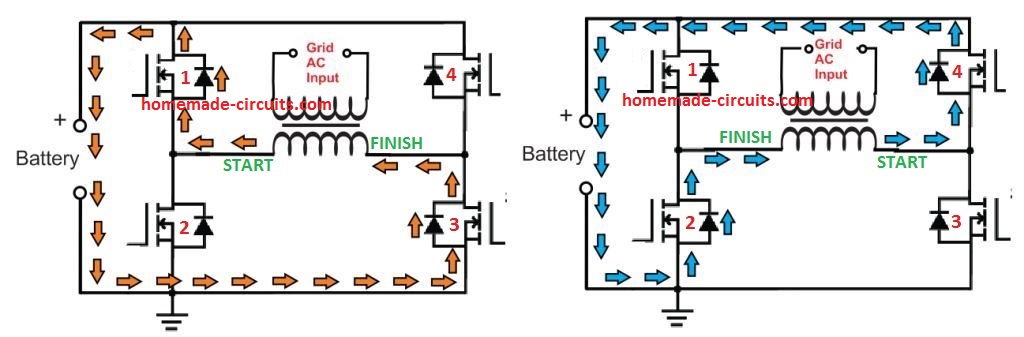
With an AC supply, the transformer wires change their polarity alternately. As shown in the left image, assuming the START as the positive wire, the orange arrows indicate the flow pattern of current via D1, battery, D3 and back to the FINISH or the negative wire of the transformer.
For the next AC cycle, the polarity reverses, and the current moves as indicated by the blue arrows via body diode D4, battery, D2, and back to the FINISH or the negative end of the transformer winding. This keeps repeating alternately, transforming both the AC cycles to DC and charging the battery.
However, since MOSFETs are also involved in the system, extreme care has to be exercised to ensure that these device do not get damaged in the process, and this calls for a perfect inverter/charger changeover operations.
Practical Design
The following diagram shows a practical design set up for implementing MOSFET body diodes as a rectifier for charging an inverter battery, with relay changeover switches.
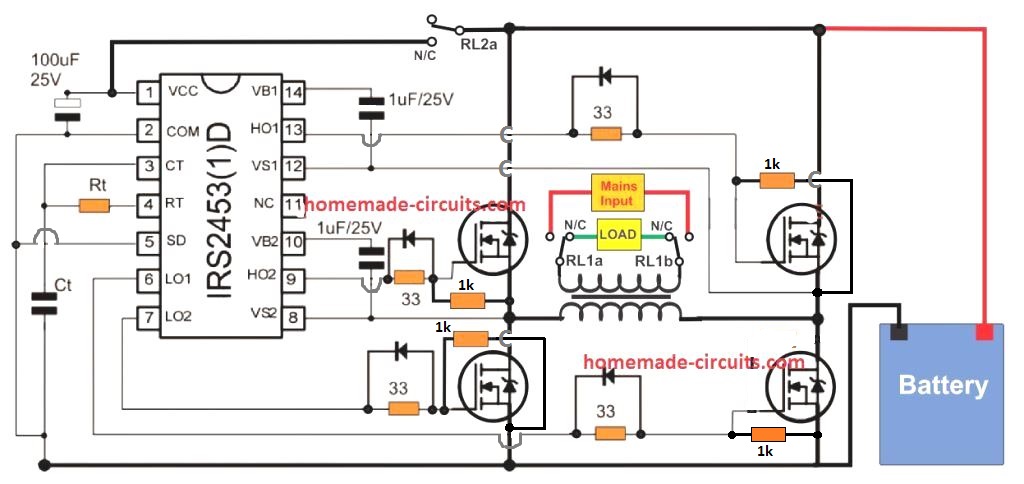
To ensure 100% safety for the MOSFETs in the charging mode and while using the body diodes with the transformer AC, the MOSFET gates must be held at the ground potential, and completely cut-off from the supply DC.
For this we implement two things, connect 1 k resistors across the gate/source pins of all the MOSFETs, and a put a cut-off relay in series with the Vcc supply line of the driver IC.
The cut-off relay is an SPDT relay contact with its N/C contacts connected in series with the driver IC supply input. In the absence of AC mains, the N/C contacts remain active allowing the battery supply to reach the driver IC for powering the MOSFETs.
When mains AC is available, this relay changes over to the N/O contacts cutting off the IC Vcc from the power source, thus ensuring a total cut off for the MOSFETs from the positive drive.
We can see another set of relay contacts connected with the transformer 220 V mains side. This winding constitutes the output 220V side of the inverter. The winding ends are connected with the poles of a DPDT relay, whose N/O an N/C contacts are configured with the mains grid input AC and the load respectively.
In the absence of mains grid AC, the system works in the inverter mode, and the power output is delivered to the load via the N/C contacts of the DPDT.
In the presence of an AC grid input, the relay activates to N/O contacts allowing the grid AC to power the 220V side of the transformer. This in turn energizes the inverter side of the transformer and the current is allowed to pass through the body diodes of the MOSFETs for charging the attached battery.
Before the DPDT relay is able to activate, the SPDT relay is supposed to cut off the Vcc of the driver IC from the supply. This slight delay in activation between the SPDT relay and the DPDT relay must be ensured in order to guarantee 100% safety for the MOSFETs and for the sound operations of the inverter/charging mode via the body diodes.
Relay Changeover Operations
As suggested above, when mains supply is available the Vcc side SPDT relay contact should activate a few milliseconds before the the DPDT relay, at the transformer side. However, when the mains input fails, both the relays must switch OFF almost simultaneously. These conditions could be implemented using the following circuit.
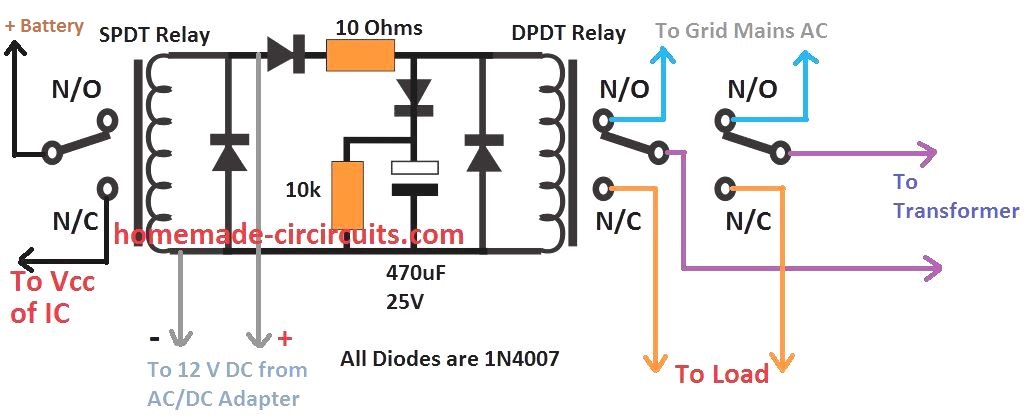
Here, the operational DC supply for the relay coil is acquired from a standard AC to DC adapter, plugged with the grid mains.
This means, when grid AC is available, the AC/DC adapter powers ON the relays. The SPDT relay being connected directly to the DC supply activates quickly before the DPDT relay can. The DPDT relay activates a few milliseconds later due to the presence of the 10 ohm and the 470 uF capacitor. This ensures that the MOSFET driver IC is disabled before the transformer is able to respond to the grid AC input at its 220 V side.
When mains AC fails, both the relay switch OFF almost simultaneously, since the 470uF capacitor now has no effect on the DPDT due to the series reverse biased diode.
This concludes our explanation regarding using MOSFET body diodes for charging an inverter battery through a single common transformer. Hopefully, the idea will allow the many hobbyists to build cheap, compact automatic inverters with built-in battery chargers, using a single common transformer.
hi… swagatam , I have once contributed about this mosfet body diode inverter circuit.here are the research I did about it which give clear explanation on bi-directional inverter with voltage boosting and current regulations when charging and inverting.
my request here is to ask you if you can create an article with schematics for it.
this are the research documentary should I post it here or via your email what’s your email if u decide?
Thank you David,
However I will need a schematic for updating the information. Without a schematic it will be difficult for me to create the article.
If you have done the experiment yourself then please provide the images of the prototype, if possible I will try to figure out the diagram…
okay, I can draw the circuit related to block diagram but I want you to go through the research I did which can will still make it easy and understanding with that you can create a schematics with reference to the research on chatgpt
I understand your desire to learn more on this subject, however I cannot use chatgpt information to publish on this site, because Google does not like AI based research, Google always prefers practical research based on real human analysis.
okay then, I will try to sketch out the schematics diagram for you to see it.
That would be great, let me know when it is ready with you….thanks very much for your kind efforts.
Very interesting post… My experience working with inverters (mostly modified sine) has built in chargers and they usually use a triac when the public grid is present. They switch through a CH relay (sometimes use DTDP relays to do this task and transfer), botton line is that triac is controlling a “Chargin tap” in the transforner normally 90VAC tap (fed with 120AC) on a 120AC transformer (double for 220VAC) which increase the charging voltage at Mostef Side. Microcontroller takes care of the 3 stages charging profiles. My question is that I’m building a sine wave inverter with 3 stages charger, the controller is meant to work 12,24,36 and 48vdc depending of some jumpers. I’m using the traditional Triac on charging Tap in the Hivoltage side of the transformer . But my Power board (6KW) it has the snubber circuit and polarizing circuit (resistor and diode) and a 20kohm resistor across gate/source instead the 1kohm as you stated . This 20k resistor will work for the same task of charging (full bridge config is used by this sinewave inverter). Thanks in advance
Hi, thanks for the feedback, and glad you liked the post.
The resistor values across the gate/source of the MOSFFETs is not critical, so a 20k resistor should also be fine. It is simply because MOSFET gates have extremely high impedance in many Megaohms, therefore a 20k will be sufficient enough to hold the gates to the ground level while they are switched OFF.
Perfect. Thanks for your kind reply.
You are welcome…
Chinonso you cannot increase your output current when charging because input mains is low all you have to do is to design a switching stabilizing unit using a ferosonite system for your inverter mains input
Hello Mr. Swagatam. Thank you alot for the illustrations.
I’ve built an hbridge an hbridge inverter of this kind through your professional guidance, the system is working well, fully automatic. However, when in charging mode, and maybe the mains supply is of low voltage, the charging gets stagneted or slows down drastically. Please, is there a way I could include a feedback using autocoupler so as to increase the efficiency of the charging process and also no damage the MOSFETs. Thanks
Hello Chinomso,
A feedback can only help to control an excessive or over voltage situation, a feedback in inverter system are not designed to boost a low voltage situation. So in your case a feedback will not help to increase the charging voltage or efficiency.
Most of low frequency inverters (uses 50/60hz transformers) use a charging tap at high voltage side of the inverter (90vac for a 120Vac inverter as reference) . A triac it is used here and controlled by a microcontoller to achive 3 stages charging system , this will boost the voltageat low voltage side of the transformer when main are present and charging is needed.
Your post here Mr. Swagatam,partly answers my previous request for your assistance on MOSFETS dual function of this sort. However sir, my resquest is on a center-tap transformer based inverter. Does this system still applies in my own design?. If not, please what must I do to stop my MOSFETS from blowing up each time I try to charge my batteries. Thanks
Hi Chinomso, Can you please ask this question under the same post where you are having the issue. I will try to help.
While I agree with this article in principle, I do have concerns.
Using the body diode for higher-power projects is something I typically avoid, mainly for thermal management and EMI. That body diode was optimized for reactive flyback energy within the immediate circuit, in the loads, and not a whole lot more. In my view, the feasibility is not in question, but the practicability is. Very fast diodes are typically used with power MOSFETs. Putting an increased thermal load on the device is not always a great idea. These concerns become all the more important when working with larger systems involving “brick” MOSFET modules, IGBTs, and the newer Power SiC devices.
The use of a full-power diode is especially important in the bi-directional inverters we are now seeing in battery energy storage systems (BESS) that process power in both directions.
Thank you so much for the valuable information. It is much appreciated.
Hiii
Dear
How we can adjust and control the voltage and the amperes of these mosfets when we have the batery charger mode…
Please!
Hello, Unfortunately voltage and current cannot be changed in this design. However since the discharge rate of the battery will be the same as the charging rate, so the transformer current will be compatible with the battery.
Hi… Swagatam
For a 24v 220ah battery the transformer should be able to handle 220amps at inverter mode, then at charging mode the current from the transformer would be extremely high which can destroy the battery.
Charging the battery should be at 1c or 2c (22amps or 30amps).
So how do we bring down the charging current to 22amp or 30amps when the transformer is at charging mode pls i need your help…
Hi David,
A 220 Ah battery can be charged or discharged at 220 amps only if it is a Li-Ion or Li-Po battery.
If it is a lead acid battery or an SMF battery then it must charged and discharged at 0.15 C rate meaning it cannot be charged or discharged over 30 amp rate.
Therefore the transformer must be rated according to the above 30 amp current rating.
Just an observation. Having just repaired a 1000w220vac/ 12vdc inverter charger where the pcb tracks had been severely burnt, replaced 16 mosfets 40v 180amp devices, the primary winding is single 6volt load in the H bridge. The charging waveform is a switched pulse, with the current in the 6volt winding being in excess of 100amps but the initial pulsed charging current into the battery being around 30amps upto 14.8volts at the first rate and reducing to 13.8 volts. The battery used is a 64amphr at the 5hr rate. The charging waveform is not like one would expect from a normal full wave bridge. Each pulse is made up of high frequency pulses.
How about in a case of a center taped transformer with just two MOSFET, how do the charging work?
Hae sir, I have read it but does the circuit cut off whn the battery reaches the full charge threshold and whn the battery is at the low level? Secondly can I use any MOSFETs like IRF1405 or cs150n03 and instead of four pieces can I connect four in in parallel on each side?
Hi Morris, there is no provision for an automatic cut off in this circuit. You will have to employ opamps for getting this feature.
Yes you can use any desired mosfets provided the power rating is correctly matched with the power of the transformer. You can as many mosfets as you want for increasing its power handling capacity.
But can u check if cs150n03 mosfet can be used in a 24v inverter despite it voltage rating pliz confirm or it’s best suited for 12v inverter
Its VDSS rating is 30V, while a fully charged 24V battery may have a voltage level of 26V which is quite close to 30V so i won’t recommend this mosfet for a 24V inverter. You can try IRF3205 instead.
How efficient is this body diode inverter compared to the normal ordinary one which u use a separate charger? Secondly I got a power supply with a fixed 12v 12.5amp. Can this charge 200ah battery to the full level threshold despite the more time it will take? Advise, thanks.
I have not it tested the design practically so it can be difficult for me to tell how efficient the design is. A 12V 200 Ah battery will require a minimum of 14 V 20 amp supply, so your power supply cannot be used for charging the battery.
And is there any using a center tap wire pliz? Secondly, is there any modified sine wave inverter using a two wire without center tap?
Right now I don’t have any of those circuits, if I happen to find one will surely update it for you…
Sir what is the Rt value
You can calculate it using the following formula
f = 1/1.453 x Rt x Ct
f is frequency, Ct is capacitor which must be in Farads.
Thanks for this tutorial. In this schematic, there is no current control for the battery charging. If battery charging current is very high, the battery life will decrease. What should I do to limit the battery charging current?
Yes you are right, the only apparent way to control the input current is by adding a 10uF or 20uF capacitor in series with the Mains Input line connecting the transformer primary, 10uF would limit 500 mA input maisn at 220V, 20uF would limit 1 amp at 220V and so on. This means 9 amp at the battery side at 12 V for 10uF, and 18 amps at 12 V….
Hi Swagatam,
Can you post boost fpc charging techniques in h bridge inverter for pure sinewave.
This will be very helpful for the new inverter system repair and find out charging issues.
Hi Sherafudheen, Can you please elaborate more on the topic, because I have not yet investigated boost fpc tech, so don’t know much about it at this moment of time!
In sine wave inverters charging technique is called boost pfc.
In h-bridge configuration during battery charge we shorted lower mosfet with 7 khz pwm signal.
And due to leakage inductance of transformer in 7v winding we can get 13.8v.
OK, thank you! Actually Boost power factor correction is a technology for improving the power factor of the input AC supply using a boost converter inductor.
I don’t think it is specifically used in sine wave inverters.
It can be used in all types of power supplies, inverters, and converters.
Also this may be relevant in online UPS systems where the AC supply is used for charging the battery and also for powering the inverter simultaneously.
In charging concept as above where a MOSFET body diodes are used, using boost PFC can be very difficult, and could make the design too complex!
Anyway, I will try to post one article on boost PFC which is meant for improving the efficiency of a power supply
Hi Swagatam,
Thanks for your support,
Actually almost new h-bridge sine vawe inverter the primary voltage is 6 to 7 volts for the 12 volts system.
So when we supply 240volts to secondary for charging thr volts will be below 12 volts and not possible to charge the battery?
In this case what we can do?
You are welcome Sherafudheen,
Yes I understand, the boost converter boosts the lower voltage from the transformer upto the battery charging level, since in PWM circuits, the transformer primary is rated lower than the battery, in order to be compatible with the PWM average DC level.
But while using body diodes, adding the boost circuit between the transformer and the battery can be quite complex, I am not sure how this can be done in a simple way…
may be this can be implemented by adding another set of relay contacts…?
Hello, I am actually looking for solution to this problem. In a 12v inverter, a 7v-220v transformer is often used. If you apply 220v AC mains, the voltage at the mosfet side will be 6v, which is not enough to charge a 12v battery. I have also read it online that the boost Pfc method is used to boost the voltage. But I can’t find any circuit anywhere.
Pls help.
I think there is a small correction—cathode is connected to Drain of the Device——–“The anode of the diode is connected with the source pin, while the cathode pin is associated with the source pin of the device. “
Thank you, noted and corrected!
Also sir,can any mosfet charge? Also how should one match battery charging amperes and the mosfet amperes. Can high mosfet switching amperes have effect to the battery and or the mosfets during charging?.I have tried the charging side and it’s working fine but for my sake I used irfp1404 . The circuit did well for sometime like 2hrs but blew mosfets on one side. My transformer has an output of 0-20v 50A charging 2×12v 200Ah batteries. I connected the gates to source using a 10k resistor. What do you think is wrong or what might have I done wrong?
I am glad it is working…The back diodes are provided for supporting low current spikes, it is not provided for consistent high current use, therefore for the above explained battery charging application, we must reinforce the body diodes with external high current diodes.
MOSFETs have no role in this application and will remain unresponsive and safe, unless the diode functioning breaks or stops working
Sir so when the back diode breaks causes the whole mosfet to be affected? Again sir advise me,say I need 50A min charging current,how many amperes of a diode should I use for each mosfet for the reinforcement?. Or what if I parallel more mosfets to deal with the issue of back diode amps?
Evans, the diodes must be rated at two times the estimated charging current value.
Okay sir
Sir I have read a certain article on Google,the article says that the mosfet current rating is the same as the mosfet’s body diode,an yet to understand with regard to what you had told me earlier that mosfets body diodes are provided for supporting low current spikes, please where can I send you the article so you can go through so you can advise? Your address please and I will appreciate.
Evans, It was just an assumption because I thought it did not make sense to put a body diode with the same current specs as the MOSFET. But it seems the diodes are being introduced not just for spike protection but also for a full-fledged use as reverse diodes. the following datasheet shows that the mosfet Id and the diode current specs are actually similar
https://www.vishay.com/docs/91560/sihw47n60ef.pdf
That’s right sir,now what could lead to blowing of one side of mosfets infact 4 of irf1404 when charging 1 n70 12v battery? Just like that. But in inveter mode,the inverter function very well in no heat is felt. Even when charging,no heating at all but one side of mosfets just blows off,this has happened to me twice?? Any help or anything am not doing right?? Coz I did as you directed interms of mosfets protection.
I think you should try disconnecting the MOSFETs gates completely from the drive source, and have a 1k resistor connected across gate/source of each MOSFETs. With this configuration try applying their reverse diodes for the rectification of the transformer AC and see how it works.
Fine Sir,let me try that and will be back with feedback soon
OK!
I like it sir, very clear and up to task. Now I see both the coils of the two relays connected to one supply,from the diagram above on the change over operation,it’s clear that both the DPDT relays will get energized from the delay supply. My worry is that there will be a delay in connecting grid to the load. How do we deal with that? Or we remove the delay?
No problem Evans, you can remove the delay effect, it is introduced for ensuring guaranteed safety to the MOSFETs, but removing it might still allow the circuit to work without issues.
Sir,think about this ,what if I introduce another coil to the transformer for the charging purpose alone and another relay to work with the delay alone,such that in the presence of mains supply,grid is connected with the loads first with the oscillatilor supply being cut off at the same time the coil from the transformer that outputs the inverter power is disconnected from the load,then a small delay before the charging coil is engaged to the mains. How about that.
Evans, that seems to be a good idea, which will also help to get rid of the boost converter circuit.
Thanks sir
Good job sir, atleast you promised and delivered. Now my other questions are:
1. From the diagram above,I can see in the presence of mains,the grid is connected to the transformer for charging after the delay,now what about for the appliances,coz I would like in the presence of mains,also the appliances get connected to grid uninterrupted?.
2. What will be the effect of instead of using 1k between gate and source I use a 10k resistor?.
3. Full bridge Inverters involving pwm have their transformer voltage almost half of the battery,now how will the battery be charged to full charge in such a situation,any incorporated diagram will be appreciated.
4. Also sir,what about current limiting , float charging and or auto fully charged cut off?.
Sir I have already constructed the inverter and it’s working,just waiting for your response for further upgrade.
Thank you Evans, For the appliances you will have to use another DPDT relay which will simultaneously connect the load with the grid input. The poles of the relay will connect with the load, and the N/O contacts with the grid input.
10k will also do, but lower value will provide better contact with the source line, although the value may not be critical due to high impedance of the gates.
For transformers rated 50% of the battery might require a boost converter, and another set of DPDT contacts for diverting the DC from the body diodes through the boost converter.
The boost converter output can have all the necessary features such as auto cut off float charging etc in case these are required.
Is it possible you design one booster converter with all the features say float charging, current limiting extra and show how to connect to the circuit above? I’ll really appreciate
Again thanks for your endless help,I even lack words to describe you but all I can say is God almighty bless you and Grant you your desires.
Thanks Evans, the cut off and the float can be introduced at the output of the boost charger, but I cannot design the boost charger, you will have to refer to some reliable source for the circuit such as ti.com etc for the drawing.
Okay.. then how do i reduce the current to 30a i once saw your reply using a non polar capacitor at the 220v line so what spec would fit for 30amps output when transformer is at charging mode without tempering the output voltage needed to charge the battery.
And again you reply to @evans saying he should add an external body diode to the MOSFET which i think even without additional diode the built-in body diode can handle and provide 30amps or 50amps let say using irfB4110 or ssf1006 fet ?
And again
Evans complaint that the mosfet blew up with out any reasons i think the reason the mosfet blew up was that,when the transformer is at charging mode the body diode will rectify the ac voltage to charge the battery then at rhe same time ac current will Flow through the gate/source resistor causing the mosfet to switch or open and with that mosfet bypasses the body diode and that will cause the mosfet to blow up
So i think to avoid that can we and a reverse bias diode in series with the 1k gate/source resistor to block current from switching the MOSFET so that mosfet can only switch when is it at inverter mode and at the same time gate capacitance will discharge to source pin when operating at inverter mode and if its possible can we use a diode like IN4007 for the purpose or we have to use a bigger diode ??… Pls i will be grateful to see your replys in all my questions and suggestions
Your transformer must be rated at 30 amps so that it cannot supply more than 30 amps to the load…which will ensure the battery is discharged at around 30 amps
Your assumption regarding Evans question is partially correct, however the mosfet gate is internally isolated from its source and drain so current leaking into gate might not be possible.
Okay!
You mean current won’t be able to flow through 1k resistor causing the mosfet to close and shorting the body diode?
The gate is separated by the drain and source through a capacitive region, so current cannot flow from drain or source towards the gate.
Okay..then,if so i can successfully design my inverter system using Tlp250 gate driver and Sg3524 pwm signal?
Yes, that’s right, however the body diode battery charging concept has not been tested by me practically, so please proceed with caution.
Okay! , I will try and give a feedback Thank you very much appreciated
God bless you.
No problem David, all the best to you!
Once again, Thank you.
Am Greatfull
You are most welcome, David.
Hi.. swag
Pls what will my transformer primary voltage be when using an Egs002 card ?
Hi David,
It will depend on the voltage connected with the drains of the high side mosfets
https://www.homemade-circuits.com/egs002-datasheet-circuit-diagram-explained/
Sorry i forgot mentioning the voltage. is a 24v battery. What will the transformer primary voltage be ?
And can i use wire instead of a shunt resistor at the pin 1of the egs002?
I don’t need current sensing.
The transformer primary can be 0-22V.
If you use a wire link for the current limiting resistor then your inverter will not have the over current protection.
Hi… Swagatam
Been awhile making some research about this circuit how about using a AC dimmer circuit? Using a TRIAC at the inverters output to control the secondary current coupled with relays. how possible will it be ? Can you modify the post on this exact topic? Plz I will be very greatfull if you do so…
Hi Davis,
A triac dimmer can be used at the primary of the transformer to control the secondary voltage, however i am not sure how this can be implemented to control current?
Okay,
That mean when the primary voltage changes to either high or low , it will be directly proportional to it secondary too ?
If so you once talked about using a capacitor to reduce the current but you said it will be at the secondary,why can’t we use it at the primary??
Pls what other idea is efficient, to use the same transformer for inverter and as battery charger using mosfet body diode like other professional inverters do ?
A capacitor can be added neither at the secondary or the primary, because that would restrict the inverter from operating normally in the inverter mode.
You can try the same circuit which is explained in the above, however a current controller cannot be added or maybe it could be added through an additional relay changeover stage.
Yes I would prefer using an additional relay changeover stage.
And if I am to use the transformer in charger mode, what will be the value of the capacitor and it’s voltage for restricting the current when charging the battery let say charging a 12v 7ah SLA battery.
I will like you to give me a bench mark for the capacitance value,so that I can be able to change the current used in charging the battery according to my needs
And I will prefer the capacitor to be at the primary terminal (220v side ) in serial line.
Pls help me…
Referring to the diagram, it seems we can simply add the capacitor in series with one of the N/O contacts of the secondary side DPDT relay.
However why do we even need a current regulation, because the transformer is already rated correctly to provide the calculated amount of charging current to the battery.
Yes but I mean if am not to use this circuit maybe I choose to use another circuit designed by me, what capacitor should I use for regulating the current used for charging 12v 7ah battery for example and 200ah battery?
And I will like the capacitor to be at the secondary terminal not the MOSFET terminal. Please help me
For 7Ah battery a capacitor of 1uf 400v can be used in series with the 220v side winding of the transformer, and for 200Ah this capacitor can be rated at 25uF 400v. Both should be non polar type.
Okay,sorry for much questions…
For 7ah battery, how many ampere is the 1uf 400v capacitor allowing to flow to the transformer?
And 200ah?
For 7Ah it is around 900ma on the 12v side of the transformer and around 24 amps for the 200 Ah battery, again on the 12v side of the transformer.
Okay…
Thank you very much appreciated
Am grateful…
You are welcome.
If my transformer is rated 200amp or 220amps what capacitance can i add in series line of the 220v to bring down the output current to 22amps or 30amps when using the transformer in charging mode ?
A 1uF capacitor allows around 50 ma current, so you can use this benchmark to calculate the total capacitor value for allowing 30 amps. The capacitor must be non-polar.
Ohh wow…
That means for 4amps current to flow at 220v i will use an 80uf non polarized capacitor ( Code 806) (1uf 50ma) 50ma multiply by 80 = 4,000 (4amps)
Which mean at 220v ac multiply by 4amps = 880w at the transformers output when is at charging mode .
I will use a relay to control the non polar capacitor when needed to charge the battery. Is my calculations correct??
Honestly am so excited for ur kind feedback merry Christmas in advance..
Your battery is rated at 24V 220 Ah so the charging current requirement will be around 30 amps, not 4 amps.
Merry Christmas to you too, in advance. Let me know if you have any further questions.
I’m a little bit confused here.
You mean 30amps current should be able to flow through the 220vac line ? Or the 28vac line?
Where would the capacitor be placed. at the mains input ? or the the transformers output ? before rectification.
220V is for the output winding of the transformer (load side). The actual charging voltage is coming from the input side of the transformer which is supposed to be rated at 28V. So the 30 amp is relevant to this 28V side of the transformer, not the 220V side.
Actually, the capacitor cannot be used here, because that would interfere with the normal working of the circuit while in the inverter mode.
Yes, true
And that’s makes it complex
I think adding a different windings for charging and controlling them with high amps relay would makes things more easy. And make it to be on a safer side
Thank you very much Swag.!!
That’s correct. Adding a separate winding for charging is the best and safest way to go. Appreciate your feedback.
Hi.. swag
Its a 220ah SLA battery i will be charging it at 24ac ×1.414 rms = 33vdc with respect to the filter capacitors but at 30amps current but the discharge rate won’t be same as charging rate is it possible?
Hi David,
For a 12v battery the charging voltage can be 14v and for 24v battery it can be 28v.
Discharging rate and charging rate are supposed to be identical (0.15C) to ensure long battery life
Okay its clear
a 24v 200amps = 4800w battery.
Charging current mode is 28v multiply by 30amps = 840w charger.
Does that means the inverter would be 840w ?
And if so drawing more than 840w from the transformer when loaded on inverter mode would heat up an probably burn out the coil.?
That’s correct, the inverter then would be around 800 watts.
Drawing more than this current would cause overheating of the transformer or burning.
In traditional inverters there is a charging tap at high side of the transformer which isconnected by a triac and controlled by microcontroller for 3 stage battery system …
Hi sir swagatam, there’s an observation am seeing. I see a situation whereby if I introduce another DPDT relay that will connect the load with the grid simultaneously,that it will renter the first DPDT relay useless since we have a delay meaning the transformer will get mains from the grid through the relay tht connects the load and grid because of the delay. So sir look at that issue and advise. Inshort sir advise on how to Energizer the second DPDT relay coil,is it by the direct vcc or through the delay? Av an issue configuring this. Thanks in advance.
Hi Evans, the delay will be in milliseconds only, still I will check the working by drawing the connections, and see if there’s a possible conflict.
Again sir,from the above circuit with delay, how can I increase the delay time to about 5seconds?
for 5 seconds you may have to employ a transistor driver stage, with an appropriately calculated base RC network
Thanks for this.
You did a great job in explaining the circuit.
Thank you, and glad you liked it.
Fine Sir,will be waiting to hear from you soon
Hi Evans, here’s the drawing for the DPT contact which will make sure that the load gets connected with the grid AC during inverter charging mode, and when the grid AC is available:
Hi! Sorry to append to the middle of the discussion. But my question fits best here.
Wouldn’t it be simpler not to add a second relay and just have a permanent connection of LOAD and transformer (N/C RL1a, N/C RL1b). Then we have Mains on LOAD when Mains are available and inverter power on LOAD when Mains are off.
Am I overlooking something? Is there an issue I am not aware of?
BR Phu
Hi, I don’t think that’s feasible, because that would mean feeding the inverter AC into the grid line, which would also mean that RL2a can never cut off and keep stuttering, causing an error with the inverter working
Hi… swagtam
I think when transformer is on charging mode and body diode rectify the ac to dc
Then i think at the same time ac voltage will flow through the 1k Gate/source resistor causing the mosfet to switch or open then at that time the mosfet bypasses the body diode .
Then i think that makes the mosfet to explode in @Evans circuit.
Hi David,
I am not so sure about this working concept, no I can’t suggest much on this topic.