In this article I have explained a protection circuit which may be used for preventing a "dry run" situation in mini coffee dispenser motor pumps, by sensing the slight difference in its wet and dry current consumption levels. The idea was requested by Mr. Ken Adler.
Technical Specifications
I read with great interest your post titled, "Motor dry Running, Tank Overflow Water Level Controller Circuit." We are having a similar problem with a miniature hot water pump used in coffee machines. (see attachment).

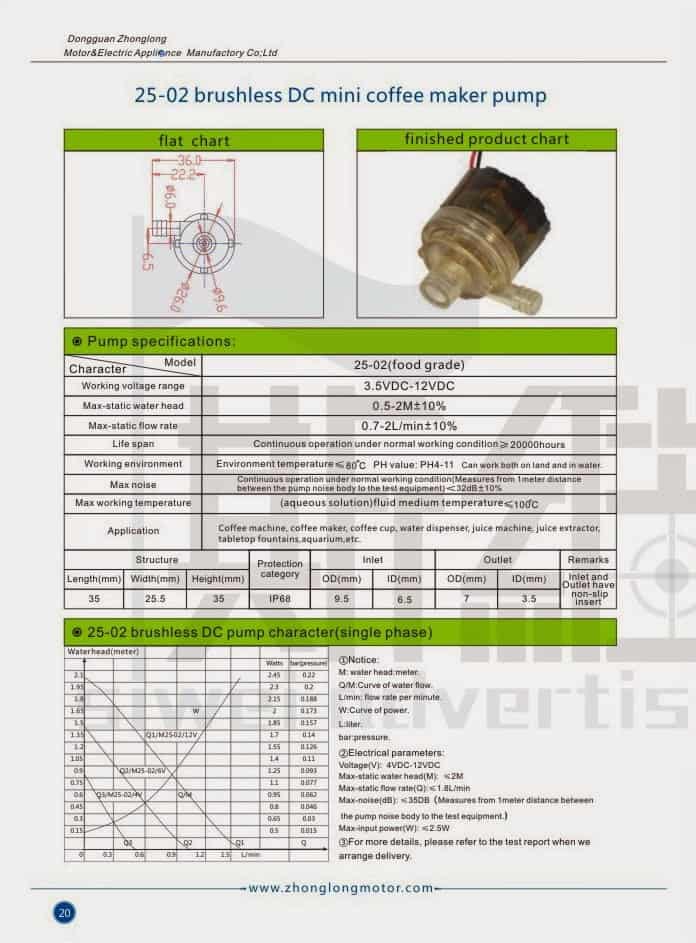
The pump typically runs at 0.15 to 0.25 amps and 4.5 to 6 volts. The data above provides the maximum operating conditions.
One end of the pump has a circuit board.
I've attached a very rough picture. Ultimately,
I'd like the manufacture to modify the circuit board to include the dry run protection. We need a very small circuit designed that would sense a change in current when the water level is below the pump.
Note that the pump is very small, and the circuit would need to be integrated into the existing board.
Would you be able to design a circuit for this application? If so, how much would you charge?
Cheers,
Ken Adler
President
Eagle Design
The Design
The requested mini coffee pump dry running protector circuit can be seen in the below given diagram, and may be understood with the help of the following points:
When power is switched ON, C1 pulls the non-inverting input pin3 of the opamp to ground so that an instantaneous low is developed at the output of the opamp.
This momentary low at the output triggers T2 which in turn initiates the connected coffee pump motor, which is assumed to be loaded here with the fluid content.
The motor switch ON causes the rated amount of current to flow through R6 which translates it into a proportionate amount of potential difference across itself and at the base of T1.
This prompts T1 to conduct and sustain pin3 of the opamp to ground so that T2 is able to hold the pump motor in the switched ON state.
Now suppose at some point of time the fluid level drops below the threshold forcing the motor to run dry, the motor current consumption also drops to a proportionate degree such that the potential across R6 becomes low enough to switch OFF T1.
As soon as T1 switches OFF, the potential at pin3 jumps above that of pin2 rendering a high at the output of the opamp which instantly switches off the motor preventing it from the "dry run" situation.
R3 makes sure that the situation gets latched ON and stays in that position until the tank gets filled and the circuit is reset by a complete switch OFF and switch ON.
Circuit Diagram
How to Set up the Circuit
- Initially keep R3 loop disconnected
- Also, disconnect the motor positive from the T2 and connect it directly with the positive of the supply so that while testing in switched ON condition the motor simulates a dry run situation (low current run)
- Now switch ON power, let the motor spin, and by little trial and error adjust VR1/VR2 until the red LED just comes ON, while the green LED shuts off.
- The pump dry run circuit is all set now, restore the R3 and the motor positive connections back to their original positions, test run the circuit under actual conditions with tank filled and empty for witnessing the intended protection features of the circuit.
Need Help? Please Leave a Comment! We value your input—Kindly keep it relevant to the above topic!